依据排列图
排列图1
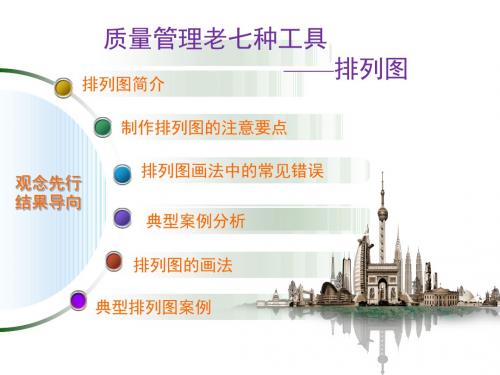
制表:张秀丽
制表时间:2012年1月
五、排列图的画法
名称 总装 油漆 电气 加工 防护 包装 铸件 其它
频数 25 16 3 2 2 2 2 3
六、典型排列图案例
★实例1:某车型车身异响质量缺陷9\10\11月产品检测结果
***车车身异响质量缺陷统计表2005.12
月份
9
10
11
统计数量 200
97% 99.4% 100%
典型案例剖析
公司要求
生产现状
XXX机床床身合格率≥ 95%
频数(个)
累计百分比%
87.5% 95.8%
79.1% 66.6% ● ●
●
100%
15
54.1% ●
80%
●
10
29.1%
60%
7● 6
40%
5
33
21 2
20%
0
0
小组选题
提高XXX机床床身导轨精度合格率
现状调查1:对2011年1~3月生产的床身抽样进行问题汇总
率)和累计比率(累计频率); • 以左侧纵坐标为频数,横坐标按频数从大到小用条状块
依次排列;以右侧纵坐标为累计频率,绘制累计频率曲 线。 • 找出主要因素。按累计百分比将影响因素分为三类:
0~80%为A类因素,主要因素; 80%~90%为B类因素,次要因素; 90%~100%为C类因素,一般因素。
二、制作排列图的注意要点
2
液压箱噪音
105
3
快速箱异响
27
4
Y向丝杠噪音
12
5
其他噪音
9
453
66.1% 89.2% 95.4% 98.0% 100.0%
排列图法
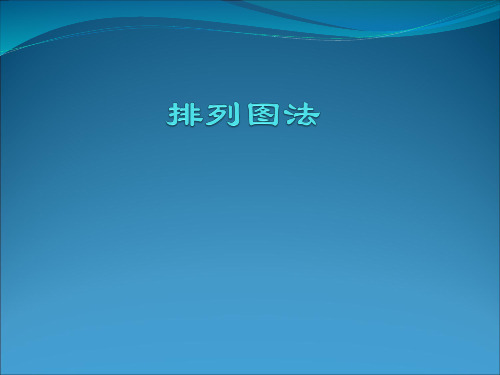
左 键 双 击
修改右侧纵坐标轴数据
出现以下图示
点击累计百分比 折线出现以下画面
点击图表区域
图表工具
依次选择“布局”“次要横坐标 轴”“显示从左向右坐标轴”
出现以下图示
右键单击 选择“设置坐标轴格式”
“坐标轴标签” 选择“无”
位置坐标轴 选择“在刻 度线上”
出现以下图表
左键点击例次的直方图
称为“劳伦兹曲线”
1930年美国品管泰斗朱兰博士将劳伦兹曲线应用到品质管理中 20世纪60年代,日本品管大师石川馨在推行自己发明的QCC品管圈时
使用了排列图法,从而成为品管七大手法
排列图的结构
折线表示累计频率 纵 坐 标
100% 50 81.13%
90.57%
94.34%
90% 80% 70% 60% 50%
40 66.04% 30 20 20 37.74% 15 8
右侧代表 不合格出现 的累计频率
例次
40%
左侧代表 不合格出现 的频数、次数
10
直方形高度表示 相应的因素的影响程度
20% 10% 5 2 3 0%
30%
累计百分比
0
0%
横坐标表示影响质量的各种因素, 按影响大小顺序排列
柏拉图意义
作为决定降低不良的依据
选择“分类 间距”为0
基本完成
进行细节调整
作为决定改善目标之依据
确定主要因素,找出改进着手点
如何制作排列图
收集资料 项目分类
如:2013年6月某日,对病区的住院患者腕
带使用现状进行容填写不完整 腕带字迹不易辨认
特殊人群未使用红色腕带 患者感觉不舒适
整理数据
质量管理工具-统计方法-排列图因果图
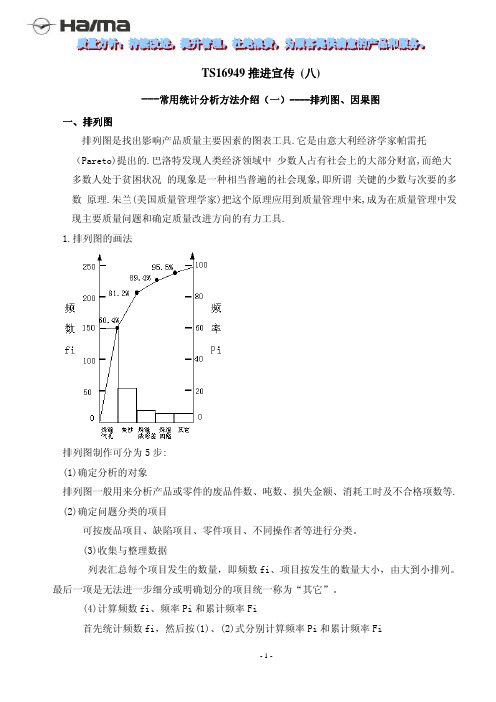
TS16949推进宣传(八)---常用统计分析方法介绍(一)----排列图、因果图一、排列图排列图是找出影响产品质量主要因素的图表工具.它是由意大利经济学家帕雷托(Pareto)提出的.巴洛特发现人类经济领域中"少数人占有社会上的大部分财富,而绝大多数人处于贫困状况"的现象是一种相当普遍的社会现象,即所谓"关键的少数与次要的多数"原理.朱兰(美国质量管理学家)把这个原理应用到质量管理中来,成为在质量管理中发现主要质量问题和确定质量改进方向的有力工具.1.排列图的画法排列图制作可分为5步:(1)确定分析的对象排列图一般用来分析产品或零件的废品件数、吨数、损失金额、消耗工时及不合格项数等.(2)确定问题分类的项目可按废品项目、缺陷项目、零件项目、不同操作者等进行分类。
(3)收集与整理数据列表汇总每个项目发生的数量,即频数fi、项目按发生的数量大小,由大到小排列。
最后一项是无法进一步细分或明确划分的项目统一称为“其它”。
(4)计算频数fi、频率Pi和累计频率Fi首先统计频数fi,然后按(1)、(2)式分别计算频率Pi和累计频率Fi(1)式中,f为各项目发生频数之和。
(2)(5)画排列图排列图由两个纵坐标,一个横坐标,几个顺序排列的矩形和一条累计频率折线组成。
如图1所示为一排列图实例。
2.排列图用途(1)确定主要因素、有影响因素和次要因素根据排列图可以确定质量问题的主要因素:累计频率Fi在0-80%左右的若干因素。
是影响产品质量的主要因素,如图中焊缝气孔和夹渣。
主要因素个数一般为1-2个,最多不超过3个。
根据排列图可以确定质量问题的有影响因素:累计频率Fi在80-95%左右的若干因素。
它们对产品质量有一定影响,称为有影响因素。
根据排列图可以确定质量问题的次要因素:累计频率Fi在95-100%左右的若干因素,其对产品质量仅有轻徽影响,称为次要因素。
(2)抓主要因素解决质量问题将质量影响因素分类之后,重点针对1-2项主要因素进行改进提高,以解决质量问题。
帕累托图

BZ35-2油田
80/20原则(帕累托法则)
1897年,意大利经济学者帕累托偶然注意到19世纪英国人的财富和收益模式。在 调查取样中,发现大部份的财富流向了少数人手里。同时,他还从早期的资料中 发现,在其他的国家,都发现有这种微妙关系一再出现,而且在数学上呈现出一 种稳定的关系。于是,帕累托从大量具体的事实中发现:社会上20%的人占有80% 的社会财富,即:财富在人口中的分配是不平衡的。 核心内容:关键的少数、次要的多数、分配不平衡 延伸:80%的质量问题是由20%的原因引起的 20%的产品或20%的客户,为企业赚得约80%的销售额 80%的时间用来做20%的事情
BZ35-2油田
排列图的起源
最早是由意大利经济学家帕累托(柏拉)用来分析社会财富的分布状况。他发现 少数人占有着绝大多数财富,而绝大多数人却占有少量财富处于贫困的状态。这 种少数人占有着绝大多数财富左右社会经济发展的现象,即所谓“关键的少数、 次要的多数”的关系。 后来,美国质量管理专家朱兰,把这个“关键的少数、次要的多数”的原理应用 于质量管理中,便成为常用方法之一(排列图),并广泛应用于其它的专业管理。
排列图(帕累托图)介绍
渤中35-2油田 尹旭
2015年6月5日
排列图的基本概念
排列图是为寻找主要问题或影响质量的主要原因所 使用的图。它是由两个纵坐标、一个横坐标、几个 按高低顺序依次排列的长方形和一条累计百分比折 线所组成的图·排列图又称帕累托(柏拉)图。
排列图用双直角坐标系表示,左边纵坐标表示频数, 右边纵坐标表示频率.分析线表示累积频率,横坐 标表示影响质量的各项因素,按影响程度的大小 (即出现频数多少)从左到右排列,通过对排列图 的观察分析可以抓住影响质量的主要因素。
6.绘制柱状图和累计曲线。
排列图

1 2 3 4 5 6
合计
4
6 200
194
200
97
100
QCC - Page ‹#› Irico Group Corporation
QCC知识
应用实例-作排列图
某商场服务质量排列图
200 180 140 80 频数
●
●
●
累计%
100% 75% 50%
●
N=200
●
40
0
25%
A
Irico Group Corporation
QCC知识
QCC - Page ‹#› Irico Group Corporation
QCC知识
二、排 列 图
遵循“关键的少数和次要的多数”的规律 来源于自然科学领域的统计规定 1.排列图的特点 2.排列图的应用 3.排列图的实例 4.排列图注意事项
频 200 数 180 140 80 40
● ● ● ●
6、图形规范,标注齐全。 7、累计百分比是折线,不是直线。 8、目标值高的情况不宜使用排列图。
QCC - Page ‹#› Irico G数 右 频率 %
排列图的特点
c、累计百分比折线 邻线夹角小于180度(“其它”对应位置除外)
QCC - Page ‹#› Irico Group Corporation
QCC知识
2.排列图的应用
按重要性顺序显示每一项目,对总体效果的作用排列 改进的机会 。
程序
明确分析的题目 收集数据(尽可能多的)
●
累计% 100 % 75 % 50 % 25%
N=200
0
A
B
C
D
E 其它 项目
2 排列图分析法

排列图分析法
8 排列图的应用实例 某化工机械厂为从事尿素合成的公司生产尿素合 成塔,尿素合成塔在生产过程中需要承受一定的压 力,上面共有成千上万个焊缝和焊点。由于该厂所 生产的十五台尿素合成塔均不同程度地出现了焊缝 缺陷,由此对返修所需工时的数据统计如表7-1所 示。
ቤተ መጻሕፍቲ ባይዱ排列图分析法
序号 1 2 3 4 5
图7-1
排列图的绘制步骤
5 能达到何目标:非常直观地展示出如何确定问题 的优先顺序,将资源集中在何处才能取得最佳 效益。这种展示让企业各级一看就懂。 6 注意事项:仔细分析结果总是很重要;不仅靠数 据还要利用常识来找出问题的原因和优先顺序。
7 使用程序: 找出问题和可能的原因。收集有关原因 的信息。绘制帕雷托分析图,横坐标表示 原因,纵坐标表示问题,以出现次数、频 率或造成的成本来表示。找出最关键的几 个原因。依据重要性排序,利用改进技术 消除产生问题的原因。
排列图分析法
8 例2 : 某洗衣机制造商出现质量危机。在一次 广泛的可信度测试中,一家大型杂志将其品 排在末位并建议消费者不要购买。 该公司具有完善的失误记录,列出的失误 种类达22种。但运用帕雷托分析法表明,仅 其中的4种失误就占了所有记录的83%。
排列图分析法
本课程学习到此
北京数码神州科技有限责任公司 质上教育
排列图的绘制步骤 排列图能够从任何众多的项目中找出最重要的问 题,能清楚地看到问题的大小顺序,能了解该项目 在全体中所占的重要程度,具有较强的说服力,被 广泛应用于确定改革的主要目标和效果、调查产生 缺陷及故障的原因。因此,企业管理人员必须掌握 排列图的绘制,并将其应用到质量过程中去。
一般说来,绘制排列图的步骤如图7-1所示, 即:确定调查事项,收集数据,按内容或原因 对数据分类,然后进行合计、整理数据,计算 累积数,计算累积占有率,作出柱形图,画出 累积曲线,填写有关事项。
柏拉图ParetoDiagram排列图

第4章柏拉图77第4章柏拉图小打式。
Diagram)排列图一、前言由生产现场所收集到的数据,有效的加以分析、运用,才能成为有价值的数据。
而将此数据加以分类、整理并作成图表,充分的掌握问题点及重要原因,则是目前不可或缺的管理工具。
而最为现场人员广泛使用于数据管理的图表为柏拉图。
二、柏拉图的由来意大利经济学家V.Pareto(1848-1923)在1897年分析社会经济结构时,赫然发现国民所得的大部份均集中于少数人身上,于是将所得的大小与拥有所得的关系加以整理。
发现有一定的方程式可以表示, 称为[柏拉图法则]。
1907年美国经济学者M.O.Lorenz使用累积分配曲线来描绘[柏拉图法则],也就是经济学所谓的劳伦兹(Lorenz)曲线。
美国品管专家J.M.Juran(朱兰博士)将劳伦兹曲线应用于品管上,同时创出[Vital Few, Trivial Many](重要的少数,次要的多数)的见解,并借用Pareto的名字,将此现象定为[柏拉图原理]。
[柏拉图]方法,由品管圈(QCC)的创始人日本石川馨博士介绍到品管圈活动中使用,而成为品管七大手法之一。
三、柏拉图的定义1.根据所搜集的数据,按不良原因、不良状况、不良项目、不良发生的位置等不同区分标准而加以整理、分类,从中寻求占最大比率的原因、状况或位置,按其大小顺序排列,再加上累积值的图形。
2.从柏拉图可看出那一项目有问题,其影响度如何,以判断问题的症结所在,并针对问题点采取改善措施,故又称为ABC图。
(所谓ABC分析的重点是强调对于一切事务,依其价值的大小而付出不同的努力,以获至效果;亦即柏拉图分析前面2-3项重要项目的控制)。
78品管七大手法3.又因图的排列系按大小顺序排列,故又可称为排列图。
四、柏拉图的制作步骤1.柏拉图的制作方法步骤1:决定数据的分类项目。
分类的方式有:(1)结果的分类包括不良项目别、场所别、时间别、工程别。
(2)原因的分类包括材料别(厂商、成份等)、方式别(作业条件、程序、方法、环境等、人员别(年龄、熟练度、经验等、设备别(机械、工具等)等。
品管(QC)七大手法之排列图(柏拉图)
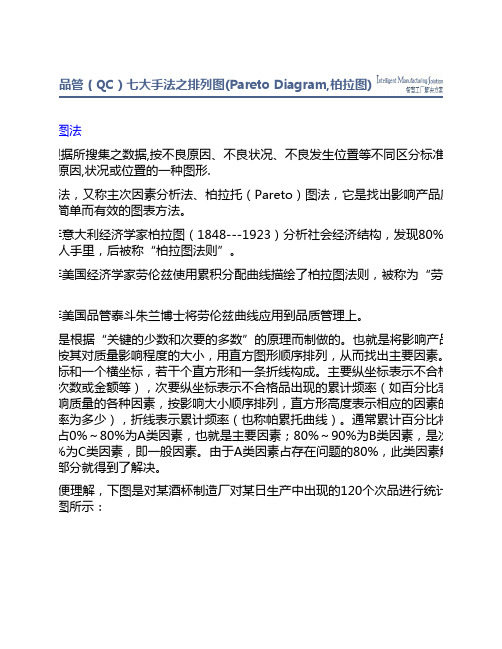
品管(QC)七大手法之排列图(Pareto Diagram,柏拉图)什么是排列图法定义:根据所搜集之数据,按不良原因、不良状况、不良发生位置等不同区分标准,以寻求占最大比率之原因,状况或位置的一种图形.排列图法,又称主次因素分析法、柏拉托(Pareto)图法,它是找出影响产品质量主要因素的一种简单而有效的图表方法。
1897年意大利经济学家柏拉图(1848---1923)分析社会经济结构,发现80%的财富掌握在20%的人手里,后被称“柏拉图法则”。
1907年美国经济学家劳伦兹使用累积分配曲线描绘了柏拉图法则,被称为“劳伦兹曲1930年美国品管泰斗朱兰博士将劳伦兹曲线应用到品质管理上。
排列图是根据“关键的少数和次要的多数”的原理而制做的。
也就是将影响产品质量的众多影响因素按其对质量影响程度的大小,用直方图形顺序排列,从而找出主要因素。
其结构是由两个纵坐标和一个横坐标,若干个直方形和一条折线构成。
主要纵坐标表示不合格品出现的频数(出现次数或金额等),次要纵坐标表示不合格品出现的累计频率(如百分比表示),横坐标表示影响质量的各种因素,按影响大小顺序排列,直方形高度表示相应的因素的影响程度(即出现频率为多少),折线表示累计频率(也称帕累托曲线)。
通常累计百分比将影响因素分为三类:占0%~80%为A类因素,也就是主要因素;80%~90%为B类因素,是次要因素;90%~100%为C类因素,即一般因素。
由于A类因素占存在问题的80%,此类因素解决了,质量问题大部分就得到了解决。
为了方便理解,下图是对某酒杯制造厂对某日生产中出现的120个次品进行统计,做出排列图,如下图所示:帕累托图排列图的作用 1、作为降低不良依据。
2、决定改善的攻击目标。
3、确认改善效果。
4、用于发现现场的重要问题点 5、用于整理报表或记录。
6、可作不同条件的评价。
排列图的使用排列图的使用要以层别法为前提,将层别法的项目从大到小的进行排列,再加上累积值的图形。
- 1、下载文档前请自行甄别文档内容的完整性,平台不提供额外的编辑、内容补充、找答案等附加服务。
- 2、"仅部分预览"的文档,不可在线预览部分如存在完整性等问题,可反馈申请退款(可完整预览的文档不适用该条件!)。
- 3、如文档侵犯您的权益,请联系客服反馈,我们会尽快为您处理(人工客服工作时间:9:00-18:30)。
9 45 54 55 55 47 63 50 49 55 60 63 45
75
0
32
漏气Βιβλιοθήκη 033出正确的措施:
工人B 不漏气
5
4
7
①使用甲厂提供的气缸垫时,
漏气率%
0
43
25
要采用工人B的操作方法;
漏气
3
7
10
工人C 不漏气
7
2
9
②使用乙厂提供的气缸垫时,
漏气率%
30
78
53
要采用工人A的操作方法。
漏气
9
10
19
不漏气
14
17
31
合计
漏气率%
39
37
38
合计
23
27
50
实践证明,分层法可以帮助我们清楚的分析 隐藏在现象背后的事物之间错综复杂的关系,从 而有助于我们尽快的发现事情的本质和原因,作 出正确的判断,采取有效的措施来解决问题。
例:在柴油机装配过程中,经常发生气缸垫漏气的现象,为解决这一问 题,对“气缸垫的装配”工序进行现场统计。 (1)搜集数据:n = 50, 漏气数f = 19 , 漏气率 p = f /n = 19/50 =38% (2)分析原因:
通过分析,得知造成漏气的原因有以下两个: ① 该工序中负责涂胶剂的三个工人A、B、C的操作方法有差异 ② 气缸垫的两个供货厂家使用的原材料有差异。 针对两个因素,将数 据进行分类列表,得到以下的表格:
H、画直方图
例:为研究某产品的质量状况,从一批产品中抽取了100个特性数 据,如下表所列:
组号
实
测
数
据
Xmax
Xmin
1 61 55 63 39 49 55 50 55 55 50 63 39
2 44 38 50 48 53 50 50 50 50 52 53 38
3 48 52 52 52 48 55 45 49 50 54 55 45
二)分层法 Stratification 分层就是将所搜集到的数据进行合理的分类,把性质相同、在同一
条件下搜集的数据归纳在一起,划分成的数据组称为“层”,通过数据 分层把错综复杂的质量影响因素分析清楚。
通常,我们需要将分层法与其他统计方法一起联合使用,即把性质 相同、在同一条件下搜集的数据归纳在一起,然后再分别使用其他方法 制成分层排列图、分层直方图、分层散布图等等。
工人 漏气 不漏气 漏气率%
A
6
13
32
B
3
9
25
C
10
9
53
合计 19
31
38
厂家 漏气 不漏气 漏气率%
甲
9
14
39
乙
10
17
37
合计 19
31
38
从右侧的表中就可以清晰
甲厂
乙厂
合计
的看出,不同的工人使用不
漏气
6
0
6
同厂家提供的气缸垫的效果
工人A 不漏气
2
11
13
是不同的,因此我们可以提
漏气率%
统计质量控制的新、老七种工具
老七种工具
调查表 分层法 直方图 散布图 排列图 因果图 控制图
新七种工具
关联图 系统图 KJ法 矩阵图 矩阵数据分析法 过程决策分析法 矢线法
§1.老七种工具
一)调查表
调查表是为了调查客观事物、产品和工作质量,或是为了分层搜集数据 而设计的图表。它通过表格的形式把产品可能出现的情况及其分类预先列出, 在检查产品时只需要在相应分类中进行统计,统计时只需要在表格上相应的 栏目内填上数字或符号即可。 调查表应具有以下特点: • 内容简单明了,重点突出 • 填写方便,符号容易记忆、辨别 • 调查、加工和检验的次序与调查表的填写次序应基本一致
h X max X min k
E、确定组界
组界为组的边界,通常最小值开始,先将最小值放在第一组的中间
位置,第一组的组界为:
F、确定各组的组中值
(X min
h) 2
~(X min
h) 2
所谓组中值,就是处于各组中心位置的数值,又叫中心值。
某组的组中值(wi )=(该组上限值+该组下限值)/ 2 G、统计各组的频数
然后在上面将缺陷位置标出;二是用语言、文字来描述具体的不合格项 目,通过调查统计出每个不合格项目的频数。 C、频数调查表
频数调查表是在数据搜集时用来进行频数统计的表格,这种表格能 很好的满足及时性需要,每调查一个数据,就可以在表格上的相应的组 内作一个标记,这样调查完毕时,频数分布表也就随之完成,我们便能 依据此表迅速的做出直方图,十分方便。
常用的调查表有以下三种:A、不合格项目调查表 质量管理中的“合格”与“不合格”,都是相对于特定的标准、规格和公 差而言的。调查表的目的是统计各种不合格项目的比例。
调查 调 合 日期 查 格
不合格品
不合格品类型
数 数 废品数 次品数 返修品数 废品类型 次品类型 返修品类型 合格品率%
B、缺陷位置调查表 这种调查表有两种表现形式:一是将产品的外形图、展开图画出来,
最大值用Xmax表示, 最小值用 Xmin 表示,极差用R表示
C、确定组数 (k) 组数通常用k表示, k与数据量有关,数据多,多分组;数据
少,少分组。有人用下面的经验公式来确定组数:
k 1 3.31 lgn
由于正态分布成对称形,故常取 k 为奇数 D、求出组距 (h)
组距即组与组之间的间隔量,等于极差除以组数,即:
三)直方图 histogram
直方图法适用于对大量计量值数据进行整理加工,找出其中的统计 规律,即分析数据的分布状态,以便于对其总体的分布特征进行推断, 对工序或批量产品的质量水平及其均匀程度进行分析。 1) 制作直方图的步骤如下: A、收集数据:一般都要随机抽取50个以上的质量特性数据,并按照先 后顺序排列 B、找出数据中的最大值、最小值,并计算出极差
4 45 50 55 51 48 54 53 55 60 55 60 45
5 56 43 47 50 50 50 63 47 40 43 63 40
6 54 53 45 43 48 43 45 43 53 53 54 43
7 49 47 48 40 48 45 47 52 48 50 52 40
8 47 48 54 50 47 49 50 55 51 43 55 43
从右边的两个表格中,我们似乎可以得到 这样的结论:降低气缸漏气率的办法可以采 用乙厂提供的气缸和工人B的操作方法。但 是实践证明,这样做的结果是漏气率非但没 有降低,反而增加到43%,这是什么原因呢? 其实原因很简单,由于上面的方法只是单纯 的分别考虑了操作者和原材料造成漏气的情 况,而没有进一步考虑不同工人使用不同工 厂提供的气缸垫,产生的漏气结果也不同, 因此需要更精细的综合分类式的分析。