双色注塑实例
双色模潜伏进浇设计案例
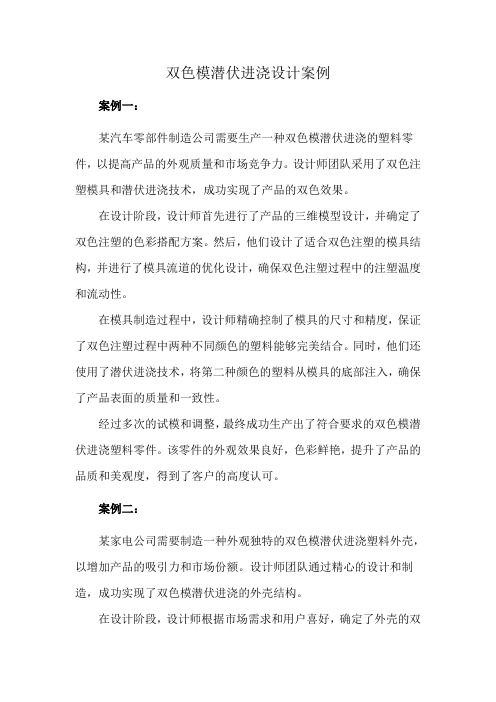
双色模潜伏进浇设计案例案例一:某汽车零部件制造公司需要生产一种双色模潜伏进浇的塑料零件,以提高产品的外观质量和市场竞争力。
设计师团队采用了双色注塑模具和潜伏进浇技术,成功实现了产品的双色效果。
在设计阶段,设计师首先进行了产品的三维模型设计,并确定了双色注塑的色彩搭配方案。
然后,他们设计了适合双色注塑的模具结构,并进行了模具流道的优化设计,确保双色注塑过程中的注塑温度和流动性。
在模具制造过程中,设计师精确控制了模具的尺寸和精度,保证了双色注塑过程中两种不同颜色的塑料能够完美结合。
同时,他们还使用了潜伏进浇技术,将第二种颜色的塑料从模具的底部注入,确保了产品表面的质量和一致性。
经过多次的试模和调整,最终成功生产出了符合要求的双色模潜伏进浇塑料零件。
该零件的外观效果良好,色彩鲜艳,提升了产品的品质和美观度,得到了客户的高度认可。
案例二:某家电公司需要制造一种外观独特的双色模潜伏进浇塑料外壳,以增加产品的吸引力和市场份额。
设计师团队通过精心的设计和制造,成功实现了双色模潜伏进浇的外壳结构。
在设计阶段,设计师根据市场需求和用户喜好,确定了外壳的双色配色方案。
然后,他们使用CAD软件进行了三维模型设计,并进行了模具结构和流道的优化,确保了产品的一致性和质量。
在模具制造过程中,设计师采用了高精度的数控机床和先进的加工工艺,保证了模具的尺寸和精度。
他们还使用了潜伏进浇技术,将第二种颜色的塑料从模具的背面注入,确保了外壳表面的色彩和质量。
经过多次的试模和调整,最终成功生产出了符合要求的双色模潜伏进浇塑料外壳。
该外壳的设计独特,色彩鲜艳,使产品在市场上具有差异化竞争力,得到了用户的喜爱和认可。
双(多)色塑料注射成型4.
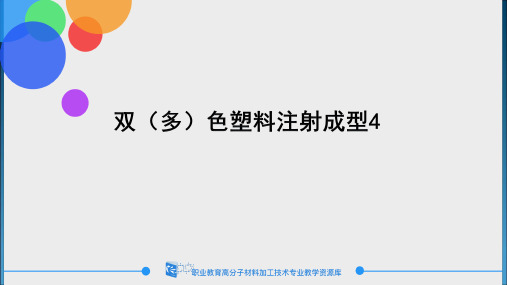
2、双色注射模结构设计 (3)成型零件结构设计 选材:因生产批量大,塑件外观要求高,成型零件的加 工要求较高,宜选用性能良好的预硬钢P20制造镶块,并 预硬化处理至35~37HRC。 结构:塑件外表面由动、定模大镶块整体成型,而内孔 部分采用局部镶拼结构,以利于内孔成型镶块表面加工。 在定、动模镶块的四角设置锁扣精定位结构,可提高动、 定模镶块的合模精度,并有利于模具制造时动、定模镶块 在模外的修配。
2、双色注射模结构设计 (2)模具浇注系统设计 浇口数量选择:因第一色塑件的4个内面板两两相连, 内面板之间仅由2.5mm宽、0.3mm厚的薄片与梯形凸台连 接,塑料熔体充模较困难,宜采用四点浇口进料,以保证 各型腔达到较好的流动平衡。 第二色塑件结构与第一色塑件有类似的特点,所以也采 用四点浇口进料。 浇注系统尺寸确定 • 因塑件的注塑量较小,浇口尺寸不宜太大,依经验选用 点浇口的内浇口尺寸为φ1.0mm,分流道截面为梯形,最 大宽度4mm,深度3mm,侧面斜度取8°。
2、双色注射模结构设计 (1)分型面与型腔数确定 1)分型面选择
2、双色注射模结构设计 (1)分型面与型腔数确定 2)型腔数的选择 因塑件生产批量较大,且为中小型件,塑件结构较为简 单,可选用一模多腔成型。 但模腔数太多将造成冷却管路连接困难,且模具尺寸受 注射机装模空间限制,不宜太大;所以确定采用一模两腔 的成型方案。
四、双(多)色塑料注射成型模具设计实例
2、双色注射模结构设计 双色注射模因生产所使用的双色注射机类型和半成品件 的换位方式的不同,其模具的浇注系统和各部分的结构会 不同,设计时应注意模具与设备的匹配问题。 (1)分型面与型腔数确定 1)分型面选择 控制开关面板塑件为扁平件,其分型面位置通常选在塑 件最大轮廓面的边界上。 由于双色塑件第一色注射成型的半成品塑件需在下一次 注射前旋转换位至第二色注射工位,它要求两种颜色塑件 的分型面应一致,故分型面应选择在二者的公共面上。
双色注塑

双射注塑一.简介双射注塑(Bi-color injection)顾名思义就是一个部件用两种塑胶注塑来实现。
广义的双射注塑包括over molding,通过普通的注塑机,两次注塑来实现,狭义的双射注塑是指利用双射注塑机,将两种不同的塑料在同一机台注塑完成部件,常见的是旋转式的。
前者对设备要求不高,但是生产效率低下,基本只适用于要求不高度软、硬胶两种材料的成型1,后者的适用范围和产品质量好,生产效率高,是目前的趋势。
我们主要介绍以双射注塑机注塑的双射注塑。
这样我们首先从认识双射注塑机和双射注塑模具。
注塑机的动模侧的转盘如下图所示,上面可以固定两个模具的动模,有两组和顶杆,它可以在开模后,先是将第二射的动模产品顶出,机械手取出产品,接着将上面固定的两套模具的动模旋转,从而将第一射完成的产品放到了另外一边,准备第二次注射,而第一射的动模侧换成了空的。
周而复始,产品不断完成注塑。
注意点是,第一次注塑时候,第二射是将整个模腔填满,注意脱模。
当然注塑机在定模侧拥有两个料管,分别注塑不同的塑料。
双射注塑的模具拥有自身的特点:1.动模是一样的,因为是旋转的,需要交换的,所以必须是一模一样的。
所以先成型的是动模侧的先成型的一般都是靠动模侧的(有特例,成型时候型腔可以不一样2)2.模具的第一射的流道注塑完成后,是不能留在模具上的,最好是热浇道,不然也是可以用机械手抓取的,最差的也是潜伏类浇口,可以自动脱落,否则会浇口在上面第二射没法阖上模具。
3.产品两次射出,产品开模后,第一射必须留在动模侧,这个比较好理解,如果留在了定模侧,旋转就没用了,就变成了单色注塑机了,就一般情况而言,一般都是选择将两射的产品都是留在动模侧的,所以模具需要开闭器、拉杆等实现顺序开模,先拉开定模侧,在定模侧需要加顶出机构,4.两组冷却系统,因为双射注塑的要求两种材料不一样,原则上要求第一射的材料的温度比第二射高出60度,可以根据实际情况而定,这个后面再讨论,因为材料不一样,模具的模温不一样,所以需要配备两套冷却系统。
双色注塑技术说明

塑料加工工艺之双色注塑技术2009-07-02 09:03:00 新闻来源:宁波塑机网近年来,国内部分塑料制品业者在严峻的经营环境下,纷纷朝向大型高附加价值产品及特殊双色制品发展。
而从近期中国展会来看,多色成型技术经常是展会亮点,展出双色机厂商成倍数增加,也显示双色机在中国日渐蓬勃发展。
华大:“共塑”注塑华大机械有限公司是中国大型的生产注塑机的厂家之一,也是大陆首家生产研制多物料注塑机的企业。
华大的多物料注塑机采用“共塑”注塑方式比传统法可节省达50%的生产时间,能够减省达20%或以上的废/次品损耗量,且产品质量稳定,还能制造如立体穿透、底面包围等复杂制品,在国内多物料注塑机行业处于领先水平。
与国内厂家双物料平行结构不同,华大的多物料注塑机是按欧洲先进思路设计,采用直角式结构,独立的副射台设置马达、油泵、射胶装置及控制系统,使机器随时能变回单物料生产方式,简单方便。
锁模部分,模板全部经有限元分析,采用优质的球墨铸铁精密制造而成,二板、尾板采用铰耳连接,减少累计误差,增加整机刚性,保证了机板的使用寿命。
五点式开合模结构,机铰经优化设计,运行平稳,结构紧凑,适合各类双物料模具。
注射部分采用耐磨氮化熔胶螺杆及料筒,电子尺控制射胶位置,射胶流量阀带位置反馈,确保注射速度的精确性和重复性。
副射台动作有同步或不同步等多种形式,供用户选用。
采用日本原装三菱控制系统,工作状态以图形显示,方便监控生产过程,数据输入使用触摸键,增加系统的可靠性,10段射胶,熔胶保压设定,5段螺杆转速及背压控制,适合精密注射。
此外,华大还可根据客户模具要求特别编写程序。
在FT多物料系列,华大自主研制的双物料共塑技术已达国际先进水平。
同时,多物料系列注塑机也正在朝更低成本、更高速度、更高精密,更低能耗的方向不断改进。
欧美厂商产品已提升至几个基本成型技术的“组合”呈现,如:双色成型加模内贴标(IML)、双色成型加模内组合(IMA)、双色成型加迭层模(Stack Mold)、双色成型加IML加IMA加迭层模、双色成型加夹层射出等。
双色注射模具设计10个实例(经典案例)

双⾊注射模具设计10个实例(经典案例)这是⼀款⼿机护套,如下图产品分析:此款为某品牌⼿机的外圈护套,由⼆种塑料(PC+TPE)组成。
由于要求外形美观光滑,分模线必须做在内侧圆弧切点,所以外模要四⾯滑开,再看内侧,四周全部是内扣的,必须全⽅位内抽芯,也就是俗称的“爆炸芯”。
关于“爆炸芯”的模具结构,假如是普通的注塑模具,已经有⾮常经典的机构,我下⾯将有详细的介绍。
现在问题是双⾊模具,有⼆组动模和⼆组定模,⼆组动模的所有部件是完全⼀致的,要在双⾊注塑机的转盘上进⾏180度旋转,⼆种不同的塑料分别射进模腔,注射硬胶(PC)时动模的顶出机构和抽芯机构不动作,再注射软胶(TPE)并开模后,对准软胶料筒的⼀侧的动模的抽芯机构和顶出机构才开始动作,将完整的双⾊制品顶出。
由于动模旋转后,交换⼜合模后的浇⼝必须在同⼀位置,所以软胶和硬胶的浇⼝的处理显得令⼈困惑。
由于模具必须四周都要进⾏“内外同抽”,内、外滑块怎样排列,轨道设置在哪⾥?这个问题同样有被逼⼊墙⾓的感觉。
且不谈模具滑块机构的复杂性,我们从双⾊模具的基本原理来考虑,硬胶部分的成型和内外同抽机构是⼀定要设置在定模⼀侧的,软胶部分的成型机构也要设置在定模。
⽽且这个部分是由内外同抽的机构组成的凸起插⼊到动模的凹槽中。
转盘旋转180度后,这组凸起刚好插⼊到另外⼀个动模的凹槽中。
也就是说,⼆个定模上的由内外同抽滑块组成的凸起的外部形状和尺⼨是完全相同的。
仅仅是成型软胶和硬胶的型⾯不同⽽已。
问题的难点是,这个凸起会分成上下⼆层,⼀层向外移动,另⼀层向内移动,也就是俗称的“内外同抽”,合成的凸起的侧⾯是⼀个统⼀的斜⾯,但是,传统的滑块必须要有滑动轨道等必要的条件,怎样设置轨道?这便成了本案例的核⼼问题。
我是这样设置动模部分的凹槽和定模部分凸起的。
动模的凹槽是这样的。
下⾯我们来探讨定模部分的设计1.01定模内外同抽的设计基本机构是这样的当A板和定模底板分开35mm后拨块拨动内滑块,同时通过齿轮的传动,外滑块向外移动。
双色注塑产品设计双色注塑产品设计_图文
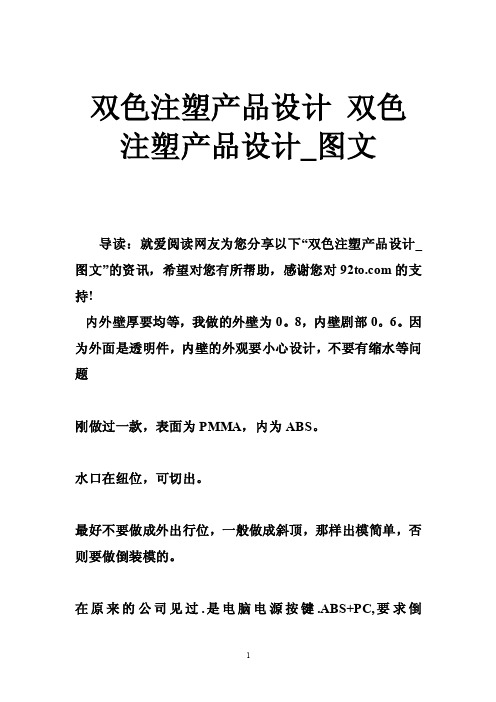
双色注塑产品设计双色注塑产品设计_图文导读:就爱阅读网友为您分享以下“双色注塑产品设计_图文”的资讯,希望对您有所帮助,感谢您对的支持!内外壁厚要均等,我做的外壁为0。
8,内壁剧部0。
6。
因为外面是透明件,内壁的外观要小心设计,不要有缩水等问题刚做过一款,表面为PMMA,内为ABS。
水口在纽位,可切出。
最好不要做成外出行位,一般做成斜顶,那样出模简单,否则要做倒装模的。
在原来的公司见过.是电脑电源按键.ABS+PC,要求倒光,ICON为PC材料,设计的时候按照同一种材料设计即可,然后拆件,模具上公模共用,第一次单次注射其中一种材质(公模部分),然后公模翻转180度后,母模两个胶口同时注射,开模后,一件成型完毕,顶出,然后翻转180度,循环往复在材料的选择上,第一射的料温一定要比第二射的高。
不然进行第二射时,会把第一射的材料挤压变形。
当然这也和水口位置和两种材料结合处的壁厚有一定关系还有一点,在两射共用一个进胶主流道时,尽量要求试模人员使用机械手自动剪切第一射的料头。
这样才能保证第二射一致。
否则很可能会造成问题误判。
这是因为第一射料头残留的多少直接影响第二射模内空膜体积的大小,在剂量(螺杆行程和速度)一定的情况下,会造成模内压力大小的不同。
正是基于这一特点,所以每次生产时第二射的成型条件会因第一射料头的剪切位置不同而有所变动。
绝大部分情况下,先注塑产品的硬胶部分,再注塑产品的软胶部分。
因为软胶易变形,成型压力大时,可以想像产品会是什么样子。
为了使二次胶与1次胶粘的更紧,常在一次胶上做序列沟槽等,当然啦必须在母模侧。
(如果第二次注胶为透明的外观,就不要这样了。
由于透明件的反光等不一样,会出现外观的黑影)二次封胶部位,劈空最好做在一次制品的边界处,不然打出的制品上会有压痕。
注塑时,第一次注塑成型的产品尺寸可以略大,以使它在第二次成型时能与另一个母模压得更紧,以达到封胶的作用。
也就是经常讲的预压。
一般采用SABIC PC EXL1414和拜尔TPU385S,两者亲和性那是相当的好。
图文详解双色注塑技术-20200609
2.双色单模
3.抽芯式双色模
4.混料成型双色
模
5.双料夹层双色模
混色射枪(单一模)
材料混成的亲和性
第一射成型
第二射成型公模互换取第一射料头
首先注射第一种材质,再通过第二色型腔完成双色成型
二色进料口
一色进料口
顶针板
两块顶出
结构分别
脱模一模二
穴型腔,
不一样,
分别成
型一/二
色材料
Shot2射台
Shot1射台转盘
转盘
变形
变形
PC材质热变形130度.Shot2硅胶在通过浇口进入模腔时的温度已超200度.a处在此种状况下,所能承受的力是极有限的.
a
流道强度小
流痕。
混合双色注塑成型
1、混合双色注塑成型
内容:
新技术-混合双色注塑成型:
海鹰混合双色/三色注塑机带领进入多物料注塑技术新领域,生产不用重新开模具,不生产双色产品时可以当单色注塑机一样使用。
海鹰混合双色/三色注塑机在使用原有模具下实现一模多色功能,本机型配置双螺杆料筒及特殊设计复合型射嘴,即可产生特殊花纹及多层颜色塑胶件,可任意变化色彩、花纹、形状,本机型适合生产灯饰、吸顶灯、工艺品、文具、表壳、表带、珠饰、头梳、发夹、塑料花、圣诞树等。
使用海鹰混合双色/三色注塑机生产塑件产品,直接提升产品之附加价值,再造模具的第二春,创造额外利润。
新技术-提供商:
海鹰塑料机械广东办事处位于深圳龙华新区民治街道办华荣路荣泰大厦11层(518131) 电话:+86-755-28186865;+86-755-33067568 总公司宁波海鹰塑料机械制造有限公司是宁波科技形企业,也是宁波市技术监督局产品质量跟踪企业。
厂址座落在著名包玉刚先生故乡,宁波市镇海区庄市工业开发区B区。
主要生产普通注塑机、伺服节能省电注塑机,尤其注重特种注塑机的开发生产,如混合双色\三色注塑机、分清双色注塑机、多物料注塑机、陶瓷专用成型机,金属粉末注射成型机、电木机、BMC注射成型机、瓶胚专用机、胶木机等。
还生产各种不同规格螺杆、料筒。
拥有高精度加工专用设备及全套热处理生产线。
双色液态硅胶注塑一体成型案例分享
双色液态硅胶注塑一体成型案例分享
▍原文作者:冯红平
▍工作单位:大洋集团东莞太洋橡塑制品有限公司
●作者:冯红平
●职务:大洋集团东莞太洋橡塑制品有限公司模具经理
●东莞论坛分享议题:双色液态硅胶模具设计 ; 塑胶射出和液态硅胶一体成型
●作者介绍:二十多年模具制造和管理经验
● 公司介绍:
大洋集团成立于1991年8月,2007年于香港上市,为全球罕见垂直整合的专业硅橡胶及塑料制品供货商,集原材料生产、加工、成品开模、生产等为一体,主要生产基地位于广东东莞樟木头与浙江湖州,员工约1500人。
东莞太洋橡塑制品有限公司为大洋集团全资子公司,主营业务为硅胶产品的设计研发及制造,业务涵盖硅橡胶、硅胶制品、薄膜电路按键、线路板插件、塑胶制品及模治具、LED节能灯、五金制品、电子产品配套件、特种劳动防护用品等。
公司以「国际质量、竞争价格、交期迅速、服务热忱」著称,拥有先进设备、完善的产品质量认证及全球领先的硅胶材料专利技术,并荣获多项国际大厂的最佳供货商奖项。
双色同步注塑成型技术
创新的双色同步注塑成型技术双色同步注塑在汽车市场,彩色仪表板渐呈流行趋势。
但此前不久,这些大型塑料制件只能是单色。
为了得到两种不同颜色的外观,喷漆是唯一的选择。
福特、伟世通、赫斯基的通力协作,使双色仪表板的成型技术揭开了全新的一页,这一创新的仪表板新工艺,即同步注射成型技术。
这种工艺可以将两种不同颜色的物料从同一注塑机的两个独立的注塑单元同时注入模腔,省却了后期的喷漆工序。
伟世通公司工程部经理Robert Stammler介绍说:“同步双色注射的概念其实很简单。
我们希望能够生产一种不需要喷漆的双色仪表板,使用传统的注塑机显然行不通。
为了简化加工与处理过程,我们试图在不需要机械转位,也不需要复杂的芯型结构的情况下同时进行两种材料的注塑。
”事实上,加工非常成功,在第七次射胶后,一个完美的双色制件加工出来了。
使用设备为Husky 的双色注塑机QD1650,配备有赫斯基Polaris控制系统和Tracer TMB机械手。
该机在Husky 底特律技术中心完成系统集成。
与传统的双色成型方法比较,部件成型所需的压力只需要传统设备的一半,而且成本大为降低。
赫斯基底特律技术中心总经理Rich Sieradzki介绍说:“同步注射成型技术能够降低成本,提供极佳的产品性能,使客户的生产风险降至最低。
赫斯基的Quadloc Dual 1650辅以Polaris控制系统,从灵活性、可靠性和不间断生产稳定性这三个方面保证了这一复杂工艺和部件的顺利实现和生产。
”新工艺的优势新工艺带给伟世通如下优势:降低仪表盘基架和组装后可能产生的噪音;提高外形美感和耐刮擦性能;降低成本:简单的模具设计,无旋转机构或复杂的型芯,与配备两套模腔和型芯的分次注射模具相比,成本更低;注塑周期与标准仪表盘相同;极大减少废品的产生。
据介绍,同步注射方法与传统两次注射方法相比,投资成本减少3.5倍,模具成本降低45%至55%。
新工艺与普通喷漆工艺相比,直接人工成本减少约13%,间接人工成本节约24万美元/年。
- 1、下载文档前请自行甄别文档内容的完整性,平台不提供额外的编辑、内容补充、找答案等附加服务。
- 2、"仅部分预览"的文档,不可在线预览部分如存在完整性等问题,可反馈申请退款(可完整预览的文档不适用该条件!)。
- 3、如文档侵犯您的权益,请联系客服反馈,我们会尽快为您处理(人工客服工作时间:9:00-18:30)。
这是一款手机护套,如下图产品分析:此款为某品牌手机的外圈护套,由二种塑料(PC+TPE)组成。
由于要求外形美观光滑,分模线必须做在内侧圆弧切点,所以外模要四面滑开,再看内侧,四周全部是内扣的,必须全方位内抽芯,也就是俗称的“爆炸芯”。
关于“爆炸芯”的模具结构,假如是普通的注塑模具,已经有非常经典的机构,我下面将有详细的介绍。
现在问题是双色模具,有二组动模和二组定模,二组动模的所有部件是完全一致的,要在双色注塑机的转盘上进行180度旋转,二种不同的塑料分别射进模腔,注射硬胶(PC)时动模的顶出机构和抽芯机构不动作,再注射软胶(TPE)并开模后,对准软胶料筒的一侧的动模的抽芯机构和顶出机构才开始动作,将完整的双色制品顶出。
由于动模旋转后,交换又合模后的浇口必须在同一位置,所以软胶和硬胶的浇口的处理显得令人困惑。
由于模具必须四周都要进行“内外同抽”,内、外滑块怎样排列,轨道设置在哪里?这个问题同样有被逼入墙角的感觉。
且不谈模具滑块机构的复杂性,我们从双色模具的基本原理来考虑,硬胶部分的成型和内外同抽机构是一定要设置在定模一侧的,软胶部分的成型机构也要设置在定模。
而且这个部分是由内外同抽的机构组成的凸起插入到动模的凹槽中。
转盘旋转180度后,这组凸起刚好插入到另外一个动模的凹槽中。
也就是说,二个定模上的由内外同抽滑块组成的凸起的外部形状和尺寸是完全相同的。
仅仅是成型软胶和硬胶的型面不同而已。
问题的难点是,这个凸起会分成上下二层,一层向外移动,另一层向内移动,也就是俗称的“内外同抽”,合成的凸起的侧面是一个统一的斜面,但是,传统的滑块必须要有滑动轨道等必要的条件,怎样设置轨道?这便成了本案例的核心问题。
我是这样设置动模部分的凹槽和定模部分凸起的。
动模的凹槽是这样的。
下面我们来探讨定模部分的设计1.01定模内外同抽的设计基本机构是这样的当A板和定模底板分开35mm后拨块拨动内滑块,同时通过齿轮的传动,外滑块向外移动。
如下图基本构想是用上图的拨块(图中玫瑰红色)拨动内滑块(图中绿色),在内滑块内滑的同时,通过齿轮的传动,使得外滑块(图中黄色)向外滑动。
这样就可以实现制品软胶部分与模具型面的分离。
同样的方法,相应的制品的硬胶部分的缺口也可以用同样的方法和模具的型面分离。
所有的这些机构都是设置在定模一侧的。
动模的每一次旋转,与定模间的配合都是吻合的。
内滑块的运动轨道(图中淡黄色)是很稳固地设置在A板上的,然而与之相对应的外滑块的轨道着落在哪里?岂不是无本之木?我利用内滑块的轨道上增加了一个凸起,兼起到了轴承的作用,见下图。
轴的另外一端是利用锁紧块,上面做了一条半圆槽,起到轴承的作用,并设置了一个小的挡块防止轴的轴向移动。
见下图。
我设计了一个内置的轨道(单轨),有点象“工字钢”同时它又是齿轮轴的固定处。
正可谓充分利用资源。
因为齿轮轴被限制移动,只能转动,所以内置轨道等于被固定在定模板上了。
这样一来,外滑块就变得非常简单.内滑块比较复杂,如下图。
内置轨道如下图为了实现拨块拨动内滑块的动作,A板与底板之间必须先分开一段距离(35mm),使得在二板分开的同时,拨块向内拨动内滑块。
这个动作是靠设置在动模上的尼龙胶钉来实现的,导向是靠设置在底板与A板间的附加小导柱来保证。
1.02双物料(双色)流道的设计当硬胶注塑完成后,开模后注射满硬胶的动模的抽芯部分和滑块部分是没有任何动作的,主流道和横流道都留在动模部分,并跟随动模由双色注塑机上的转盘转过180度,再次合模时,软胶部分的定模必须给硬胶的主流道留出一个位置,除非将硬胶部分的主流道取掉,但是这需要机械手多做一个动作,大概要多花10秒钟的时间。
这是会大大影响生产效率的。
软胶部分的浇口怎样设置?其实这个问题也是这个案例的最难的地方。
我设计了一个“同床异梦”的方法(比喻可能不恰当)。
软胶部分的主流道是在硬胶部分主流道的基础上,加上一个锥度半椭圆的空间作为软胶的主流道,当硬胶的主流道随动模一起转到软胶的定模并合模时,直接插入软胶的浇口套的预留空间,由于软胶的浇口套留出了一个半椭圆的空间,但是硬胶的主流道是圆锥体的,这就形成了截面为一个月牙形的空腔。
软胶可以顺利地被射入软胶部分的模腔。
硬胶的浇口套见下图软胶的浇口套如下图二种浇口合在一起是这样的其实,这个浇口套又是内滑块的逼紧块,也是动模一侧内滑块和所有斜顶块的逼紧块。
二组定模包括所有定模零部件的尺寸是完全相同的,只是有一点,大家仔细看,二个浇口套与注塑机射头接触的球面的深度是不同的,硬胶的浇口套深了5mm,其实道理很简单,当成型的硬胶的主流道插入软胶的浇口套时会留出5mm空间,让软胶通过,进入截面为月牙形的空腔。
在这个浇口套里,成型的软胶和硬胶的主流道各占半壁江山。
真是软硬通杀,左右逢源。
再来看横流道的设置其实,这个浇口套又是内滑块的逼紧块,也是动模一侧内滑块和所有斜顶块的逼紧块。
二组定模包括所有定模零部件的尺寸是完全相同的,只是有一点,大家仔细看,二个浇口套与注塑机射头接触的球面的深度是不同的,硬胶的浇口套深了5mm,其实道理很简单,当成型的硬胶的主流道插入软胶的浇口套时会留出5mm空间,让软胶通过,进入截面为月牙形的空腔。
在这个浇口套里,成型的软胶和硬胶的主流道各占半壁江山。
真是软硬通杀,左右逢源。
再来看横流道的设置我设计的硬胶的横流道是走下半圆的,这样使得硬胶的流道合模时与软胶的型腔形成一个上半圆的空间,正好是软胶横流道的空间。
这样设计的流道便于今后可以方便地将二种不同塑料的流道分开,以便合理利用。
1.03定模冷却系统的设计在这个模具的定模部分,仅仅是流道有较多的热量,特别是主流道,它的凝固时间的长短直接影响注塑周期。
成型软胶的部分虽然是在定模但是它是伸入到动模的凹槽里的,热量基本是集中在动模的。
因为内外同抽滑块的体积很小,无法安排水路,因此采用导热系数较高的铍铜来做内滑块,我仅仅在与内滑块贴紧的浇口套(兼逼紧块)上做了独立的冷却水回路,主要的作用是冷却主流道与横流道,这样可以缩短注塑周期。
见上图。
1.04二组定模的位置安排二组定模间的距离是由二个因素决定的,第一是双色注塑机的二组平行的料筒的中心距,第二是在这个中心距的约束下,动模的机构可否正常地工作,这个问题我们在下面动模设计部分会有详细的介绍。
暂时,我选择的双色注塑机的料筒中心距是480mm。
动模部分的设计2.01矩形制品四周全部内抽机构的动作原理矩形制品四周全部内抽机构俗称“爆炸芯”,内抽过程可用一句话来概括,一缩二抽三顶,什么意思呢?一般来说,四周全部内抽机构分三个部分,首先是中间部分可以缩下去,以便让出内抽芯的空间,第二是内抽芯部分,由于缩芯后中间有空位,矩形制品直边部分的内滑块可以向内移动。
第三是角部斜顶,由于四面直边的倒扣已经与内抽后的内滑块上的型面分开,角部的斜顶块可以沿45度方向斜顶出,这时制品是跟着斜顶块沿开模方向移动的,直到制品上的倒扣与斜顶块上的型面完全分离。
拿掉外滑块看,是这样的内抽和斜顶出后是这样的为了看得清楚些,上图有点夸张,其实内抽芯仅仅向内移动2.5mm。
缩芯仅仅缩下30mm。
这时制品的整圈倒扣与模具的型面已经完全分离了。
2.02内滑块的设计内滑块1和2是对称的,如下图有一组独立冷却水,齿条和内置轨道,这个内置轨道较难加工,是热处理后用火花机硬打出来的。
材料是用8407,硬度是HRC48度。
内滑块1在锁模时是向外撑紧的,是靠定模的浇口套来逼紧。
内滑块向内滑的动力是靠外滑块通过齿轮、齿条来传递的。
外滑块是靠外置的方形短油缸来拉动的(行程2.5mm)。
有一个细节,为了齿轮轴的装拆,在内滑块的对着齿轮轴的地方开了一条3X3的小槽。
要拆齿轮轴时,用一根2.5mm的顶针捅出来就可以了。
这个小槽的截面比轴的端面小,还可以有效防止轴的轴向移动。
2.03内滑块的设计二另外一个方向的内滑块(内滑块3、4)是这样设计的内滑块3本身带有齿条,利用外滑块的力,通过齿轮传动向内移动(2.5mm)。
它被限制在外滑块的凹槽内,所以,不需要另外的轨道。
2.04外滑块3、4的设计外滑块如下图反面是这样的冷却水的设置是这样的2.05动模轨道的设计动模轨道是动模部分的重要部件,虽然形状简单,但是在设计上有较大的难度。
我采用有高硬度且比较便宜的材料Cr12MoV来做,硬度采用HRC52度,它有二个方向的摩擦面,要求垂直度比较高。
这是我的设计风格,有很多人喜欢将动模板做得很厚,开槽后再镶硬片,我认为这样做不好,动模板开深槽后变形量很难控制,这样直接贴上去,又简单又方便,而且动模板绝对不会变形。
动模轨道的定位是靠滑动导套和一组销钉来实现的,方便可靠,并且用10毫米的螺丝固定,装拆很方便。
尼龙拉钉也是固定在动模轨道上的。
2.06摩擦片和齿轮轴座的设计如下图黄色的是摩擦片,其中外围的4件是用Cr12MoV备制,硬度为HRC56.。
中间二件兼有斜顶块导向的作用,是用耐磨青铜备制。
为了保证斜顶块的稳定,在动模板的反面还有一层青铜做的摩擦片。
在齿轮轴座的相应位置用线切割做成穿孔,齿轮轴座直接放入,因为齿轮轴座各个方向都有限制,所以不用安排螺钉。
2.07斜顶块的设计斜顶块用8407备制,硬度HRC52度。
滑座和摩擦片是用Cr12MoV备制。
硬度HRC58度。
斜顶块与内滑块、内缩块的配合面都是密配的,要起封胶的作用。
斜顶块的斜顶的角度的选择非常的重要,既要能够将制品的型面分离,制品可顺利取出,又不能与内滑块干涉,具体尺寸可以参考3D图档。
编后感:讲心里话,这套模具的难度很大,我已经63岁,眼睛也没有那么好使,但这些画图的工作是别人替代不了的。
假如没有那个“雌雄同体”的灵感,整套方案是想不出来的,感谢主给了我灵感,使得这么艰难的工作得以完成。
期间也犯了几个大大的错误。
第一是刚刚开始的方案,外滑块用了斜导柱,其后果是每一次开模时外滑块都会开一次,这样对制品的外表面有一定的伤害。
所幸在团队第一次评估时就看出了问题。
第二是齿轮轴没有固定在模板上,根本不可能进行内外同抽。
假如做出来一定会是个大笑话。
幸亏后来发现了,做了及时的改正。
模具设计的过程是不可能是一气呵成的,一定要发挥团队的作用,用集体的智慧,才能够达到最高的境界。
感谢广大网友对我的支持,尽量指出我设计中的缺陷(肯定有的),使得这套模具的设计方案不断完善。
同时也希望对广大模具爱好者通过本案例,能够在双色模具的设计方面有一点点帮助。
谢谢大家查鸿达2011年7月。