PFMEA实例
防松螺栓PFMEA分析实例

德信诚培训网
更多免费资料下载请进: 好好学习社区
潜在失效模式及后果分析
FMEA 编号: 防松螺栓04 (过程FMEA ) 编号:PFMEA-31 项目名称: 过程责任部门: 金工车间 编制者:
车型年/车辆类型: CA-153系列 关键过程: 01。
07。
15 FMEA 日期(编制) 0 1.06.24 .(修订) 主要参加人: 过程功能要 求 潜在的失效模式 潜在的 失效后果 严重度数 级别 潜在的失效原因/机理 频
度
数 现行过程控制
不易探测度数 风险顺序数RPN 建议的 措施 责任及目标完成日期
措施结果
采取的 措施
严重
度数
频度数 不易
探测
度数 风险 顺序数
RPN 滚丝过程
螺纹能通止
滚丝粗糙度达到要求
保证螺纹精度
螺纹不能通过
螺纹通不过,影响顾客装配
4
压力过小
4
首件检验 巡回检验, 4次/班 4只/次 3
48
无
螺纹止不住
螺纹止不住,抗拉强度达不到要求
10 压力过大 4 首件检验 巡回检验, 4次/班 4只/次 3 120
增加压力参数监视
金工车间 01.07.15 每班4次监视压力参数 10 2 3 60
螺纹中径高于工艺要求 不符合工艺要求,顾客难以装配
4 ◇
滚丝轮磨损严重
2 首件检验 巡回检验, 4次/班 4只/次
3 24
压力过小
4 首件检验 巡回检验, 4次/班 4只/次
3 48。
新版PFMEA案例

新版PFMEA案例
过程失
面无锈蚀、磕碰
、划痕
清洗洁度,机体安装
后,能够降低发动
机产生异响的概率
过程失效模式及后果分析(PFMEA)
2.每季度对维护保养计划的执行情况进行检查确认。
3.每月度对清洗剂的更换频次进行检查确认。
量异常;
对最终用户影响:无
点;
料:清洗剂不能满足除污、防锈要求,清洗剂过期,未得到监控法:超声波清洗机内的液体未及时更换,液体变质:
进行维护保养;3.确定清洗剂液体更换周期,并明确在作业标准中。
对机体表面100%检查针对失效起因:
1.每半年对人员的能力评影响交付或交付后顾客投诉;
对主机厂影响:表面存在锈斑、有磕碰点和划痕人员取放工件
时与传输带表面碰撞;
机:传输带长时间训,提高质量意识。
2.制定维护保养
措施。
六步法pfmea案例

六步法pfmea案例全文共四篇示例,供读者参考第一篇示例:案例背景:某家汽车零部件制造公司在生产过程中发现了一个频繁出现的问题:某零部件的尺寸偏差过大,导致装配时无法完全契合,进而影响产品的性能和质量。
为了解决这一问题,公司决定使用六步法PFMEA 进行分析和改进。
步骤一:确定分析范围团队确定了分析的范围为某零部件的生产工艺。
他们明确了问题的具体表现,以及对产品性能和质量的影响。
团队还确定了分析的目的是为了找出可能引起零部件尺寸偏差的潜在故障模式,并制定相应的控制措施。
步骤二:收集相关信息团队开始收集相关信息,包括零部件的设计图纸、生产工艺流程、设备参数、材料性质等。
他们还对生产现场进行实地考察,观察生产过程中的关键环节,并与相关工程师和操作人员进行沟通交流,了解他们对问题的认识和看法。
步骤三:识别潜在故障模式通过分析收集到的信息,团队识别出了可能导致零部件尺寸偏差的潜在故障模式。
包括:材料供应质量不稳定、设备操作不规范、工艺参数设置不当等。
每个故障模式都被赋予一个风险等级,以确定其重要性和优先级。
步骤四:确定故障影响团队分析每个故障模式的影响范围,包括对产品性能、质量、交付时间等方面的影响。
他们还评估了每个故障模式的可能性和频率,以确定其潜在风险。
步骤五:制定改进控制措施基于对故障模式和影响的分析,团队制定了一系列改进控制措施,以降低潜在风险。
加强材料供应商管理、优化生产工艺流程、规范设备操作规程等。
每个控制措施都被赋予一个责任人和执行时间表,以确保实施和落实。
步骤六:跟踪和持续改进团队制定了一个跟踪和持续改进计划,以监控改进控制措施的执行情况和效果。
他们定期对实施情况进行评估和审查,继续识别和解决可能存在的风险和问题,确保质量和性能的持续提升。
通过六步法PFMEA的分析和改进,该汽车零部件制造公司成功解决了零部件尺寸偏差的问题,提高了产品的质量和性能,降低了生产过程中的风险和损失,进一步提升了企业的竞争力和市场地位。
PFMEA审核思路及其相关例子
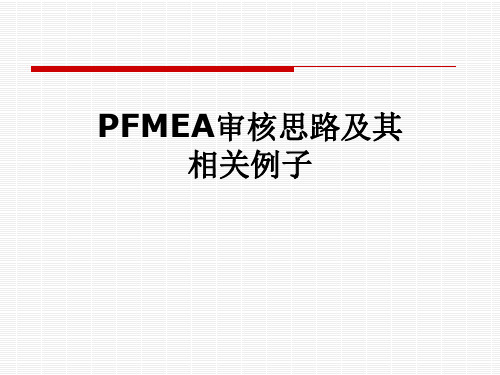
高
控制有较多机会
可探测出
很高 很高
控制几乎肯定能 探测出 肯定能探测出
检查类别
A
BC
X
X
X
X
XXபைடு நூலகம்
X
XX
XX
XX X
探测方法的推荐范围
探测度
不能探测或没有检查
10
只能通过间接或随机检查来实现控制
9
只通过目测检查来实现控制
8
只通过双重目测检查来实现目测
7
用制图的方法,如SPC(统计过程控制 6 )来实现控制
检查2次 • S=7(产品可能不得不被分选) • O=8(2%概率,每年4×1000个产品可能因铣刀断而存在
未加工的问题) • D=8(对无孔缺陷用目测探测) • RPN=392
PFMEA例子
• 产品:门铰链总成 • 产量:200,00件/年 • 工序:铣沉孔(工序库存2000件)---安装门警示开关 • 失效模式:未加工 • 失效原因:铣刀断---4次/年 • 过程控制方法:更换铣刀---1次/1000件,在加工后形成标
件 • S=7(产品可能不得不被分选) • O=2(0.1%概率,每年4×1000个产品可能因工序上马上
装配而发现问题,即铣一个装一个) • D=2(后工序防错) • RPN=28
总结
• 1.任何措施都不能改变严重度,除非变化设计 • 2只有防错才能大幅度降低RPN • 3目视检查是不可靠的 • 4对后道工序的措施并不能降低前道工序RPN值
件 • S= • O= • D= • RPN=
PFMEA例子
• 产品:门铰链总成 • 产量:200,00件/年 • 工序:铣沉孔(工序库存2000件)---安装门警示开关 • 失效模式:未加工 • 失效原因:铣刀断---4次/年 • 过程控制方法:更换铣刀---1次/1000件,通止规---1次/100
PFMEA第五版实例

Item (Part #):Process Responsi bilityModelYear(s)/Program(s)Core Team:FAMILY OF PARTS: P1市场部/开发部/制造部/采购部/物流部/质保部POTENTIALFAILURE MODE AND EFFECTS ANALYSIS(PROCESS FMEA)APQP TEAM外购件领取(1);buyer:无影响(1)位料(2);存储在不开箱数量差异(6);buyer:无影响(1)视检查不足(3);操作员和不对成品产生损伤对成品产生损伤supplier:部分(小于100%)外购件需要报废(6);Coustomer:不合格产品流入客户(6);buyer:无影响(1)6检验员技能不合格4技能评定/培训培训记录/技能矩阵更新61442装车方法正确装车方法不正确supplier:产品变形或损坏(6);Coustomer:不合格产品流入客户(6);buyer:无影响(1)6仓管员技能不合格4技能评定/培训培训记录/技能矩阵更新71682产品防护正确产品防护不正确supplier:产品变形或损坏(6);Coustomer:不合格产品流入客户(6);buyer:无影响(1)6仓管员技能不合格4技能评定/培训培训记录/技能矩阵更新71682出货检验240发运Preparedby:FMEADate (Orig.)FMEADate (Rev.)。
PFMEA的例子
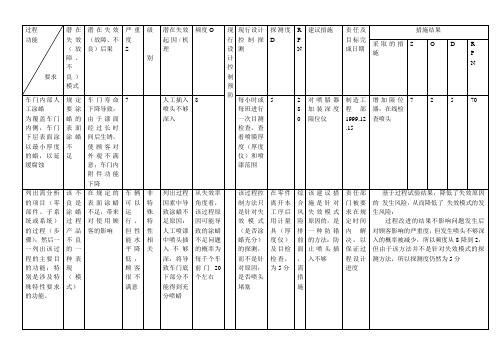
在规定的表面涂蜡不足,带来对使用顾客的影响
车辆可以运行,但性能水平降低,顾客很不满意
非特殊特性相关
列出过程因素中导致涂蜡不足原因:人工喷漆中喷头插入不够深,将导致车门底下部分不能得到充分喷蜡
从失效率角度看,该过程原因可能导致的涂蜡不足问题的概率为每千个车前门20个左右
RPN
建议措施
责任及目标完成日期
措施结果
采取的措施
S
O
D
R
P
N
车门内部人工涂蜡
为覆盖车门内侧,车门下层表面涂以最小厚度的蜡,以延缓腐蚀
规定要涂蜡的表面涂蜡不足
车门寿命下降导致:由于漆面经过长时间后生锈,使顾客对外观不满意;车门内附件功能下降
7
人工插入喷头不够深入
8
每小时或每班进行一次目测检查,查看厚度(厚度仪)和喷漆范围
7
人工插入喷头不够深入
8
每小时或每班进行一次目测检查,查看喷膜厚度(厚度仪)和喷漆范围
5
280
对喷腊器加装深度限位仪
制造工程部1999.12.15
增加限位器,在线检查喷头
7
2
5
70
列出需分析的项目(零部件、子系统或系统)的过程(步骤);然后一一列出该过程的主要目的功能;特别是涉及特殊特性要求的功能。
过程改进的结果不影响问题发生后对顾客影响的严重度,但发生喷头堵塞的概率被减少,所有频度从5降到1(完全不会发生),但由于该方法并不是针对失效模式的探测方法,所有探测度仍然为5分。
ቤተ መጻሕፍቲ ባይዱ过程
功能
要求
潜在失效(故障、不良)模式
潜在失效(故障、不良)后果
严重度
PFMEA分析范例
PFMEA分析范例PFMEA(Process Failure Mode and Effects Analysis)是产品设计和生产过程中一种常用的质量管理工具,它能够帮助企业分析和识别潜在的故障模式、评估其影响程度,并制定相应的纠正和预防措施。
本文将通过一个实际案例来展示PFMEA分析的具体过程和应用方法。
案例背景某电子制造企业生产线上的一个环节涉及到电池组装,为了保障产品质量,他们希望通过PFMEA分析来识别潜在的故障模式,并采取相应措施进行预防和纠正,以降低质量风险。
1. 确定流程步骤首先,我们需要确定电池组装过程中的流程步骤,如准备工作、电池组装、焊接、包装等。
2. 识别潜在故障模式在每个流程步骤中,我们需要识别可能出现的潜在故障模式,例如:在准备工作阶段,可能出现的故障模式包括工具缺失、物料不合格等等。
3. 评估故障影响程度针对每个潜在故障模式,我们需要评估其对产品质量和生产效率的影响程度。
例如,在电池组装阶段,如果出现电池不合格,可能导致产品连接不可靠,影响产品性能,同时还会增加后续检测和返工的工作量。
4. 确定风险等级结合故障模式的影响程度,我们可以根据一定的评估标准来确定每个故障模式的风险等级。
例如,可以设定高、中、低三个等级,将电池不合格列为高风险等级。
5. 制定预防和纠正措施对于高风险等级的故障模式,我们需要制定相应的预防和纠正措施,以降低潜在风险。
例如,对于电池不合格的风险,可以建立严格的供应商管理制度,提高物料检测的精度和效率。
6. 实施和跟踪制定好预防和纠正措施后,我们需要将其纳入到生产实践中,并建立相应的跟踪机制,及时评估其实施效果,并根据需要对措施进行调整和改进。
通过以上几个步骤的分析和实施,电子制造企业可以在电池组装过程中减少故障发生的概率,并及时采取纠正措施,以确保产品质量和生产效率的稳定性和可持续性。
总结PFMEA作为一种常用的质量管理工具,可以帮助企业在产品设计和生产过程中识别潜在故障模式,并制定相应的预防和纠正措施。
扬声器PFMEA案例
有警告的危害
当潜在的失效模式在有警告的情况下影响车辆安全运行和/或涉及不符合政府法规的情形时,严重度定级非常高
或可能在有警告的情况下对(机器或总成)操作者造成危害
9
很高
车辆/项目不能工作(丧失基本功能)
或100%的产品可能需要报废,或者车辆/项目需在返修部门返修1个小时以上
8
高
车辆/项目可运行但性能水平下降。
案例:
某音响制造公司为某汽车制造商设计制造一车用扬声器。以下是汽车制造商提出的(部分)要求:
安装尺寸▼:外形图标注,为4’扬声器。
可靠性要求:3年无故障▼。
阻抗:8.0±0.8 OHM at 400Hz
特性灵敏度级:88±2dB
f0:120±15Hz
额定功率:8W
长期最大功率:20W
注:其中带▼为特殊特性。
扬声器主要技术参数:
…………
内部要求:
易于装配,一次装配合格率(直通率)大于99%。
案例:为了保证产品设计意图完整地贯彻到生产过程中,公司组建了PFMEA小组。小组组长由工艺工程师王五担任,小组成员有品质工程师赵六,SQE钱七,以及计划将来进行该产品生产的生产车间主任贾师傅。
PFMEA小组首先利用特性矩阵,将产品关键特性对应到生产过程的中,在此基础上,PFMEA小组开发了PFMEA
2006-10-30:SQE小组,确定批准要求并完成供应商手册。2008-10-01,供应商满足手册要求
尤全
10-30前投入使用
5
2
2
20
过程FMEA的标准表
系统潜在失效模式及后果FMEA编号
子系统(PFMEA)共页,第页
部件设计责任编制人
车型年/车辆类型关键日期FEMA日期(编制)(修订)
PFMEA第五版实例全篇
PFMEA第五版实例Item (Part #):Process Responsi bilityModelYear(s)/Program(s)Core Team:FAMILY OF PARTS: P1市场部/开发部/制造部/采购部/物流部/质保部POTENTIALFAILURE MODE AND EFFECTS ANALYSIS (PROCESS FMEA)APQP TEAM外购件领取(1);buyer:⽆影响(1)位料(2);存储在不开箱数量差异(6);buyer:⽆影响(1)视检查不⾜(3);操作员和不对成品产⽣损伤对成品产⽣损伤supplier:部分(⼩于100%)外购件需要报废(6);Coustomer:不合格产品流⼊客户(6);buyer:⽆影响(1)6检验员技能不合格4技能评定/培训培训记录/技能矩阵更新61442装车⽅法正确装车⽅法不正确supplier:产品变形或损坏(6);Coustomer:不合格产品流⼊客户(6);buyer:⽆影响(1)6仓管员技能不合格4技能评定/培训培训记录/技能矩阵更新71682产品防护正确产品防护不正确supplier:产品变形或损坏(6);Coustomer:不合格产品流⼊客户(6);buyer:⽆影响(1)6仓管员技能不合格4技能评定/培训培训记录/技能矩阵更新71682出货检验240发运Preparedby:FMEADate (Orig.)FMEADate (Rev.)。
2019第五版新版pfmea注塑实例
(规划和准备(步骤一)PLANINGandPREPARATION(STEP1) FMEA 电子表格 THE FMEA SPREADSHEET过程失效模式及后果分析(PFMEA)公司名称: Company Name: XXX 塑胶模具有限公司项目: Subject:XXXPFMEA 编码: PFMEA ID Number 根据各公司体系填写工厂地址: E n g i n e e r i n g L o c a t i o n :顾客名称: Customer Name: 年款(车型)/平台 Model Year/Plantform:温州市XXXX PFMEA 开始时间: PFMEA start Date:XXX 汽车电子PFMEA 修订时间: PFMEARevisionDate: XX X 专用车 跨职能团队: C r o s s F u n c t i o nT e a m :2019.10.14设计责任 张三D e s i g n R e s p o n s i b i t y : 保密等级: 公开S e c u r i t y C l a s s i f i c a t i o n :张三,李四,王五持续改进 CONTINUOUS IMPROVEMENT结构分析(步骤二)STRUCTURE ANALYSIS功能分析(步骤三)FUNCTION ANALYSIS失效分析(步骤四)FAILURE ANALYSIS风险分析(步骤五)RISK ANALYSIS优化(步骤六)OPTIMIZATION结果文件化 (步骤七)问 历史/变更授权(适 2.1. 过程项 系统、子系统 2.2. 过程步骤2.3. 过程工作要 3.1. 过程功能 3.2. 过程步骤的功 3.3. 过程工作要系统、子系统、 5.2 当前的失效 失效起 4.1 对于上一较高级 失效影响 4.2 关注要素的失 4.3 工作要素的 5.1 当前的对失 失效起因/失 起因/失效模式 因/失效 5.3PFM筛选器 5.4 特殊 代码 6.1 预防 6.2 探测 6.3 责任 6.4 目标 6.6 采取 6.7 实际 严重度 频度 探测度6.8特殊6.9PFME 筛选器代7.1 改进措施题 用时)这一类是可选 、零件要素或 工位编号和 素 4M 零件要素或过程 能和产品特性 素的功能和过程 别要素和/或最终用 的严重度 效模式(FM ) 失效原因 效起因的预防 效模式 的频 的探测措施 模式的 EA 措施 特 性 ( 可 措 施 措施 人 姓名 完成日期 6.5 状态 基于证据完成日期 (S ) (O ) ( D ) A 措施 优 码(可特性 效果文件化 号 栏目 过程名称 关注要素名 称 的功能 (量值为可选项) 特性 户的影响(FE ) (S ) (FC ) 措施(PC ) 度(O ) (DC ) 探测度 优先级 选)(D )的措施 先级 选)(备注)O-1.领料确保领取物料准确保面板产品满足 领料材料满足要求产品不能生产,需要3 领错塑料米仓库发错材料仓库定点定位3领料时核实材 4L确无误客户要求 重新领料,耽误生产存放料型号、品牌烘烤时间和烘烤确保注塑产品无料烘烤温度110±5 产品不能使用,需要确保注塑产品有 烘烤时间和烘烤 设备上设置输设备上显示输O -2.烤料温度花,缺料等注塑缺℃烘烤时间4h 陷重新生产,延误交货 5料花,缺料等注塑缺陷 温度不足入,定期对设备进行点检3出5LO-3.注塑工射胶温度,射胶1、射胶温度290确保注塑产品无料 ±5。
- 1、下载文档前请自行甄别文档内容的完整性,平台不提供额外的编辑、内容补充、找答案等附加服务。
- 2、"仅部分预览"的文档,不可在线预览部分如存在完整性等问题,可反馈申请退款(可完整预览的文档不适用该条件!)。
- 3、如文档侵犯您的权益,请联系客服反馈,我们会尽快为您处理(人工客服工作时间:9:00-18:30)。
编制 Prepared by:
关键日期 Key Date :
o p e r . S q e .操作顺序
项目及功能 Items and function 潜在缺陷和失
效模式
Potential
Failure Mode
潜在缺陷和失效后果
Potential Effect(s) of
Failure
严重度 Sev 特性等级
C l a s s 潜在缺陷和失效发生原因 Potential Cause(s)/Mechanism(s) of Failure
发生率
O c c u r 现有过程预防措施 Current Process Preventive Method
现有过程检测措施 Current Process Control Method
探
测
度
D
e
t e c 风险评价
RPN
改进措施 Recommend Action(s)责任人员及完成日期 Responsibility & Target Completion Date 改进后的状况 Action Results
采取的措施 Actions Taken 严重度
S e v 发生率O c c u r 错漏率D e t e
c
风险评价RPN 10
进货 检验
物性指标 不合格 影响产品性能7
供应商没有严 格按照顾客要 求加工制造 2
供应商 提供报告 工厂 自检570
物料尺寸 不合格
影响产品尺寸
7 供应商没有严 格按照顾客要 求加工制造 2 供应商 提供报告 工厂 自检570
15 贮存 材料相混 领料时错领 6 无物料标识
2 做标识
定置 管理
5 60
20
折纸
滤纸折数 不对
影响滤芯 分总成的尺寸 影响滤清器的 滤清效率
7 员工数折数错误2
使用
计数器自动打点
填写自 检记录 4 56
滤纸破损
影响滤清器 的滤清效率
7
烤板温度偏低 鼓泡扎辊和折 痕扎辊配合间 隙小
滚筒上有异物2
编制作业 指导书
填写日 点检记 录表 填写自 检记录 5 70
滤纸宽度超
差影响产品尺寸
7 滤纸涨幅不确定性滤纸分切错误2
由技术部编制滤纸分切作业指导书
自检
5 70
滤芯 不密封
影响滤清器的滤 清效率,易导致发 动机吸入不干净 的气体
7 热熔胶 胶头堵塞 热熔胶温度低2
编制作业 指导书 填写自 检记录 5 70
折纸返工 R
滤纸表面脏污 影响滤清器
的滤清效率7 手工挤压手套脏污,返工工作台表面有灰尘不干净2返工作业指导书完善手工挤压操作规
范 填写返工自 检记录 5 70滤纸表面破损 影响滤清器 的滤清效率7 员工操作失误2作业人员岗前培训
目视检查 6 8425
打筋
胶丝多
胶丝多顾客不满意
4
设备设置温度偏低热熔胶粘度大4
编制作业 指导书工人外观全检
5
80
热熔胶断裂影响滤芯外观
4 材质物理指标不合格
2
供应商
提供报告/ 更新优化作业指导书
外观全检
工厂原材料
报告
6 48
1/3
编制 Prepared by:关键日期 Key Date:
o
p
e
r
.
S
q
e
.
操
作
顺
序
项目及功能
Items and
function
潜在缺陷和失
效模式
Potential
Failure Mode
潜在缺陷和失效后果
Potential Effect(s) of
Failure
严
重
度
Sev
特
性
等
级
C
l
a
s
s
潜在缺陷和失效发生原
因 Potential
Cause(s)/Mechanism(s)
of Failure
发
生
率
O
c
c
u
r
现有过程预防措施
Current Process
Preventive Method
现有过程检测措
施
Current Process
Control Method
探
测
度
D
e
t
e
c
风险评价
RPN
改进措施
Recommend
Action(s)
责任人员及完成
日期
Responsibility &
Target
Completion Date
改进后的状况 Action Results
采取的措施
Actions
Taken
严
重
度
S
e
v
发
生
率
O
c
c
u
r
错
漏
率
D
e
t
e
c
风险
评价
RPN 35去飞边
飞边没有
去除干净
影响外观4
工人粗心
剪刀磨损
2
外观全检
定期磨剪刀
填写过程检验
记录表
7 56`
40检验
外观全检未
检查出不合
格品
客户不满意5目视检查遗漏3作业人员岗前培训目视检查 5 75
45喷码
内容或
样式不正确
影响产品确认
顾客不满意
6
电脑程序
调用不正确
2
按作业指导书调节
设备参数
填写自
检记录
5 60
50包装
漏贴标签
缺数量
顾客不满意4工人粗心2使用标准箱
填写自
检记录
7 56
55终检
不合格产品
错判为合格
品
影响客户装配及使用7
检验员错检漏检
或量具失效
2
检验员
定期培训
定期
校验量具
定期考核
检验员
5 70
60入库标识不符顾客不满意4错、漏贴标签2出货检验
填写
出货检验记录
表
756
65出货检不良品未检出客户不满意4
检验员未按设定的抽样
标准实施抽样;抽样标
准不合理
3
量产初期加严抽样;
品质稳定后恢复正常
水平
按检验标准检验672
“▲”表示过程特性; “△”表示材质、功能性能及装配特性(show material, function capability and assembly speciality)。
3/3。