VAVE简介推动做法及案例-070926剖析
内部vave机制-概述说明以及解释

内部vave机制-概述说明以及解释1.引言1.1 概述内部vave机制是一种在企业内部广泛应用的管理方法。
它通过引入市场化机制,使企业内部各个部门之间形成明确的产品供给与需求关系,实现资源的优化配置和效率的提高。
内部vave机制的基本原理是建立一个内部市场,通过内部定价和交易机制来激励和约束各个部门,使其在综合利益最大化的前提下,主动调整供给和需求,从而实现企业整体的优化。
内部vave机制的应用范围广泛,涵盖了企业内部的各个环节和部门。
无论是生产、研发、销售还是行政和人力资源等,都可以通过内部vave 机制来实现资源的合理配置和协同工作。
通过引入内部市场机制,各个部门可以清晰地了解自己产品或服务的价值,根据市场需求和供应情况来调整自身的产能和资源配置。
这不仅可以提高企业的整体效率,还能促进创新和提升员工积极性。
内部vave机制的优势是显而易见的。
首先,它可以激发企业内部的活力和创造力。
通过内部市场的机制,各个部门之间形成供需关系,推动产品和服务的创新和改进。
其次,内部vave机制可以有效解决资源利用不均衡的问题。
通过内部定价和交易机制,各个部门可以清晰了解资源的价值,并在资源供需的基础上进行交易,从而实现资源的最优配置。
此外,内部vave机制还可以促进信息的流动和共享,打破了各个部门之间的壁垒,提升了企业整体的协同效率。
尽管内部vave机制在实践中也存在一些挑战和问题,例如如何建立有效的定价机制、如何确保信息的准确与透明等,但随着管理理念的不断发展和技术的迭代进步,这些问题将逐渐得到解决。
可以预见,内部vave 机制将在未来的发展中发挥越来越重要的作用,为企业提供更高效的管理手段和更强大的竞争力。
在新的经济形势下,企业无法再依靠传统的管理模式来应对日益激烈的竞争,而是需要更加开放、灵活和创新的内部vave 机制来应对挑战,实现可持续发展。
文章结构:本文将按照以下结构进行讨论和阐述内部vave机制:1. 引言:1.1 概述:介绍内部vave机制的基本背景和概念,引出对该机制的研究和分析的意义和重要性。
vave价值工程详解

vave与生产计划
生产计划
VAVE方法在生产计划中的应用,能 够更好地协调和平衡生产能力、交货 期和库存等要素,实现更优的生产计 划。
资源优化
VAVE方法可以优化资源利用,降低生 产成本和提高生产效率。例如,通过 对生产流程的优化,可以减少生产过 程中的浪费,提高资源利用效率。
生产灵活性
VAVE方法可以提高生产灵活性,更好 地应对市场变化和客户需求。例如, 通过采用模块化设计和生产,可以快 速调整和转换生产模式,满足不同客 户的需求。
vave与生产控制
生产控制
VAVE方法在生产控制中的应用,可以更好地协调和平衡生产进度和质量等要素,实现更 优的生产控制。
质量控制
VAVE方法可以优化质量控制,提高产品质量和客户满意度。例如,通过采用先进的质量 检测技术和设备,可以实现产品质量的有效控制和持续改进。
生产协调
VAVE方法可以加强生产协调,提高生产效率和生产管理水平。例如,通过采用先进的生 产管理系统和技术,可以实现各生产部门之间的有效协调和沟通,提高生产效率和生产管 理水平。
通过对产品或系统进行分析,找 到能够提高性能的关键因素,实 现产品或系统的优化设计。
增强可靠性
通过研究产品或系统的可靠性, 采取有效的措施提高产品或系统 的可靠性,降低维修和更换成本 。
价值分析的原理
以功能分析为核心
通过对产品或系统进行功能分析,了解产品或系统所能实现的功能及其重要性。
生命周期成本分析
对产品或系统进行功能分 析,了解各功能的重要性 。
制定替代方案
根据功能分析的结果,制 定替代方案,并对各方案 进行比较和分析。
进行成本分析 和比较
对各替代方案进行成本分 析和比较,找出最优方案 。
vave价值工程在汽车行业中的运用

02
对收集到的汽车产品相关数据和信息进行分析,以了解产品的性能、质量、成 本、可靠性等方面的状况。
03
对收集到的汽车制造过程中的相关数据和信息进行分析,以了解生产效率、原 材料消耗、制造成本等方面的状况,并找出可能存在的问题和改进点。
制定设计方案
根据市场和客户需求,以及产品性能、质量 、成本、可靠性等方面的状况,制定出可行 的设计方案。
环境友好化
未来汽车将更加注重环保和节能, 采用VAVE价值工程可以优化汽车 设计和制造过程,降低能源消耗和 排放,提高汽车的燃油效率和减少 环境污染。
随着智能化技术的不断发展, VAVE价值工程可以应用于智能网 联汽车中,通过智能化技术提高 汽车的驾驶体验、安全性能和舒 适性,同时也可以实现更加精细 化的生产和管理。
针对制造过程中存在的问题和改进点,制定 相应的设计方案。
进行方案评估和优化
对制定出的设计方案进行评估,以 了解方案的可行性、优缺点等。
VS
对设计方案进行优化,以提高产品 的性能、质量、成本、可靠性等方 面的指标,并降低制造过程中的成 本和风险。
05
vave在汽车行业中的案例分析
案例一:基于vave的汽车底盘减重设计
价值工程的发展历程
1 2
起源
20世纪40年代初,美国通用电气公司为了满足 战争时期物资紧缺的问题而发明的一种以功能 为导向的方法。
发展
从最初的军事领域扩展到民用领域,从美国走 向全球。
3
应用
在各种不同的行业和领域中得到应用和推广, 并取得了显著的成果。
02
vave在汽车行业中的重要性
vave对汽车行业的影响
减重设计
VAVE技术应用于汽车底盘减重设计,通过优化材料、结构、性能等方面的因素,降低底盘重量,提高汽车燃油经济性和操 控性能。
VAVE方法简介

VAVE方法简介展开全文点击“供应链管理云平台”可以订阅哦!1 简介价值工程法(Value Engineering,VE)又称为价值分析(Value Analysis,VA)是一门新兴的管理技术,是降低成本提高经济效益的有效方法。
指的都是通过集体智慧和有组织的活动对产品或服务进行功能分析,使目标以最低的总成本(寿命周期成本),可靠地实现产品或服务的必要功能,从而提高产品或服务的价值。
价值工程主要思想是通过对选定研究对象的功能及费用分析,提高对象的价值。
这里的价值,指的是反映费用支出与获得之间的比例,用数学比例式表达如下:价值=功能/成本。
价值工程法40年代起源于美国,麦尔斯(L· D· Miles)是价值工程的创始人。
1961年美国价值工程协会成立时他当选为该协会第一任会长。
在二战之后,由于原材料供应短缺,采购工作常常碰到难题。
经过实际工作中孜孜不倦地探索,麦尔斯发现有一些相对不太短缺的材料可以很好地替代短缺材料的功能。
后来,麦尔斯逐渐总结出一套解决采购问题的行之有效的方法,并且把这种方法的思想及应用推广到其他领域,例如,将技术与经济价值结合起来研究生产和管理的其他问题,这就是早期的价值工程。
1955年这一方法传人日本后与全面质量管理相结合,得到进一步发扬光大,成为一套更加成熟的价值分析方法。
麦尔斯发表的专著《价值分析的方法》使价值工程很快在世界范围内产生巨大影响。
2 如何进行进行一项价值分析,首先需要选定价值工程的对象。
一般说来,价值工程的对象是要考虑社会生产经营的需要以及对象价值本身有被提高的潜力。
例如,选择占成本比例大的原材料部分如果能够通过价值分析降低费用提高价值,那么这次价值分析对降低产品总成本的影响也会很大。
当我们面临一个紧迫的境地,例如生产经营中的产品功能、原材料成本都需要改进时,研究者一般采取经验分析法、ABC分析法以及百分比分析法。
选定分析对象后需要收集对象的相关情报,包括用户需求、销售市场、科技技术进步状况、经济分析以及本企业的实际能力等等。
vave方案

简介Vave方案是一种基于人工智能和大数据分析的创新解决方案,旨在提高企业的营销效果和客户满意度。
Vave方案通过分析大量的数据,构建智能化的推荐系统,为企业提供个性化的营销策略和服务,以实现更高的销售额和客户忠诚度。
背景在竞争日趋激烈的市场环境下,企业需要不断创新以保持竞争优势。
传统的统一化营销策略往往无法满足不同客户的需求,导致客户流失和销售额下降。
因此,企业需要一种个性化的营销方案来提高客户满意度和忠诚度。
Vave方案的特点Vave方案具有以下几个特点: - 数据驱动:Vave方案基于大数据分析,通过对客户行为和偏好的深入研究,为企业提供个性化的营销策略和服务。
- 智能推荐:Vave方案通过构建智能化的推荐系统,能够根据客户的历史行为和偏好,精准推荐产品、服务和优惠活动。
- 实时调整:Vave方案能够实时监测和分析客户的响应和反馈,及时调整营销策略和服务,以保持竞争力。
- 多渠道整合:Vave方案能够整合企业的各个渠道(线上和线下),为客户提供一致的购物体验和服务。
Vave方案的实施步骤Vave方案的实施步骤如下:1.数据采集:企业需要收集各种与客户相关的数据,包括购买记录、行为数据和反馈信息等。
这些数据将作为Vave方案的基础。
2.数据清洗和整合:企业需要对采集到的数据进行清洗和整合,以消除噪声和重复数据,并筛选出有价值的信息。
3.数据分析和模型构建:企业需要利用数据分析工具和技术,对清洗后的数据进行深入分析,并构建相应的模型和算法。
这些模型和算法将用于个性化推荐和营销策略的制定。
4.个性化推荐和营销策略:基于构建的模型和算法,企业可以为每个客户提供个性化的产品推荐和优惠活动。
同时,企业可以制定针对不同客户群体的营销策略,以提高销售额和客户满意度。
5.实时调整和优化:Vave方案能够实时监测客户的响应和反馈,并根据这些信息及时调整营销策略和服务,以提高效果和竞争力。
6.多渠道整合:Vave方案能够整合企业的各个渠道,包括线上和线下渠道。
vave工作思路
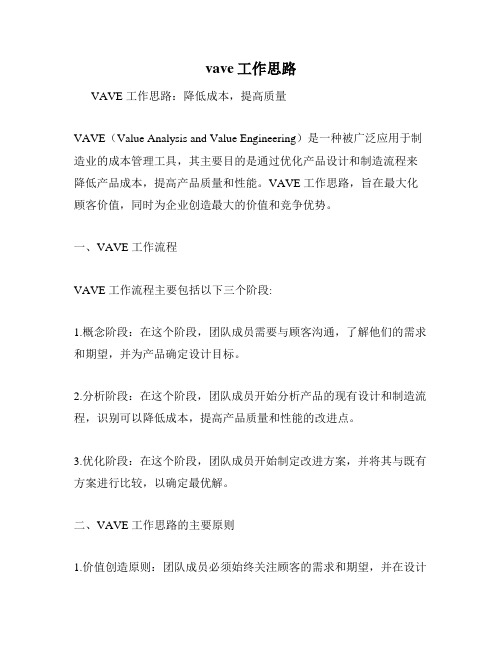
vave工作思路VAVE 工作思路:降低成本,提高质量VAVE(Value Analysis and Value Engineering)是一种被广泛应用于制造业的成本管理工具,其主要目的是通过优化产品设计和制造流程来降低产品成本,提高产品质量和性能。
VAVE 工作思路,旨在最大化顾客价值,同时为企业创造最大的价值和竞争优势。
一、VAVE 工作流程VAVE 工作流程主要包括以下三个阶段:1.概念阶段:在这个阶段,团队成员需要与顾客沟通,了解他们的需求和期望,并为产品确定设计目标。
2.分析阶段:在这个阶段,团队成员开始分析产品的现有设计和制造流程,识别可以降低成本,提高产品质量和性能的改进点。
3.优化阶段:在这个阶段,团队成员开始制定改进方案,并将其与既有方案进行比较,以确定最优解。
二、VAVE 工作思路的主要原则1.价值创造原则:团队成员必须始终关注顾客的需求和期望,并在设计和制造过程中寻找能够提高价值的改进点。
2.成本优化原则:VAVE 工作以降低产品成本为主要目标,团队成员需要通过一系列的技术和流程改进来实现这个目标。
3.品质保证原则:品质保证是 VAVE 工作的核心之一。
企业需要保证其产品在降低成本的同时,不影响产品的品质和可靠性。
三、VAVE 工作思路的优势1.降低成本,提高效率:通过 VAVE 工作思路,企业可以对制造流程进行优化,在保证产品品质的同时,减少浪费和重复劳动。
2.提高竞争力:通过降低成本和提高质量,企业可以在市场中获得更多机会,并提高其市场份额和竞争力。
3.推动创新:VAVE 工作思路可以激发团队成员的创造力和想象力,帮助企业不断推出创新的产品和服务。
四、VAVE 工作思路在实践中的应用1.在汽车制造业:汽车制造企业可以利用 VAVE 工作思路,通过启动对汽车的重新设计和制造流程的优化,达到降低成本和提高质量的目的。
2.在机械制造业:机械制造企业可以通过 VAVE 工作思路,全面优化机械产品的设计和制造流程,降低生产成本,同时提高产品的质量和性价比。
VAVE技术价值工程在汽车行业应用:价值最大化与竞争优势的追求

汽车行业应用VAVE技术:价值最大化与竞争优势的追求VAVE在汽车行业中的具体运用案例VAVE(Value Analysis and Value Engineering)是一种追求价值最大化的工程技术方法,其核心是通过优化设计、降低制造成本和提高产品质量来增加产品的价值。
在汽车行业中,VAVE被广泛应用于车辆设计、生产优化、质量管理、物流和供应链管理、安全性改进、环保技术、用户体验改善以及远程服务等方面。
1.车辆设计VAVE在车辆设计中的应用主要体现在提升汽车整体品质方面。
例如,在汽车外观设计上,VAVE可以通过分析影响外观设计的因素,优化设计方案,提高汽车的空气动力性能和审美价值。
同时,VAVE也可以应用于汽车内饰设计,通过优化材料选择、色彩搭配和布局设计等因素,提高内饰品质和舒适度。
2.生产优化VAVE在生产优化方面的应用主要体现在提高汽车产量和质量方面。
例如,在生产线设计上,VAVE可以通过分析生产流程、工位布置和设备选型等因素,优化生产线设计,提高生产效率和质量。
同时,VAVE也可以应用于生产工艺的优化,通过改进生产工艺和降低废品率,提高生产效益。
3.质量管理VAVE在质量管理方面的应用主要体现在加强汽车质量方面。
例如,在汽车质量检测上,VAVE可以通过分析质量检测方法和手段,优化质量检测流程,提高检测准确性和效率。
同时,VAVE也可以应用于质量控制方面,通过建立质量控制体系和加强质量标准控制,提高汽车产品的可靠性和稳定性。
4.物流和供应链VAVE在物流和供应链方面的应用主要体现在提高物流效率和供应链管理水平方面。
例如,在物流设计上,VAVE可以通过分析物流成本、运输效率和仓储管理等因素,优化物流设计方案,提高物流效率和降低成本。
同时,VAVE 也可以应用于供应链管理方面,通过优化供应商选择、采购策略和库存管理等因素,提高供应链的稳定性和效率。
5.安全性改进VAVE在安全性改进方面的应用主要体现在提升汽车安全性方面。
VAVE简介推动做法及案例 070926剖析

V
?
F
???Fra bibliotek?C
??
?
?
?
說 明 機能不變 機能增加 機能增加 機能大增 成本下降 成本下降 成本不變 成本稍升
合理化委員會peng
三龍
Since 1963
VA/VE 愈早提出效果愈好
構想 設計
開模 量試/量產
降低成本
成
本
VA/VE效益
投資成本
(避免成本)
早
(降低成本)
時間
晚
合理化委員會peng
三龍
3.VA/VE 活動的日程及人員設定: VA/VE 活動日期排定及相關單位參與人員之設 定。
合理化委員會peng
三龍
Since 1963
事前準備 -3
4.對象零件的各項資料: 安排相關單位事前準備 (1)依分件別的主要成本作分析 (材料、加工、塗 裝、熱處理 ...)。 (2)對象零件的主要構造組成狀況。 (3)準備對象零件 (含組立件、分件及圖面 )。 (4)準備其他車廠之相似零件 (含分件及圖面 )及構 造、成本之比較分析。
A.構造、形狀
B. 材質、表面處理
C. 尺寸、公差
D. 製程、工法
合理化委員會peng
三龍
Since 1963
4.提案分類及整理 (提案少時不用實施 ): 提案先行整理及分類清楚,並將相似提案放在一起。
5.粗略評價 (提案少時不用實施 ): 由本公司技術部及廠商研發人員先行篩選出下列明 顯
不可行提案,予以剔除 (其他人員有異議時可提出再檢 討)。 成本明顯增加。 技術上多年以後仍無法達到。 降低機能、品質及影響商品性。
(1)選擇有效者 (單價高、產量大、具複雜性、有改 善空間者 )。
- 1、下载文档前请自行甄别文档内容的完整性,平台不提供额外的编辑、内容补充、找答案等附加服务。
- 2、"仅部分预览"的文档,不可在线预览部分如存在完整性等问题,可反馈申请退款(可完整预览的文档不适用该条件!)。
- 3、如文档侵犯您的权益,请联系客服反馈,我们会尽快为您处理(人工客服工作时间:9:00-18:30)。
三
Since
龍
1963
降低成本的方向
價 格
利 益 管理費 加工費 材料費
降 低 成 本 方 向
利 益 二 不必要機能 次 機 能 部份機能 基本機能
可 再 降 低 成 本 方 向
過去降低成本方向
VE式降低成本方向
合理化委員會peng
三
Since
龍
1963
價值提升的四個方向
V=
件等刪除 式樣變更
29.便宜的替代機能有沒有? 案例 30.其他零件機能的代用可不可以? 31.是否有同時具備多種功能的替代設計? 合理化委員會peng
三
Since
三、提案發想方向彙整及案例說明
1963
龍
種類
項
目
發
想
示
例
參考案例 案例
零 件 或 材 料 來 源 變 更
材料或分 件來源變 更
32.分件使用標準品可不可以? 33.使用市售材料可不可以? 34.日本進口可否轉由他國進口? 35.進口品是否會比較便宜? 36.進口件可否轉由現地生產?
3.參與單位:研發、採購、開發、品管、生技、生管、 製造等相關單位。
合理化委員會peng
三
Since
龍
1963
集中式VA/VE的頻率:
依VA/VE年度計畫,每月排定1次,每次1~2 hr為原 則。
集中式VA/VE提案活動程序:
定期召集專案小組成員進行VA/VE活動,其步驟如 下表:
合理化委員會peng
V F C
F C
V:價值
F:機能
C:成本
說 明 機能不變 機能增加 機能增加 機能大增 成本下降 成本下降 成本不變 成本稍升
合理化委員會peng
三
Since
龍
1963
VA/VE愈早提出效果愈好
設計 開模 量試/量產
構想
降低成本
成 本
VA/VE效益
投資成本
(避免成本)
三
Since 1963
龍
VA/VE
推動、做法、發想、手法 與案例說明
1
報告者:彭雲發
三
Since
龍
1963
內容大綱
一、VA/VE基本概念
二、集中式VA/VE活動辦理程序 三、提案發想方向彙整及案例說明 四、歷年提案資料彙整與應用說明
五、提案發想訣竅
合理化委員會peng
三
Since
龍
1963
一、VA/VE基本概念
模具共通化 43.同一工程內取用數增加可不可以? 案例 44.試作模具可否沿用為量產模具? 45.可否共用BASE或共用模具? 新技術導入 46.零件改用較便宜的製法可不可以? 案例 47.新製法工程中可否製造出較便宜 的零件?
合理化委員會peng
三
Since
三、提案發想方向彙整及案例說明
1963
發
想
示
例
案例
庫存品降 低
不良率降 低 稼動率提
54.使生產線平衡,以減少半成品的方 法 有沒有?
55.降低修整及報廢率的改善方法有沒 有 ? 56.提升稼動率而降低加工成本的方法 有
案例
三
Since
龍
1963
四、歷年廠商提案資料庫彙整與應用說明
提案彙總表 04年 05年 06 年
造、成本之比較分析。
合理化委員會peng
三
Since
龍
1963
VA/VE提案活動
1.對象零件的各項狀況說明: 安排責任單位說明,由相關單位事先準備部品(零
件)及他廠相似部品,以利比較說明。
機能及裝配性說明 分件別的成本分佈狀況說明 對象零件與他廠相似件比較說明 研發單位擔當 開發單位擔當 開發單位擔當
依成本比例,再比較對象零件及他廠相似件,透過
發想表內容及提案矩陣發掘表去聯想。
30分鐘內每人提出5~10件提案(最好附簡圖)。 不批評,不論可能成立否?任何構想均可提出。 每一提案以一張MEMO紙提出。 將提案依下述分類分別貼在「VA/VE提案發想彙總
表上」,以確認提案內容是否已全盤考慮。
發現有改善之方案後,需契而不捨的水平展開 ,逐一確認其它車型是否有類似提案契機。
合理化委員會peng
三
Since
1963
五、提案發想訣竅(順藤摸瓜..)
龍
種類
項
目
其 他
物流及 LAY-OUT 49.是否製程配置變更即可節省人力? 改善 包裝或容 50.簡易包裝或去除包裝可不可以? 器改善 51.便宜的包裝代替材料有沒有?
52.料架的共通性是否有考量? 53.承載量增加而運輸費用降低的方法 有 沒有?
參考案例 48.是否有位置調整即可節省搬運作業? 案例
合理化委員會peng
三
Since
龍
1963
事前準備-3
4.對象零件的各項資料: 安排相關單位事前準備
(1)依分件別的主要成本作分析(材料、加工、塗
裝、熱處理...)。 (2)對象零件的主要構造組成狀況。 (3)準備對象零件(含組立件、分件及圖面)。 (4)準備其他車廠之相似零件(含分件及圖面)及構
1963
×:不可行
合理化委員會peng
三
Since
龍
(二)VA/VE提案活動
分別將可行、大概可行、目前不可行提案的往後日 程、作法、責任單位等作一檢討及彙整入表一中, 使後續工作得以順利進行。
項 種 次 類 1 A -----2 C ---------提案內容 (含簡圖) 意見及作法 (生產、技術、品質等考量) 效益評估 5 元/件 10 萬元/年 模治 具費 5 萬元 總合 責任 期 評價 單位 限 ○
合理化委員會peng
三
Since
1963
五、提案發想訣竅(順藤摸瓜..)
仔細觀察發想部品之結構、材質、工法..等, 多問、多聽,提出大膽假設性發想提案請技術單 位或廠商做說明,從中尋求提案契機。 針對發想部品請廠商以K/D及成本做區分,確認 各分件價格昂貴之原因,從中尋求提案契機。
龍
要求廠商對承製部品競爭車型之設計提出說明( 要求提供樣件參考),從中尋求提案契機。
廠商提案效能說明 作為新車型發想之參考→可按廠商別 / 車型別 / 課別 /篩選所需之零件,確認其提案內容及審查履歷 作為承辦/新進人員培養專業知識參考智庫→按需求 篩選瀏覽資料,參考相關單位審查結論,對於所屬廠 商所提之提案,及相關單位審查考量之角度,可有深 入之了解。 提供整體性提案改善之參考→除了了解該零件本體 之改善方向,亦可擴大搜尋該機構或者對手件之提案 改善方向。
合理化委員會peng
三
Since
三、提案發想方向彙整及案例說明
1963
龍
種類
項
目
發
想
示
例
參考案例
材質變更 或代用
規 格 變 更
品質過剩 之修正
1.便宜的代替材料有沒有? 案例 2.便宜的新材料有沒有? 3.材料改用加工性好的材料可不可以? 4.使用後工程少的材料可不可以? 5.材料等級下降可不可以? 案例 6.密度或膜厚降低可不可以? 7.零件的板厚或肉厚變薄可不可以? 8.不必要之加工工程是否可以取消? 9.精度的等級下降可不可以? 10.公差緩和(公差範圍變大)可不可以? 11.台灣環境不需要的多餘機能有沒有? 12.表面處理不要可不可以? 案例 13.表面處理作到最下限可不可以? 14.替代表面處理的方法或材料有沒有? 15.看不到部位的表面處理可否取消?
為何要推動VA/VE ?
1.企業以營利為目的,為了提升利益必須有效活用人力
、物力、財力、資訊等各項資源,而協助這些資源最
強而有力的武器就是管理技術。 2.管理技術中有IE、VE、 QC等 是降低成本最快及最 有效的方法。
IE 交期
各種方法,其中VE
企 業
VE 成本 QC 品質
合理化委員會peng
三
1963
(表一)
合理化委員會peng
三
Since
(二)VA/VE提案活動
1963
龍
7.整體效益預估及統計: 可 行 提 案:a.每台的節省金額 b.年節省金額 c.模治具費 大概可行提案:a.每件的節省金額 額 c.模治具費 b.年節省金
可行及大概可行的預估效益未達所訂目標時, 需再反覆提案及檢討。 將整體效益預估及後續作法 ( 表一 ) 呈核至經營 者 ( 推進 LEADER) ,並由事務局將可行提案整 理後送交中華汽車採購部,針對大概可行提案 F/U 後續工作之執行,並定期向本公司採購部 報告執行狀況。
A.構造、形狀 B.材質、表面處理
C.尺寸、公差
D.製程、工法
合理化委員會peng
三
Since
龍
1963
4.提案分類及整理(提案少時不用實施): 提案先行整理及分類清楚,並將相似提案放在一起。 5.粗略評價(提案少時不用實施):
由本公司技術部及廠商研發人員先行篩選出下列明 顯 不可行提案,予以剔除(其他人員有異議時可提出再檢 討 )。 成本明顯增加。
零件來源 變更 材料使用 率提昇
案例
37.變更為材料利用率高的形狀可不可 案例1 以? 案例2 38.下腳料可否再利用?餘料/廢料可否 案例3 減少?
合理化委員會peng
三
Since
三、提案發想方向彙整及案例說明
1963
龍
種類 零 件 加 工 工 法 變 更
項
目
發
想
示
例
參考案例
工程數減少 39.零件一體化還是分割化比較便宜? 案例 40.工程的簡略化或取消可不可以? 41.一模數件或一機數模可不可以? 42.無後工程的製造方法可不可以?