装配线平衡模型
汽车装配线平衡方法的

汽车装配线平衡方法汇报人:日期:•装配线平衡问题概述•装配线平衡问题的基本理论•遗传算法在装配线平衡问题中的目录应用•模拟退火算法在装配线平衡问题中的应用•基于粒子群优化算法的装配线平衡问题求解方法•实例分析目录01装配线平衡问题概述装配线是一种将零部件组装到一起的生产线,通常包括多个工作站和工序。
装配线的定义装配线具有高效、连续、重复性高的特点,能够快速大量地生产产品。
装配线的特点装配线的定义与特点装配线平衡问题的定义装配线平衡问题是指如何安排工作站和工序的顺序和时间,以使整个装配线的生产效率最高。
装配线平衡问题的重要性良好的装配线平衡可以提高生产效率、降低生产成本、减少工人的疲劳程度,提高产品质量。
装配线平衡问题的定义与重要性多目标性装配线平衡问题通常需要考虑多个目标,如生产效率、生产成本、工人的疲劳程度等,需要在这些目标之间进行权衡和折衷。
复杂性装配线平衡问题是一个复杂的组合优化问题,需要考虑多种因素,如工作站的数量、工序的顺序、工人的技能水平、设备的可用性等。
动态性装配线的生产情况是动态变化的,需要根据市场需求、产品类型、生产计划等因素进行调整,因此需要动态地进行装配线平衡。
装配线平衡问题的挑战02装配线平衡问题的基本理论装配线平衡问题的数学模型定义与公式01装配线平衡问题可以定义为在满足一系列约束条件下,寻找使得生产线总运行时间最短的工站排列组合方式。
数学模型通常涉及线性规划、整数规划、动态规划等。
变量与参数02数学模型中涉及的变量和参数包括工站数量、每个工站的工作时间、生产节拍、工作站的约束条件等。
适用范围与局限性03数学模型适用于求解具有明确数学表达形式的装配线平衡问题,但对于一些复杂问题可能需要采用更先进的求解方法。
优化目标装配线平衡问题的优化目标通常是最小化生产线的总运行时间,以提高生产效率。
此外,还可以考虑其他优化目标,如最小化生产线成本、提高产品质量等。
约束条件装配线平衡问题的约束条件包括工人的操作时间、设备的加工能力、生产计划的安排等。
装配线平衡
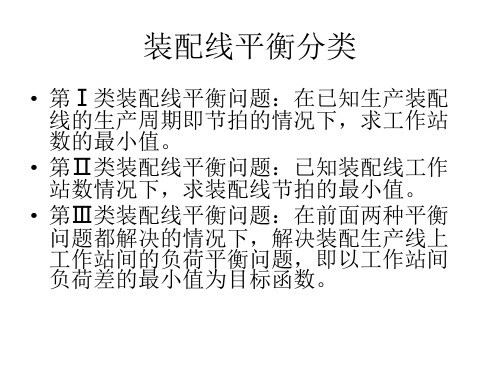
• 动平衡问题 • 在生产过程中达到装配线完全平衡是很困难的, 甚至是不可能的。最主要的原因是在生产过程中 会出现许多影响生产平衡的状况,例如原材料的 供给不足,生产的紧急插单,设备的故障,产品 需求变化引起的产品比例变化等等原因都会导致 生产的不平衡,在实际生产中我们就需要对一系 列不确定因素带来的生产不平衡进行调整,使得 生产线在生产过程中不断的达到新的平衡,这样 一个过程我们就叫生产线动态平衡或者生产过程 平衡。
混装生产线平衡影响因素
• • • • • 多品种配比变化 新产品导入或选装 操作工熟练度 生产线布局 其他
• 静平衡问题 • 混合装配线静平衡是指不考虑生产过程中 出现的各种影响生产线稳定性、连续性因 素的前提下,又称为确定性条件下,对混 合装配线进行平衡研究。主要是针对最小 生产循环,决定每个车型的操作分配方案, 在最小生产循环单元内的车型排产序列方 案。
装配线平衡分类
• 第Ⅰ类装配线平衡问题:在已知生产装配 线的生产周期即节拍的情况下,求工作站 数的最小值。 • 第Ⅱ类装配线平衡问题:已知装配线工作 站数情况下,求装配线节拍的最小值。 • 第Ⅲ类装配线平衡问题:在前面两种平衡 问题都解决的情况下,解决装配生产线上 工作站间的负荷平衡问题,即以工作站间 负类平衡分类处理
• 疫苗共生克隆选择算法 • 蚁群算法
一个MOD法在装配线平衡中应用案例

一个MOD法在装配线平衡中应用案例装配线平衡是指在保证生产效率和质量的前提下,通过合理的工作任务分配和工作站布局,使得每个工作站的工作时间基本相等,避免了一些工作站工作时间过长,造成生产线整体效率低下的问题。
其中,MOD法(Method of Difference)是一种常用的装配线平衡方法,它通过对比两个工作站的工作任务,并根据差异量来决定任务分配。
下面将介绍一个在装配线平衡中应用MOD法的案例。
假设有一个汽车零部件生产线,其中有4个工作站,每个工作站的工作内容如下:工作站1:装配发动机零部件A(每个零部件的操作时间为6分钟)工作站2:装配发动机零部件B(每个零部件的操作时间为5分钟)工作站3:装配发动机零部件C(每个零部件的操作时间为4分钟)工作站4:装配发动机零部件D(每个零部件的操作时间为3分钟)现在需要平衡这条生产线,使得每个工作站的工作时间基本相等。
下面是使用MOD法进行任务分配的步骤:1.计算工作站间的工作时间差异量首先,计算每个工作站的工作时间。
工作站1的工作时间为6分钟,工作站2的工作时间为5分钟,工作站3的工作时间为4分钟,工作站4的工作时间为3分钟。
然后,计算相邻工作站之间的工作时间差异量:-工作站1和工作站2的差异量为6分钟-5分钟=1分钟-工作站2和工作站3的差异量为5分钟-4分钟=1分钟-工作站3和工作站4的差异量为4分钟-3分钟=1分钟2.选择差异量最大的相邻工作站根据计算所得的差异量,选择差异量最大的相邻工作站。
在这个案例中,差异量最大的是工作站1和工作站2,差异量为1分钟。
3.分配任务至差异量最大的相邻工作站将工作站1的一个任务分配给工作站2,使得它们的工作时间相等化。
此时,工作站1有5个任务,工作站2有6个任务。
4.重新计算工作站间的工作时间差异量分配任务后,重新计算工作站间的工作时间差异量:-工作站1和工作站2的差异量为5分钟-5分钟=0分钟-工作站2和工作站3的差异量为4分钟-4分钟=0分钟-工作站3和工作站4的差异量为4分钟-3分钟=1分钟5.如果存在差异量不为0的相邻工作站,返回步骤2,否则结束。
精编【IE工业工程】IE装配线平衡

【IE工业工程】IE装配线平衡xxxx年xx月xx日xxxxxxxx集团企业有限公司Please enter your company's name and contentvIE:装配线平衡1. 制造环境中的元件装配装配是一个很古老的概念,是我们理解制造的基础。
很难列出制造的、用于出售的产品却没有经过装配的阶段,尽管也有一些,例如,简易扳手、斧柄、刀子、叉。
但是,我们想到的制造的产品经常是主要为装配的东西:汽车、计算机、还有飞机。
现代的装配作业还没有多少年,它包含工人的数目,移动的传送带,将分散的装配工人合理分配,使用装配传送带将部件带到他们身边。
图1解释了这个概念。
传统的装配生产线,就象图1所描绘的,通常是基于以下事实:工人可以被细分(Adam Smith concept)可以在生产线上不同的工位上分配;在生产线上工人通过传送带装配上道工序传来的部件。
但是在过去的二十年中,是如扩大提供给每个工位的工作数量的装配应用得到了很大的发展和成功的应用。
在这种方式中,移动的传送带可能将部件送到一个工位,一直到它完成才将它移走。
在这种情况下,需要一个来料的暂存区减少工作时间波动的影响。
这种装配生产线的“新”形式,让使用创新的传送带结构(被Tuggle叫做modular装配系统)成为可能,它通常需要不同的物理结构满足不同的需求。
一些这种新型的装配线的拥护者指出,通过强调技能和建立工人确认产品制度可以提高品质。
这种类的生产线需要大量的重复的工具和夹具,因为一些工人可能同时做相似的事情。
图2和图3给了两种MODULAR拉的范例。
装配也并不是一定要传送带,甚至可以不需要人。
装配可以在工作台或其他的装置上完成。
可以通过机器人或其他的可变成的设备固定元件。
相对于以传送带为导向的装配线的可供选择的现代的方法是“自动导向运载工具”(Automatic Guided Vehicle——AGV,见图4)。
AGV就象是一个移动的装配平台,它可以将要装配的产品从一个装配工位送到另一个。
装配生产线平衡原理讲义
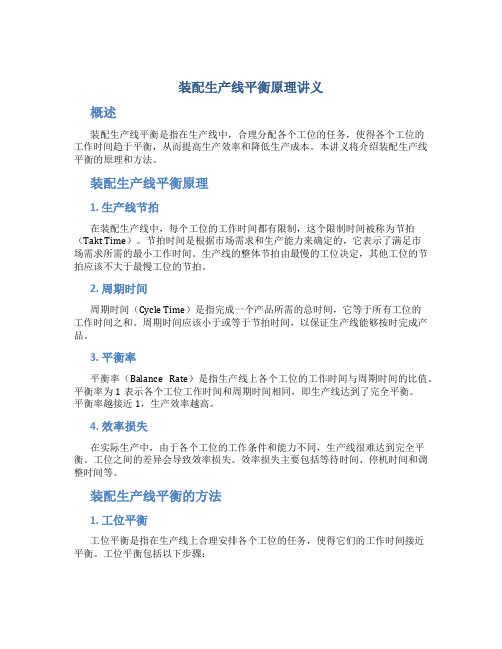
装配生产线平衡原理讲义概述装配生产线平衡是指在生产线中,合理分配各个工位的任务,使得各个工位的工作时间趋于平衡,从而提高生产效率和降低生产成本。
本讲义将介绍装配生产线平衡的原理和方法。
装配生产线平衡原理1. 生产线节拍在装配生产线中,每个工位的工作时间都有限制,这个限制时间被称为节拍(Takt Time)。
节拍时间是根据市场需求和生产能力来确定的,它表示了满足市场需求所需的最小工作时间。
生产线的整体节拍由最慢的工位决定,其他工位的节拍应该不大于最慢工位的节拍。
2. 周期时间周期时间(Cycle Time)是指完成一个产品所需的总时间,它等于所有工位的工作时间之和。
周期时间应该小于或等于节拍时间,以保证生产线能够按时完成产品。
3. 平衡率平衡率(Balance Rate)是指生产线上各个工位的工作时间与周期时间的比值。
平衡率为1表示各个工位工作时间和周期时间相同,即生产线达到了完全平衡。
平衡率越接近1,生产效率越高。
4. 效率损失在实际生产中,由于各个工位的工作条件和能力不同,生产线很难达到完全平衡。
工位之间的差异会导致效率损失。
效率损失主要包括等待时间、停机时间和调整时间等。
装配生产线平衡的方法1. 工位平衡工位平衡是指在生产线上合理安排各个工位的任务,使得它们的工作时间接近平衡。
工位平衡包括以下步骤:•收集工位工作时间数据:通过观察和记录各个工位的工作时间,了解各个工位的任务和工作量。
•分析工位的能力:评估各个工位的能力和工作速度,确定各个工位的标准工作时间。
•重新分配任务:根据工位的能力和任务量,重新分配工位的任务,使得各个工位的工作时间接近平衡。
•检查平衡度:检查调整后的生产线是否满足平衡率要求,如果不满足,需要再次调整任务分配。
2. 降低效率损失除了工位平衡外,还可以采取一些措施来降低效率损失,提高生产效率。
具体措施包括:•减少等待时间:通过优化任务分配和工作流程,减少工位之间的等待时间。
装配线平衡模型

§7 综合举例例求解非线性方程组其LINGO代码如下:model:x^2+y^2=2;2*x^2+x+y^2+y=4;end计算的部分结果为Feasible solution found at iteration: 0Variable ValueXY例装配线平衡模型一条装配线含有一系列的工作站,在最终产品的加工过程中每个工作站执行一种或几种特定的任务。
装配线周期是指所有工作站完成分配给它们各自的任务所化费时间中的最大值。
平衡装配线的目标是为每个工作站分配加工任务,尽可能使每个工作站执行相同数量的任务,其最终标准是装配线周期最短。
不适当的平衡装配线将会产生瓶颈——有较少任务的工作站将被迫等待其前面分配了较多任务的工作站。
问题会因为众多任务间存在优先关系而变得更复杂,任务的分配必须服从这种优先关系。
这个模型的目标是最小化装配线周期。
有2类约束:①要保证每件任务只能也必须分配至一个工作站来加工;②要保证满足任务间的所有优先关系。
例有11件任务(A—K)分配到4个工作站(1—4),任务的优先次序如下图。
每件任务所花费的时间如下表。
!装配线平衡模型;SETS:!任务集合,有一个完成时间属性T;TASK/ A B C D E F G H I J K/: T;!任务之间的优先关系集合(A 必须完成才能开始B,等等);PRED( TASK, TASK)/ A,B B,C C,F C,G F,J G,JJ,K D,E E,H E,I H,J I,J /;! 工作站集合;STATION/1..4/;TXS( TASK, STATION): X;! X是派生集合TXS的一个属性。
如果X(I,K)=1,则表示第I个任务指派给第K个工作站完成;ENDSETSDATA:!任务A B C D E F G H I J K的完成时间估计如下;T = 45 11 9 50 15 12 12 12 12 8 9;ENDDATA! 当任务超过15个时,模型的求解将变得很慢;!每一个作业必须指派到一个工作站,即满足约束①;@FOR( TASK( I): @SUM( STATION( K): X( I, K)) = 1);!对于每一个存在优先关系的作业对来说,前者对应的工作站I必须小于后者对应的工作站J,即满足约束②;@FOR( PRED( I, J): @SUM( STATION( K): K * X( J, K) - K * X( I, K)) >= 0);!对于每一个工作站来说,其花费时间必须不大于装配线周期;@FOR( STATION( K):@SUM( TXS( I, K): T( I) * X( I, K)) <= CYCTIME);!目标函数是最小化转配线周期;MIN = CYCTIME;!指定X(I,J) 为0/1变量;@FOR( TXS: @BIN( X));END计算的部分结果为Global optimal solution found at iteration: 1255Objective value:Variable Value Reduced Cost CYCTIMEX( A, 1)X( A, 2)X( A, 3)X( A, 4)X( B, 2) X( B, 3) X( B, 4) X( C, 1) X( C, 2) X( C, 3) X( C, 4) X( D, 1) X( D, 2) X( D, 3) X( D, 4) X( E, 1) X( E, 2) X( E, 3) X( E, 4) X( F, 1)X( F, 3) X( F, 4) X( G, 1) X( G, 2) X( G, 3) X( G, 4) X( H, 1) X( H, 2) X( H, 3) X( H, 4) X( I, 1) X( I, 2) X( I, 3) X( I, 4) X( J, 1) X( J, 2)X( J, 4)X( K, 1)X( K, 2)X( K, 3)X( K, 4)例 旅行售货员问题(又称货郎担问题,Traveling Salesman Problem )有一个推销员,从城市1出发,要遍访城市2,3,…,n 各一次,最后返回城市1。
装配生产线平衡原理讲义
装配生产线平衡原理讲义引言装配生产线平衡是一种将工作任务在装配生产线内进行分配和均衡的方法。
通过平衡装配线上的工作任务,可以提高生产效率,减少浪费,并确保整个生产过程顺利进行。
本讲义将介绍装配生产线平衡的原理和方法。
1. 装配生产线平衡的概述装配生产线平衡是指将不同工作任务均匀地分配给装配线上的工人,以达到生产线各工位的动态平衡。
通过平衡工作任务,可以减少装配线上的空闲时间和工人之间的等待时间,从而提高生产效率。
2. 装配生产线平衡的重要性装配生产线平衡可以带来以下几个重要好处: - 提高生产效率:通过优化工作任务的分配,可以缩短生产周期,提高生产效率。
- 减少浪费:平衡装配生产线可以减少工人之间的等待时间和装配线上的空闲时间,从而减少浪费。
- 降低成本:通过平衡装配线,可以减少人力资源的浪费,从而降低生产成本。
3. 装配生产线平衡的原理装配生产线平衡的原理包括以下几个方面: - 工作任务分析:首先要对装配线上的工作任务进行分析,确定每个工位所需的时间和工作内容。
- 平衡指标确定:根据工作任务的分析结果,确定装配线平衡的指标,如生产周期、生产数量等。
-工作任务分配:根据装配线平衡的指标,将工作任务均匀地分配给每个工位的工人。
- 定期调整:由于生产线上的工作任务可能会随着时间的推移而发生变化,因此需要定期对工作任务进行调整,以保持装配线的平衡状态。
4. 装配生产线平衡的方法装配生产线平衡的方法包括以下几个步骤: 1. 工作任务分析:对装配线上的工作任务进行仔细分析,确定每个工位所需的时间和工作内容。
2. 平衡指标确定:根据工作任务的分析结果,确定装配线平衡的指标,如生产周期、生产数量等。
3. 工作任务分配:根据平衡指标,将工作任务均匀地分配给每个工位的工人。
4. 定期调整:定期对工作任务进行调整,以适应生产线上的变化。
5. 装配生产线平衡的实施步骤装配生产线平衡的实施步骤包括以下几个阶段: 1. 数据收集:收集和整理装配线上的相关数据,如工作任务的时间和内容。
装配线平衡分析图表
25 22
20
使
17
用
15
15
时 15
20
19
16
16
间
22
22
22
22 22
22
17
18
16
15 14
18
18
12
10
9
tact
5
0
1
2
3
4
5
6
7
8
9 10 11 12 13 14 15 16 17 18 19 20 21 22 23
工位号
工位号 工位名称
1 2 3 4 5 6 7 8 9 10 11 12 13 14 15 16 17 18 19 20 21 22 23
不平衡损失=最高的DM*合计人数-各工序时间的合计(1人);生产线平衡率=1人实质时间合计(488)/最高的DM(22)*合计人数(27)=82%
装椅子
带
明箱
龙外
托
轮底组
上子铁
固
书
与桶柄塞合来自盖卡管定内
扣
件
组座
座
桶
件
合计
配置人数
12111212112111111111111
27
标准时间 15 17 15 22 20 16 19 16 9 22 15 14 17 18 16 22 12 22 18 22 22 18 22 423 1人标准时间 15 34 15 22 20 32 19 32 9 22 30 14 17 18 16 22 12 22 18 22 22 18 22 488 不平衡损失 7 10 7 0 2 12 3 12 13 0 15 8 5 4 6 0 10 0 4 0 0 4 0 107
《装配线平衡计算》课件
目录 CONTENTS
• 装配线平衡计算概述 • 装配线平衡计算方法 • 装配线平衡计算实例 • 装配线平衡优化策略 • 装配线平衡计算软件介绍
01
装配线平衡计算概述
装配线平衡计算的定义
装配线平衡计算是指通过合理安排装配线上的作业人员、作 业时间和作业顺序,使得装配线在稳定运行状态下完成一定 数量的产品,同时达到最优化的作业效率和资源利用率的计 算过程。
线性规划法
总结词
通过建立线性规划模型,求解最优解, 实现装配线的平衡计算。
VS
详细描述
线性规划法是一种数学优化方法,通过建 立线性方程或不等式来描述装配线平衡问 题。该方法将装配线上的作业要素、时间 、资源等作为变量,建立数学模型并求解 最优解。通过调整变量的值,可以找到最 优的装配线平衡方案,提高生产效率。
选择建议
根据企业规模和需求选择合适的软件;考虑软件的 易用性和技术支持;结合实际预算进行购买决策。
THANKS
THANK YOU FOR YOUR WATCHING
适应性和灵活性
装配线平衡计算应具有一定的适应性和灵活 性,以应对产品变化和生产调整。
02
装配线平衡计算方法
作业要素分析法
总结词
通过对作业要素的详细分析,确定各作业要素所需的时间,进而找出瓶颈作业和空闲时间,以达到装配线的平衡 。
详细描述
作业要素分析法首先对装配线上的每个作业要素进行详细分析,包括作业要素的类型、所需工具、操作步骤等, 并估算每个作业要素所需的时间。通过分析这些数据,可以找出装配线上的瓶颈作业(即耗时最长的作业要素) 和空闲时间,从而对装配线进行平衡调整,提高生产效率。
作业要素调整
《装配线平衡计算》课件
提高生产效率:通过平衡装配线,可以减少等待时间,提高生产效率。
降低生产成本:平衡装配线可以减少浪费,降低生产成本。
提高产品质量:平衡装配线可以减少错误,提高产品质量。
提高员工满意度:平衡装配线可以减少员工的工作压力,提高员工满意度。
提高生产灵活性:通过优化装配线布局,提高生产灵活性,适应市场需求变化
提高企业竞争力:通过优化装配线布局,提高企业竞争力,增强企业盈利能力
汇报人:PPT
优缺点比较:每种计算方法都有其优点和缺点,需要根据实际情况进行选择
选择原则:根据生产效率、成本、质量等因素进行综合考虑,选择最合适的计算方法
添加标题
添加标题
添加标题
添加标题
添加标题
添加标题
添加标题
确定装配线平衡计算的目标:提高生产效率,减少生产成本
计算工件加工时间:根据工件类型和加工时间,计算每个工件的加工时间
瓶颈工序分析法:分析瓶颈工序的原因,采取措施进行改进
线平衡率计算法:通过计算各工序的线平衡率,找出瓶颈工序,进行优化
工序时间优化法:通过优化工序时间,提高装配线的效率
生产线布局优化法:通过优化生产线布局,提高装配线的效率和灵活性
计算方法:包括时间计算法、效率计算法、成本计算法等
适用场景:不同计算方法适用于不同的生产环境和生产条件
计算工件加工时间总和:将所有工件的加工时间相加,得到总加工时间
优化工件加工顺序:根据工件加工效率,调整工件的加工顺序,以提高生产效率
数据整理:整理收集到的数据,确保数据的准确性和完整性
实例选择:选择具有代表性的装配线进行平衡计算
- 1、下载文档前请自行甄别文档内容的完整性,平台不提供额外的编辑、内容补充、找答案等附加服务。
- 2、"仅部分预览"的文档,不可在线预览部分如存在完整性等问题,可反馈申请退款(可完整预览的文档不适用该条件!)。
- 3、如文档侵犯您的权益,请联系客服反馈,我们会尽快为您处理(人工客服工作时间:9:00-18:30)。
精心整理§7综合举例例7.1求解非线性方程组其LINGO代码如下:model:x^2+y^2=2;2*x^2+x+y^2+y=4;end计算的部分结果为Feasiblesolutionfoundatiteration:0VariableValue!工作站集合;STATION/1..4/;TXS(TASK,STATION):X;!X是派生集合TXS的一个属性。
如果X(I,K)=1,则表示第I个任务指派给第K个工作站完成;ENDSETSDATA:!任务ABCDEFGHIJK的完成时间估计如下;T=4511950151212121289;ENDDATA!当任务超过15个时,模型的求解将变得很慢;!每一个作业必须指派到一个工作站,即满足约束①;@FOR(TASK(I):@SUM(STATION(K):X(I,K))=1);!对于每一个存在优先关系的作业对来说,前者对应的工作站I必须小于后者对应的工作站J,即满足约束②;@FOR(PRED(I,J):@SUM(STATION(K):K*X(J,K)-K*X(I,K))>=0);!对于每一个工作站来说,其花费时间必须不大于装配线周期;@FOR(STATION(K):@SUM(TXS(I,K):T(I)*X(I,K))<=CYCTIME);!目标函数是最小化转配线周期;MIN=CYCTIME;!指定X(I,J)为0/1变量;@FOR(TXS:@BIN(X));END计算的部分结果为Globaloptimalsolutionfoundatiteration:1255X(G,3)0.00000012.00000X(G,4)1.0000000.000000X(H,1)0.0000000.000000X(H,2)0.0000000.000000X(H,3)1.00000012.00000X(H,4)0.0000000.000000X(I,1)0.0000000.000000X(I,2)0.0000000.000000X(I,3)1.00000012.00000X(I,4)0.0000000.000000X(J,1)0.0000000.000000X(J,2)0.0000000.000000X(J,3)0.0000008.000000X(J,4)1.0000000.000000X(K,1)0.0000000.000000 X(K,2)0.0000000.000000 X(K,3)0.0000009.000000 X(K,4)1.0000000.000000例7.3旅行售货员问题(又称货郎担问题,TravelingSalesmanProblem )有一个推销员,从城市1出发,要遍访城市2,3,…,n 各一次,最后返回城市1。
已知从城市i 到j 的旅费为ij c,问他应按怎样的次序访问这些城市,使得总旅费最少?可以用多种方法把TSP 表示成整数规划模型。
这里介绍的一种建立模型的方法,是把该问题的每个解(不一定是最优的)看作是一次“巡回”。
在下述意义下,引入一些0-1整数变量: 其目标只是使∑=nj i ij ij x c 1,为最小。
(2)这样我们把TSP 转化成了一个混合整数线性规划问题。
显然,当城市个数较大(大于30)时,该混合整数线性规划问题的规模会很大,从而给求解带来很大问题。
TSP 已被证明是NP 难问题,目前还没有发现多项式时间的算法。
对于小规模问题,我们求解这个混合整数线性规划问题的方式还是有效的。
TSP 是一个重要的组合优化问题,除了有直观的应用外,许多其它看似无联系的优化问题也可转化为TSP 。
例如:问题1现需在一台机器上加工n 个零件(如烧瓷器),这些零件可按任意先后顺序在机器上加工。
我们希望加工完成所有零件的总时间尽可能少。
由于加工工艺的要求,加工零件j 时机器必须处于相应状态j s(如炉温)。
设起始未加工任何零件时机器处于状态0s ,且当所有零件加工完成后需恢复到0s 状态。
已知从状态i s 调整到状态)(i j s j ≠需要时间ij c 。
零件j 本身加工时间为j p。
为方便起见,引入一个虚零件0,其加工时间为0,要求状态为0s ,则{0,1,2,…,n}的一个圈置换π就表示对所有零件的一个加工顺序,在此置换下,完成所有加工所需要的总时间为 由于∑=nj j p 0是一个常数,故该零件的加工顺序问题变成TSP 。
!旅行售货员问题; model : sets :city/1..5/:u; link(city,city): dist,!距离矩阵; x;endsetsn=@size (city);data :!距离矩阵,它并不需要是对称的;dist=enddata !min =@sum @FOR !@sum !@sum );!@for @for );!限制u @for !定义X @for endU(5)0.0000000.000000DIST(1,1)0.44917740.000000 DIST(1,2)0.27245060.000000 DIST(1,3)0.12404300.000000 DIST(1,4)0.92468480.000000 DIST(1,5)0.40217060.000000 DIST(2,1)0.70914690.000000 DIST(2,2)0.16851990.000000 DIST(2,3)0.89896460.000000 DIST(2,4)0.25027470.000000 DIST(2,5)0.89475710.000000DIST(3,1)0.8648940E-010.000000 DIST(3,2)0.60205910.000000 DIST(3,3)0.33808840.000000DIST(3,4)0.68131640.000000DIST(3,5)0.22362710.000000DIST(4,1)0.97629870.000000DIST(4,2)0.88663430.000000DIST(4,3)0.71390080.000000DIST(4,4)0.22887700.000000DIST(4,5)0.71342500.000000DIST(5,1)0.85246790.000000DIST(5,2)0.23965380.000000DIST(5,3)0.57355250.000000DIST(5,4)0.14033140.000000DIST(5,5)0.69197080.000000X(1,1)0.0000000.4491774例7.4j p的距离用ij c N p,要求从决策时,过程停止。
显然这是一个不定期多阶段决策过程。
f是由i p点出发至终点N p的最短路程,由最优化原理可得定义)(i这是一个函数方程,用LINGO可以方便的解决。
!最短路问题;model:data:n=10;enddatasets:cities/1..n/:F;!10个城市;roads(cities,cities)/1,21,32,42,52,63,43,53,64,74,85,75,85,96,86,97,108,109,10/:D,P;endsetsdata:D=65369751191875410579;enddataF(n)=0;@forF(i)=);!@forP(i,j)=);endF(8)7.000000F(9)9.000000F(10)0.000000 P(1,2)1.000000 P(1,3)0.000000 P(2,4)1.000000 P(2,5)0.000000 P(2,6)0.000000 P(3,4)1.000000 P(3,5)0.000000 P(3,6)0.000000 P(4,7)0.000000 P(4,8)1.000000 P(5,7)1.000000P(5,8)0.000000P(5,9)0.000000P(6,8)1.000000P(6,9)0.000000P(7,10)1.000000P(8,10)1.000000P(9,10)1.000000例7.5露天矿生产的车辆安排(CMCM2003B)钢铁工业是国家工业的基础之一,铁矿是钢铁工业的主要原料基地。
许多现代化铁矿是露天开采的,它的生产主要是由电动铲车(以下简称电铲)装车、电动轮自卸卡车(以下简称卡车)运输来完成。
提高这些大型设备的利用率是增加露天矿经济效益的首要任务。
露天矿里有若干个爆破生成的石料堆,每堆称为一个铲位,每个铲位已预先根据铁含量将石料1卡车1.2.的解)。
矿石漏title CUMCM-2003B-01;sets:cai/1..10/:crate,cnum,cy,ck,flag;xie/1..5/:xsubject,xnum;link(xie,cai):distance,lsubject,number,che,b; endsetsdata:crate=30282932313332313331;xsubject=1.21.31.31.91.3;distance=5.265.194.214.002.952.742.461.900.641.27 1.900.991.901.131.272.251.482.043.093.51enddata!min=@sum@sum!@forb(i,j)=!@for!@for(cai(j):cnum(j)=@sum(xie(i):number(i,j)));!计算各个卸点的总产量;@for(xie(i):xnum(i)=@sum(cai(j):number(i,j)));!道路能力约束;@for(link(i,j):number(i,j)<=lsubject(i,j));!电铲能力约束;@for(cai(j):cnum(j)<=flag(j)*8*60/5);!电铲数量约束----addedbyXieJinxing,2003-09-07;@sum(cai(j):flag(j))<=7;!卸点能力约束;@for(xie(i):xnum(i)<=8*20);!铲位产量约束;@for(cai(i):number(1,i)+number(2,i)+number(5,i)<=ck(i)*10000/154);@for(cai(i):number(3,i)+number(4,i)<=cy(i)*10000/154);!产量任务约束;@for(xie(i):xnum(i)>=xsubject(i)*10000/154);!铁含量约束;@sum(cai(j):number(1,j)*(crate(j)-30.5))<=0;@sum(cai(j):number(2,j)*(crate(j)-30.5))<=0;@sum@sum@sum@sum!@for!hehe=!@for@for!ccnum=end例7.6这对的生成树。