冲压工艺与模具概述
冲压工艺与模具设计概述

冲压模具的主要功能
1 定位
确保工件在加工过程中的 准确定位
2 导向
引导模具在运动中保持正 确的轨迹
3 加工
对金属材料进行剪切、冲 裁、弯曲等加工过程
冲压模具的基本构成
上模
通常用于顶压材料,具有凹模形状
下模
位于上模下方,通常用于支撑材料,具有凸模形状
冲压模具的分类与特点
1
按用途分类
冲裁模、弯曲模、拉伸模等
2
按结构分类
单工位模、连续模、进料连续模等
冲压模具的设计流程
产品分析
了解产品形态和使用要求
模具设计详图
绘制模具构造图,确定每个零部件的加工尺寸 和工艺要求
模具构思与方案设计
根据产品要求设计模具结构与工作原理
加工制作与调试
进行模具的制造和装配,并进行调试和优化
冲压工艺与模具设计概述
冲压工艺与模具设计是现代制造业中不可或缺的重要环节。本文将介绍冲压 工艺与模具设计的概述、基本原理、分类与特点,以及应用领域等内容。
冲压加工的基本原理
冲压加工利用模具对金属材料施加压力,通过剪切、冲裁、弯曲等方式,将材料变形成所需形状的工艺过程。
冲压工艺的分类与特点
分类
单工位、多工位、连续冲压
特点
高效快速、重复性好、成本低、适用于大批量生产
冲压工艺的应用领域
1 汽车制造
车身、发动机零部件等
3 电子产品
手机、电脑等金属部件2 家电制造冰箱、空调 Nhomakorabea产品外壳
4 其他行业
金属制品、建筑材料等
冲压加工的优点与局限性
优点
• 高生产效率 • 较高的精度和重复性 • 成本较低
局限性
法兰件的冲压工艺与模具设计概述
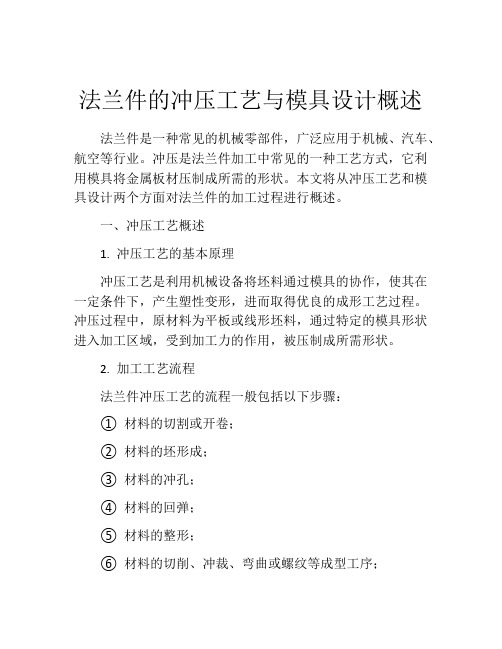
法兰件的冲压工艺与模具设计概述法兰件是一种常见的机械零部件,广泛应用于机械、汽车、航空等行业。
冲压是法兰件加工中常见的一种工艺方式,它利用模具将金属板材压制成所需的形状。
本文将从冲压工艺和模具设计两个方面对法兰件的加工过程进行概述。
一、冲压工艺概述1. 冲压工艺的基本原理冲压工艺是利用机械设备将坯料通过模具的协作,使其在一定条件下,产生塑性变形,进而取得优良的成形工艺过程。
冲压过程中,原材料为平板或线形坯料,通过特定的模具形状进入加工区域,受到加工力的作用,被压制成所需形状。
2. 加工工艺流程法兰件冲压工艺的流程一般包括以下步骤:① 材料的切割或开卷;② 材料的坯形成;③ 材料的冲孔;④ 材料的回弹;⑤ 材料的整形;⑥ 材料的切削、冲裁、弯曲或螺纹等成型工序;⑦ 生产过程的质检。
其中,材料的切割和开卷坯形成是成品生产的前置工序。
冲孔和回弹是法兰件冲压最核心的工序,整形贯穿于整个加工过程,而成品的切削、冲裁、弯曲或螺纹等成型工序则是基于成品的需求而生的。
生产过程的质检是法兰件生产过程的必要环节,主要是对加工工艺的合格率和成品的主要质量指标进行检测。
二、模具设计概述1. 模具的基本构成模具一般由复位装置、模具座、上凸模、下凹模、剪切装置、导柱和导套、拉伸装置等组成。
其中,凸模和凹模组成了法兰件真正成型的区域。
2. 模具设计的几个要点(1) 模具的凸模和凹模的尺寸大小和左右要对称;(2) 凸模的侧壁和凹模的底部需斜侧面处理,以利于法兰件在脱模时能够顺利脱离模具;(3) 在法兰件的设计中需要留一些余量的情况下,凹模底部需要加工弯曲过渡,避免切割时残留;(4) 凸模和凹模的表面需要进行抛光处理,确保成品无毛刺,以及在成型时不会夹入其他杂质。
三、加工注意事项1. 金属材质法兰件是金属材质的制品,这就需要制造商在选择板材的时候需要注意该材质的强度、韧性、塑性等参数是否符合制品设计的要求。
在加工过程中,冲压机需要根据实际板材厚度等参数的调整,以确保正常加工。
垫板冲压工艺及模具设计概述

垫板冲压工艺及模具设计概述垫板冲压工艺及模具设计概述一、垫板冲压工艺概述垫板冲压是金属加工的一种方式,其工艺包括模具设计、材料选择、工艺参数的设置等多个方面,是极其重要的金属加工技术之一。
垫板冲压的工艺流程一般如下:1.设计模具:模具是垫板冲压的核心之一。
设计好的模具要具备材料保存、产品精度、加工速度等多个方面的特点。
2.材料选择:选择合适的材料对产品的质量和生产效率都有很大的影响。
通常选择的材料有钢板、不锈钢板、铝板等。
3.冲床设备调试:冲床设备的调试直接影响到冲制产品的质量和生产效率。
4.调整冲压工艺参数:对于每个不同的产品,都需要设置不同的工艺参数,包括冲压速度、冲压力度、位移量、冲头选型等等。
5.冲制成品:经过以上的步骤之后,就可以上机冲压成品了。
二、模具设计概述模具是垫板冲压的核心,其设计影响产品的加工精度和生产效率。
常见的模具有单工位模具、多工位模具、连拍模具等。
1.单工位模具:单工位模具具有结构简单、成本低等优点。
适用于单一产品的加工,以及小批量生产。
2.多工位模具:多工位模具可以在同一个冲床上进行多个工序,其优点就在于可提高生产效率和利用率。
3.连拍模具:连拍模具是一种比较高级的模具,在一个模具中可以装多个冲头,可同时冲制多个不同形状的产品。
除此之外,模具的设计还要考虑到产品的成形精度、冲头的选型等因素。
三、工艺参数的设置工艺参数的设置对于垫板冲压工艺非常重要,能直接影响到产品的质量,包括尺寸精度、表面质量、变形量等等。
1.冲压速度:冲压速度要根据产品的特点来决定,在刚开始进行试模的时候,应逐步加快冲压速度。
2.冲压力度:冲压力度要根据材料的硬度来决定,过小会造成无法正常成形,过大会造成材料的不必要损伤。
3.位移量:位移量是冲压加工的重要参数之一,要选好位移量来保证产品尺寸精度。
4.冲头选型:选择好适当的冲头,冲制出符合要求的产品。
四、总结垫板冲压工艺涉及到多个方面,其中模具设计和工艺参数设置是非常重要的环节。
冲压工艺及模具设计

冲压工艺及模具设计冲压工艺及模具设计是现代工业制造中常用的一种技术,它通过将金属板材或者其他形状的金属件置于模具中,然后通过冲压机的动作使得金属材料发生塑性变形以得到所需的形状和尺寸。
冲压工艺及模具设计是一门综合性强的工艺技术,以下将介绍其包括冲压工艺流程、模具设计原则、模具结构设计、模具构件选用等相关内容。
一、冲压工艺流程冲压工艺分为单道冲压和多道冲压两种。
单道冲压是指在一个冲压过程中完成产品的全体造型,多道冲压是指通过多次冲压工艺来完成产品的全体造型。
下面将以多道冲压为例介绍冲压工艺流程。
1.材料准备:选择合适的板材材料,进行剪切、铺料等准备工作。
2.模具设计:根据产品的形状和尺寸要求,设计合适的冲压模具。
3.上料:将材料板厚按照模具规格要求剪切成对应尺寸,然后放置在模具上。
4.开模:通过冲压机的动作,使得模具上的凸模与凹模对压,使材料发生塑性变形。
5.去杂及模具保养:在冲压过程中会产生一些杂质,需要及时清理,并对模具进行保养和维护。
二、模具设计原则模具设计是冲压工艺的核心环节,它直接影响着产品的质量和成本。
在进行模具设计时,需要遵循以下原则:1.合理性原则:模具结构要合理,能够满足产品的形状和尺寸要求,并且易于加工和调整。
2.稳定性原则:模具要具有足够的刚性和稳定性,能够承受冲压机的冲击力和振动。
3.高效原则:模具设计要考虑工作效率,设计出能够实现快速冲压的模具结构。
4.经济原则:模具的设计和制造成本要较低,以降低产品的制造成本。
三、模具结构设计模具的结构设计是模具设计的重要环节,它包括模具的整体结构、分段结构、导向结构等。
下面将介绍常用的模具结构设计方法:1.整体结构设计:将模具设计为一个整体结构,具有较好的刚性和稳定性。
2.分段结构设计:根据产品的形状和尺寸要求,将模具分为多个部分,通过连接件进行连接。
3.导向结构设计:模具需要具有良好的导向性,避免材料在冲压过程中发生歪斜和偏移。
4.其他辅助结构设计:模具还需要考虑各种辅助结构,如剪断边缘结构、定位结构、脱模结构等。
冲压工艺与模具设计ppt课件
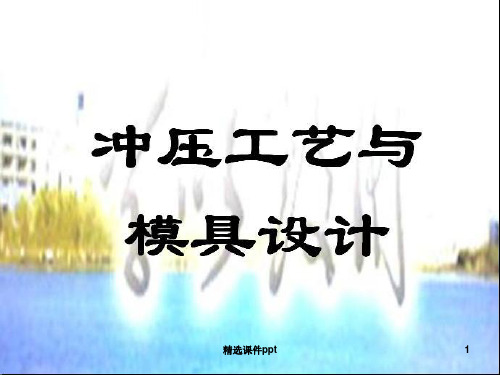
(7)大量生产时,产品成本低。
精选课件ppt
24
由此可见,冲压能集优质、高效、低能耗、 低成本于一身,这是其它加工方法无法与之相比拟的,
因此冲压的应用十分广泛,如汽车,拖拉机行业中,冲压 件占60%~70%,仪器仪表占到60~70%,还有日常生活中的 各种不锈钢餐具等等。从精细的电子元件,仪表指针到重 型汽车的覆盖件和大梁以及飞机蒙皮等均需冲压加工。
29
分离工序示意
D
D
D
落料
D
剪切
有分离现象发生,但不
改变空间形状
精选课件ppt
30
表1-1 分离工序
精选课件ppt
31
表1-1 分离工序(续)
精选课件ppt
32
(2)成形工序
冲压成形时,被加工材料在外力作用下,变形区材料所受 到的等效应力达到材料的屈服极限σs,但未达到强度极限σb, 使材料只产生塑性变形,从而得到一定形状和尺寸的零件。成 形工序主要有弯曲、拉深、翻孔、缩口、胀形等。
精选课件ppt
28
1.2 冲压工艺分类
1.按变形性质分类
➢分离工序 ➢成形工序
(1)分离工序
冲压成形时,被加工材料在外力作用下产生变形,当变 形区材料受到的剪切应力达到材料的抗剪强度,材料便产生 剪切而分离,从而形成一定形状和尺寸的零件。分离工序主 要有剪裁、冲孔、落料、切口、剖切等。
精选课件ppt
精选课件ppt
27
总之,模具工业是 一个国家的基础工业,模具设计与模 具制造水平的高低已成为衡量一个国家产品制造水平的高低。
发达国家非常重视模具的发展,日本认为:“模具就是进 入富裕社会的原动力”;德国:“金属加工业中的帝王”;罗 马尼亚:“模具就是黄金”;模具在国际上被认为是点石成金 的行业。不过这里的模具还包括塑模、锻模、压铸模、橡胶模、 食品模、建材模等等,但目前以冷冲模和塑料模的应用最广, 各占40%左右。
冲压模具工艺(3篇)
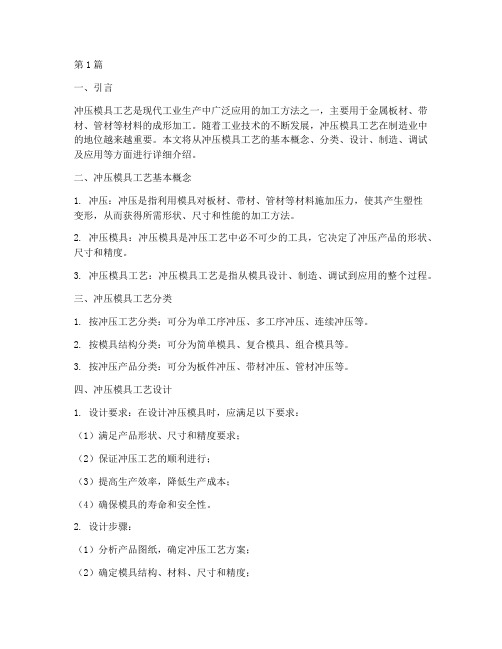
第1篇一、引言冲压模具工艺是现代工业生产中广泛应用的加工方法之一,主要用于金属板材、带材、管材等材料的成形加工。
随着工业技术的不断发展,冲压模具工艺在制造业中的地位越来越重要。
本文将从冲压模具工艺的基本概念、分类、设计、制造、调试及应用等方面进行详细介绍。
二、冲压模具工艺基本概念1. 冲压:冲压是指利用模具对板材、带材、管材等材料施加压力,使其产生塑性变形,从而获得所需形状、尺寸和性能的加工方法。
2. 冲压模具:冲压模具是冲压工艺中必不可少的工具,它决定了冲压产品的形状、尺寸和精度。
3. 冲压模具工艺:冲压模具工艺是指从模具设计、制造、调试到应用的整个过程。
三、冲压模具工艺分类1. 按冲压工艺分类:可分为单工序冲压、多工序冲压、连续冲压等。
2. 按模具结构分类:可分为简单模具、复合模具、组合模具等。
3. 按冲压产品分类:可分为板件冲压、带材冲压、管材冲压等。
四、冲压模具工艺设计1. 设计要求:在设计冲压模具时,应满足以下要求:(1)满足产品形状、尺寸和精度要求;(2)保证冲压工艺的顺利进行;(3)提高生产效率,降低生产成本;(4)确保模具的寿命和安全性。
2. 设计步骤:(1)分析产品图纸,确定冲压工艺方案;(2)确定模具结构、材料、尺寸和精度;(3)绘制模具装配图和零件图;(4)进行模具强度、刚度和耐久性计算。
五、冲压模具工艺制造1. 模具材料:模具材料应具有良好的耐磨性、耐冲击性、耐热性、耐腐蚀性等性能。
常用的模具材料有Cr12、Cr12MoV、CrWMn等。
2. 模具加工:模具加工主要包括以下步骤:(1)毛坯加工:根据模具图纸,加工出模具毛坯;(2)热处理:对模具毛坯进行热处理,提高其性能;(3)机械加工:对模具进行机械加工,达到图纸要求的尺寸和精度;(4)装配:将模具零件装配成完整的模具。
六、冲压模具工艺调试1. 调试目的:调试冲压模具的目的是使模具在正常生产条件下,达到规定的生产速度、精度和产品质量。
垫板冲压工艺及模具设计概述

垫板冲压工艺及模具设计概述1. 引言在制造业中,冲压工艺是一种常用的加工方法。
垫板冲压工艺在汽车、电器、家具等行业中广泛应用。
本文将介绍垫板冲压工艺的基本流程,并探讨垫板冲压模具的设计要点。
2. 垫板冲压工艺流程垫板冲压工艺流程通常包括以下几个步骤:•材料准备:选择适合的板材材料,并进行切割和成型。
•模具设计:根据产品要求和工艺流程,设计垫板冲压模具。
•模具制造:制造垫板冲压模具,包括模具的零件加工、组装和试模调整。
•冲压操作:将板材材料放置在模具上,并通过冲压设备进行冲压加工。
•检验:对冲压件进行质量检验,包括尺寸、外观和性能等方面的检验。
•后处理:对冲压件进行清洗、抛光、涂层等后续处理工序。
•成品入库:将符合要求的冲压件入库,以备后续的使用。
3. 垫板冲压模具设计要点垫板冲压模具的设计是垫板冲压工艺的关键环节,其设计质量直接影响到冲压件的质量和生产效率。
以下是一些垫板冲压模具设计的要点:3.1 模具结构设计•合理的结构设计能够提高模具的强度和刚度,减少变形和振动,提高冲压精度和稳定性。
•模具结构应该尽可能简洁,避免多余的部件和复杂的装配。
3.2 材料选择•模具的材料选择应考虑到耐磨性、强度和导热性等因素。
•常见的模具材料有工具钢、硬质合金和高速钢等,选择适合的材料能够延长模具的使用寿命。
3.3 模具零件设计•模具的各个零件应具备足够的强度和稳定性,能够承受冲击和压力。
•零件的设计应考虑到易于加工和拆卸,方便维修和更换。
4. 垫板冲压工艺的优点垫板冲压工艺具有以下几个优点:•高效率:冲压工艺可以实现快速批量生产,提高生产效率。
•一次成形:冲压工艺可以一次性完成许多工序,提高部件的一致性和精度。
•成本低:冲压工艺可以节约原材料和能源,并减少人工成本。
5. 垫板冲压工艺的应用领域垫板冲压工艺广泛应用于以下领域:•汽车制造:汽车车身和零部件的制造。
•电器制造:电视、洗衣机、冰箱等家电产品的制造。
•家具制造:家具产品的制造和组装。
冲压工艺与模具设计

冲压工艺与模具设计冲压工艺是一种应用广泛的加工方法,通过利用冲压模具的压力和变形能力来把金属材料压制成所需的形状和尺寸。
模具设计则是在冲压工艺中起到决定性作用的一环,好的模具设计可以提高冲压加工的效率和质量。
冲压工艺一般分为单冲工艺和连续冲工艺两种。
单冲工艺适用于对单个零件进行冲裁、成形、打孔、冲突等操作,常用于汽车、家电、航空等领域。
连续冲工艺则常用于大批量零件生产,如冰箱门板、沙发弹簧等。
其工艺流程就是通过选择合适的模具,使连续的原材料成形、裁剪成所需的形状和尺寸。
在冲压工艺中,模具设计是非常重要的一环。
好的模具设计可以有效提高冲压工艺的效率和质量,降低成本,提高产品的质量和寿命。
模具设计要考虑到许多方面的因素,例如材料的选择、模具结构的设计、工序的安排等等。
首先,模具设计者必须选择适合所要加工的材料的压力和温度范围。
不同的材料有不同的性质和加工难度,比如薄铁片很容易裂缝,钢材比较难加工,所以针对不同的材料要选择不同的模具形式。
其次,每一种模具结构都有其独特的加工特点,需要依据产品形状和工艺流程来确定,比如平面压制、剪切、冲切、拉伸等等。
最后,工序的安排也是一个很重要的因素,若在模具加工过程中有一些不注意的细节,就会造成模具设计的失败,进而导致制作出来的产品质量与效率的降低。
总之,在冲压工艺中,模具设计是有着非常重要的意义的。
模具设计人员需要全面考虑材料的特性,结合工程知识和自己的经验,在形状最简单、尺寸最精确、制作难度最小等方面进行模具设计。
随着时代的变化和新技术的不断呈现,模具设计必将越来越重要和复杂化。
必须要掌握一定的专业知识和技能,不断学习新的模具设计技巧,提高自己的创新意识和工作责任意识,那么才能更好地为冲压工艺和产品质量的提高做出贡献。
- 1、下载文档前请自行甄别文档内容的完整性,平台不提供额外的编辑、内容补充、找答案等附加服务。
- 2、"仅部分预览"的文档,不可在线预览部分如存在完整性等问题,可反馈申请退款(可完整预览的文档不适用该条件!)。
- 3、如文档侵犯您的权益,请联系客服反馈,我们会尽快为您处理(人工客服工作时间:9:00-18:30)。
冲压工艺设计方法:
在对冲压零件特征分析、工艺模拟分析、工艺计算的基础上, 遵循“高质量、高效率、低成本”的总原则,精细设计冲压 工艺。
成双工艺、连续冲压工艺、拉延切角工艺、复合冲压工艺、 往复冲裁工艺、落料成形工艺、多次修边工艺、修边整形工 艺、分次拉延工艺、反拉延工艺、拉延槛、筋的应用、回弹 变形的预测控制、工艺台阶的应用、工艺切口的应用等。
1.3覆盖件的成形分类
汽车覆盖件的冲压成形分类以零件上易破裂或起皱部位 材料的主要变形方式为依据,并根据成形零件的外形特征、 变形量大小、变形特点以及对材料性能的不同要求,可将汽
车覆盖件冲压成形分为五类:深拉深成形类、胀形拉深成形 类、浅拉深成形类、弯曲成形类和翻边成形类。
1.4覆盖件的主要成形障碍及其防止措施
图2 工艺孔和工艺切口
冲 压 工 艺(实例)
拉延切角、工艺切口
CAE分析
冲 压 工 艺(实例)
安全 破裂 起皱 回弹
Байду номын сангаас
汽车覆盖件模具制造的发展:
二十世纪中期:手工设计,手工制泥模,手工制模型样架,手工制 大量研配检验样板,大量人工修磨模具.
二十世纪后期:CAD设计,手工制泥模,手工制模型样架,大量使 用大型仿形铣床及大型加工设备,使用激光切割机加工研配检 验样板,采用研配压力机修磨模具.
防裂措施:
为了防止开裂,应从覆盖件的结构、成形工艺以及模具设 计多方面采取相应的措施。
(1) 覆盖件的结构上,可采取的措施有: 各圆角半径最好大一些、曲面形状在拉深方向的实际深 度浅一些、各处深度均匀一些、形状尽量简单且变化尽量平 缓一些等。 (2)拉深工艺方面,可采取的主要措施有: 拉深方向尽量使凸模与坯料的接触面积大、合理的压料 面形状和压边力使压料面各部位阻力均匀适度、降低拉延深 度、开工艺孔和工艺切口等 (如图2)。 (3)模具设计上 可采取设计合理的拉深筋、采用较大的模具圆角、使凸 模与凹模间隙合理等措施。
二十一世纪初: 采用CAD/CAM 软件 设计模具,开始推行“无 纸模具设计和制造”这一研究和开发项目,计算机输入产品模 型,生成高质量实体模型 . CAD/CAM技术的推广已由“甩图 板”阶段跨入到了深化应用阶段.
Delcam 方案是使用模具镶块向导程序“Die Wizard“.该程 序可自动寻找产品模型的分模线并自动将模块分为合适尺 寸的两部分, 自动产生高质量的分模面,自动分离型芯和 型腔。“Die Wizard”技术的应用,更大大提高企业工艺 编制的效率和准确性,可以对产品开发数据进行有效的管理, 提高模具设计速度和管理效率从根本上降低模具制造企业 的成本.
覆盖件成形工序:
覆盖件的主要冲压工序有:落料、拉深、校形、修边、 切断、翻边、冲孔等。
覆盖件的结构特征
和一般冲压件相比,覆盖件具有材料薄、形状复杂、 多为空间曲面且曲面间有较高的连接要求、结构尺寸较大、 表面质量要求高、刚性好等特点。
1.2覆盖件的成形特点
1.成形工序多:拉深为关键工序; 2.拉深是复合成形 :常采用一次拉深; 3.拉深时变形不均匀:工艺补充、拉深筋; 4.大而稳定的压边力:双动压机、多连杆机械压力机; 5.优质钢材:高强度、高质量、抗腐蚀的钢板;
目前法国CATIA公司开发的大型CAD/CAE/CAM一体化软件 V5R17已广泛应用于航空汽车制造业设计,不久将用于模具 制造,因一体化特性,将使模具分析、设计、制造更方便快 捷.
冲压工艺
冲压工艺设计是冲压与模具的核心技术,是衡量冲压技术的标志,是冲压成功的关键。 冲压工艺根据通用的分类方法,可将冲压的基本工序分为材料的分离和成形两大类,每一类中 又包括许多不同的工序。 分离工序:
成形工序
冲压工艺
冲压工艺
冲压模具工序及略语:
冲压工艺设计主要任务:
一是完成拉延件的设计 二是完成DL图(die Layout)的设计 DL图(模具工艺构件图)内容: 设定冲压工序的性质、工序数目、工序顺序和工序内容 设定各工序的冲压方向和送料方向 设定工艺排样和材料利用率 设定冲压设备、生产方式及流程 设计DL图、工艺卡和工艺指导书
图1 覆盖件拉深过程示意图 a) 坯料放入;b) 压边;c) 板料与凸模接触;d) 材料拉入;
e) 压型;f) 下止点;g) 卸载
2.开裂及防裂措施
原因: 是由于局部拉应力过大造成的,由于局部拉应力过大导 致局部大的胀形变形而开裂。 位置: 开裂主要发生在圆角部位,开裂部位的厚度变薄很大如
凸模与坯料的接触面积过小、拉深阻力过大等都有可能导致 材料局部胀形变形过大而开裂 。
冲压工艺与模具
冲压技术发展
冲压技术的真正发展,始于汽车的工业化生产。
20世纪初,研究工作基本上在板料成形技术和成形性两方面同时展开,关键问题 是破裂、起皱与回弹。但对冲压技术的掌握基本上是经验型的。分析工具是经典 的成形力学理论,能求解的问题十分有限,远不能满足汽车工业的需求。 60年代是冲压技术发展的重要时期,各种新的成形技术相继出现。尤其是成形极 限图的提出,推动了板材性能、成形理论、成形工艺和质量控制的协调发展,成 为冲压技术发展史上的一个里程碑。 80年代有限元方法及CAD技术开始发展。 90年代汽车冲压技术真正进入了分析阶段(数值模拟仿真及计算机应用技术在冲 压领域得以迅速发展并走向实用化)
通常厚板料零件多采用:落料 成形 翻边 冲孔
的工艺过程。
薄板料且形状复杂零件:拉延 冲孔的工艺
修边 翻边
整形
覆盖件部分
1.1覆盖件的含义:
覆盖件主要指覆盖汽车发动机和底盘、构成驾驶室和 车身的一些零件,如轿车的挡泥板、顶盖、车门外板、发 动机盖、水箱盖、行李箱盖等。由于覆盖件的结构尺寸较 大,所以也称为大型覆盖件。
由于覆盖件形状复杂,多为非轴对称、非回转体的复杂 曲面形状零件,因而决定了拉深时的变形不均匀,所以拉深 时的起皱和开裂是主要成形障碍。
1.起皱及防皱措施
原因: 覆盖件的拉深过程中,当板料与凸模刚开始接触,板面 内就会产生压应力,随着拉深的进行,当压应力超过允许值 时,板料就会失稳起皱(如图1)。 防皱措施: 解决的办法是增加工艺补充材料或设置拉深筋。