注塑模具冷却水路设计
注塑模冷却系统设计原则及结构形式
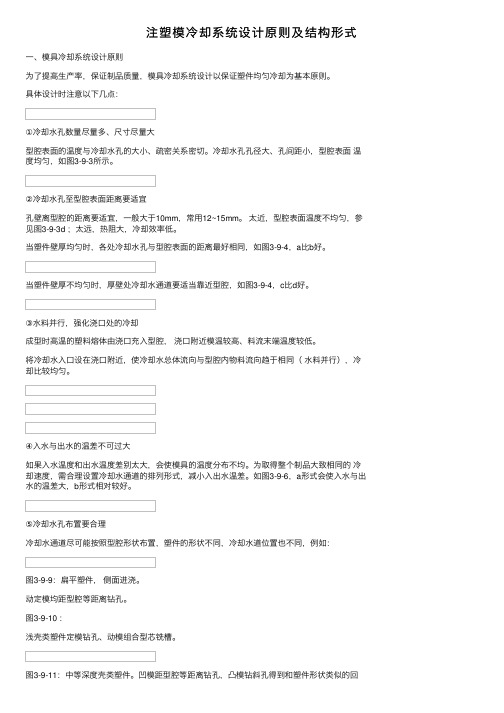
注塑模冷却系统设计原则及结构形式⼀、模具冷却系统设计原则为了提⾼⽣产率,保证制品质量,模具冷却系统设计以保证塑件均匀冷却为基本原则。
具体设计时注意以下⼏点:①冷却⽔孔数量尽量多、尺⼨尽量⼤型腔表⾯的温度与冷却⽔孔的⼤⼩、疏密关系密切。
冷却⽔孔孔径⼤、孔间距⼩,型腔表⾯温度均匀,如图3-9-3所⽰。
②冷却⽔孔⾄型腔表⾯距离要适宜孔壁离型腔的距离要适宜,⼀般⼤于10mm,常⽤12~15mm。
太近,型腔表⾯温度不均匀,参见图3-9-3d ;太远,热阻⼤,冷却效率低。
当塑件壁厚均匀时,各处冷却⽔孔与型腔表⾯的距离最好相同,如图3-9-4,a⽐b好。
当塑件壁厚不均匀时,厚壁处冷却⽔通道要适当靠近型腔,如图3-9-4,c⽐d好。
③⽔料并⾏,强化浇⼝处的冷却成型时⾼温的塑料熔体由浇⼝充⼊型腔,浇⼝附近模温较⾼、料流末端温度较低。
将冷却⽔⼊⼝设在浇⼝附近,使冷却⽔总体流向与型腔内物料流向趋于相同(⽔料并⾏),冷却⽐较均匀。
④⼊⽔与出⽔的温差不可过⼤如果⼊⽔温度和出⽔温度差别太⼤,会使模具的温度分布不均。
为取得整个制品⼤致相同的冷却速度,需合理设置冷却⽔通道的排列形式,减⼩⼊出⽔温差。
如图3-9-6,a形式会使⼊⽔与出⽔的温差⼤,b形式相对较好。
⑤冷却⽔孔布置要合理冷却⽔通道尽可能按照型腔形状布置,塑件的形状不同,冷却⽔道位置也不同,例如:图3-9-9:扁平塑件,侧⾯进浇。
动定模均距型腔等距离钻孔。
图3-9-10 :浅壳类塑件定模钻孔、动模组合型芯铣槽。
图3-9-11:中等深度壳类塑件。
凹模距型腔等距离钻孔,凸模钻斜孔得到和塑件形状类似的回路。
图3.9 1:深腔制品。
凸凹模均采⽤组合式,车螺旋槽冷却,从中⼼进⽔,在端⾯(浇⼝处)冷却后沿环绕成型零件的螺旋形⽔道顺序流出模具。
⑥冷却⽔道要便于加⼯装配冷却⽔道结构设计必须注意其加⼯⼯艺性,要易于加⼯制造,尽量采⽤钻孔等简单加⼯⼯艺。
对于镶装组合式冷却⽔道还要注意⽔路密封,防⽌冷却⽔漏⼊型腔造成型腔锈蚀。
导光板模具冷却水路的设计与分析
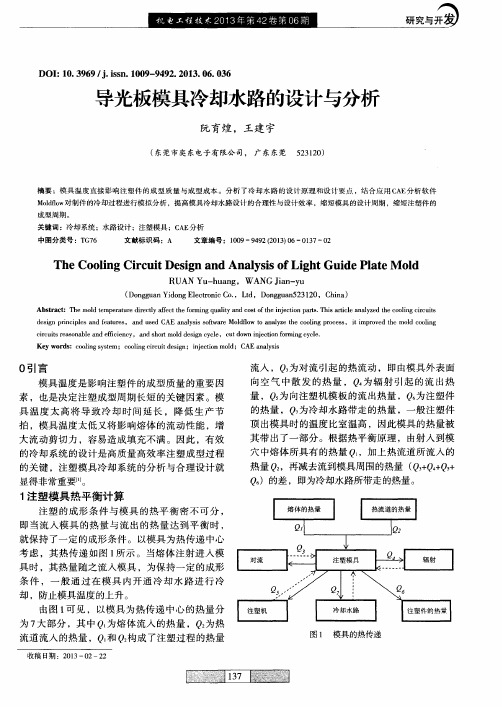
关键 词:冷却 系统 ;水路设 计 ;注塑模 具 ;C A E 分析
中图分类号 :T G 7 6 文献标识码 :A 文章编 号:1 0 0 9—9 4 9 2( 2 0 1 3 ) 0 6—0 1 3 7—0 2
Th e Co o l i n g Ci r c u i t De s i g n a n d An a l y s i s o f Li g h t Gu i d e Pl a t e Mo l d
d e s i g n p r i n c i p l e s a n d f e a t u r e s ,a n d u s e d CAE a n a l y s i s s o f t wa r e Mo l d l f o w t o a n ly a z e t h e c o o l i n g p r o c e s s ,i t i mp r o v e d t h e mo l d c o o l i n g
的热量 ,Q 为冷却水路带走 的热量 ,一般注塑件 顶 出模具 时 的温 度 比室温 高 ,因此 模 具 的 热量 被 其带出了一部分 。根据热平衡原理 ,由射人到模
穴 中熔 体所 具 有 的热量 Q ,加 上 热流 道 所 流人 的 热量 Q ,再减 去 流到模 具 周 围 的热量 ( Q , + p + Q +
的关键 ,注塑模具冷却系统的分析与合理设计就 显得非 常 重要” 】 。
Q )的差 ,即为冷却水路பைடு நூலகம்带走 的热量。
1 注塑模具热平衡计算
注 塑 的成 形 条 件 与 模 具 的热 平 衡 密 不 可 分 ,
即 当流入模具 的热量 与流 出的热量达到平衡 时 , 就保持 了一定的成形条件 。以模具为热传递 中心 考虑 ,其 热传递如 图 1 所示 。当熔体 注射进入模 具 时 ,其 热 量 随 之流 人 模 具 ,为保 持 一 定 的 成形
模具运水设计原则

Page 1
一、模具运水设计目的: 一般的塑料均是在200-280ºC左右的熔融状态下,注射入塑胶模具中,塑件冷却固
化到60ºC左右顶出,这个过程中所散发的热量只有极小部分是对流和辐射到大气环境 中,大部分都是靠冷却介质(水)带走,模具温度的控制对塑件的变形、收缩、以及 尺寸稳定性均有较大的影响,且冷却时间在整个模具注塑周期中占约2/3的时间,所以 模具需要设计最优化的运水,以便在最短的时间内生产出质量最好的产品 二、模具运水设计原则: 1.水路的直径通常公制有Φ6、Φ8、Φ10、Φ12、Φ15、Φ18,排运水时需根据产品大小
Page 3
图COOL-3 9.一模多腔时,尽量每个型腔布置单独的运水,以便调整产品变形和尺寸; 10.大产品的运水需分区域排布,600MM*300MM左右的区域布置一组单独的运水(如图
COOL-4所示)
图COOL-4
Page 4
11.热嘴需要设置单独的运水。如热嘴进胶不是在产品上,而是进胶在模板上转冷流道进 产品时,其冷却水可以同冷却产品的运水是同一条或是以水井冷却,热嘴冷水需靠近 热嘴前端配合位(如图COOL-5所示);
图COOL-7
三、模具水井设计原则: 1.水井大小需根据水路直径选择,Φ8、Φ10的水路用Φ15水井,Φ12水路用Φ18水井, Φ15水路用Φ24水井,Φ18水路用Φ30水井,水井、水孔与隔水片关系请参考\\srv7\ 模具事业部\CAD资料\公司内部标准\12-隔水片标准\QB-研-M-D-020-A0.隔水片标准; 2.水井需排布在运水无法靠近胶位的地方,水井中心间距常取3d(d为水井直径)左右; 3.水井顶部到胶位的距离常留到20-30MM,水井侧壁到胶位壁常留1d; 4.水井侧壁到镶件、顶针、螺丝的距离尽量做到8MM以上; 5.一条水路上水井不可太多,欧美模具常需保证在7个水井以内; 6.国产模和日系模具可多排水井,欧美模具常用斜水路冷却而少用水井;
塑胶模具结构设计

塑胶模具结构设计塑胶模具结构设计是制造业中至关重要的环节,它直接关系到产品的质量、生产效率和成本。
本文将围绕塑胶模具结构设计的基本原则、设计流程及注意事项进行详细阐述。
一、塑胶模具结构设计的基本原则1. 确保产品精度在设计塑胶模具时,要保证产品的尺寸精度和形状精度。
这要求设计师充分了解塑胶材料的收缩率、流动性等特性,并在模具设计中予以充分考虑。
2. 易于加工与装配模具结构应尽量简单,便于加工和装配。
复杂的设计不仅会增加制造成本,还可能影响模具的可靠性。
在设计过程中,要充分考虑模具零件的加工工艺性和装配顺序。
3. 高效生产塑胶模具结构设计应考虑生产效率,尽量减少生产过程中的辅助时间。
例如,通过优化流道设计、缩短冷却时间等措施,提高生产效率。
4. 安全可靠5. 维护方便模具在使用过程中难免会出现磨损、损坏等问题,设计时应考虑模具的维修便捷性,降低维护成本。
二、塑胶模具结构设计流程1. 分析产品结构在设计模具前,要对产品结构进行分析,了解产品的尺寸、形状、技术要求等,为模具设计提供依据。
2. 确定模具类型根据产品结构特点和生产要求,选择合适的模具类型,如单腔模具、多腔模具、热流道模具等。
3. 设计分型面分型面是模具闭合时,分离塑胶制品和浇注系统的界面。
设计分型面时要考虑产品的脱模斜度、外观质量等因素。
4. 设计浇注系统浇注系统包括主流道、分流道、浇口等部分,其设计直接影响到塑胶制品的质量。
设计时应关注流道截面积、长度、浇口位置等因素。
5. 设计冷却系统冷却系统对塑胶制品的质量和生产效率具有重要影响。
设计时要考虑冷却水路的布局、冷却水流量、冷却水温度等因素。
6. 设计顶出系统顶出系统的作用是在模具开模时,将制品从模具中顺利取出。
设计时要确保顶出力均匀、可靠,避免产品变形或损坏。
7. 绘制模具零件图及装配图三、塑胶模具结构设计注意事项1. 充分考虑塑胶材料的特性,如收缩率、流动性、热稳定性等。
2. 优化模具结构,提高生产效率,降低生产成本。
模具加热及冷却系统设计
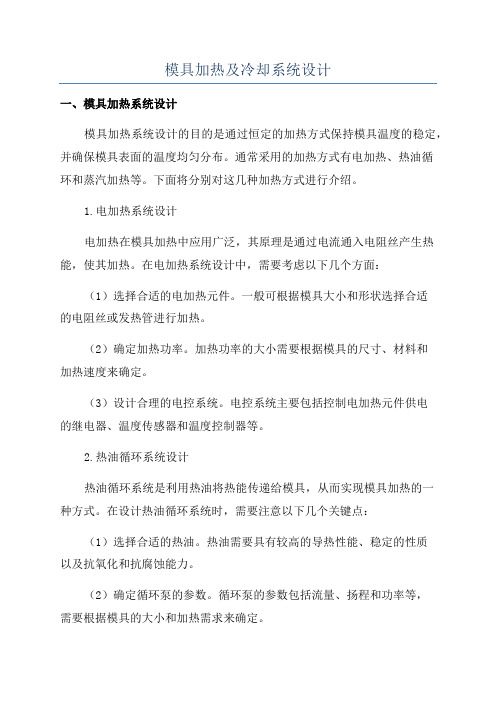
模具加热及冷却系统设计一、模具加热系统设计模具加热系统设计的目的是通过恒定的加热方式保持模具温度的稳定,并确保模具表面的温度均匀分布。
通常采用的加热方式有电加热、热油循环和蒸汽加热等。
下面将分别对这几种加热方式进行介绍。
1.电加热系统设计电加热在模具加热中应用广泛,其原理是通过电流通入电阻丝产生热能,使其加热。
在电加热系统设计中,需要考虑以下几个方面:(1)选择合适的电加热元件。
一般可根据模具大小和形状选择合适的电阻丝或发热管进行加热。
(2)确定加热功率。
加热功率的大小需要根据模具的尺寸、材料和加热速度来确定。
(3)设计合理的电控系统。
电控系统主要包括控制电加热元件供电的继电器、温度传感器和温度控制器等。
2.热油循环系统设计热油循环系统是利用热油将热能传递给模具,从而实现模具加热的一种方式。
在设计热油循环系统时,需要注意以下几个关键点:(1)选择合适的热油。
热油需要具有较高的导热性能、稳定的性质以及抗氧化和抗腐蚀能力。
(2)确定循环泵的参数。
循环泵的参数包括流量、扬程和功率等,需要根据模具的大小和加热需求来确定。
(3)设计供热系统。
供热系统包括加热炉、加热管、加热器和控制系统等。
3.蒸汽加热系统设计蒸汽加热系统是将蒸汽传导至模具表面进行加热的一种方式。
在进行蒸汽加热系统设计时,需要注意以下几个方面:(1)选择合适的蒸汽压力。
蒸汽压力需要根据模具的形状和尺寸来确定,以确保蒸汽能够充分覆盖模具表面。
(2)设计合理的蒸汽供应系统。
蒸汽供应系统包括蒸汽管道、调压阀、过滤器和控制系统等。
(3)确保安全性。
蒸汽加热系统应采取必要的安全措施,如安装安全防护装置、检测和处理漏气等。
模具冷却系统设计的目的是通过冷却水或冷却剂将模具温度降低到所需的范围内,以便于产品成型和模具的连续使用。
冷却系统设计的关键点包括冷却方式、冷却水路设计和冷却剂的选择等。
1.冷却方式常见的模具冷却方式有直接冷却和间接冷却两种。
(1)直接冷却是将冷却水通过冷却水道直接注入模具腔体中进行冷却。
基于随形水路技术的带把双色水杯注塑模具设计
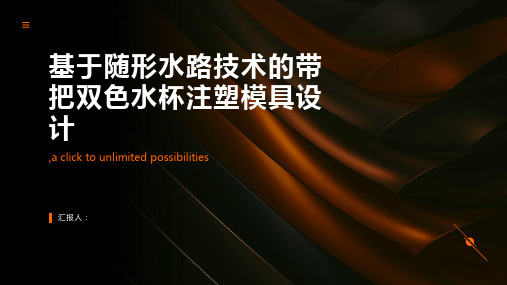
评估结果:对模具设计的效 果进行总结和评价,指出优
缺点和改进方向
反馈机制:根据评估结果, 对模具设计进行优化和改进,
提高生产效率和产品质量
06 未来研究和展望
随形水路技术的研究方向
优化设计:研究更高效、可靠的设计方案,提高模具的稳定性和使用寿命。
基于随形水路技术的带 把双色水杯注塑模具设 计
,a click to unlimited possibilities
汇报人:
目录 /目录
01
随形水路技术 的原理和特点
04
模具设计的优 化和改进
02
带把双色水杯 的设计要求和 难点
05
模具设计的实 践应用和效果 评估
03
基于随形水路 技术的带把双 色水杯注塑模 具设计
环保趋势:未来 将更加注重环保, 采用可回收材料 和绿色制造技术。
个性化需求:随 着消费者需求的 多样化,带把双 色水杯注塑模具 设计将更加注重 个性化定制。
智能化发展:模 具设计将与智能 化技术相结合, 实现自动化生产 和智能监控。
感谢您的观看
汇报人:
新型材料:探索新型材料在随形水路技术中的应用,提高模具的耐热性和耐磨性。
智能化控制:研究智能化控制技术在随形水路技术中的应用,实现注塑过程的自动化和 智能化。
绿色环保:研究环保材料和环保技术在随形水路技术中的应用,降低模具制造过程中的 能耗和污染。
带把双色水杯注塑模具设计的展望
技术创新:随形 水路技术将得到 进一步优化,提 高模具设计的灵 活性和生产效率。
延长模具寿命:随形水路技术可以减少模具温度变化,降低热应力,从而延长模具的使用寿 命。
注塑模具冷却水路设计
注塑模具冷却水路设计一、冷却系统的设计原则1.均匀性原则:冷却水应能均匀地覆盖整个模具表面,保证模具各部位的冷却效果一致,避免出现局部过热或过冷的现象。
2.高效性原则:冷却水应尽可能快速地吸收模具上的热量,提高冷却速度,并迅速排出,以提高生产效率。
3.经济性原则:冷却系统的设计应尽量减少冷却水的流量和能耗,降低生产成本。
4.安全性原则:冷却系统的设计应考虑防止冷却水泄漏、烫伤操作人员等安全问题。
二、冷却水路的布置方式1.双水路布置:常用的冷却水路设计方式是双水路布置,即将进水和出水管道分开设置。
进水管道和出水管道应相对布置,使冷却水能够充分覆盖模具的表面,使冷却效果更好。
2.直线布置:冷却水路一般采用直线布置,以迅速传递模具表面的热量,提高冷却效果。
直线布置的冷却水路应尽量减少弯头和弯管,以降低水流阻力。
3.弯头布置:当模具的形状不规则或空间有限时,可以采用弯头布置的冷却水路,使冷却水能够覆盖到模具的各个部位。
但是,弯头布置会增加水流阻力,影响冷却效果,所以应尽量减少弯头的数量。
4.分级布置:对于大型模具或需要长时间注塑的产品,可以采用分级布置的冷却水路,将冷却水路分为多段,以提高冷却效果。
三、冷却水路的设计步骤1.根据产品的形状和结构,确定冷却水路的布置方式,包括进水管道和出水管道的位置和数量。
2.根据模具的尺寸和材料,计算冷却水路的长度和直径,并确定冷却水的流量和压力。
3.选择合适的冷却水路元件,如水管、弯头、分流装置等,并计算和确定它们的尺寸和数量。
4.验算冷却水路的设计是否符合要求,包括冷却水的流速、流量、冷却时间等。
5.根据模具的具体情况,设计冷却水路的进水和出水管道的接口,确保冷却水能够顺利流入和排出。
6.绘制冷却水路的详细图纸,包括冷却水路的布置、元件的尺寸和位置等。
四、注意事项1.冷却水路的布置应尽量远离模具的加热部位,避免冷却水的温度受到影响。
2.冷却水路的材料应选择耐腐蚀的材料,如不锈钢、铜等,以防止冷却水对模具的腐蚀。
注塑件常见成型缺陷及解决方案
注塑件常见成型缺陷及解决方案注塑件常见成型缺陷及解决方案前言在注塑成型加式过程中,可能由于原材料处理不好、塑件或模具设计不合理、操作工没有掌握合适的工艺操作条件,或者因机械方面的原因,常常使塑件产品短射、凹痕、飞边、困气、开裂、翘曲变形等成型缺陷。
本文针对塑件在成型过程中出现的各种注塑缺陷,主要是:短射,困气,发脆,烧焦,飞边,分层起皮,喷流痕,流痕,雾斑(浇口晕),银纹(水花纹),凹痕,熔接痕,成型周期过长,翘曲变形,分析了问题产生的可能原因,从原材料、塑件或模具设计、成型工艺等各方面,提出解决方案。
一.短射短射是指模具型腔不能被完全充满的一种现象。
短射形成原因:1、模温、料温或注塑压力和速度过低2、原料塑化不均3、排气不良4、原料流动性不足5、制件太薄或浇口尺寸太小6、聚合物熔体由于结构设计不合理导致过早固化短射解决方案:材料:选用流动性更好的材料模具设计:1、填充薄壁之前先填充厚壁,避免出现滞留现象2、增加浇口数量和流道尺寸,减少流程比及流动阻力3、排气口的位置和尺寸设置适当,避免出现排气不良的现象注塑机:1、检查止逆阀和料筒内壁是否磨损严重2、检查加料口是否有料或是否架桥工艺条件:1、增大注塑压力和注塑速度,增强剪切热2、增大注塑量3、增大料筒温度和模具温度二.困气困气是指空气被困在型腔内而使制件产生气泡。
困气形成原因:它是由于两股熔体前锋交汇时气体无法从分型面、顶杆或排气孔中排出造成的。
困在型腔内气体不能被及时排出,易导致出现表面起泡,制件内部夹气,注塑不满等现象。
困气解决方案:结构设计:减少厚度的不一致,尽量保证壁厚均匀模具设计:1、在最后填充的地方增设排气口2、重新设计浇口和流道系统工艺条件:1、降低最后一级注塑速度.2、增加模温三.发脆塑件发脆是指制件在某些部位出现容易开裂或折断。
发脆原因:1、干燥条件不适合;使用过多回收料2、注塑温度设置不对3、浇口和流道系统设置不恰当4、熔解痕强度不高发脆解决方案:材料:1、注塑前设置适当的干燥条件2、减少使用回收料,增加原生料的比例.3、选用高强度的塑胶.模具设计:增大主流道、分流道和浇口尺寸注塑机:选择设计良好的螺杆,使塑化时温度分配更加均匀工艺条件:1、降低料筒和喷嘴的温度2、降低背压、螺杆转速和注塑速度3、通过增加料温,加大注塑压力,提高熔解痕强度四.烧焦焦痕是指型腔内气体不能及时排走,导致在流动最末断产生烧黑现象。
冷却水路设计原则与优化实例(ppt 25页)
0.3mm
Z方向收缩较之前改善较大,变形如图。 右边为放大10倍的变形,绿色框为变形前形状。
四、模具加热设备简介
1.水温加热:模具温度要求80°以下适用; 大部分塑胶原料(除高温料)要求模具成型温度为:20°~ 90°,如果部品表面光洁
度要求较高,或模具结构导致成型困难时,必须使用水温机加热。
PA 尼龙
模
收集 歧管
软管
收集 歧管
供给
歧管
泵
冷却水路2
供给 歧管
一、冷却水路设计原则
3.冷却系统水孔径间距与型腔之间的关系
H一般2.5d-3d
层流、紊流(雷诺数Re>4000为稳定的紊流):
注:1.圣度标准 最小 8mm。 2.无论多大的模具,水孔的直径不能大于14mm,
否则难以形成紊流(紊流状态热交换充分)。
有加强纤维
水温机
注:1. 根据冷却水温度选用软管; 2. 这些软管均为冷却水专用(不适用与油); 3. 一般水温机设定 70~80°,高于80度有安全隐患。
PVF
适用温度-30~120° S-PVC
适用温度0~60°
四、模具加热设备简介
2.油温加热:模具温度要求90~150°适用。 PP、PC、尼龙(PA66、PA6、PA46) 、POM 等加玻纤GF后 要求模具温度都可达到
一、冷却水路设计原则
主 要 二、冷却水路样式 内 三、冷却水路优化实例 容
四、加热设备简介
一、冷却水路设计原则
1. 注塑冷却水路设计目的
2. 水路设计目的:
水路设计目的是使产品均匀冷却,并在较短时间内顶出成型。水路排布的好 坏直接影响到产品的成型品质和成产周期(成本)。
• 对品质的影响:在成型时水路使用来控制模具温度的,而模具温度及其波 动对制品的收缩率变形、尺寸稳定性、机械强度、应力开裂和表面质量等均
注塑模具设计
注塑模具设计1. 引言注塑模具是在注塑成型过程中必不可少的工具,它的设计对产品的质量和生产效率有着重要影响。
本文将对注塑模具设计过程进行详细讲解,包括设计原则、设计流程、常见问题等内容。
2. 注塑模具设计原则在进行注塑模具设计时,需要遵循以下原则:2.1 产品需求分析在进行模具设计之前,首先要对注塑产品的需求进行详细分析。
了解产品的尺寸、形状、材料等特性,以及注塑成型过程中可能出现的问题,例如收缩、变形等。
2.2 模具结构简单模具的结构应尽量简单,便于加工和维修。
复杂的模具不仅增加了制造成本,还容易导致生产故障。
2.3 注塑模具材料选择注塑模具的材料应具有高强度、高硬度和良好的耐磨性。
常用的材料有工具钢、合金钢等。
2.4 模具冷却设计模具冷却是注塑成型中重要的一环。
合理的冷却设计可以加快成型周期,提高生产效率。
应通过合理的冷却水路设计,使冷却水均匀地冷却模具各个部位。
3. 注塑模具设计流程注塑模具设计的流程通常包括以下几个步骤:3.1 产品设计根据产品需求进行产品设计。
确定产品的形状、尺寸以及加工要求。
3.2 模具结构设计根据产品设计,确定模具的结构。
包括模具的分型面选择、模具的开合方式、模具的冷却系统设计等。
3.3 模具零件设计根据模具结构设计,对模具零件进行设计。
包括模具芯、模具腔、模具副等零件的设计。
3.4 模具加工根据模具零件设计,进行模具的加工。
包括车削、铣削、电火花等工艺。
3.5 模具装配和调试将加工好的模具零件进行装配,并进行调试。
保证模具的正常工作。
4. 常见问题及解决方法在注塑模具设计过程中,常常会遇到一些问题,下面列举几个常见问题及解决方法:4.1 收缩问题在注塑成型过程中,产品会发生一定程度的收缩。
为了解决收缩问题,可以通过增加模具开料尺寸或调整注塑工艺参数来补偿收缩。
4.2 模具冷却不均匀问题如果模具冷却不均匀,会导致产品变形或质量不稳定。
解决这个问题可以通过设计合理的冷却水路,保证冷却水均匀地流过模具各个部位。
- 1、下载文档前请自行甄别文档内容的完整性,平台不提供额外的编辑、内容补充、找答案等附加服务。
- 2、"仅部分预览"的文档,不可在线预览部分如存在完整性等问题,可反馈申请退款(可完整预览的文档不适用该条件!)。
- 3、如文档侵犯您的权益,请联系客服反馈,我们会尽快为您处理(人工客服工作时间:9:00-18:30)。
h
8
冷却水路的排布方式应根据成品的形状﹐塑料特性 以及对模温的要求而定。
扁平﹐薄壁的成品宜采用并列式的排布。
h
9
对于制品在空间收缩率不一定的﹐水路应沿着收缩 率大的方向排布。
h
10
模具冷却装置的结构形式取决于制品的形状和尺 寸﹑模具的结构﹑浇口的位置﹑模仁与模板的大小 等。现举例如下﹕
1>﹑在成品比较小﹑模仁也比较小的情况下﹐水路 可以只经过模板就可以达到冷却效果。(直流式)
h
1
冷却水路也叫温度调节系统。
模具温度调节的重要性﹕模具温度对塑料制品的质量 和成型周期影响很大。
(1)﹑模具温度的波动对制品的收缩率﹑尺寸稳定性﹑ 变形﹑应力开裂﹑表面质量等都有很大的影响。
(2)﹑模具温度对成型周期的影响﹕冷却时间约占成型 周期的80%。
h
2
模具成型周期
h
3
冷却系统设计原则﹕
h
15
隔水板通道的形式。
h
16
6>﹑对于细长的入子﹐在无法排布水路的情况下﹐可 以用导热性能比较好的铍铜材料。入子大头端与冷却 水连接﹐热量通过铍铜接触冷却水而达到冷却效果。 (间接冷却)
h
17
7>﹑冷却棒用于细长的部件上。
h
18
8>﹑喷水管用于细长的入子上。(喷流式)
h
19
9>﹑斜梢较大且斜梢上成品面积较大﹐斜梢需要冷却。
h
6
3)﹑一般浇口附近温度最高﹐流道冷却也最慢﹐冷却 水应从浇口附近开始向其它地方流。
h
7
4)﹑设计时冷却水路的排布一般为1﹕1.5~2﹕4~5﹐即水孔直 径﹕与成品的间距﹕水孔间距= 1﹕1.5~2﹕4~5﹐如图所示。
假设水路直径为Φ10MM﹐水路与水路之间的距离为
40~50MM﹐水路与成品为30~40MM。
1﹑快速冷却
2﹑冷却均匀
3﹑加工简单
h
4
1)﹑在满足冷却所需的传热面积和模具结构允许的前提 下﹐冷却回路数量应尽量多﹐冷却水路孔径要尽量大。
图a
图b
图a的冷却速度比图b要快。
水孔直径一般取Φ6~Φ12MM。
h
5
2)﹑冷却水路的布置要合理。当制品肉厚基本均匀时﹐冷却 水路离成品表面距离最好相等﹐分布与轮廓吻合﹐如图a﹔ 当成品肉厚不均一时﹐则在肉厚的地方加强冷却﹐如图b。
h
20
10>﹑热流道注射成型时﹐热流道板要加热﹐而在热流 道的进胶附近需要冷却。
h
21
11>﹑对于流动性差﹐粘度较高的塑料如 PC﹑PMMA﹑ POM等﹐注射成型时需要对模具加热。模具的加热方 式有﹕电加热﹑油加热﹑过热水加热﹑蒸汽等。
如下图中所示用电加热方式的电热管对模具加热。
h
22
h
23
h
h
11
2>﹑当成品长与宽之比例相差比较大﹐表面比较平 整﹐肉厚均一时。水路沿成品长的方向排布。 (直流循环式)
h
12
3>﹑成品面积较大的冷却水路排布。
h
13
4>﹑滑块比较大且滑块上成品面积较大时﹐滑块孔 需冷却。
h
14
5>﹑成品成拱形﹐且较高时﹐排布水路会离成品较 远﹐用隔水板可以很好的冷却。(隔板式)
h
32
“O”RING至模仁侧壁的尺寸应大于模仁 的来自角值+2MM﹐防止漏水。
h
33
水路平面图需标注﹕
或者
h
34
管螺纹型号 例如PT1/4或者PT1/8
代表第几条水路 例如#A1代表第一条水路 例如#A2代表第二条水路
IN代表进水口 OUT代表出水口
h
35
24
h
25
h
26
h
27
h
28
h
29
水管塞 PT “1/4”
a尺寸必须大于水管塞的长度
h
30
因为水管接头直径较大﹐为了防止干涉﹐水路与水路 的中心距为30MM﹐水路与其它零件的距离为15MM。
上固定板
母模板
h
31
水路与顶针﹑套筒﹑螺丝的间距为5MM以上﹐特殊情况 最小值取3MM。
顶针
螺丝