熔炼工艺操作规程1
熔炼炉工艺操作规程及注意事项

三.注意事项:
2.调整成份的合金加入顺序应合理,同时应注意温度调整。
(1)一些难熔和密度大的元素应先加入,与氧亲合力较大的合金元素则必须在脱氧良好的条件下才能加入,且加入时温度不能太高,以减少烧损。
(2)每次加入合金元素,必须根据加入量而决定升温时间。
3.熔化:
(1)开炉:打开主电源开关,检查电容是否锁定,电力控制旋钮是否在零位,打开调频器“开”按钮约10秒钟,频率达到1500hz,按顺时针方向旋转按钮,缓慢增大频率和电力,直到限制指示灯亮。
(2)维持电力限制,随着炉料的熔化,陆续将未装完的炉料加入在熔化过程中,应及时捅料,防止发生“架桥”。
(3)达到额定电力及全部炉料熔解化清时,检查冷却水排水温度应低于30℃,并应注意覆盖钢水液面。
2,要严格进行脱氧。
3.整个熔炼过程中,除渣5-7次。
4.水冷过的模头必须经过烧烤才能回炉。
5.合金加入前应预热,加入量要严格。
6.严格按设备操作维护要求进行操作维护。
7.熔炼过程中要注意检查炉的情况,防止穿炉。
4.脱氧和调整成分:当炉料化清后,取样分析成分,根据分析结果进行成分调整,先脱氧还是先加合金调整成分,要由具体加入合金种类而定。炉料化清并升温后,即可进行脱氧,先加锰再加单晶硅,或一次加入复合脱氧剂。
5.出钢浇注:停电静置,用造渣剂除净钢渣,并扫清(气吹)干净炉面及出钢口,出钢浇注。
6.停炉:把电力控制旋钮转到“零”位,关掉调频器两分钟后,断电,减小冷却水压力,延缓炉体冷却时间,避免炉衬裂纹。
熔炼炉工艺操作规程及注意事项
一、艺要求:
1.熔炼时间:100kg钢水≤30分钟
2.出炉浇注温度:视铸件大小、壁的薄厚而定,一般比金属熔点(液相线)高80-120℃。
熔炼工安全技术操作规程(7篇范文)

熔炼工安全技术操作规程(7篇范文)第1篇熔炼工安全技术操作规程1、上班时穿戴好安全帽、面罩、手套、护脚等劳保用品,严禁酒后上班。
不允许无关人员进入工作场地.2、值班期间严格遵守对设备的检查制度,密切注意仪器仪表显示的参数值是否正常,并填入巡检表。
值班人员必须严格遵守交接班制度,如实填写表格和交接班记录。
3、值班期间严禁脱岗,睡岗,不干和工作无关的事,严格遵守操作规程,上班期间保持手机开启.4、禁止私下改动操作屏参数,要改动须办理审批手续,由维修人员进行。
进入地下室检查时禁止乱动电器开关及各水系统开关。
5、开炉前确保清除炉坑周围的所有障碍物,不准堆放易燃易爆物品。
工作场地、炉前坑及炉底不得有积水.6、工作时不允许将密闭的盒子、箱子和管类炉料以及任何潮湿炉料加入电炉.7、在烧结时加入的炉料应防止搭桥。
烧结过程中禁止用铁棍等捅截正在融化中的炉料。
8、出铁水时和罐炉时要穿戴好手套、眼镜等防护用品。
并等周围人员撤离到安全位置。
操作时集中注意力,严禁错按按纽。
严格控制倾炉高度,铁水流速不要过大,铁水倒入包内不要太满,要控制在离出铁口15㎝左右,铁水快接近至规定位置时应减速,控制好倾炉高度.9、放包人员必须将铁水包放在指定位置,如放包位置不准,倾炉人员有权拒绝倾炉.10、送电档次在较大档时,倾炉人员不得大幅度倾炉,如要倾炉,须要降低电压档次,方可进行倾炉.11、倾炉时要检查电炉出铁口有无凝结堵塞,一旦堵塞处被铁水熔化而倾炉过猛,将会引起铁水喷出引发事故。
12、发现出铁口凝结时,必须用专用工具清除。
清除时要注意保持身体重心,以防跌倒。
13、出铁水、测温、扒渣等靠近电炉工作时不得随身携带手机、打火机等物品。
工作时戴好口罩、眼镜等劳保用品。
扒渣时禁止用空心铁管或潮湿物件,应用专用工具。
14、上班刚开始使用的浇包,出铁水人员须检查其内部是否有异物。
15、取样化验时样勺要先烘干。
16、出现紧急情况时头脑要清醒,不可慌乱,在认真处理的同时迅速报告领导以防问题扩大。
熔炼工序操作规程
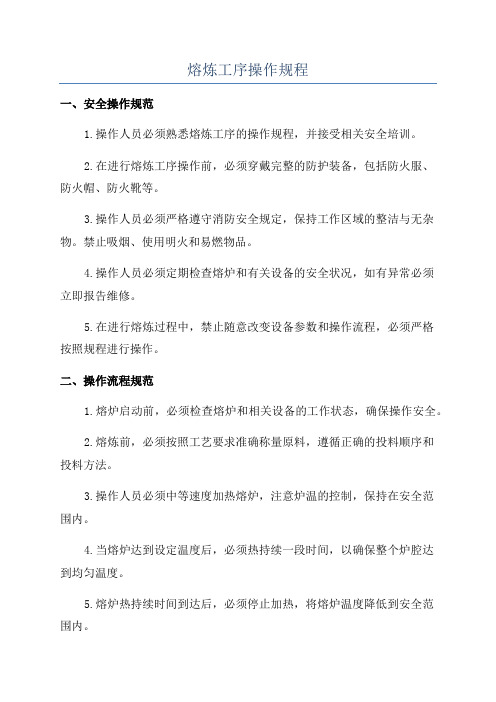
熔炼工序操作规程一、安全操作规范1.操作人员必须熟悉熔炼工序的操作规程,并接受相关安全培训。
2.在进行熔炼工序操作前,必须穿戴完整的防护装备,包括防火服、防火帽、防火靴等。
3.操作人员必须严格遵守消防安全规定,保持工作区域的整洁与无杂物。
禁止吸烟、使用明火和易燃物品。
4.操作人员必须定期检查熔炉和有关设备的安全状况,如有异常必须立即报告维修。
5.在进行熔炼过程中,禁止随意改变设备参数和操作流程,必须严格按照规程进行操作。
二、操作流程规范1.熔炉启动前,必须检查熔炉和相关设备的工作状态,确保操作安全。
2.熔炼前,必须按照工艺要求准确称量原料,遵循正确的投料顺序和投料方法。
3.操作人员必须中等速度加热熔炉,注意炉温的控制,保持在安全范围内。
4.当熔炉达到设定温度后,必须热持续一段时间,以确保整个炉腔达到均匀温度。
5.熔炉热持续时间到达后,必须停止加热,将熔炉温度降低到安全范围内。
6.停炉后,必须按照工艺要求将熔融物料倒出,注意倒出过程中的安全操作,避免烫伤。
7.倒出后,必须迅速将熔融物料移动到指定的冷却区,并按照规程进行冷却。
8.冷却完成后,必须根据工艺要求对冷却物料进行检查,并记录相关数据。
9.操作完成后,必须及时清理工作区域,彻底清除残留的熔融物料和垃圾。
三、紧急情况处理规范1.在熔炉操作过程中,如发现温度异常升高或其他异常情况,必须立即停止操作并报告上级或应急管理人员。
2.在熔炼过程中,如发生火灾、爆炸等紧急情况,必须立即按照应急预案进行紧急处理。
3.在紧急情况下,必须迅速组织人员疏散,并按照应急预案进行消防救援工作。
四、设备维护规范1.每次操作结束后,必须对熔炉和相关设备进行清洁和维护,确保其正常工作。
2.定期检查熔炉和有关设备的状况,如有异常及时维修或更换。
3.对熔炉和有关设备进行定期润滑,以保持其良好工作状态。
4.遵循设备使用和维护手册的要求,保证设备的安全性和可靠性。
五、责任分工规范1.熔炉操作人员必须熟悉相关知识和技能,并定期接受培训。
熔炼操作规程
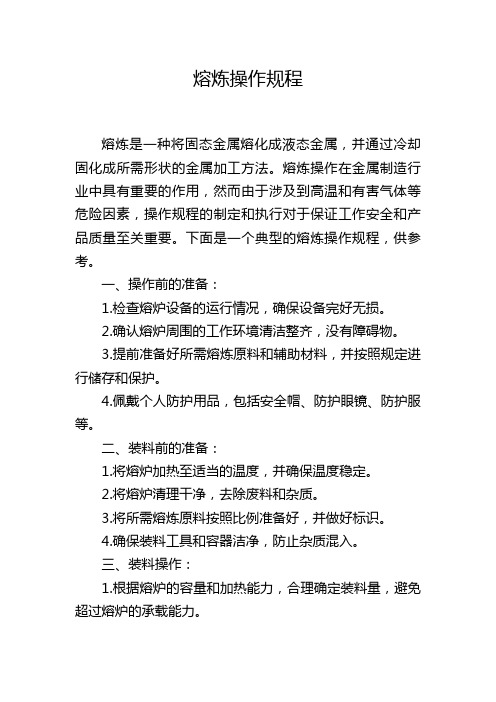
熔炼操作规程熔炼是一种将固态金属熔化成液态金属,并通过冷却固化成所需形状的金属加工方法。
熔炼操作在金属制造行业中具有重要的作用,然而由于涉及到高温和有害气体等危险因素,操作规程的制定和执行对于保证工作安全和产品质量至关重要。
下面是一个典型的熔炼操作规程,供参考。
一、操作前的准备:1.检查熔炉设备的运行情况,确保设备完好无损。
2.确认熔炉周围的工作环境清洁整齐,没有障碍物。
3.提前准备好所需熔炼原料和辅助材料,并按照规定进行储存和保护。
4.佩戴个人防护用品,包括安全帽、防护眼镜、防护服等。
二、装料前的准备:1.将熔炉加热至适当的温度,并确保温度稳定。
2.将熔炉清理干净,去除废料和杂质。
3.将所需熔炼原料按照比例准备好,并做好标识。
4.确保装料工具和容器洁净,防止杂质混入。
三、装料操作:1.根据熔炉的容量和加热能力,合理确定装料量,避免超过熔炉的承载能力。
2.小心操作,避免熔炼材料的溅 splatter。
3.将装好的熔炼材料均匀分布在熔炉中,避免堆积过高,影响熔炼过程。
4.在装料过程中,要注意防止扭动和摇晃容器,避免熔炼材料泄漏。
四、点火和加热过程:1.点火前,确保熔炉周围没有可燃材料,确保安全。
2.点火时,使用适当的点火工具,保持合适的距离。
3.点火后,逐渐提高炉温,避免过快过热,产生危险或炉温不均。
4.在加热过程中,根据需要调整燃烧器的火焰大小和位置,以保证熔炼温度的控制。
五、熔炼过程的控制:1.在熔炼过程中,要定期检查熔炉的温度、压力和其他参数,确保操作正常。
2.根据产品要求,在熔炼过程中适时加入必要的辅助材料,如助剂、氧化剂等。
3.根据需要,对熔炉进行调温、搅拌等操作,以提高熔炼效果。
4.严禁在熔炉中投入不符合规定的材料,以防止产生有毒气体或其他危害。
六、倾炉和浇注操作:1.熔炉熔化达到要求后,根据工艺要求进行倾炉。
2.在倾炉过程中要小心操作,避免翻溅和烫伤。
3.根据需要进行过滤和脱气处理,以保证铸造品的质量。
熔炼操作规程

1、工艺要求1.1 熔炼时间100kg钢水小于30rain1.2 出炉浇注温度视铸什大小、壁厚薄而定,一般比金属熔点(液相线)高80-120℃1.3 脱氧:一般件为预脱氧+终脱氧;预脱氧剂加入量0.2%锰铁。
0.25~0.3%硅铁。
终脱氧剂加入量0.15~0.2%硅钙或0.06~1%铝。
2、操作程序2.1 准备2.1.1 检查炉体情况:炉衬、铜管感应线圈、冷却水管、炉体转动机构等是否正常.炉衬如需修补,应先修补好。
2.1.2 检查电源电压和电器控制系统是否正常。
2.1.3 准备好工具及测温仪表等。
2.1.4 启动冷却水系统检查水压,铜管感应圈冷却水压力不小于0.2Mpa,中频机冷却水压力0.08~0.12Mpa:检查各接头位置及冷却水管道有无渗漏现象,出水部分是否顺畅正常,如有问题及时处理,处理不了的报告给生产主管或维修工迅速解决。
2.2 装料:根据熔炼钢号及炉衬状况,可在炉底加入烧损较少的合金。
然后加入预先洗净的新料。
粗大料和微细料搭配并用,底部垫小料,中部大小搭配,上部加大料.炉料一般不要超过感应线圈高度;长形炉料就竖直装入炉内,并力求做到“下紧上松”。
2.3 熔化2.3.1 送电开炉:将“中频电力”旋转开关按逆时钟方向旋至“零”位后,启动(拉制电力合)按钮,从左侧将630A空气开关往下复到位后再往上推到位,此时在控制面板上的“主电路合”绿色指示灯亮·,再启动“逆变启动”按钮,使“逆变工作”绿色指示灯亮,此时依顺时针方向旋转“中频电力”开关,缓慢增大频率和电力,直至限制指示灯亮。
2.3.2 维持电力限制,随着炉料的溶化,陆续将未装完的料加入.在熔化过程中,应及时捅料,防止发生架桥而引起的爆炸事故。
当发生“架桥”问题时,应及时停电或降低功率开将熔炉倾斜至一定的角度,让下部高温金属熔开“架桥”低温面,当熔开后有气浪喷出或熔渣大量涌出时,则应让气浪喷完或打掉熔渣。
此时应冷静分析熔炉炉龄和熔炉炉衬状况,决定是否继续开炉或废掉熔炉炉衬。
熔炼工安全技术操作规程
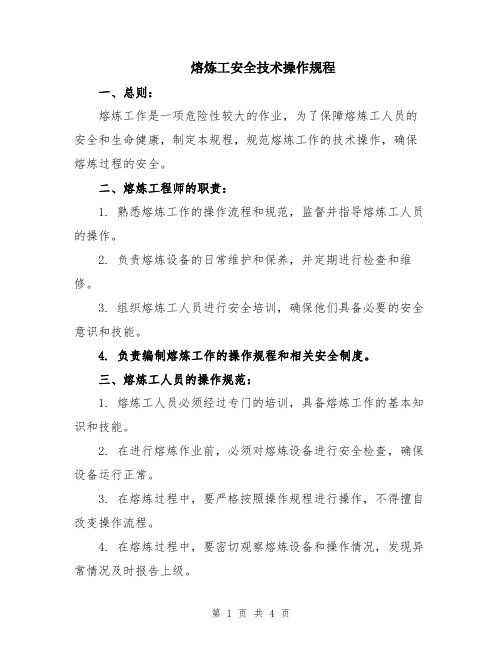
熔炼工安全技术操作规程一、总则:熔炼工作是一项危险性较大的作业,为了保障熔炼工人员的安全和生命健康,制定本规程,规范熔炼工作的技术操作,确保熔炼过程的安全。
二、熔炼工程师的职责:1. 熟悉熔炼工作的操作流程和规范,监督并指导熔炼工人员的操作。
2. 负责熔炼设备的日常维护和保养,并定期进行检查和维修。
3. 组织熔炼工人员进行安全培训,确保他们具备必要的安全意识和技能。
4. 负责编制熔炼工作的操作规程和相关安全制度。
三、熔炼工人员的操作规范:1. 熔炼工人员必须经过专门的培训,具备熔炼工作的基本知识和技能。
2. 在进行熔炼作业前,必须对熔炼设备进行安全检查,确保设备运行正常。
3. 在熔炼过程中,要严格按照操作规程进行操作,不得擅自改变操作流程。
4. 在熔炼过程中,要密切观察熔炼设备和操作情况,发现异常情况及时报告上级。
5. 在熔炼作业结束后,要对熔炼设备进行清理和检查,确保设备的安全。
四、熔炼设备的安全操作:1. 熔炉设备操作前,必须认真查看熔炉操作手册,了解设备结构和操作要点。
2. 确保熔炉设备所需的熔炼材料和催化剂均符合操作要求,并储存在指定的地方。
3. 在投料前,要确保熔炉内无明火和易燃物品,并检查熔炉设备的温度和压力是否在操作范围内。
4. 投料时要注意安全,禁止在运转中的设备中进行操作,禁止使用金属杂质投料。
5. 在熔炼过程中,要定时检查熔炉设备的温度和压力,确保操作在安全范围内。
6. 熔炉设备停机后,要关闭燃气和电源,并注意熔炉残留的高温,禁止近距离接触。
五、事故应急处理:1. 在熔炼作业中,如发生突发事故,应立即向上级报告,并采取相应应急措施。
2. 熔炼作业中因突发事故导致熔炉设备异常停机时,要立即切断燃气和电源,并进行紧急救援。
3. 熔炼作业中发生火灾时,要迅速组织疏散,使用灭火器材进行扑救,如无法控制,要迅速报警和撤离现场。
4. 在处理事故后,要及时进行事故原因的分析和记录,以便总结经验教训,避免类似事故再次发生。
中频炉熔炼操作规程
中频炉熔炼操作规程一、安全作业规定:1.操作前必须参加安全培训,并具备相应的岗位操作证书。
2.操作前应仔细检查熔炼设备及相关工具是否完好,并着装整齐,穿戴防护用品。
3.熔炼过程中不得戏谑、喧哗,禁止吸烟、嚼食、饮酒等。
4.遵守噪声控制规定,如长时间在噪音强度高的环境中工作,需佩戴耳塞或耳罩。
5.若有特殊状况或设备异常,应立即停止工作,并及时向上级汇报。
二、工艺操作规定:1.操作前应熟悉操作工艺流程,并掌握熔炼设备的操作方法。
2.启动炉体前,应先检查变压器是否正常,电流表、电压表等指示器是否准确。
3.启动炉体时,应按照设备操作流程进行操作,必要时可以和上级进行确认。
4.熔炼时应准确掌握加热温度和时间要求,严格按照配料比例进行投料。
5.在操作过程中,应注意观察炉体内的温度变化,及时调节炉体的功率和频率。
6.禁止在炉体有水的情况下投料,以免引发危险。
7.熔炼结束后,应进行炉体停机检查,关闭电源、气源等设备,确保设备安全可靠。
三、设备维护规定:1.操作前应进行设备的日常检查,确保设备正常工作,如发现异常情况,应及时报修。
2.定期对设备进行维护保养,清洁设备表面和通风孔,保持设备干净、整洁。
3.注意保养电缆,检查电缆是否磨损、老化,及时更换。
4.定期对温度计、电流表、电压表等仪表进行检查和校准,确保测量准确可靠。
5.每次停机后,应清理冷却水系统,排除水垢,以保证冷却效果。
四、事故应急措施:1.在发生事故时,要迅速切断电源,停止加热,排除危险因素。
2.遇到故障需及时报修,等待维修人员到场处理。
3.在事故发生后,应及时向上级汇报,做好事故处理记录。
4.工作场所应设有应急出口,保持通畅,以便发生事故时的疏散。
熔炼工安全技术操作规程
熔炼工安全技术操作规程一、前言熔炼工是一项涉及到高温和危险化学物质的工作,因此在进行熔炼工作过程中,必须严格遵守操作规程及安全措施,确保人员和设备的安全。
为此,本文将介绍熔炼工安全技术操作规程,以指导熔炼工在操作过程中做好安全防护工作。
二、熔炼工作前的准备2.1 安全防护装备在进行熔炼工作之前,必须准备齐全的安全防护装备,包括防护眼镜、工作服、手套、面罩、安全鞋等。
这些装备必须符合国家安全标准,能够有效抵御高温、腐蚀和有害气体等危险因素的侵害。
2.2 环境准备在进行熔炼工作之前,必须对工作现场进行环境准备。
首先要将工作场地清理干净,确保场地整洁无垃圾;其次要保持工作场地的通风。
如果有必要,可以通过安装排风系统、使用排风扇等方式来保持室内空气流通,减少空气中有害气体的含量。
2.3 人员准备在进行熔炼工作之前,必须对参与工作的人员进行岗前培训,让他们对本次工作的安全注意事项有所了解。
在培训过程中,应重点介绍各种工作场景下的安全措施和应急处理方法,让工作人员在遇到事故时能够快速、果断地处理。
三、熔炼工作过程中的安全防护3.1 熔炼和混合在进行熔炼和混合过程中,必须严格遵守下列安全要求:•必须使用符合国家标准的加热设备,确保其安全可靠;•在进行熔炼和混合时,必须戴上防护眼镜和手套等防护装备;•必须保持良好的通风状态,避免环境中存在有害气体。
3.2 浇注在进行浇注过程中,必须严格遵守下列安全要求:•浇注之前必须检查设备的密封性能,确保无溢漏情况发生;•提前安排好操作人员的工作位置,确保其不会受到溅出物的侵害;•操作人员必须戴上面罩、工作服、手套等防护装备。
3.3 清理和维护在进行清理和维护过程中,必须严格遵守下列安全要求:•在进行维修和清理时,必须按照设备的说明书进行操作,禁止随意更换或拆卸零件;•不得将有害物质排放到环境中;•在进行清理和维护时,必须戴上防护眼镜、手套等防护装备;•在进行清理和维护时,必须保持好通风状态,减少有害气体的含量。
熔炼工安全技术操作规程范本(2篇)
熔炼工安全技术操作规程范本第一章总则第一条为了确保熔炼工作的安全进行,保障工作人员的生命财产安全,根据国家相关法律法规,制定本安全技术操作规程。
第二条本规程适用于熔炼工作过程中涉及的所有人员,包括操作人员、监管人员、管理人员等。
第三条本规程的内容主要包括熔炼工作的安全要求、操作规范、事故应急救援等方面,以确保熔炼工作安全有序进行。
第二章安全要求第四条熔炼工作必须在符合相关法律法规和技术标准的前提下进行,不得违反安全规定和操作程序。
第五条熔炼工作涉及有毒、有害、易燃、易爆等危险物质的处理,必须经过专人培训并取得相应的操作资格证书后方可从事。
第六条熔炼过程中,必须严格按照操作规程进行,禁止超负荷运行和违规操作。
第七条在熔炼工作现场必须配备相应的安全设施,如防护装备、消防设施等。
第八条熔炼工作人员必须按照规定佩戴和正确使用防护装备,保证个人安全。
第九条熔炼工作涉及危险操作、高温操作和高压操作等,必须由经过培训并熟悉操作规程的操作人员进行。
第十条在熔炼工作现场,严禁吸烟、使用明火和进行其他与作业任务无关的行为。
第三章操作规范第十一条熔炼工作开始前,必须进行现场勘察和安全检查,确保环境安全和设备正常。
第十二条操作人员必须熟悉熔炼工作的相关技术要求和操作规程,遵守操作步骤和流程。
第十三条操作人员必须清楚了解自己所承担的责任和安全风险,并在操作过程中时刻保持警惕。
第十四条在熔炼工作过程中,必须定期检查和维护设备,确保其正常运行。
第十五条在熔炼工作过程中,必须按照操作规程和标准操作,禁止擅自进行改动和修理设备。
第十六条在熔炼工作过程中,必须定期清理清洁作业现场,保持通风畅通。
第四章事故应急救援第十七条熔炼工作现场必须设立应急救援专用通道,并配备相应的安全设备和应急救援物资。
第十八条熔炼工作现场必须设立应急疏散通道,并配备应急疏散指示标识。
第十九条熔炼工作现场必须配备应急救援人员,并进行定期应急演练,加强人员应急救援能力。
熔铸车间操作规程模版
熔铸车间操作规程模版一、熔炼操作规程1. 熔炼操作前的准备工作1.1 检查熔炉设备的运行状况,确保各部件正常工作;1.2 清理熔炉内外的杂物和残渣,保证熔炉干净;1.3 检查熔炉内的炉衬和保温材料,确保其完好无损;1.4 准备好熔化所需的原材料,并按照配比要求进行称量和混合;1.5 将熔炼所需的原材料送至熔炉,并正确装配炉盖和加热设备。
2. 熔炼操作步骤2.1 打开熔炉进气阀,启动熔炉加热设备,将温度调至适宜的熔化温度;2.2 监测熔炉内的温度,确保其在稳定范围内;2.3 适时添加剩余原材料,保持熔池的稳定;2.4 根据需要,进行必要的调温和翻砂操作;2.5 在熔池温度达到要求后,进行温度记录和取样分析;2.6 关闭熔炉进气阀和加热设备,待熔池温度降至安全范围后,开始倒炉操作。
3. 熔炼操作注意事项3.1 操作人员必须穿戴好防护设备,避免直接接触高温部件;3.2 操作过程中禁止随意打开熔炉门,以免引起熔池溅射和烟尘外泄;3.3 熔炉操作时必须保持专注,避免操作失误引发事故;3.4 操作结束后,必须及时清理熔炉内部和周围的残留物,确保安全和环境卫生。
二、铸造操作规程1. 铸造操作前的准备工作1.1 检查铸造设备的运行状况,确保各部件正常工作;1.2 清理铸造机台和模具,确保其干净无油污;1.3 检查铸造机台和模具的温度,确保其处于使用状态;1.4 准备好铸造所需的合金材料,并按照合金比例要求进行配料;1.5 将合金材料送至铸造机台,并按照工艺要求进行合金预热。
2. 铸造操作步骤2.1 启动铸造机台,调整好合适的压力和速度;2.2 放入预热好的合金材料,密封好铸造腔体;2.3 监控铸造过程中的温度和压力,确保其在安全范围内;2.4 根据需要,进行必要的修正和调整操作;2.5 铸造完成后,关闭铸造机台,取出铸件;2.6 对铸件进行外观检查和尺寸测量,确保其符合要求。
3. 铸造操作注意事项3.1 操作人员必须穿戴好防护设备,避免直接接触热模具和熔融合金;3.2 铸造机台运行时,禁止随意触摸和调整机台部件;3.3 铸造过程中严禁超负荷操作,以免引发设备故障和事故;3.4 操作结束后,必须及时清理铸造机台和模具,确保安全和环境卫生。
- 1、下载文档前请自行甄别文档内容的完整性,平台不提供额外的编辑、内容补充、找答案等附加服务。
- 2、"仅部分预览"的文档,不可在线预览部分如存在完整性等问题,可反馈申请退款(可完整预览的文档不适用该条件!)。
- 3、如文档侵犯您的权益,请联系客服反馈,我们会尽快为您处理(人工客服工作时间:9:00-18:30)。
铸轧车间熔炼工艺操作规程本规程规定了使用电解铝水及添加部分废铝打包块、原铝锭的熔炼工艺及操作要求。
一、设备主要技术参数1、熔炼炉主要技术参数表1、熔炼炉主要技术参数二、装炉前的准备2、装炉前应检查硅碳棒有无断裂现象,如发现应立即更改。
熔炼过程中一般不允许更换硅碳棒,严防硅碳棒落入熔体中。
特殊情况必须更换时应采取相应的保护措施。
3、装炉前必须清炉,须将炉底、炉角、炉墙各处的渣子及其它脏物彻底清除干净,否则不得装炉。
4、严格核对炉料是否与生产卡片相符,确认无误后方可装炉。
若发现卡片记载与实际炉料不符时,应经配料计算者或技术主管同意后方可更换料,并在生产卡片上注明更改情况,记录新投入料的类别和重量。
5、生产铝箔毛料时,清炉后、装炉前,在炉底均匀撒入20±2㎏粉状溶剂。
三、装炉及灌炉6、装炉工艺操作程序及注意事项6.1易烧损的废料(如薄板、铝箔打包块等)应均匀装在下层,原铝锭、复化锭应均匀地装在上层,料必须一次性装完,如有中间合金,必须在同时一次性加入。
6.2、应根据不同合金先加入30%-50%的废料或铝锭,然后关闭炉门升温,熔炼炉设定温度880℃、6.3、装炉时,金属添加剂不允许与铝锭、中间合金及废料一同加入。
6.4、装炉时熔炼操作人员应检查炉料的外观质量,发现异物应挑出、清除,发现含有其它金属的打包块不许装炉,应予以更换,过磅并做好记录。
7、灌炉工艺操作程序及注意事项7.1铝包车运输铝水到铸轧车间熔炼炉炉台后,应有专人负责指挥天车把真空包吊运至地磅过磅,要轻吊慢放轻摘钩,并认真做好称重记录,要求字迹清晰,不许涂改。
7.2倒包工应首先检查敞口包倒顺开关是否处于停止状态,确认无误后,指挥天车按指定的位置配合炉前工将铝水倒入敞口包内。
7.3打渣工向敞口包撒入10~15㎏打渣剂,然后开始搅拌,搅拌5~8分钟,搅拌要均匀,确认无误后,检查打渣扒渣的漏勺是否烘烤加热,确认无误后,开始打渣、捞渣,打渣时应先用漏勺将敞口包的渣子向一块集中,然后用漏勺把渣子捞出。
打渣时漏勺应先在敞口包上停留5~10秒,待铝液全部流尽后才将渣子捞出,并应扒开炉渣以防铝液及炉渣燃烧,冷却后扒入渣箱内。
7.4捞渣完毕后,指挥天车工吊起敞口包,按指定的炉号对准炉口,倒包工再次检查倒顺开关是否处于停止状态,确认无误后合闸,倒包工按住到顺开关按钮,将其打到正转位置,根据铝水流量控制流速。
7.5灌炉完毕后,熔炼工对敞口包进行清渣,清渣必须要彻底,清渣完毕后,指挥天车工把敞口包吊回原处。
四、熔炼8、升温熔化时间的控制8.1熔炼炉炉膛温度定温880℃.8.2待装入的铝锭、打包块等废料熔化后,应均匀地撒入一层干燥的粉状溶剂进行覆盖,用量以完全覆盖熔体表面为原则,一般为15±2㎏。
8.3如发现还有炉料爬底时,应轻轻推搅,加速金属熔化,防止金属局部过热。
8.4熔炼温度应符合表2之规定表2 金属熔炼温度9、扒渣9.1测温,并在熔炼温度范围内扒去熔体表面的浮渣。
9.2扒渣前5-10分钟,均匀地撒入一层干燥的粉状溶剂进行覆盖,用量以完全覆盖熔体表面为原则,一般为15±2㎏。
9.3扒渣时要平稳,不能用金属浪推渣,将渣子推到炉门口稍停后,再扒出炉外,应做到扒渣净、渣中金属少。
9.4扒渣结束,均匀地撒入一层干燥的粉状溶剂进行覆盖,用量以完全覆盖熔体表面为原则,一般为15±2㎏。
10、金属添加剂的加入10.1扒渣结束后,测温,当熔体温度达到表3的温度时,将准备好的金属添加剂用加料铲均匀加入到熔炼炉的熔体中。
表3 加入金属添加剂时的熔体温度10.2金属添加剂加入前,必须将包装箱、包装袋扒掉(防潮膜可以不扒),扒包装袋时应用铝盒或铁锨盛接,以防粉状添加剂散失而减少添加量。
10.3添加剂加入熔炼炉熔体后,静置45±5分钟,使其充分熔解。
11、搅拌11.1取样前,熔体应进行充分搅拌,搅拌时间不得少于15分钟。
11.2添加金属添加剂时,熔体温度达到730℃以上,才能开始搅拌。
11.3搅拌时要求对流操作,平稳、均匀不起大波浪,搅拌器不得露出液面。
11.4搅拌结束,静置10分钟以上,开始取样。
12取样和成份调整12.1取样勺应充分预热,并按合金分开使用。
12.2快速分析试样分别在两个加料炉门中间熔体深度二分之一处选取。
12.3取样后立即测温,并校正仪表。
所有合金取样终了温度不应低于熔炼温度下限。
12.4试样打上合金牌号、炉号、熔次号与熔炼生产卡片一起送到化验室快速分析。
12.5根据化学成份快速分析结果,按合金成份调整标准、生产卡片工艺要求调整成份。
12.6化学成份超合金成份调整标准上限时,要用原铝锭进行冲淡。
12.7化学成份超合金成份调整标准下限时,要用金属添加剂、中间合金进行补料。
12.8补料、冲淡重量由班长(主操作手)按合金成份调整范围的中间值(8011合金的si含量按上限值)计算确定,工艺特殊要求,按生产卡片工艺要求执行。
12.9冲淡、补料计算公式冲淡量﹦投料量(1-烧损)×(分析含量—目标含量)÷(目标含量-原铝水中的元素含量)补料量﹦投料量(1-烧损)×(目标含量—分析含量)÷(添加剂中的元素含量×实收率-目标含量)补料量﹦投料量(1-烧损)×(目标含量—分析含量)÷(中间合金中的元素含量-目标含量)实际计算时:a.烧损:按0%计算b.实收率:金属添加剂按100%计算c.最小重量单位:原铝锭为1㎏;金属添加剂和中间合金为0.5㎏.12.10冲淡计算时,首先计算冲淡超标元素所需原铝锭的重量,其次计算加入原铝锭后对其它金属元素的影响,需要补料时计算补料量。
12.11补料计算时,首先计算补料超标元素所需中间合金或金属添加剂的重量,其次计算加入中间合金或金属添加剂后对其它合金元素的影响,需要补料时计算补料量。
12.12冲淡、补料时,将准备好的原铝锭、中间合金、金属添加剂用加料铲或铁锨均匀加入到熔炼炉的让他中。
12.13冲淡、补料结束,质检员或班长将实际加入量记录在生产卡片上。
12.14冲淡量超过150㎏时,必须重新取样分析。
12.15 8011合金,金属添加剂Cu、Mn中单个补料量超过2.5㎏,金属添加剂Fe的补料量超过4㎏时或AI-Si中间合金超过16㎏时,必须重新取样分析。
12.16其它合金,金属添加剂中单个补料量超过6㎏或AI-Si中间合金超过22㎏时,必须重新取样分析。
12.17其他情况是否取样,由当班班长确定。
13、所有熔炼工具应保持洁净、干燥,严禁将水携入熔体中,以防爆炸。
14、熔体保温时间的控制14.1生产1070、1060、1145、1235等纯铝时,正常情况下,从取样到倒炉,时间不得超过两个小时。
14.2生产1100、8011、3003等合金时从取样到倒炉,正常情况下时间不得超过三个小时。
14.3生产所有合金,正常时从成份调整完毕到倒炉,一般不超过一小时,最长不超过2小时。
14.4特殊情况,须经主管人员同意,并在生产卡上注明。
15、熔炼炉精炼15.1精炼范围15.1.1生产箔材毛料、质量要求高的板带材时;15.1.2当打包块废料,复化锭超过投料量的50%时。
15.2对精炼的规定15.2.1每熔次在导炉前(本公司)采用四氯化碳进行精炼。
15.2.2精炼温度a.1××× 8×××合金在720-740℃之间;b.3×××合金在730-750℃之间。
15.2.3精炼时间:13-15分钟。
15.3使用四氯化碳时的精炼操作15.3.1作载体的轻质粘土砖必须在250-300℃的温度下干燥5小时以上,然后放入四氯化碳液体内浸泡,待砖沉底后,方可使用。
15.3.2先将精炼器放入炉膛内烘干预热,然后放入载体的轻质粘土砖,最后将精炼器插入熔体中。
15.3.3精炼前先打开排烟机。
15.3.4精炼时,精炼器在炉底平稳、缓慢、均匀地移动,不能有死角。
15.3.5精炼完毕后,扒出表面浮渣,然后撒入粉状溶剂覆盖,用量以完全覆盖熔体表面为原则,一般为15±2㎏。
16、对精炼后的熔体进行含气量测定,含气量超过规定时,应重新精炼。
五、导炉17、熔体成份合格,温度合适即可导炉。
18、导炉时若炉底不平有剩料时,则以自动流出为准;但合金转组时,必须将剩料推出或扒出。
19、导炉时,熔炼炉内熔体温度控制在740-760℃之间,具体温度由铸轧当班班长(操作手)决定,但纯铝导炉瞬间温度不得超出755℃,测温时电偶顶端应插在距离金属液面150-200㎜处的熔体中,待稳定后读数。
20、特殊情况下,短时间不能导炉时,可调整好成份,炉膛定在730℃以下保温,并用溶剂覆盖;若保温时间超过3小时,导炉前须重新搅拌、扒渣。
21、连续生产相同合金时,正常情况下,静置炉中熔体少于2吨,由铸轧班班长同意并在生产卡片上签字后方可导炉。
生产不同合金时,不能连续导炉,若遇特殊情况,须请示主管技术人员同意后执行。
六、清炉及大清炉22、熔炼炉每熔次导炉后,在下熔次装炉前,必须彻底清炉。
22.1清炉时,用三角铲把炉墙、炉角、炉底的渣子彻底铲净,扒出。
22.2清炉后,渣线以下不应有凸出物。
23、熔炼炉在下列情况下应进行大清炉。
23.1生产纯铝时,每10±1熔次大清炉一次;23.2生产合金时,每5±1熔次大清炉一次;23.3合金转组时,进行大清炉,并扒出残留金属。
24、大清炉时,先将炉内残留金属放干,把炉渣彻底清除,然后撒入20±2㎏粉状溶剂,并将炉温升至800℃以上,用三角铲把炉墙、炉角、炉底的渣子彻底铲净,扒出。
七、熔炼周期25、正常生产中,投料少于10吨,熔炼周期不大于9.5小时,投料大于10吨,熔炼周期不大于10.5小时。