物料及供应商风险评估程序
主要物料供应商风险评估制度

文件名称文件编号主要物料供应商风险管理制度批准人日期版本号审核人日期2018-00 日期生效日期起草人日期颁发部门质管部分发部门采购部、生产部、质管部一、目的:通过评估主要物料供应商,识别供应商质量风险,并进行分级,然后根据供应商质量风险等级大小,分级管理供应商,避免或降低高风险供应商对产品质量的影响,控制质量风险,保证产品质量。
二、适用范围:适用于公司主要物料合格供应商的风险评估及管理。
三、职责:质管部QA:组织风险评估小组对风险进行评估确认,参与风险评估,协调风险管理全过程,同时负责风险控制措施执行情况的跟踪与检查。
编制并提交风险评估报告。
质管部QC:参与风险识别、风险评估、风险控制。
生产部:参与风险识别、风险评估、风险控制。
生产办公室:参与风险识别、风险评估、风险控制。
采购部:参与风险识别、风险评估、风险控制。
生物副总工:参与风险识别、风险评估、风险控制,审核风险评估报告。
制造事业部总经理:参与风险识别、风险评估、风险控制,审核风险评估报告。
质管部经理:负责统筹组织协调风险管理活动,审核批准风险评估报告。
四、正文:1.定义1.1供应商风险评估是指根据物料性质、物料用量以及将物料对于产品质量影响程度综合考虑物料风险,对物料进行分级,根据风险评估的结果确认不同级别物料的供应商潜在的风险,从而制定相应的控制措施以最大限度地降低风险。
供应商质量风险等级分为A/B/C/D四等。
A-风险很小、B-风险小、C-风险中、D-风险大1.2供应商风险管理依据对物料供应商的风险识别和风险评估,确定不同级别供应商的管理体系,同时对经确认及采取管理措施后的供应商剩余风险再评价,证实对供应商的风险已进行了有效管理。
1.3风险评估要素:产品、工艺、审计历史、重大偏差、召回、CAPA、历史绩效得分等。
1.4企业风险管理重点:管理体系、质量管理体系、变更控制、供应商管理、工艺控制、实验室、纠正与预防性措施、对不合格品的处理,返工或重新加工。
物料管理中的供应商风险评估与管理

物料管理中的供应商风险评估与管理引言在物料管理的过程中,供应商的选择和管理是非常关键的环节。
一个好的供应商能够稳定地提供高质量的物料,并且能够及时配送,满足企业生产和运营的需求。
然而,供应商也存在一定的风险,比如质量问题、交货延迟、安全隐患等。
因此,对供应商进行风险评估和管理是必要的。
本文将介绍物料管理中的供应商风险评估与管理的重要性,以及常用的评估方法和管理策略。
供应商风险评估的重要性供应商风险评估是为了确定供应商在物料管理中可能面临的风险和隐患,并采取相应的措施进行管理和控制。
一个完善的供应商风险评估体系可以帮助企业识别高风险和低风险的供应商,避免和降低潜在的风险,保障物料的质量和供应的稳定性。
以下是供应商风险评估的重要性:1.保障物料质量:通过对供应商的质量管理体系进行评估,可以避免采购到质量不合格的物料,降低因质量问题带来的生产损失和返工成本。
2.提升供应的稳定性:评估供应商的生产能力和供应能力,可以减少交货延迟的风险,确保物料的及时供应,避免生产线的中断和产品的积压。
3.避免合规风险:评估供应商的环境、安全和社会责任管理能力,可以预防潜在的合规问题,避免因供应商的违法违规行为给企业造成的法律责任和声誉损失。
供应商风险评估的方法1. 供应商信用评估采用供应商信用评估的方法,可以了解供应商的财务状况、信用记录和商业信誉等方面的情况。
常用的评估指标包括供应商的信用报告、供应商的经营年限、供应商的资产负债表等。
通过供应商信用评估,可以初步判断供应商的可靠性和稳定性。
2. 供应商质量评估供应商的质量评估是评估供应商在生产过程中是否符合相关质量标准和要求的过程。
常用的评估方法包括对供应商的生产工艺和检验流程进行审核,抽样检验供应商提供的样品,以及对供应商的质量管理体系进行评估。
通过供应商质量评估,可以判断供应商的质量水平和管理能力。
3. 供应商供应能力评估供应商的供应能力评估是评估供应商在供应物料方面的能力和稳定性的过程。
物料供应商风险评估报告

物料供应商风险评估报告 This model paper was revised by the Standardization Office on December 10, 2020【最新资料,WORD文档,可编辑修改】目录1、概述2、目的3、风险评估、风险识别、风险评价、风险评价4、风险等级确认5、风险控制6、结论1、概述:、供应商评估是保证物料采购的关键过程,通过对物料供应商的资质文件审核、供应商GMP法规的执行情况、质量风险管理体系、人员、设施设备、投诉、调查、变更管理、与企业沟通、环保健康安全、运输管理等一系列过程控制;是保证物料进厂合格的管理过程,是有效降低物料采购风险的控制方法。
、根据物料对产品质量影响风险程度,结合公司产品确定物料的安全级别,其A级物料如下:对直接影响药品质量的主要原辅料,经风险分析后定为A级。
原料有氯化钠、葡萄糖、甲硝唑、XXXX、XXXX、氟罗沙星、XXXX、XXX、中药材及中药饮片。
辅料有盐酸、氢氧化钠、乳酸、枸橼酸、依地酸钙钠、盐酸半胱氨酸、焦亚硫酸钠、磷酸二氢钠、磷酸氢二钠、空心胶囊、硬脂酸镁、药用糊精、药用淀粉、蔗糖、滑石粉、微晶纤维素、包衣粉。
2、目的:建立A级物料供应商存在和可能发生的风险进行评估,确定风险等级;并采取措施将风险控制在可接受范围内。
3、物料供应商风险评估:、风险识别:A级物料是影响产品质量的关键物料,其物料供应商存在的风险程度直接影响物料产品质量风险程度。
是物料供应商风险评估的重点。
根据对物料产品的质量影响情况和其他风险影响分析物料供应供应商可能存在的风险点如下:、政策法规、产品质量、对物料供应供应商风险点进行分析,以上风险点存在风险因素:、政策法规影响的风险因素、资质批准文件、产品质量标准、经营授权书、产品质量影响的风险因素、人员与机构、厂房和设施、设备、物料管理、生产管理、质量控制管理、产品包装与运输、质量管理体系、风险分析:、风险等级判定标准:用定量分级RPN风险优先数量等级判定(危害 :存在风险项目较多,并且不能有效控制风险,从而影响其物料质量,最终影响到我公司产品的质量。
物料供应商风险评估报告

【最新资料,WORD文档,可编辑修改】目录1、概述2、目的3、风险评估3.1、风险识别3.2、风险评价3.3、风险评价4、风险等级确认5、风险控制6、结论1、概述:1.1、供应商评估是保证物料采购的关键过程,通过对物料供应商的资质文件审核、供应商GMP法规的执行情况、质量风险管理体系、人员、设施设备、投诉、调查、变更管理、与企业沟通、环保健康安全、运输管理等一系列过程控制;是保证物料进厂合格的管理过程,是有效降低物料采购风险的控制方法。
1.2、根据物料对产品质量影响风险程度,结合公司产品确定物料的安全级别,其A级物料如下:对直接影响药品质量的主要原辅料,经风险分析后定为A级。
原料有氯化钠、葡萄糖、甲硝唑、XXXX、XXXX、氟罗沙星、XXXX、XXX、中药材及中药饮片。
辅料有盐酸、氢氧化钠、乳酸、枸橼酸、依地酸钙钠、盐酸半胱氨酸、焦亚硫酸钠、磷酸二氢钠、磷酸氢二钠、空心胶囊、硬脂酸镁、药用糊精、药用淀粉、蔗糖、滑石粉、微晶纤维素、包衣粉。
2、目的:建立A级物料供应商存在和可能发生的风险进行评估,确定风险等级;并采取措施将风险控制在可接受范围内。
3、物料供应商风险评估:3.1、风险识别:A级物料是影响产品质量的关键物料,其物料供应商存在的风险程度直接影响物料产品质量风险程度。
是物料供应商风险评估的重点。
根据对物料产品的质量影响情况和其他风险影响分析物料供应供应商可能存在的风险点如下:3.1.1、政策法规3.1.2、产品质量3.2、对物料供应供应商风险点进行分析,以上风险点存在风险因素:3.2.1、政策法规影响的风险因素3.2.1.1、资质批准文件3.2.1.2、产品质量标准3.2.1.3、经营授权书3.2.2、产品质量影响的风险因素3.2.2.1、人员与机构3.2.2.2、厂房和设施、设备3.2.2.3、物料管理3.2.2.4、生产管理3.2.2.5、质量控制管理3.2.2.6、产品包装与运输3.2.2.7、质量管理体系3.3、风险分析:3.3.1、风险等级判定标准:用定量分级RPN风险优先数量等级判定(危害 :存在风险项目较多,并且不能有效控制风险,从而影响其物料质量,最终影响到我公司产品的质量。
gmp物料供应商质量体系评估程序 (1)
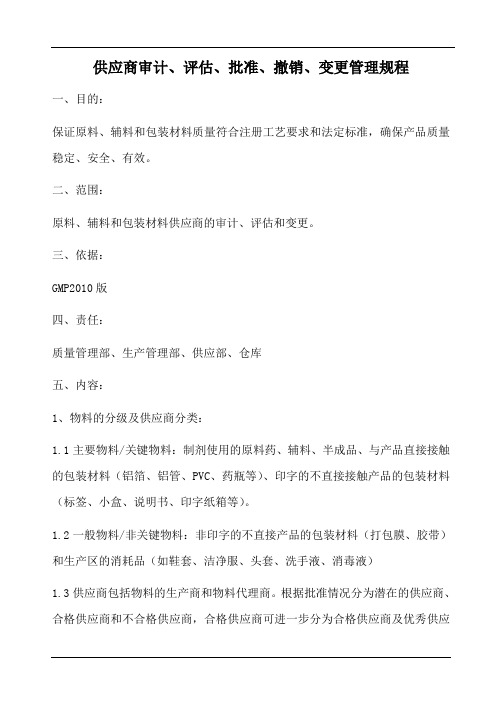
供应商审计、评估、批准、撤销、变更管理规程一、目的:保证原料、辅料和包装材料质量符合注册工艺要求和法定标准,确保产品质量稳定、安全、有效。
二、范围:原料、辅料和包装材料供应商的审计、评估和变更。
三、依据:GMP2010版四、责任:质量管理部、生产管理部、供应部、仓库五、内容:1、物料的分级及供应商分类:1.1主要物料/关键物料:制剂使用的原料药、辅料、半成品、与产品直接接触的包装材料(铝箔、铝管、PVC、药瓶等)、印字的不直接接触产品的包装材料(标签、小盒、说明书、印字纸箱等)。
1.2一般物料/非关键物料:非印字的不直接产品的包装材料(打包膜、胶带)和生产区的消耗品(如鞋套、洁净服、头套、洗手液、消毒液)1.3供应商包括物料的生产商和物料代理商。
根据批准情况分为潜在的供应商、合格供应商和不合格供应商,合格供应商可进一步分为合格供应商及优秀供应商。
2、评估部门的职责及选择原则2.1质量管理部门应当对关键物料物料的供应商进行质量审计、评估,会同生产部门、采购部门对主要物料供应商(尤其是生产商)的质量体系进行现场质量审计,并对质量评估不符合要求的供应商行使否决权。
企业法定代表人、企业负责人及其他部门的人员不得干扰或妨碍质量管理部门对物料供应商独立作出质量评估。
主要物料的确定应当综合考虑企业所生产的药品质量风险、物料用量以及物料对药品质量的影响程度等因素。
2.2质量管理部门应当指定专人负责物料供应商质量评估和现场质量审计,成立以质量管理负责人为组长的审计小组,组员由质量、生产、采购部门人员组成,负责对物料供应商质量评估和现场质量审计,向物料部门分发经批准的合格供应商名单。
审计小组人员应当具有相关的法规和专业知识,具有足够的质量评估和现场质量审计的实践经验。
2.3供应商的选择原则:生产和质量管理体系稳定,具备合法资质,产品质量稳定,供货能力较强,药品生产所用的原辅料、与药品直接接触的包装材料应当符合相应的质量标准。
物料零件RS风险等级评估程序(含表格)

物料/零件RS风险等级评估程序(QC080000-2017)1.0 目的为识别本公司所有原物料﹑零部件的环境管理物质风险等级﹐以利于生产过程中对环境管理物质的控制﹐特制订本办法作为物料/零件风险等级评估的指引。
2.0 范围2.1 本作业办法适用于FD/FG/FQ厂区的生产用料﹑外包半成品/成品﹑外买外卖产品的风险等级评估及管理。
2.2 本作业办法不适用于模具承认时的风险评估。
3.0 定义3.1 材质风险﹕指原物料﹑零部件﹑组件所构成的材质本身的风险﹐一经评定后其一般不会再发生变化。
3.2 供货商风险﹕指提供物料的供货商的环境管理物质体系的综合水平﹔一般通过对供货商RSC体系的评鉴结果﹑供货商的品牌知名度或其日常交货质量状况来进行适时评定。
3.3 物料风险﹕指材质风险与供货商风险的总体考虑﹔一般通过将这两种风险评分的乘积作为其最终评定结果。
3.4 客供料﹕指由客户方直接交付给本公司投入生产使用的物料(本公司与该物料的制造商/代理商不发生任何交易﹔亦非客户指定供货商提供的物料)。
4.0 职责4.1 零件承认工程师﹕负责材质风险的评估。
4.2 品保工程师﹕4.2.1 负责供货商风险的评估﹔4.2.2 结合材质风险完成物料风险等级识别﹔4.2.3 将所有评估结果登录于风险评估表上。
4.3 IQC: 依据风险等级结果来执行IQC进料检验抽检。
5.0 作业程序5.1 物料风险评估的时机5.1.1 新零件的物料风险评估必须在新零件承认时由相关人员进行评定完成﹔评定结果记录于零件样品承认书﹔同时由品保单位将评估结果登录于风险评估表。
相关作业流程请参考“零件承认作业办法”。
5.1.2 已被承认零件的物料风险于进料前由相关人员完成评定﹔评定结果记录于风险评估表。
5.2 物料/零件风险的识别5.2.1 为充分及有效的识别材质风险﹐针对组成各物料/零件的材质中环境管理物质的应用历史进行识别如下表﹕环境管理物质应用历史塑料添加剂﹑稳定剂﹑焊锡材料﹑油墨中的添加剂﹑玻璃及铅陶瓷中的添加剂镉塑料添加剂﹑着色剂﹑稳定剂﹑油墨中的添加剂某些塑料的添加剂﹑凝固剂﹑荧光灯泡﹑开关及继电器中的汞某些特殊元器件六价铬电镀﹑金属表面防锈处理﹑颜料PBB/PBDE 塑料中的阻燃剂Phthalate 塑料增塑剂(特别是柔性塑料材料)﹑油漆﹑颜料﹑粘着剂卤素阻燃剂塑料中的阻燃剂5.2.2 若供货商本身或其所交物料/产品制程属于下表特定情况之一﹐则该物料/零件应直接判定为高风险等级(不需执行5.2.3作业)。
HSF风险评估程序(含记录)
HSF风险评估程序(QC080000-2017)1.0目的为识别本公司所有原物料/零部件、供应商和生产过程中所产生的环境管理物质风险等级,以利于生产过程中对环境管理物质的控制。
2.0适用范围适用于本公司生产用料、过程与HSF产品相关之的风险评估。
3.0定义3.1材料风险:指原物料﹑零部件﹑组件所构成材料的本身的风险﹐一经评定后其一般不会再发生变化。
3.2供应商风险:指提供物料的供应商的环境管理物质体系的综合水准,一般通过对供应商RSC体系的评鉴结果,供应商的品牌、规模、知名度或其日常交货品质状况来进行适时评定。
3.3 物料风险:指材料风险、供应商风险的总体考量:一般通过将这两种风险评分的乘积作为其最终评定结果。
3.4生产过程风险:指产品实现过程中所有生产设备、工/夹具、测量仪器、工作环境、操作人员等在正常、异常、紧急的状况下所有可能导致交叉污染产生的风险状况。
4.0组织权责4.1零件承认工程师:负责材料风险的评估。
4.2品保/采购工程师:4.2.1负责供应商风险的评估;4.2.2结合材料风险完成HSF风险等级评估;4.2.3将所有评估结果登录于风险评估表上;4.3IE工艺工程师:负责过程风险的评估。
4.4 IQC:依据风险等级结果来执行进料检验抽检。
5.0作业程序5.1HSF风险评估时机a>对新零件材料的风险评估在设计初期或有任何设计或物料更改的阶段进行;已被承认零件的HSF风险于进料前由IQC依《进料检验规范》进行评估。
b>对供应商的风险评估为一年一次,或有新供应商加入时进行;c>生产过程的风险评估在生产前或有任何工艺更改时依《首件确认规范》进行。
5.2物料风险的识别5.2.1若供货商本身或其所交物料﹑产品制程属于下表特定情况之一﹐则该物料应直接判定为高风险等级。
特定供应商 1.一年内曾经发生过超标的供应商特定物料 1.线路板(PCB、PCBA)2.外购线材(CABLE)3.外购射出成型塑料件特定制程 1.表面处理(电镀、喷涂、移印、丝印)制程2.电子焊接(插件、SMT焊接)制程3.注塑成型制程5.2.2若无法通过5.2.1的方法来直接判定出物料的风险等级,则零件承认工程师及品保工程师必须分别按照下表的评定准则来识别出零件材料风险及供应商风险﹔评估时必须依照以下要求作业﹐并按要求记录于风险评估表上。
HS物料风险等级评估控制程序
HS物料风险等级评估控制程序引言为保证公司生产过程中的安全性和有序性,在生产过程中需要对物料进行风险等级评估和控制。
本文档介绍了HS物料风险等级评估控制程序的实施方法和操作流程。
相关定义•HS物料:指根据国际贸易惯例,对所涉及的商品予以编号的一种国际通行方法,具有唯一性和权威性•风险等级:对物料所带来风险的程度进行分类划分,通常分为高、中、低三种等级•评估:对物料的安全性、法律合规性等方面进行综合评估•控制:通过采取适当措施,对物料的风险进行控制和降低程序流程第一步:物料资料收集首先,需要从相关部门或供应商处收集HS物料的资料,包括物料名称、编号、安全数据表、生产厂家和供应商等。
第二步:物料分类根据物料资料,对物料进行分类,判断是否是危险品、易燃品等高风险物料。
对于未分类的物料,需进行进一步鉴定和确认。
第三步:风险评估根据物料分类,对每种物料进行风险评估。
评估方法包括查阅相关规定、安全数据表、风险评估软件等工具,综合考虑物料的安全性、政策法规合规性、生产厂家信誉度等方面。
评估结果按风险等级分为高、中、低三种等级,并做好相应的风险等级标识和记录。
第四步:控制措施根据物料的风险等级,采取相应的控制措施,确保物料在生产过程中的安全。
高风险等级物料,应尽可能采取替代品或减少使用量等措施;中风险等级物料,应采取隔离存储、标识管理等措施;低风险等级物料,应定期检查控制措施是否有效。
第五步:监督检查对控制措施的执行情况进行监督和检查。
针对不合规的情况,及时采取措施进行整改,确保风险控制处于有效状态。
结论HS物料风险等级评估控制程序是保证公司生产过程中的安全性和有序性的关键措施。
通过本文档的介绍和实施,可以提高公司对物料风险的识别和控制能力,更好地保障公司生产过程的安全性和稳定性。
物料供应商风险评估
物料供应商风险评估在现代供应链管理中,物料供应商的选择和评估是企业成功运营的关键因素之一。
由于供应链的复杂性和不确定性,企业需要对供应链中的各种风险进行评估,以确保物料供应的稳定性和可靠性。
本文将重点讨论物料供应商风险评估的重要性,并提出一种有效的评估方法。
一、物料供应商风险的背景和挑战物料供应商风险是指供应商出现的各种可能带来负面影响的情况,包括质量问题、延误交付、供应中断、价格波动等。
这些风险可能导致产品质量下降,交货延迟,甚至生产线停工,对企业造成严重影响。
同时,全球化和供应链的广泛延伸增加了供应商风险的复杂性,如国际贸易政策的变化、供应链中断、自然灾害等。
因此,对物料供应商的风险进行评估和管理对企业至关重要。
二、物料供应商风险评估的重要性1. 确保供应链的稳定性:通过对供应商进行风险评估,可以及时发现和解决潜在的问题,以确保物料供应的稳定性。
这有助于降低企业面临的风险和不确定性,提高供应链的整体效能。
2. 提高产品质量和安全性:合格的供应商能够提供高质量和安全的物料,从而确保产品在市场上的竞争力和信誉。
物料供应商的风险评估可以帮助企业避免与低质量或不合规的供应商合作,提高产品的质量和安全性。
3. 降低成本和提高效率:通过对供应商进行风险评估,企业可以避免与不可靠或不稳定的供应商合作,减少物料短缺和生产线停运的风险,降低库存水平,并提高供应链的效率。
三、物料供应商风险评估的方法和指标1. 供应商审核和调查:企业可以通过与供应商进行面谈、访厂和调查等方式,了解供应商的经营规模、资质、生产能力、质量管理体系等信息,以评估其供应风险。
2. 财务分析:通过分析供应商的财务状况、资产负债表、现金流量表等财务指标,了解供应商的偿债能力、盈利能力和成长性,对供应商的财务风险进行评估。
3. 历史记录和口碑:通过查阅供应商的历史记录、业绩评价和客户反馈等信息,评估其供应可靠性、售后服务和整体声誉。
4. 风险评估指标:企业可以建立一套供应商风险评估指标体系,包括供应能力、质量控制、交货可靠性、供应链灵活性等指标,根据这些指标对供应商进行综合评估和排名。
物料管理与供应商风险评估计划
物料管理与供应商风险评估计划1. 引言物料管理是每个企业都要面临的重要任务之一。
它涉及到从供应商采购物料、存储物料、分配物料到最终使用物料的整个过程。
供应商风险评估计划则是评估和管理与供应商相关的各种风险,以确保企业的物料管理工作能顺利进行。
本文将介绍物料管理与供应商风险评估计划的重要性、目标和实施方法。
2. 物料管理的重要性物料管理对企业的运营和效益至关重要。
良好的物料管理可以帮助企业实现以下目标:•确保物料供应的及时性和稳定性,以满足生产计划和客户需求;•最小化物料库存水平,减少库存占用的资金投入;•降低采购和物料管理的成本;•提高供应链的可靠性和效率;•提升客户满意度。
3. 供应商风险评估计划的目标供应商风险评估计划的目标是评估和管理与供应商相关的各种风险,包括但不限于以下方面:3.1 供应商可靠性风险评估供应商的可靠性,包括供应商的信用状况、交货能力、质量管理体系等,以减少供应链中断的风险。
3.2 供应商合规风险评估供应商是否符合相关法规和标准,以降低因供应商违法违规而导致的风险,避免对企业形象和责任造成影响。
3.3 供应商质量风险评估供应商的质量管理体系、产品质量和供应链质量控制流程,以保证物料质量符合企业的要求和客户的期望。
3.4 供应商地理风险评估供应商所在地的政治环境、法律法规、自然灾害风险等因素,以降低由于供应商地理风险而导致的供应链中断和物料供应不稳定的风险。
4. 实施供应商风险评估计划的方法为了实施供应商风险评估计划,企业可以采取以下方法:4.1 收集供应商信息收集供应商的基本信息,包括企业、规模、信用状况、产品质量等方面的信息。
可以通过与供应商的沟通、企业信息查询等方式获取。
4.2 进行供应商评估基于收集到的供应商信息,对供应商进行评估。
可以采用评分法、层次分析法等方法,对供应商的可靠性、合规性、质量管理和地理风险等方面进行评估和打分。
4.3 制定风险管理措施根据评估结果,制定相应的供应商风险管理措施,包括但不限于建立备选供应商、制定合作协议、监督供应商的质量管理和合规情况等。
- 1、下载文档前请自行甄别文档内容的完整性,平台不提供额外的编辑、内容补充、找答案等附加服务。
- 2、"仅部分预览"的文档,不可在线预览部分如存在完整性等问题,可反馈申请退款(可完整预览的文档不适用该条件!)。
- 3、如文档侵犯您的权益,请联系客服反馈,我们会尽快为您处理(人工客服工作时间:9:00-18:30)。
有限公司
物料及供应商风险评估程 序
版次 A0 修订章节 修订内容/原因
文件编号: 制订单位: -QP-12 品管部 文件版本: 制订日期: A0 1
修订
审核
批准
修订日期
诚信
务实
团结
奉献
页码
第 1 页 共 3 页
有限公司
物料及供应商风险评估程 序
文件编号: 制订单位: -QP-12 品管部 文件版本: 制订日期: A0 1
1.目的: 明确公司物料及供应商风险,确保公司对供应商及其提供的物料进行分级管理。
2.适用范围: 本公司所有 HSF 物料及供应商均适用之。
3.权责权限: 3.1 品管部:负责对 HSF 产品中有关危害物质含量的验证,负责对危害物质允许标准的修订和 更新。
3.2 业务部:负责获取最新的国际上国家法律法规和客户有关危害物质允许标准的最新信息。
3.3 采购部:负责与供应厂商沟通公司内有关危害物质政策。
确保供应厂商所提供的原材料、 辅料、包材等符合公司相关的 HSF 产品中危害物质含量的标准。
4.内容: 4.1 材料因子评估: 根据有害物质调查表分析,针对原料、辅料及包材中有害物质含量的多少,测试数据的统 计数据的分析,公司把所有原料、辅料及包材进行评价后评定为以下三个级别: 风险级别 高风险 材料类别 包装材料 胶料类 化工类 塑胶配件 中风险 五金配件 外购件 辅料类 低风险 / 材料名称 包装袋(PVC、PE)、包装箱、工字 针、纸盒等 PS、尼龙等 油漆 子母扣、塑胶夹等 铁夹等 客户提供的混包配件等 热熔胶类 暂无 备注
4.2 供应商风险因子评估: 4.2.1 对提供 HSF 供应商进行风险评估,风险评估指标包括以下方面: 1) 公司规模; 2) 公司注册资本; 3) 公司产能水平; 4) 供应商有害物质管控体系情况; 5) 过去一年交货品质及有害物质管控情况。
诚信
务实
团结
奉献
页码
第 2 页 共 3 页
有限公司
物料及供应商风险评估程 序
文件编号: 制订单位: -QP-12 品管部 文件版本: 制订日期: A0 1
采购部与品质部对所有合格供应商进行风险评估,填写在《供应商风险评估表》,供应 商评估为高、中、低风险三个等级,评分为 85 分以上的为低风险,65~85 分为中风险,65 分 以下为高风险。
4.3 材料风险综合评估:
材料风险因子 供应商风险因子 高 中 低
高 高 高 高
中 高 高 中
低 高 中 低
4.4 危害物质含量标准的更新:业务部或品质部获取最新的国际上、国家法律法规或客户有关危 害含量标准,呈报管理者代表后,对公司内所执行的标准进行更新,同时将相关资料传达给各 相关部门。
4.5 物料测试要求: 1.物料风险测试频率一般为 2 年测试一次; 2.高风险物料 1 年测试一次; 3.提交物料的第三方检测报告(检测机构主要为 SGS、BV 等); 4.必须与公司或各分工厂签订《不使用有害物质保证书》。
5.参考文件: 5.1《危害管理物质限用标准》 6.表格: 6.1《供应商风险评估表》
诚信
务实
团结
奉献
页码
第 3 页 共 3 页
。