BMC缺陷分析及解决方法
BMC注塑

BMC是热固性材料。
注塑机料筒温度不能太多,一般设定再60度,便于材料流动即可。
BMC/DMC:团状模玻璃钎维塑料主要特点是轻质、高强、绝缘、耐腐蚀,还具有利用率高,成型率高,产品质量稳定,操作方便等优点,广泛应用于汽车制造、铁路交通、建筑配件、机电产品等领域。
应用于1、电气部件;2、汽车配件;3、电机部件;4、日用产品。
PBT: 聚对苯二甲酸丁二醇酯(PBT)又名聚苯二甲酸四次甲基酯。
是一种热塑性工程塑料。
聚对苯二甲酸丁二醇酯为结晶形,熔点为224度,相对密度1.31~1.55,吸水率为热塑料中最低者之一,公0.07%。
具有优良的强韧性和抗疲劳性,冲击强度,有自润滑性和耐磨性,磨擦系数小,但缺口敏感性大。
耐热、耐气候性好,耐燃,但能慢燃。
尺寸稳定性好,电性能优良,耐电弧好。
但体积电阻率高频介质损耗角正切值大。
聚对苯二甲酸丁二醇酯成型加工可注塑、挤出、吹塑、涂覆、焊接、粘接、机加工、真空成型、真空镀金属、涂饰等。
用途:机械工业如齿轮、轴承、泵壳、阀门、导向板等;汽车工业如各种嵌板、防护板、汽化器配件、汽车内外装饰件、油管、油箱、各种车挡,点火器零件、继电器;电子、电器工业如阻燃、耐热、电绝缘,耐电弧;尺寸稳定、耐化学药品的接插件、线圈骨架、调谐器,端子盘,输出变压器壳,电机内转向器等PEBY:透明杂料。
各种原料混合体。
BMC注塑机和普通塑料机的主要区别在于加热系统,BMC注塑机通过模具加热来达到产品固化成型,普通注塑机是通过料筒加热,将塑料颗料熔融,通过模具冷确达到产品固化成型。
另外BMC的射出结构以前油路系统和普通注塑机也有一些不同之处。
BMC材料属于热固性材料,不可回收利用。
普通塑料(包括很多工程塑料)都属于热塑性,可二次回收利用的热固性材料BMC的成型工艺原有方法费时费力,产量低、生产成本高、次品率高.采用注塑成型方法对BMC进行成型加工.不仅可以使产量得到发幅度提高,企业生产成本得到下降.产品更精密报废率更低。
BMC缺陷以及原因

BMC的缺陷以及原因一气泡乃是加压BMC基材时出现气体导致在制品表层突起。
可能的原因及纠正的措施:1.BMC原料中的“干玻纤”引起模塑料铺层中的空隙,这些空隙在成型时其内集合的气体可能膨胀为气泡。
要完全纠正就要在制备BMC时改变工艺或减少玻纤的含量。
2.BMC原料被湿气、压机的油花、润滑油或外脱模剂所沾染,在成型时受热可能转变成蒸汽而引成气泡,碳酸钙和硬脂酸盐都是亲水物质故所以容易沾染水份。
3.捕获空气的机会应减到最少,这种机会取决于BMC铺料的面积和位置,实际上采用减少铺料的面积,类似像金字塔一样铺放在模具中央部位是有效的,可以迫使空气在成型中跑在BMC料流的前面而逸出。
4.当合模至最后尺寸前,应尽量减慢合模速度,较低的合模速度会减少物料的搅动并削弱捕获空气的机会。
5.上述较低的闭模速度如果结合较低的模温,能导致较平坦地流动和较少的予凝胶,也减少了捕获空气的机会,但固化时间必须加长。
6.减少模塑的压力是有效的,可形成较平坦的料流,减少了捕获空气的机会。
7.检查模具安装的平行度和压机本身的平行度。
由于模具安装失水准会引起料流之搅动(不平坦流动)就会增加捕获空气的机会。
8.超量的引发剂或阻聚剂能引起予凝胶和不平坦流动,同样,低收缩添加剂也会引起气体的产生,此刻,改进BMC的配方就有必要。
9.材料的粘度极大地影响料流,故要调整其到适当的范围,平时要注重不同的粘度水平将在多大程度上影响到气泡发生的位置与频度。
10.制品变截面变厚度部位能改变平坦的料流,过厚的截面在固化时并不能得到充分的热度和压力,为此可从产品设计上进行检讨。
11.通常成型中捕获的空气会使制品发生缺肉、自燃和气泡,因此适当的出料飞边是必要的,利于排气。
12.过分干硬的料团致使料流不稳定,导致予凝胶,针孔和气泡。
二蜘蛛网白色螺旋丝束状的热塑性塑料的集聚,这种症状指示热塑性塑料和聚酯是不相容的。
可能的原因及纠正的措施:1.由于起始增稠不快,热塑性塑料添加剂从基体复合物中分离出来,应使复合物起始一小时增稠到50万Cps。
塑料件缺陷原因及改进方法
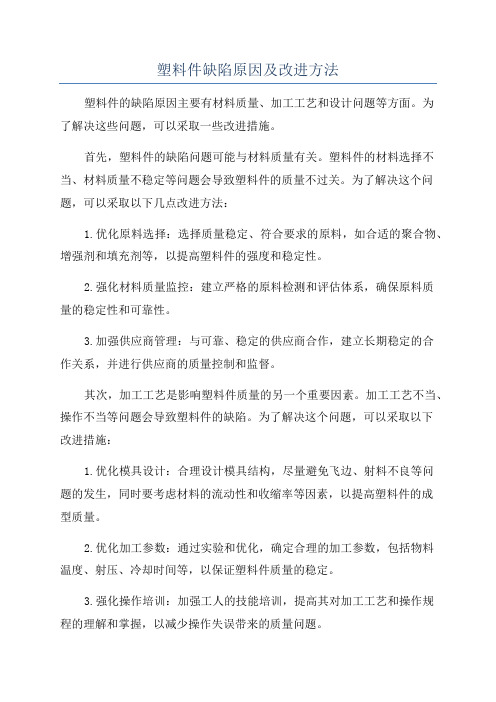
塑料件缺陷原因及改进方法塑料件的缺陷原因主要有材料质量、加工工艺和设计问题等方面。
为了解决这些问题,可以采取一些改进措施。
首先,塑料件的缺陷问题可能与材料质量有关。
塑料件的材料选择不当、材料质量不稳定等问题会导致塑料件的质量不过关。
为了解决这个问题,可以采取以下几点改进方法:1.优化原料选择:选择质量稳定、符合要求的原料,如合适的聚合物、增强剂和填充剂等,以提高塑料件的强度和稳定性。
2.强化材料质量监控:建立严格的原料检测和评估体系,确保原料质量的稳定性和可靠性。
3.加强供应商管理:与可靠、稳定的供应商合作,建立长期稳定的合作关系,并进行供应商的质量控制和监督。
其次,加工工艺是影响塑料件质量的另一个重要因素。
加工工艺不当、操作不当等问题会导致塑料件的缺陷。
为了解决这个问题,可以采取以下改进措施:1.优化模具设计:合理设计模具结构,尽量避免飞边、射料不良等问题的发生,同时要考虑材料的流动性和收缩率等因素,以提高塑料件的成型质量。
2.优化加工参数:通过实验和优化,确定合理的加工参数,包括物料温度、射压、冷却时间等,以保证塑料件质量的稳定。
3.强化操作培训:加强工人的技能培训,提高其对加工工艺和操作规程的理解和掌握,以减少操作失误带来的质量问题。
此外,塑料件的设计问题也会导致质量缺陷。
设计不当、结构不合理等问题会影响塑料件的使用寿命和功能。
1.优化产品设计:在设计阶段就要充分考虑材料特性、工艺要求和使用环境等因素,合理确定塑料件的结构和尺寸,以提高产品的可靠性和使用寿命。
2.强化模拟分析:通过使用CAD、CAE等软件工具进行模拟分析,预测设计在使用过程中的变形、应力分布等问题,在设计阶段就可以进行修正和优化。
3.进行实际测试:在设计验证阶段进行实际测试,包括强度测试、耐久性测试等,以验证设计的合理性和可靠性。
综上所述,塑料件的缺陷问题可能与材料质量、加工工艺和设计问题有关。
通过优化原料选择、加强材料质量监控、优化模具设计、优化加工参数、强化操作培训、优化产品设计、强化模拟分析和进行实际测试等改进方法,可以有效解决这些问题,提高塑料件的质量和可靠性。
BMC缺陷分析及解决方法

2.增加玻纤的含量(玻纤 3.降低顶出机构的速度 2.改善模具型腔厚度, 2.降低开裂部位的固化速度
的含量应控制在15%~20% (控制在20~35之间) 使其均衡(厚度:2mm (电加热模具可降低此处模
之内)。
~2.5mm)。
温或增加此处壁厚;而油温
3.模具表面进行抛光 加热模具可增加此处壁厚)
4.滑块进行修复 5.调整顶针长度 6.增加脱模斜度
BMC缺陷分析及解决方法
缺陷
定义
材料
分析
设备
模具
工艺
材料
解决方法
设备
模具
工艺
气孔
是由于注射成型 时,气体不能够 顺利的排出而形 成的。
1.材料玻纤、 CaCO3中含有水分 2.料的流动性不 好
1.螺杆背压太 低,2.储料速度 过快,3.料筒温 度太低,
由于模具温度过 1.引发剂的高温
高而对产品表面 与低温配比不
48h以上。
℃~35℃之间
4.将模具设置为抽真空 4.分担注射位置(如位置:
模具。
15、10、5改25、15、5)
1.模具表面的温度不 1.模具温度太高。 均 2.模具型腔厚度不够 均衡,
1.根据产品的不同厚度及 1.增加一个续压设备 1.改善模具水路,使其 1.适当降低模温(160℃~
模具构造,选定不同的配 2.改用大型号的注塑机 表面温度均衡(模芯温 180℃)之间。
2.脱模剂分散不 均3.团料塑化时
、镀铝的隔离膜 间不够。
。
1.顶出机构不均 衡,或顶出机构 压力太大、速度 太快。
1.储料背压不 够,2.注塑机压 力不够3.料筒温 度太低,4.喷嘴 受损,跑料
1.模具表面温度不均 1.顶出压力太大,
BMC模具设计、制造与维修控制要点
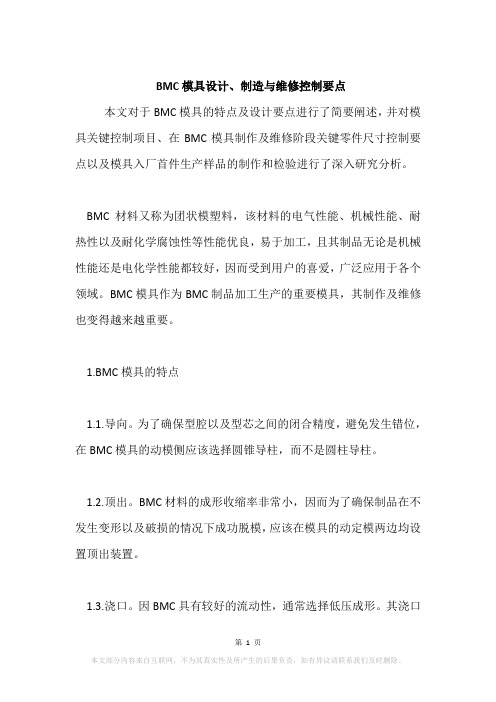
BMC模具设计、制造与维修控制要点本文对于BMC模具的特点及设计要点进行了简要阐述,并对模具关键控制项目、在BMC模具制作及维修阶段关键零件尺寸控制要点以及模具入厂首件生产样品的制作和检验进行了深入研究分析。
BMC材料又称为团状模塑料,该材料的电气性能、机械性能、耐热性以及耐化学腐蚀性等性能优良,易于加工,且其制品无论是机械性能还是电化学性能都较好,因而受到用户的喜爱,广泛应用于各个领域。
BMC模具作为BMC制品加工生产的重要模具,其制作及维修也变得越来越重要。
1.BMC模具的特点1.1.导向。
为了确保型腔以及型芯之间的闭合精度,避免发生错位,在BMC模具的动模侧应该选择圆锥导柱,而不是圆柱导柱。
1.2.顶出。
BMC材料的成形收缩率非常小,因而为了确保制品在不发生变形以及破损的情况下成功脱模,应该在模具的动定模两边均设置顶出装置。
1.3.浇口。
因BMC具有较好的流动性,通常选择低压成形。
其浇口的大小以及形状是由制品的来确定的,通常情况下选用侧浇口以及扇形浇口,且最好选用大浇口。
为减少大浇口对成型产品外形的影响,模具通常采用自切水口结构将浇口切断。
1.4.排气。
BMC材料是由不饱和聚酯树脂等物质组合而成的,因而在模腔中成形时会发生化学反应并且会有气体产生,所以模具要设有排气槽。
通常情况下排气槽设在分型面上,以避免发生填充不良以及熔缝等现象。
另外,模具的拼缝以及顶杠的配合间隙等也可以用来排气。
2.BMC模具的设计要点2.1.分型面设计。
为了保证制品在确保加工精度和强度的前提条件下能够顺利脱模,在对模具进行分型面的选择时应注意将分型面尽可能设在模具的下模,使得顶出机构尽量简单,以方便制品的推出;便于对飞边的清除,避免飞边对制品精度的影响;模具的制造以及零件的加工简单易行;确保制品的强度能够满足要求。
分型面的设计是制品能否顺利脱模的关键因素,因此在模具设计的初级阶段应该分型设计并做出设计图纸。
2.2.加工精度要求。
BMC成型工艺及设备模具的使用
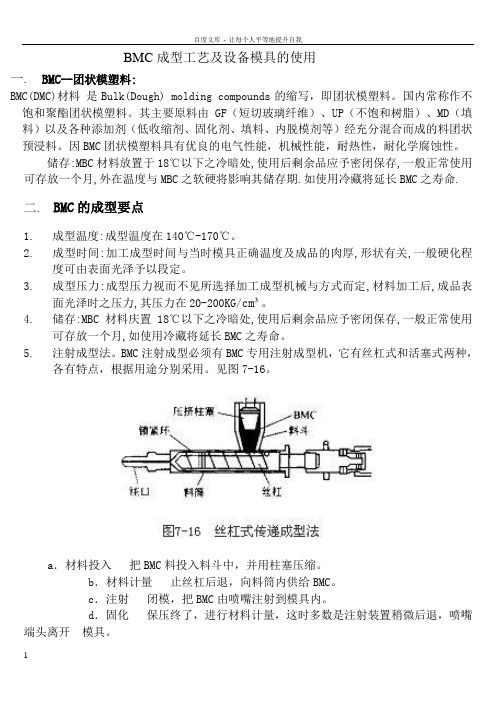
BMC成型工艺及设备模具的使用一.BMC--团状模塑料:BMC(DMC)材料是Bulk(Dough) molding compounds的缩写,即团状模塑料。
国内常称作不饱和聚酯团状模塑料。
其主要原料由GF(短切玻璃纤维)、UP(不饱和树脂)、MD(填料)以及各种添加剂(低收缩剂、固化剂、填料、内脱模剂等)经充分混合而成的料团状预浸料。
因BMC团状模塑料具有优良的电气性能,机械性能,耐热性,耐化学腐蚀性。
储存:MBC材料放置于18℃以下之冷暗处,使用后剩余品应予密闭保存,一般正常使用可存放一个月,外在温度与MBC之软硬将影响其储存期.如使用冷藏将延长BMC之寿命.二. BMC的成型要点1.成型温度:成型温度在140℃-170℃。
2.成型时间:加工成型时间与当时模具正确温度及成品的肉厚,形状有关,一般硬化程度可由表面光泽予以段定。
3.成型压力:成型压力视而不见所选择加工成型机械与方式而定,材料加工后,成品表面光泽时之压力,其压力在20-200KG/cm³。
4.储存:MBC材料庆置18℃以下之冷暗处,使用后剩余品应予密闭保存,一般正常使用可存放一个月,如使用冷藏将延长BMC之寿命。
5.注射成型法。
BMC注射成型必须有BMC专用注射成型机,它有丝杠式和活塞式两种,各有特点,根据用途分别采用。
见图7-16。
a.材料投入把BMC料投入料斗中,并用柱塞压缩。
b.材料计量止丝杠后退,向料筒内供给BMC。
c.注射闭模,把BMC由喷嘴注射到模具内。
d.固化保压终了,进行材料计量,这时多数是注射装置稍微后退,喷嘴端头离开模具。
e.取出制品开启模具,取出固化了的制品。
6. BMC产品设计注意事项①基本壁厚~3mm(最小在lmm以上)。
②拐角半径只要在l以上。
③脱模锥度要大于1°(局部可无锥度)。
④可设计加强筋结构。
⑤在凸起、销等单独存在的产品中其根部可带R。
⑥尖头部及熔接处可用气体脱模。
⑦飞边难脱模,要设计成易于脱模的结构。
成型缺陷及改善对策大全
塑料注塑成型不良现象的原因及处理办法
注塑成型概论
1. 何谓注塑成型
所谓注塑成型(Injection Molding)是指,
将已加热融化的材料喷射注入到模具内,经由冷
却与固化後,得到成形品的方法。
适用于量产与形状复杂产品等成形加工领域。
射出成形工程是以下列六大顺序执行:
1.合模
2.注射
3.保压
4.冷却
5.开模
6.取出产品
重复执行这种作业流程,就可连续生产制品。
2. 注塑成型机
注塑成型机可区分为合模装置与注射装置。
合模装置是开闭模具以执行脱模(eject)作业,而且也有如图所示的肘杆方式,以及利用油压缸直接开闭模具的直压方式。
注射装置是将树脂予以加热融化後再射入模具内。
此时,要旋转螺杆,并如图所示让投入到料斗的树脂停留在螺杆前端(称之为计量),经过相当于所需树脂量的行程储藏後再进行射出。
当树脂在模具内流动时,则控制螺杆的移动速度(射出速度),并在填充树脂後用压力(保压力)进行控制。
当达到一定的螺杆位置或一定射出压力时,则从速度控制切换成压力控制。
3. 模具
所谓模具(Mold)是指,为了将材料树脂做成某种形状,而用来承接射出注入树脂的金属制模型。
虽然没有图示记载,但实际上有几个空孔,并用温水、油、加热器等进行温度管理。
已溶解的材料是从浇口进入模具内,再经由流道与流道口填充到模槽内。
接下来则经由冷却工程与开模成型机脱模杆上的模具脱模板,推顶出成形品。
DMC,BMC,PC
1.团状模塑料DMCDMC:团状模塑料;BMC(DMC)--团状模塑料:BMC(DMC)材料是Bulk(Dough) molding compounds的缩写,所以国内外有BMC/DMC两种称呼,即团状模塑料。
国内常称作不饱和聚酯团状模塑料。
其主要原料由GF(短切玻璃纤维)、UP(不饱和树脂)、MD(填料)以及各种添加剂经充分混合而成的料团状预浸料。
DMC材料于二十世纪60年代在前西德和英国,首先得以应用,而后在70年代和80年代分别在美国和日本得到了较大的发展。
因BMC团状模塑料具有优良的电气性能,机械性能,耐热性,耐化学腐蚀性,又适应各种成型工艺,即可满足各种产品对性能的要求,因此越来越受到广大用户的喜爱。
BMCBMC(DMC)材料是Bulk(Dough) molding compounds的缩写,即团状模塑料。
国内常称作不饱和聚酯团状模塑料。
其主要原料由GF(短切玻璃纤维)、UP(不饱和树脂)、MD(填料碳酸钙)以及各种添加剂经充分混合而成的料团状预浸料。
DMC 材料于二十世纪60年代在前西德和英国,首先得以应用,而后在70年代和80年代分别在美国和日本得到了较大的发展。
因BMC团状模塑料具有优良的电气性能,机械性能,耐热性,耐化学腐蚀性,又适应各种成型工艺,即可满足各种产品对性能的要求,因此越来越受到广大用户的喜爱。
团状模塑料(BMC) 是一种热固性塑料,其中混合了各种惰性填料、纤维增强材料、催化剂、稳定剂和颜料,形成一种用于压塑或注塑的胶粘“油灰状”复合材料。
团状模塑料(BMC) 通过短纤维进行高度填充和增强,玻璃纤维增强材料占10% 至30%,长度通常在1/32 英寸至1/2 英寸(12.5mm)之间。
根据不同的最终应用领域,配制的复合材料可精确控制尺寸,阻燃性和抗电痕性良好,具有很高的介电强度、耐腐蚀性和耐污性,机械性能卓越,收缩性低且色泽稳定。
团状模塑料(BMC) 的流动特性和绝缘及阻燃性极好,对于细节和尺寸要求精确的各种应用非常适用。
常见注塑成型缺陷成因及解决办法
常见注塑成型缺陷成因及解决办法不正确的操作条件,损坏的机器及模具会产生很多成型缺点,下面提供了一些解决的方法供参考。
为了减少停机的时间,及能尽快找出操作问题的原因,操作人员应把所有最好的注塑机型条件记录在“注塑成型条件记录表”上,以供日后解决问题时参考之用。
(1)成品不完整故障原因处理方法塑料温度太低提高熔胶筒温度射胶压力太低提高射胶压力射胶量不够增多射胶量浇口衬套与射嘴配合不正,塑料溢漏重新调整其配合射前时间太短增加射胶时间射胶速度太慢加快射胶速度低压调整不当重新调节模具温度太低提高模具温度模具温度不匀重调模具水管模具排气不良恰当位置加适度排气孔射嘴温度不低提高射嘴温度进胶不平均重开模具溢口位置浇道或溢口太小加大浇道或溢口塑料内润滑剂不够增加润滑剂背压不足稍增背压过胶圈、熔胶螺杆磨损拆除检查修理射胶量不足更换较大规格注塑机制品太薄使用氮气射胶(2)制品收缩故障原因处理方法模内进胶不足熔胶量不足加熔胶量射胶压力太低高射压背压压力不够高背压力射胶时间太短长射胶时间射胶速度太慢快射速溢口不平衡模具溢口太小或位置射嘴孔太细,塑料在浇道衬套内凝固,整模具或更换射嘴减低背压效果。
料温过高低料温模温不当整适当温度冷却时间不够延冷却时间蓄压段过多射胶终止应在最前端产品本身或其肋骨及柱位过厚检讨成品设计射胶量过大更换较细的注塑机过胶圈、熔胶螺杆磨损拆除检修浇口太小、塑料凝固失支背压作用加大浇口尺寸(3)成品粘模故障原因处理方法填料过饱降低射脱压力,时间,速度及射胶量射胶压力太高降低射胶压力射胶量过多减小射胶量射胶时间太长减小射胶间时料温太高降低料温进料不均使部分过饱变更溢口大小或位置模具温度过高或过低调整模温及两侧相对温度模内有脱模倒角修模具除去倒角模具表面不光滑打磨模具脱模造成真空开模或顶出减慢,或模具加进气设备注塑周期太短加强冷却脱模剂不略为增加脱模剂用量(4)浇道(水口)粘模故障原因处理方法射胶压力太高降低射胶压力塑料温度过高降低塑料温度浇道过大修改模具浇道冷却不够延长冷却时间或降低冷却温度浇道脱模角不够修改模具增加角度浇道衬套与射嘴配合不正重新调整其配合浇道内表面不光或有脱模倒角检修模具浇道外孔有损坏检修模具无浇道抓销加设抓销填料过饱降低射胶量,时间及速度脱模剂不足略为增加脱模剂用量(5)毛头、飞边故障原因处理方法塑料温度太高降低塑料温度,降低模具温度射胶速度太高降低射胶速度射胶压力太高降低射胶压力填料太饱降低射胶时间,速度及剂量合模线或吻合面不良检修模具锁模压力不够增加锁模压力或更换模压力较大的注塑机(6)开模时或顶出时成品破裂故障原因处理方法填料过饱降低射胶压力,时间,速度及射胶量模温太低升高模温部份脱模角不够检修模具有脱模倒角检修模具成品脱模时不能平衡脱离检修模具顶针不够或位置不当检修模具脱模时局部产生真空现象开模可顶出慢速,加进气设备脱模剂不足略为增加脱模剂用量模具设计不良,成品内有过多余应力改良成品设计侧滑块动作之时间或位置不当检修模具(7)结合线故障原因处理方法塑料熔融不佳提高塑料温度、提高背压、加快螺杆转速模具温度过低提高模具温度射嘴温度过低提高射嘴温度射胶速度太慢增快射胶速度射胶压力太低提高射胶压力塑料不洁或渗有其它料检查塑料脱模油太多少用胶模油或尽量不用浇道及溢口过大或过小调整模具熔胶接合的地方离浇道口太远调整模具模内空气排除不及增开排气孔或检查原有排气孔是否堵塞熔胶量不足使用较大的注塑机太多脱模剂不用或减少脱模剂微注塑整理,转载需注明来源,未注来源将视为侵权。
注塑缺陷原因分析与解决方案
注塑缺陷原因分析与解决方案一、引言注塑是一种常见的塑料加工方法,广泛应用于各个行业。
然而,在注塑过程中往往会浮现一些缺陷,如短射、气泡、热缩等。
本文将对注塑缺陷的原因进行分析,并提出相应的解决方案,以匡助企业提高产品质量和生产效率。
二、注塑缺陷原因分析1. 短射短射是指注塑过程中无法将塑料彻底填充模具腔体的现象。
短射的原因可能包括以下几点:- 模具设计不合理:模具的流道设计不合理或者过小,导致塑料无法充分流动。
- 注塑参数设置不当:注塑机的注射速度、压力等参数设置不当,影响了塑料的充填性能。
- 塑料材料选择不当:选择的塑料材料流动性差,导致无法充分填充模具腔体。
2. 气泡气泡是指注塑制品中浮现的气体会萃的现象。
气泡的原因可能包括以下几点:- 塑料材料含水量高:塑料材料含水量高会在注塑过程中产生蒸汽,形成气泡。
- 注塑机排气不畅:注塑机排气系统不畅,无法及时排出注塑过程中产生的气体。
- 模具设计不合理:模具中存在死角或者过小的通气孔,导致气体无法顺利排出。
3. 热缩热缩是指注塑制品在冷却后发生尺寸变化的现象。
热缩的原因可能包括以下几点:- 注塑温度过高:注塑温度过高会导致塑料在冷却后收缩过大。
- 模具温度不均匀:模具的温度分布不均匀,导致注塑制品冷却不均匀,进而引起热缩。
- 塑料材料热性能不稳定:选择的塑料材料热性能不稳定,导致注塑制品在冷却后发生尺寸变化。
三、注塑缺陷解决方案1. 短射解决方案- 模具设计合理化:优化模具的流道设计,增加流道的截面积,确保塑料能够充分流动。
- 注塑参数优化:根据塑料材料的特性,合理设置注塑机的注射速度、压力等参数,保证塑料充填模具腔体。
- 选择合适的塑料材料:根据产品的要求,选择流动性好的塑料材料,提高充填性能。
2. 气泡解决方案- 塑料材料干燥处理:在注塑过程前,对塑料材料进行干燥处理,降低含水量,减少气泡的产生。
- 注塑机排气系统改进:优化注塑机的排气系统,增加排气孔的数量和大小,提高排气效果。
- 1、下载文档前请自行甄别文档内容的完整性,平台不提供额外的编辑、内容补充、找答案等附加服务。
- 2、"仅部分预览"的文档,不可在线预览部分如存在完整性等问题,可反馈申请退款(可完整预览的文档不适用该条件!)。
- 3、如文档侵犯您的权益,请联系客服反馈,我们会尽快为您处理(人工客服工作时间:9:00-18:30)。
造成的缺陷
好,
花斑
1.注塑机压力、 速度不够
1.模具分形面不平整 1.模具温度太低,
2.模具型腔壁厚不均 2.注射压力太低,
3.模具排气不顺
3.注射速度太快,
4.模具内有残余气 4.注射位置太快,
体,
将排气孔堵死。
1.重、轻钙和玻纤要进行 1.适当增大储料背压 1.改善模具分形面 1.升高模温(控制在160℃~
BMC缺陷分析及解决方法
缺陷
定义
材料
分析
设备
模具
工艺
材料
解决方法
设备
模具
工艺
气孔
是由于注射成型 时,气体不能够 顺利的排出而形 成的。
1.材料玻纤、 CaCO3中含有水分 2.料的流动性不 好
1.螺杆背压太 低,2.储料速度 过快,3.料筒温 度太低,
由于模具温度过 1.引发剂的高温
高而对产品表面 与低温配比不
2.脱模剂分散不 均3.团料塑化时
、镀铝的隔离膜 间不够。
。
1.顶出机构不均 衡,或顶出机构 压力太大、速度 太快。
1.储料背压不 够,2.注塑机压 力不够3.料筒温 度太低,4.喷嘴 受损,跑料
1.模具表面温度不均 1.顶出压力太大,
2.模具型腔壁厚不均 2.固化速度不均,
3.模具表面不平整 3.产品叠放太多压
比。(模具型腔厚度较薄 可增加最大注射压力 差控制在5℃以内)
、结构简单选用5:5的配 (最大注射压力应在 2.改善模具型腔厚度,
比;模具型腔较厚、结构 140KN以上)。
使其均衡(厚度:2mm
复杂选用7:3的配比)
~2.5mm)。
由于产品固化不 1.材料中含有水 均而造成局部收 分2.玻纤含量较 缩应力开裂。或 低, 是因脱模困难而 造成拉裂、顶裂 开裂 。
48h以上。
℃~35℃之间
4.将模具设置为抽真空 4.分担注射位置(如位置:
模具。
15、10、5改25、15、5)
1.模具表面的温度不 1.模具温度太高。 均 2.模具型腔厚度不够 均衡,
1.根据产品的不同厚度及 1.增加一个续压设备 1.改善模具水路,使其 1.适当降低模温(160℃~
模具构造,选定不同的配 2.改用大型号的注塑机 表面温度均衡(模芯温 180℃)之间。
大型号的注塑机
4.修复或更换浇口道
3.适当增加料筒温度
(控制在25℃~35℃)
4.修复或更换喷嘴
1.增大注射压力(120KN~ 140KN)、速度 (70~99) 2.增加储料位置 3.升高模具温度(160℃~ 180℃)之间。
1.PS聚集模具表面 1.材料中增加BPIB,可减 太多,滴落在产品 少PS的溢出。 表面。
注射时,料不能 1.料的流动性不 够将模具填满而 好2.固化剂含量 造成的缺陷。 过量
欠注
由于团料中的 1.PS易受高温溢
PS(苯乙烯)遇 出
拉丝/ 胶印
高温溢出而聚集 在模具表面,在 开模时,PS滴落
在产品表面而造
成的缺陷
在成型时硬脂酸 1.脱模剂的含量
锌受热溢出,残 过高。
油斑留在产品表面形 成源自层难以喷漆1.每天清理模具表面两次以 上
1.喷漆、镀铝之前 未进行表面处理。
1.调节脱模剂的含量(含 量≦1%) 2.搅拌时间增长(25min ~40min之间) 3.增加塑化时间(48h以 上)
1.喷漆、镀铝之前需进行表 面处理(如:火焰处理、紫 外线处理、等离子处理)
4.滑块磨损,
裂。
5.顶针太长,
4.撞击开裂
6.脱模斜度不够,
1.重、轻钙和玻纤要进行 1.调节顶出机构平衡性 1.改善模具水路,使其 1.降低顶出压力 (控制在50
烘烤(使其水分控制在 2.降低顶出机构的压力 表面温度均衡 (模芯 ~80之间)、速度(控制在
0.2%以下)。
(控制在50~80之间) 温差控制在5℃以内) 20~35之间)
3.要求产品不能叠放 4.提高包装要求,避免撞击
开裂
1.模具排气不顺
1.注射压力、速度
2.模具分形不够平整 不够,
3.模具内有残余气体 2.储料太少,
4.浇口道受损
3.模具温度太低
1.调节固化剂的配比
1.适当增大储料背压 1.增加排气。
(应控制在10~20之间) 2.改善模具分形面。
2.增加续压设备或改用 3.采用抽真空模具。
2.增加玻纤的含量(玻纤 3.降低顶出机构的速度 2.改善模具型腔厚度, 2.降低开裂部位的固化速度
的含量应控制在15%~20% (控制在20~35之间) 使其均衡(厚度:2mm (电加热模具可降低此处模
之内)。
~2.5mm)。
温或增加此处壁厚;而油温
3.模具表面进行抛光 加热模具可增加此处壁厚)
4.滑块进行修复 5.调整顶针长度 6.增加脱模斜度
烘烤,使其水分控制在 (应控制在10~20之间) 2.尽量调整产品壁厚使 180℃之间)
0.2%以下。
2.减慢储料速度 ,应 其均衡。
2.增大压力(120KN~
2.团料要在干燥、阴暗, 控制在20~40之间 。 3.增加排气槽:宽度≦ 140KN)
15℃~20℃之间进行塑化 3.增加料筒温度到达25 0.2mm,厚度≦0.5mm。 3.降低速度(70~99)