8D报告模板及实例
8D报告模板

实施时间
D6-第六步骤:执行及验证永久对策
7. 对策确认
Y
N
Y
N
D7-第七步骤: 防止再发。
8.跟踪措施
考慮事项
Yes/No
实施时间
实施部门
工序作业/检查指导书
Y
过程流程图
N
质量保证标准
N
控制计划 / 控制图
N
F.M.E.A. / A.M.D.E.C.
N
图纸
N
量规
N
其他 (調査, 防错)
NБайду номын сангаас
二级供应商跟踪
防止再发生对策报告书―8D
编号:
D1-第一步骤:建立解决问题小组
组长:
组员:
D2-第二步骤: 描述问题
康普结构件生产不稳定:
1、
2、
1 问题详情
图号
7659084
名称
腔体/盖板
发生地(或现场)
问题分类
数量(分子/分母)
发生日
再发不良
N
N
受影响的数量
(或追溯)
2. 向类似零件的展开
该问题在其他零件上发生过吗?
4.临时对策–立即的
组织相关人员针对此问题开现场分析会。
考虑事项
处置
OK数
NG数
在制品
中间在库品(半成品)
仓库存品
服务备件
其他
首批交付合格部品如何特殊标识/标记 ?
标牌
D4-第四步骤: 找出问题真正原因
5最终分析
时间
原因
责任部门
生产管理部
生产管理部
D5-第五步骤: 选择永久对策
6.永久対策
8d报告完整版范文3篇
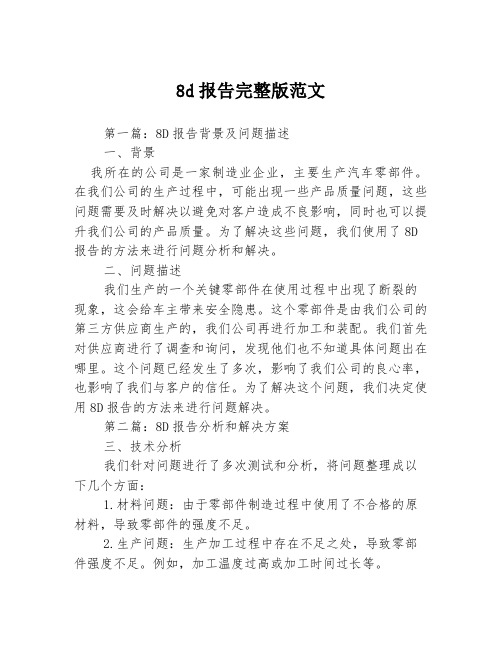
8d报告完整版范文第一篇:8D报告背景及问题描述一、背景我所在的公司是一家制造业企业,主要生产汽车零部件。
在我们公司的生产过程中,可能出现一些产品质量问题,这些问题需要及时解决以避免对客户造成不良影响,同时也可以提升我们公司的产品质量。
为了解决这些问题,我们使用了8D 报告的方法来进行问题分析和解决。
二、问题描述我们生产的一个关键零部件在使用过程中出现了断裂的现象,这会给车主带来安全隐患。
这个零部件是由我们公司的第三方供应商生产的,我们公司再进行加工和装配。
我们首先对供应商进行了调查和询问,发现他们也不知道具体问题出在哪里。
这个问题已经发生了多次,影响了我们公司的良心率,也影响了我们与客户的信任。
为了解决这个问题,我们决定使用8D报告的方法来进行问题解决。
第二篇:8D报告分析和解决方案三、技术分析我们针对问题进行了多次测试和分析,将问题整理成以下几个方面:1.材料问题:由于零部件制造过程中使用了不合格的原材料,导致零部件的强度不足。
2.生产问题:生产加工过程中存在不足之处,导致零部件强度不足。
例如,加工温度过高或加工时间过长等。
3.设计问题:设计过程中没有考虑到应力分布的均匀性,导致零部件在使用过程中容易产生应力过大的现象。
四、解决方案1.材料问题:我们将与供应商重新协商并重新规定原材料标准,以保证原材料的质量。
2.生产问题:我们将对生产过程进行检查和测试,改进加工温度和加工时间,并进一步探究生产中存在的不足之处,以最大程度地提高相关生产能力。
3.设计问题:我们会重新设计零部件,考虑应力分布的均匀性,并对原有零部件进行更加严格的测试和分析以验证新设计的可行性。
第三篇:8D报告措施计划和预防五、措施计划1.与供应商合作并重新规定原材料标准。
2.对生产过程进行检查和测试,并改进加工温度和加工时间。
3.重新设计零部件,考虑应力分布的均匀性,并进行严格的测试和分析。
4.对生产和供应链流程进行跟踪和监控,确保问题不再发生。
8D报告实例

D4根本原因分析-Root Cause
分析原因时,团队的力量就显现出来,通过4M1E、5W2H方法以及一些QC手 法结合现场、现物、现状的实际,对原因做鱼刺图,人机料法环逐等。
D5&D6 預防措施-Corrective Action
一般性對策:1.對相關人員進行教育培訓,ETA: 2.更換對應的治具和零件 3.SOP中增加對應的動作
问题产生的主因 端铣刀D1.5断刀 验证发现1710、1711、 CNC4更换端铣刀 1712这三台机经排查, D1.5靠近刀寿的 刀具有磨损,导致尺寸 刀具,共15把 偏下限 已于3/5改善 完毕 DRI: 孙理想 1.端铣刀D1.5易断刀具作业人员每2H 自检一次 2.发现不良根据机台号,立即向前追踪 2H的物料,共18pcs 每天持续 DRI: 孙理想 短期改善对策 长期改善对策
Action
排查相應風險點,并改善 [3/10]ME分析出相關風險點,待FATP回復相關對策 FAE機台返CP點,增加檢驗外觀螺絲相關動作 確定無塵室5S和潔淨度是否達標,并提供相關數據 針對WK09&WK10周CG Frame PSA DPPM有上升,持續改善 [3/10]FATP&OQC&PT 上線排查風險點 PT 提供改善報告 重新對STOM站位人員進行教線 [3/11]ME已經重新對STOM站位人員進行教線
DRI
PT:Yue He ME:Sanvier_Hu FATP:Mingking Wang FATP:Mingking Wang Pack:Jiangwei Fu PT:Livi Liu Pack:Jiangwei Fu FATP:Mingking Wang Xiaolong Shi PT:Livi Liu PT:Yue He ME:Sanvier_Hu
变压器8D报告(骨架pin距尺寸偏小)实例

Report Finish Date Verify date Approved date
2020.01.13
Owner(责任 人)
Due day(完成日期)
2020.01.13
Root cause analysis(根本原因分析):
根本原因:插 PIN 刀模钝剉,切pin过程中将CP线强制性内拉切断,切断过程中pin尖顶部受力导致倾斜,调机自检手法有 误未测量其顶部PIN距,造成不能及时发现问题将其纠正.
D4初步分析及 暂时对策
(Preliminary Analysis & Short
term action)
初步原因: 插pin机调试人员确认样品时,测量pin间距手法存在误区,习惯性整体测量pin距底部,忽略了尖部的pin距.
Short term action(暂时对策)
库存:20k(返工). 在制品:无 客户库存:4455PCS(安排驻厂人员全检后入库).
QA经理 生产部经理 工艺部经理
Name(姓名)
Function(职务) 工程师 主管 高管 高管
Name(姓名)
Problem Analysis (对不良品进行现状 分析)
pin距不良模号为1.2.5,不良部位在pin尖部偏小0.03,尖部pin针内趴造成.
Preliminary Analysis and why why escaped (初步原因分析&不良品外流原因确认):
Failure rate(不良率) How much(产生费 用) Who(客诉类型)
when(发生时间):2020.1.09
where(发生地点): 进料 What(问题描述):1/10入料排距不良
规格:24.5±0.25
8D报告以和案例分析

字模冲子修模时 未依图面配置
跳屑造成迭料
模具
字模高度设计 安全系数尺寸 偏低
字模磨损
材料
材料厚度 0.3±0.01
三. 临时对策:
3.1.对嫌疑品全部重工
在途物流 厂内
sorting日期 11/23 11/24 11/24
不良率 52/18,000= 0.28% 40/9,000= 0.44% 22/61,300 =0.03%
D2: 问题描述
• 从客户观点来描述问题,他们看到什么? 照片or 寄 不良样品回来分析 .
• 阐明全部客户提供之数据. • 涵盖范围 ? Lot No?批号?Date Code?制造日期? • 问题有多严重 ? 不良数?不良率? • 是制造还是设计旳问题 ? 层别法 - 模号? • 阐明规格之要求. • 阐明电子,机械验证,及任何失效分析之成果. • 所报告旳问题是真正旳问题吗?连续问5次为何. 重工, 全检 ,报废 .若要 重工或全检 , 有执行旳原则吗 ?
• 详述检验措施, 措施可行吗?有作有效性验 证吗?
• 紧急对策引起其他问题吗?
• 紧急对策进行中?已完毕? 注意时效.
• 检验/测试/分析成果阐明. 详列检验数,不良 数,不良率.
D4:原因分析
• 详列永久对策旳运营时间表.
D6:效果验证
• 验证紧急对策及永久对策之有效性,应以 量化表达验证成果(如:Cpk值可达1.33, 或不良发生率降至 0 等).
• 在永久对策验证有效之前,应连续进行紧 急对策.
• 追踪永久对策执行后之品质推移情况. • 在没有完全把握问题已彻底处理之前 , 不
要轻率旳结案 .
不良品生产日期
11/4 11/7 11/19,11/20
8D分析报告模板(标)

8D问题分析报告8D问题详细分析报告一、问题及团队1、问题问题名称。
2、团队解决问题的团队成员:具体分工倡导者(负责8D程序进程跟踪及控制、会议召集):文员(负责会议记录、材料汇总及整理):其他成员分工……二、问题描述1、问题的产生是什么、何时、何地、多少、严重程度等方面描述问题。
2、问题的影响详细剖析问题对设备生产、技术工艺、经济效益、管理、公司声誉形象、法律纠纷等的影响。
3、问题涉及的对象和问题的发生有关联或将受到问题的影响的对象,如:客户、政府部门、公司部门和供应商。
三、临时措施为了防止问题的负面影响扩大或者是问题进一步恶化,采取什么临时处置措施(包括应急措施),采取临时措施的依据及标准,何时开始实施临时措施。
及时调查其他地方是否存在类似问题?正常状况应该如何?四、根本原因1、原因查找采用脑力激荡法查找可能原因:团队成员分头去调查问题相关人员,在规定时间汇总可能原因。
相关检测数据及资料收集。
2、原因分析针对汇总的可能原因进行关联分类,并采用鱼骨图法将分类的可能原因表示出来,并针对这些可能原因进行分析验证(查找产生原因的依据数据及资料),去除伪原因,对确定的原因采取5W法(5问法:原因、原因的原因、原因的原因的原因、……)揭示更深层次的原因。
最后用鱼骨图法将分类的真原因表示出来。
生产类问题原因寻找及分析鱼骨图:根据推断,应该或可能是先发生什么,接着发生什么,在什么情况下进一步发生什么,最终导致问题的发生。
4、问题发现机制说明问题是如何发现的,处于什么阶段(隐患阶段、未遂先兆阶段、轻微阶段、严重阶段),分析这种发现方法是否合理?问题是否及时被发现?为什么未能及时发现?五、解决方案1、对问题采取的纠正措施针对每个原因制定解决办法,最后综合成解决问题的方案。
2和制定新解决方案。
七、预防问题再次发生(制度化)1、防止类似问题再次发生根据原因分析及解决方案的验证结果,确定防止此类问题再次发生的方法,制定(或修改、补充)相关制度确保解决方案能够常态化运行(明确制度制定负责人及完成时间),相关制度见附件。
8D报告样本3篇

8D报告样本第一篇:8D报告样本一、问题描述在质量检测过程中,发现某批次产品存在一个严重的缺陷,即产品存在漏电现象,导致安全问题。
该批次产品是用于家庭使用的电视机,漏电问题不仅会影响产品的正常使用,还会对消费者的人身安全造成潜在威胁。
二、立即避免影响1.暂停该批次产品的销售和发货;2.暂停涉及到该批次产品的相关生产线的生产工作;3.通知已经购买该批次产品的消费者停止使用,并为他们提供免费的维修、更换或退货服务;4.成立问题解决小组,立即着手开展问题解决工作。
三、防止再次发生1.重新评估该批次产品所使用的材料的质量,采取更加严格的质量控制措施;2.对所有生产线的工作人员进行安全知识培训,强化产品质量意识;3.加强检验工作,确保产品的质量符合国家和行业标准;4.建立缺陷反馈机制,及时发现并解决潜在缺陷问题。
四、解决方案1.对该批次产品进行召回处理,进行维修、更换或退货处理;2.制定严格的质量控制标准和检测标准,确保产品质量;3.加强生产线工作人员的安全培训,提高其质量意识;4.建立缺陷反馈机制,及时发现和解决潜在的问题。
五、验证方案1.在所有生产线的每一步骤中使用严格的质量标准和检测标准;2.组织定期安全培训,提高员工的质量和安全意识;3.建立缺陷反馈机制,及时处理和解决缺陷问题;4.承担社会责任,让消费者享受到更好的产品和服务。
六、持续改进1.通过不断地优化工艺、提高质量标准和检测标准,提高产品质量;2.加强员工的培训和教育,提高他们的安全和质量意识;3.建立完善的缺陷反馈机制,及时发现和解决问题;4.听取消费者的意见和建议,不断改进产品和服务。
七、结论通过以上的改进工作,我们已经成功地解决了该批次产品的漏电问题,并采取一系列有效的措施,防止类似问题再次发生。
我们将坚持持续改进的原则,为消费者提供更加优质的产品和服务。
第二篇:8D报告样本一、问题描述本次问题为某款产品在使用时出现频繁停机,严重影响用户正常使用体验。
8D报告-8d报告

四. 8D步骤-D7效果确认及标准化
验证预防再发对策并监控长期的效果。 水平展开,以防同一问题及类似问题再 度发生。将相关对策形成书面文件(管 理制度、程序文件、作业指导书、表单、 技术文件、工程图纸等)。
四. 8D步骤-D7效果确认及标准化
效果确认 实事求是,以事实和数据为依据,对数据用统计工具处 理后得出相应的结论,不应未做对比分析即判定效果。
16.00% 14.00% 12.00% 10.00%
8.00% 6.00% 4.00% 2.00% 0.00%
slot1
slot2
slot3
slot4
slot5
改善前
改善后
数据点多按日期来建议走势图,数据点少可用上面的柱状图
数据来源: 时 间:
➢关键点一 :改善前后对比,数量及比例。 ➢关键点二: 结果收集的数据来源要说明。
TOYOTA 5-Why?
1W
WHY 问题
2W
WHY 中间原因
3W
WHY 中间原因
4W
WHY 中间原因
5-WHY分析案例1 状态1 一辆汽车出了故障不能行驶(WHY1)
状态2-原因1 引擎故障(WHY2)
状态3-原因2
火花塞不点火(WHY3)
状态4-原因3
3.措施 尽量具 体化。
四. 8D步骤—D6预防再发对策
计划和执行选取的预防再发对策。去除 临时行动。
需要考虑的问题:
1.确定并执行预 防再发对策, 并应注意持续 实施监控,以 确定根因已经 消除。
2.待步入生产阶 段,应即监视 纠正措施之长 期效果,并于 必要时采行补 救措施。
3.验证 预防再发 对策有效 后,可以 停止临时 措施。