下料成型通用工艺规范汇总
下料及成型吊装安全操作规程模版(三篇)
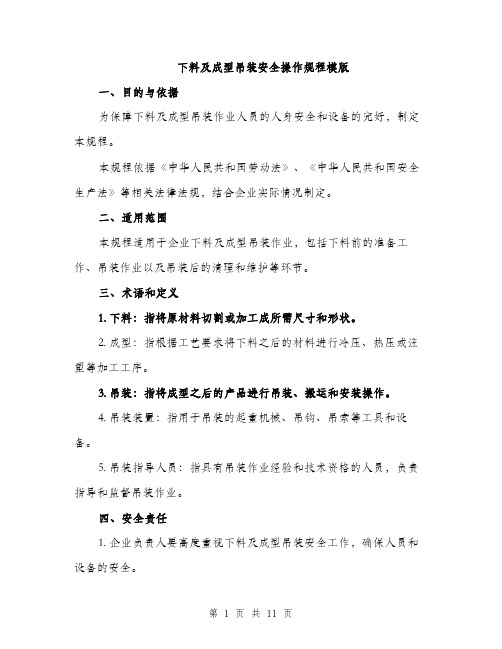
下料及成型吊装安全操作规程模版一、目的与依据为保障下料及成型吊装作业人员的人身安全和设备的完好,制定本规程。
本规程依据《中华人民共和国劳动法》、《中华人民共和国安全生产法》等相关法律法规,结合企业实际情况制定。
二、适用范围本规程适用于企业下料及成型吊装作业,包括下料前的准备工作、吊装作业以及吊装后的清理和维护等环节。
三、术语和定义1. 下料:指将原材料切割或加工成所需尺寸和形状。
2. 成型:指根据工艺要求将下料之后的材料进行冷压、热压或注塑等加工工序。
3. 吊装:指将成型之后的产品进行吊装、搬运和安装操作。
4. 吊装装置:指用于吊装的起重机械、吊钩、吊索等工具和设备。
5. 吊装指导人员:指具有吊装作业经验和技术资格的人员,负责指导和监督吊装作业。
四、安全责任1. 企业负责人要高度重视下料及成型吊装安全工作,确保人员和设备的安全。
2. 吊装作业负责人要做好下料及成型吊装作业的组织、安排和监督工作,并负责相关安全事故的调查和处理。
3. 吊装作业人员要按照规范操作,严格遵守安全操作规程,做好个人安全保护措施。
五、作业前准备1. 吊装作业前,应对吊装设备和吊装装置进行检查和测试,确保其正常运行状态。
2. 吊装作业前,应对吊装区域进行清理和标识,确保作业区域的安全。
3. 吊装作业前,应对相关人员进行安全培训和技术交底,确保其了解作业流程和安全注意事项。
4. 吊装作业前,应对吊装物进行重量和尺寸的测定,选择合适的吊装设备和吊装装置。
六、吊装作业操作流程1. 吊装作业按照作业计划和程序进行,严禁违规操作和私自改变吊装方案。
2. 吊装作业前,应将吊装物与吊装装置牢固连接,并进行试吊检查。
3. 吊装过程中,操作人员应保持通讯畅通,密切配合指挥和信号人员的指示。
4. 吊装过程中,严禁人员随意进入吊装作业区域,确保周边人员的安全。
5. 吊装结束后,应将吊装装置撤离,清理吊装区域,并进行设备检查和维护。
七、应急措施1. 在吊装作业中,如遇突发事故或异常情况,应立即停止作业,并采取相应措施进行应急处置。
机械加工下料通用工艺

引 入 / 出 切割高度
设置弧压
切割电流
mm/min
半径
2mm
1800
0.1s
1mm
121V
6mm
35A
3mm
1400
0.1s
1mm
130V
共 5 页 第4 页
4mm
2400
0.1s
1.5mm
120V
5mm
2000
0.3s
2mm
125V
60A
6mm
3200
0.5s
2mm
120V
8mm
1200
0.8s
3.5.1 端面不规则的型钢、钢板、管材等材料号料时必须将不规则部分让出。钢材表面上如有不平、 弯曲、扭曲、波浪等缺陷,在下料切割和成形加工之前,必须对有缺陷的钢材进行矫正。
3.5.2 号料时,应考虑下料方法,留出切口余量。 3.5.3 有下料定尺挡板的设备,下料前要按尺寸要求调准定尺挡板,并保证工作可靠,下料时材料 靠实挡板。
18~25
200~320
100~150
6
2.3
24~32
140~260
150~180
7
2.5
31~40
130~180
注:此表使用条件:
ⅰ切割氧压力 7~8kg/cm2;乙炔压力>0.3kg/cm2.
ⅱ氧气纯度>99.5%。
4.6.2 钢板的切割速度是与钢材在氧气中的燃烧速度相对应的。在实际生产中,应根据所用割嘴
3.1 看清下料单上的材质、规格、尺寸及数量等。 3.2 各种零件的材料必须严格按工艺要求(或图纸要求)选用,不得随意更改。对代用材料必须由有 关部门申请代用手续后方可使用。 3.3 查看材料的外观质量(疤痕、夹层、变形、锈蚀等)是否符合有关质量规定。 3.4 将不同工件所用相同材质、规格的料单集中,考虑能否套料。 3.5 号料
下料工艺规范
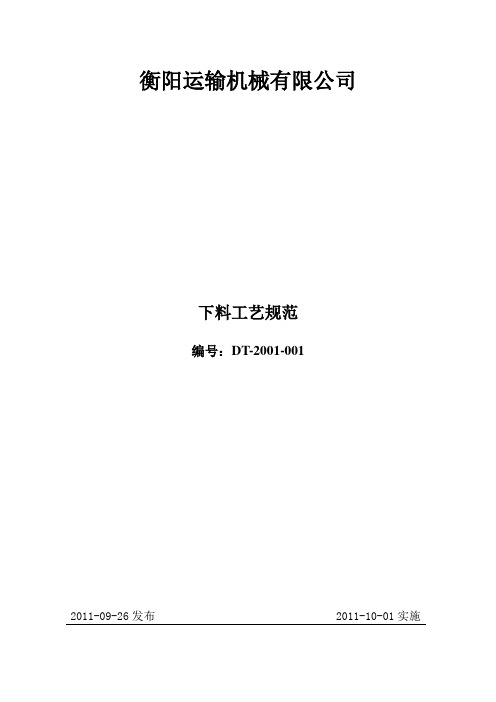
衡阳运输机械有限公司下料工艺规范编号:DT-2001-0012011-09-26发布 2011-10-01实施下料工艺规范1、适用范围本规范规定了下料应遵守的基本原则,适用于企业各切削加工所材料的下料。
下料还应遵守JB/Z 307.1标准。
2、引用标准GB 4863 机械制造工艺基本术语JB 3092 火焰切割面质量技术要求JB 3174 快速割嘴JB 307.1 切削加工通用工艺守则,总则3、下料前的准备3.1.看清下料单上的材质、规格、尺寸及数量等。
3.2.核对材质、规格与下料单要求是否相符。
材料代用必须严格履行代用手续。
3.3. 查看材料外观质量(疤痕、夹层、变形、锈蚀等)是否符合有关质量规定。
3.4.将不同工件所用的相同材质,规格的料单集中,考虑能否套料。
3.5.号料3.5.1 端面不规格的型钢、钢材、管材等材料号料时必须将不规则部分让出。
3.5.2 号料时,应考虑下料方法,留出切口余量。
3.6 有下料定尺挡板的设备,下料前要按尺寸要求调准定只挡板,并保证工作可靠,下料时材料一定靠实挡板。
4、下料4.1.剪切下料4.1.1钢板、扁钢下料时,应优先使用剪切下料。
4.1.2 用剪床下料时,剪刃必须锋利,并且应根椐下料板厚调整好剪刃间隙,其值参见附录A。
4.1.3 剪切最后剩下的料头必须保证剪床的压料板能压牢。
4.1.4 下料时应先将不规则的端头切掉。
4.1.5 切口断面不得有撕裂、裂纹、棱边。
4.2.气割下料4.2.1气割前应根椐被切割板材厚度换好切割嘴(参见附录B),调整好表压,点火试验合格后方可切割。
4.2.2 气割下料,毛坯每边应留适当加工余量,手工气割下料毛坯加工余量参见附录C。
4.2.3 气割下料后,应将气割边的挂碴、氧化物等打麿干净。
4.3 锯削下料4.3.1 用锯削下料时,应根椐材料的牌号和规格选好锯条或锯片。
4.3.2 锯削下料时,工艺留量应适当。
常用各种型材的锯削下料工艺留量参见附录D。
1下料通用工艺守则(内容)

安徽四汇机械集团有限公司下料通用工艺守则编制:陆玲玲审核:游安军批准:梁永强2014-05-13发布2014-05-28实施1.总则1.1本守则适用于压力容器主要受压元件的下料,其他零部件下料可参照执行。
1.2下料人员必须严格执行产品图样和工艺文件的规定,当图样无特殊要求时,工艺人员在编制下料工艺文件时应遵照本守则的相应规定。
2基本要求2.1下料人员凭领料单办理领料手续。
2.2下料人员必须熟悉产品图样和工艺文件的要求。
2.3切割设备必须完好,现场有足够的下料场地,四周无有碍下料工作的堆积物。
计量器具能满足测量工作的基本要求,且在检定周期内。
2.4主要元件材料必须是经检验合格入库,且经监检确认的材料。
2.5材料上有清晰的出厂标记及入库检验标记,表面质量符合要求、牌号、规格必须与产品设计图样或工艺文件一致。
2.6筒体由若干个筒节拼焊而成时,筒节最小长度不得小于300mm。
2.7压力容器主要元件下料划线结束后应进行材质标记移植,并由专职检验人员进行检验确认,打上确认标记后方可切割下料。
2.8切割方法:碳素钢,低合金钢板材可选用剪板机或气割的方法;管材、棒材可以选用砂轮切割机。
2.9筒体下料尺寸的确定筒节展开长度,可按下式进行估算L=π(Di+δn)+2c式中:L:筒节展开长度Di:筒节内直径δn :壁厚C:边缘加工余量实际下料展开长度,还应以实际周长为准。
3.0划线3.1划线尺寸的依据是产品图样和工艺文件。
3.2划出工件毛坯尺寸线和切割线。
毛坯尺寸线和切割线之间的距离应保证工件切割后毛坯尺寸线不被破坏。
常用下料方法,毛坯尺寸线和切割线之间的距离可按表一推荐的数据选用。
表一mm材料厚度火焰切割等离子切割碳弧气刨剪板机手工自动、半自动手工自动、半自动手工≤10 3 2 9 6 8 010~30 4 3 11 8 10 032~50 5 4 14 10 14 052~65 6 4 16 12 18 03.3工件毛坯尺寸取工件展开尺寸和周边加工余量之和。
下料成型操作规范
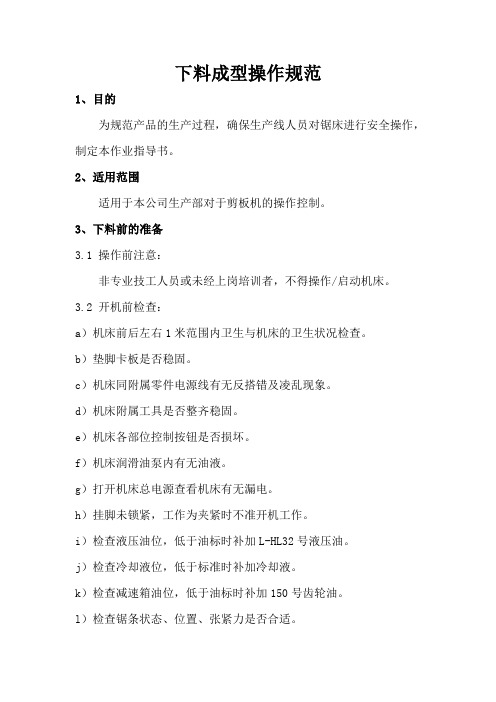
下料成型操作规范1、目的为规范产品的生产过程,确保生产线人员对锯床进行安全操作,制定本作业指导书。
2、适用范围适用于本公司生产部对于剪板机的操作控制。
3、下料前的准备3.1 操作前注意:非专业技工人员或未经上岗培训者,不得操作/启动机床。
3.2 开机前检查:a)机床前后左右1米范围内卫生与机床的卫生状况检查。
b)垫脚卡板是否稳固。
c)机床同附属零件电源线有无反搭错及凌乱现象。
d)机床附属工具是否整齐稳固。
e)机床各部位控制按钮是否损坏。
f)机床润滑油泵内有无油液。
g)打开机床总电源查看机床有无漏电。
h)挂脚未锁紧,工作为夹紧时不准开机工作。
i)检查液压油位,低于油标时补加L-HL32号液压油。
j)检查冷却液位,低于标准时补加冷却液。
k)检查减速箱油位,低于油标时补加150号齿轮油。
l)检查锯条状态、位置、张紧力是否合适。
3.3 熟悉图纸和有关工艺要求,充分了解所加工的零件的几何形状、尺寸要求,及财质、规格、数量等。
3.4 核对材质、规格与派工单要求是否相符。
材料代用时是否有代用手续。
3.5 查看材料外观质量(疤痕、夹层、变形、锈蚀等)是否符合质量要求。
3.6 为了降低消耗,提高材料利用率,要合理套裁下料。
3.7 熟悉所用的设备、工具的使用性能,严格遵守安全操作规程和设备维护保养规则。
4、操作过程4.1打开锯床总电源。
4.2 装夹工件a)按住锯床栋梁上移开关,使锯床栋梁上一道合适位置方便放料,根据加工材料的范围,时针转动手动手柄或向上搬动台虎钳液压开关手柄,将台虎钳松开到合适位置后复位。
b)将条料放入工作台面,按下锯床下移开关,当锯齿离工件为20-30mm 时点动下移开关,当锯齿距工作件表面为10-20mm时用钢板尺或角尺截取要锯削的尺寸,调节好工件的位置后,逆时针转动手动手柄或向下搬动台虎钳液压开关将台虎钳夹紧后复位。
c)结合安全锯削和工件精度要求,在夹紧工作时注意:要拿木槌敲击工件表面使工件底部与工作平面完全贴合,调节台虎钳使夹紧的工件与锯条运转方向垂直;工件装夹必须过台虎钳中心线5-10cm,如果工件较短需在台虎钳另一端垫上与工件夹紧部位同等规格的材料,使加工工件完全夹紧,避免加工过程中产生振动使锯条绷断伤人。
(完整版)下料工艺
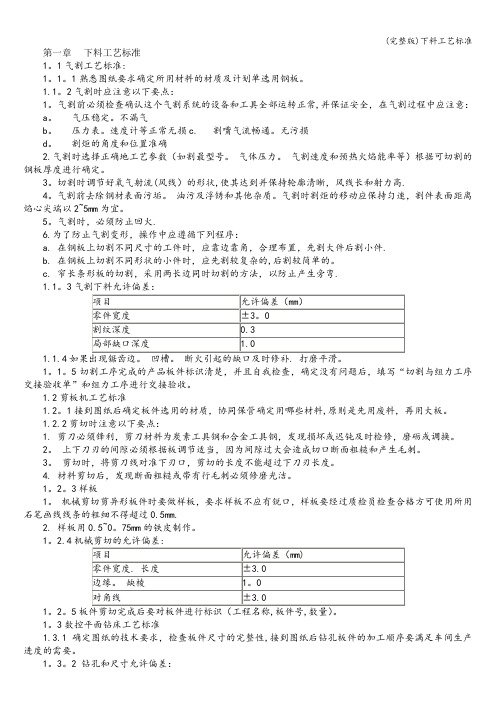
第一章下料工艺标准1。
1气割工艺标准:1。
1。
1熟悉图纸要求确定所用材料的材质及计划单选用钢板。
1.1。
2气割时应注意以下要点:1。
气割前必须检查确认这个气割系统的设备和工具全部运转正常,并保证安全,在气割过程中应注意:a。
气压稳定。
不漏气b。
压力表。
速度计等正常无损c. 割嘴气流畅通。
无污损d。
割炬的角度和位置准确2.气割时选择正确地工艺参数(如割最型号。
气体压力。
气割速度和预热火焰能率等)根据可切割的钢板厚度进行确定。
3。
切割时调节好氧气射流(风线)的形状,使其达到并保持轮廓清晰,风线长和射力高.4。
气割前去除钢材表面污垢。
油污及浮锈和其他杂质。
气割时割炬的移动应保持匀速,割件表面距离焰心尖端以2~5mm为宜。
5。
气割时,必须防止回火.6.为了防止气割变形,操作中应遵循下列程序:a. 在钢板上切割不同尺寸的工件时,应靠边靠角,合理布置,先割大件后割小件.b. 在钢板上切割不同形状的小件时,应先割较复杂的,后割较简单的。
c. 窄长条形板的切割,采用两长边同时切割的方法,以防止产生旁弯.1.1。
31.1.4如果出现锯齿边。
凹槽。
断火引起的缺口及时修补. 打磨平滑。
1。
1。
5切割工序完成的产品板件标识清楚,并且自我检查,确定没有问题后,填写“切割与组力工序交接验收单”和组力工序进行交接验收。
1.2剪板机工艺标准1.2。
1接到图纸后确定板件选用的材质,协同保管确定用哪些材料,原则是先用废料,再用大板。
1.2.2剪切时注意以下要点:1. 剪刀必须锋利,剪刀材料为炭素工具钢和合金工具钢,发现损坏或迟钝及时检修,磨砺或调换。
2。
上下刀刃的间隙必须根据板调节适当,因为间隙过大会造成切口断面粗糙和产生毛刺。
3。
剪切时,将剪刀线对准下刃口,剪切的长度不能超过下刀刃长度。
4. 材料剪切后,发现断面粗糙或带有行毛刺必须修磨光洁。
1。
2。
3样板1。
机械剪切剪异形板件时要做样板,要求样板不应有锐口,样板要经过质检员检查合格方可使用所用石笔画线线条的粗细不得超过0.5mm.2. 样板用0.5~0。
(完整版)下料工艺标准
第一章下料工艺标准1.1气割工艺标准:1.1.1熟悉图纸要求确定所用材料的材质及计划单选用钢板。
1.1.2气割时应注意以下要点:1.气割前必须检查确认这个气割系统的设备和工具全部运转正常,并保证安全,在气割过程中应注意:a. 气压稳定。
不漏气b. 压力表。
速度计等正常无损c. 割嘴气流畅通。
无污损d. 割炬的角度和位置准确2.气割时选择正确地工艺参数(如割最型号。
气体压力。
气割速度和预热火焰能率等)根据可切割的钢板厚度进行确定。
3.切割时调节好氧气射流(风线)的形状,使其达到并保持轮廓清晰,风线长和射力高。
4.气割前去除钢材表面污垢。
油污及浮锈和其他杂质。
气割时割炬的移动应保持匀速,割件表面距离焰心尖端以2~5mm为宜。
5.气割时,必须防止回火。
6.为了防止气割变形,操作中应遵循下列程序:a. 在钢板上切割不同尺寸的工件时,应靠边靠角,合理布置,先割大件后割小件。
b. 在钢板上切割不同形状的小件时,应先割较复杂的,后割较简单的。
c. 窄长条形板的切割,采用两长边同时切割的方法,以防止产生旁弯。
1.1.3气割下料允许偏差:1.1.4如果出现锯齿边。
凹槽。
断火引起的缺口及时修补。
打磨平滑。
1.1.5切割工序完成的产品板件标识清楚,并且自我检查,确定没有问题后,填写“切割与组力工序交接验收单”和组力工序进行交接验收。
1.2剪板机工艺标准1.2.1接到图纸后确定板件选用的材质,协同保管确定用哪些材料,原则是先用废料,再用大板。
1.2.2剪切时注意以下要点:1. 剪刀必须锋利,剪刀材料为炭素工具钢和合金工具钢,发现损坏或迟钝及时检修,磨砺或调换。
2. 上下刀刃的间隙必须根据板调节适当,因为间隙过大会造成切口断面粗糙和产生毛刺。
3. 剪切时,将剪刀线对准下刃口,剪切的长度不能超过下刀刃长度。
4. 材料剪切后,发现断面粗糙或带有行毛刺必须修磨光洁。
1.2.3样板1. 机械剪切剪异形板件时要做样板,要求样板不应有锐口,样板要经过质检员检查合格方可使用所用石笔画线线条的粗细不得超过0.5mm.2. 样板用0.5~0.75mm的铁皮制作。
(完整版)下料工艺守则
下料工艺守则1 主体内容与适用范围本守则规定了钢材划线、下料及矫正的有关技术要求。
本守则适用于板材、型材和管材的划线、下料及矫正。
2 操作前的准备2.1 操作人员应熟悉图样、技术要求及工艺文件的内容,并熟悉所用的设备、工具的使用性能,严格遵守安全操作规程和设备维护保养规则。
数控切割应预先输入图形或编制程序。
气割及设备操作人员须考试合格后上岗。
2.2 操作人员应按有关文件的规定,认真做好现场管理工作。
对工件和工具应备有相应的工位器具,整齐地放置在指定地点,防止碰损、锈蚀。
2.3 操作前,操作人员应准备好作业必备的工具、量具,并仔细检查、调试所用的设备、仪表、量检具、模具、刀具,使其处于良好的状态。
使用的仪表、量检具应在有效检定期内。
3 划线3.1 一般规定3.1.1 钢材存在影响划线的弯曲、凹凸不平时,应先进行矫正。
3.1.2 划线前,钢材表面必须清理干净,去除油污、锈蚀等,发现钢材有裂纹、严重锈蚀等缺陷,应经检查部门做出处理后,方可划线。
3.1.3 自行制作的划线样板、样杆,应得到检验部门的确认。
3.2 划线的技术要求3.2.1 应按设计图样、工艺文件在钢材上以1:1实样进行划线,根据不同的下料方法,划线时应留出适当的切割余量。
3.2.2 断面不规则的板材、型材及管材等材料划线时,必须将不规则部分让出。
应注意个别件对材料轧制纹络的要求。
3.2.3 用石笔所划出的线条及粉线所弹出的线条必须清晰。
3.2.4 划线时,应首先划基准线,而后再划其它线;对于对称的工件,一般应先划中心线,以此为基准在划圆弧,最后在划各直线。
划线时可用样冲打小眼让圆规定脚。
3.2.5 需要剪切的工件,划线时应考虑剪切线是否合理,避免发生不适于操作的情况。
3.2.6 在带有毛边的钢板上下料线时,要根据钢板毛边的实际情况,去除不符合钢板质量要求的部分,并在此基础上再向内让出10mm划出下料线。
3.3 划线的标记3.3.1 划线时,当所划的线除有下料线外,还有其它线时应对主要的线加注标记,并用油漆笔标出,以示区别。
(工艺技术)下料成型通用工艺规范汇总
T —0908--01剪板下料通用工艺规范编制/日期:审核/日期:批准/日期:剪板机下料通用工艺规范1总则本标准根据结构件厂现有的剪床,规定了剪板机下料应遵守的工艺规范,适用于在剪板机上下料的金属材料。
剪切的材料厚度基本尺寸为0.5~13mm (不同设备剪切的板厚不同),料宽最大为2500mm2引用标准GB/T 16743-1997 冲裁间隙JB/T 9168.1-1998 切削加工通用工艺守则下料3 下料前的准备3.1 熟悉图纸和有关工艺要求,充分了解所加工的零件的几何形状、尺寸要求,及材质、规格、数量等。
3.2 核对材质、规格与派工单要求是否相符。
材料代用时是否有代用手续。
3.3 查看材料外观质量(疤痕、夹层、变形、锈蚀等)是否符合质量要求。
3.4 为了降低消耗,提高材料利用率,要合理套裁下料。
3.5 厚板件有材质纤维方向要求的应严格按工序卡片要求执行。
3.6 下料前要按尺寸要求调准定尺挡板,并保证工作可靠,下料时材料一定靠实挡板。
3.7 熟悉所用的设备、工具的使用性能,严格遵守安全操作规程和设备维护保养规则。
3.8 操作人员应按有关文件的规定,认真做好现场管理工作。
对工件和工具应备有相应的工位器具,整齐地放置在指定地点,防止碰损、锈蚀。
3.9 操作前,操作人员应准备好作业必备的工具、量具、样板,并仔细检查、调试所用的设备、仪表、量检具、样板,使其处于良好的状态。
剪板机各油孔加油。
3.10下料好的物料应标识图号与派工单一同移工。
4剪板下料4.1剪床刀片必须锋利及紧固牢靠, 并按板料厚度调整刀片间隙。
4.2钢板剪切时,剪刃间隙符合JB/T 9168.1 标准要求,见表1表1:钢板剪切时剪刃间隙(单位:mm4.3先用钢笔尺量出刀口与挡料板两断之间的距离,反复测量数次,然后先试剪一块小料核对尺寸正确与否,如尺寸公差在规定范围内,即可进行入料剪切,如不符合公差要求,应重新调整定位距离,直到符合规定要求为止。
下料工艺守则
下料工艺守则1.材料1.1.1采购部负责供给符合设计图纸、工艺文件要求的合格材料,施工人员领料时应复核以下内容1.材料标记(钢号、炉批号、复验号)、规格及数量;2.材料表面质量:无机械损伤,无严重锈蚀等;3.如要求进行逐张超探或冲击试验的,其检测报告。
2.排版对于设备需自己加工的封头、筒体、变径段、裙座以及结构复杂的配件等应进行排版。
具体如下:2.1根据图样及实际材料规格进行排版。
2.2除图样有特殊规定外,通常按一下规定进行排版:a.壳体的最短筒节长度不小于300mm;b.同一筒节纵缝应相互平行,相邻焊缝间距的弧长应不小于500mm;c.相邻筒节A类接头焊缝中心线外圆弧长以及封头A类焊缝中心线与相邻筒节A类焊缝中心线间外圆弧长应大于钢材厚度δ s的3 倍,且不小于100mm;d.排版时焊缝位置应尽量避开开孔位置,容器内件焊缝边缘应避开壳体的纵环缝;e.卧式容器下部140°范围内不应设置纵焊缝;f.封头由瓣片和顶圆板拼接制成时,焊缝方向只允许是径向和环向的,封头各种不相交的拼缝中心线间距离至少应为钢材厚度δS的3倍,且不小于Ioomm,如图1-1:图ITh.球壳瓣片最小宽度不小于500mm;1.筒节展开周长按中径计算L= π (Di+δn) -∆L+HDi——圆筒的内直径;δn——钢板的名义厚度;——钢板的伸长量;H——焊缝收缩量。
J.材料切割前应先进行标记移植,移植时应有检验员的确认,确保标记移植的准确性。
k.排版图应包括:度数线、筒节中径展开长度、筒体总长、筒体件号、板规格、材质、筒节编号、筒节尺寸、焊缝编号、开孔编号、开孔中心标高及轴线的距离、收口缝位置、编制、审核、排版日期等内容。
1.排版前应考虑焊缝收缩余量。
m.对于分段出厂的设备,排版图上应标注分段处位置。
分段的基本原则:(I)根据设备的形状特征、结构,分段线应尽量避开内件焊缝、塔壁不等厚处及材质不相同处。
(2)根据运输条件、起重能力及工艺装备的允许尺寸或合同确定分段。
- 1、下载文档前请自行甄别文档内容的完整性,平台不提供额外的编辑、内容补充、找答案等附加服务。
- 2、"仅部分预览"的文档,不可在线预览部分如存在完整性等问题,可反馈申请退款(可完整预览的文档不适用该条件!)。
- 3、如文档侵犯您的权益,请联系客服反馈,我们会尽快为您处理(人工客服工作时间:9:00-18:30)。
T—0908--01剪板下料通用工艺规范编制/日期:审核/日期:批准/日期:剪板机下料通用工艺规范1、总则本标准根据结构件厂现有的剪床,规定了剪板机下料应遵守的工艺规范,适用于在剪板机上下料的金属材料。
剪切的材料厚度基本尺寸为0.5~13mm(不同设备剪切的板厚不同),料宽最大为2500mm。
2 引用标准GB/T 16743-1997 冲裁间隙JB/T 9168.1-1998 切削加工通用工艺守则下料3 下料前的准备3.1 熟悉图纸和有关工艺要求,充分了解所加工的零件的几何形状、尺寸要求,及材质、规格、数量等。
3.2 核对材质、规格与派工单要求是否相符。
材料代用时是否有代用手续。
3.3 查看材料外观质量(疤痕、夹层、变形、锈蚀等)是否符合质量要求。
3.4 为了降低消耗,提高材料利用率,要合理套裁下料。
3.5 厚板件有材质纤维方向要求的应严格按工序卡片要求执行。
3.6 下料前要按尺寸要求调准定尺挡板,并保证工作可靠,下料时材料一定靠实挡板。
3.7 熟悉所用的设备、工具的使用性能,严格遵守安全操作规程和设备维护保养规则。
3.8 操作人员应按有关文件的规定,认真做好现场管理工作。
对工件和工具应备有相应的工位器具,整齐地放置在指定地点,防止碰损、锈蚀。
3.9 操作前,操作人员应准备好作业必备的工具、量具、样板,并仔细检查、调试所用的设备、仪表、量检具、样板,使其处于良好的状态。
剪板机各油孔加油。
3.10 下料好的物料应标识图号与派工单一同移工。
4 剪板下料4.1 剪床刀片必须锋利及紧固牢靠,并按板料厚度调整刀片间隙。
4.2 钢板剪切时,剪刃间隙符合JB/T 9168.1标准要求,见表1。
表1:钢板剪切时剪刃间隙(单位:mm)4.3 先用钢笔尺量出刀口与挡料板两断之间的距离,反复测量数次,然后先试剪一块小料核对尺寸正确与否,如尺寸公差在规定范围内,即可进行入料剪切,如不符合公差要求,应重新调整定位距离,直到符合规定要求为止。
然后进行纵挡板调正,使纵与横板或刀口成90°并紧牢。
4.4 剪切最后剩下的料头必须保证剪床的压料板能压牢。
4.5 下料时应先将不规则的端头切掉,切最后剩下的料头必须保证剪床的压料板能压牢。
4.6 切口端面不得有撕裂、裂纹、棱边,去除毛刺。
4.7 剪床上的剪切4.7.1 清理工件并划出剪切线,将钢板放至剪床的工作台面上,使钢板的一端放在剪床台面上以提高它的稳定性,然后调整钢板。
4.7.2 剪切线的两端对准下刀口,控制操作机构将剪床的压紧机构先将钢板压牢,再进行剪切。
4.7.3 剪切狭料时,在压料架不能压住板料的情况下可加垫板和压板,选择厚度相同的板料作为垫板。
剪切板料的宽度不得小于20毫米。
4.7.4 剪切尺寸相同而数量又较多时,必须先进行试剪,并检验被剪尺寸是否正确,然后才能成批剪切。
4.8零件为弯曲件或有料纹要求的,应按其料纹、轧展的方向进行裁剪。
弯曲件必须保持折弯两端的同一板面下刀剪切,防止折弯开裂倾向。
5 质量检查首件必须经检查符合工艺或图纸的要求,合格后方可进行批量下料,中间要进行抽验。
6 工作结束6.1 关闭电源。
6.2 清除机床上的铁屑,并将各部分擦拭干净。
6.3 整理零件,清除机床周围的杂物,把剩余零件摆齐。
6.4 产品图样以及所有工艺文件在使用中均应保持整洁。
7 安全及注意事项7.1 严格遵守操作规程,穿戴好规定的劳保用品。
7.2 在操作过程中,要精神集中,送料时严禁将手伸进压板以内。
7.3 剪切所用的后挡板和纵向挡板必须经机械加工,外形平直。
7.4 安装更换、调整刀刃时必须切断电源,先用木板或其他垫板垫好刀刃,以防失手发生事故,操作过程中要经常停车检查刀片、紧固螺丝钉及定位挡板是否松动、移位。
7.5 上班工作前应空车运转2~3分钟检查机床是否正常,发现异常或杂音,应及时检修,运转过程要及时加注润滑油保持机床性能好。
7.6 启动机床前必须拿掉机床上所有工具、量具及其他物件。
7.7 操作中严禁辅助工脚踏闸板,操作者离开机床必须停车。
7.8 下好的原材料应标记图号和规格,以防错乱。
T—0908-17仿形切割通用工艺规范编制/日期:审核/日期:批准/日期:仿形切割通用工艺规范1 范围本标准根据结构件厂现有仿形切割机,规定了仿形切割机下料应遵守的工艺规范,适用于在仿形切割机上下料的金属材料。
2 下料前的准备2.1 熟悉图纸和有关工艺要求,充分了解所加工的零件的几何形状、尺寸要求,及材质、规格、数量等。
2.2 核对材质、规格与派工单要求是否相符。
材料代用时是否有代用手续。
2.3 查看材料外观质量(疤痕、夹层、变形、锈蚀等)是否符合质量要求。
2.4 为了降低消耗,提高材料利用率,要合理套裁下料。
2.5检查工作场地是否符合安全生产要求。
2.6检查回火防止器工作状态是否正常。
2.7将电源插头(220V,交流电源)与操作板上的插座连接起来。
2.8分别将氧气和乙炔橡皮管接到气体分配器上并加以紧固使其接通,同时开启氧气和乙炔。
2.9把需要的割嘴装在割具上,并需注意要缓慢地拧紧割嘴螺帽,供接触部分能很好的贴合。
2.10将气割靠模固定在支架上,并调整好磁铁滚轮与气割靠模的位置,如滚轮与气割靠模不在一个平面上,则可调节底座上四个螺钉来平衡,使磁铁滚轮与气割靠模的接触在同一水平面上,以保证气割质量。
2.11 下料好的物料应标识图号与派工单一同移工。
3 下料3.1首先将切割边缘用热火焰加热到燃烧速度(实际常加热到表面熔化温度),开启切割氧进行切割。
3.2火焰焰心离切割表面3~5㎜,此距离要求在整个切割过程中保持均匀。
3.3气割过程中若有割不穿现象,应立即停止气割,以免气涡及熔渣在割缝中旋转,使割缝产生凹坑,重新起割时应选择另一方向作为起割点,整个气割过程必须保持均匀一致的速度,以免影响割缝宽度和表面光洁度。
3.4气割快结束时,速度可适当减慢,以减小后拖量。
在气割时可采用割矩后倾,使后拖量减少。
附表:Array3.5气割规范(氧-乙炔)切割那轮廓零件时,气割靠模的尺寸公差应符合:3.00)]([+-+-=b d B A式中d —磁力机头直径(常用d =12)b —切口宽度 A —气割靠模 B —零件尺寸 附表: 气割金属厚度(㎜)切口宽度(㎜)气割金属厚度(㎜)切口宽度(㎜) 5~12 2~2.3 53~62 3.6~3.8 13~24 2.4~2.6 63~74 3.9~4.1 23~32 2.7~2.9 75~86 4.2~4.5 33~40 3~3.2 87~1004.6~5.041~523.3~3.53.7、切割外轮廓零件时,气割靠模外形的尺寸公差应符合下式规定:3.0)]([+---=b d B A3.8、靠模切割零件的公差不得超过:内形1+- 外形01+- 3.9、消除熔渣。
外靠模:内靠模:4 质量检查首件必须经检查符合工艺或图纸的要求,合格后方可进行批量下料,中间要进行抽验。
5 工作结束5.1 关闭机电源。
5.2 清除仿形切割机上的熔渣,并将各部分擦拭干净。
5.3整理零件,清除加工场地的杂物,把零件摆齐,符合5S 管理要求。
6 安全及注意事项6.1 严格遵守操作规程,穿戴好规定的劳保用品。
6.2在气割过程中要特别防止燃烧爆炸,防止的主要措施有:6.2.1、割嘴不要过分接近熔融金属。
6.2.2、避免焊嘴过热,过热可以水冷。
6.2.3、严防焊嘴被熔化金属堵塞。
6.2.4、割枪通道和皮管应畅通无阻。
6.2.5、各处阀门应严密,严防氧气倒回乙炔管道,形成混合气体。
6.2.6、操作场地10米以内不能有易燃物品。
6.2.7、割枪各部分不能沾粘油污。
6.3 下好的原材料应标记图号和规格,以防错乱。
T—0908—19数控火焰下料通用工艺规范编制/日期:审核/日期:批准/日期:数控火焰下料通用工艺规范1 范围范围:本标准适用于原材料切割下料的加工过程。
适用于结构件厂数控火焰切割机EXA6000作为切割方式的切割下料过程。
材料厚度基本尺寸为δ20mm以上。
2 引用标准数控火焰切割机厂家说明及安全规程3 下料前的准备3.1 操作人员必须按照规定经专门的安全技术培训,操作者必须熟悉本机的性能、结构、传动系统,掌握操作程序。
取得作业操作资格证书,方能独力上岗操作。
3.2 操作人员必须严格遵守操作安全规程,和有关橡胶软管、氧气瓶、各种工业切割气瓶的安全使用规则和焊割安全操作规则。
3.3 工作前必须穿戴好劳动防护用品,操作时必须戴好防护眼镜。
3.4 熟悉图纸和有关工艺要求,充分了解所加工的零件的几何形状、尺寸要求,及材质、规格、数量等。
3.5 核对材质、规格与派工单要求是否相符。
材料代用时是否有代用手续。
3.6 查看材料外观质量(疤痕、夹层、变形、锈蚀等)是否符合质量要求。
3.7 开动设备前检查各部是否完好,按润滑要求做好润滑工作,检查各管道接口是否牢靠。
)检查各气路、阀门,是否有无泄漏,气体安全装置是否有效。
检查所提供气体入口压力是否符合规定要求。
检查所提供电源电压是否符合规定要求。
3.8 检查设备机架纵横移动,割炬调整是否灵活、正常。
3.9 将编制好的程序用U盘或磁盘拷入机床的控制柜内分类储存。
3.10 为了降低消耗,提高材料利用率,要合理套下料。
3.11 中、厚板件有材质纤维方向要求的应严格按工序卡片要求执行。
3.12 熟悉所用的设备、工具的使用性能,严格遵守安全操作规程和设备维护保养规则。
3.13 操作人员应按有关文件的规定,认真做好现场管理工作。
对工件和工具应备有相应的工位器具,整齐地放置在指定地点,防止碰损、锈蚀。
3.14 操作前,操作人员应准备好作业必备的工具、量具、样板,并仔细检查、调试所用的设备、仪表、量检具、样板,使其处于良好的状态。
4 下料4.1 调整被切割的钢板、尽量与轨道保持平行。
4.2 根据板厚和材质,选择适当割嘴。
使割嘴与钢板垂直。
4.3 根据不同板厚和材质、重新设定机器中的切割速度和预热时间,设定预热氧、切割氧合理的压力。
4.4 在点火后,不得接触火焰区域。
操作人员应尽量采取飞溅小的切割方法,保护割嘴。
4.5 检查加热火焰,以及切割氧射流,如发现割嘴有损坏,应及时更换、清理。
清理割嘴应用专用工具清理。
4.6 切割过程中发生回火现象,应及时切断电源,停机并关掉气体阀门,回火阀片若被烧化,应停止使用,等厂家或专业人员进行更换。
4.7 数控火焰操作工操作切割机时,要时刻注意设备运行状况,如发现有异常情况,应按下紧停开关,及时退出工作位,严禁开机脱离现场。
4.8 操作人员应注意,切割完一个工件后,应将割炬提升回原位,运行到下一个工位时,再进行切割。
4.9 操作人员应按给定切割要素的规定选择切割速度,不允许单纯为了提高工效而增大设备负荷,处理好设备寿命与效率和环保之间的关系。