马钢第一钢轧总厂车轮钢冶炼工艺过程简介
炼钢生产工艺流程-概述说明以及解释

炼钢生产工艺流程-概述说明以及解释1.引言1.1 概述炼钢生产工艺流程是指钢铁制造过程中的一系列步骤和工艺,旨在将生铁转化为高品质的钢材。
这个过程通常包括炼铁和炼钢两个主要阶段。
炼铁是将铁矿石经过冶炼和还原等多个步骤,从中提取出生铁的过程。
生铁是含有较高碳含量的铁合金,一般还含有一些杂质,需要进行炼钢进一步提纯。
炼钢是在特定条件下,通过控制温度、压力、氧气流量等参数,对生铁进行加工和熔炼,以去除杂质并调整钢材的成分和性能。
炼钢生产工艺流程在各个钢铁企业和工厂可能存在差异,但通常包括以下几个关键步骤:配料、炼钢炉装料、炉前处理、溶解炼炉、精炼、铸钢、连铸以及后续的淬火、热处理和表面处理等工序。
在配料阶段,各种原材料,包括铁矿石、废钢、合金等,按照一定比例混合,以满足最终产品的技术要求。
接下来是炼钢炉装料,将配料装入炼钢炉中,并控制好加热和冶炼条件。
炉前处理是指在进入炼钢炉之前对原料进行预处理,以去除杂质和调整成分。
这一步通常包括破碎、磁选、筛分等物理处理和烧结、还原等化学处理。
溶解炼炉是炼钢的关键过程,原料在高温下熔化,各种杂质被氧化、还原或浮渣分离的方式去除。
精炼是对溶解炼炉的产物进行进一步处理,通过吹氧、渣化反应等技术手段,去除残余杂质,调整成分组成和温度。
接下来是铸钢阶段,将精炼后的钢液倒入连铸机中,通过结晶器冷却凝固,形成连续块或板。
这些块或板可用于制造各种钢材产品,如钢板、钢管、钢坯等。
炼钢生产工艺流程的最后几个过程是后续处理,包括淬火、热处理和表面处理。
通过这些工序,钢材的性能、硬度、韧性、耐腐蚀性等可以得到进一步改善和优化,以满足特定应用需求。
总的来说,炼钢生产工艺流程是一个复杂且关键的过程,需要合理的工序安排、严格的质量控制和先进的技术手段。
它不仅影响到钢材质量和性能,也对钢铁企业的生产效率和经济效益产生重大影响。
1.2 文章结构文章结构部分的内容应该是对整篇文章的组成部分进行简要介绍。
炼钢生产流程详细讲解

钢铁生产工艺主要包括:炼铁、炼钢、轧钢等流程。
(1)炼铁:就是把烧结矿和块矿中的铁还原出来的过程。
焦炭、烧结矿、块矿连同少量的石灰石、一起送入高炉中冶炼成液态生铁(铁水),然后送往炼钢厂作为炼钢的原料。
(2)炼钢:是把原料(铁水和废钢等)里过多的碳及硫、磷等杂质去掉并加入适量的合金成分。
(3)连铸:将钢水经中间罐连续注入用水冷却的结晶器里,凝成坯壳后,从结晶器以稳定的速度拉出,再经喷水冷却,待全部凝固后,切成指定长度的连铸坯。
(4)轧钢:连铸出来的钢锭和连铸坯以热轧方式在不同的轧钢机轧制成各类钢材,形成产品。
炼钢工艺总流程图炼焦生产流程:炼业是将焦煤经混合,破碎后加入炼焦炉经干馏后产生热焦碳及粗焦炉气之制程。
烧结生产流程:烧结作业系将粉铁矿,各类助熔剂及细焦炭经由混拌、造粒后,经由布料系统加入烧结机,由点火炉点燃细焦炭,经由抽气风车抽风完成烧结反应,高热之烧结矿经破碎冷却、筛选后,送往高炉作为冶炼铁水之主要原料。
高炉生产流程:高炉作业是将铁矿石、焦炭及助熔剂由高炉顶部加入炉,再由炉下部鼓风嘴鼓入高温热风,产生还原气体,还原铁矿石,产生熔融铁水与熔渣之炼铁制程。
转炉生产流程:炼钢厂先将熔铣送前处理站作脱硫脱磷处理,经转炉吹炼后,再依订单钢种特性及品质需求,送二次精炼处理站(RH真空脱气处理站、Ladle Injection盛桶吹射处理站、VOD真空吹氧脱碳处理站、STN搅拌站等)进行各种处理,调整钢液成份,最后送大钢胚及扁钢胚连续铸造机,浇铸成红热钢胚半成品,经检验、研磨或烧除表面缺陷,或直接送下游轧制成条钢、线材、钢板、钢卷及钢片等成品。
连铸生产流程:连续铸造作业乃是将钢液转变成钢胚之过程。
上游处理完成之钢液,以盛钢桶运送到转台,经由钢液分配器分成数股,分别注入特定形状之铸模,开始冷却凝固成形,生成外为凝固壳、为钢液之铸胚,接着铸胚被引拔到弧状铸道中,经二次冷却继续凝固到完全凝固。
经矫直后再依订单长度切割成块,方块形即为大钢胚,板状形即为扁钢胚。
钢制车轮生产工序说明
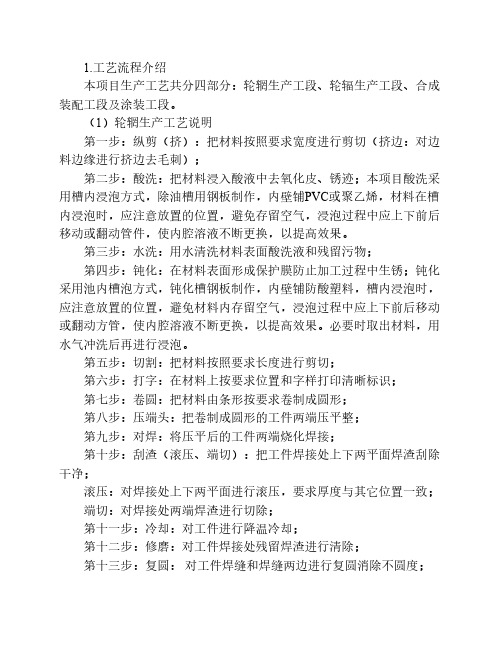
1.工艺流程介绍本项目生产工艺共分四部分:轮辋生产工段、轮辐生产工段、合成装配工段及涂装工段。
(1)轮辋生产工艺说明第一步:纵剪(挤):把材料按照要求宽度进行剪切(挤边:对边料边缘进行挤边去毛刺);第二步:酸洗:把材料浸入酸液中去氧化皮、锈迹;本项目酸洗采用槽内浸泡方式,除油槽用钢板制作,内壁铺PVC或聚乙烯,材料在槽内浸泡时,应注意放置的位置,避免存留空气,浸泡过程中应上下前后移动或翻动管件,使内腔溶液不断更换,以提高效果。
第三步:水洗:用水清洗材料表面酸洗液和残留污物;第四步:钝化:在材料表面形成保护膜防止加工过程中生锈;钝化采用池内槽泡方式,钝化槽钢板制作,内壁铺防酸塑料,槽内浸泡时,应注意放置的位置,避免材料内存留空气,浸泡过程中应上下前后移动或翻动方管,使内腔溶液不断更换,以提高效果。
必要时取出材料,用水气冲洗后再进行浸泡。
第五步:切割:把材料按照要求长度进行剪切;第六步:打字:在材料上按要求位置和字样打印清晰标识;第七步:卷圆:把材料由条形按要求卷制成圆形;第八步:压端头:把卷制成圆形的工件两端压平整;第九步:对焊:将压平后的工件两端烧化焊接;第十步:刮渣(滚压、端切):把工件焊接处上下两平面焊渣刮除干净;滚压:对焊接处上下两平面进行滚压,要求厚度与其它位置一致;端切:对焊接处两端焊渣进行切除;第十一步:冷却:对工件进行降温冷却;第十二步:修磨:对工件焊接处残留焊渣进行清除;第十三步:复圆:对工件焊缝和焊缝两边进行复圆消除不圆度;第十四步:扩口:把工件两端扩成要求的角度和直径;第十五步:旋压:对工件进行旋压成型底槽R并确认定位点;第十六步:一序滚压成型:对工件进行滚压预成形底槽等各部形状;二序滚压成型:对工件进行滚压成形底槽和胎圈座部位;三序滚压成型:对工件进行滚压成形胎圈座和轮缘部位。
(2)轮辐生产工艺说明第一步:开平:将进厂卷板料进行校平的工序;第二步:落圆:将校平后的板料毛坯通过油压机和模具,冲出一定规格的圆料毛坯;第三步:冲预孔:在冲床上冲出圆料毛坯中心预孔,用于后序定位;第四步:旋压:以中心预孔定位,将圆料毛坯通过旋压机旋压成一定形状的轮辐毛坯;第五步:整形:通过压力机和模具对轮辐毛坯安装面进行整形,使安装面的平面度达到规定的要求;第六步:组合冲压:通过压力机和模具对轮辐毛坯中心孔和螺栓孔同时冲出的工序;第七步:冲风孔:在冲床上通过带分度装置的模具对轮辐毛坯冲出规定数量的通风孔;第八步:挤风孔:在冲床上通过模具对轮辐毛坯冲通风孔形成的冲裁毛刺进行挤压的工序;第九步:平端面:主要是将轮辐端面进行平整,使轮辐高度符合要求,同时也有利于后续焊接;第十步:车中孔:主要是将轮辐中心孔在车床上通过车胎进行精加工至规定的尺寸;第十一步:整平面:通过压力机和模具对轮辐毛坯安装面进行整形,使安装面的平面度达到规定的要求;第十二步:整外径:通过压力机和模具对轮辐外径进行精整的工序;第十三步:精加螺孔:对轮辐螺栓孔进行精加工的工序,一般在多头钻上进行,通过扩孔、划窝使螺栓孔几何尺寸及精度达到规定的要求。
车轮钢轮毂钢的制造工艺
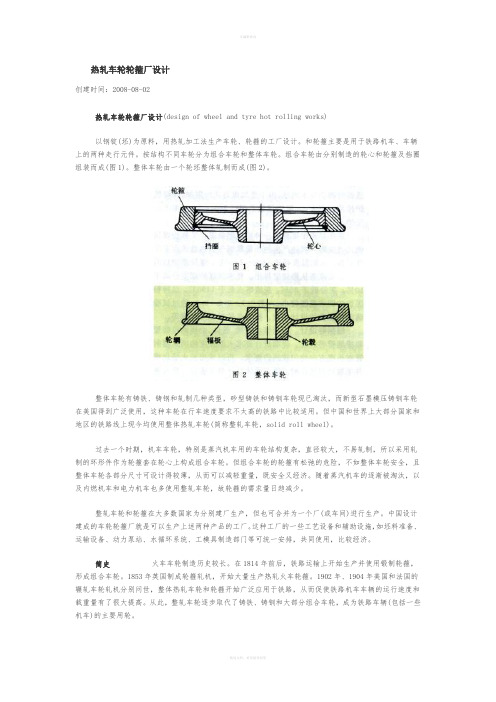
热轧车轮轮箍厂设计创建时间:2008-08-02热轧车轮轮箍厂设计(design of wheel and tyre hot rolling works)以钢锭(坯)为原料,用热轧加工法生产车轮、轮箍的工厂设计。
和轮箍主要是用于铁路机车、车辆上的两种走行元件。
按结构不同车轮分为组合车轮和整体车轮。
组合车轮由分别制造的轮心和轮箍及挡圈组装而成(图1)。
整体车轮由一个轮坯整体轧制而成(图2)。
整体车轮有铸铁、铸钢和轧制几种类型,砂型铸铁和铸钢车轮现已淘汰,而新型石墨模压铸钢车轮在美国得到广泛使用,这种车轮在行车速度要求不太高的铁路中比较适用。
但中国和世界上大部分国家和地区的铁路线上现今均使用整体热轧车轮(简称整轧车轮,solid roll wheel)。
过去一个时期,机车车轮,特别是蒸汽机车用的车轮结构复杂,直径较大,不易轧制,所以采用轧制的环形件作为轮箍套在轮心上构成组合车轮。
但组合车轮的轮箍有松弛的危险,不如整体车轮安全,且整体车轮各部分尺寸可设计得较薄,从而可以减轻重量,既安全又经济。
随着蒸汽机车的逐渐被淘汰,以及内燃机车和电力机车也多使用整轧车轮,故轮箍的需求量日趋减少。
整轧车轮和轮箍在大多数国家为分别建厂生产,但也可合并为一个厂(或车间)进行生产。
中国设计建成的车轮轮箍厂就是可以生产上述两种产品的工厂。
这种工厂的一些工艺设备和辅助设施,如坯料准备、运输设备、动力泵站、水循环系统、工模具制造部门等可统一安排,共同使用,比较经济。
简史火车车轮制造历史较长。
在1814年前后,铁路运输上开始生产并使用锻制轮箍,形成组合车轮。
1853年英国制成轮箍轧机,开始大量生产热轧火车轮箍。
1902年、1904年美国和法国的辗轧车轮轧机分别问世,整体热轧车轮和轮箍开始广泛应用于铁路,从而促使铁路机车车辆的运行速度和载重量有了很大提高。
从此,整轧车轮逐步取代了铸铁、铸钢和大部分组合车轮,成为铁路车辆(包括一些机车)的主要用轮。
钢制车轮生产工艺

钢制车轮生产工艺钢制车轮生产工艺是指将钢材经过一系列的工艺流程加工成最终的车轮产品的过程。
下面将详细介绍一下钢制车轮的生产工艺。
首先是原材料的准备。
钢制车轮的主要原材料是高强度钢材,通过对钢材进行化学成分分析,以及进行金相分析,确定其质量。
然后根据车轮的设计要求,确定钢材的硬度和强度等机械性能。
第二步是钢材的预处理。
首先,对钢材进行退火处理,以消除应力和改善塑性。
然后进行锻造处理,将钢材加热到一定的温度,然后用锻压机将其锻造成具有一定形状和尺寸的车轮毛坯。
第三步是车轮的成型和加工。
首先,将锻造好的车轮毛坯进行热处理,以提高其显微组织和力学性能。
然后进行车轮的精整,通过专用的机床对车轮进行车削、铣削、钻孔等加工操作,将车轮毛坯加工成具有一定精度和表面质量的车轮毛胚。
第四步是车轮的组装。
将车轮毛胚上的轮缘和轮辐进行组装,并进行校验和调整,以确保车轮的几何尺寸和轮轴孔位的精度和间隙符合要求。
然后进行焊接等加工,将车轮的各个部件焊接在一起。
第五步是车轮的表面处理。
对车轮进行表面喷砂或喷丸处理,以去除车轮表面的氧化物等污染物。
然后对车轮进行酸洗处理,以去除车轮表面的氧化层,提高车轮的表面质量和附着力。
最后一步是车轮的检验和质量控制。
对车轮的各项技术指标进行检测,包括轮缘直径、轮缘高度、轮辐的刚度和强度等。
对车轮进行质量控制,确保产品的合格率和质量稳定性。
综上所述,钢制车轮的生产工艺包括原材料准备、钢材的预处理、车轮的成型和加工、车轮的组装、车轮的表面处理和车轮的检验和质量控制等环节。
通过这些工艺步骤,可以生产出具有高强度、高精度和表面质量稳定的钢制车轮产品。
马钢车轮生产工艺

马钢车轮生产工艺
马钢车轮是马钢集团公司生产的高质量车辆配件,采用先进的工艺和设备制造而成。
以下是马钢车轮的生产工艺的简要介绍。
首先,原材料准备。
马钢车轮的主要原材料是高强度的轮辋钢和轮辐钢,这些钢材经过严格的选材和质量检测,保证了车轮的材质符合要求。
其次,钢材的预处理。
马钢车轮的钢材经过切割、锻造和热处理等工艺,以提高材料的强度和硬度,增强车轮的耐用性和承载能力。
然后,车轮的成型。
马钢车轮采用现代化的车辆轮毂冷态穿孔成形工艺,在特定的机器设备中通过冲击加工将钢材冷态穿孔成形,从而形成车轮的基本形状。
接着,车轮的热处理。
马钢车轮经过高温处理,以调整其组织结构和性能。
热处理过程包括淬火和回火,通过控制温度和冷却速度,使车轮达到理想的硬度和韧性。
然后,车轮的机加工。
马钢车轮经过车削、铣削和钻孔等机加工工艺,以进一步精确车轮的尺寸和形状,确保其符合设计要求。
最后,车轮的表面处理和涂装。
马钢车轮经过喷砂、除锈和涂装等工艺,以增强车轮的耐腐蚀性和外观质量,延长其使用寿命。
整个生产工艺中,马钢车轮严格控制每个环节的质量,确保产品符合相关标准和规范要求。
此外,马钢还注重研发和创新,不断改进生产工艺,提高车轮的质量和性能。
总之,马钢车轮的生产工艺包括原材料准备、钢材预处理、车轮成型、热处理、机加工、表面处理和涂装等环节。
通过严格的质量控制和持续的创新改进,马钢车轮以其高质量和可靠性被广泛应用于各种车辆和机械设备中。
钢制车轮生产工序说明

钢制车轮生产工序说明 Final revision by standardization team on December 10, 2020.1.工艺流程介绍本项目生产工艺共分四部分:轮辋生产工段、轮辐生产工段、合成装配工段及涂装工段。
(1)轮辋生产工艺说明第一步:纵剪(挤):把材料按照要求宽度进行剪切(挤边:对边料边缘进行挤边去毛刺);第二步:酸洗:把材料浸入酸液中去氧化皮、锈迹;本项目酸洗采用槽内浸泡方式,除油槽用钢板制作,内壁铺PVC或聚乙烯,材料在槽内浸泡时,应注意放置的位置,避免存留空气,浸泡过程中应上下前后移动或翻动管件,使内腔溶液不断更换,以提高效果。
第三步:水洗:用水清洗材料表面酸洗液和残留污物;第四步:钝化:在材料表面形成保护膜防止加工过程中生锈;钝化采用池内槽泡方式,钝化槽钢板制作,内壁铺防酸塑料,槽内浸泡时,应注意放置的位置,避免材料内存留空气,浸泡过程中应上下前后移动或翻动方管,使内腔溶液不断更换,以提高效果。
必要时取出材料,用水气冲洗后再进行浸泡。
第五步:切割:把材料按照要求长度进行剪切;第六步:打字:在材料上按要求位置和字样打印清晰标识;第七步:卷圆:把材料由条形按要求卷制成圆形;第八步:压端头:把卷制成圆形的工件两端压平整;第九步:对焊:将压平后的工件两端烧化焊接;第十步:刮渣(滚压、端切):把工件焊接处上下两平面焊渣刮除干净;滚压:对焊接处上下两平面进行滚压,要求厚度与其它位置一致;端切:对焊接处两端焊渣进行切除;第十一步:冷却:对工件进行降温冷却;第十二步:修磨:对工件焊接处残留焊渣进行清除;第十三步:复圆:对工件焊缝和焊缝两边进行复圆消除不圆度;第十四步:扩口:把工件两端扩成要求的角度和直径;第十五步:旋压:对工件进行旋压成型底槽R并确认定位点;第十六步:一序滚压成型:对工件进行滚压预成形底槽等各部形状;二序滚压成型:对工件进行滚压成形底槽和胎圈座部位;三序滚压成型:对工件进行滚压成形胎圈座和轮缘部位。
钢铁冶炼流程详解,各版本都有!

钢铁冶炼流程详解,各版本都有!
1
图文版
钢铁生产工艺总流程
1.炼焦生产流程
炼焦生产流程:炼焦作业是将焦煤经混合,破碎后加入炼焦炉内经干馏后产生热焦碳及粗焦炉气之制程。
2.烧结生产流程
烧结生产流程:烧结作业系将粉铁矿,各类助熔剂及细焦炭经由混拌、造粒后,经由布料系统加入烧结机,由点火炉点燃细焦炭,经由抽气风车抽风完成烧结反应,高热之烧结矿经破碎冷却、筛选后,送往高炉作为冶炼铁水之主要原料。
3.高炉生产流程
高炉生产流程:高炉作业是将铁矿石、焦炭及助熔剂由高炉顶部加入炉内,再由炉下部鼓风嘴鼓入高温热风,产生还原气体,还原铁矿石,产生熔融铁水与熔渣之炼铁制程。
4.转炉生产流程
转炉生产流程:炼钢厂先将熔铣送前处理站作脱硫脱磷处理,经转炉吹炼后,再依订单钢种特性及品质需求,送二次精炼处理站进行各种处理,调整钢液成份,最后送大钢胚及扁钢胚连续铸造机,浇铸成红热钢胚半成品,经检验、研磨或烧除表面缺陷,或直接送下游轧制成条钢、线材、钢板、钢卷及钢片等成品。
5.连铸和连轧
连铸连轧:是把液态钢倒入连铸机中铸造出钢坯(称为连铸坯),然后不经冷却,在均热炉中保温一定时间后直接进入热连轧机组中轧制成型的钢铁轧制工艺。
2
动画版
3
视频版
各钢厂钢材生产工艺流程各有不同,文章篇幅有限,不能一一详述,如有错误敬请指正!
来源:材易通宝钢股份。
- 1、下载文档前请自行甄别文档内容的完整性,平台不提供额外的编辑、内容补充、找答案等附加服务。
- 2、"仅部分预览"的文档,不可在线预览部分如存在完整性等问题,可反馈申请退款(可完整预览的文档不适用该条件!)。
- 3、如文档侵犯您的权益,请联系客服反馈,我们会尽快为您处理(人工客服工作时间:9:00-18:30)。
• VD炉布置形式: 双罐位、半高架式 • 公称容量:100吨, 最大110吨 • 主要功能:脱氢、 脱氮、脱氧、去除 夹杂。
VD炉具有如下优点: • 脱氢率高,高达60~90%; • 脱氧效果好,经真空处理后,钢水氧 含量≤20ppm; • 去夹杂物效果好,钢中夹杂物总量及 形态都得到明显的改善; • 脱气过程中,[S]进一步降低。
马钢第一钢轧总厂 车轮钢冶炼工艺过程简介
吴耀光 2010-10-21
•
•
车轮、轮箍是从事铁路运输的货车、旅客列 车、机车的重要行走部件。随着国民经济的 快速提升,铁路运输迅速向高密度、高速、 重载方向发展,车轮、轮箍的质量直接关系 到铁路运输的安全,直接关系到和谐社会的 建设,已上升到质量安全的政治高度,还关 系到企业的经济效益和声誉。 不断提高马钢车轮产品的内在质量,以满足 铁路运输事业快速发展的质量安全需要,是 我们的首要任务。
马钢车轮、轮箍生产的发展历程
平炉→模铸 平炉→喷粉,喂线→模铸 平炉→SKF→模铸 转炉→SKF→模铸 转炉→LF+VD→模铸 转炉→吹氩→LF精炼→VD真空→弧形圆坯连铸 (2002.4)
质量控制内容
气体含量控制: • 可以使钢中全氧含量控制在15ppm以下。 通过对原辅材料的严格管理、LF炉和VD优 化操作,确保钢水中H含量控制在2.0ppm以 下,N含量在60ppm以下。
夹杂物控制:
• 通过洁净化处理和保护浇注,以控制夹杂 物总量和夹杂物尺寸。
化学成分的均匀性和稳定性: • LF炉进行成分精确微调,以保证浇次的成 分稳定性。 • 连铸参数的科学设计和控制保证铸坯成分 的均匀性,最大限度的缩小偏析。
铸坯质量控制: • 通过对过热度与拉速的不断优化控制,保护 渣性能的优化,M-EMS对铸坯组织的控制技 术,合理科学的二次冷却方式和冷却制度优 化,有效改善了铸坯的疏松、偏析、裂纹、 晶粒度细化等问题,有效地提高了等轴晶比 率,最高可达72%。
主ห้องสมุดไป่ตู้设备介绍
• 120吨转炉(3座) • 主要功能: 脱C、脱Si、脱P、 脱S、脱氧、升温、 合金化
• LF炉公称容量: 95吨,最大处理 110吨 • 主要功能:脱硫、 温度调整、精确 的成分调整、改 善钢水洁净度、 造渣。
LF炉具有如下优点: • • • • 能够准确的调整温度; 准确的调整钢水成分; 优越的合金化条件; 深脱硫。
全弧形连铸机 • 铸坯弧形半径: R=12m • 铸机流数: 三机三流, 流间距: 1800mm
• 主要功能: 成型、去除 夹杂物,给 车轮公司提 供合格的连 铸坯
• 铸坯尺寸:380mm、450mm • 注流保护:大包长水口+浸入式水口+ 结晶器保护渣 • 电磁搅拌:M-EMS • 二冷方式:气雾冷却 • 矫直机:三点五机架矫直