qa返品检验报告
QA成品出货检验作业规范
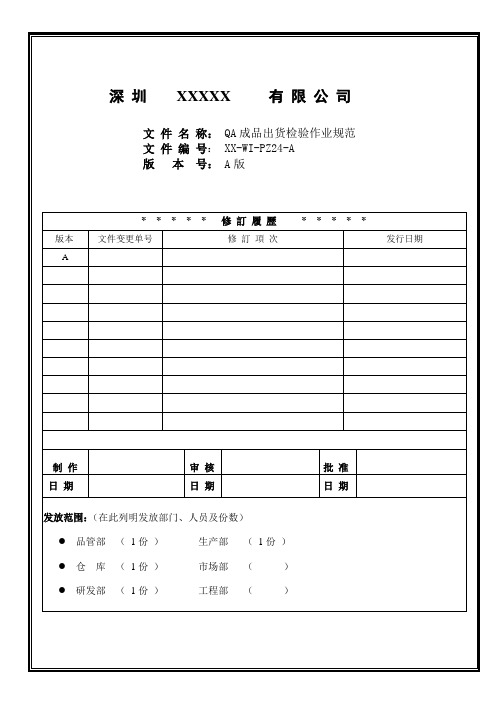
QA成品出货检验作业规范文件类型三阶文件
第 1 页共 4 页
一.目的
明确QA成品出货检验流程及品质判定标准,保证产品出货质量,确保客户满意。
二.范围
适用于本公司各类型产成品之成品出货检验作业,若本标准与客户标准相抵触时,则依双方约定为准。
三.参考文件:
《QA成品品质检验项目及判定标准》、《产品条形码编码规则》、《系统软硬件配置表》、产品资料及调试说明、《技术更改通知》、《特采作业办法》、《产品流程单》等。
四.承认样品
对于文字难以叙述清楚或不易判定合格与否的外观缺点,则以样品、图纸及说明图片作为检验时判定的依据。
五.作业程序
1.仓库送检
1.1成品每批次出货前财务部仓库必需开出《出库单》连同该批产品对应之《产品流程单》和
产品一起报送品管部QA检验。
1.2对于急需出货的物料,仓库必须在送检单上标注“急用”字样,并标明出货具体时间。
2.QA抽样检验
2.1 QA接到送检单后,按送检单所述到生产部抽取检验样本至检验台实施检验。
2.2抽样前先确认所抽物料规格型号要与送检单一致,对不符合送检单描述的产品QA可拒绝
检验,并即时反馈仓管确认处理。
2.3抽样计划:(见下表所示)
送检总量正常抽样数量加严抽样数量
5个以下 1 2
5-10 2 4
11-100 4 8
101以上 5 10
当出现以下情况时也可采用加严或全检作业:
技术变更后首次交付;
屡次发生质量问题。
2.4 检验项目:
2.4.1一般包括产品外观、标识、烧录软件、包装及配件的几项或更多内容。
PCB终检QA检验标准

目2.适3.职序项目抽样标准使用工具内容1随工单全检目视检查随工单2板厚抽样3件数显卡尺板厚度线路开/短路油墨入孔MARK点不良焊盘环宽孔环破孔导通孔环宽在连线一侧(偏孔)图 示标 准孤立区域内的孔环导通孔环宽破环(偏孔)客户有要求时按客户要求,客户没要求时符合标准孤立区域内的孔环客户板厚有要求的按客户要求检验测量板厚时要测量板的基材、铜箔、加防焊层、字符层的厚度标识要齐全.不可返工返修:退油(锡)不净、氧化变色、线路做反、烧坏、漏钻(孔化孔)、钻坏、未镀上、板面起泡、显影不净、油入孔、阻焊做反、字符印反、MARK点不良。
可返工返修:短路、开路、未沉(镀)上金、胶渍、蚀不足、漏钻(不孔化孔)、阻焊露线、擦花油、焊盘盖油、漏印字符、板材杂物(与导线距离不能小于0.15mm,杂物长度不大于2mm,宽不大于1mm,而且每块板上杂物数量不超过2个,Ⅲ级板不允许有板面杂物)由于麻点、凹坑、缺口、针孔、偏孔等缺陷的存在,允许最小环宽减少20%元件孔环宽核对随工单与板编号是否与随工单一至、产品类别、表面处理,是否有不孔化孔、最小线宽。
本工序有无特别注明,最后有无特别要求3.2品保部负责督促检查4.检验标准4.1检验流程及内容缺口符合客户要求。
或孔位不在于焊盘中心(偏孔),但环宽不小于0.05mm在焊盘与导线的连接区导线连接处应不小于0.05mm按C=0抽样方案AQL0.65抽检目视3板表面按C=0抽样方案AQL0.65抽检3.1本标准由终检QA具体遵照执行目视 孤立焊盘90°无导线连接处破环不大于90°由于麻点、凹坑、缺口、针孔、偏孔等缺陷的存在,允许最小环宽减少20%符合客户要求。
任意方向的环宽均不小于0.05mm导线连接区4金属化孔环5非金属化孔环按C=0抽样方案AQL0.65抽检目视金手指绿油杂物焊盘偏移方焊盘、测试点上绿油金属表面金属变色阻焊下变色字符重影等未冲穿或漏冲绿油掩孔14绿油桥按C=0抽样方案AQL0.65抽检目检焊盘、铜箔阻焊桥按C=0抽样方案AQL0.65抽检按C=0抽样方案AQL0.65抽检(1)符合客户要求目视不可返工返修:擦花(伤)、冲偏,冲断线、冲坏,压伤、冲爆、冲破孔、冲反、孔变形、铣断线、铣坏、铣伤、多铣、压伤、V断板、V断线、V爆板可返工返修:塞孔、毛刺大、变形、漏冲、未冲穿、漏铣、铣偏、未铣穿、漏V、V偏、变形、擦花字符、标识、周期导通孔目视阻焊底下变色所有要求掩蔽的孔都有阻焊剂覆盖1、如规定有阻焊桥(为防止焊料与导通孔桥连,阻焊桥应保留在铜被覆盖的区域。
IQA检验报告

检验单号(Ref.No.)
物料名称 Material Name 物料编号 Material Part No. 报检单号 Application Bill No.
流水号
报检时间 Application Time
I- XXXXXXXX
退货 RTV 报废 SCRAP 选料 SORT 返工 REWORK 接受使用 USE-AS-IS 物料/计划部-PMC 本厂 By In-house 本厂 By In-house 暂时使用直到: Temporary Use Until 业务部-Sales 工程部-Engineering 供应商 By In-Vendor 供应商 By In-Vendor
检验时间 Inspection Time
:
抽样计划 (Sampling Plan Based on ) 不良类别 允收水准 AQL Defective Classify 致命缺陷(CR) 严重缺陷(MAJOR) 轻微缺陷(MINOR) 高温试验 试验条件 试验温度: 试验时间: 编号 Item 1 2 3 4 5 判定 Judge 检验人/日期 Inspector/Date 核查/日期 Verified by/Date 不良描述 Defective Discription 致命缺陷 Critical 严重缺陷 Major Level 抽样数量 Sample Size 允收 Acceptt 拒收 Rejec
Material
是/否要求客户批准-签名&日期 Customer Approval RequiredSignature/or No & Date
生产部-Production
QA检验规范

1.概述本规范规定了本厂通过生产定型稳定生产后的声频功率放大器,适用于本厂质检部门经过车间按工艺要求全数检验的连续批生产的产品,最终交收检验。
2.引用标准及检验项目①GB2828《逐批检查计数抽样程序及抽样表》②GB9001《声频功率放大器测量方法》③SJ/T10406《声频功率放大器通用技术条件》④Q/(ZS)A VL 1-2001《声频功率放大器企业产品标准》3.交收检验项目及程序3.1开箱检查3.1.1开箱检查内容a.包装质量检查:不合格判据按QA成品检验标准中(二)的规定。
b.外观检查:不合格判据按QA成品检验标准中(一)的规定。
c.功能控制件及功能检查:不合格判据按QA成品检验标准中(三)的规定。
d.整机装配工艺检查:不合格判据按QA成品检验标准中(五)的规定。
3.1.2检查方法a.用直观检查法和模拟实际使用。
b.交收双方发生争议,则以品质经理之裁决为准。
3.2安全检查3.2.1安全检查内容及不合格判据按QA成品检验标准中(四)的规定。
3.2.2检查方法QA成品检验标准中4.1,4.2项按GB8898所规定的方法进行,第4.3,4.4,4.5项用目测法。
3.3常温主要电性能测量3.3.1测量项目(以各机型说明书为基准)a.失真限制的输出功率b.增益限制的有效频率范围c.过载源电动势d.对应于额定失真限制的输出功率的最小源电动势e.总谐波失真f.信噪比g.最大噪声电平h.残余噪声电平3.3.2测量方法按GB9001《声频功率放大器测量方法》规定,性能要求按《声频功率放大器企业产品标准》规定。
3.3.3主要测量项目见QA成品检验标准中(六)的规定。
3.4特别说明对于产品的老化试验、温升试验、跌落试验、故障试验、环境试验和融断试验等试验项目,只作为新产品开发阶段、工程试制阶段和小批量试产阶段QE试验内容,不作为QA常规检验内容。
4.检查水平开箱检查按《逐批检查计数抽样程序及抽样表》中表2的一般检查水平Ⅱ5.抽样方案按《逐批检查计数抽样程序及抽样表》中一次检查抽样方案。
新版GMP产品返工、重新加工管理规程

产品返工、重新加工管理规程1. 目的Objective / Purpose制定一个规程,规定本公司产品或生产过程发生异常情况时的处理要求,并规范其返工和重新加工操作。
2. 适用范围Scope适用于本公司各种疫苗,包括其原液、半成品及成品的返工和重新加工。
3. 责任部门(人)及权限Responsible department (person) and authority3.1公司各生产车间负责返工与重新加工操作,并配合必要的验证工作,严格按此规程执行。
3.2质量保证部负责对产品的质量进行评估,负责返工与重新加工操作的监督,并决定是否允许返工和重新加工,返工与重新加工后的产品是否允许放行,工登记返工台帐。
3.3物流部负责返工及重新加工所需物料的供应。
3.4成品仓库负责返工包装时产品的进、出库。
3.5验证部负责返工生产验证。
3.6QC负责返工产品检测、额外测试以及稳定性考察。
4.定义、符号和缩略语- definition, signal and abbreviation返工:将某一生产工序生产的不符合质量标准的一批中间产品或待包装产品、成品的一部分或全部返回到之前的工序,采用相同的生产工艺进行再加工,以符合预定的质量标准。
重新加工:将某一生产工序生产的不符合质量标准的一批中间产品或待包装产品的一部分或全部,采用不同的生产工艺进行再加工,以符合预定的质量标准。
5. 物料和设备Materials and equipment无。
6. 规程Procedure6.1返工及重新加工的条件和依据6.1.1重新加工条件本公司所有上市产品,包括其原液、半成品及成品均应严格按照相应的工艺规程进行生产加工,当产品质量不符合要求时不得进行重新加工,非法重新加工的产品不得放行。
故此规程以下不再描述重加工管理,仅描述有可能发生的返工。
6.1.2 返工条件只有不影响产品质量、符合相应质量标准,且根据预定、经批准的操作规程以及对相关风险充分评估后,才允许返工处理。
新供应商QSA QPA审核checklist及审核报告

b.核心技术人员的成就(如工作经历、技术成就等);
技术研发能力及产品发展规划
a.主要的研发技术能力行业水平对比(如在行业的排名等)
b.核心技术是否自主完成?例如结构件的模具、NCVM、按键组装夹具
4.2
等; c.公司的技术产品规划何技术创新(如是否为行业主流趋势或引领行业趋
势);
d.获得或正在申请的专利情况(关注数量和是否为核心专利,是否对行
2.4.1
检验标准 a.检验标准是否适用?是否每种产品都有标准?是否确定抽样计划?AQL 是否根据客户要求确定?是否确定检验转移规则?是否明确关键测试参 数及使用工具? b.检验项目是否涵盖客户要求(包括环保要求)?例行可靠性检验是否 有?是否自己完成?或者需要外发完成? c.样板管理:是否有标准样板?是否进行版本管理?
c.是否有满意度调查记录?抱怨处理记录?
6 组织结构
组织结构配置
6.1 a.质量部门是否独立? b.质量部门权限如何?
组织结构 质量、设计人员配置比率
6.2 a.主要质量、设计人员的构成(如数量比例、学历、工作经验等); b.核心技术人员的成就(如工作经历、技术成就等);
7
变更管理
变更管理流程(完善性、适宜性、有效性)
7.1
a.是否有5M1E变更管理流程?怎样定义变更? b.通过什么方式进行变更传递(含内部及客户)?是否受控状态?
变更管理
c.变更后产品是否重新签样认可?是否需要客户认可? 记录
a.是否有变更记录?相关联的资料能否很快找到?
7.2 b.各工序是否第一时间获得变更信息?怎样获得?怎样执行变更后信
息?
c.出货时是否在产品及包装上明确标识变更信息?
于失准前的测试产品是否重新测试?
IQC、IPQC、QA检验方法
IQC、IPQC、QA检验方法一、原材料检验(IQC)1.原材料检验(IQC)u库检:原材料品名规格、型号、料号、数量是否符合实际,一般由仓管人员完成。
v质检:检验原材料物理,化学等特性是否符合相应原材料检验规定,一般采用抽验方式。
w试检:取小批量试样进行生产、检查生产结果是否符合要求。
2.来料不合格的处理标识:在外包装箱上标明“ 不合格”,堆转置于“不合格区“或挂上“不合格”标识牌等。
处置:退货、调货或其它特采纠正措施:对供应商提出相关要求,并要求防止批量不合格的再次出现。
3.紧急上线:因生产急需,在检验报告出来前需采用的物资,为紧急放行,需留样检验,并对所放行物资进行特殊标识并记录,以便需要时进行追踪。
4.特采:u从非合格供应商中采购的物资——加强检验;v检验不合格而采用物资——挑选或加工后使用。
5.应特别关注不合格品所造成的损失:u投入阶段发现,损失成本为1元;v生产阶段发现,损失成本为10元;w在客户手中发现,损失成本为100元二、过程检验(IPQC)1.IPQC的检验范围包括:l 产品:半成品、成品的质量;l 人员:操作员工艺执行质量,设备技能差;l 设备:设备运行状态,负荷程度;l 工艺、技术:工艺是否合理,技术是否符合产品特性要求;l 环境:环境是否适宜产品生产需要。
2.工序产品检验:对产品的检验,检验方式有较大差异和灵活性,可依据生产实际情况和产品特性,检验方式更灵活。
3.质检员全检:适用于关键工序转序时,多品种小批量,有致命缺陷项目的工序产品。
工作量较大,合格的即准许转序或入库,不合格则责成操作员工立即返工或返修。
4.质检员抽检:适用于工序产品在一般工序转序时,大批量,单件价值低,无致命缺陷的工序品。
5.员工自检:操作员对自己加工的产品先实行自检,检验合格后方可发出至下道工序,可提高产品流转合格率和减轻质检员工作量,不易管理控制,时有突发异常现象。
6.员工互检:下道工序操作人员对上道工序产品先实行检验,可以不予接收上道工序的不良品,互相监督,有利于调动积极性,但也会引起包庇,争执等造成品质异常现象。
质量检查报告
质量检查报告一、背景介绍质量检查是生产过程中至关重要的一个环节,通过对产品的质量进行检查和评估,能够发现问题,及时进行调整和改进,确保产品的质量符合标准和客户的要求。
本报告旨在对最近一次质量检查的结果进行总结与分析,以便更好地指导后续的生产工作。
二、检查时间与地点•检查时间: 2022年4月1日至4月5日•检查地点:公司生产车间三、检查项目本次质量检查主要围绕以下几个项目展开:1.原材料质量检查2.生产工艺流程检查3.产品外观质量检查4.产品功能性能检查四、检查结果1. 原材料质量检查•原材料存储条件良好,无异味和变质现象。
•所有原材料均有相关合格证明,并符合国家标准。
2. 生产工艺流程检查•生产工艺流程严格执行,未发现重大偏差。
•工艺操作人员操作规范,有意识地执行操作规程。
3. 产品外观质量检查•产品外观整洁、无明显划痕和变形现象。
•外包装完好,无破损,符合公司标准。
4. 产品功能性能检查•产品功能齐全,性能符合设计要求。
•对产品进行抽样测试,合格率达到95%以上。
五、改进建议根据本次检查结果,提出以下改进建议:1.进一步加强原材料检查,确保产品质量的稳定性。
2.加强对生产工艺和操作规程的培训,降低操作人员的失误率。
3.定期对产品外观和功能性能进行全面检查,及时发现问题并采取措施解决。
六、总结通过本次质量检查,发现公司产品质量整体良好,但仍存在一些细微问题需要改进和提升。
希望公司能够重视这些问题,持续改进产品质量管理工作,确保产品质量始终达到客户的期望和要求。
以上为本次质量检查报告的汇总内容,如有不足之处,欢迎提出意见和建议。
QA检验记录
序号
Hale Waihona Puke 品名/图番制造单位
QA 检验记录
检验日 期:
生产日/班 客户名称 送检数量 AQL值 Ac/Re 抽样数 不良数
判定 OK NG
NO:
处理建议
备注
说明:1、产品标准按《检查标准书》和客户要求的相关项目执行,抽样标准按本公司抽样计划执行;
2、若判定为不合格需返工、返修等处理的,需在返工、返修后按报检程序重新送检,直到合格为止,并在备注栏中注明重检结果;
3、此表一式三份,制造单位、仓库、质审量核部人各一/ 份;每日检验完成后及时提报质量部文确员认统计;
日期:
人/日
检验员/日期:
客退品判定和报废处理程序
4.3对客户用后退次,品保部OQC需全检外观,若因机能退回,需全检机能尺寸。对批量退货,品保部OQC判定能将不合格品挑出则以《筛选-修改通知书》通知生产部门或全检班进行挑选;否则,品保部副经理会同生产部门确定处理方法(包括报废、返工等)。生产部门挑选、返工后的合格品,生产部门责任组长以《返工结果报告单》通各品保部FQC进行检验;品保部全检班挑选、。
QA:复审并确认客退品报废申请。
物控部成品科:将判定为报废的客退品退物料加工科粉碎,回收胶料。
物料加工科:依据批准的《不合格品报废申请单》实施客退品粉碎。
4.【内容】
4.1市场部收到客户退货信息后通知品保部和物控部,责成品保部QA与客户联络确认退货原因;QA确定接收退货后以《联络单》通知物控部,由其安排有关退货接收、运输事宜。
5.【制定/改订履历】
NO
制定/改订日
变更内容
作成
确认
承认
1
2005-8-12
新规制定
2
3
4.6客户退货的处理结果由OQC记录于《客户退货分析报告》中,并报品保部经理批准。
4.7客户批量退货量超过当次出货量的5%(含5%)时,品保部需发起纠正预防措施。
4.8单据保存:
《不合格品报废申请单》原件由品质文员归口统一保管,其余各部门如:物控部、成形科、物料加工科保留复印件,以备数据核查。
保存期限:1年。
4.4拣出的单个不合格报废品由FQC或全检班长填写《不合格品报废申请单》报上级主管决定处理方法。拣出的多个不合格报废品由返工部门填写《不合格品报废申请单》由本部门班长以上人员确认后交FQC科长确认,再将报废品与单据一起送物料加工科粉碎处理。