断口的宏观形貌、微观形态及断裂机理
疲劳断口宏观分析

1 疲劳断口的形貌特征疲劳断口是指金属材料或零构件在疲劳断裂过程中形成的一种匹配的表面,称断裂面或断口。
分析它的目的在于确定零构件是否属于疲劳破坏?其破坏的原因是什么?从而提出防止事故的措施和方法,为今后的设计、选材以及加工等问题提出改进意见。
对断口的形貌进行分析包括两个方面,即宏观断口分析和微观断口分析。
所谓宏观分析是指用肉眼或20—30倍以下放大镜观察断口的形貌特征。
微观分析是指用光学显微镜或电子显微镜对断口进行分析。
宏观分析不要求专门设备,被观察断口尺寸不受限制,可以观察断件和断口全貌,了解各个方面变化情况,所以说宏观分析是断口分析的基础。
微观分析是用高倍的光学显微镜、c透射电镜,扫描电镜对断口进行分析,能观察断口的精细结构及裂纹形态。
1.1 疲劳断口宏观特征由于零构件经常承受拉、压、弯、扭或复合应力的作用,因载荷类型不同,在宏观断口上表现出的形貌特征也不相同。
(1)弯曲应力作用下的疲劳断口图1-2是在弯曲疲劳载荷作用下的断口示意图。
零件在弯曲疲劳载荷作用下,其表面应力最大,中心应力最小,疲劳源首先在表面形成,然后沿着与最大正应力相垂直方向扩展,到最后瞬断。
图中(a)是单向弯曲疲劳断口,它的疲劳源首先在受拉应力一侧表面形成,瞬断区在疲劳源相对侧,其面积大小由材料抗拉强度和外加载荷的大小来决定。
图中(b)是双向弯曲疲劳断口,由于双向弯曲,试件上下两侧交替承受拉应力作用,故疲劳源在相对两侧面形成,瞬断区在中间。
图1-3是轴在旋转弯曲应力作用下的疲劳断口示意图,由于旋转弯曲应力也是表面最大,中心最小,疲劳源也开始于表面,且疲劳源两侧裂纹发展速度较中心快,故贝纹线比较扁平。
最终瞬断区虽然也在疲劳源对面,但总是相对于轴的旋转方向逆偏转一个角度,此种现象称为偏转现象。
因此,从疲劳源与瞬断区的相对位置便能推知轴的旋转方向。
轴上有无应力集中及应力集中大小,其最终瞬断区的位置是不同的。
若应力集中较小时,疲劳源只在一处发生,最终瞬断区在疲劳源相对应的一侧。
合金钢冶金缺陷断口的宏观形貌和微观形态

合金钢冶金缺陷断口的宏观形貌和微观形态1 纤维状断口断口特征:呈暗灰绒毯状,无结晶颗粒,断口边缘常有显著的塑性变形,形成剪切唇。
微观特征;多为等轴状和抛物线状韧窝。
纤维状断口一般属于钢材的正常断口,它表示钢材有良好的韧性。
2 萘状断口宏观特征:较平坦的粗晶断口,用掠射光照射时,由于各晶面具有不同的反光能力,因而闪烁着结晶萘一般的光泽。
微观特征:准解理或解理特征。
河流很短,有时出现舌状花样。
局部有硫化锰析出,它们可能沿原始奥氏体晶界析出或沿奥氏体晶面析出。
萘状断口分别是合金结构钢和高速钢因过热或重复淬火而产生的一种粗晶缺陷。
为不允许存在的断口。
3 结晶状断口宏观特征:断口齐平,呈亮灰色,有强烈的金属光泽和明显的结晶颗粒。
微观特征:解理或准解理断裂。
4 横列结晶断口:宏观特征:与加工方向成一定角度的灰色小平面,一般多出现在相当于钢锭的柱状晶发达部位。
微观特征:一般为沿柱状晶粒边界断裂的韧性晶界断口,韧窝尺寸变化大,其中有夹杂物。
5 瓷状断口宏观特征:类似细碎片的断口,呈亮灰色。
微观特征:准解理断口为主。
瓷状断口对于淬火后低温回火的钢平说属于正常断口。
对于淬火后中温或高温回火的钢来说,表明热处理工艺不当。
6 非金属夹杂断口宏观特征:为各种颜色的非结晶的条状或块状缺陷。
微观特征:缺陷区为大量的颗粒状非金属夹杂物,其种类随钢种不同而异。
7 偏析线断口宏观特征:为反射能力较强的银亮色线条,其方向与加工方向相同。
酸性平炉钢大锻件的偏析线多为粗而亮,而碱怍电炉钢薄壁管的偏析线多为细而密的。
微观特征:为穿晶断口。
偏析线处为光滑的沟坑,其中布满夹杂物。
在粗而亮的偏析线中多为不易变形的硫化钙、氧化铝和氮化铝等,在细而密在偏析线中多为可变形的硫化物。
金属断口机理及分析
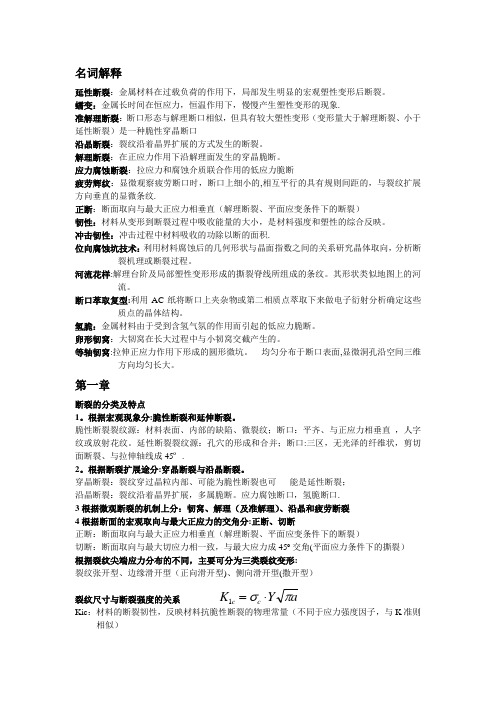
名词解释延性断裂:金属材料在过载负荷的作用下,局部发生明显的宏观塑性变形后断裂。
蠕变:金属长时间在恒应力,恒温作用下,慢慢产生塑性变形的现象.准解理断裂:断口形态与解理断口相似,但具有较大塑性变形(变形量大于解理断裂、小于延性断裂)是一种脆性穿晶断口沿晶断裂:裂纹沿着晶界扩展的方式发生的断裂。
解理断裂:在正应力作用下沿解理面发生的穿晶脆断。
应力腐蚀断裂:拉应力和腐蚀介质联合作用的低应力脆断疲劳辉纹:显微观察疲劳断口时,断口上细小的,相互平行的具有规则间距的,与裂纹扩展方向垂直的显微条纹.正断:断面取向与最大正应力相垂直(解理断裂、平面应变条件下的断裂)韧性:材料从变形到断裂过程中吸收能量的大小,是材料强度和塑性的综合反映。
冲击韧性:冲击过程中材料吸收的功除以断的面积. 位向腐蚀坑技术:利用材料腐蚀后的几何形状与晶面指数之间的关系研究晶体取向,分析断裂机理或断裂过程。
河流花样:解理台阶及局部塑性变形形成的撕裂脊线所组成的条纹。
其形状类似地图上的河流。
断口萃取复型:利用AC 纸将断口上夹杂物或第二相质点萃取下来做电子衍射分析确定这些质点的晶体结构。
氢脆:金属材料由于受到含氢气氛的作用而引起的低应力脆断。
卵形韧窝:大韧窝在长大过程中与小韧窝交截产生的。
等轴韧窝:拉伸正应力作用下形成的圆形微坑。
均匀分布于断口表面,显微洞孔沿空间三维方向均匀长大。
第一章断裂的分类及特点1。
根据宏观现象分:脆性断裂和延伸断裂。
脆性断裂裂纹源:材料表面、内部的缺陷、微裂纹;断口:平齐、与正应力相垂直 ,人字纹或放射花纹。
延性断裂裂纹源:孔穴的形成和合并;断口:三区,无光泽的纤维状,剪切面断裂、与拉伸轴线成45º .2。
根据断裂扩展途分:穿晶断裂与沿晶断裂。
穿晶断裂:裂纹穿过晶粒内部、可能为脆性断裂也可 能是延性断裂; 沿晶断裂:裂纹沿着晶界扩展,多属脆断。
应力腐蚀断口,氢脆断口. 3根据微观断裂的机制上分:韧窝、解理(及准解理)、沿晶和疲劳断裂 4根据断面的宏观取向与最大正应力的交角分:正断、切断正断:断面取向与最大正应力相垂直(解理断裂、平面应变条件下的断裂) 切断:断面取向与最大切应力相一致,与最大应力成45º交角(平面应力条件下的撕裂) 根据裂纹尖端应力分布的不同,主要可分为三类裂纹变形:裂纹张开型、边缘滑开型(正向滑开型)、侧向滑开型(撒开型)裂纹尺寸与断裂强度的关系Kic :材料的断裂韧性,反映材料抗脆性断裂的物理常量(不同于应力强度因子,与K 准则相似)a Y K c c πσ⋅=1:断裂应力(剩余强度) a :裂纹深度(长度) Y:形状系数(与试样几何形状、载荷条件、裂纹位置有关) 脆性材料K 准则:KI 是由载荷及裂纹体的形状和尺寸决定的量,是表征裂纹尖端应力场强度的计算量; KIC 是材料固有的机械性能参量,是表示材料抵抗脆断能力的试验量第二章裂纹源位置的判别方法: T 型法(脆断判别主裂纹),分差法(脆断判别主裂纹),变形法(韧断判别主裂纹),氧化法(环境断裂判别主裂纹),贝纹线法(适用于疲劳断裂判别主裂纹). 断口的试样制备:截取,清洗,保存。
金属材料断口机理及分析
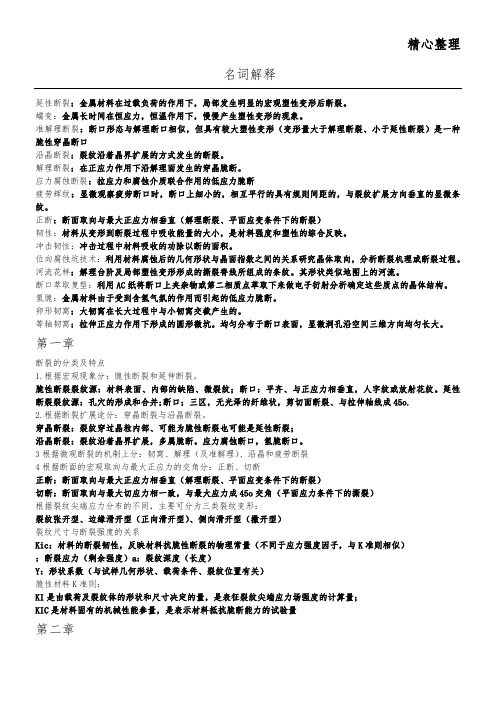
精心整理名词解释延性断裂:金属材料在过载负荷的作用下,局部发生明显的宏观塑性变形后断裂。
蠕变:金属长时间在恒应力,恒温作用下,慢慢产生塑性变形的现象。
准解理断裂:断口形态与解理断口相似,但具有较大塑性变形(变形量大于解理断裂、小于延性断裂)是一种脆性穿晶断口沿晶断裂:裂纹沿着晶界扩展的方式发生的断裂。
解理断裂:在正应力作用下沿解理面发生的穿晶脆断。
应力腐蚀断裂:拉应力和腐蚀介质联合作用的低应力脆断疲劳辉纹纹。
正断韧性: 河流花样 氢脆:卵形韧窝等轴韧窝1.2.34裂纹张开型、边缘滑开型(正向滑开型)、侧向滑开型(撒开型) 裂纹尺寸与断裂强度的关系Kic :材料的断裂韧性,反映材料抗脆性断裂的物理常量(不同于应力强度因子,与K 准则相似) :断裂应力(剩余强度)a :裂纹深度(长度)Y :形状系数(与试样几何形状、载荷条件、裂纹位置有关) 脆性材料K 准则:KI 是由载荷及裂纹体的形状和尺寸决定的量,是表征裂纹尖端应力场强度的计算量; KIC 是材料固有的机械性能参量,是表示材料抵抗脆断能力的试验量第二章裂纹源位置的判别方法:T型法(脆断判别主裂纹),分差法(脆断判别主裂纹),变形法(韧断判别主裂纹),氧化法(环境断裂判别主裂纹),贝纹线法(适用于疲劳断裂判别主裂纹)。
断口的试样制备:截取,清洗,保存。
断口分析技术设备:1.宏观断口分析技术(用肉眼,放大镜,低倍率光学显微镜观察分析)2.光学显微断口分析(扫描电子显微镜光学显微镜,透射电子显微镜),3.电镜断口分析。
第三章延性断裂:12.3.1(1约成45(2(321.2.(1)内颈缩扩展:质点大小、分布均匀,韧窝在多处形核(裂纹萌生),随变形增加,微孔壁变薄,以撕裂方式连接(2)剪切扩展:材料中具有较多夹杂物,同时具有细小析出相时,微孔之间可能以剪切方式相连接。
注意:内颈缩扩展与剪切扩展在同一韧窝断口上可能同时发生。
影响韧窝的形貌因素:夹杂物或第二相粒子,基体材料的韧性,试验温度,应力状态。
6-断口失效分析技术
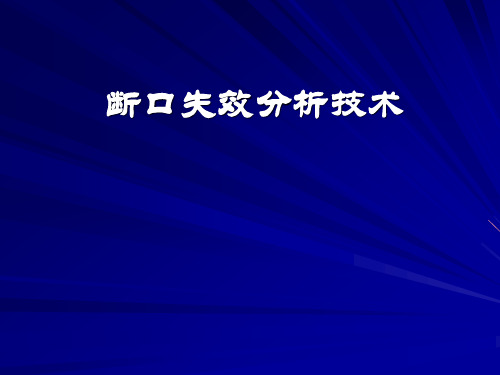
工程中的疲劳断裂
微动磨蚀疲劳-两个紧配合零件表面之 间发生周期性的、幅值极小的相对运动 而造成的磨损腐蚀疲劳
a
b
40CrNiMoA钢旋翼梳状接头耳孔的微动磨蚀 疲劳断口形貌 a.磨蚀坑 b.磨蚀裂纹
68
工程中的疲劳断裂
多次冲击疲劳-承受冲击载荷的零件, 如锤杆、凿岩机活塞和钎尾等,其冲 击能量小于一次冲击断裂的能量,经 多次(>1000次)冲击后发生断裂, 称为小能量多次冲击疲劳
f.4000×
c.900×
d.1000×
e.1200×
59
铸镁合金脆性疲劳辉 纹的形貌
依据微观变形: a.延性疲劳辉纹:光滑连续 b.脆性疲劳辉纹:放射解理台 阶分割
60
请仔细辨认易混淆的花样
61
工程中的疲劳断裂
高周疲劳、低周疲劳和高低周复 合疲劳
800×
800×
高低周复合应力疲劳断口的微观形貌 a.多条复合辉纹 b.单条复合辉纹
按照断裂过程的先后有三个 明显的特征 疲劳源区 扩展区 瞬断区 特点 名义应力远低于屈服,甚 至低于弹性极限 缺陷、表面、形状、环境 敏感性 突然性
分类: (载荷、寿命)低周、 高周 (载荷)轴向疲劳:拉 -拉、拉-压、脉动;弯 曲(单向、双向、旋转) 扭转、振动 (载荷源、环境)机械、 热、高温、腐蚀、接触、 微动等
通过二次解 理形成的解 理台阶
解理裂纹与螺位错相交形成 解理台阶的示意图
42
河流花样形成过程示意图
特征2—河流花样
43
特征3—舌状花样
解理舌状花样 SEM 2000×
舌状花样的形成示意图
44
特征4—鱼骨花样
解理羽毛状花样1000× 鱼骨状花样2000×
断口分析及其微观机制
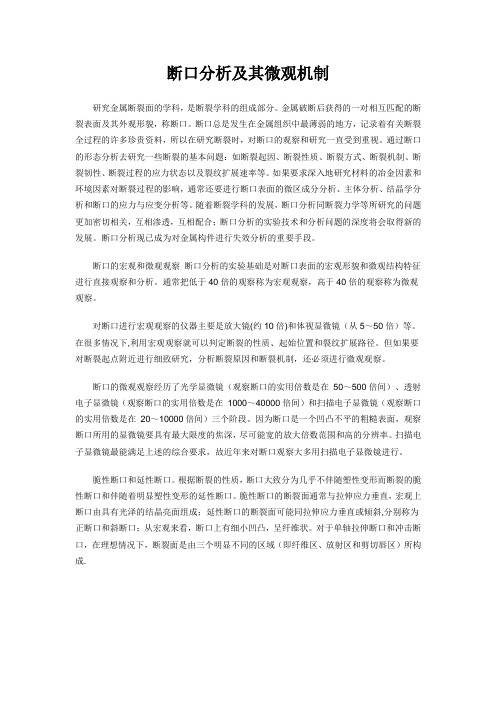
断口分析及其微观机制研究金属断裂面的学科,是断裂学科的组成部分。
金属破断后获得的一对相互匹配的断裂表面及其外观形貌,称断口。
断口总是发生在金属组织中最薄弱的地方,记录着有关断裂全过程的许多珍贵资料,所以在研究断裂时,对断口的观察和研究一直受到重视。
通过断口的形态分析去研究一些断裂的基本问题:如断裂起因、断裂性质、断裂方式、断裂机制、断裂韧性、断裂过程的应力状态以及裂纹扩展速率等。
如果要求深入地研究材料的冶金因素和环境因素对断裂过程的影响,通常还要进行断口表面的微区成分分析、主体分析、结晶学分析和断口的应力与应变分析等。
随着断裂学科的发展,断口分析同断裂力学等所研究的问题更加密切相关,互相渗透,互相配合;断口分析的实验技术和分析问题的深度将会取得新的发展。
断口分析现已成为对金属构件进行失效分析的重要手段。
断口的宏观和微观观察断口分析的实验基础是对断口表面的宏观形貌和微观结构特征进行直接观察和分析。
通常把低于40倍的观察称为宏观观察,高于40倍的观察称为微观观察。
对断口进行宏观观察的仪器主要是放大镜(约10倍)和体视显微镜(从5~50倍)等。
在很多情况下,利用宏观观察就可以判定断裂的性质、起始位置和裂纹扩展路径。
但如果要对断裂起点附近进行细致研究,分析断裂原因和断裂机制,还必须进行微观观察。
断口的微观观察经历了光学显微镜(观察断口的实用倍数是在50~500倍间)、透射电子显微镜(观察断口的实用倍数是在1000~40000倍间)和扫描电子显微镜(观察断口的实用倍数是在20~10000倍间)三个阶段。
因为断口是一个凹凸不平的粗糙表面,观察断口所用的显微镜要具有最大限度的焦深,尽可能宽的放大倍数范围和高的分辨率。
扫描电子显微镜最能满足上述的综合要求,故近年来对断口观察大多用扫描电子显微镜进行。
脆性断口和延性断口。
根据断裂的性质,断口大致分为几乎不伴随塑性变形而断裂的脆性断口和伴随着明显塑性变形的延性断口。
金属断口分析
延性断裂为金属材料在过载负荷的作用下,局部发生明显的宏观塑性变形后断裂。延性断裂分两种,一种是韧窝-微孔聚集型断裂;另一种是滑移分类断裂。一些高强度材料其裂缝扩展阻力较小,对裂纹十分敏感,较小的裂纹
即可使其产生宏观脆性的低应力断裂,其断口为韧窝状,断裂机制是微孔聚
集型。
第一节韧窝断口的宏观形貌特征
从宏观上看,断裂分为脆性断裂和延性断裂
脆性断裂指以材料表面、内部的缺陷或是微裂纹为源,在较低的应力水平下(一般不超过材料的屈服强度),在无塑性变形或只有微小塑性变形下裂纹急速扩展。在多晶体中,断裂时沿着各个晶体的内部解理面产生,由于材料的各个晶体及解理面方向是变化的,因此断裂表面在外观上呈现粒状。脆性断裂主要沿着晶界产生,称为晶间断裂。其断口平齐。
此外,高强度马氏体钢纤维区还有环状花样特征。
第二节韧窝断口的微观形貌特征
韧窝断口的微观特征是一些大小不等的圆形或是椭圆形的凹坑(即韧窝)
在韧窝内经常看到夹杂物或是第二相粒子。
凹坑形状有等轴韧窝、剪切韧窝和撕裂韧窝三种,其形状与应力状态。
等轴韧窝是圆形微坑,在拉伸正应力作用下形成的。应力在整个断口表面分布均匀。
2.分叉法
样品断裂中,产生许多分叉,裂纹分叉的方向为裂纹扩展方向,扩展的反方向为裂源位置。
【注】T型法和分叉法是判别脆性断裂的主裂纹和裂纹源
3.变形法
延性断裂的样品,在断裂过程中发生变形后碎成几块,将碎片拼合后变形量大的部位为主裂纹,裂纹源在主裂纹所在的断口上
4.因环境因素引起的断裂的样品,如应力腐蚀、氢脆。裂纹源位于腐蚀或是
延性断裂是在较大的塑性变形产生的断裂。它是由于断裂缓慢扩展而造成的。其断口表面为无光泽的纤维状。延性断裂经过局部的颈缩,颈缩部位产生分散的空穴,小空穴不断增加和扩大聚合成微裂纹。
材料断口分析(第二至四章)
§2、解理断口形貌特征
一、宏观形貌特征
1、放射状条纹
2、人字纹
3、小刻面(facet):发亮的小晶面
解理断口上的结晶面 宏观上呈无规则取向
强光下可见到闪闪发光的特征
解理断口是由许多小刻面组成 的,每个小刻面代表一个晶粒
二、微观形貌特征及形成机理
特征:
扇形花样 解理台阶(cleavage step) 河流花样(river pattern) 舌状花样(tongue pattern)
2、产生的原因是什么?
3、正火后为什么强度和塑性均有提高?
例2:
在什么条件下易出现沿晶断裂?怎样防止沿晶断裂?
例 1: 1、结晶状脆性断口(过热脆性结晶状断口) 2、产生原因: ①锻造温度过高,使原奥氏体晶粒过分粗大;
②压下量不足,晶粒破碎不够;
③终锻温度过高,发生了晶粒长大,使晶粒过粗或粗 细不均。
青鱼骨花样(spine pattern)
瓦纳线(wallner line)
扇形花样
解理台阶
河流花样
舌状花样
青鱼骨花样
瓦纳线
(二)形成机理(模型) 1、解理台阶
解理裂纹与螺位错交截形成台阶
台阶形成过程的简化图
通过二次解理或撕裂相互连接形成台阶(撕裂棱)
台阶的性质
台阶在扩展过程中会发生合并或消失(台阶高度减小) 相同方向的台阶合并后高度增加 相反方向的台阶合并后高度减小或消失 台阶高度与柏氏矢量大小、位错密度之间存在一定关系
3、正火发生可使晶粒细化,改善锻件质量。
例2
晶粒过分粗大—细化晶粒处理
晶界弱化——净化晶界 环境介质——改善工作环境 热应力——退火消除
本章完
一、宏观形貌特征
金属断裂的微观机理与典型形貌
金属断裂的微观机理与典型形貌金属断裂是指金属材料在受到应力作用下发生破裂现象。
金属断裂的微观机理和典型形貌是金属材料断裂过程中所呈现出的微观变化和破裂形态。
本文将从金属断裂的微观机理和典型形貌两个方面进行探讨。
一、金属断裂的微观机理在金属断裂的微观机理中,主要涉及到晶体的变形、晶界滑移和裂纹扩展等过程。
1. 晶体的变形金属材料的断裂是由于晶体内部发生了塑性变形。
当金属受到外力作用时,晶体内的原子会发生位移和重排,导致晶体的形状发生变化。
晶体的变形过程中,会产生位错,即晶格中的原子出现错位。
位错的运动和积累是金属材料塑性变形和断裂的基础。
2. 晶界滑移金属材料由多个晶粒组成,晶粒之间存在晶界。
晶界是晶粒内部晶格的不连续区域。
当金属受到应力作用时,晶界处的原子会沿着晶界面滑移,从而使晶粒发生形变。
晶界滑移是金属材料塑性变形和断裂的重要机制之一。
3. 裂纹扩展裂纹是金属材料中的缺陷,是断裂的起始点。
当金属受到应力作用时,应力集中在裂纹处,导致裂纹的扩展。
裂纹扩展的机理主要包括塑性扩展和脆性扩展两种形式。
塑性扩展是指裂纹周围发生塑性变形,裂纹沿着塑性区域扩展;脆性扩展是指裂纹周围没有发生塑性变形,裂纹直接沿着晶体的晶面或晶界扩展。
二、金属断裂的典型形貌金属断裂的典型形貌是指金属材料断裂后所呈现出的形态特征。
根据金属断裂的不同性质和机理,金属材料的断裂形貌可以分为韧性断裂、脆性断裂和疲劳断裂等。
1. 韧性断裂韧性断裂是指金属材料在受到较大应力时,发生大量的塑性变形和能量吸收,最终以拉伸断裂为主。
韧性断裂的断口面平滑,有明显的塑性变形迹象,断口两侧呈现出韧带状的纹理。
韧性断裂通常发生在具有良好延展性的金属材料中,如钢材、铝合金等。
2. 脆性断裂脆性断裂是指金属材料在受到较小应力时,发生较少的塑性变形和能量吸收,最终以断裂为主。
脆性断裂的断口面光洁平整,没有明显的塑性变形迹象,断口两侧呈现出晶粒状的纹理。
脆性断裂通常发生在具有较低延展性的金属材料中,如铸铁、高碳钢等。
断力讲义-2(断口分析简介)
5.4 准解理断口的形貌特征
准解理断裂:介于解理与韧窝断裂之间的 断裂(回火马氏体钢)
一、宏观形貌特征
比较平整、塑性变形小,近似于解理 断口的宏观形貌
二、微观形貌特征
* 亦有解理台阶、撕裂脊线、舌状花样 * 微观上有较大的塑性变性(图4-4)
5.5 韧性断口的形貌特征
断口形貌取决于:材料类型、质量、变形 速度、应力状态、试验温度等
二、宏观形貌特征
• 三个区域:平滑区(含疲劳源)、过渡区、 瞬断区
1.疲劳源:单源、多源;表面、次表面
2 平滑区:裂纹萌生、稳定扩展; 呈脆性断口形貌
1)裂纹扩展方向,结合贝壳状、年轮、 海滩状、前沿线等宏观条纹标记来判断;
2)机械磨光标记 3)裂纹扩展区的颜色(黑、黑红) 4)疲劳台阶(多源疲劳断裂) 5)棘轮状标记(应力大、应力集中) • 贝壳状条纹 (图6-22) * 鉴别疲劳断口的重要宏观依据 * 产生、形状、变化
续的,且其长度也大致相等。
4.轮胎压痕
* 疲劳断口微观形貌特征的第二重要依据 * 轮胎压痕是疲劳断口上最小特征花样,
是在疲劳裂纹形成后,由匹配断口上的 “突起”、“刃边”等反复挤压或刻入而 引起的压痕
5.7 环境断口
1.应力腐蚀断口
金属材料、受拉应力、腐蚀环境;多源脆性 断裂,穿晶、沿晶或混晶断裂 2.氢脆断口 体心立方金属及合金;穿晶或晶间断裂 3.腐蚀疲劳断口 往往在材料表面萌生裂纹,多个疲劳源 特征:有腐蚀或氧化形貌、颜色(疲劳区)
5.8 其它断口
1.蠕变断口
金属材料在高温蠕变条件下,可能出现两 种晶间裂开形式:楔形裂纹,圆形或椭 圆形孔穴
2.过热断口
3.沿晶断口
5.9 失效分析概论
- 1、下载文档前请自行甄别文档内容的完整性,平台不提供额外的编辑、内容补充、找答案等附加服务。
- 2、"仅部分预览"的文档,不可在线预览部分如存在完整性等问题,可反馈申请退款(可完整预览的文档不适用该条件!)。
- 3、如文档侵犯您的权益,请联系客服反馈,我们会尽快为您处理(人工客服工作时间:9:00-18:30)。
断口的宏观形貌、微观形态及断裂机理
按断裂的途径,断口可分为穿晶断裂和沿晶断裂两大类。
穿晶断裂又分为穿晶韧性断裂和穿晶解理断裂(其中包括准解理断裂)。
沿晶断裂也分为沿晶韧性断裂和沿晶脆性断裂。
下面分别加以讨论。
1.穿晶断口
(1)穿晶韧窝型断口断裂穿过晶粒内部,由大量韧窝的成核、扩展、连接而形成的一种断口。
宏观形貌:在拉伸试验情况下,总是先塑性变形,引起缩颈,然后在缩颈部位裂纹沿与外力垂直的方向扩展,到一定程度后失稳,沿与外力成45°方向快速发展至断裂。
众所周知,这种断口称为杯锥状断口。
断口表面粗糙不平,无金属光泽,故又称为纤维状断口。
微观形态:在电子显微镜和扫描电镜下观察,断口通常是由大量韧窝连接而成的。
每个韧窝的底部往往存在着第二相(包括非金属夹杂)质点。
第二相质点的尺寸远小于韧窝的尺寸。
韧窝形成的原因一般有两种形成情况:
1)韧窝底部有第二相质点的情况。
由于第二相质点与基体的力学性能不同(另外,还
有第二相质点与基体的结合能力、热膨胀系数、第二相质点本身的大小、形状等的影响),所以在塑性变形过程中沿第二相质点边界(或穿过第二相质点)易形成微孔裂纹的核心。
在应力作用下,这些微孔裂纹的核心逐渐长大,并随着塑性变形的增加,显微孔坑之间的连接部分逐渐变薄,直至最后断裂。
图3-41是微孔穿过第二相质点的示意图。
若微孔沿第二相点边界成核、扩展形成韧窝型裂纹后,则第二相质点留在韧窝的某一侧。
2)在韧窝的底部没有第二相质点存在的情况。
韧窝的形成是由于材料中原来有显微孔穴或者是由于塑性变形而形成的显微孔穴,这些显微孔穴随塑性变形的增大而不断扩展和相互连接,直至断裂。
这种韧窝的形成往往需要进行很大的塑性变形后才能够实现。
因此,在这类断口上往往只有少量的韧窝或少量变形状韧窝,有的甚至经很大的塑性变形后仍见不到韧窝。
当变形不大时,断口呈波纹状或蛇形花样,而当变形很大时,则为无特征的平面。
韧窝的形状与应力状态有较大关系。
由于试样的受力情况可能是垂直应力、切应力或由弯矩引起的应力,这三种情况下韧窝的形状是不一样的。
(2)解理与准解理断口
1)解理断口。
断裂是穿过晶粒、沿一定的结晶学平面(即解理面)的分离,特别是在低温或快速加载条件下。
解理断裂一般是沿体心立方晶格的{100}面,六方晶格的{0001}面发生的。
宏观形貌:解理断裂的宏观断口叫法很多,例如称为“山脊状断口”、“结晶状断口”、以及“萘状断口”等(见图片3-53)。
山脊状断口的山脊指向断裂源,可根据山脊状正交曲线群判定断裂起点和断裂方向。
萘状断口上有许多取向不同、比较光滑的小平面,它们象条晶体一样闪闪发光。
这些取向不同的小平面与晶粒的尺寸相对应,反映了金属晶粒的大小。
微观形态:在电子显微镜下观察时,解理断口呈“河流花样”和“舌状花样”。
2)准解理断口。
这种断口在低碳钢中最常见。
前述的结晶状断口就是准解理断口,它在宏观上类似解理断口。
准解理断口的微观形态主要是由许多准解理小平面、“河流花样”、“舌状花样”及“撕裂
岭”组成。
2.沿晶断口
沿晶断口是沿不同取向的晶粒边界发生断裂。
其产生的主要原因是由于晶界弱化,使晶界强度明显低于晶内强度而引起的。
造成晶界弱化的原因很多,例如,锻造过程中加热和塑性变形工艺不当引起的严重粗晶;高温加热时气氛中的C、H等元素浓度过高以及炉中残存有铜,渗人晶界;过烧时的晶界熔化或氧化;加热及冷却不当造成沿晶界析出第二相质点或脆性薄膜;合金元素和夹杂偏析造成沿晶界的富集;另外沿晶界的化学腐蚀和应力腐蚀等等,都可以造成晶界弱化,产生沿晶断口。
(1)沿晶韧窝型断口
若第二相质点沿晶界析出的密度很高,或因有一定密度的第二相质点再加上晶粒粗大,都会发生沿晶韧窝型断裂。
沿晶韧窝形成的原因与穿晶韧窝相同。
这种断裂的显微裂纹是沿着或穿过第二相质点成核的。
显微裂纹的扩展和连接,伴随有一定量的微观塑性变形。
在断口表面可看到许多位向不同、无金属光泽的“小棱面”或“小平面”。
这些“小棱面”或“小平面”的尺寸与晶粒尺寸相对应(如果晶粒细小,则断口表面上的“小棱面”或“小平面”用肉眼就不能看到或不明显)。
在电子显微镜下观察“小校面”或“小平面”,它是由大量韧窝组成的,韧窝底部往往存在有第二相质点(或薄膜)。
石状断口和棱面断口都是沿晶韧窝型断口。
另外,偏析线也是一种沿晶韧窝型断口。
(2)沿晶脆性断口
在沿晶脆性断口上,几乎没有塑性变形的痕迹或仅看到极少的韧窝。
例如,过烧后的断口,就是沿晶界氧化物薄膜发生的一种沿晶脆性断裂。
另外,18-8奥氏体不锈钢沿晶界大量析出碳化物后,也易产生沿晶脆断;沿晶界化学腐蚀和应力腐蚀(包括氢脆)后产生的断口,也都是沿晶脆性断口。
属于这类断口的还有层状断口和撕痕状断口等。
上面介绍的断口微观形态,是按照断裂的途径来分类的。
而实际生产中见到的断口有时往往是由几种类型并存的混合断口。
例如,石状断口中,如果“小棱面”或“小平面”不是贯穿整个断面,断口常常是沿晶和穿晶混合断口。
在实际生产中根据缺陷断口的宏观形貌和微观形态就可以判断出缺陷的类型、缺陷产生的原因和应采取的对策。
例如某厂生产的迫击炮炮尾,在试炮时经常发生折断的情况,经断口试验发现是石状断口,经选区电子衍射分析确认韧窝底部的析出相颗粒是MnS再结合现场调查认为该缺陷产生的原因是终锻前的加热温度过高,终锻时的变形程度过小造成的。
由于加热温度高,使奥氏体晶粒粗大,并使MnS大量溶入基体,锻后冷却时,MhS沿粗大的奥氏体晶界析出,造成晶界严重弱化所致,后来改变预制坯的尺寸以增大终锻的变形量,并降低终锻前的加热温度,问题就圆满地解决了。
又例如某厂生产的Cr—Ni—Mo—V钢某种大型轴类锻件,在运行中发生的脆性断裂,经断口检验发现:此类锻件存在有棱面断口。
该锻件用的钢是在5t碱性电弧炉中用氧化法冶炼的,锭重2.2t,锻造加热温度为1180~
1200℃,保温3h以上,锻后立即送热处理炉进行退火、扩氢处理,然后进行粗加工和调质处理。
调质后在两端切取试片,作纵向断口检验,发现有棱面断口,棱面断口大多出现在大型锻件的心部,而锻件边部仍为正常的纤维状断口,金相组织中有沿原粗大奥氏体晶界的析出相的链状网络。
棱面断口的微观形态,韧窝内的析出相为不规则的四边形,呈薄片状,经选区电子衍射确定为AlN。
由AlN的等温析出曲线可见,在约900℃缓慢冷却时,将有大量的AlN析出。
根据上述检验结果分析认为:
1)该Cr—Ni—Mo—V钢大型轴类锻件,其棱面断口主要是在锻造加热时温度较高,保温时间过长,在锻后缓冷过程中,固溶入基体的大量AlN呈薄片状沿粗大的奥氏体晶界呈链状网络析出,造成微孔聚合型沿晶断裂而形成的。
奥氏体晶粒越粗大,析出相密度愈高,晶界弱化愈严重。
2)锻造高温加热的时间越长,固溶人基体的AlN越多,随后缓冷过程中形成校面断口的倾向越大,因此适当控制锻造加热规范是很重要的。
3)由于AlN在奥氏体区析出峰值的温度约为900℃,其析出相随保温时间的延长而增加。
因此,采取降低待料温度,增加一次过冷工艺,则能加快锻后冷却速度,减少锻件在奥氏体区AlN析出峰值温度的停留时间,因而就能抑制AlN沿粗大奥氏体晶界的析出。
生产实践证明,这是避免Cr—Ni—Mo—V钢锻件产生棱面断口的有效措施。