烤漆房设计方案结构图
标准喷烤漆房设计方案
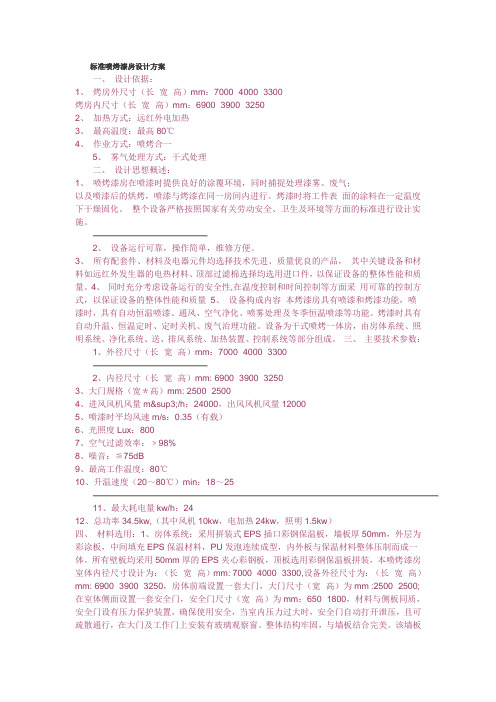
具有如下特点:轻型,新颖,造型美观; 保温,隔热,隔声性能良好;强度,刚度,稳定性,抗冲击性能好预制装配化程度高,施工快捷2、框架系统:由于该喷烤漆房的高度达到了56000mm,为了使该喷烤漆房达到更安全和精益求精的目的,我们设计了该框架结构。
(在一般的喷烤漆房没有这一块)。
采用75mm×100mm的方型钢管,从内部穿过复合板,并且横竖各个方向连接起来,形成一个整体。
共6组。
3、照明系统:采用顶侧部与腰侧灯相结合照明的方法,此结构使房内光线柔和,光照均匀明亮,且室内光强达800Lum以上,照明灯管采用菲利浦灯管进行照明,镇流器为专用镇流器,性能稳定,使用寿命长。
4、净化系统:采用具有精粗双重过滤结构,粗郊过滤层能有效地捕捉直径大于10μm的尘粒,精密级亚高效过滤层为荷兰产特厚过滤棉具有多层结构,能有效地捕捉直径大于4μm的尘粒,整个过滤系统尘量大、阻力小、寿命长、过滤效率可达98%以上。
5、送、排风系统:根据喷烤漆室风量的要求,取总的送风量为18000m³/h,喷烤漆房采用2套送、排风系统,每套送、排风系统设置1台和2台3kw的风机,此风机采用引进西门子技术生产的YDW系列双进风离心风机,采用镀锌板模压成型,风量大,耐温性好。
均有专用风机厂制造。
①送风量的确定:根据公式Qs﹦1800FV式中Qs—送风量(m³/h)F—送风区截面积(m³)V—设计风速(m/s)计算得:送风量及考虑风阻等其他因素。
这里取送风两位Qs﹦18000 m³/h。
考虑到设备启动功率、噪音、送风的均匀性,故给喷漆室均配置两套送风系统、两套排风系统。
送、排风及主要技术参数如下:型号:YDW-4.5L 流量;12000 m³/h/台全压:820Pa 转速:900r/min 功率:4kw 数量:1台6、加热系统:采用远红外电加热装置。
烤漆房设计方案
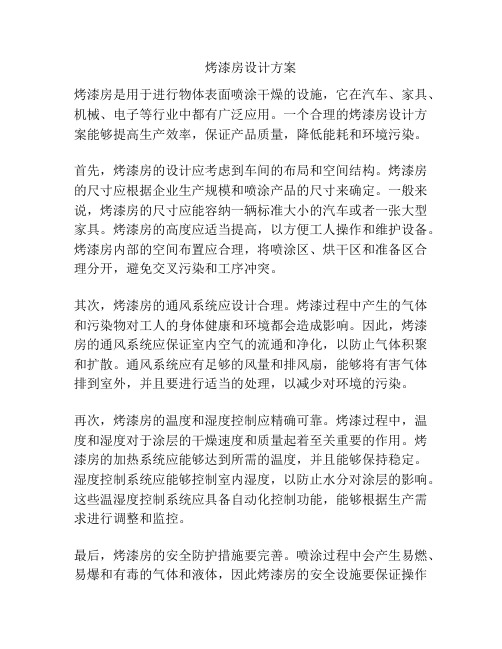
烤漆房设计方案烤漆房是用于进行物体表面喷涂干燥的设施,它在汽车、家具、机械、电子等行业中都有广泛应用。
一个合理的烤漆房设计方案能够提高生产效率,保证产品质量,降低能耗和环境污染。
首先,烤漆房的设计应考虑到车间的布局和空间结构。
烤漆房的尺寸应根据企业生产规模和喷涂产品的尺寸来确定。
一般来说,烤漆房的尺寸应能容纳一辆标准大小的汽车或者一张大型家具。
烤漆房的高度应适当提高,以方便工人操作和维护设备。
烤漆房内部的空间布置应合理,将喷涂区、烘干区和准备区合理分开,避免交叉污染和工序冲突。
其次,烤漆房的通风系统应设计合理。
烤漆过程中产生的气体和污染物对工人的身体健康和环境都会造成影响。
因此,烤漆房的通风系统应保证室内空气的流通和净化,以防止气体积聚和扩散。
通风系统应有足够的风量和排风扇,能够将有害气体排到室外,并且要进行适当的处理,以减少对环境的污染。
再次,烤漆房的温度和湿度控制应精确可靠。
烤漆过程中,温度和湿度对于涂层的干燥速度和质量起着至关重要的作用。
烤漆房的加热系统应能够达到所需的温度,并且能够保持稳定。
湿度控制系统应能够控制室内湿度,以防止水分对涂层的影响。
这些温湿度控制系统应具备自动化控制功能,能够根据生产需求进行调整和监控。
最后,烤漆房的安全防护措施要完善。
喷涂过程中会产生易燃、易爆和有毒的气体和液体,因此烤漆房的安全设施要保证操作人员的安全。
烤漆房应配置火灾报警器、喷淋系统、泄漏报警器等装置,以应对突发状况。
同时,烤漆房的操作人员也应接受相关培训,掌握安全操作规程和紧急处置措施,提高对安全风险的认识和处理能力。
综上所述,一个合理的烤漆房设计方案应考虑到车间布局、通风系统、温湿度控制和安全防护。
通过科学合理的设计,可以提高生产效率,保证产品质量,降低能耗和环境污染,同时保障操作人员的安全。
这对于企业的可持续发展和提高市场竞争力具有重要意义。
喷漆烘干房方案及配制单

喷漆烘干房方案及配制单喷烤漆房设计方案及配制一、设计依据1、工件名称: 木制品2、加热方式: 远红外线3、温度:20?,45?任意可调4、漆雾处理方式:干式处理5、废气处理方式:湿式处理6、喷漆烘干房尺寸:4米×10米×3.1米(不含水槽尺寸) 二、设计目标1、喷漆房具备通风速度快,换气次数多,空气净化度高,使物体表面光洁度高,漆雾排放量合理等功能。
2、整台设备严格按照国家相关劳动、安全、卫生、消防、环保等方面标准进行设计(实施)。
3、设备运行可靠、操作维护简便。
4、选用配套件材料及电器原件均选择技术先进、质量优良领先的产品。
5、控制系统充分考虑相互之间的联锁性,在温度、风力方面都采取了保护措施。
三、设备组成说明该设备由房体系统、净化系统、照明系统、送风系统、漆雾废气处理系统、控制系统、加热装置、底部钢格栅和排风道组成。
1、房体主要有:墙板、骨架、顶板静压室、工件进出门、隔断门成。
12、墙板采用拼装式彩钢复合板,此板阻燃、保温、新颖、隔热隔音、施工快捷,彩钢板厚度0.3?,强度、稳定性、抗冲击性能好。
3、在房体顶部高设有静压室,高500?,从进风系统送来的新鲜风进入静压室,在静压室与操作室这之间,铺有钻石漆房专用,型钢顶网骨架,无接缝式连接(能更好地防止灰尘掉落)及意大利进口材料生产的精密级亚高效过滤棉,风经过此棉后,气流流向操作间更平稳,避免了紊流现象的产生。
4、工件进出门为手动折叠式,大门上设有钢化玻璃观察窗,外侧装有安全压力锁,内侧配有大门插销总成,内外能开,操作方便。
喷漆、烘干房中间隔断门为推拉门。
5、照明系统采用腰侧灯与过滤网相结合照明方法,此结构使房内各点光线柔和,光照均匀明亮,顶侧灯组成45?角安装,灯管采用高效光源进行照明,镇流器采用喷漆房专用镇流器,从而保证每个角度喷漆时光照度达到850lux(勒克司)满足工件各端面的喷漆作业。
6、空气过滤净化系统;采用干式处理,整个空气过滤为亚高效过滤,此过滤形式可以降低风速,增加容尘量,减少滤棉更换次数,有效地捕捉、阻挡直径大于5um的尘粒。
喷漆房及烤漆房设计及相关计算
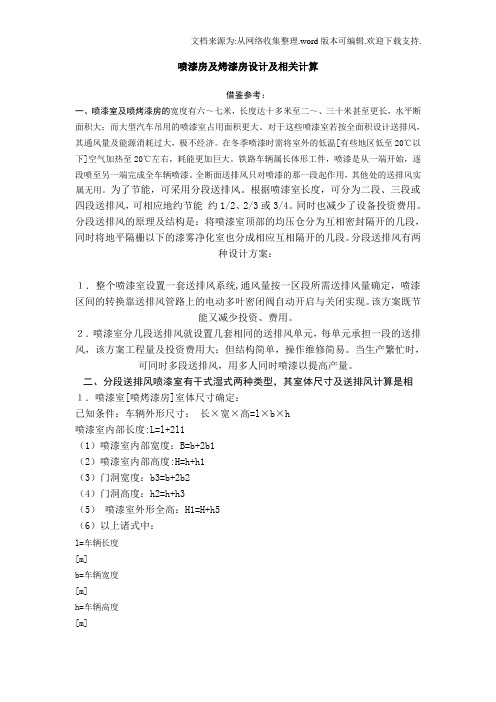
喷漆房及烤漆房设计及相关计算借鉴参考:一、喷漆室及喷烤漆房的宽度有六~七米,长度达十多米至二~、三十米甚至更长,水平断面积大;而大型汽车吊用的喷漆室占用面积更大。
对于这些喷漆室若按全面积设计送排风,其通风量及能源消耗过大,极不经济。
在冬季喷漆时需将室外的低温[有些地区低至20℃以下]空气加热至20℃左右,耗能更加巨大。
铁路车辆属长体形工件,喷漆是从一端开始,逐段喷至另一端完成全车辆喷漆。
全断面送排风只对喷漆的那一段起作用,其他处的送排风实属无用。
为了节能,可采用分段送排风。
根据喷漆室长度,可分为二段、三段或四段送排风,可相应地约节能约1/2、2/3或3/4。
同时也减少了设备投资费用。
分段送排风的原理及结构是:将喷漆室顶部的均压仓分为互相密封隔开的几段,同时将地平隔栅以下的漆雾净化室也分成相应互相隔开的几段。
分段送排风有两种设计方案:1.整个喷漆室设置一套送排风系统,通风量按一区段所需送排风量确定,喷漆区间的转换靠送排风管路上的电动多叶密闭阀自动开启与关闭实现。
该方案既节能又减少投资、费用。
2.喷漆室分几段送排风就设置几套相同的送排风单元,每单元承担一段的送排风,该方案工程量及投资费用大;但结构简单,操作维修简易。
当生产繁忙时,可同时多段送排风,用多人同时喷漆以提高产量。
二、分段送排风喷漆室有干式湿式两种类型,其室体尺寸及送排风计算是相1.喷漆室[喷烤漆房]室体尺寸确定:已知条件:车辆外形尺寸:长×宽×高=l×b×h喷漆室内部长度:L=l+2l1(1)喷漆室内部宽度:B=b+2b1(2)喷漆室内部高度:H=h+h1(3)门洞宽度:b3=b+2b2(4)门洞高度:h2=h+h3(5)喷漆室外形全高:H1=H+h5(6)以上诸式中:l=车辆长度[m]b=车辆宽度[m]h=车辆高度[m]l1=车辆端面至室体端墙内面距离[m]无三维工作台时,取l1=1.5m有三维工作台时,取l1=2~2.2mb1=车辆侧边至室体侧墙内面距离 [m]无三维工作台时,取1.5m有三维工作台时,取1.5~2m,根据三维工作台尺寸定。
烤漆房

10、烤漆房考核内容
1、标准烤漆房的尺寸;外部尺寸 ,内部尺寸 。 2、标准烤漆房进,排风风量 ,马达功率 。 3、标准烤漆房照明亮度 。 4、燃烧机功率 ,耗油量为 。 5、标准烤漆房实际操作步骤: 烤漆: 喷漆: 6、烤漆房过滤棉更换时间,地棉 ,初效过滤棉、顶棉 7、标准烤漆房工作压力 。 8、燃烧机故障排除的步骤:
Classic : 1000*1000=21块;1000*400=7块 Master : 1000*1000=24块;1000*400=12块 Euromat: 1000*1000=21块;1000*400=7块
3、下顶棉尺寸:Classic
Classic : 3200*970=7块 Master : 2200*970=12块
解答:燃烧机在工作当中吸了空气导致油路不畅通,或是燃烧介子太脏导致油路不畅通;
解决方案:清理油路,按控制盒上复位钮。 燃烧机在长期的使用当中,会使一些机件磨损引起油路不畅通或是没注意柴油箱内柴油不够引起吸入空气 若时吸入空气只需复位排除空气;若是燃烧介子太脏导致油路不畅通则需把燃烧机前端进油过滤杯拆洗、 燃烧机内柴油泵前端过滤网拆洗、燃烧机喷油嘴拆洗(可建议每月拆洗一次)。 3、烤漆房温度感应探头数量:(两个) 所有烤漆房均有两组温度感应探头,壹组为实际温度显示探头安装于烤漆房内或是烤漆房屋顶;用来控制 烤漆房内实际温度。壹组为安全限温感应探头安装于燃烧机后端烤漆房前商;用来控制燃烧机电源。 4、燃烧机不工作:(偶尔故障) 若有燃烧机不工作经排查以上1、2、3项均正常后还是不能工作;那就得仔细检查燃烧机内部的接线端是 否有松托的现象比如:控制盒出来的对插头、输油泵电磁阀的对插头及燃烧机电源进线的对插头等。
8、简易故障排除
烤漆房燃烧机不工作故障解答: 1、烤漆房温度设置正常(预设温度高于实际温度);烤漆房不升温、燃烧机没点火故障判断: 解答:燃烧机限温开关保护,解决方案,只需把开关复位。 在燃烧机主机上方有安装温度保护开关(温度安全开关);原厂来时安全开关温度设置最高为90度; 当预设温度于85度以上时,燃烧室内温度将会高于90度时,这时安全开关就会作动把燃烧机电源切断不让 其燃烧,以保证烤漆房内温度不会过高。 2、烤漆房温度设置正常(预设温度高于实际温度);烤漆房不升温、燃烧机没点火并且于燃烧机控制盒 上复位钮亮红灯故障判断:
喷漆房及烤漆房设计及相关计算

喷漆房及烤漆房设计及相关计算借鉴参考:一、喷漆室及喷烤漆房的宽度有六~七米,长度达十多米至二~、三十米甚至更长,水平断面积大;而大型汽车吊用的喷漆室占用面积更大。
对于这些喷漆室若按全面积设计送排风,其通风量及能源消耗过大,极不经济。
在冬季喷漆时需将室外的低温[有些地区低至20℃以下]空气加热至20℃左右,耗能更加巨大。
铁路车辆属长体形工件,喷漆是从一端开始,逐段喷至另一端完成全车辆喷漆。
全断面送排风只对喷漆的那一段起作用,其他处的送排风实属无用。
为了节能,可采用分段送排风。
根据喷漆室长度,可分为二段、三段或四段送排风,可相应地约节能约1/2、2/3或3/4。
同时也减少了设备投资费用。
分段送排风的原理及结构是:将喷漆室顶部的均压仓分为互相密封隔开的几段,同时将地平隔栅以下的漆雾净化室也分成相应互相隔开的几段。
分段送排风有两种设计方案:1.整个喷漆室设置一套送排风系统,通风量按一区段所需送排风量确定,喷漆区间的转换靠送排风管路上的电动多叶密闭阀自动开启与关闭实现。
该方案既节能又减少投资、费用。
2.喷漆室分几段送排风就设置几套相同的送排风单元,每单元承担一段的送排风,该方案工程量及投资费用大;但结构简单,操作维修简易。
当生产繁忙时,可同时多段送排风,用多人同时喷漆以提高产量。
二、分段送排风喷漆室有干式湿式两种类型,其室体尺寸及送排风计算是相1.喷漆室[喷烤漆房]室体尺寸确定:已知条件:车辆外形尺寸:长×宽×高=l×b×h喷漆室内部长度:L=l+2l1(1)喷漆室内部宽度:B=b+2b1(2)喷漆室内部高度:H=h+h1(3)门洞宽度:b3=b+2b2(4)门洞高度:h2=h+h3(5)喷漆室外形全高:H1=H+h5(6)以上诸式中:l=车辆长度[m]b=车辆宽度[m]h=车辆高度[m]l1=车辆端面至室体端墙内面距离[m]无三维工作台时,取l1=1.5m有三维工作台时,取l1=2~2.2mb1=车辆侧边至室体侧墙内面距离 [m]无三维工作台时,取1.5m有三维工作台时,取1.5~2m,根据三维工作台尺寸定。
烤漆房方案
烤漆房方案内部编号:(YUUT-TBBY-MMUT-URRUY-UOOY-DBUYI-0128)一、概述a)设计依据:该设备项目主要用于车辆外表面的喷涂,生产连续性强,产品质量要求较高。
b)设计思想:1、喷漆房在喷漆时提供良好的涂覆环境,同时捕捉处理漆雾、废气,整个设备严格按照国家有关劳动安全、卫生及环境等方面的标准进行设计实施。
2、设备运行可靠,操作简单,维修方便。
3、所有配套件、材料及电器元件均选择技术先进、质量优良的产品,其中关键设备和材料、顶部过滤棉选择进口件,以保证设备的整体性能和质量。
4、同时充分考虑设备运行的安全性,在温度控制等方面采用可靠的控制方式,以保证设备的整体性能和质量。
5、设备构成内容设备具有喷漆、流平和烘干功能。
喷漆时具有通风、空气净化、漆雾处理及冬季送热风功能。
喷漆工作完成后,设备转入烤漆状态,烤漆前期可以为工件提供适宜的流平温度和流平所需的风速,这有利于提高油漆涂层的质量,防止出现可燃气体浓度过高引起爆炸的危险。
烤漆状态下具有升温、保温、定时功能。
二、喷烤漆房组成及性能主要技术参数1、喷烤漆房尺寸:长×宽×高 20米××3米.(高温房宽另加一米高度2.5米)(另外再加长6米宽4米高2.5米的70度的烤漆房)烤漆房使用液化气升温2、喷漆时平均风速 m/s: ≥(满载)3、光照度 Lux:≥7004、空气过滤效率:>98%5、噪音:≤85dB6、总功率kw:≤78千瓦喷漆房的组成与功能设备具有喷漆、流平功能。
喷漆时具有通风、空气净化、漆雾处理及冬季送热风功能。
设备由室体、供风系统、排风及漆雾处理系统、空气净化系统、压力测试系统及电控系统组成。
室体是由漆室主体、大门、钢骨架、照明装置、地板格栅等部分组成的封闭空间,形成涂装作业有限场所。
供风系统由送风系统和热风循环系统组成。
供风系统的功能是满足室内风速要求,保证喷漆过喷漆雾被良好捕捉,并使工人操作环境达到劳动保护要求。
方案设计——喷漆烘干房
实用标准中国兵器工业喷漆烘干室设计方案市中宝机械制造二0一0年8月28日目录1.设计主要参数2.设计标准3.设计目标4.设计原则5.设计要求6.设备主要性能7.设备主要技术参数8.喷漆、烘漆工作原理9.设备结构简介10.产品制造、安装、调试11.工程进度12.设备验收13.培训14.售后服务15.动力能源表16.主要外购件配套单位17.易损件及备品备件一览表18.附图:1).喷漆烘干室(总图)设计方案1、设计主要参数根据需方提出的有关技术规格和要求确定。
1.1最大工件外形尺寸(L×W×H):10000×4500×5000(mm)1.2最大工件重量:20T1.3喷烘要求:喷漆烘干两用、冬季升温喷漆,雨季升温除湿喷漆。
1.4加热方式:超导电加热1.5烘干温度:60℃(可调)1.6烘干时间:0—120min(可任意设定)1.7喷烘室的温度误差:≤±5℃1.8烘干时室体表面温度:周围环境温度+5℃1.9空气净化率:≥98%1.10漆雾处理方式:采用干式过滤的方式来捕捉废漆雾。
1.11漆雾净化率:≥96%1.12噪音:≤80db(A)1.13光照度:≥500LX1.14室有载风速:0.3~0.5m/s1.15送排风方式:上送下排1.16工件输送方式:卷线式电动平车1.17室压力:室呈微负压50~100Pa1.18喷漆室门结构形式:电动大门。
1.19三维工作台:左、右侧各1台(设置空气辅助无气喷涂系统)1.20送风洁净度:室气体中5μm以上的尘埃100%过滤1.21控制方式:自动、手动两种控制。
具有多种保护、报警功能。
2、设计标准2.1 GB6514-2008《涂装作业安全规程涂漆工艺安全及其通风净化》2.2 GB7691-2003《涂装作业安全规程安全管理通则》2.3 GB14444-2006《涂装作业安全规程喷漆室安全技术规定》2.4 GB14443-2007《涂装作业安全规程涂层烘干室安全技术规定》2.5 GB20101-2006《涂装作业安全规程有机废气净化装置安全技术规定》2.6 GB12348-1990《工业企业厂界噪声标准》2.7 GB16297-1996《大气污染物综合排放标准》2.8 GBJ87-1985《工业企业噪声控制设计规》2.9 GB50058-1992《爆炸和火灾危险场所电力装置设计规》2.10 GBZI-2002《工业企业设计卫生标准》2.11 GB50034-1992《工业企业照明设计标准》2.12 JT/T324-1997《汽车喷烤漆房通用技术条件》2.13 GBZ2-2002《工作场所有害因素职业接触限值》2.14 SDJ8-1979《电力设备接地设计技术规程》2.15 GB3096-1993 《城市区域环境噪声标准》2.16 GB4053-1983 《登高梯台栏杆安全标准》2.17 GB50016-2006 《建筑设计防火规》2.18 GB50140 《建筑灭火器配置设计规》3、设计目标本公司一直致力于涂装设备的研究和生产。
设计方案——喷漆烘干房
中国兵器工业喷漆烘干室设计方案盐城市中宝机械制造有限公司二0一0年8月28日目录1.设计主要参数2.设计标准3.设计目标4.设计原则5.设计要求6.设备主要性能7.设备主要技术参数8.喷漆、烘漆工作原理9.设备结构简介10.产品制造、安装、调试11.工程进度12.设备验收13.培训14.售后服务15.动力能源表16.主要外购件配套单位17.易损件及备品备件一览表18.附图:1).喷漆烘干室(总图)设计方案1、设计主要参数根据需方提出的有关技术规格和要求确定。
1.1最大工件外形尺寸(L×W×H):10000×4500×5000(mm)1.2最大工件重量: 20T1.3喷烘要求:喷漆烘干两用、冬季升温喷漆,雨季升温除湿喷漆。
1.4加热方式:超导电加热1.5烘干温度: 60℃(可调)1.6烘干时间: 0—120min(可任意设定)1.7喷烘室内的温度误差:≤±5℃1.8烘干时室体表面温度:周围环境温度+5℃1.9空气净化率:≥98%1.10漆雾处理方式:采用干式过滤的方式来捕捉废漆雾。
1.11漆雾净化率:≥96%1.12噪音:≤80db(A)1.13光照度:≥500LX1.14室内有载风速: 0.3~0.5m/s1.15送排风方式:上送下排1.16工件输送方式:卷线式电动平车1.17室内压力:室内呈微负压50~100Pa1.18喷漆室门结构形式:电动大门。
1.19三维工作台:左、右侧各1台(设置空气辅助无气喷涂系统)1.20送风洁净度:室内气体中5μm以上的尘埃100%过滤1.21控制方式:自动、手动两种控制。
具有多种保护、报警功能。
2、设计标准2.1 GB6514-2008《涂装作业安全规程涂漆工艺安全及其通风净化》2.2 GB7691-2003《涂装作业安全规程安全管理通则》2.3 GB14444-2006《涂装作业安全规程喷漆室安全技术规定》2.4 GB14443-2007《涂装作业安全规程涂层烘干室安全技术规定》2.5 GB20101-2006《涂装作业安全规程有机废气净化装置安全技术规定》2.6 GB12348-1990《工业企业厂界噪声标准》2.7 GB16297-1996《大气污染物综合排放标准》2.8 GBJ87-1985《工业企业噪声控制设计规范》2.9 GB50058-1992《爆炸和火灾危险场所电力装置设计规范》2.10 GBZI-2002《工业企业设计卫生标准》2.11 GB50034-1992《工业企业照明设计标准》2.12 JT/T324-1997《汽车喷烤漆房通用技术条件》2.13 GBZ2-2002《工作场所有害因素职业接触限值》2.14 SDJ8-1979《电力设备接地设计技术规程》2.15 GB3096-1993 《城市区域环境噪声标准》2.16 GB4053-1983 《登高梯台栏杆安全标准》2.17 GB50016-2006 《建筑设计防火规范》2.18 GB50140 《建筑灭火器配置设计规范》3、设计目标本公司一直致力于涂装设备的研究和生产。
烤漆房配置(6.95米)
参数型号外形尺寸(m)房内尺寸(m)进车门宽(m)进车门高(m)风量(m3/h)房内有载风速(m/s)ZS09-16.95×3.95(5.2)×3.26.9×3.85×2.6 2.7 2.5230000.25-0.35配置1:部件名称标准配置一、房体墙板彩板保温材料,总厚度δ=50mm,保温材料:聚苯乙烯地台钢结构地台,3条纽纹承重地格栅,2条防滑板上车板2件,地栅式,宽度 0.6m×1.7 m安全门(工作门)1扇,带观察窗,带压力锁大门3扇,大门,带观察窗二、热风发生器框架钢板成型送风机国标1台7.5KW专业烤房风机,电机外置式防火型排风机无进风管无,从风门机柜顶直接进风排风管2米直管,1条90度弯头排烟管1米直管,1个盖帽喷烤漆风门转换器手动燃烧机RIELLO/G10,最大发热量16万大卡热交换器耐热不锈钢,循环加热,废烟气从发生器前端排出三、过滤系统顶棉TWB2-600G过滤棉,托网式安装,棉架为型材焊接,表面烤漆处理底棉平铺安装,三行地格栅封闭式风口棉2组,M型结构过滤四、照明系统上排灯8组,每组4支×36W,佛山T8型下排灯无五、电器控制系统电控箱主要为进口元器件,过载、过热、缺相、保护。
压差计1只,指针式恒温喷漆具有恒温喷漆功能总功率9KW注:选配部件在订购时要特别注明进风管道和排风管道长度,费用另算。
以上配置,加热可选用电远红外线加热,功率:22KW配置2:部件名称标准配置一、房体墙板彩板保温材料,总厚度δ=75mm,保温材料:聚苯乙烯地台钢结构地台,3条纽纹承重地格栅,2条防滑板上车板2件,地栅式,宽度 0.6m×1.7 m安全门(工作1扇,带观察窗,带压力锁门)大门3扇,大门,带观察窗二、热风发生器框架钢板成型送风机国标1台7.5KW专业烤房风机,电机外置式防火型排风机无进风管无,从风门机柜顶直接进风排风管2米直管,1条90度弯头排烟管1米直管,1个盖帽自动转换风门喷烤漆风门转换器燃烧机RIELLO/G20,最大发热量20万大卡热交换器耐热不锈钢,循环加热,废烟气从发生器前端排出三、过滤系统顶棉TWB2-600G过滤棉,托网式安装,棉架为型材焊接,表面烤漆处理底棉平铺安装,三行地格栅封闭式风口棉2组,M型结构过滤四、照明系统上排灯8组,每组4支×36W,佛山T8型下排灯8组,每组2支×20W,竖式安装五、电器控制系统电控箱主要为进口元器件,过载、过热、缺相、保护。