02-IE讲义与标准工时
IE与标准工时
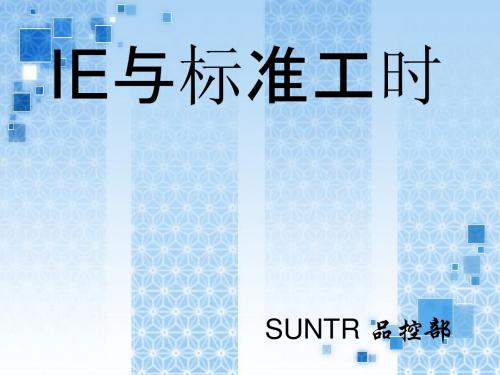
IE与标准工时SUNTR 品控部主要内容:一.IE简介二.标准工时的意义与制定一、什么是IE?IE是英文Industrial Engineering的简称,直译为工业工程,是以人、物料、设备、能源和住处组成的集成系统为主要研究对象,综合应用工程技术、管理科学和社会科学的理论与方法等知识,对其进行规划、设计、管理、改进和创新等活动,使其达到降低成本,提高质量和效益的目的的一项活动。
简单地说,IE是改善效率、成本、品质的方法科学。
IE研究的对象与方法工序分析动作分析搬运与布局时间分析什么工序分析?对工序加以分析、调查,找出其中浪费、不均匀、不合理的地方,进而进行改善的方法,称之为工序分析。
工序分析的目标整理工序流程工序流程中是否存在不经济、停滞现象工序顺序是否合理工序流程是否顺畅,设备配置、搬运方法是否合理工序中的作业是否必要,是否可以取消,是否有更好的作业方法TIB1-63系列断路器流程改进装配瞬动延时铆合移印复瞬标延包装合格不合格装配延时铆合移印瞬动标延包装合格不合格改善前改善后何谓动作分析?把作业动作进行细致的分解,一个一个记录下来,通过分析,对其进行删除、换序、合并、简化,达到减少动作提高速度的目的称之为动作分析。
动作分析的目标动作分析就是对作业动作进行细致的分解研究,消除以下不合理现象,使动作更为简化,更为合理,从而提升生产效率的方法。
停滞无效动作次序不合理不均衡(如:太忙碌、太清闲等)浪费搬运与布局研究搬运与布局的目的:1.提高搬运活性2.缩短搬运距离3.使工序没有堵塞,物流顺畅4.有效利用空间TIB2L搬运与布局改善改善前测试台装配拉瞬动台延时房改善后装配拉瞬动台测试台延时房时间分析什么是时间分析?所谓时间分析,就是针对时间及产出做定量的分析,找出时间利用不合理的地方,从而进行改善的方法,是IE 方法的一种基本方法。
时间分析的用途1.作为改善现行作业方法和设定标准作业的基础资料2.作为设定标准工时的基础资料3.作为决定人员分配的基础资料4.作为决定人员应操作机械台数的基础资料5.用时间值来确定作业的改善效果6.作为公正的评价作业者技能及熟练程度和教导个人的资料7.提供标准成本的基础资料时间分析有哪些方法?时间分析直接法间接法秒表法摄影法其他经验估计法既定时间法(PTS)标准时间法WF MTM二、标准工时定义:所谓的标准工时,就是指在正常条件下,一位受过训练的熟练工作者,以规定的作业方法和用具,完成一定的质和量的工作所需的时间。
标准工时管理培训讲义
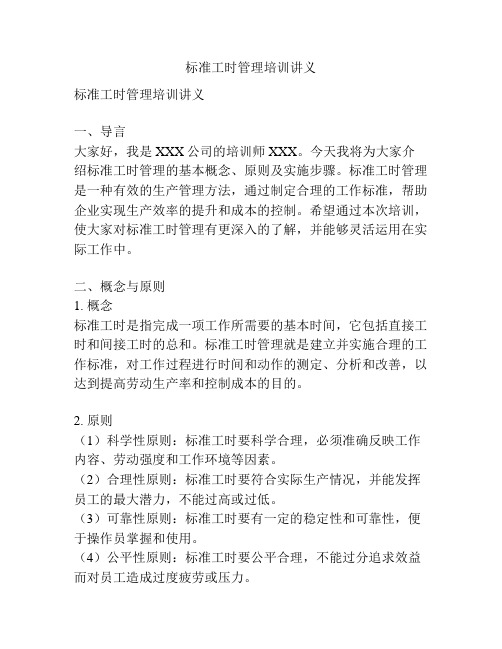
标准工时管理培训讲义标准工时管理培训讲义一、导言大家好,我是XXX公司的培训师XXX。
今天我将为大家介绍标准工时管理的基本概念、原则及实施步骤。
标准工时管理是一种有效的生产管理方法,通过制定合理的工作标准,帮助企业实现生产效率的提升和成本的控制。
希望通过本次培训,使大家对标准工时管理有更深入的了解,并能够灵活运用在实际工作中。
二、概念与原则1. 概念标准工时是指完成一项工作所需要的基本时间,它包括直接工时和间接工时的总和。
标准工时管理就是建立并实施合理的工作标准,对工作过程进行时间和动作的测定、分析和改善,以达到提高劳动生产率和控制成本的目的。
2. 原则(1)科学性原则:标准工时要科学合理,必须准确反映工作内容、劳动强度和工作环境等因素。
(2)合理性原则:标准工时要符合实际生产情况,并能发挥员工的最大潜力,不能过高或过低。
(3)可靠性原则:标准工时要有一定的稳定性和可靠性,便于操作员掌握和使用。
(4)公平性原则:标准工时要公平合理,不能过分追求效益而对员工造成过度疲劳或压力。
三、标准工时管理步骤1. 测定工作内容合理的工作标准首先要明确工作内容,包括具体的工作任务、工作环境、工作方法等。
通过观察、访谈、问卷调查等方法,获取相关信息,综合分析明确工作内容。
2. 测定工作时间根据测定工作内容,确定完成每项工作所需的时间。
可以借鉴历史数据、现场观察、实际操作等方法,精确测算工作所需时间。
3. 制定标准工时依据测定的工作时间,制定出符合实际情况的标准工时。
标准工时应当考虑到员工的工作能力、工作环境、工作任务等因素,同时也要确保生产效率和质量。
4. 引入标准工时将制定好的标准工时引入到实际工作中,让员工按照标准工时进行工作,并监控工时的使用情况。
同时,也要进行追踪调整,不断完善和优化标准工时。
5. 培训员工培训是标准工时管理的重要环节,通过向员工普及标准工时的概念、原则和操作方法,提高员工对标准工时的认识和运用能力,使其能够积极配合标准工时的执行。
标准工时培训讲义

标准工时培训讲义标准工时培训讲义一、概述标准工时是一种衡量工作时效的方法,通过设定合理的工作时间来评估员工的工作效率。
标准工时的引入可以帮助企业全面提高工作效率,优化生产流程,实现资源的合理配置。
本次培训将重点介绍标准工时的概念、原理和实施步骤,帮助员工掌握标准工时的基本知识和应用技巧。
二、标准工时的定义和意义1. 标准工时的定义:标准工时是指在不超过正常工作强度和保证生产质量的前提下,按照合理的工作方法和工作速度,完成一个标准工作任务所需要的时间。
2. 标准工时的意义:- 评估员工的工作效率,帮助企业确定合理的工作时间;- 优化生产流程,提高企业的生产效率;- 增强生产线的稳定性,减少资源浪费;- 为企业的奖惩制度提供依据;- 为企业提供参考,实现资源的合理分配。
三、标准工时的计算方法1. 标准工时计算公式:标准工时 = 标准工作量 / 标准工作效率其中,标准工作量指的是完成一个标准工作任务所需的工作量;标准工作效率表示单位时间内完成工作量的能力。
2. 标准工作量的确定:- 调研比较法:通过调研其他企业类似工作任务所需的时间,综合考虑因素,确定标准工作量。
- 样本分析法:选择一部分典型样本进行时间观察和数据分析,得出标准工作量。
- 经验估算法:根据过往的经验和实际情况,估算出标准工作量。
3. 标准工作效率的确定:- 工作速度法:根据实际工作任务完成的时间和标准工作量,计算出工作速度。
- 经验估算法:根据过往的经验和实际情况,估算出标准工作效率。
四、标准工时的实施步骤1. 了解企业现状:- 收集和整理各个工作岗位的工作内容和工作要求;- 分析各个工作岗位的工作特点和工作流程。
2. 设定标准工作任务:- 综合考虑工作岗位的工作内容和要求,确定标准工作任务; - 区分常见和特殊工作任务,分别制定标准工作任务。
3. 观察和记录时间数据:- 选择一定数量的样本进行时间观察和记录,统计得出样本的平均工作时间;- 根据样本数据进行推算,确定标准工作量。
ie标准工时计算
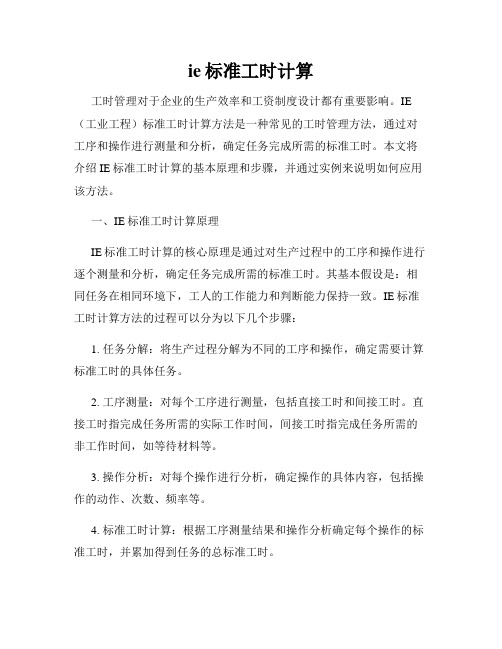
ie标准工时计算工时管理对于企业的生产效率和工资制度设计都有重要影响。
IE (工业工程)标准工时计算方法是一种常见的工时管理方法,通过对工序和操作进行测量和分析,确定任务完成所需的标准工时。
本文将介绍IE标准工时计算的基本原理和步骤,并通过实例来说明如何应用该方法。
一、IE标准工时计算原理IE标准工时计算的核心原理是通过对生产过程中的工序和操作进行逐个测量和分析,确定任务完成所需的标准工时。
其基本假设是:相同任务在相同环境下,工人的工作能力和判断能力保持一致。
IE标准工时计算方法的过程可以分为以下几个步骤:1. 任务分解:将生产过程分解为不同的工序和操作,确定需要计算标准工时的具体任务。
2. 工序测量:对每个工序进行测量,包括直接工时和间接工时。
直接工时指完成任务所需的实际工作时间,间接工时指完成任务所需的非工作时间,如等待材料等。
3. 操作分析:对每个操作进行分析,确定操作的具体内容,包括操作的动作、次数、频率等。
4. 标准工时计算:根据工序测量结果和操作分析确定每个操作的标准工时,并累加得到任务的总标准工时。
二、IE标准工时计算步骤下面以一家制造企业的生产线上的装配工序为例,介绍IE标准工时计算的具体步骤:1. 任务分解:将装配工序分解为多个具体操作,如零件装配、调试、清洁等。
2. 工序测量:对每个工序进行测量,记录实际完成该工序所需的工作时间。
例如,在零件装配工序中,测量实际装配一件零件所需时间为10分钟。
3. 操作分析:对每个操作进行分析,记录操作的具体内容和频率。
例如,在零件装配工序中,操作包括拆卸、安装、固定等,其中拆卸操作的频率为10次/小时,安装操作的频率为20次/小时。
4. 标准工时计算:根据工序测量结果和操作分析确定每个操作的标准工时。
例如,拆卸操作的标准工时为实际拆卸一次所需时间乘以频率,即10分钟/次×10次/小时=100分钟/小时。
三、IE标准工时计算实例假设某企业的装配工序共有5个具体操作,它们的实际工时和频率如下表所示:操作名称实际工时(分钟)频率(次/小时)零件装配 10 20调试 15 15清洁 5 30固定 8 25质检 12 10根据上述数据,可以计算每个操作的标准工时,然后累加得到任务的总标准工时。
ie标准工时
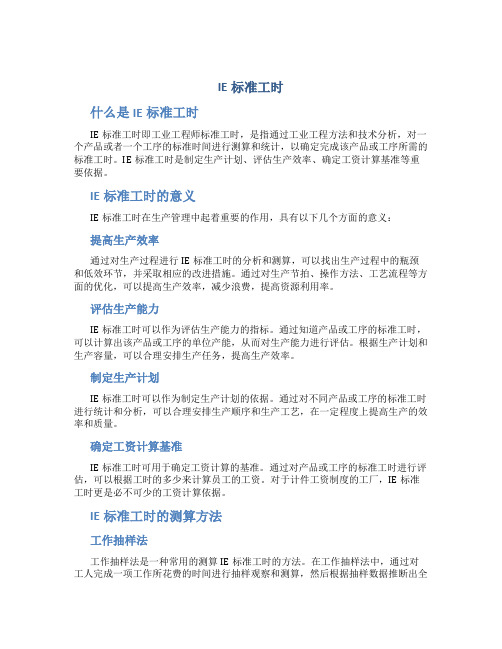
IE标准工时什么是IE标准工时IE标准工时即工业工程师标准工时,是指通过工业工程方法和技术分析,对一个产品或者一个工序的标准时间进行测算和统计,以确定完成该产品或工序所需的标准工时。
IE标准工时是制定生产计划、评估生产效率、确定工资计算基准等重要依据。
IE标准工时的意义IE标准工时在生产管理中起着重要的作用,具有以下几个方面的意义:提高生产效率通过对生产过程进行IE标准工时的分析和测算,可以找出生产过程中的瓶颈和低效环节,并采取相应的改进措施。
通过对生产节拍、操作方法、工艺流程等方面的优化,可以提高生产效率,减少浪费,提高资源利用率。
评估生产能力IE标准工时可以作为评估生产能力的指标。
通过知道产品或工序的标准工时,可以计算出该产品或工序的单位产能,从而对生产能力进行评估。
根据生产计划和生产容量,可以合理安排生产任务,提高生产效率。
制定生产计划IE标准工时可以作为制定生产计划的依据。
通过对不同产品或工序的标准工时进行统计和分析,可以合理安排生产顺序和生产工艺,在一定程度上提高生产的效率和质量。
确定工资计算基准IE标准工时可用于确定工资计算的基准。
通过对产品或工序的标准工时进行评估,可以根据工时的多少来计算员工的工资。
对于计件工资制度的工厂,IE标准工时更是必不可少的工资计算依据。
IE标准工时的测算方法工作抽样法工作抽样法是一种常用的测算IE标准工时的方法。
在工作抽样法中,通过对工人完成一项工作所花费的时间进行抽样观察和测算,然后根据抽样数据推断出全体工人完成该项工作所需的标准工时。
这种方法通常适用于每个工序都比较固定且重复性高的情况。
预定时间法预定时间法是另一种常用的测算IE标准工时的方法。
预定时间法通过将一个工序分解成为多个最小动作单位,并对每个动作单位的时间进行测算,然后根据动作单位的时间累加得出该工序的标准工时。
这种方法适用于工序比较繁杂且包含多个动作单位的情况。
标准数据法标准数据法则是以已确定的标准化数据标准和国内外行业标准作为IE标准工时的测算依据,从而快速准确地测算出工序的标准工时。
IE入门培训标准工时ppt课件
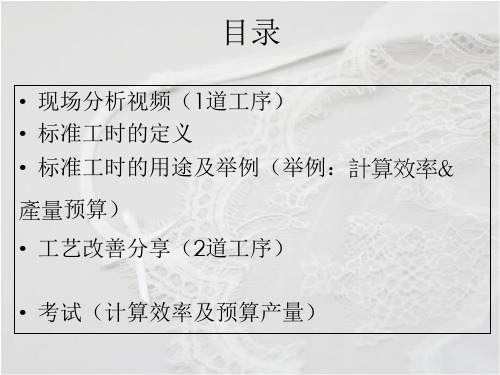
標准工時(SAM)的介紹
SAM的其中主要功用:
(A) 計算效率
産出工時=SAM/件 x 件數
效率 =
產出 x 100%
投入
工作時間
5
標准工時(SAM)的介紹
例子:
工人用9小時完成以下两款工序:
款式 A B
工序 埋杯底 冚脚
SAM/件 5.26 5.80
産量/件 36 48
投入時間:540分鐘 産出工時:(5.26 x 36) + (5.80 x 48) = 467.76
2
標准工時(SAM)的介紹
SAM的定義:
標准:
* 熟練操作員
* 在正常情況下
+
* 標准方法
* 可接受品質水平
寬放:
* 個人宽放 * 機械宽放
量度單位: 分鐘
S A M tandard llowed
inute
3
標准工時(SAM)的介紹
SAM的其中主要功用:
(1)計算效率 (2)產量預算 (3)計算工價 (4)生産線平衡 (5)排期 (6)量度産能
目录
• 现场分析视频(1道工序) • 标准工时的定义 • 标准工时的用途及举例(举例:計算效率& 產量预算) • 工艺改善分享(2道工序)
• 考试(计算效率及预算产量)
標准工時(SAM)的介紹
SAM(Standard Allowed Minutes) 的定義:
標準工時(SAM) 是一個 100%熟練工人, 於 良好的工作環境 下用 正常速度 去完成一個 特定工作(可接受品質水平)所需的時間。
效率 =
467.76xΒιβλιοθήκη 100% = 86.6%540
6
IE基础标准工时
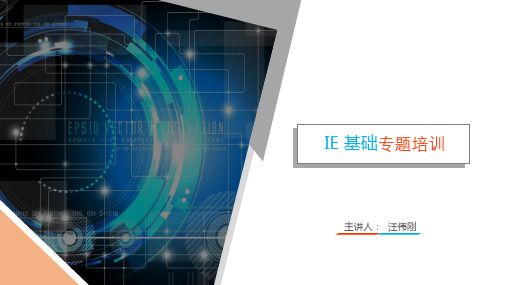
主讲人: 汪伟刚
目 录
Part 1 Part 2 Part 3 Part 4
标准作业 标准工时
OEE 抽样法
01
标准作业
标准作业是以人的动作为中心、以没有浪费的 作业顺序有效的进行生产的作业方法。
三要素
标准节 拍
作业顺 序
标准手持
标准作业
作业标准是对作业者的作业要求,强调的是作业的
1
BB101 K211/ 15右后C柱包边
460
5. 62
1
7
4% 5. 8448 86. 11% 100. 00% 531 15. 43% 6372
3
BB106 2SV右前中/ 左后中/ 后柱
60
48. 46
1
4
4% 50. 3984 86. 11% 100. 00% 62
3. 33%
744
4
BB106 2SV左前中/ 右后中/ 后柱
品质不良人工整修损失
◊ 机能的停止,为恢复机能 需要更换零件或修理,发 生的停止时间,一般在5 分钟以上
OEE架构
时间结构
OEE
时间损失
稼动损失
投入时间
SD
负荷时间 损 失
稼
稼动时间
动 损
失
速
净稼动时间
度 损
失
不
价值稼动时间
良 损
失
计划停机损失
故障损失 ❖换模(线)损失 换刀具损失 暖机损失 小停机空转损失 速度降低损失
为什么要标准作业
▪ 质量 ▪ 缺陷发生 ▪ 操作缺失
▪ 生产效率 ▪ 不同班次采用不同的工作方法 ▪ 作业操作时间波动
▪健康&安全 ▪机器设备使用不当
IE培训讲义标准工时课件
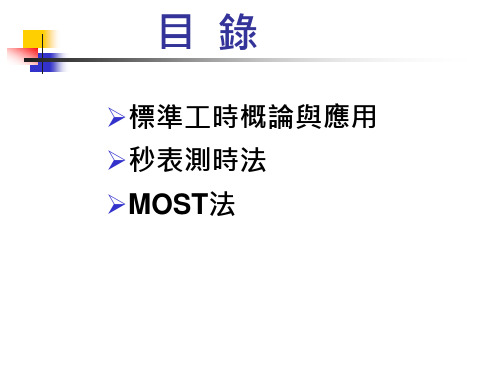
恢復係數
0%~5%
1
6%~10%
0.9
11%~15%
0.8
16%~20%
0.71
21%~25%
0.62
26%~30%
0.54
是整個周程中,其機械自動作業單元中人體可以休息以恢復疲勞的時間佔整個周程時間的比率,依此比率所訂出的恢復係數。
秒表測時法
產業別寬放率之參考
產業別
MOST法
產品的生產過程是各有效操作動作的總和,只要動作單元相同,在同一BSI時間等級下,其時間值也相同.將產品的操作動作按一般動作、控制動作、使用工具動作分成三大類,用特定的公式表示.將各類動作細分成手和手指的動作、身体動作、裝配動作、工具的使用等動作,并各用不同的字母表示.根据動作性質,依据《標准時間基本元素數据表》,檢索相應的動作序號,并換算成TMU值。左,右手同時操作時,選取動作時間最長者的序號.
代表公司
生產形態
生理寬放
疲勞寬放
管理寬放
精密工業
A
量產
2%~3%
0%~2%
4%~5%
量測儀器
B
量產
2%~3%
0%~2%
4%~5%
輕電機
C
量產
2%
5%
8%
輕電機
D
量產
4%
1%~10%
3%
重電機
E
量產
3%
2%~10%
4%~7%
汽車
F
量產
3%~4%
0%~8%
6%
汽車
G
量產
4%
1%~12%
5%
橡膠
I
量產
2%~5%
目 錄
- 1、下载文档前请自行甄别文档内容的完整性,平台不提供额外的编辑、内容补充、找答案等附加服务。
- 2、"仅部分预览"的文档,不可在线预览部分如存在完整性等问题,可反馈申请退款(可完整预览的文档不适用该条件!)。
- 3、如文档侵犯您的权益,请联系客服反馈,我们会尽快为您处理(人工客服工作时间:9:00-18:30)。
評比之定義
是一種判斷或評價,亦即將實際利用
碼錶觀測所得之單元操作時間值,將 其調整為正常或平均水平值之程度。
轉換為百分之百工作步調或稱為正常 作業員之水準。
簡易的自我訓練評比方法:
在4個6〞的方塊內,花費30秒,發完 52張撲克牌。
寬放之定義
作業員在工作時間內遇到不可避免之 延誤,而不得不暫停工作,或因工作 環境影響,使作業員感覺疲倦,必須
暫停工作,藉以稍作休息等因素,而
給予合理的調整。
寬放時間:獲得經過評比後之正常時 間再加上某種百分比之寬放。
寬放之分類
1.作業(重複性﹚:
主作業--車縫或使用工具對材料加工。 副作業--取拿、比齊、對準、切線。
2.作業寬放:製品整理、副件整備、換線、故障、
判斷、記錄、修改。
3.職場寬放:商談、等待、搬運、移動。 4.生理寬放:疲勞、如廁、飲水。 5.其他:私語、觀望、幫手(分配以外之工作)。
Ans: 10*60*60*8*0.6/1426 = 121
✓ 20000件,IE=0.8 由10人工作8小時,效率80%,幾個 工作天可完成?
Ans: 20000*0.8*1426 = 22,816,000 10*60*60*8*0.8 = 230,400 22,816,000 / 230,400 = 99
工業工程課之工作任務
工時/廠務(效率)/專案
公司報價之特定用法
工時(方法與時間分析)
IE=1之定義
車縫工時=1426秒 1426秒=標準款 標準款與標準工時之功用
1. 業務接單依據 2. 掌握人工成本 3. 掌握工廠產能與進度 4. 生產設備需求評估 5. 評估工廠生產效率與獎工發放 6. 現場工作指派 7. 工作改善之評估
THANKS
未來將運用在業務報價、財務成本計算、 效率計算、產出預估。
第二節 效率與產能
效率 IE與產能
效率=產出 / 投入
效率:指在有限的資源中,創造出的產值
有限的資源 = 投入
時間 金錢
產值 = 產出
成衣件數 (標準件數=實際件數*IE值)
IE與產能之關係
IE值 1件標準件
1426秒
產能 20.2標準件 (1人8HR) (效率100%)
精品
02-IE与标准工时
第一節 標準款
標準款 學習率
IE之定義(Industry Engineer)
產業界及學界之一般用法
工程經濟.組織與管理. 心理學.行銷學.預測方法. 工廠佈置與物料搬運. 生產計劃與管制.物料管理.方法研究.工作衡量. 學習曲線應用.工業安全. 品質管理.價值分析.作業研究.
(PT法﹚:如MTM 5.標準資料法:如GSD
標準時間之定義
係指一個合格的作業員,在正常的主 客觀條件下,依照作業標準,完成一
個工段所需的時間。
操作之實際完成時間<標準時間→節省 操作之實際完成時間>標準時間→浪費
標準時間結構圖
觀測時間
評比 因素
正常化時間
標準時間
寬放時間
正常化時間 ﹦觀測時間 ×評比 標準時間 ﹦正常化時間 ×(1+寬放百分比)
標準款之作工說明
學習率
人的作業在執行相同的工作時,由於產品製程 的重複性,於是透過其學習的過程,往往隨著 產量的增加,操作愈來愈熟悉。
操作某一作業所需要的時間,將隨著數量的增 加而減少。
換款生產之效率差異比較
100
80
60
效率
平均效率=95%
1=80%
裁燙包IE
目前依大陸產區之裁燙包工作時間定出, 裁、燙、包之IE值。
第三節 標準工時之應用
標準工時之定義 標準工時之來源 馬錶測時
時間研究之管理功能
1.記錄作業員的工作績效 2.計算產品的成本 3.決定工廠之生產規模 4.平衡各部門之工作進度 5.預估未來之工作 6.建立獎工制度 7.改進操作方法
標準工時之設定方法
1.歷史資料法 2.直接測時法(碼錶測時法) 3.工作抽查法 4.預定動作時間標準法
Ans: 60*60*10/1426 = 25.25
✓ 每組20人工作8小時,產出標準件數?
Ans: 20*60*60*8/1426 = 403.9
✓ A款之IE=0. 4,10人工作8小時,產出之實際件數?
Ans: 10*60*60*8/1426/0.4 = 505
✓ 10人工作8小時,效率60%,產出之標準件數?
Q&A •1人工作10小時,產出標準件數? •每組20人工作8小時,產出標準件數? •A款之IE=0. 4,10人工作8小時,產出之實際件數? •10人工作8小時,效率60%,產出之標準件數? •20000件,IE=0.8,由10人工作8小時,效率80%,幾個工作天可完成?
解答
✓ 1人工作10小時,產出標準件數?