第四章 钢的表面淬火
表面淬火工艺
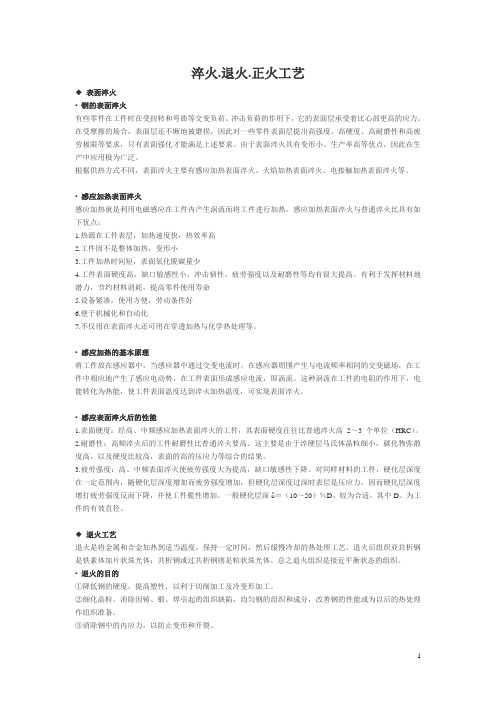
淬火.退火.正火工艺◆表面淬火• 钢的表面淬火有些零件在工件时在受扭转和弯曲等交变负荷、冲击负荷的作用下,它的表面层承受着比心部更高的应力。
在受摩擦的场合,表面层还不断地被磨损,因此对一些零件表面层提出高强度、高硬度、高耐磨性和高疲劳极限等要求,只有表面强化才能满足上述要求。
由于表面淬火具有变形小、生产率高等优点,因此在生产中应用极为广泛。
根据供热方式不同,表面淬火主要有感应加热表面淬火、火焰加热表面淬火、电接触加热表面淬火等。
• 感应加热表面淬火感应加热就是利用电磁感应在工件内产生涡流而将工件进行加热。
感应加热表面淬火与普通淬火比具有如下优点:1.热源在工件表层,加热速度快,热效率高2.工件因不是整体加热,变形小3.工件加热时间短,表面氧化脱碳量少4.工件表面硬度高,缺口敏感性小,冲击韧性、疲劳强度以及耐磨性等均有很大提高。
有利于发挥材料地潜力,节约材料消耗,提高零件使用寿命5.设备紧凑,使用方便,劳动条件好6.便于机械化和自动化7.不仅用在表面淬火还可用在穿透加热与化学热处理等。
• 感应加热的基本原理将工件放在感应器中,当感应器中通过交变电流时,在感应器周围产生与电流频率相同的交变磁场,在工件中相应地产生了感应电动势,在工件表面形成感应电流,即涡流。
这种涡流在工件的电阻的作用下,电能转化为热能,使工件表面温度达到淬火加热温度,可实现表面淬火。
• 感应表面淬火后的性能1.表面硬度:经高、中频感应加热表面淬火的工件,其表面硬度往往比普通淬火高2~3 个单位(HRC)。
2.耐磨性:高频淬火后的工件耐磨性比普通淬火要高。
这主要是由于淬硬层马氏体晶粒细小,碳化物弥散度高,以及硬度比较高,表面的高的压应力等综合的结果。
3.疲劳强度:高、中频表面淬火使疲劳强度大为提高,缺口敏感性下降。
对同样材料的工件,硬化层深度在一定范围内,随硬化层深度增加而疲劳强度增加,但硬化层深度过深时表层是压应力,因而硬化层深度增打疲劳强度反而下降,并使工件脆性增加。
表面淬火设备介绍

5)晶闸管中频电源装置在运行中,能根据负载变化自动调整频率 系统的输出功率一直保持在额定值
器结构示意图及说明。
表4-11 高频感应器结构
表4-11 中频感应器结构
三、感应器基本尺寸的确定
1.感应器与工件之间的间隙确定 表4-13为推荐采用的感应器与零件表面之间间隙的经验
数据。 2.感应器尺寸的确定
(1)感应器直径的确定 加热外圆表面时,感应器的内径 可由下式计算:
加热圆孔表面时,感应器的外径可由下 式计算:
3.前进法:火焰喷嘴和冷却装置沿淬火零件表面作平行移动,一边加 热,一边冷却,淬火零件可缓慢移动和不动。这种方法可以使很长 的工件进行表面淬火(如长轴、机床床身、导轨等),也适用于大模 数齿轮进行逐齿的淬火。
4.联合法:是指淬火零件绕其轴线作迅速旋转,而喷嘴及喷水装置同时沿 零件轴线平行移动。该法加热比较均匀,可作冷轧辊的表面淬火用。
二、感应器的分类及结构
1 分类 (1)加热方法 同时加热感应器和连续加热感应器
(2)零件加热部位形状 外表面加热感应器 内表面加热感应器 平面加热感应器 特殊形状加热感应器
(3)电源频率 高频 中频
2 结构
(1).制造感应器用纯铜厚度
纯铜厚度应稍大于感应电流冷态透入深度。
• 高频电流较小,不需要很高的机械强度,可用薄壁纯铜管绕制而 成,也可用薄铜片焊接而成。
如采用多匝时,则匝间距不超过零件与感应器之间的间隙, 以提高效率,一般匝间距为3~6mm。
表面工程学-第四章

表面淬火和表面形变强化技术
在表面工程技术中,不需要外加其它材料,主要依靠材料自身组 织与结构转变来进行表面改性的工艺主要有两类: 一、表面淬火与退火技术 二、表面形变强化技术 特点:工艺简单、效果显著、应用广泛
一
(一)原理:
表面淬火技术
定义: 采用特定热源将钢铁材料表面快速加热到Ac3(对亚共析钢)或者Ac1(对 过共析钢)之上,然后使其快速冷却并发生马氏体相变,形成表面强化层的 工艺过程。 注意:凡是能通过整体淬火强化的金属材料,原则上都可以进行表面淬火。
注:P/(Dv)称为比能量,物理意义为单位面积激光作用区注入的激光能量
(3)表面预处理状态 • 表面组织准备:
通过调制处理等手段,获得较 细的材料表面组织(细片状珠光体、 回火马氏体或奥氏体)
•
表面“黑化”处理:
磷化法、氧化法、喷刷涂料法、 镀膜法
二、激光表面熔凝技术原理
定义:
采用激光束将基材表面加热到熔化温度以上,当激光束移开后由于基材 内部导热冷却而使熔化层表面快速冷却并凝固结晶的表面处理工艺。(液相淬
2.受控喷丸对材料表面形貌与性能的影响 (1)对材料表面硬度的影响:
表面硬度可大幅度提高,且硬化层深度最高 可达0.8mm
(2)对表面粗糙度的影响:
表面粗糙度对其疲劳寿命影响很大, 降低表面粗糙度可以增加零件的疲劳强度。 受控喷丸以后的表面痕迹没有方向性, 有利于增加零件的疲劳强度。
(3)对疲劳寿命与抗应力腐蚀能力的影响:
三、适用范围:
主要用于单件、小批量生产及大型齿轮、轴、轧辊、导轨等
四、组织特征:过渡区较宽
第三节
激光淬火与电子束淬火技术
一、激光淬火技术的原理及应用:
表面淬火
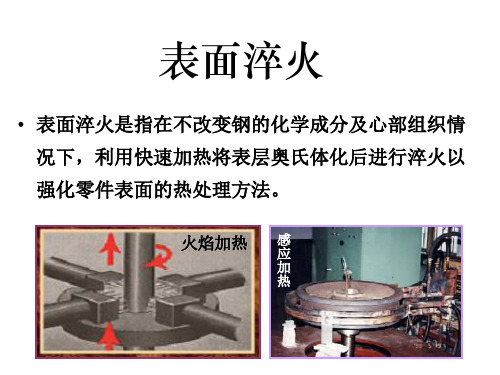
轴 的 感 应 加 热 表 面 淬 火
ቤተ መጻሕፍቲ ባይዱ
• ①表面淬火用材料 • ⑴ 0.4-0.5%C的中碳钢。
• 含碳量过低,则表面硬度、耐磨性下降。
• 含碳量过高,心部韧性下降; • ⑵ 铸铁 提高其表面耐磨性。
机床导轨
表面淬火齿轮
• ②预备热处理
• ⑴工艺: • 对于结构钢为调质或正火。 • 前者性能高,用于要求高的重 要件,后者用于要求不高的普
感应淬火机床
• ⑤表面淬火常用加热方法 • ⑴ 感应加热: 利用交变电流 在工件表面感应巨大涡流,
使工件表面迅速加热的方法。
感应加热 表面淬火 示意图
• 感应加热分为: • 高频感应加热 频 率 为 250-300KHz , 淬 硬层深度0.5-2mm
火传 感动 应轴 器连 续 淬
感应加热表面淬火齿轮的截面图
表面淬火
• 表面淬火是指在不改变钢的化学成分及心部组织情
况下,利用快速加热将表层奥氏体化后进行淬火以
强化零件表面的热处理方法。
火焰加热
感 应 加 热
• 表面淬火目的: • ① 使表面具有高的硬度、耐磨性和疲劳极限; • ② 心部在保持一定的强度、硬度的条件下,具有足够的 塑性和韧性。即表硬里韧。 • 适用于承受弯曲、扭转、摩擦和冲击的零件。
通件。
• ⑵目的: • 为表面淬火作组织准备; • 获得最终心部组织。
回火索氏体
索氏体
• ③表面淬火后的回火 • 采用低温回火,温度不高于200℃。 • 回火目的为降低内应力,保留淬火高硬度、耐磨性。 • ④表面淬火+低温回火后的组织 • 表层组织为M回;心部组织为S回(调质)或F+S(正火)。
感应加热表面淬火
第四章 表面淬火10 1
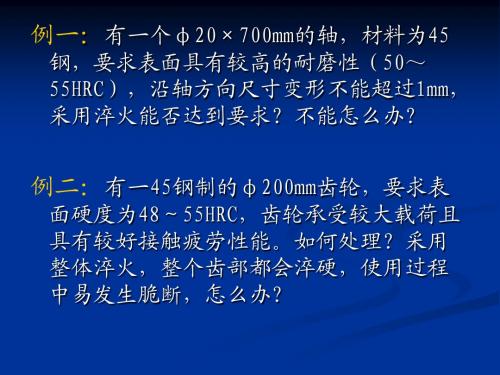
(b)比功率的选择:
f 最佳
600 2 x
比功率是指感应加热时工件单位表面积上所吸收的 电功率。比功率选择主要决定于频率和要求硬化层 深度 设备比功率 :设备输出功率与零件同时被加热的面 积比
P P A
P P工 P A
实验表明:
●在工件直径一定的情况下,随着硬化层深度 的增厚,表面残余压应力先增大,达到一定 值后,继续增加硬化层厚度,表面残余压应 力反而减少。 ●残余应力与沿硬化层深度的硬度分布有关。 过渡区硬度降落愈陡,表面压应力虽较大, 但紧靠过渡区的张应力峰值也最大;过渡区 硬度降得愈平缓,过渡区愈宽,张应力峰值 内移且减少,表面的残余压应力也减少。 ●残余应力的分布和钢中的含碳量有关。含碳 量愈高,残余压应力愈大
§4-3:表面淬火方法
一、感应加热表面淬火
工件在交变磁场作用下产生了较高的感
应电势并在表面形成涡流,利用感应电流
在零件表面产生的热效应而使零件加热称 为感应加热;将感应加热后的零件快速冷 却的淬火工艺称为感应加热淬火。
根据设备输出频率高低,感应加热的种类如下表所示:
加热方法 工频 中频 高频、超音频 超高频脉冲
流条;冷却装置等
▲感应圈形状与结构
感应圈的几何形状主要根据工件硬化部位 的几何形状、尺寸及选择的加热方式来确定。 设计时应注意以下几种效应:
▲临近效应:(采用旋转加热方法)
▲环状效应:(有利于圆柱体外表面)
▲尖角效应:(调节线圈与零件间的间隙或改 进感应圈的结构来改善)
▲感应圈尺寸的确定
感应圈管壁厚度应略大于高频电流穿透厚度。
67 / f (mm) 4、感应加热时的驱流和屏蔽
钢的表面淬火和化学热处理

3.钢的碳氮共渗 碳氮共渗又叫氰化,是在奥氏体状态下同时将碳、氮渗入工件表层,并以渗碳为 主的化学热处理工艺。 常用的气体碳氮共渗法,即在气体渗碳的基础上,同时向炉内 送入定量的氨气, 使它们分解为活性碳原子和氮原子。共渗温度 820~870℃,共渗层表面 wc 约 0.7%~1.0%, wN 约 0.15%~0.50%。
生一个频率相同的交变磁场。将工件放入线圈内,在工件内部产生同频率的感应电流 (涡流)。由于感应电流的集肤效应(电流集中分布在工件表面)和热效应,使工件表 层迅速加热到淬火温度,而心部则仍处于相变点温度以下,随即快速冷却,从而达到 表面淬火的目的。
钢的表面淬火和化学热处理
1.1钢的表面淬火
图 2-38 感应加热表面淬火示意图
钢的表面淬火和化学热处理
1.1钢2)的感表应面加淬热表火面淬火的特点
与普通加热淬火相比,感应加热表面淬火具有如下特点: ①加热速度快,只需几秒至几十秒就可将工件表层一定深度加热至淬火温度,使 表层获得晶粒细小的奥氏体组织,淬火后表层组织为细隐晶马氏体,表面硬度比普通 淬火高 2~3HRC,且脆性较小。 ②因加热时间短,减少了氧化脱碳工件。 ③因工件内部并未加热,淬火变形小。 ④易于控制淬硬层深度,可满足各种工件对淬硬层深度的不同要求。 ⑤便于机械化和自动化生产,生产率高,适于大批量生产。 但感应加热表面淬火设备比较昂贵,零件形状复杂时感应器制造困难,因而不适 于单件小批生产。
钢的表面淬火和化学热处理
1.1钢2.的火焰表加面热淬表面火淬火
火焰淬火是应用氧乙炔(或其他可燃气体)火焰对零件表面进行快速加热,随之 快速冷却的工艺,如图 2-39 所示。
金属工艺学电子教学教案——第四章 钢的热处理02(高教版 王英杰主编)
第四节淬火教学重点与难点1.重点淬火、回火2.难点淬透性和淬硬性教学方法与手段1.利用挂图等教具。
2.举生活中应用淬火与回火的现象,分析原理与应用,触类旁通。
教学组织1.复习提问10分钟2.讲解75分钟3.小结5分钟教学内容♦钢的淬火是指工件加热奥氏体化后以适当方式冷却获得马氏体或(和)贝氏体组织的热处理工艺。
♦临界冷却速度是指获得马氏体的最低冷却速度。
♦马氏体是碳或合金元素在α-Fe中的过饱和固溶体,是单相亚稳组织,硬度较高,用符号M表示。
马氏体的硬度主要取决于马氏体中碳的质量分数。
马氏体中由于溶入过多的碳原子,从而使α-Fe晶格发生畸变,增加其塑性变形抗力,故马氏体中碳的质量分数越高,其硬度也越高。
一、淬火(一)淬火的目的淬火的目的主要是使钢件得到马氏体(和贝氏体)组织,提高钢的硬度和强度,与适当的回火工艺相配合,更好地发挥钢材的性能潜力。
(二)淬火工艺1.淬火加热温度的确定亚共析钢淬火加热温度为Ac以上30℃~50℃。
3以上30℃~50℃。
共析钢和过共析钢淬火加热温度为Ac12.淬火介质常用的淬火冷却介质有油、水、盐水、硝盐浴和空气等。
3.淬火方法(1)单液淬火。
♦将已奥氏体化的钢件在一种淬火介质中冷却的方法。
例如,低碳钢和中碳钢在水中淬火,合金钢在油中淬火等。
单液淬火方法主要应用于形状简单的钢件。
(2)双液淬火。
♦将工件加热奥氏体化后先浸入冷却能力强的介质中,在组织即将发生马氏体转变时立即转入冷却能力弱的介质中冷却的方法,称为双液淬火。
例如,先在水中冷却后在油中冷却的双液淬火。
双液淬火主要适用于中等复杂形状的高碳钢工件和较大尺寸的合金钢工件。
(3)马氏体分级淬火♦工件加热奥氏体化浸入温度稍高于或稍低于Ms点的盐浴或碱浴中,保持适当时间,在工件整体达到冷却介质温度后取出空冷以获得马氏体组织的淬火方法,称为马氏体分级淬火。
马氏体分级淬火能够减小工件中的热应力,并缓和相变过程中产生的组织应力,减少淬火变形。
四、表面淬火
快速加热: 要在工件表面有限深度内达到相变点以上的温度, 必须给工件表面以极高的能量密度来加热,使工件表面的热量来 不及向心部传导,以造成极大的温差。
-
2
三、表面淬火的分类: 表面淬火常以供给表面能量的形式不同而命名及分类。目前表
面淬火可以分成以下几类: 1.感应加热表面淬火 2.火焰淬火 3.电接触加热表面淬火 4.电解液加热表面淬火 5.激光加热表面淬火 6.电子束加热表面淬火
-
4
2. 奥氏体成分不均匀性随着加热速度的增加而增大 如前所述,随着加热速度的增大,转变温度提高,转变温度范
围扩大. 随着转变温度的升高,与铁素体相平衡的奥氏体碳浓度 降低,而与渗碳体相平衡的奥氏体碳浓度增大. 因此,与铁素体 相毗邻的奥氏体碳浓度将和与渗碳体相毗邻的奥氏体中碳浓度有 很大差异。由于加热速度快,加热时间短,碳及合金元素来不及 扩散,将造成奥氏体中成分的不均匀,且随着加热速度的提高, 奥氏体成分的不均匀性增大。例如0.4%C碳钢,当以130℃/s 的加热速度加热至900℃时,奥氏体中存在着1.6%C的碳浓度区. 显然,快速加热时,钢种、原始组织对奥氏体成分的均匀性有很 大影响. 对热传导系数小,碳化物粗大且溶解困难的高合金钢采 用快速加热是有困难的。
快速加热使奥氏体成分不均匀及晶粒细化,减小了过冷奥氏体 的稳定性,使c曲线左移. 由于奥氏体成分的不均匀性,特别是亚 共析钢,还会出现二种成分不均匀性现象。在珠光体区域,原渗 碳体片区与原铁素体片区之间存在着成分的不均匀性,这种区域 很傲小,即在微小体积内的不均匀性. 而在原珠光体区与原先共 析铁素体块区也存在着成分的不均匀性,这是大体积范围内的不 均匀性. 由于存在这种成分的大体积不均匀性,将使这二区域的 马氏体转变点不同,马氏体形态不同. 即相当于原铁素体区出现 低碳马氏体,原珠光体区出现高碳马氏体. 由于快速加热奥氏体 成分的不均匀性,淬火后马氏体成分也不均匀,所以,尽管淬火 后硬度较高,但回火时硬度下降较快,因此回火温度应比普通加 热淬火的略低。
钢的表面淬火和化学热处理
2)钢的渗氮(氮化) 渗氮是在一定温度下使活性氮原子渗入工件表面的化学热 处理工艺,又称氮化。 渗氮能使零件获得比渗碳更高的表面硬度、耐磨性以及提 高其耐腐蚀性和疲劳强度。 (1)气体氮化 目前应用最广的是气体渗氮。气体渗氮是将工件置于通有 氨气(NH3)的密闭炉内,加热到500~560℃,氨分解产生的 活性氮离子[N]被工件表面吸收,并逐渐向心部扩散,从而形成 渗氮层。渗氮层的深度一般为0.1~0.6mm。 C:\Documents and Settings\Administrator\桌面\热处理 录像4(钢的表面热处理与化学热处理)\氮化.rm
名称频率淬硬深度mm适用零件高频感应加热100500khz0525淬硬层较薄的中小型零件如小模数齿轮小的轴感应加热表面淬火种类及应用中频感应加热110khz310承受较大载荷和磨损零件如大模数齿轮较大凸轮等工频感应加热50hz1020要求硬层深的大型零件和钢材的穿透加热如轧辊火车车轮等感应加热速度极快时间很短仅为几秒钟加热淬火有如下特点
解的有机液体(如煤油、丙酮等),保温一段时间,渗碳气体 或有机液体在高温下分解产生活性碳原子,活性碳原子逐渐滲 入工件表面,并向心部扩散,形成一定深度的渗碳层。渗碳层 深度可通过控制保温时间来达到,一般为0.5~2.5mm。
井式渗碳炉
第1章 机械工程材料
工件渗碳后必须进行淬火和低温回火,最终表层为细小片 状的回火高碳马氏体及少量的渗碳体,这样表面可获得高的硬 度(60~64HRC)、耐磨性及疲劳强度;而心部组织取决于 钢的淬透性,一般低碳钢心部组织为铁素体和珠光体,硬度为 110~150HBS,低合金钢(20CrMnTi钢)通常心部组织为回 火低碳马氏体和少量铁素体,硬度为35~45HRC,具有较高 的强韧性和塑性。 气体渗碳的渗碳层质量高,渗碳过程易于控制,生产率 高,劳动条件好,易于实现机械化和自动化,适于成批或大量 生产。主要用于受磨损和较大冲击载荷的零件,如齿轮、活塞 销、凸轮、轴类等。
材料力学第四章钢的热处理
本章练习1 4、过共析钢的等温转变图(C曲线)如右图所示,试指出图中各点位置所
对应的组织。
本章练习1
5、两块碳的质量分数均为Wc=0.77%的钢片加热至727℃以上,分别以不同 方式冷却,钢片的冷却曲线及该种钢材的奥氏体等温转变图如图所示。 试问图中①、②、③、④点各是什么组织?定性地比较②、④点组织的 硬度大小。
a)A1~650℃:P,5~25HRC,片间距为0.6~0.7μm,( 500× )。 b)650℃ ~600℃:细片状P---索氏体(S),片间距为0.2~0.4μm,25~36HRC。 c)600℃ ~550℃:极细片状P---托氏体(T),片间距为<0.2μm,35~40HRC。
a)
b)
c)
第二节 钢在冷却时的组织转变 二、过冷奥氏体等温转变的组织和性能 2.贝氏体型转变 半扩散相变(C)550℃~Ms,根据其组织形态不同,分为:
铸锭或铸件在凝固过程中不可避免的要产生枝晶偏析等化学成分不均匀 现象,为达到化学成分的均匀化,必须对其进行扩散退火。 特点:加热温度高(一般在Ac3或Acm以上150~200℃),保温时间长(10h以上) 去应力退火
用来消除因变形加工及铸造、焊接过程中引起的残余内应力,以提高工 件的尺寸稳定性,防止变形和开裂。 特点:工件随炉缓慢加热至Ac1-(100 ~ 200 ℃),经一段时间保温后随炉
除Co、Al (>2.5% ) 外,所有合金元素溶入 奥氏体中,都可增加过冷奥氏体的稳定性,使等 温转变图右移。其中非碳化物形成元素或弱碳化 物形成元素只改变等温转变图的位置,不改变形 状,而碳化物形成元素不仅使等温转变图的位置 发生变化,还改变等温转变图的形状。 3.加热温度和保温时间
加热温度越高,保温时间越长,TTT曲 线向右移。
- 1、下载文档前请自行甄别文档内容的完整性,平台不提供额外的编辑、内容补充、找答案等附加服务。
- 2、"仅部分预览"的文档,不可在线预览部分如存在完整性等问题,可反馈申请退款(可完整预览的文档不适用该条件!)。
- 3、如文档侵犯您的权益,请联系客服反馈,我们会尽快为您处理(人工客服工作时间:9:00-18:30)。
(4)快速加热对过冷奥氏体的转变及马氏体回火有明显影响
快速加热使奥氏体成分不均匀及晶粒细化,减小 了过冷奥氏体的稳定性,使c-曲线左移。
例子:亚共析钢
① 微小体积内的不均匀性:P区域; ② 大体积范围内的不均匀性:P和先共析F;
淬火后马氏体成分也不均匀
4.2.2 表面淬火的组织与性能
一 表面淬火的金相组织 ① 钢种 ② 淬火前的原始组织 ③ 淬火加热时沿截面温度的分布
2) 中频感应加热表面淬火:电流频率为500~10000Hz,最常用
频率为2500~8000Hz。可获淬硬层深度为3~5mm。主要用于要求淬硬 层较深的较大尺寸的轴类零件及大中模数齿轮的表面淬火。
3) 工频感应加热表面淬火:电流频率为50Hz,不需要变频设
备。可获得淬硬层深度为10~15mm。适用于轧辊、火车车轮等大直径 零件的表面淬火。
4)残余应力与钢中含碳量有关 C↑→M比容↑→组织应力越显著→残余压应力↑
5)结论
对于高频表面淬火 ✓ 中、小尺寸零件淬硬层深度为工件半径的10~20%; ✓ 过渡区的宽度为淬硬层深度的25~30%;
3 硬化层分布对工件承载能力的影响
当工件进行局部表面淬火 时,存在着淬火区段与非淬火 区段间的过渡问题;
4.1 表面淬火的目的、分类及应用
一 定义
被处理工件在表面有限深度范围内加热至相变点以 上,然后迅速冷却,在工件表面一定深度范围内达到淬 火目的的热处理工艺。
二 目的
✓ 表面:一定深度的M组织 ✓ 心部:仍保持着淬火前的组织状态
三 分类 依据:供给表面能量的形式不同
1) 感应加热表面淬火
以电磁感应原理在工件表面产生电流密度很高的涡 流来加热工件表面的淬火方法。
第四章 钢的表面淬火
主要内容
表面淬火的目的、分类及应用 表面淬火工艺原理 表面淬火方法
基本要求
掌握表面淬火的目的、分类及应用,表面淬火工艺原理及方法。
本章重点
表面淬火的目的、分类及应用,表面淬火工艺原理及方法。
本章难点
表面淬火方法,包括感应加热表面淬火、火焰加热表面淬火、其他表 面淬火法。
2) 火焰淬火
用温度极高的可燃气体火焰直接加热工件表面的表 面淬火方法。
3) 电接触加热表面淬火
当低电压大电流的电极引入工件并与之接触,以电 极与工件表面的接触电阻发热来加热工件表面的淬火方 法。
4) 电解液加热表面淬火 工件作为一个电极(阴极)插入电解液中,利用阴
极效应来加热工件表面的淬火方法。 5) 激光加热表面淬火
有关
1 原始组织为退火状态的共析钢
自表面向心部:M区(包括残余 奥氏体)、M十P区和P区。
2 原始组织为正火状态的45钢 淬火烈度很大的淬火介质
从表面到中心:M、M+F、 M+F+P、P+F
3 原始组织为调质状态的45钢
由于S回为粒状渗碳 化均匀分布在铁素体基 体上的均匀组织,因此 表面淬火后不会出现由 于上述那种碳浓度大体 积不均匀性所造成的淬 火组织的不均匀。
感应加热表面淬火的特点
与普通加热淬火相比
1) 由于感应加热速度极快,钢的奥氏体化温度明显升高, 奥氏体化时间显著缩短,即奥氏体化是短时间内在一个很 宽的温度范围内完成的。
2) 由于感应加热时间短、过热度大,使得奥氏体形核多, 且不易长大,因此淬火后表面得到细小的隐晶马氏体,硬 度比普通淬火的高2-3HRC,韧性也明显提高。
6) 电子束加热表面淬火
四 应用
1) 普遍应用:感应加热表面淬火、火焰淬火 2) 迅速发展:激光加热表面淬火、电子束加热表面淬火 3) 适用材料
① 中碳调质钢、球墨铸铁——机械零件(机床主轴、 齿轮、柴油机曲轴、凸轮轴);
② 高碳钢——承受较小冲击和交变载荷下工作的工具、 量具及高冷硬轧辊;
4.2 表面淬火工艺原理 4.2.1 钢在非平衡加热时的相变特点
(1) 在一定的加热速度范围内,临界点随加热速度的 增加而提高
(2) 奥氏体成分不均匀性随着加热速度的增加而增大
快速加热时,钢种、原始组织对奥氏体成分的 均匀性有很大影响。对热传导系数小,碳化物粗大 且溶解困难的高合金钢采用快速加热是有困难的。
(3) 提高加热速度可显著细化奥氏体晶粒
① 过热度大→奥氏体晶核不仅在铁素体一碳化物相界 面上形成,而且也可能在铁素体的亚晶界上形成,因此 使奥氏体的成核率增大; ② 加热时间极短→奥氏体晶粒来不及长大;
例如:40Cr钢 调质+表面淬火:324N/mm2 调质处理:235N/mm2
原因
✓ 表层本身的强度增高; ✓ 在表层形成很大的残余压应力;
三 表面淬火淬硬层深度及分布对工件承载能力的影响
1 表面淬火硬化层与工件 负载时应力分布的匹配
传动轴,承受扭矩, 截面上剪切应力分布如右 图所示。
2 表面淬硬层深度与工件内残余应力的关系
4.3 表面淬火方法 4.3.1 感应加热表面淬火
定义
利用感应电流通过工件产生的热效应,使工件表面 局部加热,继之快速冷却,以获得M组织的工艺。
种类和用途
所用电流频率的不同
1) 高频感应加热表面淬火:电流频率为100~500kHz,最常用
频率为200~300kHz,可获淬硬层浓度为0.5~2.0mm,主要适用于中、 小模数齿轮及中、小尺寸轴类零件的表面淬火。
3) 表面淬火后,不仅工件表层强度高,而且由于马氏体 转变产生的体积膨胀,在工件表层造成了有利的残余压应 力,从而有效地提高了工件的疲劳强度并降低了缺口敏感 性。
1)表面淬火时截面上 残余应力的分布如右 图。
2)硬化层深度与残余应力的关系
在工件直径一定的 情况下,随着硬化层深 度的增厚,表面残余压 应力先增大,达到一定 值后,若再继续增厚硬 化层深度,表面残余压 应力反而减小。
3)残余应力与沿淬火层深度的硬度分布的关系
与M层的深 度、过渡区的 宽度及工件截 面尺寸之间的 速加热,激冷淬火后 的工件表面硬度比普通加热 淬火高。
影响因素
奥氏体成分不均匀性、 奥氏体晶粒及亚结构细化
2 耐磨性 比普通淬火的高
影响因素
✓奥氏体晶粒细化 ✓奥氏体成分的不均匀 ✓表面硬度较高 ✓表面压应力状态
3 疲劳强度
✓ 显著地提高零件的抗疲劳性能; ✓ 显著地降低疲劳试验时的缺口敏感性;