浅谈烧结工序能耗
浅谈烧结工序能耗
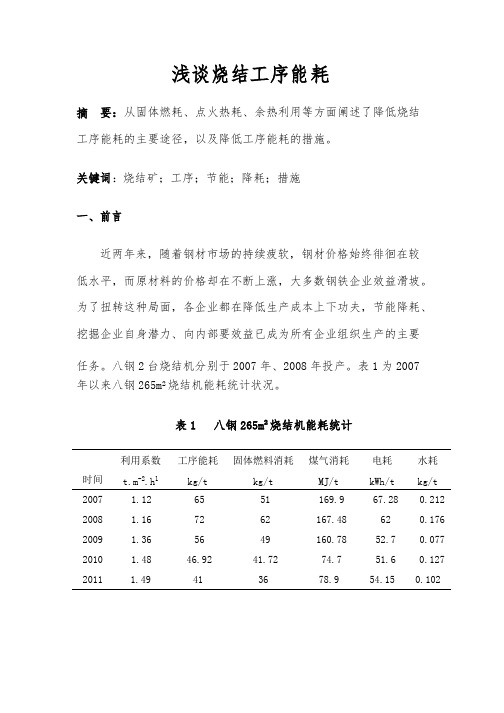
摘 浅谈烧结工序能耗要:从固体燃耗、点火热耗、余热利用等方面阐述了降低烧结工序能耗的主要途径,以及降低工序能耗的措施。
关键词:烧结矿;工序;节能;降耗;措施一、前言近两年来,随着钢材市场的持续疲软,钢材价格始终徘徊在较低水平,而原材料的价格却在不断上涨,大多数钢铁企业效益滑坡。
为了扭转这种局面,各企业都在降低生产成本上下功夫,节能降耗、挖掘企业自身潜力、向内部要效益已成为所有企业组织生产的主要任务。
八钢 2 台烧结机分别于 2007 年、2008 年投产。
表 1 为 2007 年以来八钢 265m 烧结机能耗统计状况。
表 1八钢 265m 烧结机能耗统计时间利用系数t.m .h工序能耗kg/t固体燃料消耗kg/t煤气消耗MJ/t电耗kWh/t水耗kg/t 2007 1.12 65 51 169.9 67.28 0.212 2008 1.16 72 62 167.48 62 0.176 2009 1.36 56 49 160.78 52.7 0.077 2010 1.48 46.92 41.72 74.7 51.6 0.127 20111.49413678.954.150.1022 2 -2 1二、降低烧结工序能耗的措施(一)降低固体燃料的消耗固体燃料消耗在烧结工序能耗中占的比重最大,达 75 %~80%,降低工序能耗首先要考虑的是降低固体燃料的消耗。
分析整个烧结工艺过程,影响固体燃料消耗的主要因素为含铁原料的物理化学性质、混合料的温度、混合料水分、混合料的粒度组成、固体燃料 的粒度、烧结料层厚度、熔剂的性质及添加量等。
1、原料合理搭配由于赤铁矿在烧结过程中与 CO 发生还原反应:Fe 2O 3+CO →Fe 3O 4+CO 2,消耗了一部分燃料,另外,由于赤铁矿可以在燃烧时进行分解:3Fe 2O 3=2Fe 3O 4+0.5O 2,也吸收一部分热量,而磁铁矿在烧结过程中与氧气发生氧化放热反应,节省燃料。
浅谈降低烧结工序能耗的措施
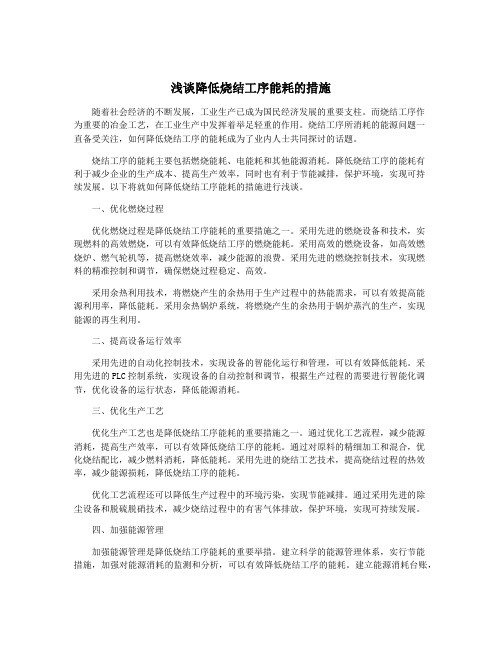
浅谈降低烧结工序能耗的措施随着社会经济的不断发展,工业生产已成为国民经济发展的重要支柱。
而烧结工序作为重要的冶金工艺,在工业生产中发挥着举足轻重的作用。
烧结工序所消耗的能源问题一直备受关注,如何降低烧结工序的能耗成为了业内人士共同探讨的话题。
烧结工序的能耗主要包括燃烧能耗、电能耗和其他能源消耗。
降低烧结工序的能耗有利于减少企业的生产成本、提高生产效率,同时也有利于节能减排,保护环境,实现可持续发展。
以下将就如何降低烧结工序能耗的措施进行浅谈。
一、优化燃烧过程优化燃烧过程是降低烧结工序能耗的重要措施之一。
采用先进的燃烧设备和技术,实现燃料的高效燃烧,可以有效降低烧结工序的燃烧能耗。
采用高效的燃烧设备,如高效燃烧炉、燃气轮机等,提高燃烧效率,减少能源的浪费。
采用先进的燃烧控制技术,实现燃料的精准控制和调节,确保燃烧过程稳定、高效。
采用余热利用技术,将燃烧产生的余热用于生产过程中的热能需求,可以有效提高能源利用率,降低能耗。
采用余热锅炉系统,将燃烧产生的余热用于锅炉蒸汽的生产,实现能源的再生利用。
二、提高设备运行效率采用先进的自动化控制技术,实现设备的智能化运行和管理,可以有效降低能耗。
采用先进的PLC控制系统,实现设备的自动控制和调节,根据生产过程的需要进行智能化调节,优化设备的运行状态,降低能源消耗。
三、优化生产工艺优化生产工艺也是降低烧结工序能耗的重要措施之一。
通过优化工艺流程,减少能源消耗,提高生产效率,可以有效降低烧结工序的能耗。
通过对原料的精细加工和混合,优化烧结配比,减少燃料消耗,降低能耗。
采用先进的烧结工艺技术,提高烧结过程的热效率,减少能源损耗,降低烧结工序的能耗。
优化工艺流程还可以降低生产过程中的环境污染,实现节能减排。
通过采用先进的除尘设备和脱硫脱硝技术,减少烧结过程中的有害气体排放,保护环境,实现可持续发展。
四、加强能源管理加强能源管理是降低烧结工序能耗的重要举措。
建立科学的能源管理体系,实行节能措施,加强对能源消耗的监测和分析,可以有效降低烧结工序的能耗。
钢铁烧结工序能耗计算公式
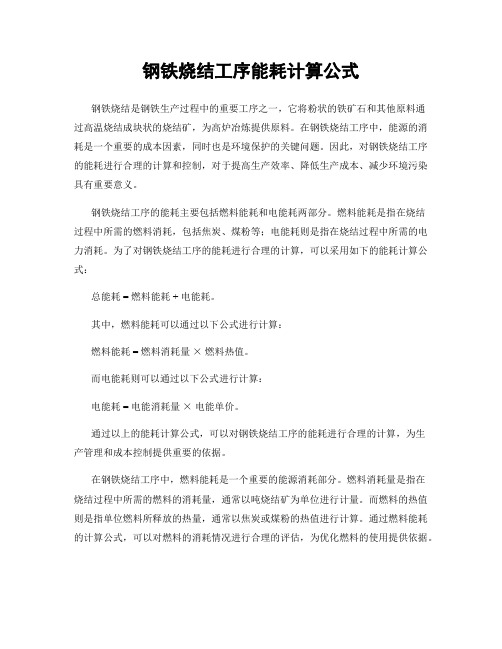
钢铁烧结工序能耗计算公式钢铁烧结是钢铁生产过程中的重要工序之一,它将粉状的铁矿石和其他原料通过高温烧结成块状的烧结矿,为高炉冶炼提供原料。
在钢铁烧结工序中,能源的消耗是一个重要的成本因素,同时也是环境保护的关键问题。
因此,对钢铁烧结工序的能耗进行合理的计算和控制,对于提高生产效率、降低生产成本、减少环境污染具有重要意义。
钢铁烧结工序的能耗主要包括燃料能耗和电能耗两部分。
燃料能耗是指在烧结过程中所需的燃料消耗,包括焦炭、煤粉等;电能耗则是指在烧结过程中所需的电力消耗。
为了对钢铁烧结工序的能耗进行合理的计算,可以采用如下的能耗计算公式:总能耗 = 燃料能耗 + 电能耗。
其中,燃料能耗可以通过以下公式进行计算:燃料能耗 = 燃料消耗量×燃料热值。
而电能耗则可以通过以下公式进行计算:电能耗 = 电能消耗量×电能单价。
通过以上的能耗计算公式,可以对钢铁烧结工序的能耗进行合理的计算,为生产管理和成本控制提供重要的依据。
在钢铁烧结工序中,燃料能耗是一个重要的能源消耗部分。
燃料消耗量是指在烧结过程中所需的燃料的消耗量,通常以吨烧结矿为单位进行计量。
而燃料的热值则是指单位燃料所释放的热量,通常以焦炭或煤粉的热值进行计算。
通过燃料能耗的计算公式,可以对燃料的消耗情况进行合理的评估,为优化燃料的使用提供依据。
另外,电能耗也是钢铁烧结工序中的重要能耗部分。
电能消耗量是指在烧结过程中所需的电能的消耗量,通常以千瓦时为单位进行计量。
而电能单价则是指单位电能的价格,通常以元/千瓦时为单位进行计算。
通过电能耗的计算公式,可以对电能的使用情况进行合理的评估,为降低电能消耗提供依据。
除了能耗的计算,钢铁烧结工序中还可以采取一系列的节能措施,进一步降低能耗。
例如,可以优化燃料的配比和燃烧条件,提高燃料的利用率;可以采用先进的烧结设备和技术,提高生产效率;可以采用余热回收技术,充分利用余热资源。
通过这些节能措施的实施,可以进一步降低钢铁烧结工序的能耗,减少生产成本,提高经济效益。
浅议科学分析能耗结构降低烧结能耗
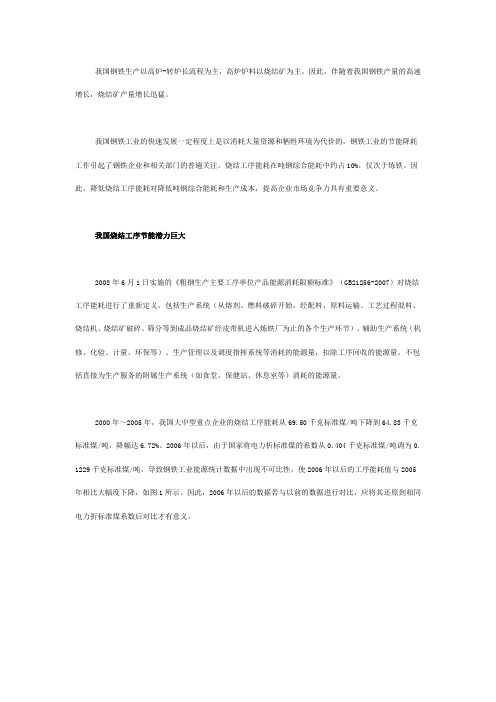
我国钢铁生产以高炉-转炉长流程为主,高炉炉料以烧结矿为主。
因此,伴随着我国钢铁产量的高速增长,烧结矿产量增长迅猛。
我国钢铁工业的快速发展一定程度上是以消耗大量资源和牺牲环境为代价的,钢铁工业的节能降耗工作引起了钢铁企业和相关部门的普遍关注。
烧结工序能耗在吨钢综合能耗中约占10%,仅次于炼铁。
因此,降低烧结工序能耗对降低吨钢综合能耗和生产成本,提高企业市场竞争力具有重要意义。
我国烧结工序节能潜力巨大2008年6月1日实施的《粗钢生产主要工序单位产品能源消耗限额标准》(GB21256-2007)对烧结工序能耗进行了重新定义,包括生产系统(从熔剂、燃料破碎开始,经配料、原料运输、工艺过程混料、烧结机、烧结矿破碎、筛分等到成品烧结矿经皮带机进入炼铁厂为止的各个生产环节)、辅助生产系统(机修、化验、计量、环保等)、生产管理以及调度指挥系统等消耗的能源量,扣除工序回收的能源量,不包括直接为生产服务的附属生产系统(如食堂、保健站、休息室等)消耗的能源量。
2000年~2005年,我国大中型重点企业的烧结工序能耗从69.50千克标准煤/吨下降到64.83千克标准煤/吨,降幅达6.72%。
2006年以后,由于国家将电力析标准煤的系数从0.404千克标准煤/吨调为0. 1229千克标准煤/吨,导致钢铁工业能源统计数据中出现不可比性,使2006年以后的工序能耗值与2005年相比大幅度下降,如图1所示。
因此,2006年以后的数据若与以前的数据进行对比,应将其还原到相同电力折标准煤系数后对比才有意义。
图1 我国重点大中型企业烧结工序能耗变化虽然我国重点企业烧结工序能耗逐年降低,但是各企业之间的能耗水平相差很大,因此我国烧结工序节能潜力很大。
固体燃料消耗、电耗和点火煤气消耗是节能重点烧结工序节能方向。
通过对多家企业烧结工序的能源消耗情况进行调研,得到了其能源消耗典型结构(如图2所示)。
由图2可以看出,烧结工序能耗中固体燃料占80%左右,电力消耗紧跟其后,再是点火煤气的消耗,其他能源消耗不到1%。
工信部钢铁能耗标准
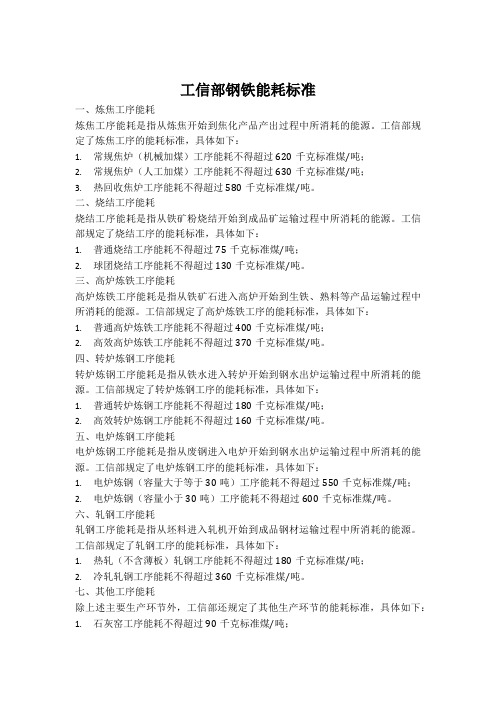
工信部钢铁能耗标准一、炼焦工序能耗炼焦工序能耗是指从炼焦开始到焦化产品产出过程中所消耗的能源。
工信部规定了炼焦工序的能耗标准,具体如下:1.常规焦炉(机械加煤)工序能耗不得超过620千克标准煤/吨;2.常规焦炉(人工加煤)工序能耗不得超过630千克标准煤/吨;3.热回收焦炉工序能耗不得超过580千克标准煤/吨。
二、烧结工序能耗烧结工序能耗是指从铁矿粉烧结开始到成品矿运输过程中所消耗的能源。
工信部规定了烧结工序的能耗标准,具体如下:1.普通烧结工序能耗不得超过75千克标准煤/吨;2.球团烧结工序能耗不得超过130千克标准煤/吨。
三、高炉炼铁工序能耗高炉炼铁工序能耗是指从铁矿石进入高炉开始到生铁、熟料等产品运输过程中所消耗的能源。
工信部规定了高炉炼铁工序的能耗标准,具体如下:1.普通高炉炼铁工序能耗不得超过400千克标准煤/吨;2.高效高炉炼铁工序能耗不得超过370千克标准煤/吨。
四、转炉炼钢工序能耗转炉炼钢工序能耗是指从铁水进入转炉开始到钢水出炉运输过程中所消耗的能源。
工信部规定了转炉炼钢工序的能耗标准,具体如下:1.普通转炉炼钢工序能耗不得超过180千克标准煤/吨;2.高效转炉炼钢工序能耗不得超过160千克标准煤/吨。
五、电炉炼钢工序能耗电炉炼钢工序能耗是指从废钢进入电炉开始到钢水出炉运输过程中所消耗的能源。
工信部规定了电炉炼钢工序的能耗标准,具体如下:1.电炉炼钢(容量大于等于30吨)工序能耗不得超过550千克标准煤/吨;2.电炉炼钢(容量小于30吨)工序能耗不得超过600千克标准煤/吨。
六、轧钢工序能耗轧钢工序能耗是指从坯料进入轧机开始到成品钢材运输过程中所消耗的能源。
工信部规定了轧钢工序的能耗标准,具体如下:1.热轧(不含薄板)轧钢工序能耗不得超过180千克标准煤/吨;2.冷轧轧钢工序能耗不得超过360千克标准煤/吨。
七、其他工序能耗除上述主要生产环节外,工信部还规定了其他生产环节的能耗标准,具体如下:1.石灰窑工序能耗不得超过90千克标准煤/吨;2.耐火材料及制品生产工序能耗不得超过450千克标准煤/吨;3.铁合金生产(包括硅系、锰系等)工序能耗不得超过580千克标准煤/吨。
探究降低烧结工艺能耗的措施
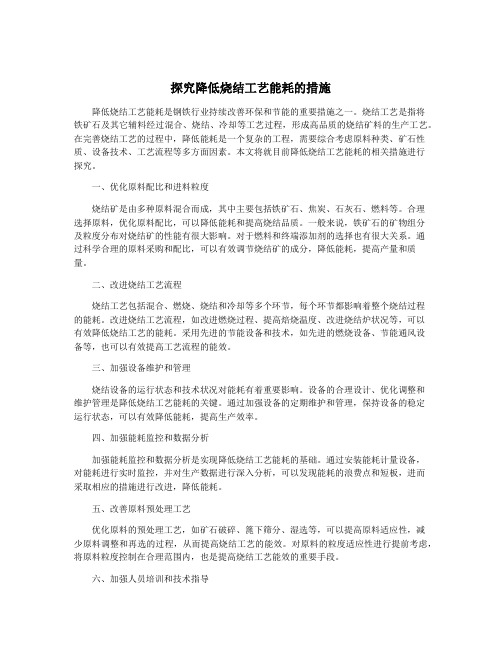
探究降低烧结工艺能耗的措施降低烧结工艺能耗是钢铁行业持续改善环保和节能的重要措施之一。
烧结工艺是指将铁矿石及其它辅料经过混合、烧结、冷却等工艺过程,形成高品质的烧结矿料的生产工艺。
在完善烧结工艺的过程中,降低能耗是一个复杂的工程,需要综合考虑原料种类、矿石性质、设备技术、工艺流程等多方面因素。
本文将就目前降低烧结工艺能耗的相关措施进行探究。
一、优化原料配比和进料粒度烧结矿是由多种原料混合而成,其中主要包括铁矿石、焦炭、石灰石、燃料等。
合理选择原料,优化原料配比,可以降低能耗和提高烧结品质。
一般来说,铁矿石的矿物组分及粒度分布对烧结矿的性能有很大影响。
对于燃料和终端添加剂的选择也有很大关系。
通过科学合理的原料采购和配比,可以有效调节烧结矿的成分,降低能耗,提高产量和质量。
二、改进烧结工艺流程烧结工艺包括混合、燃烧、烧结和冷却等多个环节,每个环节都影响着整个烧结过程的能耗。
改进烧结工艺流程,如改进燃烧过程、提高焙烧温度、改进烧结炉状况等,可以有效降低烧结工艺的能耗。
采用先进的节能设备和技术,如先进的燃烧设备、节能通风设备等,也可以有效提高工艺流程的能效。
三、加强设备维护和管理烧结设备的运行状态和技术状况对能耗有着重要影响。
设备的合理设计、优化调整和维护管理是降低烧结工艺能耗的关键。
通过加强设备的定期维护和管理,保持设备的稳定运行状态,可以有效降低能耗,提高生产效率。
四、加强能耗监控和数据分析加强能耗监控和数据分析是实现降低烧结工艺能耗的基础。
通过安装能耗计量设备,对能耗进行实时监控,并对生产数据进行深入分析,可以发现能耗的浪费点和短板,进而采取相应的措施进行改进,降低能耗。
五、改善原料预处理工艺优化原料的预处理工艺,如矿石破碎、篦下筛分、湿选等,可以提高原料适应性,减少原料调整和再选的过程,从而提高烧结工艺的能效。
对原料的粒度适应性进行提前考虑,将原料粒度控制在合理范围内,也是提高烧结工艺能效的重要手段。
浅谈降低烧结工序能耗的措施

浅谈降低烧结工序能耗的措施1. 引言1.1 烧结工序对能源消耗的重要性烧结工序是冶金工业重要的炼铁生产工序之一,其能源消耗对整个生产过程的能耗影响极为重要。
烧结工序主要是通过将铁矿石等原料在高温下加热,使其在烧结炉中发生一系列物理化学反应,最终形成高强度的铁制品。
烧结工序的能源消耗占据了整个冶金生产的重要比重,对于企业的生产成本和环境影响都具有重要的意义。
烧结工序所需能源包括燃料能源和电力能源,其中以燃料消耗较大。
在烧结工序中,煤炭、焦炭等燃料被用来提供高温热能,使原料得以烧结。
传统的烧结工序存在能源利用率低、排放浪费等问题,导致能源消耗较高。
降低烧结工序的能源消耗具有重要意义。
通过优化烧结工艺参数、采用先进的设备和技术、加强热能回收利用、提高烧结燃料的利用率以及应用节能技术等措施,可以有效降低烧结工序的能源消耗,提高生产效率,减少生产成本,实现可持续发展。
节能减排也是当前社会发展的重要趋势,降低烧结工序的能源消耗,不仅符合环保要求,也能提升企业的竞争力。
2. 正文2.1 优化烧结工艺参数优化烧结工艺参数是降低烧结工序能耗的重要措施之一。
通过调整烧结工艺中的各项参数,可以实现更高效的烧结过程,减少能源的消耗。
优化烧结工艺参数可以提高烧结的热效率。
合理调节烧结温度、烧结时间等参数,可以使烧结过程中的热能更加充分利用,减少能源的浪费。
优化参数还可以提高烧结矿的燃烧效率,减少燃料的使用量,降低能耗。
优化烧结工艺参数还可以改善产品质量。
通过精确控制烧结过程中的各项参数,可以确保产品的成分和性能达到要求,避免因为工艺参数不合理导致的质量问题,减少了产品的废品率,提高了资源利用率。
优化烧结工艺参数还可以减少设备运行时的能耗。
通过合理设置烧结设备的工作参数,有效控制能源的消耗,延长设备的使用寿命,减少了能源的浪费,降低了生产成本。
优化烧结工艺参数是降低烧结工序能耗的有效途径之一,可以提高烧结热效率,改善产品质量,减少设备能耗,从而实现节能减排的目标。
烧结降能耗具体方式分析
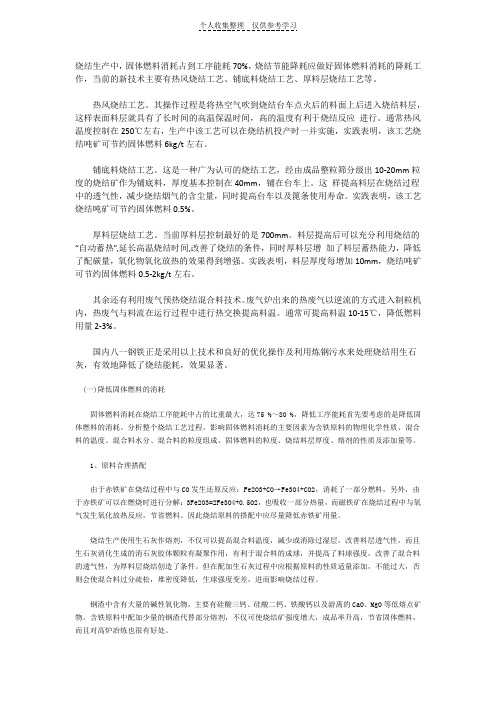
烧结生产中,固体燃料消耗占到工序能耗70%,烧结节能降耗应做好固体燃料消耗的降耗工作,当前的新技术主要有热风烧结工艺、铺底料烧结工艺、厚料层烧结工艺等。
热风烧结工艺。
其操作过程是将热空气吹到烧结台车点火后的料面上后进入烧结料层,这样表面料层就具有了长时间的高温保温时间,高的温度有利于烧结反应进行。
通常热风温度控制在250℃左右,生产中该工艺可以在烧结机投产时一并实施,实践表明,该工艺烧结吨矿可节约固体燃料6kg/t左右。
铺底料烧结工艺。
这是一种广为认可的烧结工艺,经由成品整粒筛分级出10-20mm粒度的烧结矿作为铺底料,厚度基本控制在40mm,铺在台车上。
这样提高料层在烧结过程中的透气性,减少烧结烟气的含尘量,同时提高台车以及篦条使用寿命。
实践表明,该工艺烧结吨矿可节约固体燃料0.5%。
厚料层烧结工艺。
当前厚料层控制最好的是700mm。
料层提高后可以充分利用烧结的“自动蓄热”,延长高温烧结时间,改善了烧结的条件,同时厚料层增加了料层蓄热能力,降低了配碳量,氧化物氧化放热的效果得到增强。
实践表明,料层厚度每增加10mm,烧结吨矿可节约固体燃料0.5-2kg/t左右。
其余还有利用废气预热烧结混合料技术。
废气炉出来的热废气以逆流的方式进入制粒机内,热废气与料流在运行过程中进行热交换提高料温。
通常可提高料温10-15℃,降低燃料用量2-3%。
国内八一钢铁正是采用以上技术和良好的优化操作及利用炼钢污水来处理烧结用生石灰,有效地降低了烧结能耗,效果显著。
(一)降低固体燃料的消耗固体燃料消耗在烧结工序能耗中占的比重最大,达75 %~80 %,降低工序能耗首先要考虑的是降低固体燃料的消耗。
分析整个烧结工艺过程,影响固体燃料消耗的主要因素为含铁原料的物理化学性质、混合料的温度、混合料水分、混合料的粒度组成、固体燃料的粒度、烧结料层厚度、熔剂的性质及添加量等。
1、原料合理搭配由于赤铁矿在烧结过程中与CO发生还原反应:Fe2O3+CO→Fe3O4+CO2,消耗了一部分燃料,另外,由于赤铁矿可以在燃烧时进行分解:3Fe2O3=2Fe3O4+0.5O2,也吸收一部分热量,而磁铁矿在烧结过程中与氧气发生氧化放热反应,节省燃料。
- 1、下载文档前请自行甄别文档内容的完整性,平台不提供额外的编辑、内容补充、找答案等附加服务。
- 2、"仅部分预览"的文档,不可在线预览部分如存在完整性等问题,可反馈申请退款(可完整预览的文档不适用该条件!)。
- 3、如文档侵犯您的权益,请联系客服反馈,我们会尽快为您处理(人工客服工作时间:9:00-18:30)。
浅谈烧结工序能耗
摘要:从固体燃耗、点火热耗、余热利用等方面阐述了降低烧结工序能耗的主要途径,以及降低工序能耗的措施。
关键词:烧结矿;工序;节能;降耗;措施
一、前言
近两年来,随着钢材市场的持续疲软,钢材价格始终徘徊在较低水平,而原材料的价格却在不断上涨,大多数钢铁企业效益滑坡。
为了扭转这种局面,各企业都在降低生产成本上下功夫,节能降耗、挖掘企业自身潜力、向内部要效益已成为所有企业组织生产的主要任务。
八钢2台烧结机分别于2007年、2008年投产。
表1为2007年以来八钢265m2烧结机能耗统计状况。
表1 八钢265m2烧结机能耗统计
时间利用系数
t.m-2.
h1
工序能耗
kg/t
固体燃料消耗
kg/t
煤气消耗
MJ/t
电耗
kWh/
t
水耗
kg/t
2007 1.126551169.967.280.212 2008 1.167262167.48620.176 2009 1.365649160.7852.70.077
2010 1.4846.9241.7274.751.60.127 2011 1.49413678.954.150.102
二、降低烧结工序能耗的措施
(一)降低固体燃料的消耗
固体燃料消耗在烧结工序能耗中占的比重最大,达75 %~
80 %,降低工序能耗首先要考虑的是降低固体燃料的消耗。
分析整
个烧结工艺过程,影响固体燃料消耗的主要因素为含铁原料的物理化
学性质、混合料的温度、混合料水分、混合料的粒度组成、固体燃料
的粒度、烧结料层厚度、熔剂的性质及添加量等。
1、原料合理搭配
由于赤铁矿在烧结过程中与CO发生还原反应:Fe2O3+CO→Fe3O4+CO2,消耗了一部分燃料,另外,由于赤铁矿可以在燃烧
时进行分解:3Fe2O3=2Fe3O4+0.5O2,也吸收一部分热量,
而磁铁矿在烧结过程中与氧气发生氧化放热反应,节省燃料。
因此烧
结原料的搭配中应尽量降低赤铁矿用量。
合理使用冶金废杂料,不仅可以解决污染问题,还能变废为宝。
八钢烧结厂目前使用的冶金废杂物有:高炉瓦斯灰,各种布袋除尘灰,
轧钢氧化铁皮,除尘红灰,炼钢压滤污泥等。
表2为八钢265m2烧结用料成分。
表2 八钢265m2烧结用料成分
名称单耗,
kg/t SiO,%CaO,%MgO,%TFe,%C,%Zn,%S,
高炉瓦斯灰12.5 5.71 4.510.9521.1448.950.7/氧化铁皮12.12 1.98 3.10.8870.86//0.轧钢除尘灰 3.39 2.68 2.150.9965.16//0.2炼钢污泥9.878.317.15 2.2353.25 3.50.360.1烧结除尘灰11.1 5.3516.7 2.2946.29 1.10.0460.8
烧结生产使用生石灰作熔剂,不仅可以提高混合料温度,减少
或消除过湿层,改善料层透气性,而且生石灰消化生成的消石灰胶体
颗粒有凝聚作用,有利于混合料的成球,并提高了料球强度,改善了
混合料的透气性,为厚料层烧结创造了条件。
但在配加生石灰过程中
应根据原料的性质适量添加,不能过大,否则会使混合料过分疏松,
堆密度降低,生球强度变差,进而影响烧结过程。
2、控制燃料粒度及粒度组成
烧结所用固体燃料的粒度与混合料的特性有关,一般应由实验确定。
但实验室和实际生产都证明了在精矿烧结时,固体燃料的最好粒度范围是0.5~3 mm,大于3 mm和小于0.5 mm粒级的存在都是不希望的,这部分粒级含量的增加均会使固体燃耗增加,烧结矿成品率降低。
设法控制固体燃料的粒度及组成是所有的烧结厂为高产、优质、低耗而应采取的一项重要措施。
3、提高混合料温度
(1)当烧结混合料温度较低时,水汽在料层中冷凝,形成过湿现象,使烧结料层透气性变坏。
提高混合料的温度,使其达到露点以上,可以显著减少或消除水汽在料层中的冷凝量,降低过湿层对气流的阻力,从而改善了料层透气性,使抽过料层的空气量增加,为料层内的热交换创造了良好的条件,燃烧速度加快,提高台时产量,节约固体燃料。
(2)提高混合料温度的措施主要有:生石灰预热、热水预热、热返矿预热、蒸汽预热及烧结废气预热等。
(3)另外使用生石灰作为强化烧结与节能的重要措施,并用
80 ℃左右的热水消化生石灰,使混合料的温度提高了20 ℃左右。
同时,改一次混合加冷水为加热水工艺。
另外,由于我厂采用的热返矿不直接参加配料工艺,热振筛筛下的小于5 mm的热返矿直接用链板输送机送到预热滚筒和部分一次混合料混匀、润湿,使混合料
温度提高了50 ℃以上。
通过这些方法,使送往烧结机的烧结料温度可达70 ℃左右,为节能降耗、提高产量创造了条件。
八钢烧结厂在生产过程中,配加适量的烧结剂,因为烧结剂在节能降耗中的作用也是不可忽视的。
(二)强化烧结剂的合理搭配
(1)降低固体燃料消耗
烧结料中的配碳量决定着烧结温度、气氛性质及烧结速度。
因本产品含有增氧、助燃物质,可催化加快固体燃料的燃烧反应速度,特别是对固体燃料中非碳物质的催化作用更强,激活混合料中可燃元素及固体燃料的反应活性,加上烧结剂固有的强力可燃、助燃放热物质,使料层总热量大大增加,温度升高,固定燃耗相对降低。
(2)提高烧结矿强度,提高成品率,降低粉化率,提高烧结矿品质由于增强剂和稳定剂的加入,改善增加了生成液相的数量和性质,增加了湿润性良好的胶结相。
同时,抑制了正硅酸钙的晶型转化(晶型转化时,体积增大10%,发生体积膨胀,导致烧结矿冷却时的自行粉碎)。
同时由于FeO的降低,烧结气氧的改善减少了难还原的铁橄榄石和正硅酸钙的形成(CaO与SiO3及FeO的化学亲和力比CaO 和Fe2O3的亲和力大得多),利于赤铁矿和铁酸钙的形成,
抑制了粉化现象,提高了烧结矿的强度,粒级趋于优化合理,同时改善了烧结矿的还原性,成品率上升,返矿量下降。
(3)提高烧结矿产量
垂直烧结速度是决定产量的重要因素,与产量基本成正比关系。
而垂直烧结速度是燃料的燃烧速度和传热速度决定的,当配碳量适宜或较高时,烧结过程总速度取决于碳的燃烧速度,燃烧速度与供氧强度成正比,强效剂中的富氧离子加快了碳的燃烧速度,提高了燃烧效率,同时高温使料层中水的气化速度变快,过湿层透气性变好,气体的传热速度加快,垂直烧结速度提高,产量提升,同时含粉率降低,强度的提高,使成品率上升,返矿下降,产量相应提高。
(4)降低燃料消耗
燃料消耗的降低是FeO含量降低的重要因素,同时由于烧结剂的加入给烧结料层增加了适量氧离子,缓解了碳粒附近的供氧不足,降低了CO浓度,减少了还原气氛,增强扩大了氧化气氛,抑制降低了FeO的生成。
(5)提高生铁产量,降低焦比
由于烧结强效剂的加入,改善了烧结矿的粒度组成和矿物组成,提高了烧结矿的冶金性能,还原性提高,FeO下降,铁产量增加,焦比同步降低。
(6)降低烧结废气中硫含量,利于环境保护
烧结原料在装卸、破碎、筛分和储运的过程中将产生含尘废气;在混合料系统中将产生水汽—粉尘的共生废气;混合料在烧结时,将产生含有粉尘、SO2和NOx的高温废气;烧结矿在破碎、筛分、冷却、贮存和转运的过程中也将产生含尘废气。
废气的气量很大,含尘和含SO2的浓度较高,所以对大气的污染较严重。
为了改善厂区环境,八钢对烧结废气经脱硫处理再排放到大气中,有利于改善环境。
(7)厚料层烧结
在抽风烧结过程中,台车上部的烧结饼受空气急剧冷却的影响,结晶程度差,玻璃质含量高,强度差。
随着料层厚度的增加,强度差的所占的比重相应降低,成品率相应提高,返矿率下降,进而减少了固体燃料消耗。
烧结料层的自动蓄热作用随着料层高度的增加而加强,当料层高度为180~220 mm时,蓄热量只占燃烧带热量总收入的35 %~
45 %,当料层厚度达到400 mm时,蓄热量达55 %~60 %。
因此,提高料层厚度,采用厚料层烧结,充分利用烧结过程的自动蓄热,可以降低烧结料中的固体燃料用量,根据实际生产情况,料层每增加10 mm,燃料消耗可降低1.5 kg/t左右。
除此之外,还可以对主抽风机进行扩容改造、加高台车挡板、加强设备维护、减少系统漏风等措施,使料层厚度有一定提高。
(三) 余热回收利用
烧结过程正常时,从烧结机尾部风箱排出的废气温度可达300 ℃左右,热烧结矿在冷却机前段用空气冷却后也可产生
300 ℃以上的热废气,这两部分热废气所含热量占整个烧结矿热能消耗的23 %~28 %,充分利用好这两部分热量将会使烧结工序能耗明显降低。
受工艺布置等方面的影响,对烧结机尾部风箱排出的热废气进行回收利用的厂家目前还不多,但很多厂家已对冷却机高温段热废气进行了回收利用,主要方法有:安装余热锅炉生产蒸汽;送入烧结机上部热风罩内,进行热风烧结;通入二次混合机内预热混合料;除尘后用作点火助燃空气;进行余热发电等。
四、结语
由此可以看出,我国烧结节能的潜力是很大的。
作为烧结设计工作者要不懈努力的探索。
在设计中采用节能降耗技术,以求有效而合理的利用能源。
所以在设计生产采取有效措施最大幅度的降低烧结过程中的固体燃料消耗,对降低烧结成本具有重大意义。
只要充分认识节能降耗技术的优越性和诱人的巨大经济效益的潜力,完全有可能迅速把我国烧结节能技术的应用推进到一个新水平。
八钢的265m2烧结机自投产以来,通过技术改造,工艺革新,加强原料管理等综合措施,使其能耗逐年下降,
工序能耗由投产初期的72kg/t,降到目前的45 kg/t,居国内先进水平。