移动从动件盘形凸轮机构设计实验
机械设计对心直动滚子从动件盘形凸轮的设计
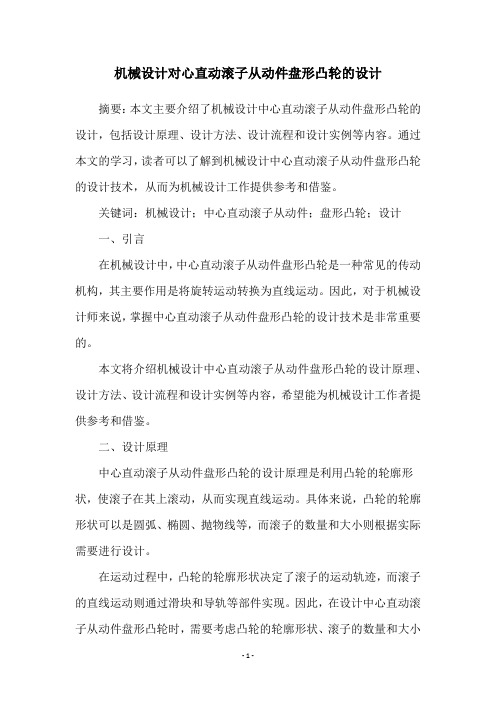
机械设计对心直动滚子从动件盘形凸轮的设计摘要:本文主要介绍了机械设计中心直动滚子从动件盘形凸轮的设计,包括设计原理、设计方法、设计流程和设计实例等内容。
通过本文的学习,读者可以了解到机械设计中心直动滚子从动件盘形凸轮的设计技术,从而为机械设计工作提供参考和借鉴。
关键词:机械设计;中心直动滚子从动件;盘形凸轮;设计一、引言在机械设计中,中心直动滚子从动件盘形凸轮是一种常见的传动机构,其主要作用是将旋转运动转换为直线运动。
因此,对于机械设计师来说,掌握中心直动滚子从动件盘形凸轮的设计技术是非常重要的。
本文将介绍机械设计中心直动滚子从动件盘形凸轮的设计原理、设计方法、设计流程和设计实例等内容,希望能为机械设计工作者提供参考和借鉴。
二、设计原理中心直动滚子从动件盘形凸轮的设计原理是利用凸轮的轮廓形状,使滚子在其上滚动,从而实现直线运动。
具体来说,凸轮的轮廓形状可以是圆弧、椭圆、抛物线等,而滚子的数量和大小则根据实际需要进行设计。
在运动过程中,凸轮的轮廓形状决定了滚子的运动轨迹,而滚子的直线运动则通过滑块和导轨等部件实现。
因此,在设计中心直动滚子从动件盘形凸轮时,需要考虑凸轮的轮廓形状、滚子的数量和大小以及滑块和导轨等部件的设计。
三、设计方法中心直动滚子从动件盘形凸轮的设计方法主要包括以下几个步骤:1. 确定传动比和运动要求:首先需要确定传动比和运动要求,包括传动比、滚子数量和大小、滑块和导轨的设计等。
2. 计算凸轮的轮廓形状:根据运动要求和传动比,计算出凸轮的轮廓形状。
具体来说,可以利用数学模型或计算机模拟等方法进行计算。
3. 设计滑块和导轨:根据凸轮的轮廓形状和滚子的运动轨迹,设计滑块和导轨等部件。
其中,滑块的设计需要考虑其密封性、耐磨性和承载能力等因素。
4. 完善设计:在完成初步设计后,需要进行完善设计,包括进行力学分析、动态模拟和优化设计等。
同时,还需要考虑制造工艺、材料选择和装配等问题。
四、设计流程中心直动滚子从动件盘形凸轮的设计流程主要包括以下几个步骤:1. 确定传动比和运动要求:首先需要确定传动比和运动要求,包括传动比、滚子数量和大小、滑块和导轨的设计等。
哈工大机械原理大作业直动从动件盘形凸轮机构满分完美版哈尔滨工业大学

end
%曲率半径
dx=diff(x);
dx(36001)=0;
dy=diff(y);
dy(36001)=0;
dydx=dy./dx;
ddy=diff(dydx);
ddy(36001)=0;
ddy=ddy./dx;
~7~
xlabel('凸轮转角φ/°');
ylabel('从动件加速度 a/(mm/s^2)');
title('加速度');
subplot(2,3,4);
plot(dsdPhi,s);
axis equal
axis([-30 50 -50 30]);
hold on
plot(x1,f1,'r');
hold on
axis equal
hold on
plot(x,y,'k')
legend('理论廓线',-1);
hold on
%轮廓图
%实际廓线
%理论廓线
~8~
哈尔滨工业大学
直动从动件盘型凸轮机构设计说明书
plot(x0,y0,':')
hold on
%基圆
plot(xe,ye,'k:')
%偏距圆
legend('实际廓线','理论廓线','基圆','偏距圆',-1);
subplot(2,3,1);
plot(Phi,s);
grid on
axis([0 360 0 27]);
11凸轮机构运动参数的测定

课题十一凸轮机构运动参数的测定凸轮机构主要是由凸轮,从动件和机架三个基本构件组成的高副机构。
其中凸轮是一个具有曲线轮廓或凹槽的构件,一般为主动件,作等速回转运动或往复直线运动。
从动件与凸轮轮廓接触,传递动力和实现预定的运动规律故从动件的运动规律取决于凸轮轮廓曲线。
由于组成凸轮机构的构件数较少,结构比较简单,只要合理地设计凸轮的轮廓曲线就可以使从动件获得各种预期的运动规律。
凸轮机构能将主动件的连续运动转变为从动件的移动或转动,因而广泛用于各种机械中,特别是自动机械、自动线中的机械控制装置中。
1.凸轮机构运动参数的测定实验台及其工作原理进行凸轮机构运动参数的测定实验台有多种形式,现以如图11—1所示的连杆机构与凸轮组合实验台,完成凸轮机构运动参数的测定。
图11—1 连杆机构与凸轮组合实验台a)b)图11—2 凸轮机构实验台的运动简图1--同步脉冲发生器 2—减速器 3--电机 4—传感器5--光栅盘 6--凸轮 7--平底直动从动件 8--回复弹簧9--滑块 10--滚子直动从动件如图11—2a)、b)所示,凸轮机构的实验台是电机、减速器、凸轮、直动从动件、滑块、传感器、同步脉冲发生器、光栅盘和回复弹簧等组成。
通过调速器调节电机的转速输出后,经蜗杆减速器带动凸轮转动,驱动从动件运动,其位移量通过直线位移传感器由模/数转换模块在嵌入式计算机系统的控制下,将位移量转换成数字信号,计算出其往复移动的周期、线速度、线加速度等机构运动参数。
也可更换不同廓线的盘形凸轮,从而调节从动件的偏心距。
2.凸轮机构运动参数的测定实验注意事项(1) 调节电机的转速时应缓慢转动调速旋钮,在关闭实验台电源前,应将电动机的转速调到最小。
(2) 用手转动凸轮盘1~2 周,检查各运动构件的运行状况,各螺母紧固件应无松动,各运动构件应无卡滞现象。
(3) 测试时,凸轮的转速不应过高,以免产生大的冲击,造成零件损坏。
(4) 调节从动件偏心距时,偏心距不宜过大,否则有可能使凸轮机构卡死,造成零件损坏。
凸轮设计报告

H a r b i n I n s t i t u t e o f T e c h n o l o g y课程设计说明书(论文)课程名称:机密机械基础设计题目:直动从动件盘形凸轮机构的设计院系:航天学院班级:0804201设计者:王有松学号:1080420118指导教师:郭玉波设计时间:2010年10月23日哈尔滨工业大学摘要:凸轮机构广泛应用于自动化机械,仪器仪表及各种操纵控制装置中,其最大的特点是,只要凸轮的轮廓曲线设计适当,就可以使从动件获得任何预期的运动规律。
因此,凸轮设计的核心问题是根据从动件的运动规律来确定凸轮的轮廓曲线。
本文利用C语言(基于WIN-TC)设计运动规律为余弦加速的直动从动件盘形凸轮。
关键词:凸轮 C语言余弦加速一、从动件位移、速度、加速度曲线绘制绘制从动件位移、速度、加速度曲线需外界输入H、j1、j2、j3、j4五个数据,将屏幕初始化后,画出坐标轴,然后以横轴为角度(j),纵轴为位移(S)、速度(dS)、加速度(d2S),角度每变化一度,作出相应的位移、速度、加速度,当j从0度变化到360度时,即得到相应的位移、速度、加速度曲线。
二、凸轮轮廓绘制及动画显示凸轮机构的运动过程1、凸轮轮廓绘制提示信息,有外界输入R、E、H、j1、j2、j3、j4七个数据,然后将屏幕初始化。
画出坐标轴,基圆。
由于凸轮工作时为逆时针转动,根据“反转法”,画凸轮轮廓曲线时应顺时针描点。
本实验首先用白线画出基圆及凸轮轮廓,然后用红线将凸轮轮廓顺时针描一遍。
2、动画显示凸轮机构的运动过程实现凸轮动态转动的总体理论:首先用白线画出凸轮轮廓,然后用黑线将白线凸轮轮廓抹掉,接着再用白线画出下一角度的凸轮轮廓,用delay函数延时一定时间,即可得到凸轮机构动态过程。
具体实现:本实验的凸轮动态过程用三个for循环实现,最外层for循环控制角度j 的变化(即控制凸轮机构转动的位置),内部并列两个for循环,作用分别为用黑线和白线画凸轮。
凸轮机构设计实验报告体会与建议

凸轮机构设计实验报告体会与建议凸轮机构设计实验报告一、引言凸轮机构是一种常见的传动机构,广泛应用于各种机械设备中。
本次实验旨在通过设计一个简单的凸轮机构,加深对凸轮机构原理和设计方法的理解,并通过实际操作验证设计结果的正确性。
二、实验目的1. 理解凸轮机构的工作原理和基本结构;2. 学习凸轮曲线的绘制方法;3. 设计一个满足特定要求的凸轮机构;4. 通过实验验证设计结果。
三、实验步骤1. 确定要求:根据给定要求,确定凸轮机构所需完成的任务和性能指标。
2. 绘制凸轮曲线:根据所需任务和性能指标,选择适当的凸轮曲线类型,并利用图纸或计算软件绘制出相应的凸轮曲线。
3. 设计从动件:根据所绘制的凸轮曲线,确定从动件(如滚子或推杆)与凸轮之间的运动关系,并进行相应尺寸设计。
4. 设计传动装置:根据从动件与被驱动件之间的运动关系,选择合适的传动装置(如连杆机构或齿轮传动)进行设计。
5. 组装凸轮机构:按照设计结果,将凸轮、从动件和传动装置进行组装,并进行必要的调试和修正。
6. 进行实验验证:通过实验验证凸轮机构是否满足要求,如运动精度、工作稳定性等。
四、实验结果根据所给要求,我们设计了一个满足特定任务和性能指标的凸轮机构。
经过实验验证,该凸轮机构能够正常工作,并且满足了运动精度和工作稳定性的要求。
在不同负载条件下,凸轮机构均能保持稳定的工作状态,并且输出运动符合预期。
五、体会与建议通过本次实验,我对凸轮机构的原理和设计方法有了更深入的理解。
在设计过程中,我发现绘制凸轮曲线是关键步骤之一,需要掌握绘制方法并注意曲线的光顺性和连续性。
在选择从动件和传动装置时,需要考虑其与凸轮曲线之间的运动关系以及整个系统的稳定性。
对于今后的改进与优化,我建议可以进一步研究凸轮曲线的优化方法,以提高凸轮机构的运动精度和工作效率。
同时,可以尝试使用更先进的材料和制造工艺,以提高凸轮机构的耐久性和可靠性。
凸轮机构设计实验为我提供了一个实践操作的机会,加深了对凸轮机构原理和设计方法的理解。
基于Pro/E的摆动从动件盘形凸轮设计
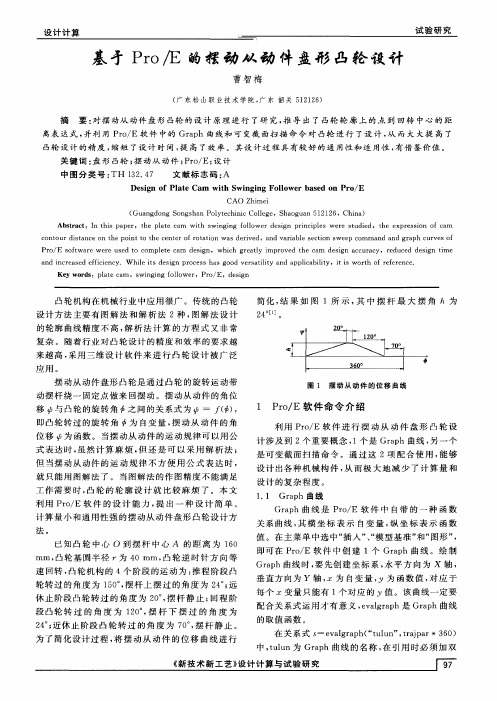
关 键词 : 盘 形 凸轮 ; 摆 动从 动件 ; P r o / E; 设 计
中图分 类号 : TH 1 3 2 . 4 7
文献标 志 码 : A
CA 0 Zhi me i
D e s i g n o f P l a t e Ca m wi t h S wi n g i n g F o l l o w e r b a s e d o n P r o / E
法 。
图 1 摆 动 从 动 件 的 位 移 曲线
1 P r o / E软 件 命 令 介 绍
利用 P r o / E软 件 进 行 摆 动 从 动件 盘 形 凸轮 设 计 涉及 到 2个重 要概 念 , 1 个 是 Gr a p h曲线 , 另 一个
是可变 截 面扫描 命 令 。通 过 这 2项 配合 使 用 , 能够
应用。
摆 动从 动件 盘形 凸轮是 通过 凸轮 的旋 转运 动带 动摆杆 绕 一 固定 点做 来 回摆 动 。摆 动从 动 件 的角位 移 与 凸轮 的旋转 角 之 间 的关 系式 为 一 厂 ( ) , 即凸轮 转 过 的旋 转 角 为 自变量 , 摆 动从 动 件 的角 位 移 为 函数 。当摆动 从动 件 的运动 规律 可 以用公 式 表达 时 , 虽然 计算 麻烦 , 但 还是 可 以采 用 解 析 法 ; 但 当摆 动从 动件 的运 动 规 律 不方 便 用 公 式 表 达 时 , 就 只能 用 图解法 了。 当图解 法 的作 图精度 不能 满足 工作 需要 时 , 凸 轮 的 轮廓 设 计 就 比较 麻 烦 了。本 文 利用 P r o / E软 件 的设 计 能 力 , 提出一种设计 简单、 计算 量 小 和通用性 强 的摆 动从 动件 盘形 凸轮设 计 方
实验六 凸轮机构实验

实验六 凸轮机构实验一、实验目的1.熟悉凸轮机构的结构组成,学会控制并观察它们的运动过程;2.掌握机构运动参数测试的原理和方法,了解两种机构从动件位移、速度、加速度的变化规律。
二、实验设备及工具1.凸轮机构实验台;2.活动扳手,固定扳手,内六角扳手,螺丝刀,钢直尺。
三、 实验台结构及工作原理1.凸轮机构实验台凸轮机构实验台,由盘形凸轮、圆柱凸轮和滚子推杆组件构成,提供了等速运动规律 、等加速等减速运动规律、多项式运动规律、余弦运动规律、正弦运动规律、改进等速运动规律、改进正弦运动规律、改进梯形运动规律等八种盘形凸轮和一种等加速等减速运动规律的圆柱凸轮供检测使用,可拼装平面凸轮和圆柱凸轮两种凸轮机构。
主要构件尺寸参数如下:盘形凸轮:基圆半径为 mm R 400=最大升程为 mm H 15max =圆柱凸轮:升程角为 150=α升程为 mm H 5.38=2.数据采集系统实验台采用单片机与A/D 转换集成相结合进行数据采集,处理分析及实现与PC 机的通信,达到适时显示运动曲线的目的。
该测试系统先进、测试稳定、抗干扰性强。
同时该系统采用光电传感器、位移传感器作为信号采集手段,具有较高的检测精度。
数据通过传感器与数据采集分析箱将机构的运动数据通过计算机串口送到PC 机内进行处理,形成运动构件运动参数变化的实测曲线,为机构运动分析提供手段和检测方法。
本实验台电机转速控制系统有两种方式:手动控制:通过调节控制面板上的液晶调速菜单调节电机转速。
软件控制:在实验软件中根据实验需要来调节。
其原理框图如下:四、注意事项1.机构运动速度不易过快。
2.机构启动前一定要仔细检查联接部分是否牢靠;手动转动机构,检查曲柄是否可整转。
3.运行时间不宜太长,隔一段时间应停下来检查机构联接是否松动。
4.因振动和干扰等原因,采集曲线会有毛刺。
六、实验报告及思考题1.选取合理的数据,绘制凸轮机构的从动件运动规律曲线(主动件旋转一周,从动件的位移、速度、加速度的变化规律)。
凸轮机构设计实验报告体会与建议

凸轮机构设计实验报告体会与建议引言凸轮机构是机械传动系统中常用的机械元件,用于实现复杂的运动变换。
在凸轮机构的设计实验中,我们对凸轮机构的结构、运动学和动力学性能进行了研究和测试。
本报告将总结我们在实验中的体会和经验,并提出一些建议用于改进凸轮机构的设计。
实验目的1.掌握凸轮机构的结构和运动学特性;2.进行凸轮机构的动力学性能测试;3.分析凸轮机构的不足之处,并提出改进方案。
实验方法1. 凸轮机构的结构凸轮机构由凸轮、从动件和传动件组成。
我们首先了解了凸轮的特点和凸轮曲线的设计方法。
然后选择了合适的从动件和传动件,完成了凸轮机构的总体结构设计。
2. 凸轮机构的运动学分析为了了解凸轮机构的运动学特性,我们使用理论计算和模拟仿真的方法进行分析。
通过分析凸轮的几何参数、从动件的运动规律和传动件的速度变化,我们得出了凸轮的轮廓曲线、从动件的位移-时间曲线和传动件的速度-时间曲线。
3. 凸轮机构的动力学测试为了测试凸轮机构的动力学性能,我们进行了实际的实验。
我们测量了凸轮机构的负载、转速和功率,并分析了凸轮机构的动力学特性,如动态特性、能量转换和损耗。
实验结果与讨论1. 凸轮机构的结构设计结果我们设计了一个具有合理几何参数的凸轮,使从动件能够按照预定的规律运动。
从动件和传动件的选择也符合凸轮机构的传动要求。
2. 凸轮机构的运动学分析结果通过理论计算和模拟仿真,我们获得了凸轮的轮廓曲线、从动件的位移-时间曲线和传动件的速度-时间曲线。
我们发现凸轮机构的运动学性能与凸轮的几何形状、从动件的工作范围和传动件的速度比等因素密切相关。
3. 凸轮机构的动力学测试结果在实际测试中,我们发现凸轮机构的负载、转速和功率与凸轮的几何参数、从动件的工作负荷和传动件的摩擦有关。
我们还观察到了凸轮机构的动态特性、能量转换和损耗等现象。
结论凸轮机构是一种重要的机械传动元件,具有复杂的结构和运动学、动力学特性。
通过实验和分析,我们对凸轮机构的设计、运动学和动力学性能有了更深入的理解。
- 1、下载文档前请自行甄别文档内容的完整性,平台不提供额外的编辑、内容补充、找答案等附加服务。
- 2、"仅部分预览"的文档,不可在线预览部分如存在完整性等问题,可反馈申请退款(可完整预览的文档不适用该条件!)。
- 3、如文档侵犯您的权益,请联系客服反馈,我们会尽快为您处理(人工客服工作时间:9:00-18:30)。
(4)
1
6
或
2 2 450 J 0 (ω0max ω0min ) JF 2 δ 2 nm
(5)
式中: n m ——主轴的转速,r/min 。 当给定机械系统主轴的转速速度 nm,给定(或计算得到)机械系统的等效转 动惯量 J0,通过实际测量可得未安装飞轮时主轴的最大角速度0max 和最小角速 度0min 后,对应不同的许用不均匀系数[],即可求得所要安装的飞轮的转动惯 量 JF
2 Bρ 4 m D12 D2 JF D1 D24 2 4 32
(7)
图1
辐条飞轮
2
6
当根据飞轮在机械中的安装空间, 选择了轮缘平均直径 D (D
D1 D2 ) , 2
再选定飞轮的材料(密度为 )和(H/B) (通常取 H/B=2)值后,即可得到飞 轮的结构尺寸:D1,D1,B。 (2)盘形飞轮 当飞轮的转动惯量不大时, 可采用形状简单的盘形飞轮, 如图 2 所示。 设m、
(kgmm2)
(kgmm2)
(kgmm2)
0º 30º 60º 90º
等效转动惯量的平均值 J0
120º 150º 180º 210º 30000
240º 270º 300º 330º
(kgmm ) (2)不安装飞轮,启动设备,将主轴(曲柄)的转速调到 nm=120r/min,待机 器稳定运动后,测量得出主轴(曲柄)的角速度曲线,得到未安装飞轮时主轴的 最大角速度0max 和最小角速度0min 值,计算得出不均匀系数0 的大小。 (3) 在下表中 选取一个许用的不均匀系数[],依据式(6)计算出在主轴转 速为 nm=120r/min 和 nm=150r/min 时所需要安装飞轮的转动惯量 JF 的大小。 表 2 许用不均匀系数[]取值
4. 实验操作注意事项 (1)开机前的准备:初次使用时,需仔细参阅本产品的说明书,特别是注 意事项。 a. 拆下有机玻璃保护罩用清洁抹布将实验台, 特别是机构各运动构件清理干 净,加少量 N68~48 机油至各运动构件滑动轴承处; b. 面板上调速旋钮逆时针旋到底(转速最低) ; c. 用于转动曲柄盘 1~2 周,检查各运动构件的运行状况,各螺母紧固件应 无松动,各运动构件应无卡死现象。 一切正常后,方可开始运行按实验指导书的要求操作。 (2)开机后注意事项: a. 开机后,人不要太靠近实验台,更不能用手触摸运动构件; b. 调速稳定后才能用软件测试。测试过程中不能调速,不然测曲线混乱,不 能反映周期性; c. 测试时,转速不能太快或太慢。因传感器量程,软件采集不到数据,将自 动退出系统或死机。
ω0 min ——未安装飞轮时主轴的最小角速度,rad/s; ωmax ——安装飞轮时主轴的最大角速度,rad/s; ωmin ——安装飞轮时主轴的最小角速度,rad/s。
依据式(3) ,进一步推导得飞轮的转动惯量 JF 为:
2 2 J 0 (ω0max ω0min ) JF 2 2 δωm
5
6
主轴(曲柄)的角速度曲线,得到主轴的最大角速度max 和最小角速度min 值, 计算得出不均匀系数的大小。 (8) 比较速度不同,其他条件不变情况下,速度波动调节的效果,分析速度大 小对速度波动调节效果的影响。 (9)整理实验数据,完成实验报告。 选取飞轮的材料为钢(密度=7800kg/m3) ,根据飞轮的结构形式,设计计算出 飞轮的几何尺寸。
D 和 B 分别为其质量、外径及宽度,则飞轮的转动惯量为
m D ρBD 4 Jf 22 32
的宽度 B 为
2
(8)
当根据安装空间选定飞轮直径 D 后,据飞轮的材料(密度为 ) ,求出飞轮
B
4m
D 2
(9)
图2 2.实验设备
盘形飞轮
实验台如图 3 所示,其结构组成示意图如图 4 所示。
[W ]
1 1 2 2 2 2 J 0 (ω0max ω0min ) ( J 0 J F )(ωmax ωmin ) 2 2
(3)
式中: J 0 ——机械系统的等效转动惯量,kgmm2;
J F ——飞轮的转动惯量 ,kgmm2;
ω0 max ——未安装飞轮时主轴的最大角速度,rad/s;
(1)
式中: max ——主轴的最大角速度,rad/s;
min ——主轴的最小角速度,rad/s;
m ——主轴的平均角速度,rad/s,
m
max min 2
(2)
机械周期性速度波动的调节,就在在机械系统的主轴(或其它轴上)上安装 一个飞轮, 使机械系统的主轴运转速度波动程度减小,即减小机械系统的运转速 度不均匀系数 δ,使其不超过许用值 。 在一个周期中最大动能 Emax 与最小动能 Emin 之差称为最大盈亏功 W ,即
3
6
图 3 实验台
图 4 实验台组成示意图
实验台的主体机构为一偏置曲柄滑块机构,机构运动简图如图 5 所示。已知 条件为:曲柄长 lAB=50mm,连杆长 lBC=180mm;连杆质心 S2 到 B 点的距离、 lBS2=45mm,偏距 e=20mm;曲柄 1 的绕 A 轴的转动惯量 J1=7040.125 kgmm2, 连杆 2 的质量 m2=0.579 ㎏,连杆绕质心 S2 的转动惯量 JS2=8100kgmm2,滑块质 量 m3=0.335kg。
0.3 0.27 0.25
2
(4) 选取飞轮的材料为钢(密度=7800kg/m3) ,根据飞轮的结构形式,设计 计算出飞轮的几何尺寸。 依据所计算的飞轮几何尺寸,选取满足速度波动调节要 求的飞轮。 (5 ) 将飞轮安装到实验台上,启动设备,将主轴(曲柄)的转速调到 nm= 150r/min,待机器稳定运动后,测量得出主轴(曲柄)的角速度曲线,得到安装 飞轮时主轴的最大角速度max 和最小角速度min 值,计算得出不均匀系数的大 小。 (6) 判断此飞轮的速度波动调节是否满足要求。 (7)将主轴(曲柄)的转速调到 nm=150r/min,待机器稳定运动后,测量得出
6
B 1 A M1 C S2 2
e
F3 4 3
图 5 偏置曲柄滑块机构
3.实验步骤 (1)曲柄 1 从水平位置开始,按 30º的间隔,计算曲柄为转换件时的等效转动 惯量 Je 的大小,填于表 1,并求出等效转动惯量的平均值 J0。
4
6
表 1e 曲柄转角1 (º) 等效转动惯量 Je 曲柄转角1 (º) 等效转动惯量 Je
2 2 450 J 0 (ω0max ω0min ) JF 2 2 [δ ] nm
(6)
确定飞轮的转动惯量后, 便可根据所希望的飞轮结构,按理论力学中有关不 同截面形状的转动惯量计算公式,求出飞轮的主要尺寸。飞轮按构造大体可分为 轮形和盘形两种。 (1)辐条飞轮 如图 1 所示,这种飞轮由轮毂、轮辐和轮缘三部分组成。因轮辐和轮毂的转 动惯量比轮缘小得多,因此,这两部分转动惯量一般可略去不计,将飞轮转动惯 量取为轮缘转动惯量。 这样简化后, 飞轮的实际转动惯量稍大于计算的转动惯量。 设飞轮外径为 D1 ,轮缘内径为 D2 ,轮缘质量为 m ,则轮缘的转动惯量为
6
机械系统周期性速度波动调节实验
1.理论基础 机械系统在运动运转阶段,机械主轴的角速度呈现周期性速度波动的特点。 在一个周期内, 当不考虑摩擦等有害阻力的损耗功时,驱动力所做的输入功等于 工作阻力所做的阻抗功。主轴速度运转的波动程度,用运转速度不均匀系数 δ 来 衡量:
max min m