数控车床主轴系统
(FANUC 0i-mate-TC)数控车床主轴驱动系统的装调

2.
三菱E700变频器参数设置
(1)、三菱E700变频器操作要领
将所有参数 恢复至出厂 值
变更参数设定值
Pr.160 用户参数组读取选择= “1”,用户参数组中未登录 Pr.79 。Pr.77= “1”,禁止写入参数。
需要设置的参数
四、任务检查
(1) 操作数控系统FANUC 0i-mate-TC ,运行模式为“手动”运行模 式,摁下“主轴正转”键,则主轴电机正向旋转。摁下“主轴倍率”增 加键(减少键),主轴转速增大(减小); (2)操作数控系统FANUC 0i-mate-TC ,运行模式为“手动”运行模 式,摁下“主轴反转”键,则主轴电机反向旋转。摁下“主轴倍率”增 加键(减少键),主轴转速增大(减小); ; (3) 操作数控系统FANUC 0i-mate-TC ,运行模式为“手动”运行模式 ,摁下“主轴停”键,则主轴电机停止旋转; (4) 操作数控系统FANUC 0i-mate-TC ,运行模式为“MDI”运行模式, 输入“M03S800”,或者“M04S800”或者“M05”主轴能正确动作。
编码器用在主轴系统上: (1)测主轴转速显示在NC屏幕上; (2)车削螺纹时,不至于乱牙;
(二)MITSUBISHI E700 系列变频器
主轴伺服驱动装置
主轴电机
1. 变频器连接图
变频器
三相异步电机
端 子 、任务实施
(一)电气线路测绘
每一组随机抽检2份PPT课件,并通过PPT汇报展示电气测绘的成 果,教师现场打分。
60 f 1 n 1 s n0 1 s p 1 变频调速 (无级调速)
f=50Hz +
整流器 逆变器
三种电气 调速方法
f1、U1可调 M
车床CA6140主轴系统的数控化改造及仿真毕业设计
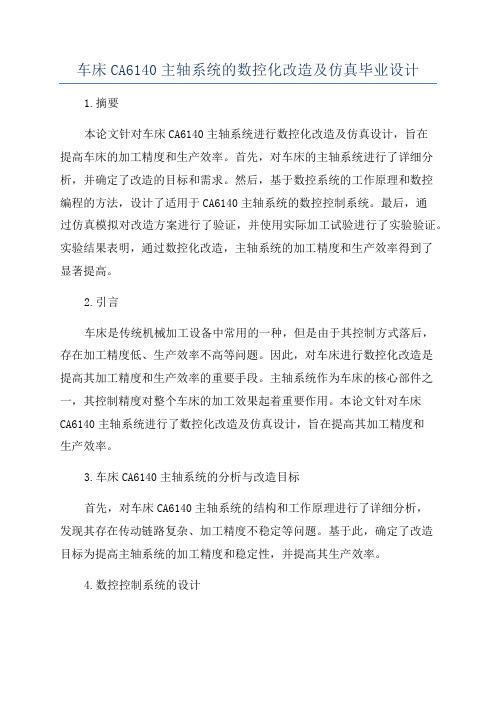
车床CA6140主轴系统的数控化改造及仿真毕业设计1.摘要本论文针对车床CA6140主轴系统进行数控化改造及仿真设计,旨在提高车床的加工精度和生产效率。
首先,对车床的主轴系统进行了详细分析,并确定了改造的目标和需求。
然后,基于数控系统的工作原理和数控编程的方法,设计了适用于CA6140主轴系统的数控控制系统。
最后,通过仿真模拟对改造方案进行了验证,并使用实际加工试验进行了实验验证。
实验结果表明,通过数控化改造,主轴系统的加工精度和生产效率得到了显著提高。
2.引言车床是传统机械加工设备中常用的一种,但是由于其控制方式落后,存在加工精度低、生产效率不高等问题。
因此,对车床进行数控化改造是提高其加工精度和生产效率的重要手段。
主轴系统作为车床的核心部件之一,其控制精度对整个车床的加工效果起着重要作用。
本论文针对车床CA6140主轴系统进行了数控化改造及仿真设计,旨在提高其加工精度和生产效率。
3.车床CA6140主轴系统的分析与改造目标首先,对车床CA6140主轴系统的结构和工作原理进行了详细分析,发现其存在传动链路复杂、加工精度不稳定等问题。
基于此,确定了改造目标为提高主轴系统的加工精度和稳定性,并提高其生产效率。
4.数控控制系统的设计根据数控系统的工作原理和数控编程的方法,设计了适用于CA6140主轴系统的数控控制系统。
首先,选取了适合主轴系统控制的数控设备,并设计了相应的控制算法和程序。
然后,对数控编程进行了详细设计,并使用仿真软件进行了仿真验证。
5.改造方案的仿真与验证为了验证改造方案的有效性,使用仿真软件对其进行了仿真模拟。
首先,建立了CA6140主轴系统数学模型,并将其运行参数与改造后的数控控制系统进行了耦合。
然后,通过调整控制系统的参数,对加工过程进行了仿真模拟,并对加工结果进行了分析和评估。
最后,使用实际加工试验进行了实验验证,并与仿真结果进行了对比分析。
6.结论通过车床CA6140主轴系统的数控化改造及仿真设计,本论文有效提高了主轴系统的加工精度和生产效率。
(完整版)数控车床主轴设计

绪论随着市场上产品更新换代的加快和对零件精度提出更高的要求,传统机床已不能满足要求。
数控机床由于众多的优点已成为现代机床发展的主流方向。
它的发展代表了一个国家设计、制造的水平,在国内外都受到高度重视。
现代数控机床是信息集成和系统自动化的基础设备,它集高效率、高精度、高柔性于一身,具有加工精度高、生产效率高、自动化程度高、对加工对象的适应强等优点。
实现加工机床及生产过程的数控化,已经成为当今制造业的发展方向。
可以说,机械制造竞争的实质就是数控技术的竞争。
本课题的目的和意义在于通过设计中运用所学的基础课、技术基础课和专业课的理论知识,生产实习和实验等实践知识,达到巩固、加深和扩大所学知识的目的。
通过设计分析比较机床的某些典型机构,进行选择和改进,学习构造设计,进行设计、计算和编写技术文件,达到学习设计步骤和方法的目的。
通过设计学习查阅有关设计手册、设计标准和资料,达到积累设计知识和提高设计能力的目的。
通过设计获得设计工作的基本技能的训练,提高分析和解决工程技术问题的能力,并为进行一般机械的设计创造一定的条件。
一、设计题目及参数1.1 题目本设计的题目是数控车床的主轴组件的设计。
它主要由主轴箱,主轴,电动机,主轴脉冲发生器等组成。
我主要设计的是主轴部分。
主轴是加工中心的关键部位,其结构优劣对加工中心的性能有很大的影响,因此,在设计的过程中要多加注意。
主轴前后的受力不同,故要选用不同的轴承。
1.2参数床身回转空间400mm尾架顶尖与主轴端面距离1000mm主轴卡盘外径Φ200mm最大加工直径Φ600mm棒料作业能力50~63mm主轴前轴承内和110~130mm最大扭矩480N·m二、主轴的要求及结构2.1主轴的要求2.1.1旋转精度主轴的旋转精度是指装配后,在无载荷,低转速的条件下,主轴前端工件或刀具部位的径向跳动和轴向跳动。
主轴组件的旋转精度主要取决于各主要件,如主轴、轴承、箱体孔的的制造,装配和调整精度。
CK6140数控车床主传动系统设计

CK6140数控车床主传动系统设计数控车床的主传动系统是整个机床的核心组成部分,它主要由主轴、主轴驱动装置和主动工具头等组成。
设计一个稳定可靠的数控车床主传动系统,需要考虑诸多因素,如主轴精度、刚度、转速范围、加工能力等。
首先,主轴是数控车床主传动系统的核心部件,其精度和刚度直接影响到整个机床的加工质量。
主轴通常由高强度、高刚性的合金钢材料制成,并通过精密加工和热处理工艺提高其表面质量和硬度。
主轴的设计应考虑转动稳定性、轴向和径向刚度等因素,以确保在高速运转和大负载下能保持较小的振动和变形。
其次,主轴驱动装置主要是通过电机将动力传递给主轴,实现车床的加工运行。
常见的主轴驱动装置包括皮带传动、齿轮传动、液压传动等。
不同的传动方式具有不同的特点,需要根据数控车床的具体要求进行选择。
同时,主轴驱动装置还需要考虑电机的功率、转速调节范围、动态响应性能等因素,以满足不同加工工艺和加工材料的需求。
另外,主动工具头也是数控车床主传动系统的重要组成部分。
主动工具头一般由进给系统和切削工具组成,其主要功能是控制刀具的进给速度和刀具路径,实现工件的加工。
进给系统通常由伺服电机、滚珠丝杠等组成,将电机的旋转运动转化为刀具的直线运动。
切削工具的选择要根据不同的加工工件和加工要求进行,可以是转动刀具、切削刀具或磨削工具等。
除了上述部件,数控车床主传动系统的设计还需要考虑其控制方式和辅助装置。
传统的数控车床主传动系统采用闭环控制,通过编码器和反馈系统实现对主轴和主动工具头运动的精确控制。
辅助装置如冷却系统、润滑系统、自动换刀系统等,可以提高加工效率和工作环境的安全性。
总的来说,设计一个稳定可靠的数控车床主传动系统需要充分考虑主轴精度、刚度,主轴驱动装置的选择,主动工具头的设计以及控制方式和辅助装置的配置等因素。
只有在满足加工要求的前提下,才能实现高效、精确和安全的数控车床加工操作。
数控车床主轴速度控制

C.有较完善的刀具自动交换和管理系统
D.有工件自动交换、工件夹紧与放松机构
E.床身机架具有很高的动刚度和静刚度
F.采用全封闭罩壳
2.2 数控机床的基本工作过程
首先根据零件图样,结合加工工艺进行程序编制,然后通过键盘或者其它输入设备送入数控系统后再经过调试、修改,最后把它存储起来。加工时就按所编程序进行有关数字信息处理。一方面通过插补运算器进行加工轨迹运算处理,从而控制伺服系统驱动机床各坐标轴,使刀具与工件的相对位置按照被加工零件的形状轨迹进行运动,并通过位置检测回馈以确保其位移精度。另一方面按照加工要求,通过PLC控制主轴及其它辅助装置协调工作,如主轴变速、主轴齿轮换挡、适时进行ATC刀具自动交换、工件夹紧与放松、润滑系统的开停、切削液的开关,必要时超载或限位保护起作用,控制机床运动迅速停止。
3.2 数控车床主轴速度控制方式
3.2.1 主轴速度CNC控制方式
主轴速度CNC控制方式指,主轴的速度是由系统CNC加工程序的S码指定的速度值决定,可以通过机床面板上的主轴倍率开关进行修调(通常为50%~120%),这是数控机床通常的控制方式。
3.2.2 主轴速度的特殊S码控制方式
这种控制方式主要用于普通型数控车床的主轴速度控制,该类主轴传动控制方式为手动换挡(低、中和高速选择),以及电磁离合器配合双速电动机自动变速控制,在加工程序中通过S码(一般在每挡有四种S码速度选择)实施电磁离合器和双速电动机的控制。
随着技术的不断发展,机床结构有了很大的改进,从而对主轴系统提出了新的要求,而且因用途而异。在数控机床中,数控车床占42%,数控钻镗铣床占33%,数控磨床、冲床占23%,其它只占2%。为了满足现代数控机床对主轴驱动的更高要求,主轴电动机必须具备如下功能:
数控车床工作原理
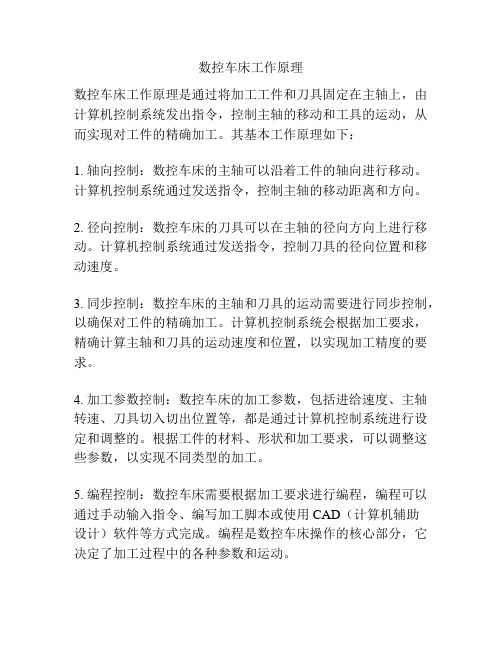
数控车床工作原理
数控车床工作原理是通过将加工工件和刀具固定在主轴上,由计算机控制系统发出指令,控制主轴的移动和工具的运动,从而实现对工件的精确加工。
其基本工作原理如下:
1. 轴向控制:数控车床的主轴可以沿着工件的轴向进行移动。
计算机控制系统通过发送指令,控制主轴的移动距离和方向。
2. 径向控制:数控车床的刀具可以在主轴的径向方向上进行移动。
计算机控制系统通过发送指令,控制刀具的径向位置和移动速度。
3. 同步控制:数控车床的主轴和刀具的运动需要进行同步控制,以确保对工件的精确加工。
计算机控制系统会根据加工要求,精确计算主轴和刀具的运动速度和位置,以实现加工精度的要求。
4. 加工参数控制:数控车床的加工参数,包括进给速度、主轴转速、刀具切入切出位置等,都是通过计算机控制系统进行设定和调整的。
根据工件的材料、形状和加工要求,可以调整这些参数,以实现不同类型的加工。
5. 编程控制:数控车床需要根据加工要求进行编程,编程可以通过手动输入指令、编写加工脚本或使用CAD(计算机辅助
设计)软件等方式完成。
编程是数控车床操作的核心部分,它决定了加工过程中的各种参数和运动。
总之,数控车床工作原理是通过计算机控制系统对主轴和刀具的运动进行精确定位和控制,以达到对工件的精确加工要求。
这种工作方式使得加工过程更加高效、准确,并能够满足不同类型工件的加工需求。
数控机床主轴驱动变频控制
数控机床主轴驱动变频控制一、前言数控机床是传统机床向智能化方向发展的结果,其操作简单、精度高、效率高等特点,使得其在现代制造业中大有用处。
数控机床中的主轴驱动控制是其中的一个重要环节,其精度和可靠性对整个机床的操作效果有着至关重要的作用。
本篇文档将主要介绍数控机床主轴驱动变频控制相关知识。
二、数控机床主轴驱动变频控制的原理数控机床的主轴驱动控制系统主要是由相关电气元件组成的变频器控制系统。
变频器就是将市电通过整流、滤波、逆变后输出一定的频率、电压并控制电机转速的电子装置。
在数控机床的主轴驱动系统中,变频器通过对电机控制进行电压和频率的调整,来实现主轴的旋转,进而控制其转速和输出功率。
变频器输出的频率、电压均可调整,因此可以通过控制变频器的输出,来实现对主轴的速度调节。
电气控制系统通过实时监测机床运行状态、主轴运行状态、机床速度、主轴转速等信息,根据预先设定的运转条件,通过控制变频器输出的电压、频率实现对机床的工作状态并实现对主轴的速度调节。
三、数控机床主轴驱动变频控制的优点与传统机床的主轴驱动方式相比,数控机床主轴驱动变频控制有诸多优点,主要体现在以下几个方面:1.可调性强:通过对变频器的控制,可以实现精确的主轴转速调节,可以满足不同需求的工件加工。
2.精度高:由于采用了电气控制系统,可以实现主轴转速的精确控制,进而实现加工精度的提高。
3.效率高:数控机床主轴驱动变频控制由于能够实现电气控制,减少了机械传动过程中的机械损耗,因此其效率远高于传统机床主轴驱动方式。
4.运转平稳:变频器可以调节输出电压和频率,可以进一步实现对主轴转速的控制,从而实现机床运转的平稳。
四、数控机床主轴驱动变频控制的应用数控机床主轴驱动变频控制技术的应用相当广泛,可以应用于各种数控机床类型,包括数控车床、数控加工中心、数控铣床等。
特别是在高速、高精度、高效率的加工应用中,其优势更加明显。
五、数控机床主轴驱动变频控制的维护和保养为了确保数控机床主轴驱动变频控制系统的长期稳定运行,必须进行日常的维护和保养。
一种新型的数控管螺纹车床主轴系统设计
文 章 编 号 :0 1—2 6 2 1 0 10 2 5( 0 0) 8—0 8 0 3—0 2
・ 艺与装备 车床 主 轴 系统 设 计
倪 晓 东, 晓进 , 宏 , 代 王 田振 强 , 旺 黄
( 兰州 理工 大 学 材 料科 学 与工 程 学院 , 兰州 7 0 5 ) 3 0 0
( c o lo tra S in e a d E gn eig a z o iest f e h oo y,L n h u 7 0 5,C ia S h o fMaeil ce c n n ie r ,L n h u Unv ri o c n lg n y T a z o 3 0 hn )
Absr c :I d rt a hn n ype o r e d a e e t e pe w e d sg e e s y e s n d es tm f t a t n or e o m c ii g a t fl g ・ im t rse lpi e in d a n w t l pi l yse o a
A e i n f r a Ne t l e dsoc C pe t e d M ac n D sg o wsy e H a t k ofN Pi -hr a hi e
NIXio d n ,D a - n a —o g AIXioj ,WANG Ho g,T a h nq a g i n in Z e — in ,HUANG Wa g n
进 给 运 动 。 该 设 计 在 满 足 管件 加 工 要 求 的 同 时 , 服 了 传 统 机 床 的 各 种 缺 点 , 高 了 生 产 率 , 低 了机 克 提 降
床 设备 的投 入成 本 。 关 键 词 : 传 动 系统 ; 螺 纹 ; 联 齿 轮 主 管 三 中 图 分 类 号 : G 5 . ; G5 6 T 7 1 1T 3 文献 标识 码 : A
数控机床主轴驱动与控制
特点,还可以实现定向和进给功能,当然价格也是最高的, 通常是同功率变频器主轴驱动系统的2--3倍以上。
伺服主轴驱动系统主要应用于加工中心上,用以满足系 统自动换刀、刚性攻丝、主轴C轴进给功能等对主轴位置 控制性能要求很高的加工。
6.2.3主轴分段无级调速
6.2主轴驱动与控制(Spindle Drive and Control)
图6.3所示为西 门子802C数控系 统的变频调速控 制连接图。主轴 电机的正反转通 过继电器KA2和 KA3控制,转速 大小通过X7口模 拟电压值大小控 制。
6.2主轴驱动与控制(Spindle Drive and Control)
6.1 概述
1.主轴驱动系统的功能
主轴驱动系统通过控制主轴电机的旋转方向和转速, 从而调节主轴上安装的刀具或工件的切削力矩和切削速度, 配合进给运动,加工出理想的零件。因此,主轴驱动的主 要功能是为各类工件的加工提供所需的切削功率。
此外,当数控机床具有螺纹加工、恒线速加工以及准 停要求(比如加工中心换刀)时,对主轴也提出了相应的 位置控制要求,所以此类数控机床还具有主轴与进给联动 功能和准停控制功能。
6.1 概述
(3)DANFOSS(丹佛斯)公司系列变频器 该公司目前应用于数控机床上的变频器系列常用的有:
VLT2800,可并列式安装方式,具有宽范围配接电机功率: 0.37KW-7.5KW 200V/400;VLT5000,可在整个转速范围内进行 精确的滑差补偿,并在3ms内完成。在使用串行通讯时,VLT 5000对每条指令的响应时间为0.1ms,可使用任何标准电机与VLT 5000匹配。
对于中档数控机床而言主要采用这种方案。其主轴传动仅采用两 挡变速甚至仅一挡即可实现100—200 r/min左右时车、铣的重力切 削。一些有定向功能的还可以应用于要求精镗加工的数控镗铣床。 但若应用在加工中心上,还不很理想,必须采用其他辅助机构完成 定向换刀的功能,而且也不能达到刚性攻丝的要求。
数控车床说明书
数控车床说明书一、产品概述数控车床是一种能够通过计算机控制来实现自动化加工的工作机床。
它能够精确地控制工件的运动和切削操作,提高生产效率和加工精度。
本说明书旨在向用户介绍数控车床的结构、工作原理、使用方法以及维护保养等内容。
二、结构和工作原理数控车床由控制系统、主轴系统、刀具系统、进给系统、润滑系统、冷却系统等多个部件组成。
其中,控制系统是数控车床的核心,控制着各个部件的工作。
通过输入刀具路径、切削参数和工件尺寸等设定值,控制系统可以实现工件的精确加工。
主轴系统是数控车床的主要动力部件,通过电机驱动主轴旋转,实现切削操作。
刀具系统则用于固定不同类型和规格的刀具,满足不同加工要求。
进给系统控制刀具的运动,使其按照预设的路径进行加工。
润滑系统和冷却系统则保证数控车床的稳定工作和有效散热。
三、使用方法1. 开机准备:确保数控车床的工作环境清洁干燥,检查电源和气源的连接是否正常。
然后按照操作手册的指引打开数控车床的电源。
2. 设定加工参数:根据实际需要,使用数控车床的控制系统设置合适的切削参数,包括转速、进给速度、切削刀具的尺寸等。
3. 设定工件路径:在控制系统中输入工件的加工路径,可以手动设定或者通过CAD软件导入工件的数控程序。
4. 夹紧工件:使用合适的夹具将工件固定在数控车床的工作台上,确保工件的稳固。
5. 开始加工:将刀具设置到合适的位置,调整好刀具和工件的相对位置,然后启动数控车床,开始加工。
6. 监控加工过程:在加工过程中,及时观察数控车床的工作状态,确保加工过程正常进行。
7. 结束加工:加工完成后,关闭数控车床的电源,清理加工区域,并对数控车床进行维护保养。
四、维护保养1. 定期润滑:根据数控车床的使用频率,定期给予润滑部件添加适量的润滑油,保证各个部件的正常工作。
2. 清洁保养:定期清洁数控车床的各个部件,包括导轨、传动装置等,保持其清洁干燥。
3. 检查维修:定期进行数控车床的检查和维修,及时发现并处理问题,确保数控车床的正常运行。
- 1、下载文档前请自行甄别文档内容的完整性,平台不提供额外的编辑、内容补充、找答案等附加服务。
- 2、"仅部分预览"的文档,不可在线预览部分如存在完整性等问题,可反馈申请退款(可完整预览的文档不适用该条件!)。
- 3、如文档侵犯您的权益,请联系客服反馈,我们会尽快为您处理(人工客服工作时间:9:00-18:30)。
模块一对主轴驱动系统的认识任务一掌握主轴驱动系统各种故障排查方法。
1.主轴驱动系统概述主轴驱动系统也叫主传动系统,是在系统中完成主运动的动力装置部分。
主轴驱动系统通过该传动机构转变成主轴上安装的刀具或工件的切削力矩和切削速度,配合进给运动,加工出理想的零件。
它是零件加工的成型运动之一,它的精度对零件的加工精度有较大的影响。
引言主轴驱动系统控制数控车床的旋转运动,为车床主轴提供驱动功率以及所需的切削力。
目前在数控车床中,主轴驱动常使用交流电动机,直流电动机已被逐渐淘汰,由于受永磁体的限制,交流同步电动机功率做得很大时,电动机成本太高。
因此目前在数控机床的主轴驱动中,均采用笼型异步电动机。
为了获取良好的主轴特性,设计中采用矢量变频控制的交流主轴电动机,矢量部分分无速度传感器和有速度传感器的两种方式,后者具有更高的速度控制精度,在数控车床中无速度传感器的矢量变频器已经符合控制要求,因此,本设计中采用无速度的矢量变频器。
知识目标:1、了解主轴驱动系统的控制原理。
2、了解各种故障的产生原因。
能力目标:1、能够对主轴驱动系统启动故障进行排除和处理。
2、熟练掌握变频器的使用方法。
一、相关知识1、数控机床对主轴驱动系统的要求机床的主轴驱动和进给驱动有较大的差别。
机床主轴的工作运动通常是旋转运动,不像进给驱动需要丝杠或其它直线运动装置作往复运动。
数控机床通常通过主轴的回转与进给轴的进给实现刀具与工件的快速的相对切削运动。
在20纪60-70年代,数控机床的主轴一般采用三相感应电动机配上多级齿轮变速箱实现有级变速的驱动方式。
随着刀具技术、生产技术、加工工艺以及生产效率的不断发展,上述传统的主轴驱动已不能满足生产的需要。
现代数控机床对主轴传动提出了更高的要求:1)调速范围宽并实现无极调速为保证加工时选用合适的切削用量,以获得最佳的生产率、加工精度和表面质量。
特别对于具有自动换刀功能的数控加工中心,为适应各种刀具、工序和各种材料的加工要求,对主轴的调速范围要求更高,要求主轴能在较宽的转速范围内根据数控系统的指令自动实现无级调速,并减少中间传动环节,简化主轴箱。
主轴变速分为有级变速、无级变速和分段无级变速三种形式,其中有级变速仅用于经济型数控机床,大多数数控机床均采用无级变速或分段无级变速。
在无级变速中,变频调速主轴一般用于普及型数控机床,交流伺服主轴则用于中、高档数控机床。
2)、恒功率范围要宽主轴在全速范围内均能提供切削所需功率,并尽可能在全速范围内提供主轴电动机的最大功率。
由于主轴电动机与驱动装置的限制,主轴在低速段均为恒转矩输出。
为满足数控机床低速、强力切削的需要,常采用分级无级变速的方法(即在低速段采用机械减速装置),以扩大输出转矩。
3)、具有4象限驱动能力要求主轴在正、反向转动时均可进行自动加、减速控制,并且加、减速时间要短。
目前一般伺服主轴可以在1秒内从静止加速到6000r/min。
4)、具有位置控制能力即进给功能(C轴功能)和定向功能(准停功能),以满足加工中心自动换刀、刚性攻丝、螺纹切削以及车削中心的某些加工工艺的需要。
5)、具有较高的精度与刚度,传动平稳,噪音低。
数控机床加工精度的提高与主轴系统的精度密切相关。
为了提高传动件的制造精度与刚度,采用齿轮传动时齿轮齿面应采用高频感应加热淬火工艺以增加耐磨性。
最后一级一般用斜齿轮传动,使传动平稳。
采用带传动时应采用齿型带。
应采用精度高的轴承及合理的支撑跨距,以提高主轴的组件的刚性。
在结构允许的条件下,应适当增加齿轮宽度,提高齿轮的重叠系数。
变速滑移齿轮一般都用花键传动,采用内径定心。
侧面定心的花键对降低噪声更为有利,因为这种定心方式传动间隙小,接触面大,但加工需要专门的刀具和花键磨床。
6)、良好的抗振性和热稳定性。
数控机床加工时,可能由于持续切削、加工余量不均匀、运动部件不平衡以及切削过程中的自振等原因引起冲击力和交变力,使主轴产生振动,影响加工精度和表面粗糙度,严重时甚至可能损坏刀具和主轴系统中的零件,使其无法工作。
主轴系统的发热使其中的零部件产生热变形,降低传动效率,影响零部件之间的相对位置精度和运动精度,从而造成加工误差。
因此,主轴组件要有较高的固有频率,较好的动平衡,且要保持合适的配合间隙,并要进行循环润滑2、主轴驱动装置的特点主轴驱动系统是数控机床的大功率执行机构,其功能是接受数控系统(CNC)的S码(速度指令)及M码(辅助功能指令),驱动主轴进行切削加工。
它接受来自CNC的驱动指令,经速度与转矩(功率)调节输出驱动信号驱动主电动机转动,同时接受速度反馈实施速度闭环控制。
它还通过PLC将主轴的各种现实工作状态通告CNC用以完成对主轴的各项功能控制。
为满足数控机床对主轴驱动的要求,主轴电动机必须具备下述功能:1)输出功率大。
2)在整个调速范围内速度稳定,且恒功率范围宽。
3)在断续负载下电动机转速波动小,过载能力强。
4)加速时间短。
5)电动机温升低。
6)振动、噪声小。
7)电动机可靠性高,寿命长,易维护。
8)体积小、质量轻。
3、主轴驱动装置分类1)直流主轴驱动装置直流主轴电动机的结构与永磁式伺服电动机不同,主轴电动机要能输出大的功率,所以一般是他磁式。
为缩小体积,改善冷却效果,以免电动机过热,常采用轴向强迫风冷或采用热管冷却技术。
直流驱动装置有晶闸管和脉宽调制PWM调速两种形式。
由于脉宽调制PWM调速具有很好的调速性能,因而在数控机床特别是对精度、速度要求较高的数控机床的进给驱动装置上广泛使用。
而三相全控晶闸管调速装置则在大功率应用方面具有优势,因而常用于直流主轴驱动装置。
2)交流主轴驱动装置主轴伺服提供加工各类工件所需的切削功率,因此,只需完成主轴调速及正反转功能。
但当要求机床有螺纹加工、准停和恒线速加工等功能时,对主轴也提出了相应的位置控制要求,因此,要求其输出功率大,具有恒转矩段及恒功率段,有准停控制,主轴与进给联动。
与进给伺服一样,主轴伺服经历了从普通三相异步电动机传动到直流主轴传动。
随着微处理器技术和大功率晶体管技术的进展,现在又进入了交流主轴伺服系统的时代。
4、变频器1)工作原理根据公式:n=60f/p 可知交流异步电机的转速与电源频率 f 成正比与电机的极对数成反比,因此,改变电机的频率可调节电机的转速。
通常我们为了保证在一定的调速范围内保持电动机的转矩不变,在调节电源频率 f 时,必须保持磁通Φ不变,由公式 U≈E=4.44fWK Φ可知,Φ∝U/f 所以改变频率 f 时,同时改变电源电压 U,可以保持磁通Φ不变。
目前大部分变频器都采用了上述原理。
用同时改变f和U 的方法来实现电机转速 n的调速控制,并使得输出扭矩在一定范围内保持不变。
注:电机的极对数与转速V,U,W代表三相电机的每一相,电机内部共有3组线圈,每一组就是一相,出来两个线头,3相共出6个线头,分别按照一定的接法接到三相电源上。
一组线圈或一相包含多个线圈,但不会是单数的,因为它要组成南北两个极,而且在电机内部是对称的,例如图1,其中一相V,有两个线圈一个在上部一个在下部,两个线圈是串联的,通电时就产生两个磁极,图2的V相有4个线圈,也串联在一起,也是对称的,但它有4个极,这个图只是告诉大家线圈在电机内部的方位,和所谓的磁极对数。
第一个图每一相有南北两个极,就是一对磁极,磁极对数是1,通常叫它2极电机,转速最快。
实物图:二、任务分析1、主轴变频系统常见故障处理1)主轴电机不转主要有以下原因:①检查CNC系统是否有速度控制信号输出。
②主轴驱动装置故障。
③主轴电动机故障。
④变频器输出端子U、V、W不能提供电源。
造成此种情况可能有以下原因:报警;频率指定源和运行指定源的参数是否设置正确;智能输入端子的输入信号是否正确。
2)电机反转造成电机反转的原因主要有:①检查输出端子U/T1,V/T2和W/T3的连接是否正确?(使得电机的相序与端子连接相对应,通常来说:正转(FWD)=U-V-W,和反转(REV)=U-W-V)。
②检查控制端子(FW)和(RV)连线是否正确?(端子(FW)用于正转,(RV)用于反转)。
3)电机转速不能到达额定转速主要原因可能有:①如果使用模拟输入,是否用电流或电压“O”或“OI”。
检查连线;检查电位器或信号发生器。
②负载太重。
减少负载;重负载激活了过载限定。
4)主轴振动或噪声太大:检查振动的周期是否与转速有关,如无关,一般是主轴驱动装置未调整好;如有关,应检查主轴机械部分是否良好,测速装置是否不良2、主轴驱动系统启动常见故障分析:对于主轴驱动系统启动故障的原因有很多,首先检查外围电路,确保主轴电机、变频器电源正常供电;也有可能是CNC无速度信号输出,如果CNC无速度信号输出,要检测速度给定信号,检查系统参数;另外还可能是主轴驱动器故障,首先要检查是否有报警错误代码显示,如有报警,对照相关说明书解决(主要有过流、过、过压、欠压以及功率块故障等)。
其次还要检查频率指定源和运行指定源的参数是否设置正确。
三、思考题1、如何判断变频器自身故障?2、如何修改变频器的参数?3、阐述电机的两种启动方式。
模块二主轴驱动系统参数设置与修改任务目标知识目标1、明白数控系统参数在数控系统中的作用。
2、了解数控系统硬件连接与系统参数的关系能力目标1、掌握各种参数的意义2、能够对主轴驱动系统参数进行设置和修改相关知识1、华中HNC-21TF数控系统参数设置(1).参数树数控系统中的参数进行分级管理,各级参数组成参数树。
华中HNC-21TF数控系统的参数树如图2.1.1所示。
系统参数硬件配置参数通道参数通道0通道1通道2通道3轴0轴1轴3轴2轴0轴1轴2轴3坐标轴参数轴补偿参数参数索引PMC系统参数外部报警系统PMC用户参数DNC参数参数树2.1.1(2).参数管理权限数控装置的运行,严格依赖于系统参数的设置,因此,对参数修改的权限采用分级管理。
在华中HNC-21TF数控装置中,设置了三种级别的权限,即数控厂家、机床厂家、用户;不同级别的权限,可以修改的参数是不同的。
1)数控厂家:最高级权限,能修改所有参数。
2)机床厂家:中间级权限,能修改机床调试时需要设置的参数。
3)用户厂家:最低级权限,仅能修改用户使用时需要改变的参数。
数控机床在最终用户处安装调试后,一般不需要修改参数。
在特殊的情况下,如需要修改参数,首先应输入参数修改的密码,所输入的密码正确,则可进行此权限级别的参数修改;否则,系统会提示密码输入错,不能进行该权限级别参数的修改。
(3)、主菜单与子菜单在华中HNC-21TF数控装置中主操作界面下,用Enter键选中某项后,若出现另一个菜单,则前者称主菜单,后者称子菜单。
菜单可以分为两种:弹出式菜单和图形按键式菜单,如图2.1.2所示。