压片机冲模与片重关系
压片机冲模介绍和常见问题解决方案
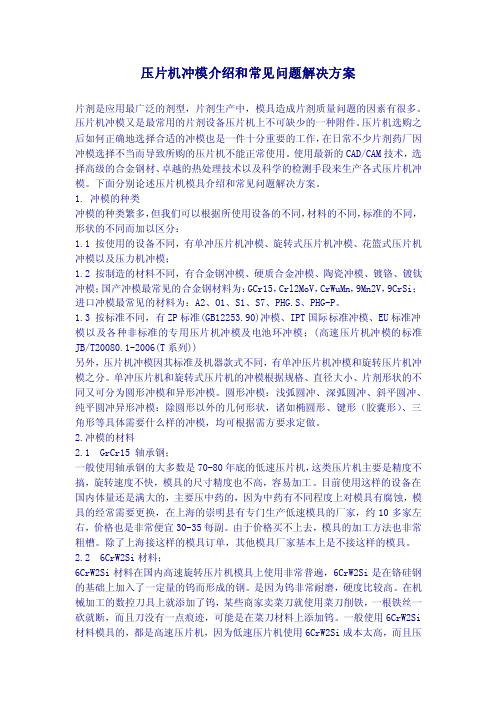
压片机冲模介绍和常见问题解决方案片剂是应用最广泛的剂型,片剂生产中,模具造成片剂质量问题的因素有很多。
压片机冲模又是最常用的片剂设备压片机上不可缺少的一种附件。
压片机选购之后如何正确地选择合适的冲模也是一件十分重要的工作,在日常不少片剂药厂因冲模选择不当而导致所购的压片机不能正常使用。
使用最新的CAD/CAM技术,选择高级的合金钢材、卓越的热处理技术以及科学的检测手段来生产各式压片机冲模。
下面分别论述压片机模具介绍和常见问题解决方案。
1. 冲模的种类冲模的种类繁多,但我们可以根据所使用设备的不同,材料的不同,标准的不同,形状的不同而加以区分:1.1 按使用的设备不同,有单冲压片机冲模、旋转式压片机冲模、花篮式压片机冲模以及压力机冲模;1.2 按制造的材料不同,有合金钢冲模、硬质合金冲模、陶瓷冲模、镀铬、镀钛冲模;国产冲模最常见的合金钢材料为:GCr15,Crl2MoV,CrWuMn,9Mn2V,9CrSi;进口冲模最常见的材料为:A2、O1、S1、S7、PHG.S、PHG-P。
1.3 按标准不同,有ZP标准(GB12253.90)冲模、IPT国际标准冲模、EU标准冲模以及各种非标准的专用压片机冲模及电池环冲模;(高速压片机冲模的标准JB/T20080.1-2006(T系列))另外,压片机冲模因其标准及机器款式不同,有单冲压片机冲模和旋转压片机冲模之分。
单冲压片机和旋转式压片机的冲模根据规格、直径大小、片剂形状的不同又可分为圆形冲模和异形冲模。
圆形冲模:浅弧圆冲、深弧圆冲、斜平圆冲、纯平圆冲异形冲模:除圆形以外的几何形状,诸如椭圆形、键形(胶囊形)、三角形等具体需要什么样的冲模,均可根据需方要求定做。
2.冲模的材料2.1 GrCr15 轴承钢;一般使用轴承钢的大多数是70-80年底的低速压片机,这类压片机主要是精度不搞,旋转速度不快,模具的尺寸精度也不高,容易加工。
目前使用这样的设备在国内体量还是满大的,主要压中药的,因为中药有不同程度上对模具有腐蚀,模具的经常需要更换,在上海的崇明县有专门生产低速模具的厂家,约10多家左右,价格也是非常便宜30-35每副。
实验二-片剂的制备与质量检查
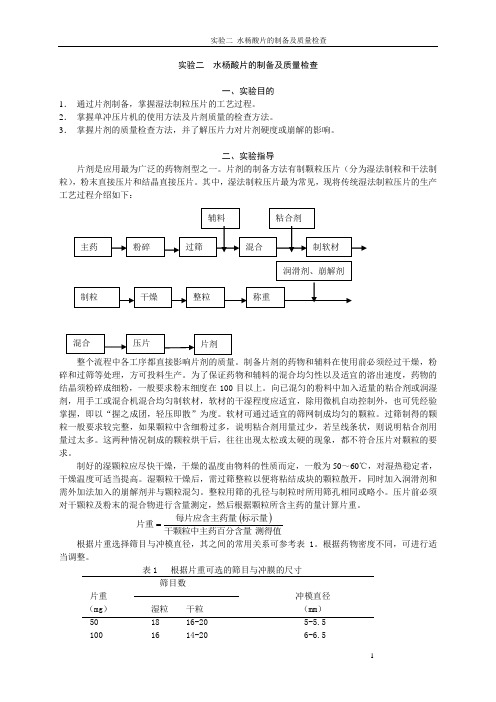
实验二 水杨酸片的制备及质量检查一、实验目的1. 通过片剂制备,掌握湿法制粒压片的工艺过程。
2. 掌握单冲压片机的使用方法及片剂质量的检查方法。
3. 掌握片剂的质量检查方法,并了解压片力对片剂硬度或崩解的影响。
二、实验指导片剂是应用最为广泛的药物剂型之一。
片剂的制备方法有制颗粒压片(分为湿法制粒和干法制粒),粉末直接压片和结晶直接压片。
其中,湿法制粒压片最为常见,现将传统湿法制粒压片的生产工艺过程介绍如下:整个流程中各工序都直接影响片剂的质量。
制备片剂的药物和辅料在使用前必须经过干燥,粉碎和过筛等处理,方可投料生产。
为了保证药物和辅料的混合均匀性以及适宜的溶出速度,药物的结晶须粉碎成细粉,一般要求粉末细度在100目以上。
向已混匀的粉料中加入适量的粘合剂或润湿剂,用手工或混合机混合均匀制软材,软材的干湿程度应适宜,除用微机自动控制外,也可凭经验掌握,即以“握之成团,轻压即散”为度。
软材可通过适宜的筛网制成均匀的颗粒。
过筛制得的颗粒一般要求较完整,如果颗粒中含细粉过多,说明粘合剂用量过少,若呈线条状,则说明粘合剂用量过太多。
这两种情况制成的颗粒烘干后,往往出现太松或太硬的现象,都不符合压片对颗粒的要求。
制好的湿颗粒应尽快干燥,干燥的温度由物料的性质而定,一般为50~60℃,对湿热稳定者,干燥温度可适当提高。
湿颗粒干燥后,需过筛整粒以便将粘结成块的颗粒散开,同时加入润滑剂和需外加法加入的崩解剂并与颗粒混匀。
整粒用筛的孔径与制粒时所用筛孔相同或略小。
压片前必须对干颗粒及粉末的混合物进行含量测定,然后根据颗粒所含主药的量计算片重。
()测得值干颗粒中主药百分含量标示量每片应含主药量片重=根据片重选择筛目与冲模直径,其之间的常用关系可参考表1。
根据药物密度不同,可进行适当调整。
表1 根据片重可选的筛目与冲膜的尺寸筛目数片重 冲模直径(mg ) 湿粒 干粒 (mm )50 18 16-20 5-5.5100 16 14-20 6-6.5150 16 14-20 7-8200 14 12-16 8-8.5300 12 10-16 9-10.5500 10 10-12 12制成的片剂需按照《中国药典》规定的片剂的质量检查项目进行检查。
压片机压片过程可能出现的问题及解决办法
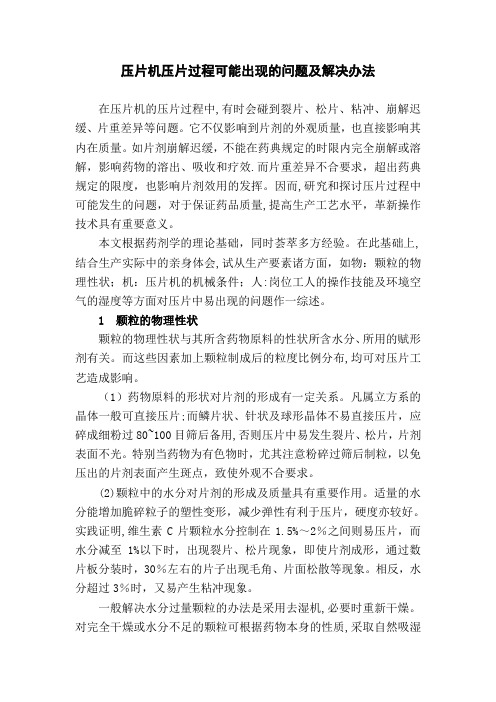
压片机压片过程可能出现的问题及解决办法在压片机的压片过程中,有时会碰到裂片、松片、粘冲、崩解迟缓、片重差异等问题。
它不仅影响到片剂的外观质量,也直接影响其内在质量。
如片剂崩解迟缓,不能在药典规定的时限内完全崩解或溶解,影响药物的溶出、吸收和疗效.而片重差异不合要求,超出药典规定的限度,也影响片剂效用的发挥。
因而,研究和探讨压片过程中可能发生的问题,对于保证药品质量,提高生产工艺水平,革新操作技术具有重要意义。
本文根据药剂学的理论基础,同时荟萃多方经验。
在此基础上,结合生产实际中的亲身体会,试从生产要素诸方面,如物:颗粒的物理性状;机:压片机的机械条件;人:岗位工人的操作技能及环境空气的湿度等方面对压片中易出现的问题作一综述。
1 颗粒的物理性状颗粒的物理性状与其所含药物原料的性状所含水分、所用的赋形剂有关。
而这些因素加上颗粒制成后的粒度比例分布,均可对压片工艺造成影响。
(1)药物原料的形状对片剂的形成有一定关系。
凡属立方系的晶体一般可直接压片;而鳞片状、针状及球形晶体不易直接压片,应碎成细粉过80~100目筛后备用,否则压片中易发生裂片、松片,片剂表面不光。
特别当药物为有色物时,尤其注意粉碎过筛后制粒,以免压出的片剂表面产生斑点,致使外观不合要求。
(2)颗粒中的水分对片剂的形成及质量具有重要作用。
适量的水分能增加脆碎粒子的塑性变形,减少弹性有利于压片,硬度亦较好。
实践证明,维生素C片颗粒水分控制在1.5%~2%之间则易压片,而水分减至1%以下时,出现裂片、松片现象,即使片剂成形,通过数片板分装时,30%左右的片子出现毛角、片面松散等现象。
相反,水分超过3%时,又易产生粘冲现象。
一般解决水分过量颗粒的办法是采用去湿机,必要时重新干燥。
对完全干燥或水分不足的颗粒可根据药物本身的性质,采取自然吸湿或酌喷适宜浓度乙醇,静置或密闭吸湿5小时左右过筛后压片.如含结晶水的药物颗粒,结晶水失去过多时出现的裂片、松片、崩解迟缓等情况则可采用此法解决。
片剂产生松片,裂片,粘冲与吊冲,片重差异超限的原因及解决办法
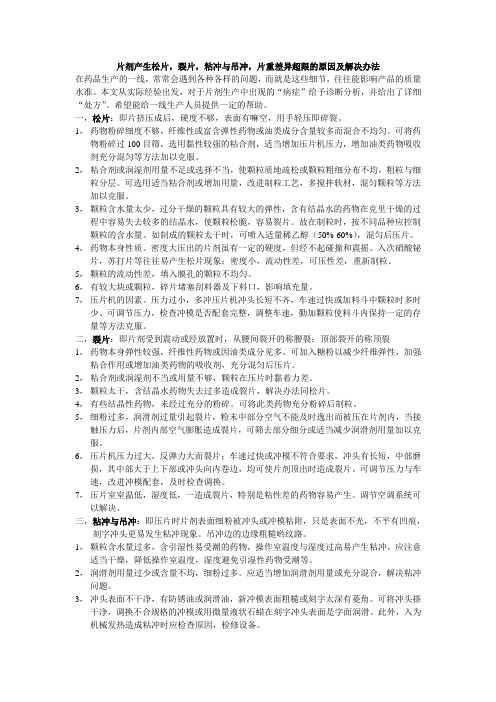
片剂产生松片,裂片,粘冲与吊冲,片重差异超限的原因及解决办法在药品生产的一线,常常会遇到各种各样的问题,而就是这些细节,往往能影响产品的质量水准。
本文从实际经验出发,对于片剂生产中出现的“病症”给予诊断分析,并给出了详细“处方”。
希望能给一线生产人员提供一定的帮助。
一,松片:即片挤压成后,硬度不够,表面有嘛空,用手轻压即碎裂。
1,药物粉碎细度不够,纤维性或富含弹性药物或油类成分含量较多而混合不均匀。
可将药物粉碎过100目筛,选用黏性较强的粘合剂,适当增加压片机压力,增加油类药物吸收剂充分混匀等方法加以克服。
2,粘合剂或润湿剂用量不足或选择不当,使颗粒质地疏松或颗粒粗细分布不均,粗粒与细粒分层。
可选用适当粘合剂或增加用量,改进制粒工艺,多搅拌软材,混匀颗粒等方法加以克服。
3,颗粒含水量太少,过分干燥的颗粒具有较大的弹性,含有结晶水的药物在克里干燥的过程中容易失去较多的结晶水,使颗粒松脆,容易裂片。
故在制粒时,按不同品种应控制颗粒的含水量。
如制成的颗粒太干时,可喷入适量稀乙醇(50%-60%),混匀后压片。
4,药物本身性质。
密度大压出的片剂虽有一定的硬度,但经不起碰撞和震摇。
入次硝酸铋片,苏打片等往往易产生松片现象;密度小,流动性差,可压性差,重新制粒。
5,颗粒的流动性差,填入膜孔的颗粒不均匀。
6,有较大块或颗粒,碎片堵塞刮料器及下料口,影响填充量。
7,压片机的因素。
压力过小,多冲压片机冲头长短不齐,车速过快或加料斗中颗粒时多时少。
可调节压力,检查冲模是否配套完整,调整车速,勤加颗粒使料斗内保持一定的存量等方法克服。
二,裂片:即片剂受到震动或经放置时,从腰间裂开的称腰裂:顶部裂开的称顶裂1,药物本身弹性较强,纤维性药物或因油类成分见多。
可加入糖粉以减少纤维弹性,加强粘合作用或增加油类药物的吸收剂,充分混匀后压片。
2,粘合剂或润湿剂不当或用量不够,颗粒在压片时黏着力差。
3,颗粒太干,含结晶水药物失去过多造成裂片,解决办法同松片。
单冲压片机的压片原理

单冲压片机的压片原理
单冲压片机是一种常用的冲压设备,用于对金属或非金属材料进行冲压成型。
其工作原理主要分为以下几个步骤:
1.上死点位置:压片机的上模和下模紧密结合,形成一定的工作空间。
2.下行移动:压片机的上模开始下行移动,材料被夹在上模和下模之间。
3.下死点位置:上模完全与下模接触,形成冲压区域。
4.冲压:上模施加一定的力量,冲击压实材料,使其在冲模的作用下发生塑性变形。
5.上行移动:上模开始上行移动,材料被释放出来。
6.脱模:上模和下模之间的材料脱离,制成所需形状。
单冲压片机主要通过模具和机械力将材料冲压成所需形状,其压片原理是利用力学原理实现的。
通过上模的移动和施加力量,使材料在模具内发生塑性变形,最终成型。
不同的模具设计和压力设置可以制造出不同形状和尺寸的零件。
制剂压片中常见问题与解决方法
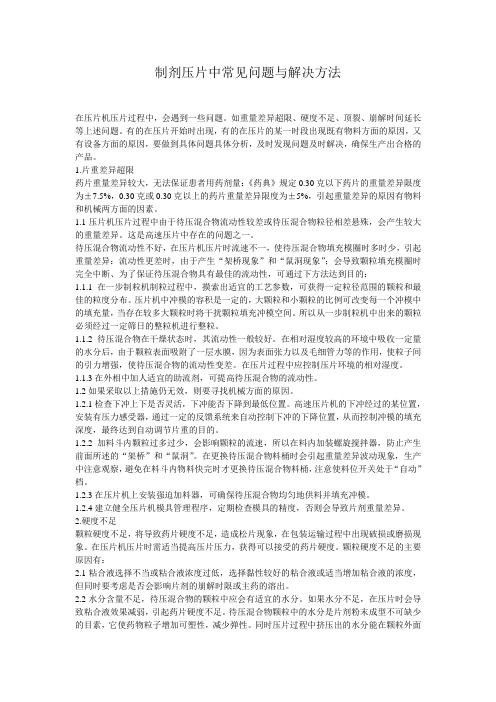
制剂压片中常见问题与解决方法--------------------------------------------------------------------------------在压片机压片过程中,会遇到一些问题。
如重量差异超限、硬度不足、顶裂、崩解时间延长等上述问题。
有的在压片开始时出现,有的在压片的某一时段出现既有物料方面的原因,又有设备方面的原因,要做到具体问题具体分析,及时发现问题及时解决,确保生产出合格的产品。
1.片重差异超限药片重量差异较大,无法保证患者用药剂量:《药典》规定0.30克以下药片的重量差异限度为±7.5%,0.30克或0.30克以上的药片重量差异限度为±5%,引起重量差异的原因有物料和机械两方面的因素。
1.1压片机压片过程中由于待压混合物流动性较差或待压混合物粒径相差悬殊,会产生较大的重量差异。
这是高速压片中存在的问题之一。
待压混合物流动性不好,在压片机压片时流速不一,使待压混合物填充模圈时多时少,引起重量差异:流动性更差时,由于产生“架桥现象”和“鼠洞现象”;会导致颗粒填充模圈时完全中断、为了保证待压混合物具有最佳的流动性,可通过下方法达到目的:1.1.1在一步制粒机制粒过程中,摸索出适宜的工艺参数,可获得一定粒径范围的颗粒和最佳的粒度分布。
压片机中冲模的容积是一定的,大颗粒和小颗粒的比例可改变每一个冲模中的填充量,当存在较多大颗粒时将干扰颗粒填充冲模空间。
所以从一步制粒机中出来的颗粒必须经过一定筛日的整粒机进行整粒。
1.1.2待压混合物在干燥状态时,其流动性一般较好。
在相对湿度较高的环境中吸收一定量的水分后,由于颗粒表面吸附了一层水膜,因为表面张力以及毛细管力等的作用,使粒子间的引力增强,使待压混合物的流动性变差。
在压片过程中应控制压片环境的相对湿度。
1.1.3在外相中加人适宜的助流剂,可提高待压混合物的流动性。
1.2如果采取以上措施仍无效,则要寻找机械方面的原因。
压片常见问题及解决方法
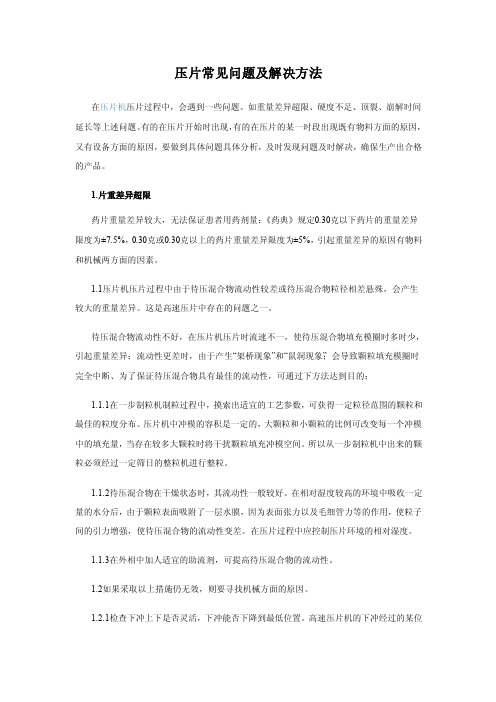
压片常见问题及解决方法在压片机压片过程中,会遇到一些问题。
如重量差异超限、硬度不足、顶裂、崩解时间延长等上述问题。
有的在压片开始时出现,有的在压片的某一时段出现既有物料方面的原因,又有设备方面的原因,要做到具体问题具体分析,及时发现问题及时解决,确保生产出合格的产品。
1.片重差异超限药片重量差异较大,无法保证患者用药剂量:《药典》规定0.30克以下药片的重量差异限度为±7.5%,0.30克或0.30克以上的药片重量差异限度为±5%,引起重量差异的原因有物料和机械两方面的因素。
1.1压片机压片过程中由于待压混合物流动性较差或待压混合物粒径相差悬殊,会产生较大的重量差异。
这是高速压片中存在的问题之一。
待压混合物流动性不好,在压片机压片时流速不一,使待压混合物填充模圈时多时少,引起重量差异:流动性更差时,由于产生“架桥现象”和“鼠洞现象”;会导致颗粒填充模圈时完全中断、为了保证待压混合物具有最佳的流动性,可通过下方法达到目的:1.1.1在一步制粒机制粒过程中,摸索出适宜的工艺参数,可获得一定粒径范围的颗粒和最佳的粒度分布。
压片机中冲模的容积是一定的,大颗粒和小颗粒的比例可改变每一个冲模中的填充量,当存在较多大颗粒时将干扰颗粒填充冲模空间。
所以从一步制粒机中出来的颗粒必须经过一定筛日的整粒机进行整粒。
1.1.2待压混合物在干燥状态时,其流动性一般较好。
在相对湿度较高的环境中吸收一定量的水分后,由于颗粒表面吸附了一层水膜,因为表面张力以及毛细管力等的作用,使粒子间的引力增强,使待压混合物的流动性变差。
在压片过程中应控制压片环境的相对湿度。
1.1.3在外相中加人适宜的助流剂,可提高待压混合物的流动性。
1.2如果采取以上措施仍无效,则要寻找机械方面的原因。
1.2.1检查下冲上下是否灵活,下冲能否下降到最低位置。
高速压片机的下冲经过的某位置,安装有压力感受器,通过一定的反馈系统来自动控制下冲的下降位置,从而控制冲模的填充深度,最终达到自动调节片重的目的。
影响片剂质量的主要原因及解决方法
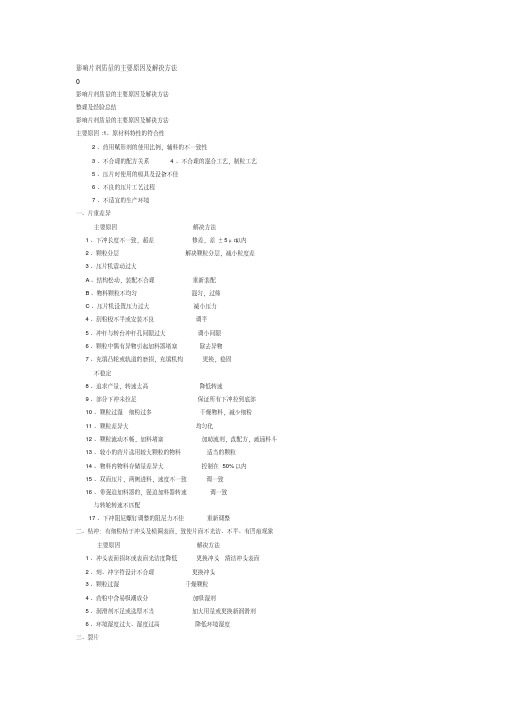
影响片剂质量的主要原因及解决方法影响片剂质量的主要原因及解决方法整理及经验总结影响片剂质量的主要原因及解决方法主要原因:1、原材料特性的符合性2、药用赋形剂的使用比例,辅料的不一致性3、不合理的配方关系4、不合理的混合工艺,制粒工艺5、压片时使用的模具及设备不佳6、不良的压片工艺过程7、不适宜的生产环境一、片重差异主要原因解决方法1、下冲长度不一致,超差修差,差±5μm以内2、颗粒分层解决颗粒分层,减小粒度差3、压片机震动过大A、结构松动,装配不合理重新装配B、物料颗粒不均匀混匀,过筛C、压片机设置压力过大减小压力4、刮粉板不平或安装不良调平5、冲杆与转台冲杆孔间隙过大调小间隙6、颗粒中偶有异物引起加料器堵塞除去异物7、充填凸轮或轨道的磨损,充填机构更换,稳固不稳定8、追求产量,转速太高降低转速9、部分下冲未拉足保证所有下冲拉到底部10、颗粒过湿细粉过多干燥物料,减少细粉11、颗粒差异大均匀化12、颗粒流动不畅,加料堵塞加助流剂,改配方,疏通料斗13、较小的药片选用较大颗粒的物料适当的颗粒14、物料内物料存储量差异大控制在50%以内15、双面压片,两侧进料,速度不一致调一致16、带强迫加料器的,强迫加料器转速调一致与转轮转速不匹配17、下冲阻尼螺钉调整的阻尼力不佳重新调整二、粘冲:有细粉粘于冲头及模圈表面,致使片面不光洁、不平、有凹痕现象主要原因解决方法1、冲头表面损坏或表面光洁度降低更换冲头清洁冲头表面2、刻、冲字符设计不合理更换冲头3、颗粒过湿干燥颗粒4、药粉中含易吸潮成分加吸湿剂5、润滑剂不足或选型不当加大用量或更换新润滑剂6、环境湿度过大、湿度过高降低环境湿度三、裂片主要原因解决方法1、压片时有空气存在于药片当中调整压力、减慢车速、增加预压时间或用有预压的工艺2、冲模磨损严重更换冲模3、黏结剂选型不当或不足更换黏结剂或加量4、颗粒含水量过低增加含水量5、颗粒过细或过粗调整颗粒粒度6、颗粒中油类成分较多加吸油剂7、模具间隙太小、不能顺利排气更换模具四、松片主要原因解决方法1、压力不够增加压力2、受压时间太少、转速快延长受压时间、增加预压、减低转速3、冲头长短不齐调整冲头4、活络冲冲头发生松动进行紧固5、下冲杆掉冲紧固6、黏结剂选型不当或太少更换黏合剂或加量7、颗粒中润滑剂比例不当调节比例8、颗粒太干燥增加颗粒水分9、物料粉碎粒度不够、纤维性或高弹性粉碎粒度过100目筛、加强黏合剂、药物或油类成分多,混合不均吸油剂10、药片压制后,置空气中过久,受潮缩短放置时间五、变色及斑点主要原因解决方法1、颗粒受油脂或其他杂质污染杜绝油脂及杂质污染2、颗粒过硬或含糖品种及有色降低颗粒硬度、有色片剂用片剂颗粒易出现乙醇为润滑剂制粒3、颗粒过大或过小颗粒适宜4、冲模型面出现锈斑清除锈斑5、加料器与转台表面摩擦有金属细粉调节加料器高度随颗粒进入模孔6、冲头与模圈内壁发生摩擦调节模圈致有色金属粉末进入颗粒六、崩解迟缓主要原因解决方法1、黏结剂粘性太强或用量过多,更换黏结剂或降低用量颗粒过硬过粗2、崩解剂选型不当、用量不足更换崩解剂或加量疏水性润滑剂太多降低疏水性润滑剂3、压力过大、片子过硬减低压力七、刻字或线条不清晰主要原因解决方法1、冲模的字符设计、布置不合理更换字符2、冲模型面磨损或破坏更换冲模3、冲模尺寸过大或不够更换冲模4、预压力过大降低预压力粉末直接压片粉末直接压片的应用方法及其注意事项由于粉末直接压片具有较明显的优点,如工艺过程比较简单,不必制粒、干燥,产品崩解或溶出快,成品质量稳定,在国外约有40%的片剂品种已采用这种工艺生产。
- 1、下载文档前请自行甄别文档内容的完整性,平台不提供额外的编辑、内容补充、找答案等附加服务。
- 2、"仅部分预览"的文档,不可在线预览部分如存在完整性等问题,可反馈申请退款(可完整预览的文档不适用该条件!)。
- 3、如文档侵犯您的权益,请联系客服反馈,我们会尽快为您处理(人工客服工作时间:9:00-18:30)。
1) 片形美观原则:厚度:直径=0.2-0.35。
2) 根据物料密度轻重,直径会有少许变化,可有交叉。
比如有时可用6mm,也可用5.5mm。
3) 平冲一般用于咀嚼片、口含片等,浅凹形片可包薄膜衣,深凹形片可包糖衣,也可包薄膜衣。
片重较大(≥500mg)时,用异形片看起来比较小,患者心理容易接受。
测定硬度时异形片需测定长轴的两端。
4) 冲模的保护:长期不用需卸下插干净后用32号机油保存,短期不用可涂抹硬镁或滑石粉。
5) 冲模生锈:用细砂纸轻轻打磨,不能摩擦过头,否则容易漏粉。
再用硬镁加可压性淀粉反复压片清除锈斑。
6) 平片、浅凹形片、深凹形片对药物的释放可能有一定影响。
刚做了一组对比实验,分别测了水平放置和竖直放置的硬度,每组10片,圆形片,直径11mm,片重525mg,未包衣。
水平放置的硬度分别为16.0、19.5、18.1、16.7、19.2、16.1、17.2、21.9、17.5、17.0 kp平均值17.92 SD1.83
竖直放置的硬度分别为18.9、21.9、18.5、17.9、17.6、22.6、18.9、17.8、18.0、17.7kp平均值18.98 SD1.79
竖直放置的硬度更大一些,原因可以通过附图来理解,A挡板不动,B挡板向A方向移动,竖直放置的时候片子重心更高,A挡板会向前轻微变形移动,需额外增加一部分力量克服这种变形产生的反作用力,B挡板会向后变形,而且竖直放置的片子因为重心高,A和B挡板变形的程度要大于水平放置时的变形程度,所以需要更多的力来克服,导致硬度偏大。
如果片子的硬度比较小,竖直放置和水平放置的硬度差别不会太大。
正确的放置方式应该是水平放置,这样不管片子直径多大,都能保证沿直径方向破坏。
可以参考下面的一片资料:
另外,硬度仪与片子接触的水平部分比较光滑的,而且片子从受力到破裂,相对于水平部分几乎没有发生位移,所以与片子接触的水平部分对片子的作用力并不大,不管是竖直放还是水平放。
片子受到的破坏力是水平方向的,与竖直方向的支持力没有关系的,所以水平面与硬度没有直接关系。