降低烧结工序能耗的实践
莱钢降低265m 2烧结机工序能耗的实践

烧结 工 序 能 耗 ¨ 是 指 生 产 一 吨烧 结 矿 生 产 和
固体 燃耗 约 占烧 结 总 能耗 的 7 % , 5 因此 , 低 降 固体 燃耗对 烧 结节 能至关 重要 。 自莱 钢股份 炼铁 厂
新 二 区 2 5 结机 投产 以来 ,烧结二 车间非 常 重 6m 烧
生 活 ( 场 内 ) 需 的全 部 煤 、 炭 、 气 、 油 及 指 耗指标 k 标煤/ g t
20 0 7年
5 .6 2 7
钢铁 股份 有 限公 司 炼 铁 厂新 二 区烧 结二 车 间 ( 下 以 简称 烧 结 二 车 间 ) 6 m 2 5 烧 结 机 于 2 0 0 5年 1 0月建
视 固体燃耗 的 问题 , 取 了 多种 措 施 ,取 得 了 一定 采 的成 效 ,使 固 体 燃 耗 指 标 呈 稳 步 下 降 趋 势 ( 表 见 2 。但 莱钢 固体 燃 耗 指 标 与 国 内 重 点 钢 铁 企 业 相 ) 比 , 有较 大差 距 。 仍
王 炜 王 珂 李连 海 熊 伟
( 芜钢 铁股 份有 限公 司 , 莱 山东 莱芜 2 10 ) 7 14
摘 要 莱 钢 股 份 炼 铁 厂 新 二 区 2 5 烧 结 机 采 取 控 制 原 燃 料 粒 度 、 定 烧 结 生 产 、 格 生 产 管 理 、 善工 艺 设 施 6m 稳 严 完
b neis we e o t i e . e ft r b a n d K e r sn e i g;p o e s e e g o s m p in;s ld f lc n u pi n;g s c n u pi n y wo ds i t rn rc s n ry c n u t o o i ue o s m t o a o s m t o
浅谈降低烧结工序能耗的措施
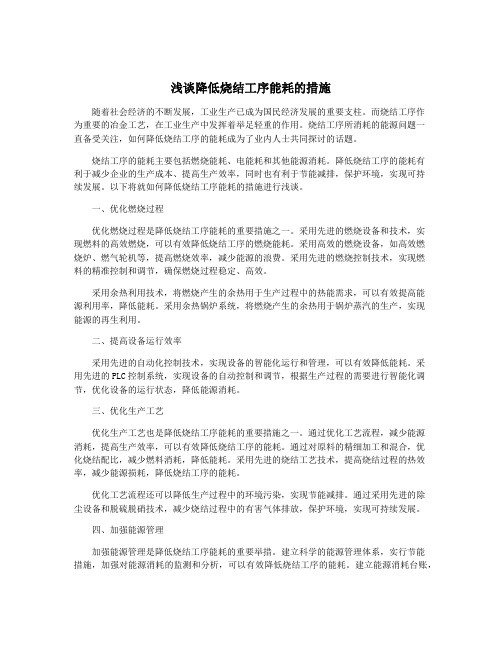
浅谈降低烧结工序能耗的措施随着社会经济的不断发展,工业生产已成为国民经济发展的重要支柱。
而烧结工序作为重要的冶金工艺,在工业生产中发挥着举足轻重的作用。
烧结工序所消耗的能源问题一直备受关注,如何降低烧结工序的能耗成为了业内人士共同探讨的话题。
烧结工序的能耗主要包括燃烧能耗、电能耗和其他能源消耗。
降低烧结工序的能耗有利于减少企业的生产成本、提高生产效率,同时也有利于节能减排,保护环境,实现可持续发展。
以下将就如何降低烧结工序能耗的措施进行浅谈。
一、优化燃烧过程优化燃烧过程是降低烧结工序能耗的重要措施之一。
采用先进的燃烧设备和技术,实现燃料的高效燃烧,可以有效降低烧结工序的燃烧能耗。
采用高效的燃烧设备,如高效燃烧炉、燃气轮机等,提高燃烧效率,减少能源的浪费。
采用先进的燃烧控制技术,实现燃料的精准控制和调节,确保燃烧过程稳定、高效。
采用余热利用技术,将燃烧产生的余热用于生产过程中的热能需求,可以有效提高能源利用率,降低能耗。
采用余热锅炉系统,将燃烧产生的余热用于锅炉蒸汽的生产,实现能源的再生利用。
二、提高设备运行效率采用先进的自动化控制技术,实现设备的智能化运行和管理,可以有效降低能耗。
采用先进的PLC控制系统,实现设备的自动控制和调节,根据生产过程的需要进行智能化调节,优化设备的运行状态,降低能源消耗。
三、优化生产工艺优化生产工艺也是降低烧结工序能耗的重要措施之一。
通过优化工艺流程,减少能源消耗,提高生产效率,可以有效降低烧结工序的能耗。
通过对原料的精细加工和混合,优化烧结配比,减少燃料消耗,降低能耗。
采用先进的烧结工艺技术,提高烧结过程的热效率,减少能源损耗,降低烧结工序的能耗。
优化工艺流程还可以降低生产过程中的环境污染,实现节能减排。
通过采用先进的除尘设备和脱硫脱硝技术,减少烧结过程中的有害气体排放,保护环境,实现可持续发展。
四、加强能源管理加强能源管理是降低烧结工序能耗的重要举措。
建立科学的能源管理体系,实行节能措施,加强对能源消耗的监测和分析,可以有效降低烧结工序的能耗。
浅谈降低烧结工序能耗的措施
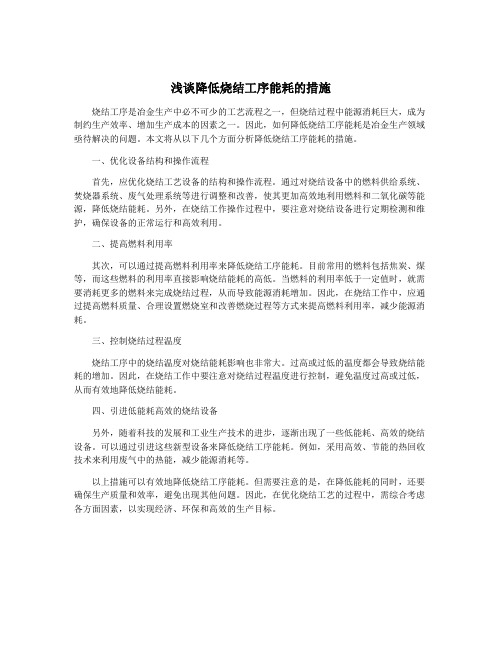
浅谈降低烧结工序能耗的措施烧结工序是冶金生产中必不可少的工艺流程之一,但烧结过程中能源消耗巨大,成为制约生产效率、增加生产成本的因素之一。
因此,如何降低烧结工序能耗是冶金生产领域亟待解决的问题。
本文将从以下几个方面分析降低烧结工序能耗的措施。
一、优化设备结构和操作流程首先,应优化烧结工艺设备的结构和操作流程。
通过对烧结设备中的燃料供给系统、焚烧器系统、废气处理系统等进行调整和改善,使其更加高效地利用燃料和二氧化碳等能源,降低烧结能耗。
另外,在烧结工作操作过程中,要注意对烧结设备进行定期检测和维护,确保设备的正常运行和高效利用。
二、提高燃料利用率其次,可以通过提高燃料利用率来降低烧结工序能耗。
目前常用的燃料包括焦炭、煤等,而这些燃料的利用率直接影响烧结能耗的高低。
当燃料的利用率低于一定值时,就需要消耗更多的燃料来完成烧结过程,从而导致能源消耗增加。
因此,在烧结工作中,应通过提高燃料质量、合理设置燃烧室和改善燃烧过程等方式来提高燃料利用率,减少能源消耗。
三、控制烧结过程温度烧结工序中的烧结温度对烧结能耗影响也非常大。
过高或过低的温度都会导致烧结能耗的增加。
因此,在烧结工作中要注意对烧结过程温度进行控制,避免温度过高或过低,从而有效地降低烧结能耗。
四、引进低能耗高效的烧结设备另外,随着科技的发展和工业生产技术的进步,逐渐出现了一些低能耗、高效的烧结设备。
可以通过引进这些新型设备来降低烧结工序能耗。
例如,采用高效、节能的热回收技术来利用废气中的热能,减少能源消耗等。
以上措施可以有效地降低烧结工序能耗。
但需要注意的是,在降低能耗的同时,还要确保生产质量和效率,避免出现其他问题。
因此,在优化烧结工艺的过程中,需综合考虑各方面因素,以实现经济、环保和高效的生产目标。
烧结节能降耗
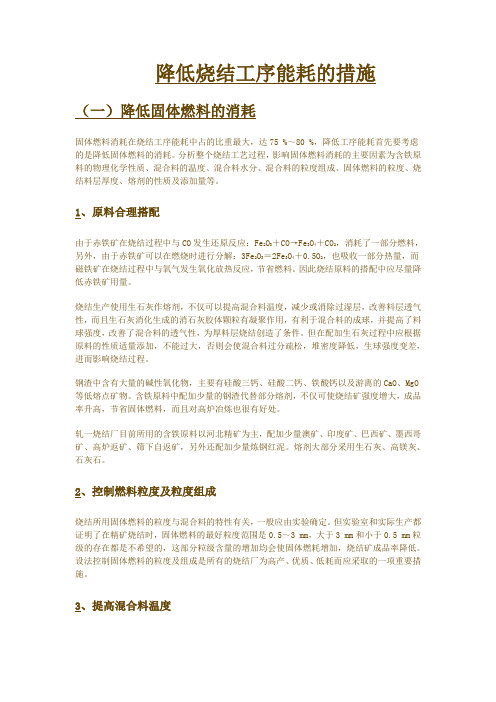
降低烧结工序能耗的措施(一)降低固体燃料的消耗固体燃料消耗在烧结工序能耗中占的比重最大,达75 %~80 %,降低工序能耗首先要考虑的是降低固体燃料的消耗。
分析整个烧结工艺过程,影响固体燃料消耗的主要因素为含铁原料的物理化学性质、混合料的温度、混合料水分、混合料的粒度组成、固体燃料的粒度、烧结料层厚度、熔剂的性质及添加量等。
1、原料合理搭配由于赤铁矿在烧结过程中与CO发生还原反应:Fe2O3+CO→Fe3O4+CO2,消耗了一部分燃料,另外,由于赤铁矿可以在燃烧时进行分解:3Fe2O3=2Fe3O4+0.5O2,也吸收一部分热量,而磁铁矿在烧结过程中与氧气发生氧化放热反应,节省燃料。
因此烧结原料的搭配中应尽量降低赤铁矿用量。
烧结生产使用生石灰作熔剂,不仅可以提高混合料温度,减少或消除过湿层,改善料层透气性,而且生石灰消化生成的消石灰胶体颗粒有凝聚作用,有利于混合料的成球,并提高了料球强度,改善了混合料的透气性,为厚料层烧结创造了条件。
但在配加生石灰过程中应根据原料的性质适量添加,不能过大,否则会使混合料过分疏松,堆密度降低,生球强度变差,进而影响烧结过程。
钢渣中含有大量的碱性氧化物,主要有硅酸三钙、硅酸二钙、铁酸钙以及游离的CaO、MgO 等低熔点矿物。
含铁原料中配加少量的钢渣代替部分熔剂,不仅可使烧结矿强度增大,成品率升高,节省固体燃料,而且对高炉冶炼也很有好处。
轧一烧结厂目前所用的含铁原料以河北精矿为主,配加少量澳矿、印度矿、巴西矿、墨西哥矿、高炉返矿、筛下自返矿,另外还配加少量炼钢红泥。
熔剂大部分采用生石灰、高镁灰、石灰石。
2、控制燃料粒度及粒度组成烧结所用固体燃料的粒度与混合料的特性有关,一般应由实验确定。
但实验室和实际生产都证明了在精矿烧结时,固体燃料的最好粒度范围是0.5~3 mm,大于3 mm和小于0.5 mm粒级的存在都是不希望的,这部分粒级含量的增加均会使固体燃耗增加,烧结矿成品率降低。
降低烧结工序能耗的措施

增加 而加强 , 当 料层高度为1 8 0 - 2 2 0 二 时, 蓄 热 量只占燃烧带热量总收入的 3 5 %- - 4 5 %, 当
料层厚 度 达到 4 0 0 m m 时, 蓄热量达 5 5 %一
b 0 % [ " 。因 此, 提 高料层厚度, 采用厚料层烧结,
充分利用烧结过程的 自 动蓄热, 可 以降低烧结料
力, 从而改善了 料层透气性, 使抽过料层的空气 量增加, 为 料层内 的热交换创 造了良 好条件, 燃 烧速度加快川, 提高了台时产量, 节约了固体
燃料。 提高混合料温度 的措施主要 有: 生石灰预 热、 热水 予热、 热返 矿预热、 蒸气预热 及烧结废 气预热等。 安钢烧结 厂 自从 1 9 8 6年研 制成 功 H A S 作
四辊上料方式, 使粘料趋 于平稳、 均 匀, 并通过
机; 将两台一次混合机由必2 . 7mx 5 m加长 到必 2 . 7 m x 7 m , 1 9 9 7 年在第二配料室由容
积配料 向微机 自动重量 配料 改造时, 又将该配
严格控制上料皮带流量, 限制最低开车台时、 加 强设备的维护和检修等措施, 使燎料粒度组成 中。 - 3 m m部分达到了8 5 % 以上, 为降低固 体 燃料消耗创造了条件。1 9 9 7 年, 固 体燃耗仅为
( k g " t 一 t )
6 9 . 9 8 6 9 . 5 5 6 7 . 6 7 6 6 . 0 4 6 7 . 2 1 6 8 . 8 9 6 5 . 9 4 6 口7 3
1 9 9 0 1 9 9 1 1 9 9 2 1 9 9 3 1 9 9 4 1 9 9 5 1 9 9 6 1 9 9 7
占7 5 %- 8 0 %左右, 电 力占 1 3 %-2 0 %, 点火
浅谈降低烧结工序能耗的措施
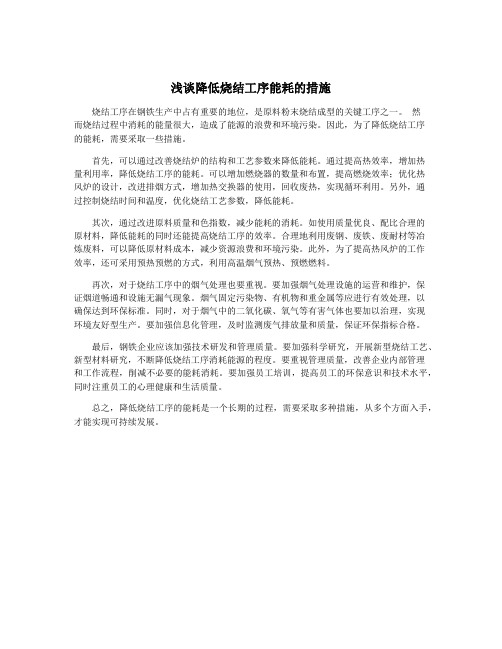
浅谈降低烧结工序能耗的措施烧结工序在钢铁生产中占有重要的地位,是原料粉末烧结成型的关键工序之一。
然而烧结过程中消耗的能量很大,造成了能源的浪费和环境污染。
因此,为了降低烧结工序的能耗,需要采取一些措施。
首先,可以通过改善烧结炉的结构和工艺参数来降低能耗。
通过提高热效率,增加热量利用率,降低烧结工序的能耗。
可以增加燃烧器的数量和布置,提高燃烧效率;优化热风炉的设计,改进排烟方式,增加热交换器的使用,回收废热,实现循环利用。
另外,通过控制烧结时间和温度,优化烧结工艺参数,降低能耗。
其次,通过改进原料质量和色指数,减少能耗的消耗。
如使用质量优良、配比合理的原材料,降低能耗的同时还能提高烧结工序的效率。
合理地利用废钢、废铁、废耐材等冶炼废料,可以降低原材料成本,减少资源浪费和环境污染。
此外,为了提高热风炉的工作效率,还可采用预热预燃的方式,利用高温烟气预热、预燃燃料。
再次,对于烧结工序中的烟气处理也要重视。
要加强烟气处理设施的运营和维护,保证烟道畅通和设施无漏气现象。
烟气固定污染物、有机物和重金属等应进行有效处理,以确保达到环保标准。
同时,对于烟气中的二氧化碳、氧气等有害气体也要加以治理,实现环境友好型生产。
要加强信息化管理,及时监测废气排放量和质量,保证环保指标合格。
最后,钢铁企业应该加强技术研发和管理质量。
要加强科学研究,开展新型烧结工艺、新型材料研究,不断降低烧结工序消耗能源的程度。
要重视管理质量,改善企业内部管理和工作流程,削减不必要的能耗消耗。
要加强员工培训,提高员工的环保意识和技术水平,同时注重员工的心理健康和生活质量。
总之,降低烧结工序的能耗是一个长期的过程,需要采取多种措施,从多个方面入手,才能实现可持续发展。
浅谈降低烧结工序能耗的措施

浅谈降低烧结工序能耗的措施1. 引言1.1 烧结工序对能源消耗的重要性烧结工序是冶金工业重要的炼铁生产工序之一,其能源消耗对整个生产过程的能耗影响极为重要。
烧结工序主要是通过将铁矿石等原料在高温下加热,使其在烧结炉中发生一系列物理化学反应,最终形成高强度的铁制品。
烧结工序的能源消耗占据了整个冶金生产的重要比重,对于企业的生产成本和环境影响都具有重要的意义。
烧结工序所需能源包括燃料能源和电力能源,其中以燃料消耗较大。
在烧结工序中,煤炭、焦炭等燃料被用来提供高温热能,使原料得以烧结。
传统的烧结工序存在能源利用率低、排放浪费等问题,导致能源消耗较高。
降低烧结工序的能源消耗具有重要意义。
通过优化烧结工艺参数、采用先进的设备和技术、加强热能回收利用、提高烧结燃料的利用率以及应用节能技术等措施,可以有效降低烧结工序的能源消耗,提高生产效率,减少生产成本,实现可持续发展。
节能减排也是当前社会发展的重要趋势,降低烧结工序的能源消耗,不仅符合环保要求,也能提升企业的竞争力。
2. 正文2.1 优化烧结工艺参数优化烧结工艺参数是降低烧结工序能耗的重要措施之一。
通过调整烧结工艺中的各项参数,可以实现更高效的烧结过程,减少能源的消耗。
优化烧结工艺参数可以提高烧结的热效率。
合理调节烧结温度、烧结时间等参数,可以使烧结过程中的热能更加充分利用,减少能源的浪费。
优化参数还可以提高烧结矿的燃烧效率,减少燃料的使用量,降低能耗。
优化烧结工艺参数还可以改善产品质量。
通过精确控制烧结过程中的各项参数,可以确保产品的成分和性能达到要求,避免因为工艺参数不合理导致的质量问题,减少了产品的废品率,提高了资源利用率。
优化烧结工艺参数还可以减少设备运行时的能耗。
通过合理设置烧结设备的工作参数,有效控制能源的消耗,延长设备的使用寿命,减少了能源的浪费,降低了生产成本。
优化烧结工艺参数是降低烧结工序能耗的有效途径之一,可以提高烧结热效率,改善产品质量,减少设备能耗,从而实现节能减排的目标。
济钢320m2烧结机节能降耗实践

Ke o d e e g o s mp o tc nc la v n e n ; q i me t df ain y W r s: n r c n u t n;e h ia d a c me t e up n y i mo i c t i o
1 引言
由于 目前我 国能源 比较 紧缺 , 价格在大幅度上
k c /t ge 。
固体燃耗
k/ gt
5.3 4 3
5.8 3 0 5.4 2 5 5.4 2 2
电耗
k / Wh t
3 8 3 .2 6 1
煤气消耗
m3t /
1 .8 68
1 7 5. 6 1 61 4. 1 1 4. 1
kg 。 /t
低, 于是我们利用带冷机 3 烟 囱的热废气来助燃点 # 火( 1 , 可以使得助燃空气的温度由以前 的 图 )这样 常温 2 5℃提高到 15℃左右 , 2 助燃空气温度 的提 高, 使得带入部分物理热而使燃烧温度得 以提高使 得煤气用量降低 , 该项技术年节省煤气价值达 28 2. 5 8万元 , 提高成品率的年效益 87 0 3 .7万元 , 由此取 得年经济效益 10 00多万元 的显著效果。
得我们将使用这些工业废弃物时对生产造成的影响
降到了最低点 , 确保了烧结矿产量和质量 , 从而使得 固体燃耗有了明显降低。
2 8 实施 热风 点火技 术 .
降低了固体燃料消耗 , 同时保证 了烧结矿产量、 质
量。
25 曲面 多辊布 料技 术 .
为了进一步增强料层透气性 , 降低固体燃耗 , 我
低工序能耗 的潜力 , 经过不懈的努力, 取得 了比较明 显 的效 果 ( I 。 表 )
- 1、下载文档前请自行甄别文档内容的完整性,平台不提供额外的编辑、内容补充、找答案等附加服务。
- 2、"仅部分预览"的文档,不可在线预览部分如存在完整性等问题,可反馈申请退款(可完整预览的文档不适用该条件!)。
- 3、如文档侵犯您的权益,请联系客服反馈,我们会尽快为您处理(人工客服工作时间:9:00-18:30)。
降低烧结工序能耗的实践张义明薛凤萍李素芹顾桂萍王娜(唐山钢铁集团有限责任公司炼铁厂,唐山 063020)摘要本文分析了唐钢炼铁厂烧结工序能耗的现状,采取了一系列降低烧结工序能耗的措施。
通过优化烧结配矿、低温厚料层烧结、配料自动化、提高混合料温度、控制燃料粒度、改善燃料分布等措施降低了固体燃耗;通过降低烧结系统漏风率、提高设备作业率、减少设备的空运转时间降低了烧结系统电耗;通过采用微负压点火技术和低温点火技术降低了点火煤气消耗;通过烧结余热的回收利用实现了循环经济,取得了较好的经济效益和社会效益。
关键词烧结工序能耗措施实践Practice of Reducing Consumption of the Sinter Procedure Zhang Yiming Xue Fengping Li Suqin Gu Guiping Wang Na(Tangshan Iron & Steel Co., Ltd., Tangshan, 063020)Abstract Through analyzing the actuality consumption of the sinter Procedure and taking a series of measure to reduce the consumption of sinter Procedure. By optimizing the sintering ore ration structure, taking thick material layer-low temperature sinter, automatic immingling ore ration, increasing mix --material temperature, controlling the fuel granularity , improving fuel distributing and so on to reduce solid-fuel consumption . By decreasing the air leaking rate of the sinter system, increasing equipment working ratio, decreasing equipment empty--running time to save electric energy. By taking atom- minus pressure and low--temperature ignition techniques to decrease the burning gas consumption. By reclaiming residual heat of sinter to realize circle- economy, obtain better benefits of economy and social.Key words sinter, working procedure consumption, measure, practice1 引言唐钢炼铁厂北区现有1台265m2和3台180m2烧结机,2座2000m3高炉和1座3200m3高炉。
2009年全年产铁592万吨,3座高炉的主要炉料结构是烧结矿、球团矿和天然块矿,其中烧结矿是炼铁的主要原料,占入炉矿配比的80.44%。
近几年,随着烧结矿产量的增加,操作技能水平的提高及新设备的投入,唐钢炼铁厂北区的烧结工序能耗指标逐年降低,但与国内各大中型钢铁企业相比,仍比先进企业高10kgce/t。
炼铁厂北区根据烧结机的工艺流程和生产特点,采用新工艺、新技术,同时采用新的管理理念和管理措施,把节能降耗与技术进步有机结合,降低了烧结工序能耗,取得了较好的效果。
2 烧结工序能耗现状钢铁企业是能耗大户,能耗是吨钢成本的重要组成部分。
烧结工序能耗约占钢铁生产总能耗的8.3%,仅次于炼铁,是钢铁生产的第二耗能大户。
烧结工序能耗主要包括固体燃料消耗、电力消耗、点火煤气消耗、动力(压缩空气、蒸汽、水等)消耗,其中固体燃料消耗占70%~80%,电力消耗占13%~20% ,点火消耗占5%~10% [1]。
降低烧结工序能耗的实践多年来,炼铁厂北区在节能减排,降低成本方面做了大量工作,也取得了比较好的效果,但与一些先进企业相比,烧结工序能耗指标还比较高,还有一定差距。
2009年与相同或相近规格烧结机能耗指标对比见表1。
表1各企业2009年1~12月烧结能耗指标对比企业名称规格/m2料层/mm固体燃耗/kgce−1/t 新水耗量/t−1t蒸汽/kg−1/t 电耗/kWh−1/t 工序能耗/kgce−1/t 涟(源)钢180 600 45.7 0.24 42.6 54.7 新(余)钢180 650 38.66 37.08 45.44 山西海鑫198 690 45.31 39.57 53.47 长治198 700 37.36 0.76 48.49 47.53 唐钢180 695 48.39 0.4 2.08 35 55.5 从表1可以看出:唐钢炼铁厂北区烧结工序能耗比同规格烧结机的新(余)钢高 10.06 kgce/t,与涟(源)钢相比也有0.8 kgce/t的差距,因此,唐钢炼铁厂北区烧结工序节能降耗还有很大的潜力。
3 降低烧结工序能耗的措施3.1降低固体燃耗固体燃料消耗占烧结工序能耗的70%~80%,因此将降低固体燃料消耗作为主攻方向。
3.1.1 优化烧结配矿技术唐钢烧铁厂北区烧结使用的铁矿粉品种较多,有地方精粉、澳矿粉、巴西精矿和其他粉矿、褐铁矿等;各种矿粉的成矿条件不同,烧结性能也不同,为发挥各种矿粉的最佳烧结功效,需进行优化配矿的研究。
与河北理工大学合作,对炼铁厂北区使用的铁矿粉进行烧结性能研究。
澳矿粉的SiO2和Al2O3的含量较高,但粒度组成较好,具有熔点低、易同化的优点,使用后能降低烧结负压;而巴西矿粉SiO2、Al2O3含量低,但同化性及液相生成的能力差,两者搭配使用,烧结矿的各项经济指标明显提高,对降低燃料消耗起到了关键作用。
3.1.2 低温厚料层烧结技术的应用据资料介绍料层每提高10mm可降低固体燃料消耗2~3kg/t。
烧结料层提高后,在烧结机速相同的条件下高温保持时间延长,有利于铁酸钙的发育和黏结相的发展,而且料层越厚,料层中下部自动蓄热作用越强,在相同燃料比时料层中下部获得的热量也就越多,料层所能达到的温度也就越高,有利于液相的形成。
为实现厚料层烧结采取的措施如下:(1)布料方式上选用了梭式布料器、圆辊给料机、九辊布料器联合布料技术。
(2)利用余热锅炉低压过热蒸汽预热混合料提高料温,消除过湿层。
(3)改善生石灰质量,提高生石灰配比。
(4)外矿配比增加,透气性过好,将原来的双排疏料器改为单排疏料器。
通过以上措施的实施,2010年烧结机的料层厚度达到了700mm,实现了厚料层烧结技术,降低了烧结固体燃耗。
3.1.3 烧结配料自动化烧结配料由中控室联动调整,1号烧结机、2号烧结机、4号烧结机配料仓下料实现了PID调节,3号烧结机实现了配料室各仓补偿下料,即当一个下料仓出现故障下料量减少时,系统将自动调整其他料仓的下料量而使配料总量保持不变,从而达到稳定配料的目的。
实现配料自动化后,烧结原料的配料精度由原来的0.8%提高到0.3%,烧结矿的TFe稳定率提高了2%,达到98.5%以上。
3.1.4 提高混合料温度提高混合料温度,使其达到露点以上,降低过湿层对气流的阻碍而改善料层的透气性,加快燃烧速度,提高台时产量,节约固体燃耗。
另外,混合料温度提高后,部分显热可代替固体燃料的燃烧热,降低固体燃第八届(2011)中国钢铁年会论文集耗。
主要采取以下措施提高混合料温度:(1)改造生石灰消化器。
对1号、2号烧结机生石灰消化器进行扩容改造,延长消化时间,混合料温度提高4℃,改善了混合料混匀和制粒,混合料+3mm粒级平均提高了5%。
(2)在混合矿槽通蒸汽预热混合料。
二次混合机通入蒸汽预热混合料提高料温存在热利用率低、热损失大的缺点,经多次试验和设备改进,在混合料槽两侧安装两排阀门,通过调节阀门开度控制蒸汽量,使混合料水分及料温分布达到均匀,1号、2号、3号烧结机实现了在混合料矿槽通蒸汽预热混合料。
目前烧结机泥辊处的混合料温度达到了55℃以上。
3.1.5 精细化管理盯入烧的原燃料质量,稳定烧结燃料比炼铁厂北区烧结使用的燃料有焦粉和无烟煤两种。
焦粉主要是高炉筛下碎焦,成分较稳定;而无烟煤的质量波动较大,特别是灰分的波动不但影响燃料的消耗,还会影响烧结矿的碱度。
为给烧结创造良好的条件,除对进厂烧结煤的质量提出要求外,在烧结煤进厂时取样,掌握进厂成分,将成分差异较大的在一次料场分开造堆存放,一堆一取,堆、取料采取平铺直取的方式进行预混匀。
开始取料向燃料仓库上料时由专人跟踪取断面样,按标准缩分后送化验室检验成分值;烧结使用前再次在燃料破碎后的输出皮带处取样,送化验室化验。
经过三次跟踪和数据对比掌握无烟煤的成分,看火工可以有预见性地调整燃料配比,保持烧结燃料比的长周期稳定。
3.1.6 控制燃料粒度,改善燃料分布,降低烧结燃料比烧结过程的燃烧速度和传热速度相接近,才能实现用尽可能少的燃料达到所需温度。
燃料粒度过细时燃烧速度过快,高温保持时间短,燃烧带变薄,铁矿粉之间的黏结不牢固,烧结矿的强度降低,成品率降低。
随着铁矿石资源的紧缺,外矿粉比例逐年增加,烧结混合料经混匀、造球、制粒后大于3mm粒级65%左右,外矿粉的大颗粒部分难以熔化,过细的燃料不能满足烧结过程中的热量需求。
经多方论证,将焦粉、无烟煤粒度标准重新修订,焦粉小于3mm粒级由85%降到75%,无烟煤小于3mm粒级由80%降到70%。
并制定了燃料粒度的考核标准,在燃料破碎前对四辊间隙进行调整,根据焦粉和无烟煤的硬度不同制定了不同的调整标准。
这一措施实施后,燃料的粒度发生了明显的改变,提高了利用率,降低了燃料配比。
3.1.7 更换成品筛网,控制返矿平衡,提高成品率在烧结冷返矿粒度组成中,5~8mm粒级一般控制在25%左右,冷返矿中大颗粒的部分偏多,料层的透气性过好,负压低成矿差。
随着混匀矿中外矿配比的提高,现总配比已大于65%,混匀矿中+5mm粒级已达25%左右。
为提高烧结矿强度,唐钢炼铁厂北区对原有筛网尺寸进行部分更换,由6.3mm改为5mm,将冷返矿中5~8mm粒级控制在15%以下,烧结成品率提高了2%。
3.2降低烧结系统的电耗3.2.1 降低烧结系统漏风率烧结机头部密封板为四连杆机构,由于该密封装置的重力连杆不灵活,台车经过四连杆密封装置时,密封盖板被台车压下去后不能复位,造成密封板与台车大梁底板之间出现一道空隙[2],导致烧结机容易卡劲出现漏风点,为此2008年9月利用定修的机会将密封板改造为自调分体密封板。