数控机床润滑系统的PLC控制
PLC在数控机床中的自动化控制应用
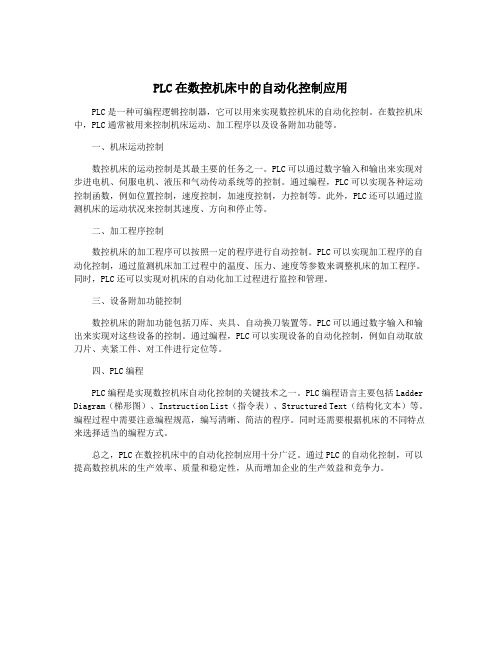
PLC在数控机床中的自动化控制应用PLC是一种可编程逻辑控制器,它可以用来实现数控机床的自动化控制。
在数控机床中,PLC通常被用来控制机床运动、加工程序以及设备附加功能等。
一、机床运动控制数控机床的运动控制是其最主要的任务之一。
PLC可以通过数字输入和输出来实现对步进电机、伺服电机、液压和气动传动系统等的控制。
通过编程,PLC可以实现各种运动控制函数,例如位置控制,速度控制,加速度控制,力控制等。
此外,PLC还可以通过监测机床的运动状况来控制其速度、方向和停止等。
二、加工程序控制数控机床的加工程序可以按照一定的程序进行自动控制。
PLC可以实现加工程序的自动化控制,通过监测机床加工过程中的温度、压力、速度等参数来调整机床的加工程序。
同时,PLC还可以实现对机床的自动化加工过程进行监控和管理。
三、设备附加功能控制数控机床的附加功能包括刀库、夹具、自动换刀装置等。
PLC可以通过数字输入和输出来实现对这些设备的控制。
通过编程,PLC可以实现设备的自动化控制,例如自动取放刀片、夹紧工件、对工件进行定位等。
四、PLC编程PLC编程是实现数控机床自动化控制的关键技术之一。
PLC编程语言主要包括Ladder Diagram(梯形图)、Instruction List(指令表)、Structured Text(结构化文本)等。
编程过程中需要注意编程规范,编写清晰、简洁的程序。
同时还需要根据机床的不同特点来选择适当的编程方式。
总之,PLC在数控机床中的自动化控制应用十分广泛。
通过PLC的自动化控制,可以提高数控机床的生产效率、质量和稳定性,从而增加企业的生产效益和竞争力。
机床润滑剂制备工艺PLC控制系统的设计

机床润滑剂制备工艺PLC 控制系统的设计Design of PLC control system for machine tool lubricant preparation朱志豪,李 阳,陈再良ZHU Zhi-hao, LI Yang, CHEN Zai-liang(苏州大学 机电工程学院,苏州 215021)摘 要:为了满足现今机床润滑剂制备的工艺要求,针对其主要工艺流程,研发出一套新一代生产设备,设计了以PLC为控制器,硬件电路为主体,集编程、液位监测,传感器为一体的自动控制系统。
介绍了设备的主要工艺流程,控制系统的设计、安装及调试过程。
设备运行结果证明,该设备投入生产后,效率提高了120%,精度高并且性能稳定。
关键词:润滑剂制备;PLC;自动控制中图分类号:TH16 文献标识码:B 文章编号:1009-0134(2017)06-0027-04收稿日期:2017-03-10基金项目:青海省科技厅资助项目(2014-Z-Y09;2014-GX-219);江苏省科技厅资助项目(BY2016043-02)作者简介:朱志豪(1992 -),男,江苏泰州人,硕士研究生,研究方向为机械工程。
0 引言润滑剂的生产属于化工类行业,可以应用于机床加工、汽车机械等行业,能够降低摩擦副的摩擦阻力,减缓其磨损,还能够起到冷却、清洗和防止污染等作用[1]。
润滑剂的制备是依靠不等量融合工艺进行生产的。
传统的生产工序分为加料、放料、反应和储存,加料过程是整个制备过程的关键。
在升级改造之前,加料过程只能够依赖人工进行加料。
加料液位的准确性和进料的时间点精确度都较低,直接影响了成品的质量。
工人在人工加料的同时不可避免的会接触原料和带入杂质,不仅影响了精度,也会造成一定的人身损伤[2,3]。
针对传统加工工序所存在的问题,文章提出了一种新型的以PLC 为控制器的润滑剂加料控制系统,并对其控制方案、安装和调试过程进行了详细讨论。
机床润滑剂制备工艺PLC控制系统的设计
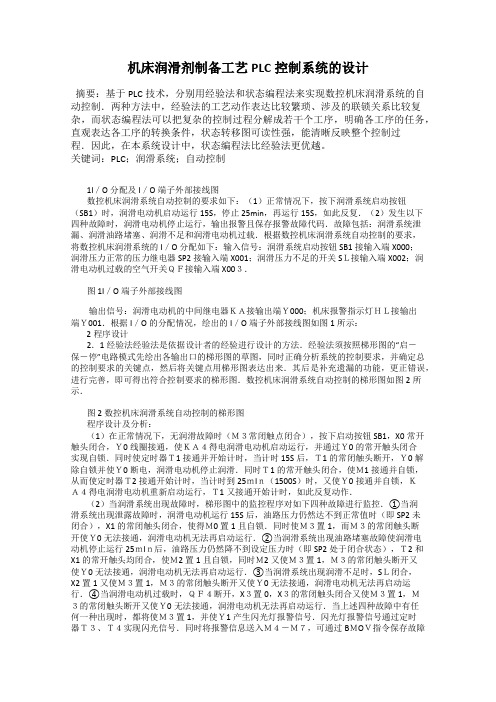
机床润滑剂制备工艺PLC控制系统的设计摘要:基于PLC技术,分别用经验法和状态编程法来实现数控机床润滑系统的自动控制.两种方法中,经验法的工艺动作表达比较繁琐、涉及的联锁关系比较复杂,而状态编程法可以把复杂的控制过程分解成若干个工序,明确各工序的任务,直观表达各工序的转换条件,状态转移图可读性强,能清晰反映整个控制过程.因此,在本系统设计中,状态编程法比经验法更优越。
关键词:PLC;润滑系统;自动控制1I/O分配及I/O端子外部接线图数控机床润滑系统自动控制的要求如下:(1)正常情况下,按下润滑系统启动按钮(SB1)时,润滑电动机启动运行15S,停止25min,再运行15S,如此反复.(2)发生以下四种故障时,润滑电动机停止运行,输出报警且保存报警故障代码.故障包括:润滑系统泄漏、润滑油路堵塞、润滑不足和润滑电动机过载.根据数控机床润滑系统自动控制的要求,将数控机床润滑系统的I/O分配如下:输入信号:润滑系统启动按钮SB1接输入端X000;润滑压力正常的压力继电器SP2接输入端X001;润滑压力不足的开关SL接输入端X002;润滑电动机过载的空气开关QF接输入端X003.图1I/O端子外部接线图输出信号:润滑电动机的中间继电器KA接输出端Y000;机床报警指示灯HL接输出端Y001.根据I/O的分配情况,绘出的I/O端子外部接线图如图1所示:2程序设计2.1经验法经验法是依据设计者的经验进行设计的方法.经验法须按照梯形图的“启-保-停”电路模式先绘出各输出口的梯形图的草图,同时正确分析系统的控制要求,并确定总的控制要求的关键点,然后将关键点用梯形图表达出来.其后是补充遗漏的功能,更正错误,进行完善,即可得出符合控制要求的梯形图.数控机床润滑系统自动控制的梯形图如图2所示.图2数控机床润滑系统自动控制的梯形图程序设计及分析:(1)在正常情况下,无润滑故障时(M3常闭触点闭合),按下启动按钮SB1,X0常开触头闭合,Y0线圈接通,使KA4得电润滑电动机启动运行,并通过Y0的常开触头闭合实现自锁.同时使定时器T1接通并开始计时,当计时15S后,T1的常闭触头断开,Y0解除自锁并使Y0断电,润滑电动机停止润滑.同时T1的常开触头闭合,使M1接通并自锁,从而使定时器T2接通开始计时,当计时到25mIn(1500S)时,又使Y0接通并自锁,KA4得电润滑电动机重新启动运行,T1又接通开始计时,如此反复动作.(2)当润滑系统出现故障时,梯形图中的监控程序对如下四种故障进行监控.①当润滑系统出现泄露故障时,润滑电动机运行15S后,油路压力仍然达不到正常值时(即SP2未闭合),X1的常闭触头闭合,使得M0置1且自锁.同时使M3置1,而M3的常闭触头断开使Y0无法接通,润滑电动机无法再启动运行.②当润滑系统出现油路堵塞故障使润滑电动机停止运行25mIn后,油路压力仍然降不到设定压力时(即SP2处于闭合状态),T2和X1的常开触头均闭合,使M2置1且自锁,同时M2又使M3置1,M3的常闭触头断开又使Y0无法接通,润滑电动机无法再启动运行.③当润滑系统出现润滑不足时,SL闭合,X2置1又使M3置1,M3的常闭触头断开又使Y0无法接通,润滑电动机无法再启动运行.④当润滑电动机过载时,QF4断开,X3置0,X3的常闭触头闭合又使M3置1,M3的常闭触头断开又使Y0无法接通,润滑电动机无法再启动运行.当上述四种故障中有任何一种出现时,都将使M3置1,并使Y1产生闪光灯报警信号.闪光灯报警信号通过定时器T3、T4实现闪光信号.同时将报警信息送入M4-M7,可通过BMOV指令保存故障信息.3结语本文基于三菱PLC技术,分别用经验法和状态编程法来实现数控机床润滑系统的自动控制.总体来看,两种方法中,经验法的工艺动作表达比较繁琐,涉及的联锁关系比较复杂,梯形图可读性差,很难从梯形图看出具体控制工艺过程;对比而言,状态编程法可以把复杂的控制过程分解成若干个工序,明确各工序的任务,直观的表达各工序的转换条件,状态转移图的可读性强,能清晰反映整个控制过程.因此,在本系统的设计中,状态编程法比经验法更优越。
(完整版)数控机床润滑系统的自动控制毕业论文设计
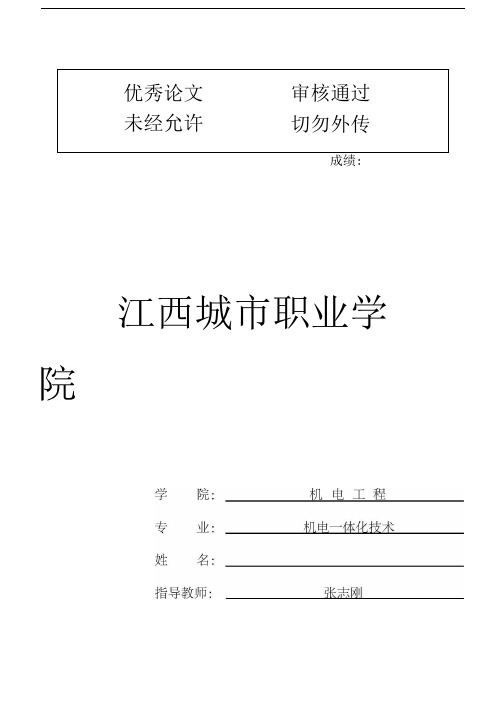
成绩: 江西城市职业学二0—二年三月摘要机床润滑系统的设计、调试和维修保养,对于提高机床加工精度、延长机床使用寿命等都有着十分重要的作用。
但是在润滑系统的电气控制方面,仍存在以下问题:一是润滑系统工作状态的监控。
数控机床控制系统中一般仅设油箱油面监控,以防供油不足,而对润滑系统易出现的漏油、油路堵塞等现象,不能及时做出反应。
二是设置的润滑循环和给油时间单一,容易造成浪费。
数控机床在不同的工作状态下,需要的润滑剂量是不一样的,如在机床暂停阶段就比加工阶段所需要的润滑油量要少。
针对上述情况,在数控机床电气控制系统中,对润滑控制部分进行了改进设计,时刻监控润滑系统的工作状况,以保证机床机械部件得到良好润滑,并且还可以根据机床的工作状态,自动调整供油、循环时间,以节约润滑油。
关键字:数控机床,润滑系统,PLC故障分析目录第1章引言 (1)第2章数控机床的系统构成 (2)第3章润滑的分类 (3)3.1单线阻尼式润滑系统......................................... 3.3.2递进式润滑系............................................... 3.3.3容积式润滑系统.............................................4.第4章润滑系统的控制原理...............................................5.4.1电气控制原理..............................................5.4.2自动控制原理............................................... 6.第5章数控机床润滑系统的PLC控制 (7)5.1润滑PLC控制原理.......................................... 7.5.2润滑系统10地址分配........................................ 9.第6章润滑系统故障分析. (10)6.1润滑系统工作状态的监控 (10)6.2润滑时间及润滑次数的控制 (10)6.3润滑报警信号的处理 (12)结语 (13)致谢 (14)主要资料 (15)附录 (16)引言众所周知,要使运动副的磨损减小,必须在运动副表面保持适当的清洁的润滑油膜,即维持磨擦副表面之间恒量供油以形成油膜。
分析PLC在数控机床控制系统中的应用
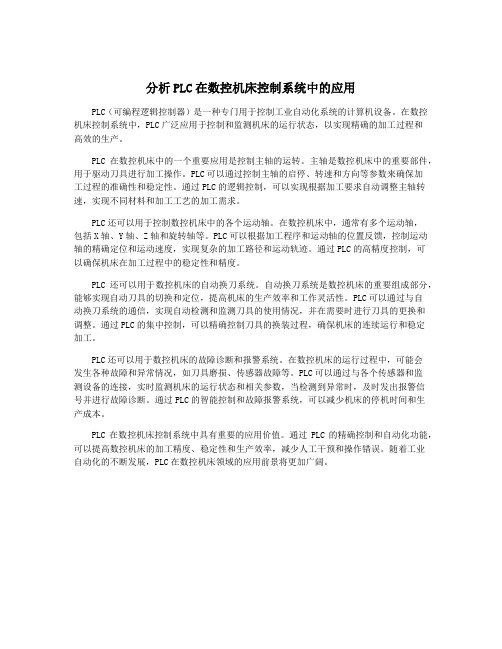
分析PLC在数控机床控制系统中的应用PLC(可编程逻辑控制器)是一种专门用于控制工业自动化系统的计算机设备。
在数控机床控制系统中,PLC广泛应用于控制和监测机床的运行状态,以实现精确的加工过程和高效的生产。
PLC在数控机床中的一个重要应用是控制主轴的运转。
主轴是数控机床中的重要部件,用于驱动刀具进行加工操作。
PLC可以通过控制主轴的启停、转速和方向等参数来确保加工过程的准确性和稳定性。
通过PLC的逻辑控制,可以实现根据加工要求自动调整主轴转速,实现不同材料和加工工艺的加工需求。
PLC还可以用于控制数控机床中的各个运动轴。
在数控机床中,通常有多个运动轴,包括X轴、Y轴、Z轴和旋转轴等。
PLC可以根据加工程序和运动轴的位置反馈,控制运动轴的精确定位和运动速度,实现复杂的加工路径和运动轨迹。
通过PLC的高精度控制,可以确保机床在加工过程中的稳定性和精度。
PLC还可以用于数控机床的自动换刀系统。
自动换刀系统是数控机床的重要组成部分,能够实现自动刀具的切换和定位,提高机床的生产效率和工作灵活性。
PLC可以通过与自动换刀系统的通信,实现自动检测和监测刀具的使用情况,并在需要时进行刀具的更换和调整。
通过PLC的集中控制,可以精确控制刀具的换装过程,确保机床的连续运行和稳定加工。
PLC还可以用于数控机床的故障诊断和报警系统。
在数控机床的运行过程中,可能会发生各种故障和异常情况,如刀具磨损、传感器故障等。
PLC可以通过与各个传感器和监测设备的连接,实时监测机床的运行状态和相关参数,当检测到异常时,及时发出报警信号并进行故障诊断。
通过PLC的智能控制和故障报警系统,可以减少机床的停机时间和生产成本。
PLC在数控机床控制系统中具有重要的应用价值。
通过PLC的精确控制和自动化功能,可以提高数控机床的加工精度、稳定性和生产效率,减少人工干预和操作错误。
随着工业自动化的不断发展,PLC在数控机床领域的应用前景将更加广阔。
数控机床润滑系统的自动控制

数控机床润滑系统的自动控制机床的控制系统在整个机床中起到很重要的作用。
现代机械制造系统内零件的平均公差,每十年大约少一个数量级。
目前,精密和超精密机械零件的制造公差都可以被控制在粗糙度范围内。
机床的润滑系统运行稳定性由于精度提高,运行更稳定。
系统的自动控制更使得发现问题能够及时发现。
以提高机械的使用寿命。
现在机械的润滑都是采用的是集中润滑系统,通过分流器来控制所需的油量。
1、润滑系统对机床温度的自动控制当机床开始运行时,齿轮泵由主机带动进行运转将润滑油箱的油输入机床的各个需要润滑的部位,循环一周后经回油孔进而进入润滑油箱。
此过程中假如实际油箱的温度值与设定值不符的时候自动控制系统就会启动润滑油箱温度测控电路。
通过加热或降温使油箱温度一直保持设定温度值。
润滑油过多过少都不行,会产生浪费和产生过多的热量,这样既不合理也不经济。
因此,润滑系统均采用定期、定量的工作方式。
保证系统的油量能够均匀供给。
机床周围的现场环境比较复杂,对机床产生相应干扰是不可避免的。
例如线路和电源上的输入、输出都会对机床进行干扰,AT89S52单片机控制系统能够通过安装抗干扰抑制器(低通滤波)及在一些I /o线路上采用光电隔离技术来解决。
在软件上由于可重复可釆取设置陷阱和设置软件Watchdog 的方法来避免程序的跳飞,使得程序能够正常运行。
其原理图如图一所示,可直接在线编程,调试修改程序非常方便。
使机床温度不受外界影响,更加稳定。
2、润滑系统对机床油量的自动控制假如润滑循环和给油时间单一,就会造成浪费。
数控机床在不同的工作状态下,所需的润滑剂量是不一样的,如在机床暂停阶段就比加工阶段所需要的润滑油量要少。
只有在机械的表面有足够的润滑油,才能形成完整的油膜,这时才能保证机床运动副的磨损减小,也就是维持摩擦表面之间恒量供油以形成油膜。
机床导轨需要的润滑油量我们常用的计算公式是:(长度+移动行程)X 宽度X Ko润滑油量与该导轨上的轴的移动距离是紧密联系的。
基于PLC技术实现数控机床润滑系统的自动控制研究
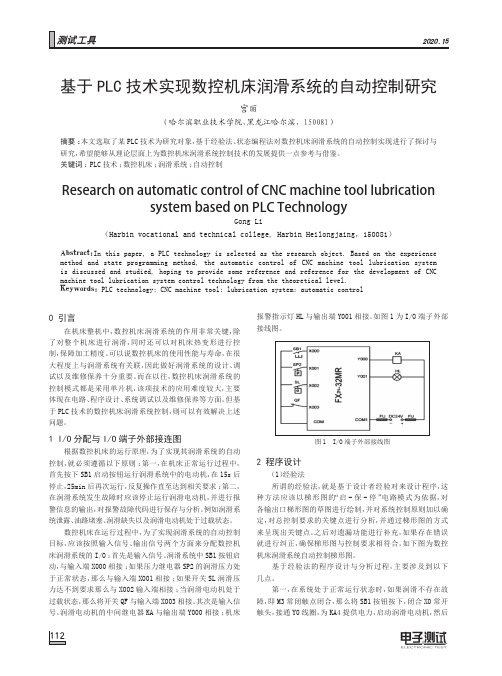
0 引言在机床整机中,数控机床润滑系统的作用非常关键,除了对整个机床进行润滑,同时还可以对机床热变形进行控制,保障加工精度。
可以说数控机床的使用性能与寿命,在很大程度上与润滑系统有关联,因此做好润滑系统的设计、调试以及维修保养十分重要。
而在以往,数控机床润滑系统的控制模式都是采用单片机,该项技术的应用难度较大,主要体现在电路、程序设计、系统调试以及维修保养等方面。
但基于PLC 技术的数控机床润滑系统控制,则可以有效解决上述问题。
1 I/O 分配与I/O 端子外部接连图根据数控机床的运行原理,为了实现其润滑系统的自动控制,就必须遵循以下原则:第一,在机床正常运行过程中,首先按下SB1启动按钮运行润滑系统中的电动机,在15s 后停止,25min 后再次运行,反复操作直至达到相关要求;第二,在润滑系统发生故障时应该停止运行润滑电动机,并进行报警信息的输出,对报警故障代码进行保存与分析。
例如润滑系统泄露、油路堵塞、润滑缺失以及润滑电动机处于过载状态。
数控机床在运行过程中,为了实现润滑系统的自动控制目标,应该按照输入信号、输出信号两个方面来分配数控机床润滑系统的I/O :首先是输入信号。
润滑系统中SB1按钮启动,与输入端X000相接;如果压力继电器SP2的润滑压力处于正常状态,那么与输入端X001相接;如果开关SL 润滑压力达不到要求那么与X002输入端相接;当润滑电动机处于过载状态,那么将开关QF 与输入端X003相接。
其次是输入信号。
润滑电动机的中间继电器KA 与输出端Y000相接;机床报警指示灯HL 与输出端Y001相接。
如图1为I/O 端子外部接线图。
图1 I/O 端子外部接线图2 程序设计(1)经验法所谓的经验法,就是基于设计者经验对来设计程序,这种方法应该以梯形图的“启-保-停”电路模式为依据,对各输出口梯形图的草图进行绘制,并对系统控制原则加以确定,对总控制要求的关键点进行分析,并通过梯形图的方式来呈现出关键点。
分析PLC在数控机床控制系统中的应用
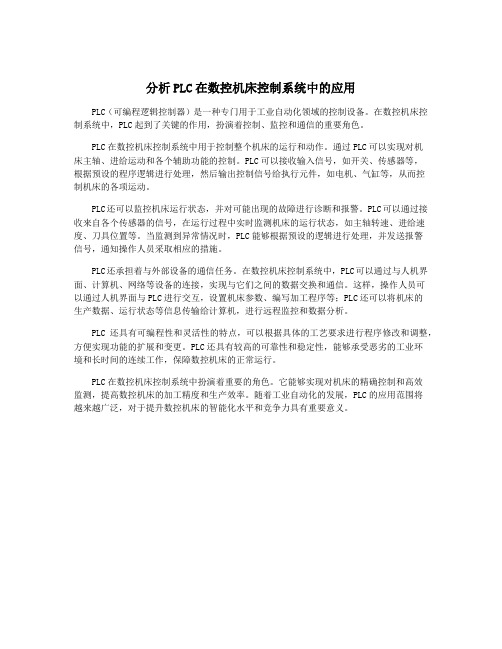
分析PLC在数控机床控制系统中的应用PLC(可编程逻辑控制器)是一种专门用于工业自动化领域的控制设备。
在数控机床控制系统中,PLC起到了关键的作用,扮演着控制、监控和通信的重要角色。
PLC在数控机床控制系统中用于控制整个机床的运行和动作。
通过PLC可以实现对机床主轴、进给运动和各个辅助功能的控制。
PLC可以接收输入信号,如开关、传感器等,根据预设的程序逻辑进行处理,然后输出控制信号给执行元件,如电机、气缸等,从而控制机床的各项运动。
PLC还可以监控机床运行状态,并对可能出现的故障进行诊断和报警。
PLC可以通过接收来自各个传感器的信号,在运行过程中实时监测机床的运行状态,如主轴转速、进给速度、刀具位置等。
当监测到异常情况时,PLC能够根据预设的逻辑进行处理,并发送报警信号,通知操作人员采取相应的措施。
PLC还承担着与外部设备的通信任务。
在数控机床控制系统中,PLC可以通过与人机界面、计算机、网络等设备的连接,实现与它们之间的数据交换和通信。
这样,操作人员可以通过人机界面与PLC进行交互,设置机床参数、编写加工程序等;PLC还可以将机床的生产数据、运行状态等信息传输给计算机,进行远程监控和数据分析。
PLC还具有可编程性和灵活性的特点,可以根据具体的工艺要求进行程序修改和调整,方便实现功能的扩展和变更。
PLC还具有较高的可靠性和稳定性,能够承受恶劣的工业环境和长时间的连续工作,保障数控机床的正常运行。
PLC在数控机床控制系统中扮演着重要的角色。
它能够实现对机床的精确控制和高效监测,提高数控机床的加工精度和生产效率。
随着工业自动化的发展,PLC的应用范围将越来越广泛,对于提升数控机床的智能化水平和竞争力具有重要意义。
- 1、下载文档前请自行甄别文档内容的完整性,平台不提供额外的编辑、内容补充、找答案等附加服务。
- 2、"仅部分预览"的文档,不可在线预览部分如存在完整性等问题,可反馈申请退款(可完整预览的文档不适用该条件!)。
- 3、如文档侵犯您的权益,请联系客服反馈,我们会尽快为您处理(人工客服工作时间:9:00-18:30)。
沈阳城市学院《数控机床电气控制与PLC技术》课程设计说明书学院:机电工程学院班级:机自二班姓名:xxxxx学号: 4指导教师:xxxxxxx2013年12月10日课程设计任务书学院机电学院班级机自二班姓名xx 设计起止日期2013年12月16日-2013年12月27日设计题目:数控机床润滑系统的PLC控制设计任务:应用S7-200SPLC完成数控机床润滑系统的PLC控制要求完成以下工作:1.课题相关任务及PLC的描述;的型号选择3.完成主电路设计以及相应电器元件的选择4.设计PLC 的I/O接线图5.完成梯形图的设计6.编写、整理设计说明书。
指导教师评分:项目分值出勤情况10 一次缺席扣2分,两次缺席扣4分,三次缺席扣10分,出勤情况连带影响学习态度和质疑答辩成绩。
学习态度10 学习态度认真,遵守纪律质疑答辩第一次10 PLC硬件选型第二次10 主电路(5分)和I/O接线图(5分)设计第三次10 梯形图设计答辩30 1、程序仿真:正确打开仿真软件(5分),成功导入程序(5分),正确操作并仿真(10分)2、回答问题:老师根据设计内容提问2-3个问题,答对一个5分说明书质量20 内容完整(5分),结构设计合理(5分),撰写规范工整(5分),排版准确(5分)总分教师签字:年月日摘要机床润滑系统的设计、调试和维修保养,对于提高机床加工精度、延长机床使用寿命等都有着十分重要的作用。
但是在润滑系统的电气控制方面,仍存在以下问题:一是润滑系统工作状态的监控。
数控机床控制系统中一般仅设油箱油面监控,以防供油不足,而对润滑系统易出现的漏油、油路堵塞等现象,不能及时做出反应。
二是设置的润滑循环和给油时间单一,容易造成浪费。
数控机床在不同的工作状态下,需要的润滑剂量是不一样的,如在机床暂停阶段就比加工阶段所需要的润滑油量要少。
针对上述情况,在数控机床电气控制系统中,对润滑控制部分进行了改进设计,时刻监控润滑系统的工作状况,以保证机床机械部件得到良好润滑,并且还可以根据机床的工作状态,自动调整供油、循环时间,以节约润滑油。
关键字:数控机床,润滑系统,PLC,故障分析引言众所周知,要使运动副的磨损减小,必须在运动副表面保持适当的清洁的润滑油膜,即维持磨擦副表面之间恒量供油以形成油膜。
这通常是连续供油的最佳特性(恒流量),然而,有些小型轴承需油量仅为每小时1-2滴,一般润滑设备按此要求连续供油是非常困难的。
此外,很多事实表明,过量供油与供油不足是同样有害的。
例如:对一些轴承在过量供油时会产生附加热量、污染和浪费。
大量实验证明,周期定量供油,既可使油膜不被损坏又不会产生污染和浪费,是一种非常好的润滑方式。
因此当连续供油成为不合适时可采用经济的周期供油系统来实现。
该系统使定量的润滑油按预定的周期时间对各润滑点供油,使运动副均适合采用周期润滑系统来润滑机床润滑系统在机床整机中占有十分重要的位置,其设计、调试和维修保养,对于提高机床加工精度、延长机床使用寿命等都有着十分重要的作用。
现代机床导轨、丝杆等滑动副的润滑,基本上都是采用集中润滑系统。
集中润滑系统是由一个液压泵提供一定排量、一定压力的润滑油,为系统中所有的主、次油路上的分流器供油,而由分流器将油按所需油量分配到各润滑点:同时,由控制器完成润滑时间、次数的监控和故障报警以及停机等功能,以实现自动润滑的目的。
集中润滑系统的特点是定时、定量、准确、效率高,使用方便可靠,有利于提高机器寿命,保障使用性能。
目录1、润滑系统的分类 (4)单线阻尼式润滑系统 (4)递进式润滑系 0容积式润滑系统 (1)2、任务分析 (1)PLC简介 (2)具体任务原解释 (2)4、主电路、I/O接线图的设计以及对应元器件的选择 (5)5、梯形图的设计 (6)6、程序仿真 (9)7、润滑系统故障分析 (10)润滑系统工作状态的监控 (10)润滑时间及润滑次数的控制 (10)润滑报警信号的处理 (12)结语 (12)8、致谢 (13)9、参考文献: (13)1、润滑系统的分类集中润滑系统按使用的润滑元件可分为阻尼式润滑系统、递进式润滑系统和容积式润滑系统。
单线阻尼式润滑系统此系统适合于机床润滑点需油量相对较少,并需周期供油的场合。
它是利用阻尼式分配器,把泵打出的油按一定比例分配到润滑点。
一般用于循环系统,也可以用于开放系统,可通过时间的控制,以控制润滑点的油量。
该润滑系统非常灵活,多一个润滑点或少一个都可以,并可由用户安装,且当某一点发生阻塞时,不影响其他点的使用,故应用十分广泛。
图1-1所示为单线阻尼式润滑系统。
图 1-1 单线阻尼式润滑系统递进式润滑系递进式润滑系统主要由泵站、递进片式分流器组成,并可附有控制装置加以监控。
其特点是能对任一润滑点的堵塞进行报警并终止运行,以保护设备;定量准确、压力高,不但可以使用稀油,而且还适用于使用油脂润滑的情况。
润滑点可达100个,压力可达21MPa。
图 1-2 递进式润滑系统递进式分流器由一块底板、一块端板及最少三块中间板组成。
一组阀最多可有8块中间板,可润滑18个点。
其工作原理是由中间板中的柱塞从一定位置起依次动作供油,若某一点产生堵塞,则下一个出油口就不会动作,因而整个分流器停止供油。
堵塞指示器可以指示堵塞位置,便于维修。
图1-2所示为递进式润滑系统。
容积式润滑系统该系统以定量阀为分配器向润滑点供油,在系统中配有压力继电器,使得系统油压达到预定值后发讯,使电动机延时停止,润滑油从定量分配器供给,系统通过换向阀卸荷,并保持一个最低压力,使定量阀分配器补充润滑油,电动机再次起动,重复这一过程,直至达到规定润滑时间。
该系统压力一般在50MPa以下,润滑点可达几百个,其应用范围广、性能可靠,但不能作为连续润滑系统。
图 1-3 容积式润滑系统定量阀的结构原理是:由上下两个油腔组成,在系统的高压下将油打到润滑点,在低压时,靠自身弹簧复位和碗形密封将存于下腔的油压入位于上腔的排油腔,排量为~,并可按实际需要进行组合。
图1-3 所示为容积式润滑系统。
2、任务分析当系统准备好之后,CNC发出信号,使得润滑系统开始工作,首次润滑15s后,电机停止工作。
当压力开关SP2因压力降低而接通时,开始计时25min,计时完成后,当压力开关SP2断开,润滑电机再次工作15s,并循环工作。
QF4为润滑电动机过载保护开关,SL为润滑油检测开关,SP3为油路泄露开关,SP4为油路堵塞开关,当电机过载或润滑油不足时则使系统发出报警信号。
PLC简介★PLC的概念可编程序控制器,英文称Programmable Controller,简称PC。
但由于PC容易和个人计算机(Personal Computer)混淆,故人们仍习惯地用PLC作为可编程序控制器的缩写。
它是一个以微处理器为核心的数字运算操作的电子系统装置,专为在工业现场应用而设计,它采用可编程序的存储器,用以在其内部存储执行逻辑运算、顺序控制、定时/计数和算术运算等操作指令,并通过数字式或模拟式的输入、输出接口,控制各种类型的机械或生产过程。
PLC是微机技术与传统的继电接触控制技术相结合的产物,它克服了继电接触控制系统中的机械触点的接线复杂、可靠性低、功耗高、通用性和灵活性差的缺点,充分利用了微处理器的优点,又照顾到现场电气操作维修人员的技能与习惯,特别是PLC的程序编制,不需要专门的计算机编程语言知识,而是采用了一套以继电器梯形图为基础的简单指令形式,使用户程序编制形象、直观、方便易学;调试与查错也都很方便。
用户在购到所需的PLC后,只需按说明书的提示,做少量的接线和简易的用户程序编制工作,就可灵活方便地将PLC 应用于生产实践。
★PLC的组成PLC的构成: PLC的类型繁多,功能和指令系统也不尽相同,但结构与工作原理则大同小异,通常由主机、输入/输出接口、电源扩展器接口和外部设备接口等几个主要部分组成。
PLC的硬件系统结构如图1所示:具体任务原解释如图2-2,为润滑系统自动控制流程图。
当系统准备好之后,CNC发出信号,使得润滑系统开始工作,首次润滑15s后,电机停止工作。
当压力开关SP2因压力降低而接通时,开始计时25min,计时完成后,当压力开关SP2断开,润滑电机再次工作15s,并循环工作。
QF4为润滑电动机过载保护开关,SL为润滑油检测开关,SP3为油路泄露开关,SP4为油路堵塞开关,当电机过载或润滑油不足时则使系统发出报警信号。
图 2-2 润滑系统自动控制流程图3、PLC型号的选择输入输出名称地址编码符号名称地址编码符号启动按钮SB1 电动机启动M1 油路堵塞开关SP4 油路堵塞L1润滑油不足开关SL 润滑油不足L2油路漏油开关SP3 油路漏油L3 润滑电动机过载开关QF4 润滑电动机过载L4 压力开关SP2 压力开关未接通L5压力开关SP2 压力开关未断开L6S7-200 系列可编程控制器有CPU21X 系列和CPU22X 系列,其中CPU22X 系列可编程控制器提供了CPU221、CPU222、CPU224 和CPU226 4 种基本型号。
CPU222 集成8 输入/6 输出,I/ O 点数为14 点,有两个模块的扩展,6 KB 程序和数据存储容量,可进行一定模拟量的控制,是S7-200 系列中低成本的单元-200系列是一类可编程逻辑控制器(Micro PLC)。
这一系列产品可以满足多种多样的自动化控制需要,下图展示一台S7-200 Micro PLC的 CPU222系列PLC的CPU外型图,具有紧凑的设计、良好的扩展性、低廉的价格以及强大的指令,使得S7-200可以近乎完美地满足小规模的控制要求。
此外,丰富的CPU类型和电压等级使其在解决用户的工业自动化问题时,具有很强的适应性。
S7-200 CPU模块包括一个中央处理器单元(CPU)、电源以及数字量I/O点,这些都被集成在一个紧凑、独立的设备中。
S7S7-200 CPU外型图●CP U负责执行程序和存储数据,以便对工业自动控制任务或过程进行控制。
●输入和输出是系统的控制点:输入部分从现场设备(例如传感器或开关)中采集信号,输出部分则控制泵、电机、以及工业过程中的其他设备。
●电源向CPU及其所连接的任何模块提供电力。
●通讯端口允许将S7-200CPU同编程器或一些设备连接起来。
●状态信号灯显示了CPU的工作模式(运行或停止),本机的I/O的当前状态,以及检查出来的系统错误。
●通过扩展模块可以增加CPU的I/O点数。
●通过扩展模块可以提供其通讯功能。
●EEPROM卡可以存储CPU程序,也可以将一个CPU中的程序传送到另一个CPU中。
4、主电路、I/O接线图的设计以及对应元器件的选择在数控系统中,大部分的自动控制都是通过PLC来实现的,润滑系统的控制也一样,通过PLC程序控制电机的工作。