高功率超高功率电弧炉炼钢技术
超高功率电炉无氧状态下冶炼低磷、硫钢
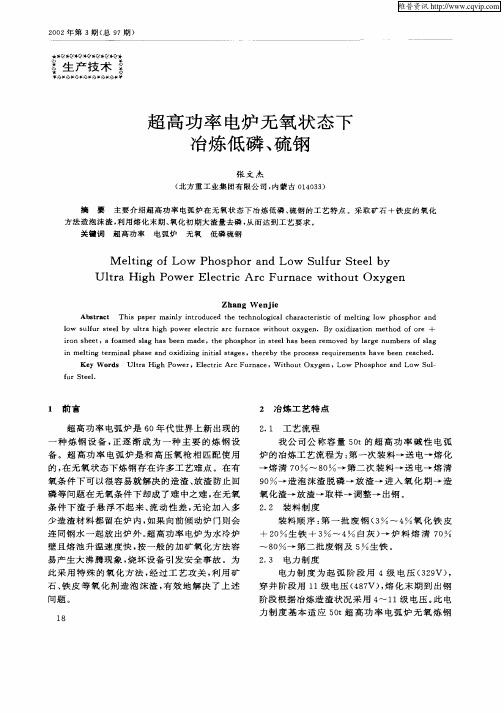
1 前 言
2 冶 炼 工 艺 特 点
2 1 工 艺 流 程 .
超 高 功 率 电弧 炉 是 6 年 代 世 界 上 新 出现 的 0
一
种 炼 钢 设 备 , 逐 渐 成 为 一 种 主 要 的 炼 钢 设 正
我 公 司 公 称 容 量 5 t的 超 高 功 率 碱 性 电弧 0
炉 的 冶 炼 工 艺 流 程 为 : 一 次 装 料 一 送 电一 熔 化 第 一 熔 清 7 ~ 8 一 第 二 次 装 料 一 送 电一 熔 清 O O 9 %一 造 泡 沫 渣 脱 磷 一 放 渣 一 进 入 氧 化 期 一 造 O 氧 化 渣 一 放 渣 一 取 样 一 调 整 一 出钢 。
大 型铸 锻 件
操 作 , 有 效 地 控 制 熔 池 温 度 , 脱 磷 操 作 创 造 能 为
问题 。
18
2 3 电力 制 度 . 穿 井阶段用 1 1级 电压 ( 8 V) 熔 化 末 期 到 出 钢 47 , 阶 段 根 据 冶 炼 造 渣 状况 采 用 4 1级 电 压 。 电 ~1 此
力 制 度 基 本 适 应 5 t 高 功 率 电 弧 炉 无 氧 炼 钢 0超
维普资讯
维普资讯
2 0 年 第 3期 ( 9 02 总 7期 )
★斗e斗辜斗 斗e斗e斗辜斗e
生产 技术 l
声 牛
超 高 功 率 电炉 无 氧 状 态 下 冶炼 低 磷 、 钢 硫
张 文 杰
( 方重 工业 集 团有 限公 司 , 蒙古 04 3 ) 北 内 103
壁且 熔 池 升 温 速 度 快 , 一 般 的 加 矿 氧 化 方 法 容 按
8 %一 第 二 批 废 钢 及 5 生 铁 。 O 电力 制 度 为 起 弧 阶 段 用 4级 电 压 ( 2 V) 39 ,
11.4 现代电炉炼钢技术
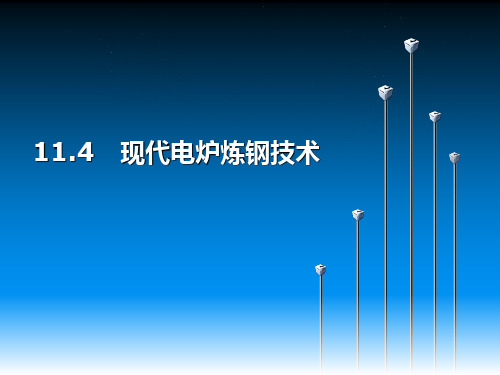
功率水平是UHP电炉的主要技术特征,它表示每吨钢占有的变压器额定容量,即
并以此来区分普通功率(RP)、高功率(HP)和超高功率(UHP)。
在UHP电炉发展过程,曾出现过许多分类方法,目前许多国家均采用功率水平表 示方法。1981年,国际钢铁协会(IISI)在巴西会议上,提出了具体的分类方法 ,见表11—8。
Strengths
Your strengths relative to competitors
Weaknesses
Your weaknesses relative to competitor
Your company slogan
Chart Documents
92%
70%
example1 example2 example3
变压器利用率指时间利用率与功率利用率,它反映了电炉车间的生产组织、管理 、操作及技术水平。 时间利用率:指一炉钢总通电时间与总冶炼时间之比,用Tu表示。 功率利用串:指一炉钢实际输入能量与变压器额定能量的比值,或指一炉钢总的 有功能耗与变压器的额定有功能耗的比值,用C2表示。
Your company slogan
Your company slogan
11.4.1 超高功率电炉的发展及其特 征
实际电网公害的抑制常采取闪烁、谐波综合抑制,即SVC装置一静止式动态力功补 偿装置(图11-13)。
Your company slogan
11.4.2 超高功率电炉相关技术
uHP电炉的出现和发展伴随着新技术的广泛采用。这些新技术包括uhp 电炉生产必须解决的问题,否则将限制生产的关键技术.如电极、耐火材料等 ;又包括高效、节能进一步降低成本的深化技术。这些都加速了电炉的更新换 代,确立了电炉在炼钢法中的地仿。 11.4.2.1 相关名词术语 (1)电炉的热点(区)与冷点(区)。在电炉炉衬的渣线水平上,距电极最近 点叫热点,而据电极最远点叫冷点。 电炉炉衬的侵蚀状况与丰要原因见表11-9。电炉炉体的更换,常常以2号 热点区炉衬的损坏程度作为依据。
浅谈超级电弧炉技术
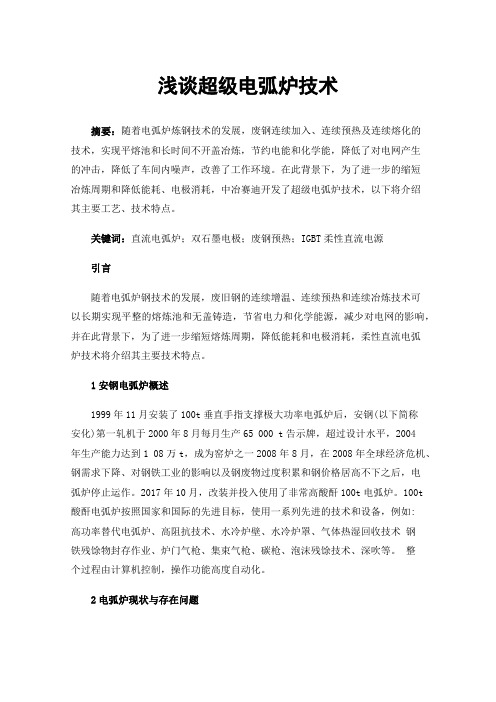
浅谈超级电弧炉技术摘要:随着电弧炉炼钢技术的发展,废钢连续加入、连续预热及连续熔化的技术,实现平熔池和长时间不开盖冶炼,节约电能和化学能,降低了对电网产生的冲击,降低了车间内噪声,改善了工作环境。
在此背景下,为了进一步的缩短冶炼周期和降低能耗、电极消耗,中冶赛迪开发了超级电弧炉技术,以下将介绍其主要工艺、技术特点。
关键词:直流电弧炉;双石墨电极;废钢预热;IGBT柔性直流电源引言随着电弧炉钢技术的发展,废旧钢的连续增温、连续预热和连续冶炼技术可以长期实现平整的熔炼池和无盖铸造,节省电力和化学能源,减少对电网的影响,并在此背景下,为了进一步缩短熔炼周期,降低能耗和电极消耗,柔性直流电弧炉技术将介绍其主要技术特点。
1安钢电弧炉概述1999年11月安装了100t垂直手指支撑极大功率电弧炉后,安钢(以下简称安化)第一轧机于2000年8月每月生产65 000 t告示牌,超过设计水平,2004年生产能力达到1 08万t,成为窑炉之一2008年8月,在2008年全球经济危机、钢需求下降、对钢铁工业的影响以及钢废物过度积累和钢价格居高不下之后,电弧炉停止运作。
2017年10月,改装并投入使用了非常高酸酐100t电弧炉。
100t酸酐电弧炉按照国家和国际的先进目标,使用一系列先进的技术和设备,例如:高功率替代电弧炉、高阻抗技术、水冷炉壁、水冷炉罩、气体热湿回收技术钢铁残馀物封存作业、炉门气枪、集束气枪、碳枪、泡沫残馀技术、深吹等。
整个过程由计算机控制,操作功能高度自动化。
2电弧炉现状与存在问题电弧炉的特点是能量的快速传递、多元性、电弧炉的温度;它们广泛应用于冶金、冶炼、熔炼和矿物热等领域以及一些新的材料部门。
电弧炉是一种快速、大规模地将电能转化为热能并传递给加热材料的环境。
电弧炉用户感到电能消耗巨大,电费占产品成本的很大一部分,甚至是价格竞争的一个主要因素减少电弧炉的能耗和提高电耗效率是电弧炉用户的期望。
如果电弧炉控制得当,能源消耗足够低,钢铁工业就有可能从长期矿石加工转变为短期废钢加工+降低铁粉(氢),这可能导致钢铁工业发生重大变化这远远超出了想象。
超高功率电弧炉的单渣法炼钢工艺
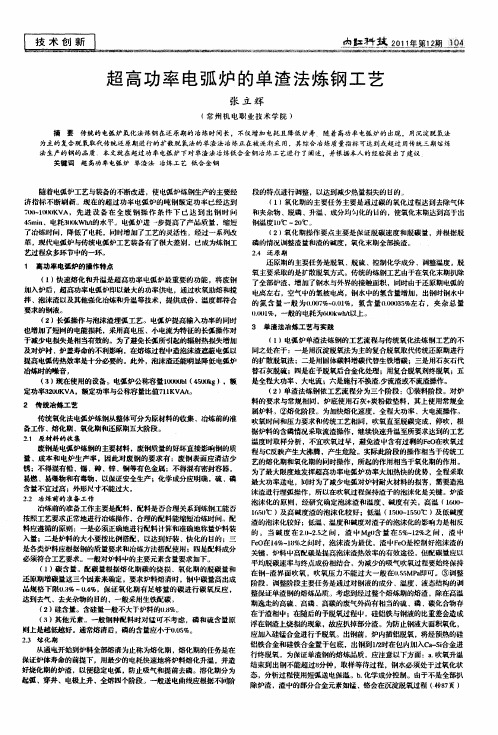
随着电弧炉工艺与装 备的不断改进 ,使 电弧炉炼钢生产的主要经
济指标 不断刷新 现 在的超过 功率 电弧 炉的吨 钢额定功 率已经达 到 71 I I V o) tI A,先 进 没备 在 全废 钢操 作 条 件 下 已 达 到 出 钢 时 『 一  ̄) K 廿 J
段的特点进 行渊整 ,以达到减少热量损失的 目的. , ( ) 1 氧化期的 主要 任务主要是通过碳 的氧化过程达到 去除气体 和夹杂物 、脱磷 、升温 、成分均 匀化的 目的 ,使氧化末期达到高于出
为主的复合脱 氧取代传统还原期进行的扩散脱氧法 的单渣 法冶炼正在被逐渐采 用,其综合 冶炼质量指标可达到或超过用传统三期 熔炼 法生产 的锏的品质 ,本文就在超过功 率电弧炉 下对单渣法冶炼低合金铜冶炼工艺进行 了阐述 ,并根据本人的经验提 出了建议 关键词 超 高功率电弧 炉 单渣 法 冶炼工艺 低合金钢
3 单渣法冶炼工艺与实践
( )长弧操 作与泡沫渣埋弧工 艺。电弧炉提 高输入功率的 同时 2 也增j了短嘲的电能损耗 ,采用高电压 、小 电流 为特征 的长弧操作对 I I I 于减少电损失是相当有效的。为了避 免长弧所 引起 的辐射热损失增 加 及对炉衬 炉盏寿命的不利影响。在熔炼过程 中造泡沫渣遮蔽 电弧 以
22 冶炼前的准备工作 .
冶炼前的准 备工作主要是配料 。配料是否合理 关系到炼钢工能否 按照工艺要求正常地进行冶炼操作 ,合理 的配料能缩 短冶炼时问 配 料应遵循的原则 :一是必须正确地进 行配料 计算和准确地 称量炉料装 入量 ;二是炉料的大小要按比例搭配 ,以达到 好装 、 快化 的 目的 ;三 是各类炉料应根 据譬的质量要求 和冶炼 方法搭配使 用;四是配料 成分 I 畸 必须符合工艺要求 一般对炉料 中的主要元素含量要求如下
电弧炉炼钢——第五章 超高功率电弧炉和直流电弧炉

(3)短网 (4)无功功率静止式动态补偿 (5)计算机的应用
二.直流电弧炉
1.直流电弧炉的结构特点 (1)炉体结构 (2)底电级 A 多根风冷底电极(MAN型电极) B 单根水冷底电极(CLECIM型底电极) C 整体炉底电极(ASEA型底电极) (3)直流电弧炉的电源 A 变压器 B 整流设备
C 直流电抗器 (4)直流电弧炉的电弧特征 A 燃烧稳定 B 石墨电极和炉底电极的级性是固定的; 2.直流电弧炉的冶炼特点 (1)熔化特点 (2)出钢 3.直流电弧炉的优越性 (1)电极的消耗明显降低 (2)耐火材料的消耗降低
(3)降低电极消耗和缩短冶炼时间; (4)电压闪烁程度小,对电网干扰小; (5)噪音低; (6)熔池温度均匀; (7)操作费用低;
三.计算机的应用
1.计算机控制 2.可编程序控制器的应用 3.电弧炉自动化的扩展功能
一.超高功率电弧炉的功率水平:变压器的额定功率与 炉衬公称容量或实际出钢量之比; 超高电弧炉:700-1000kwh/t; (2)高的电弧炉变压器最大功率和时间利用率;
(3)较高的电效率和热效率; (4)较低的电弧炉短网电阻和电抗,且短网
第二篇 电弧炉炼钢
主要内容
❖ 绪论 电炉炼钢及其发展 ❖ 第一章 电弧炉的电器设备 ❖ 第二章 电弧炉炉体构造与炉衬 ❖ 第三章 电弧炉炼钢原材料 ❖ 第四章 碱性电弧炉冶炼工艺 ❖ 第五章 超高功率电弧炉和直流电弧炉 ❖ 第六章 典型钢种冶炼 ❖ 第七章 电炉新技术、新工艺
第五章 超高功率电弧炉和直流电弧炉
电弧炉炼钢

二、电弧炉炼钢的特点
1、温度高而且容易控制 2、可以制造还原性气氛,有利于去硫 3、热效率高,可达65%以上 4、冶炼设备简单,投资少
缺陷: 1、耗电量大 500~700kwh/t 2、成品钢中H、N含量偏高 3、炭质电极可能使钢液增碳,给低碳钢冶炼带来困难
❖ 三、长流程与短流程 ❖ 长流程: 铁矿石 高炉 铁水 转炉 钢水 浇注
钢坯 轧钢 钢材 ❖ 短流程: 废钢等 电炉 钢水 浇注 轧钢 钢材
废钢—电炉炼钢流程,具有流程短,设备布置、工艺衔接紧凑,投入产出 快。
§1—2 电弧炉的主电路及主电路上 的电器设备
一.电弧炉的主电路
❖ 由高压电缆线至电极的电路称为电弧炉的 主电路。
1.主电路组成
❖ 隔离开关、高压断路器、电抗器、电炉变 压器、低压短网等。
2.主电路作用 ❖ 从高压电网取得高压电能,转变为低电压、
大电流输送到电极。
二.主电路上的电器设备
1.隔离开关
❖ 作用:电炉设备检修时断开高压电源,或 进行切换操作。
❖ 结构:三相刀闸开关。
❖ 特点:无灭弧装置,必须在无负载时接通 或切断电路。
❖ 开关操作顺序:送电时先合上隔离开关, 后合上高压断路器;停电时先断开高压断 路器,后断开隔离开关。
❖ 操作机构:手动、电动、气动三种。
2.高压断路器
❖ 作用:是电弧炉的操作开关,用以切断电 炉变压器的空载电流、工作电流和炉中发 生短路时的工作短路电流。
2.电弧柱中气体电离的原因 ⑴ 阴极斑点的热电子发射。 ⑵ 电场电离。 ⑶ 热电离。 3.消电离的两种形式 ⑴ 扩散。 ⑵ 复合。
90 t超高功率电弧炉短流程生产P5钢的工艺实践
!"#$%&$’ () *&+&,)-(. !"($’// .&%0 "$1 20! ’#) %( !"(32$’ !; /%’’=* -+5)*’ =*+,2 >*5?’* @)., A’, &* B’5,2?’.
( :+,2+,2 >15*C @).,2D* E15, F &/..0 @56 ,A/D6 ,@).,2D* <#$$<<)
[#4516781] E,/15D*(.D ’, /). C+C.1 ’G /). H’,’IJ05K H.0/’,2 C15(.GG 5J :; &/..0 K’/) /). "$/ L=: MN8 +D5C/.D 93 :+,2+,2 >15*C @).,2D* E15, F &/..0 @56 ,A/D6 O+G.D 5, /). +,+03G’G 5J +00 /). (1’/’(+0 /.(),’(+0 ’GG*.G,C15C.1 H.+G*1.G +1. /+P., J51 /.(),5052’(+0 (5,/150 5J G*() C5’,/G +G ’, Q C15(.GG : (5,/.,/,+DD’/’5, 5J +0053 .0.H.,/G, H.0/’,2 /.HC.1+/*1.,().H’(+0 (5HC5G’/’5, )5H52.,.’/3 +,D (5,G’G/.,(3 5J 1.J’,.D 0’R*’D G/..0, R*+0’/3 5J /). 0+D0. J51 1.J’,’,2 +,D R*+0’/3 5J /). ’,25/, ./( 6 NG + 1.G*0/, /). :; &/..0 ’G G*((.GGJ*003 C15D*(.D K’/) /). H’,’IJ05K C15(.GG,+,D +00 /). C15C.1/3 D+/+ 5J /). G/..0 )+S. 9.., *C /5 /). 1.R*’1.H.,/G +G GC.(’J’.D ’, +CC0’(+90. /.(),’(+0 G/+,D+1D6 [9:; <=6>5] L=: MN8, H’,’IJ05K C15(.GG, :; G/..0, H.0/’,2 C15(.GG 大批量生产的要求。超高功率电弧炉短流程的优势 是电弧炉炉容量大, 冶炼周期短, 生产效率高。但对 于冶炼合金含量高的钢种, 如果工艺技术措施控制 不当, 会导致生产周期长, 不能充分发挥其优势, 因 此国内用超高功率电弧炉短流程大批量生产 :; 钢 的厂家甚少。本文结合实际生产情况, 对超高功率 电弧炉短流程生产 :; 钢的冶炼工艺技术控制措施 进行探讨。 ! :; 钢的技术条件及要求 ! 6# 技术标准 采用 N&T- NUU; V NUU;- 标准。 ! 6! 化学成分 对 :; 钢的化学成分要求列于表 # 。
高功率超高功率电弧炉炼钢技术
另外,电熔氧化铝也是很好的坩埚材料,氧化铝为中性的耐火材料, 其耐火度和抗热冲击性能都较好。使用电熔镁砂与电熔氧化铝配合制 作的大吨位感应电炉的坩埚的使用寿命较长。
4.3感应电炉炼钢设备及工艺简介
4.3.1 炼钢用感应电炉的主要技术性能 通常用于炼钢的感应电炉为无芯感应电炉。
电流频率根据电炉容量选用高频感应电炉、 中频感应电炉与工频感应电炉。 4.3.1.1 高频感应电炉 高频感应电炉使用的电流频率一般在200~ 300kHz,电炉容量一般在10~60kg。这类 电炉常用于科学实验的少量合金熔炼。
4.3.2.2 坩埚的烧结
烧结坩埚一般采用供电烘烤法。用钢板或 铸钢板制作模样在烘烤时,由于感应发热 可起到烘烤和烧结坩埚的作用。为此,在 钢模样上可钻些φ3㎜的小孔,以增强模样 的发热能力,加快烘干和烧结的速度。第 一次开炉时,最好连续多熔化几炉,以便 使坩埚充分烧结。每次开炉熔化后,应将 炉盖盖好,以防坩埚急剧受冷而产生裂纹。
4.2.4 无渣出钢技术
电弧炉实现超高功率化后,如果还原期继续仍在电弧炉中 进行,会造成变压器功率的浪费。若将还原期转移到精炼 炉中进行,氧化渣就不能进入精炼炉。因此,采用无渣出 钢技术非常必要。目前,常使用的无渣出钢技术为偏心炉 底出钢(EBT),从而导致留钢留渣操作。
无渣出钢避免了电弧炉内的氧化性炉渣随着钢水进入钢包 内,为下一步进行炉外精炼进行脱硫、脱氧及合金化创造 非氧化性条件,从而提高精炼炉内的脱硫、脱氧效果,提 高合金收得率,利于钢中化学成分的稳定;无渣出钢杜绝 了炉内氧化性炉渣进入钢包内,从而避免了氧化渣对钢包 衬的侵蚀,提高了包衬的寿命;无渣出钢杜绝了炉内氧化 性炉渣进入钢包内减少了精炼时加入的造渣量,从而有利 于钢包吹氩或搅拌强度的提高。无渣出钢为冶炼超低磷钢 提供了有利条件,并利于熔化时热量的传递和熔池的快速 形成。
电弧炉炼钢工艺设备(一)
4 电弧炉炼钢工艺设备4.1 废钢加工设备常见的废钢加工方式为剪切、打包和破碎处理。
目前公司废钢料场对废钢的加工方式主要有三种:废钢剪切、废钢打包以及废钢人工火焰切割。
人工火焰切割方式较为简单,即按照电弧炉冶炼要求将废钢切割为合格尺寸。
废钢剪切和打包则是利用专用设备对废钢进行加工处理,达到减小废钢尺寸及增加炉料堆比重的目的,下面对废钢加工方设备做简要介绍。
4.1.1 废钢打包机废钢打包设备是将废钢放在钢结构箱体内,采用液压驱动进行三维方向强行挤压处理,最终将分散的、堆比重小的废钢加工为堆比重大的单一包块。
废钢打包机见图4.1。
图4.1 废钢打包机料场的废钢打包机是1990年从德国LINDEMANN公司引进,1991年投入使用。
设备主要由滑动门机构、进给压力机构、压盖机构、中间压力机构、最终压力机构五个部分组成。
1)滑动门机构是依靠安装于门上的液压缸控制门在滑道上垂直动作,在打包过程中,门是关闭的。
打包结束,门开启以使包块可被推出;2)进给压力机构依靠水平安装的液压缸控制进给压力平台,以将废钢推进打包室的同时进行水平轴向挤压,进给压力平台的动作由引导机构引导,进给压力平台上设有剪切装置,多余的废钢在进入打包室时将被剪切掉,防止工作过程中造成机械卡阻;3)压盖机构由液压缸驱动压盖动作,可将露出箱体的废钢压入箱体内,同时防止加工过程中废钢的弹出;4)中间压力机构由垂直安装的液压缸驱动,对废钢进行垂直挤压,通过调整安装在机构上的限位开关,可调整垂直挤压缓冲及停止位置;5)最终压力机构依靠水平安装的液压缸,利用最大工作压力控制最终压力平台,对废钢在打包室内进行水平径向挤压;分散的废钢在受到三个方向的强行挤压后最终形成单一包块。
液压系统动力部分由4台90kw交流电机驱动8台轴向柱塞泵,系统最大工作压力达315bar,最大流量达1836L/min,最大挤压力可达1050tf,成品包块截面尺寸为800×800mm,厚度根据所加工废旧金属的多少有所变化。
超高功率电弧炉炼钢新技术和工艺操作要点
超高功率电弧炉炼钢新技术和工艺操作要点广告现代电炉炼钢生产技术手册作者:王新江主编当当1、快速熔化与升温操作快速熔化和升温是超高功率电弧炉最重要的功能,将第1篮预热废钢加入炉后,此过程即开始进行。
超高功率电弧炉以最大的功率供电,氧一燃烧嘴助熔,吹氧助熔和搅拌,底吹搅拌,泡沫渣以及其他强化冶炼和升温等技术,为二次精炼提供成份、温度都符合要求的初炼钢液。
2、脱磷操作脱磷操作的三要素,即磷在渣一钢间分配的关键因素有:炉渣的氧化性(%TFeO)、石灰含量(%CaO)和温度。
随着渣中%TFeO. %CaO的升高和温度的降低,磷在渣钢间的分配比(% (P) /% [P])明显提高。
采取的主要工艺有:强化吹氧和氧一燃助熔,提高初渣的氧化性;提前造成氧化性强、氧化钙含量较高的泡沫渣,并充分利用熔化期温度较低的有利条件,提高炉渣脱磷的能力,及时放掉磷含量高的初渣,并补充新渣,防止温度升高后和出钢时下渣回磷,采用氧气将石灰与萤石粉直接吹入熔池,脱磷率一般可达80%,脱硫率<50%:采用无渣(或少渣)出钢技术,严格控制下渣量,把出钢后磷降至最低。
一般下渣量可控制在2kg。
出钢磷含量控制应根据产品规格、合金化等情况综合考虑,一般P<O. 01%。
3、脱碳操作配碳可以用高碳废钢和生铁,也可以用焦炭或煤等含碳材料。
后者可以和废钢同时加入炉内,或以粉状喷入。
配碳量和碳的加入形式、吹氧方式、供氧强度及炉子配备的功率(决定周期时间)关系很大,需根据实际情况确定。
炉料中有一定的碳含量与脱碳反应的作用:熔化期吹氧助熔时,碳先于铁氧化,从而减少了铁的烧损;渗碳作用可使废钢熔点降低,加速熔化;碳氧反应造成熔池搅拌,促进了钢一渣反应,有利于早期脱磷:在精炼升温期,活跃的碳氧的反应,扩大了钢一渣界面,有利于进一步脱磷,有利于钢液成分和温度的均匀化和气体、夹杂物的上浮;活跃的碳氧反应有助于泡沫渣的形成,提高传热效率,加速升温过程。
- 1、下载文档前请自行甄别文档内容的完整性,平台不提供额外的编辑、内容补充、找答案等附加服务。
- 2、"仅部分预览"的文档,不可在线预览部分如存在完整性等问题,可反馈申请退款(可完整预览的文档不适用该条件!)。
- 3、如文档侵犯您的权益,请联系客服反馈,我们会尽快为您处理(人工客服工作时间:9:00-18:30)。
2021/3/7
5
4.3感应电炉炼钢设备及工艺简介
4.3.1 炼钢用感应电炉的主要技术性能 通常用于炼钢的感应电炉为无芯感应电炉。
电流频率根据电炉容量选用高频感应电炉、 中频感应电炉与工频感应电炉。 4.3.1.1 高频感应电炉 高频感应电炉使用的电流频率一般在200~ 300kHz,电炉容量一般在10~60kg。这类 电炉常用于科学实验的少量合金熔炼。
2021/3/7
9
4.3.2.1 坩埚的打结
② 石棉绝缘层
为了保证感应器与坩埚内 部的炉料之间绝缘性并减 少坩埚内部热量向外部扩 散,在靠近感光器制有一 层用石棉板(石棉布或玻 璃丝布)围成的绝缘筒, 同时,坩埚底部也用2~ 3层石棉板做成隔热片, 以减少坩埚底部热量散失。 如图1-45所示。
2021/3/7
1
ቤተ መጻሕፍቲ ባይዱ
4.2.1 水冷炉壁和水冷炉盖技术
水冷炉壁和水冷炉盖技术解决了在高功率操作时,电弧对 炉壁和炉盖强烈辐射引起的耐火材料熔炼损耗问题。
现代电弧炉的平均水冷炉壁面积已达70%,水冷炉盖的 面积已达85%。采用水冷炉壁后,炉壁的使用寿命已超 过1000炉次。将管式水冷件用于水冷炉盖,可使炉盖寿 命达到4000炉次。尽管水冷技术的使用,使电弧炉的热 量损失增加了5%~10%,但使耐火材料的成本和喷补成 本节约了50%~70%,由于取消了渣线上部的耐火材料 修补作业,大大减轻了操作人员的劳动强度。同时,由于 停炉时间大幅度减少,使生产率提高8%~10%,每吨钢 液电极消耗量降低0.5kg,生产成本下降5%~10%.因 此,总体效益非常显著。
2021/3/7
6
4.3感应电炉炼钢设备及工艺简介
4.3.1.2 中频感应电炉 中频感应电炉使用工业用电流频率为1000~
2500Hz。中频感应电炉的容量一般为50~ 1000kg。其主要技术性能可参考有关手册。 4.3.1.3 工频感应电炉 工频感应电炉使用工业用电的电流频率(我国为 50Hz,有些国家为60Hz)的电源。使用的电流容 量为100~10000kg,其主要技术性能可参考有关 手册。
2021/3/7
3
4.2.3 氧-燃烧嘴
超高功率电弧炉熔化时靠近炉壁处的两根
电极之间的冷区炉料熔化困难,为了加快 熔化,开发的氧-燃烧嘴技术解决了上述难 题。现代大型电弧炉均配备氧-燃烧嘴,起 到了消除“冷区”和辅助熔化的作用。因
此,电弧炉的综合熔化功率达到每吨钢液 1000kw以上。对于大型电弧炉,氧-燃烧 嘴每吨钢消耗1m3氧气相当于每吨钢节省 3~5kw.h的电能,并且缩短熔化时间 2min。
2021/3/7
2
4.2.2 泡沫渣埋弧技术
超高功率电弧炉的输入电流过大会引起电量消耗 及电极消耗量的增加。使用工作电流的选择成为 关键问题。因此,输入高功率依靠长弧的高电压 来实现。长弧操作不仅提高功率因数,但也增大 电弧热辐射损失和炉壁的热负荷。泡沫渣技术就 是在不增加渣量的前提下使炉渣厚度增加,由于 向渣中喷入碳粉和氧气而产生CO气体,在熔池表 面形成泡沫渣,使电弧埋入渣层。泡沫渣技术的 采用取得明显效果:功率因数由0.63提高到0.88, 热效率提高30%~70%,电压和电流波动明显减 小,并加快了电弧热量向熔池传递。
4.2 高功率、超高功率电弧炉炼钢技 术
从20世纪60年代起,高功率和超高功率大 型电弧炉已在全世界范围内得到广泛普及。 超高功率技术给电弧炉炼钢带来了一系列 变化,例如采用水冷炉壁和水冷炉盖、泡 沫渣、氧燃烧嘴、炉底出钢等技术,超高 功率技术本身也由原来的大电流低电压的 粗短弧操作改变成大电流高电压的长弧操 作。
2021/3/7
4
4.2.4 无渣出钢技术
电弧炉实现超高功率化后,如果还原期继续仍在电弧炉中 进行,会造成变压器功率的浪费。若将还原期转移到精炼 炉中进行,氧化渣就不能进入精炼炉。因此,采用无渣出 钢技术非常必要。目前,常使用的无渣出钢技术为偏心炉 底出钢(EBT),从而导致留钢留渣操作。
无渣出钢避免了电弧炉内的氧化性炉渣随着钢水进入钢包 内,为下一步进行炉外精炼进行脱硫、脱氧及合金化创造 非氧化性条件,从而提高精炼炉内的脱硫、脱氧效果,提 高合金收得率,利于钢中化学成分的稳定;无渣出钢杜绝 了炉内氧化性炉渣进入钢包内,从而避免了氧化渣对钢包 衬的侵蚀,提高了包衬的寿命;无渣出钢杜绝了炉内氧化 性炉渣进入钢包内减少了精炼时加入的造渣量,从而有利 于钢包吹氩或搅拌强度的提高。无渣出钢为冶炼超低磷钢 提供了有利条件,并利于熔化时热量的传递和熔池的快速 形成。
表1-30 感应电炉酸性坩埚材料组成
材料名称
炉衬材料
炉领材料
硅砂粒度/ ㎜
5~6
2~3
0.5~1 硅石粉
1~2
0.2~0.5
硅石粉
配比(质量 分数,%)
25
20
30
25
30
50
2021/3/7
20
8
4.3.2.1 坩埚的打结
打结炉衬用的材料可使用质量分数1.7~2.0%的硼酸做粘结剂。对 硼酸化学成分的要求是:ω(B2O3)≥98%;ω(水分)≤0.6%。 硼酸的粒度应小于5㎜。将硅砂与硼酸干混,不加湿润剂来配制炉衬 材料。打结坩埚时,采用干法打结,以便保证炉衬质量。在感应圈以 上的炉领(坩埚上口)部分采用强度较高的炉领材料打结,使用粒度 较细的硅砂或硅石粉。另外加质量分数为10%的水玻璃或用质量分 数为20%的粘土加少量水玻璃做粘结剂。
2021/3/7
7
4.3.2 感应电炉炼钢工艺 4.3.2.1 坩埚的打结
坩埚材料一般分为酸性坩埚材料和碱性坩埚材料。
酸性坩埚材料以硅砂作为耐火材料,对化学成分的要求为ω (SiO2)=90%~99.5%;杂质含量:ω(Fe2O3) ≤0.5%,ω(CaO)≤0.25%,ω(Al2O3)≤0.2%,ω(水) ≤0.5%。对粒度的要求见表1-30。
碱性坩埚使用镁砂做耐火材料。镁砂分为烧结镁砂和电熔镁砂。电熔 镁砂抗热冲击性能比烧结镁砂好,但价格昂贵。使用镁砂须经磁选, 清除其中含铁的杂质,以保证坩埚的绝缘性。
另外,电熔氧化铝也是很好的坩埚材料,氧化铝为中性的耐火材料, 其耐火度和抗热冲击性能都较好。使用电熔镁砂与电熔氧化铝配合制 作的大吨位感应电炉的坩埚的使用寿命较长。