[VIP专享]年产4万吨低氧铜杆废铜连铸连轧生产线(拉法格倾动炉)
无氧铜杆连铸连轧生产线
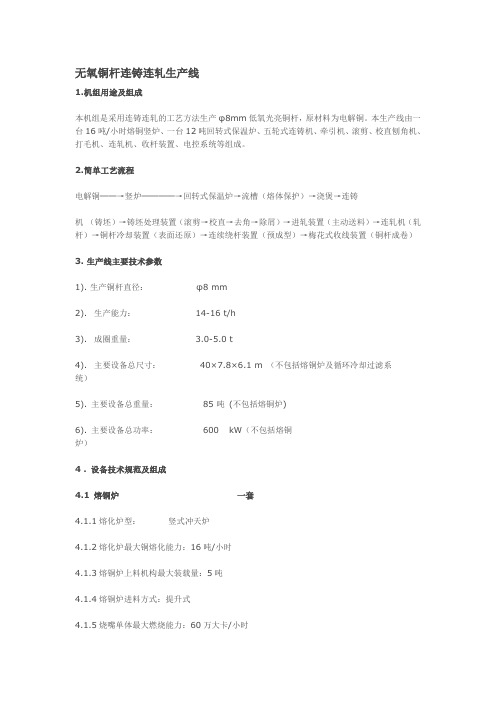
无氧铜杆连铸连轧生产线1.机组用途及组成本机组是采用连铸连轧的工艺方法生产φ8mm低氧光亮铜杆,原材料为电解铜。
本生产线由一台16吨/小时熔铜竖炉、一台12吨回转式保温炉、五轮式连铸机、牵引机、滚剪、校直刨角机、打毛机、连轧机、收杆装置、电控系统等组成。
2.简单工艺流程电解铜──→竖炉────→回转式保温炉→流槽(熔体保护)→浇煲→连铸机(铸坯)→铸坯处理装置(滚剪→校直→去角→除屑)→进轧装置(主动送料)→连轧机(轧杆)→铜杆冷却装置(表面还原)→连续绕杆装置(预成型)→梅花式收线装置(铜杆成卷)3. 生产线主要技术参数1). 生产铜杆直径:φ8 mm2). 生产能力:14-16 t/h3). 成圈重量: 3.0-5.0 t4). 主要设备总尺寸: 40×7.8×6.1 m (不包括熔铜炉及循环冷却过滤系统)5). 主要设备总重量: 85 吨(不包括熔铜炉)6). 主要设备总功率: 600 kW(不包括熔铜炉)4 .设备技术规范及组成4.1熔铜炉一套4.1.1熔化炉型:竖式冲天炉4.1.2熔化炉最大铜熔化能力:16吨/小时4.1.3熔铜炉上料机构最大装载量:5吨4.1.4熔铜炉进料方式:提升式4.1.5烧嘴单体最大燃烧能力:60万大卡/小时4.1.6熔铜炉烧嘴数量:15只4.1.7烧嘴冷却方式:水冷4.1.8烧嘴点火方式:自动4.1.9使用燃料:天然气、液化气、城市煤气4.1.10保温炉炉型:液压回转式4.1.11保温炉有效容量:12吨4.1.12保温炉最高倾力角度:>70º4.1.13烧嘴单体最大燃烧能力:60万大卡/小时4.1.14保温炉烧嘴数量:1只4.1.15燃烧控制方式:比例燃烧,具有保护装置4.1.16燃气阀检漏方式:手动/自动熔铜炉包括冲天式铜熔化炉、回转式保温炉、上下流槽、燃烧控制系统等四大部分。
具有熔化速度快、铜水含氧量低、流量连续可调、铜水温度独立可控、单位铜水燃气消耗量低等特点。
浅析杂质元素对铜杆质量的影响

引法连 铸  ̄ m 杆时加 入 过多 的紫 杂 铜 或 回炉 料 , b m 8 导 致 多种 杂质元 素进 入 炉 内 , 其 在生 产 高 端产 品 时基 使 本 不达 标 , 后续 拉制 过 程 中断 线 率 非常 高 。 图 1为 在
广东 某 铜加工 企 业 在 上 引炉 内加 入 3 % 的一 r ez 法 C Po ri p
( ) 。这 些杂质 元素含 量在 一定 范 围时对 铜杆 塑 性 P等 及 热加 工性 能 无太 大影 响 , 能 稍微 提 高 铜 的 硬 度 , 还 但却 降低 了铜 杆 的导 热 性 或导 电性 , 还有 可 能影 响铜 的冷加 工性能 。当杂质 元 素含 量 超 出允 许范 围时 , 不 但 降低 铜杆 的塑性 和加 工 性 能 , 会 降低 铜 杆 的导 热 更
1 1 较 多固溶 于铜的 杂质元 素对铜 杆 的影响 .
素很多 , 目 但 前我国在大量紫杂铜或废杂铜直接用于
铜 杆生产 的情 况下 , 出 的 问题就 是 能 否提 高铜 杆 的 突
“ 轧 性 ” “ 拉 性 ” “ 退 火 性 ” 这 是 铜 线 材 生 产 可 、可 及 可 , 的 技 术 质 量 核 心 和 发 展 方 向 。
作 者 通 讯 : 云 ( 9 4一) 男 , 读 硕 士 研 究 生 , 要 从 事 有 色 金 罗 18 , 在 主
属加工成型理论与应用研究。
液 的流 动性 , 磷 作 为 杂 质 进 入 铜 固熔 体 内, 但 即使 极
第 3期
有 色 金 属 加 工
2 7
其微 量 也 会 严 重 降 低 铜 电 导 率 。另 外 , 生 产 过 程 在 中, 易进 入铜 液 中 的 杂 质 元 素 还 有 锌 、 、 、 等 金 铬 锰 钙 属元 素 , 这些 元 素的共 同特性 是 能 较 大 降低 铜 的 导 电
2024年无氧铜杆市场规模分析

2024年无氧铜杆市场规模分析引言无氧铜杆是一种重要的铜制品,具有优良的导电性和导热性能。
它在电子、电力、交通等领域广泛应用。
本文将对无氧铜杆市场的规模进行深入分析。
市场概况市场定义无氧铜杆市场是指无氧铜杆生产和销售的市场,涉及的主要产品包括精密无氧铜杆、扁平无氧铜杆等。
市场发展历程随着电子、电力行业的快速发展,无氧铜杆市场得到了迅猛的增长。
近年来,随着新能源等行业的兴起,无氧铜杆市场的发展进入了新的阶段。
市场趋势1.高导电性需求增加:随着电子设备的普及和电力需求的增长,对高导电性的无氧铜杆的需求将持续增加。
2.新能源产业发展:无氧铜杆是太阳能、风能等新能源设备的重要组成部分,新能源行业的快速发展将带动无氧铜杆市场的增长。
3.环保要求提高:随着环保意识的提高,对无氧铜杆的环保性能要求也在不断增加,市场上具备环保认证的产品将受到青睐。
市场规模分析产量分析无氧铜杆市场的产量受到生产能力和市场需求的影响。
根据统计数据显示,过去五年内无氧铜杆市场的年均产量保持了稳定的增长,预计未来几年内产量将继续增加。
销售额分析无氧铜杆市场的销售额与市场需求和产品价格密切相关。
根据市场调研数据显示,过去五年内无氧铜杆市场的年均销售额呈现出稳步增长的趋势。
市场需求分析无氧铜杆市场的需求主要受到电子、电力、交通等行业的影响。
随着这些行业的持续发展,无氧铜杆的需求将保持稳定增长。
此外,新能源等行业的崛起也将促进无氧铜杆市场的需求增加。
市场竞争分析无氧铜杆市场竞争激烈,主要的竞争者包括国内外的生产厂商。
国内生产厂商占据了市场的主导地位,具备较高的市场份额。
而国外厂商则通过技术创新和产品优势来争夺市场份额。
市场前景展望随着电子、电力、交通等行业的不断发展,无氧铜杆市场的前景十分广阔。
预计未来几年内,无氧铜杆市场的规模将继续扩大,并且市场竞争将进一步加剧。
为了在激烈的市场竞争中取得竞争优势,无氧铜杆企业需要加强技术创新、提高产品质量,并注重环保要求,以满足市场需求。
广州江铜40万吨铜杆线项目联动试车成功

广州江铜40万吨铜杆线项目联动试车成功
佚名
【期刊名称】《《中国金属通报》》
【年(卷),期】2012(000)034
【摘要】8月24日下午,随着钟大拉生产线联动试车成功,并生产出合格铜线产品,广州江铜40万吨铜杆线项目联动试车全部结束,全面进入试生产阶段。
8月7日,广州江铜铜材公司正式启动40万吨铜杆线项目联动试车工作。
当天,华南地区产量最大、最先进的CR3700生产线蛏炉开始点火熔铜,
【总页数】1页(P6-6)
【正文语种】中文
【中图分类】TQ225.3
【相关文献】
1.广州江铜铜材打造华南最大铜杆线生产基地 [J],
2.广州江铜40万t铜杆线项目联动试车成功 [J],
3.10万吨/年石膏粉生产线联动试车成功 [J],
4.50万吨合成氨、80万吨尿素项目试车成功 [J],
5.江钨集团年产60万吨再生铜杆(线)项目落户河南大周 [J],
因版权原因,仅展示原文概要,查看原文内容请购买。
年产4万吨低氧铜杆废铜连铸连轧生产线(拉法格倾动炉)

年产4万吨低氧铜杆废铜连铸连轧生产线(选用拉法格倾动炉)初步可行性研究分析上海浦东力生电工机械有限公司2013年6月25日目录一.总论二.厂址三.建设方案四.环境保护、职业安全与卫生五.节能与能耗六.消防七.人员培训八.原料供应九.投资估算十.经济评估及投资回收期十一. 初步可行性研究分析的结论和建议1.总论1.1 项目名称年产4万吨低氧铜杆废铜连铸连轧生产线项目。
(选用拉法格倾动炉)1.2 低氧铜杆的基本情况按照我国现行标准GB/T3952-2008规定,用于导体的铜杆分为两大类:低氧铜杆和无氧铜杆(合金铜杆除外)。
用电解铜生产的无氧铜杆牌号为TU1、TU2,低氧铜杆牌号为T1、T2;用废铜生产的无氧铜杆和低氧铜杆的牌号统称为T3。
所有牌号的铜杆的电性能、机械性能、化学成份等各项指标均可在标准中查得。
1.3 立项背景(1)我国改革开放三十多年来,国民经济高速发展,随着城乡人民生活水平的不断提高,促使我国电力工业的飞速发展。
我国已成为世界第一用铜大国,2007年国内导体用铜从2000年的172万吨增至378万吨,2008年达到了412万吨。
这几年都在快速增长,预计到2015年将达到705万吨。
(2)我国的铜资源非常贫乏,每年用铜量的大部分靠国外进口,世界的铜资源也很有限,所以每年大量进口废铜。
同时我国正成为世界最大的废铜产生国,拆拣废铜、再生利用,符合循环经济可持续发展的规律,是科学发展观的体现。
(3)长期以来,我国没有先进的装备和工艺用于废铜作为原料生产低氧铜杆,只是利用反射炉进行冶炼。
反射炉炼铜污染不易治理、能耗高、产品质量差,所以早在1997年3月国家发出通知,淘汰反射炉炼铜。
去年,由上海电缆研究所黄院士牵头,申报用西班牙拉法格炉子炼铜连铸连轧生产低氧铜杆的项目获得国家有关部门批准,研发工作正在进行中。
(4)西班牙拉法格的FRHC废杂铜精炼技术,使低氧铜杆的品质大为提高,含铜量大于99.93%,导电率大于100.4%IACS,最高可到100.9%IACS。
2024年无氧铜杆市场前景分析

2024年无氧铜杆市场前景分析引言无氧铜杆是一种重要的导电材料,在电工、电子、汽车、航空航天等领域都有广泛应用。
本文将深入分析无氧铜杆市场的前景,并探讨市场发展趋势和推动因素。
市场概述无氧铜杆的定义与特点无氧铜杆,又称电解铜杆,是指通过电解工艺在无氧条件下制备的铜杆,具有高纯度、优异的导电性能和耐腐蚀性能。
无氧铜杆广泛应用于电线电缆、电机、变压器等领域。
市场规模与发展趋势随着电动汽车、新能源设备等行业的快速发展,无氧铜杆市场呈现出良好的发展势头。
根据市场调研数据显示,全球无氧铜杆市场规模逐年增长,预计未来几年将保持稳定增长。
市场驱动因素电动汽车市场的快速增长电动汽车市场的快速增长是推动无氧铜杆市场发展的重要驱动因素。
电动汽车采用大量的无氧铜杆制成的线缆和线圈,因其导电性能优越,能有效提高电动汽车的性能和功率输出。
新能源设备的普及随着新能源设备的不断普及,如太阳能光伏发电、风力发电等,无氧铜杆的需求也在逐渐增加。
这些新能源设备都需要大量的无氧铜杆作为导电材料,以确保设备的高效稳定运行。
工业自动化的提升随着工业自动化水平的不断提升,对高品质导电材料的需求也在增加。
无氧铜杆作为优质导电材料之一,可以满足工业自动化设备对高速传输、低能耗的要求。
市场挑战与风险原材料价格波动无氧铜杆的生产需要大量的铜矿石作为原材料,铜矿石价格的波动性对无氧铜杆市场造成一定影响。
原材料价格上涨可能增加无氧铜杆的生产成本,影响市场竞争力。
环保压力与能源消耗无氧铜杆的生产过程相对能源密集,对环境造成一定的压力。
随着环保意识的提升,市场对环保型无氧铜杆的需求将越来越高,企业需要加大技术研发和创新,提高生产效率和降低能源消耗。
市场前景展望无氧铜杆市场前景广阔,有以下几个方面的发展趋势值得关注:1.技术创新:随着科技的进步,无氧铜杆的制造工艺将不断改进,不仅能够提高纯度和导电性能,还能减少能源消耗和环境污染。
2.市场竞争:市场竞争将更加激烈,企业需要不断提高产品质量、降低成本,提升市场竞争力。
工艺验证方案

文件编号:******* 版本号:00 *****工艺再验证方案*****有限公司验证方案目录1.概述 (3)1.1产品基本信息 (3)1.2验证背景 (3)1.3验证目的 (3)1.4适用范围 (3)2.职能部门及职责 (4)3.风险评估 (4)3.1目的 (4)3.2范围 (4)3.3评估方法 (4)3.4评估标准 (5)3.5风险评估结果及风险控制 (5)4.验证项目、接受标准、实测结果及验证结论 (9)4.1验证文件确认 (9)4.2设备、设施及公用系统确认 (10)4.3关键人员确认 (11)4.4工艺参数控制确认 (12)4.5成品质量确认 (14)4.6稳定性考察试验 (15)4.7偏差和变更控制 (15)5.验证结果评定与结论 (15)6.时间进度安排 (15)7.附件附件1:称量情况确认表附件2:制粒生产过程记录表附件3:压片生产过程记录表附件4:包装质量检查记录表其他附件:合格物料供应商名单、中间产品报告单、成品报告单、生产记录、培训记录、药品生产工艺验证合格证1.概述1.1产品基本信息1.1.1产品名称:***1.1.2产品剂型:片剂1.1.3产品规格:***1.1.4药品批准文号:国药准字***1.1.5制剂批量:***1.1.6内包装:****1.1.7产品有效期:***1.1.8制剂生产工艺流程图:1.2验证背景****为我公司中药制剂品种,制剂生产工艺于***年进行了再验证,验证结果判定为合格。
***年月因生产需要,*******。
1.3验证目的按照GMP及“附录2 确认与验证”的要求,应对*****制剂生产工艺进行再验证,以证明*******按照现行批准的生产工艺仍能生产出符合GMP要求、质量标准及注册标准要求的*****。
1.4适用范围本验证方案适用于本方案指定的厂房、设施、设备、公用系统、批准的工艺规程、批生产记录、标准操作规程进行生产,并连续生产3个批次,根据验证方案的要求进行取样,并按质量标准、经验证的分析方法进行检测。
合肥院EP项目巴西MIZU水泥厂投产

仪 式 结 束 后 ,集 团公 司 马建 国副 总 经 理 与 业 主就 双方在 风力 发 电、商 品混凝土 等其他 领域 开展
岷 县 签 海 螺 1 亿 元新 型 干法 水 泥 生产 项 目 0
立 足 南 疆 面 向全 疆
争通过3 年 时间,打造青松化 工产业规模 。” ~5 青松 建化 以参股 方式 涉足 的 电力 、煤炭 、新 能 源 行业 即将 开花 结果 。甘 军介 绍说 : “ 司与 国 电 公
集 团合资建设 的库车 大平滩年产2 0 4 万吨煤矿 明年底
近 年来 ,在甘 军 的率 领下 ,青松 建化 “ 立足 南
方 资源 ,帮助青 松建化 获得 哈密 及乌苏 的煤炭 资源 项 目,并在 其他 煤炭 、石油 、天然 气等 资源项 目上 向青松建化倾斜 。
今 年 4 ,阿拉 尔青 松 化工 一期 1 万 吨烧 碱 l 月 0 2
万吨P c 目提前试车投 产 。甘军说 : “ V项 青松建化建
合肥院E 项 目巴西…z 水泥厂投产 P U
合 肥 院E 工 程 一 巴西 M R C M N O 水 泥 公 司 P A E IE T S
泥生产 商V t r n 集 团共 同投 资 的水 泥项 目,厂 o o at m i
址位 于 巴西 北 部 N t lH a a n 市 。 a a 4 B ru a 、
M Z 水泥厂 日产 3 0 吨熟料 生产 线于2 1年 5 4 IU 00 0 2 月2 日 正式投 料试 生产 。中 国建材集 团公 司副总 经理 马建 国 、合 肥 院副院长 陈章 水 、院工程 公司 副总经 理兼 该项 目的项 目经理黄志远等应邀参加了庆 典。 该 生产线 是 巴西最大 的混凝土 制造商P lm x o y i 集
- 1、下载文档前请自行甄别文档内容的完整性,平台不提供额外的编辑、内容补充、找答案等附加服务。
- 2、"仅部分预览"的文档,不可在线预览部分如存在完整性等问题,可反馈申请退款(可完整预览的文档不适用该条件!)。
- 3、如文档侵犯您的权益,请联系客服反馈,我们会尽快为您处理(人工客服工作时间:9:00-18:30)。
年产4万吨低氧铜杆废铜连铸连轧生产线(选用拉法格倾动炉)初步可行性研究分析上海浦东力生电工机械有限公司2013年6月25日目录一一总论一一厂址一一建设方案一一环境保护、职业安全与卫生一一节能与能耗一一消防一一人员培训一一原料供应一一投资估算一一经济评估及投资回收期十一. 初步可行性研究分析的结论和建议1.总论1.1 项目名称年产4万吨低氧铜杆废铜连铸连轧生产线项目。
(选用拉法格倾动炉)1.2 低氧铜杆的基本情况按照我国现行标准GB/T3952-2008规定,用于导体的铜杆分为两大类:低氧铜杆和无氧铜杆(合金铜杆除外)。
用电解铜生产的无氧铜杆牌号为TU1、TU2,低氧铜杆牌号为T1、T2;用废铜生产的无氧铜杆和低氧铜杆的牌号统称为T3。
所有牌号的铜杆的电性能、机械性能、化学成份等各项指标均可在标准中查得。
1.3 立项背景(1)我国改革开放三十多年来,国民经济高速发展,随着城乡人民生活水平的不断提高,促使我国电力工业的飞速发展。
我国已成为世界第一用铜大国,2007年国内导体用铜从2000年的172万吨增至378万吨,2008年达到了412万吨。
这几年都在快速增长,预计到2015年将达到705万吨。
(2)我国的铜资源非常贫乏,每年用铜量的大部分靠国外进口,世界的铜资源也很有限,所以每年大量进口废铜。
同时我国正成为世界最大的废铜产生国,拆拣废铜、再生利用,符合循环经济可持续发展的规律,是科学发展观的体现。
(3)长期以来,我国没有先进的装备和工艺用于废铜作为原料生产低氧铜杆,只是利用反射炉进行冶炼。
反射炉炼铜污染不易治理、能耗高、产品质量差,所以早在1997年3月国家发出通知,淘汰反射炉炼铜。
去年,由上海电缆研究所黄院士牵头,申报用西班牙拉法格炉子炼铜连铸连轧生产低氧铜杆的项目获得国家有关部门批准,研发工作正在进行中。
(4)西班牙拉法格的FRHC废杂铜精炼技术,使低氧铜杆的品质大为提高,含铜量大于99.93%,导电率大于100.4%IACS,最高可到100.9%IACS。
目前在世界上使用该技术和设备的生产线有2O多条。
FRHC火法精炼的工艺和设备,主要为COS—MELT倾动炉。
该设备和工艺的精髓和核心是调整杂质成分和含氧量,而不是最大限度的去除杂质。
利用计算机辅助设计,找到各种元素相互化合后形成的微化合物铜合金,不影响铜杆的导电性能和机械性能。
因此,废杂铜通过FRHC火法精炼后,接近于纯净电解铜实际生产出一类微化合物铜合金,不影响铜杆的导电率,而且其再结晶软化温度、抗拉强度、扭曲次数等机械性能优异。
在长期导电状态和超常温状态下均能使用,适合于代替电解铜生产光亮铜杆。
(5)韩国在本世纪初就引进了西班牙拉法格的精炼技术和设备,主要为COS—MELT组合炉。
经过几年的摸索和改进,去除了组合炉中的竖炉,对倾动炉的结构和工艺作了改进,使该精炼技术又有很大的提高。
组合炉可处理含铜量96%以上的废铜,而倾动炉可处理94%以上甚至是92%以上的废铜。
倾动炉精炼,实现了燃烧风量和燃气流量比例的自动调节,使燃气完全燃烧,降低能耗;精炼炉熔化速度快,热效率高;倾动炉熔化温度低于国内固定式反射炉,炉子寿命长。
(6)上海浦东力生电工机械有限公司,与湖南湘潭汇智科技有限公司联合制造连铸连轧生产线。
并与韩国合作于2007年和2010年分别在韩国两家工厂,投产废铜连铸连轧生产线。
生产线的拉法格炉子和除尘设备由韩国生产制造,生产线运行情况很好。
力生公司正着手在浦东进行:与韩国合作生产拉法格炉子;与台湾合作生产除尘设备。
(力生公司2004年卖给马来西亚的废铜连铸连轧生产线的除尘设备,由台湾该公司生产制造)。
2.厂址项目配有环保除尘系统,能达到排放标准,主要燃料使用天然气,装机容量约1000KW,一般的工业园区都能容纳。
厂址选择,主要考虑原料废铜的供应,地域优势、政策的优势以及有利于生产经营。
3.建设方案3.1 生产纲领年产 8mm低氧铜杆4万吨。
3.2 项目建设方案生产车间:32m×120m 计3840平方米。
原料成品库:18m×120m 计2160平方米。
办公设施:可放在上述建筑内。
配电、水池、公用设施等。
3.3 技术方案(1)工艺流程(2)生产线80吨精炼炉2台,除尘系统2套(或共用1套),流槽系统1套,10吨保温炉1台,连铸连轧1套(每小时16-18吨)。
4.环境保护、职业安全与卫生4.1 环境保护原料为废铜,燃料为天然气,精炼炉配置除尘系统,达到排放标准。
冷却水无污染,循环使用。
噪声达标。
4.2 职业安全与卫生(1)车间高大宽敞,通风、采光良好,室内干净。
(2)设备电气均符合国家有关规定,且全部接地。
(3)操作平台、扶梯均有符合规定的栏杆、扶手。
(4)工人必须穿戴劳防用品。
5.节能与能耗(1)每吨铜杆消耗天然气约145m3,(西气东输天然气),消耗电约150KWH。
(2)水:循环使用,配冷却塔,不会造成水浪费。
(3)铜损耗与传统反射炉相比大为降低。
6.消防项目生产设备有大量电气柜、台,炼铜、连铸有铜水,需设置消防设施。
(1)整个车间的各个作业点,在适当的位置设置适量的灭火器。
(2)生产工艺中,需要使用冷却水,将生产用水系统作为消防系统的备用。
(3)在厂区内留出足够的消防通道。
7.人员培训生产人员、管理人员的培训分三个方面:(1)供方指导安装调试时,需方相关人员介入,边安装边培训。
(2)调试时边调试边培训。
(3)调试结束进入试生产,供方可派员留下(最长不超过3个月),边试生产边培训。
8.原料供应可联系废铜拆拣市场,签订合同,建立长期采购供应合作关系。
9.投资估算(人民币)固定资产投资:5000万元,流动资金投资:15000万元。
9.1 固定资产投资:4660万元(估算为5000万元)9.1.1 设备投资:3860万元A. 生产线投资:3230万元(1)炉子系统:①倾动式精炼炉系统:1927万元含80吨倾动炉2台,10吨保温炉1台,流槽系统1套,电控等。
②韩国工程师调试:58万元小计:1985万元(2)除尘系统:2套,350万元(3)连铸连轧:B型(新型)635万元其中:①机组:605万元。
②指导安装免费,调试8万元,试生产22万元。
(4)韩国精炼技术转让费:260万元A合计:3230万元注:运费还未测算出来,未计入。
B. 配套设备投资:180万元(1)测试设备、装载设备:约80万元(2)行车4台:100万元(5吨×32m 2台、5吨×18m 2台)小计:180万元C. 安装、公用设施投资:450万元合计:3860万元9.1.2 厂房、基础设施投资:800万元(1)车间:3840m2×1000元/m2计384万元(2)原料成品库:2160m2×1000元/m2计216万元(3)设备基础、公用设施、水池:200万元合计:800万元(4)说明:①配电房、1200KVA变压器,无法估计,均未计入。
②厂区道路均未列入。
③固定资产投资合计:4660万元。
④如土质不好,估计土建部分还会增加100-200万元,再加上配电房、变压器等,估计固定资产投资会超过5000万元。
9.2流动资金投资流动资金估算为:15000万元。
10.经济效益评估及投资回收期10.1 盈亏平衡点分析(1)年固定费用:项目生产人员:32人,辅助人员:10人,行政、管理人员:10人,计52人表10-1 年固定费用明细表序号名称数量金额(万元)201.60 1.工人、辅助人员工资福利4000元/月×12月×42人54.002.管理人员工资福利4500元/月×12月×10人3.设备折旧3860万元×0.95÷10年366.70 4.厂房折旧800万元×0.95÷10年76.005.管理费用30.006.资金利息5000万元×10%500.00合计:1228.30万元≈1228万元(2)单位变动费用:因铜价变化很大,所以按进、出差价计算,不含铜价。
表10-2 单位变动费用明细表(每吨废铜含铜量99%)序号名称数量金额(元)1.天然气150m3×3.50元/m3525.002.电150度×1.00元/度150.003.精炼剂25kg×5.00元/kg125.004.铜耗(1.5%)48000元/T×1.5%720.005.维修费(2%)5000万元×2%÷4万吨25.006.增值税3000元×14.53%436.007.流动资金利息15000万元×10%÷4万吨375.008.运费及其他144.00合计:2500.00(3) 销售价:4700元/T (含铜价销售价:52700元/T )① 铜价变化很大,以电解铜53000元/T 为例,含铜量99%的废铜含税价为48000元/T ,差价5000元/T 。
② 废铜低氧铜杆销售价为电解铜价格-300元/T ,即:52700元/T 。
③ 以差价计算:5000元/T -300元/T 计4700元/T 。
(4) 盈亏平衡点产量:X O ===5582吨式中:X O - 盈亏平衡点产量F - 年固定费用W - 售价(不含铜价)C V - 单位变动费用(不含铜价)盈亏平衡点产量占年产量的比率:5582吨÷40000吨=13.96%10.2 各项经济指标(年)(1) 年产量:4万吨(2) 销售额:5.27万元/T×4万吨 计:210800万元(21.08亿元)(3) 增值税:436元/T×4万吨 计:1744万元(4) 折 旧:366.7万元+76万元 计:442.7万元(5) 利 税:P =X (W-CV )-F=4万吨×(0.47万元-0.25万元)-1228万元=7572万元 式 中:P - 利税X - 年产量10.3 投资回收期F W -CV1228万元0.47万元-0.25万元(1)固定资产投资:5000万元,流动资金投资:15000万元,投资回收期按固定资产投资计算。
(2)工程建设期6个月,安装调试3个月,试生产3个月。
(3)达产年利税:7572万元,利润所得税25%,计:1893万元。
利润:7572万元-1893万元计5679万元。
注:本利税中没有计入土地费用、配电房、变压器费用,应减除。
(4)第一年应达到计划产量的70%。
(5)估计投资回收期为: 2.5年。
11.初步可行性研究分析的结论和建议11.1 研究分析的结论(1)本分析因是投资机会选择的分析,所以很粗不太准确。
(2)生产能力4万吨,盈亏平衡点产量为5582吨,占年产量的13.96%,项目抗风险能力非常强。