工业工程学6-秒表测时法
基础工业工程工作抽样

(1 0.25) 4 0.25 0.0025
4800次
n (1 P)Z 2 (1 0.3) 4 3733次 PS 2 0.3 0.0025
注意:P为观察事件发生率
2024/10/9
18
练习:对某机器作业率进行观察,估计该机 器停机率为25.6%,需要观察精度旳绝对精度为 0.01,可靠度为95%,求需观察旳次数。
20次观察时刻旳 顺序
1
午休
2
3
*4
5
×
6
7
8
×
9
*10
×
×
×
11
12
13
14
15
*16
17
18
表8-10由 时刻随机 数表换算 观察时刻
注:前面 标有
“*”为 追加观察 时间,因 要减去午 休旳3次
。
25
2)利用系统抽样原理拟定观察时刻 书上例子旳阐明:
✓ 例8-2 设在某厂旳一种车间实施工作抽样。决定观察5 天,每天观察20次,该车间上午8时上班,下午5时下 班,中午12时至下午1时为午间休息。试拟定每天观察 时刻。
首先,选择每个观察旳列号。为预防每天在同一时刻观察 会产生偏差,一般可用骰子来选择使用不同旳列号码。
2024/10/9
23
✓ 其次,根据随机时刻表进行换算观察时间。因为作业开 始时间为8:00,所以随机时刻表旳列上时间全部加上8 个小时。例如用骰子选择了第一列,(19)0: 05+8=8:05即8时05分。表8-10显示了此实例旳20次 旳换算时刻。
一、作业测定概述 二、秒表测时法 三、工作抽样 四、预定动作时间 五、原则资料法
2024/10/9
内容安排
7.基础工业工程__第7章_秒表时间研究

一、秒表实验研究的含义 二、秒表时间研究的特点 三、秒表时间研究的适用对象
基础工业工程
一、秒表时间研究的含义
秒表时间研究是作业测定技术中的一种常用方法, 也称直接时间研究——密集抽样。 秒表时间研究是在一段时间内运用秒表或电子计时 器对操作者的作业执行情况进行直接、连续地观测, 把工作时间和有关工作的其他参数,以及与标准概 念相比较的对执行情况的估价等数据,一起记录下 来,并结合组织所制定的宽放政策,来确定操作者 完成某项工作所需的标准时间的方法。
方法。
4.掌握秒表测时标准时间的定义及其构成,领会标准 时间计算的几个主要公式,并能正确计算标准时间。
基础工业工程
☆教学内容
第一节 秒表时间研究的含义、特点和适用对象
第二节 秒表时间研究的工具 第三节 秒表时间研究的步骤 第四节 常用的几种评定方法 第五节 作业评定的培训及应用案例 复习与思考
基础工业工程
基础工业工程
3. 时间研究表格
时间研究表是指记录、汇总与分析时间研究观测数 据的各种表格。 时间研究记录表要记载与时间研究有关的所有详细 资料及每单元的时间及评比资料。 表7-1列示了一种时间研究记录表形式。如果作业 时间短而循环进行时,利用表7-2所示的表格式样 比较方便。几种时间研究表也可以合成为一张表。 表7-3、表7-4是常用的较详细的时间研究表格,其 正面(表7-3)为记录一切有关当时实际状况的资 料,研究表的反面(表7-4)为现场记录之用。
✓ ③可将操作内生产工作(有效时间)与非生产工作(无效时间) 分开。
✓ ④各单元分别评比,使标准时间更为精确,尤其高度疲劳单 元应独立,这样其疲劳宽放时间的确定会更加合理。
基础工业工程
秒表时间研究

归零法 累计测时法 累计测时法 周程测时法 周程测时法 测时 连续测时法 连续测时法
LOGO
第三步骤: 第三步骤:测量时间
剔除异常值
某一单元的秒表读数, 由于一些外 某一单元的秒表读数, 来因素的影响, 来因素的影响,而使其超出正常范围 的数值 剔除异常值常用的方法——三倍标 剔除异常值常用的方法——三倍标 —— 准差法。 准差法。
LOGO
第四步骤: 第四步骤:正常時間
所谓正常时间则是以一种不快不慢的正常速度 完成工作所需要的时间 评比
评比就是时间研究人员将所观测到的操作者的 操作速度,与自己理想中的理想速度(正常速度 操作速度,与自己理想中的理想速度 正常速度 )作一想像的比较 作一想像的比较
LOGO
理想速度(正常速度)的建立
X= 21 σ =2
管制上限: + × 管制上限:21+(3×2)=27 管制下限: - × 管制下限:2l-(3×2)=15
超出管制 上限,要剔除 上限 要剔除
LOGO
第三步骤: 第三步骤:测量时间
误差界限法 此法计算观测次数N的公式如下 误差为± % 的公式如下(误差为 此法计算观测次数 的公式如下 误差为±5% 可靠度为95% ; ,可靠度为 %);
100分法 分法 观测时间18s,你的评比为 你的评比为133 观测时间 你的评比为
LOGO
第四步骤: 第四步骤:正常時間
熟练 超佳 调整系数 身体部位 足踏 两手 6 2 5 5 优
努力
平准化法 平准化法
良 平均
工作环境 可
一致性 欠佳
客观评比 2
实际值
评比系数K =
预定时间标准 ×100% 相同单元实测平均时间
LOGO
【IE知识】81个IE(工业工程)专业术语,基础掌握牢很重要!

【IE知识】81个IE(工业工程)专业术语,基础掌握牢很重要!展开全文1.标准工时/标准时间在适宜的操作条件下,用最合适的操作方法,以普通熟练工人的正常速度完成标准作业所需的劳动时间标准时间=正常时间*(1 宽放率)=(观测时间*评比系数)*(1 宽放率)2.工时定额对某种作业的工时规定一个额度,即使对同一作业,由于用途不同可能有不同量值的定额,如现行定额、计划定额、目标定额等3.标准时间与工时定额的关系标准时间是制定工作定额的依据、工时定额是标准时间的结果4.时间研究时间研究是一种作业测定技术,旨在决定一位合格、适当、训练有素的操作者,在标准状态下,对一特定的工作以正常速度操作所需要的时间5.时间研究的研究方法时间研究是用抽样调查技术来对操作者的作业进行观测,以决定作业的时间标准6.剔除异常值的方法三倍标准偏差法:正常值为x /-3 内的数据,超出者为异常值7.每一单元的平均操作时间平均操作时间=Σ(观测时间值)/ 观测次数8.正常时间正常时间=Σ(单元观测时间X单元评比百分率)/ 观测次数9.宽放时间的种类私事宽放\疲劳宽放\周期动作宽放时间\干扰宽放时间\临时宽放时间\政策宽放时间\程序宽放10.宽放率宽放率(%)=(宽放时间/正常时间) X100%11.宽放时间宽放时间=正常时间X宽放率12.标准时间标准时间=平均操作时间X评比宽放时间13.瓶颈生产线作业工时最长的工站的标准工时称之为瓶颈\产出的速度取决于时间最长的工站14.实测时间作业者完成操作的实际时间15.节拍根据生产计划所得的一个工程所需的时间16.平衡率生产线各工程工作分割的均衡度,用于衡量流程中各工站节拍符合度的一个综合比值=Σ(T1 T2 ...... Tk)/Tbottleneck*K17.不平衡率生产线各工程工作分割的不均衡度不平衡率=(最大值-最小值)/平均值*100%18.平衡损失平衡损失=瓶颈工站的实际时间×工站数×FG-正常时间19.操作损失生产中异常及不良造成的损失操作损失=(设定产能-实际产量)?单件标准时间-额外产出工时=不良品损失计划外停线(机)工时20.总损失总损失=稼动损失平衡损失操作损失21.快速切换通过各种手段,尽可能的缩短作业切换时间,以减少时间浪费,达成提高综合效益之目的22.作业切换时间是指前一品种加工结束到下一品种加工出良品的这段时间23.外部切换时间不必停机也能进行的切换作业时间24.内部切换时间必须停机才能进行的切换以及为保证质量进行的调整、检查等占用的切换时间25.JIT的基本思想只在需要的时候、按需要的量、生产所需的产品,故又被称为准时制生产、适时生产方式、广告牌生产方式26.JIT的核心零库存和快速应对市场变化27.劳动定额的时间构成劳动定额的时间构成=作业时间布置工作地时间休息与生理需要时间准备与结束时间/批量劳动定额的时间构成可供时间:上班时间内,为某产品生产而投入的所有时间可供工时=可供时间 *人数-借出工时投入工时=可供工时-计划停线工时稼动率=投入工时/可供工时 *100%计划停线工时=计划停线时间*人数计划停线时间=无计划时间换线时间判停时间设定产能(H) =3600(S)/瓶颈时间(S)设定产能(班)=投入时间/瓶颈时间(S)总工时=瓶颈时间*作业人数实际产量是可供时间内所产出的良品数人均产能=实际产量/投入时间/人数单机台产能=实际产量/投入时间/机台数平衡损失=(总工时-单件标准时间)*设定产能操作效率=实际产量/设定产能*100%整体工厂效率(OPE)=平衡率*稼动率*操作效率平衡损失=(瓶颈*作业人数-单件标准时间)*设定产能操作损失=(设定产能-实际产量)*单件标准时间-额外产出工时=不良品损失计划外停线(机)工时28.工费率平均每小时发生费用=单位时间内发生总费用/单位时间内投入工时29.单件成本平均每件分摊成本=某批产品花费总成本/该批产品总量30.成本下降率Σ[(上期单件成本-本期单件成本)*实际产量]/Σ(上期单件成本*实际产量)*100%31.机会成本机会成本=投资额*行业平均盈利率经营收益=收益-机会成本节省成本﹕=(改善前需求工时-改善后需求工时)*工费率交付周期=∑(CT*批量)32.所有机器效率=Total S.T*Output/(可利用时间*机台数)人工利用率 = 人工操作时间*目标产能/工作时间机器稼动率 = 机器作业时间*目标产能/工作时间MFG效率=实际产量/除非计划停机损失后可生产数量总生产效率=实际产量/可生产数量33.无效时间指花费在进行与生产不是有直接关系的活动之时间,如:开会,培训,消防演习,健康枪查,5S等.34.生产是一切社会组织将它的输入转化为输出的过程,是人们创造物质产品的有组织的活动35.时间序列模型以时间为独立变量,利用过去需求随时间变化的关系来预测未来的需求36.预测监控通过预测监控来检验过去起作用的预测模型是否仍然有效37.因果关系模型利用变量(包括时间,如广告投入vs销量)之间的相互关系,通过一种变量的变化来预测另一种变量的未来变化38.CYCLE TIME(C/T)周期时间每单位工序中1个循环的作业所需的时间单位工序C/T的和/ 测试次数39.(T/T)节拍时间制造一件物品时所需要的实际时间作业时间/ 需求数40.NECK TIME整个工序中1个循环作业时间最长的工序时间=最大的CYCLE TIME41.RATING作业按标准方法进行时作业速度的快或慢的程度用数字进行换算的时间很快︰125%;快︰100%;一般︰85%;慢︰60%42.净作业时间作业按标准方法进行时所需的最少时间CYCLE TIME*RATING(%)43.运转率产品所需的时间及实际生产中所用的时间之比NECK TIME /TACT × 100 %44.运转损失生产产品所需的时间和实际所用的时间之比(Tact Time-Neck Time)/ TACT TIME× 100 %45.平衡损失作业人员之间由于作业量的不公平导致的作业要素时间的不均衡程度的比(Neck Time-Cycle Time)/TACT TIME× 100 %46.效率损失按标准方法进行作业时需要的最少时间和与实际作业中所用的时间之差的比(Cycle Time-净作业时间)/ TACT TIME× 100 %47.综合损耗损耗的总合计运转损失+平衡损失+效率损失48.时间观测法用秒表观测分析作业人员的作业时间或设备运转的方法49.防呆法作业人员或设备上装上无需小心作业也绝不出错的防止出错装置50.生产率一般用产量对投入的比OUT PUT /IN PUT51.工时人或机器能做的或已做的量用时间来表示52.拥有工时拥有人员的工时拥有人员×正常作业时间53.考勤工时实际上没投入到作业的工时(缺勤、休假、出差、支持等)相关人员×相关时间54.出勤工时实际投入到作业的人员的工时拥有工时-考勤工时55.追加工时正常出勤工时以外追加作业的工时,即加班,特殊出勤、接受支持等相关人员×相关时间56.作业工时投入到作业中的总工时出勤工时+追加工时57.实际生产工时作业工时中去掉损失工时,实际投入到作业的工时作业工时-损失工时58.损失工时不属于作业人员责任范围的损耗工时(会议、教育、早会、待料、材料不良、机械故障、机型变更、不良返工等)相关人员×相关时间59.作业工时效率生产产品所需的时间(标准时间)和实际用的时间之比标准工时/作业工时× 100 %60.实际生产工时效率损失工时以外的纯作业时间和实际生产所用的时间之比标准工时/实动工时× 100 %61.实际生产率生产产品所需的时间和纯生产所需的时间之比标准工时/实动工时× 100 %62.效率管理为了减少生产要素的损耗,用一线监督人员的指导监督来达到适当地提升并维持作业人员对作业的态度的一种管理模式标准时间/实际时间63.PAC (Performance Analysis & Control)为了能做到只要作业努力就能提升及维持能力的效率管理模式的一种。
第6章秒表时间研究-工业工程

研
(X i X )2
i 1
n
31.98 1.5991.6 20
究
管理上限 UCL X 3 2 0 .9 3 1 .6 2 5 .7
管理下限 L C L X 3 2 0 .9 3 1 .6 1 6 .1
数值28大于25.7,为异常值,剔除。
表
若观测误差控制在5%以内,取置信度为
95%,则观测次数为:
时
2
间 研
n
40R / X
d2
2
40Rn
n
d2 Xi
i1
究
R是级差;d2是以观测次数为基础的系数, 可查表;n’为应进行的观测次数;n为试观测
次数。
秒 表 时 间 研 究
究
数与标准差,再按允许的误差界限求应观测的次数。
标准差是各数据偏离平均数的距离的平均数 。
确定观测次数
秒
表
假定观测值x i 呈正态分布,n为观测次数(样本数)
x 为样本均值; S 为样本标准差; x 为样本均值标准差.
时
为总体标准差;
间
2
2
研
x
x
究
X
秒 其中
确定观测次数
表
X
研
究
测时
秒
(2)归零测时法 在观测过程中,每一个操作单元结
表
束,即按停秒表,读表,将秒表快速回零,在下一个操
作单元开始时重新启动。
时
(3)累计测时法 用两个或三个秒表联动测时。
间
两表联动,把两表用一联动机构连结。观测时,在一
IE工业工程标准工时测量

规划 设计 评价 改进 创新
工业工程的特点
工业工程是工程学的重要分支,具有典型的工程学属性。 它不是解决具体的产品、工程等问题,而是面对所有产品 、所有过程解决所投入系统的资源效率。
工业工程同其他工程学科最大的不同在于,工业工程的关 键要素—人和组织—是开发系统的两个知识本体。
与其他工程学科相比,工业工程的数学模型化和定量化还 比较弱,因而更注重实践、经验和技巧。
----------------
X 100%= 82%
5 X 29
平衡损失率=1 - 平衡率=1-82%=18%
问题
0.1分钟
0.7分钟
1.0分钟
0.5分钟
0.8分钟
0.4分钟
0.2分钟 0.6分钟
1、假设每天运转8小时(480分钟),请问这流水线的产 量范围?
2、假如每天计划生产480个产品,那么需要设定多少工 序呢?
经典IE研究
Taylor 搬运实验与 劳动定额
Gilbreth 砌墙实验与
经典的工作研究 动作经济性原则
时间研究
动作研究
IE的使命
人员 物料 设备 时间 信息
综 合 通过 体 系
观察 学习 思考
专门的
利用
数学 物理学 社会科学
知识 技术
工学的
分析 原理 设计 方法
期待的成果
P Q C D S M
عx
68.72%
n---真正合理的观测次数 m---指预先观测的 次数
95.45%
99.73%
-3
-2 -1
X1
2
3
例子:
序号 1 2 3 4 5 6 7 8 时值 7 8 9 8 8 7 9 10 平方 49 64 81 64 64 49 81 100
秒表法测定标准工时的探究
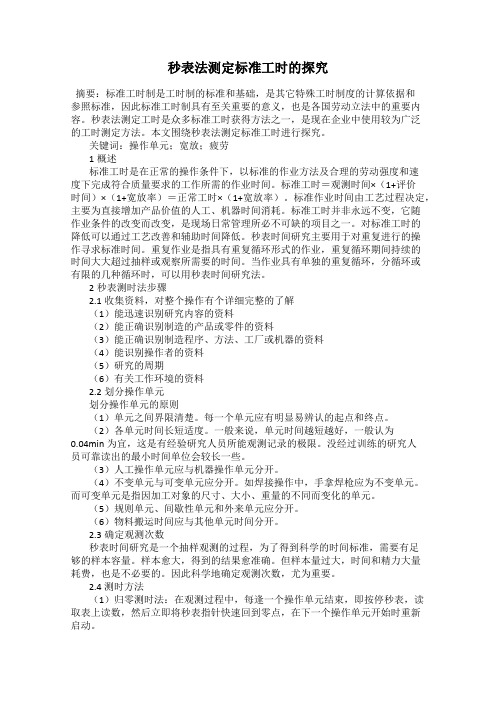
秒表法测定标准工时的探究摘要:标准工时制是工时制的标准和基础,是其它特殊工时制度的计算依据和参照标准,因此标准工时制具有至关重要的意义,也是各国劳动立法中的重要内容。
秒表法测定工时是众多标准工时获得方法之一,是现在企业中使用较为广泛的工时测定方法。
本文围绕秒表法测定标准工时进行探究。
关键词:操作单元;宽放;疲劳1概述标准工时是在正常的操作条件下,以标准的作业方法及合理的劳动强度和速度下完成符合质量要求的工作所需的作业时间。
标准工时=观测时间×(1+评价时间)×(1+宽放率)=正常工时×(1+宽放率)。
标准作业时间由工艺过程决定,主要为直接增加产品价值的人工、机器时间消耗。
标准工时并非永远不变,它随作业条件的改变而改变,是现场日常管理所必不可缺的项目之一。
对标准工时的降低可以通过工艺改善和辅助时间降低。
秒表时间研究主要用于对重复进行的操作寻求标准时间。
重复作业是指具有重复循环形式的作业,重复循环期间持续的时间大大超过抽样或观察所需要的时间。
当作业具有单独的重复循环,分循环或有限的几种循环时,可以用秒表时间研究法。
2秒表测时法步骤2.1收集资料,对整个操作有个详细完整的了解(1)能迅速识别研究内容的资料(2)能正确识别制造的产品或零件的资料(3)能正确识别制造程序、方法、工厂或机器的资料(4)能识别操作者的资料(5)研究的周期(6)有关工作环境的资料2.2划分操作单元划分操作单元的原则(1)单元之间界限清楚。
每一个单元应有明显易辨认的起点和终点。
(2)各单元时间长短适度。
一般来说,单元时间越短越好,一般认为0.04min为宜,这是有经验研究人员所能观测记录的极限。
没经过训练的研究人员可靠读出的最小时间单位会较长一些。
(3)人工操作单元应与机器操作单元分开。
(4)不变单元与可变单元应分开。
如焊接操作中,手拿焊枪应为不变单元。
而可变单元是指因加工对象的尺寸、大小、重量的不同而变化的单元。
秒表测时法

4.秒表测时法的步骤 (3/6)
4.3 测量时间----4.3.4 决定观测次数
某一单元试行观测l0次,结果如下: 7,5,6,8,7,6,7,6,6,7 平均值欲得±5%误差,95%可靠度,问需观测多少次? 此处n=10
¢ Ü
T
¢ Ý
T
失去记录
T 90.25 30.66
µ Ã Ë ÷ ü » Æ ¸ ¤´ ø ü » ² ¸ ¢ µ ÷Õ û Â Ý Ë ¿ ¹ ¾ ¤ ß ô µ µ Ø Ï É £ ¬ Ê ° ð ² Æ Á » Ò ¬ £ ² ¢ ÷ µ Õ û
X 7.39 6.85
外来单元(1)
10.67 ¨ M 11.22 10.38 11.49
适用于流水方式计时
长周期作业
作业时间很短的工序
优 点
测时方便,连续计时,能 保证所有时间均可记录而 无遗漏
对于长周期作业要素测定 时,该误差影响不大
在测定作业时间很短的工 序时采用,因为在这种场 合下要按单个作业要素计 时非常困难。
缺 点
受观测者技术影响会产生 误差,但影响不大。
1.观测者测量技术不熟练, 易产生读数误差; 2.对短周期作业要素测定, 误差相对值过大。
记录表
其他
需要用到的其他仪器设备,如步行测量, 速度测量等仪器
2.秒表测时法的工具
秒表的构成
存储的道数 103 A键 103 00:00′00〞00 每道时间 (SPLIT) 00 : 00′00〞00 00 : 00′00〞00 累计时间 D键 每一圈(LAP)的时间 B键 C键
A键——LAP/SPLIT RESET B键——ADJUST C键——START/STOP
- 1、下载文档前请自行甄别文档内容的完整性,平台不提供额外的编辑、内容补充、找答案等附加服务。
- 2、"仅部分预览"的文档,不可在线预览部分如存在完整性等问题,可反馈申请退款(可完整预览的文档不适用该条件!)。
- 3、如文档侵犯您的权益,请联系客服反馈,我们会尽快为您处理(人工客服工作时间:9:00-18:30)。
6. 秒表测时法-6.1 秒表测时原理
二、测时的计时方法 (一)连续计时法 以秒表为计时工具,按先后顺序对工序各作业要素 逐一观察,连续记录其起止时间。 1.技术要求:划分的作业要素延续时间应大于0.1min, 定时点应明显易辩,选择从声响、视觉上能够明确区别 各作业要素起止的标志,在下一作业要素定时点出现前, 应完成该作业要素时间的观察和记录 2.操作要求 (1)观测。在测时开始前秒表复零,于第一个操作 周期第一个作业要素开始同时开动秒表,到最后一个操 作周期最后一个作业要素观察结束时停止秒表。 (2)记录。在每个作业要素的定时点处观察秒表读 数并记录于该作业要素相应操作周期的终止时间栏内
6. 秒表测时法-6.1 秒表测时原理
例,假设某工序由a,b,c,d,e共五个作业要素组成, 需要采用循环计时法对该工序进行秒表测时。 解:(1)将5要素组合成A(b.c.d.e)、B (c.d.e.a)、C(d.e.a.b)、D(e.a.b.c)、E(a.b.c.d) 五个循环体(亦即五个组合要素),每个循环体含四个 单元。 (2)观测并记录——依次记录各个循环体的终止 时间值为:25s,55s,81s,105s,130s。 (3)计算每个循环体的延续时间 A=25-0=25s (亦即A=b+c+d+e=25s) B=55-25=30s (亦即B=c+d+e+a=30s) C=81-55=26s (亦即C=d+e+a+b=26s) D=105-81=24s (亦即D=e+a+b+c=24s) E=130-105=25s(亦即E=a+b+c+d=25s)
6. 秒表测时法-6.1 秒表测时原理
(3)计算该工序的平均延续时间 ∵ A+B+C+D+E=4(a+b+c+d+e) =25+30+26+24+25=130 S 即5个循环体时间之和是5作业要素时间之和的4倍
a b c d e 130 ∴ X 32.5 S 5 1 4
6. 秒表测时法பைடு நூலகம்
采用秒表测时法制定工时定额的完整过程包括: (1)测时 →作业时间实测值T测 (2)测时结果的评比 →作业时间正常值Tz (3)宽放时间的确定 →宽放时间Tkf (4)准结时间的确定 →准结时间Tzj (5)计算定额 →工时定额T
6. 秒表测时法-6.1 秒表测时原理
6.1 秒表测时原理 一、测时的观察次数 测时实质是对工序操作活动的一次密集抽样。要提 高测时的正确性和可靠性,关键是提高样本的代表性。 根据统计原理,在满足95%可靠度要求的情况下,测时 2 观察次数如下: n n
2 N S
2 n X i 2 ( X i) i 1 i 1 n X i i 1
(6—1)
式中 N ——某作业要素的应观测次数; S ——给定测时数据的相对误差.常用5 % 、10% n ——某作业要素的已观测次数; xi——某作业要素的观测时间值。
单元①
R 8 T 8
单元②
R 15 T 7
单元③
R 23 T 8
单元④
R 29 T 6
6. 秒表测时法-6.1 秒表测时原理
(二)循环计时法 以秒表为计时工具,按操作顺序依次将若干个作业 要素(作业要素数-1)合并成组,以组为对象进行测定, 最后计算获得各个作业要素的延续时间值。 本法也称周程计时法(或差值计时法)。对于单元 甚小且周期甚短的作业,读出并记录时间很难准确,于 是常将几个操作单元(每次去掉一个单元)组合在一起 测时。 1.技术要求 作业要素之间应有明显易辩的定时点,测时秒表选 择精度较高的的数字式电子秒表,观测点应选在能够清 楚观测到作业要素定时点的地点,观察次数应大于工序 作业要素数。
工业工程学
Industrial Engineering
主讲:秋枫 部门:IE部
苏州XX精密制造股份有限公司 2016年5月
第六讲:秒表测时法
本章学习内容
6.1 6.2 6.3 6.4 6.5 6.6
秒表测时原理 秒表测时步骤 秒表测时实例 工时评定 宽放时间 标准时间
6. 秒表测时法
秒表测时法是以工序作业时间为对象,对构成工序 的作业要素进行周期重复观察,并测定其工时消耗的方 法。 IE的定义:“以秒表作为工具,在一段时间内,连 续不断地直接测定某一作业操作者的一种测定技术,用 以决定一位合格适当训练有素的操作者,在标准状态下, 对一特定的工作以正常速度操作所需的时间” 秒表测时法适用于以工序为测时对象和相对集中生 产、工作的场所。实施时需要得到生产工作场所的管理 者和被测时对象的配合以维持原有生产工作状态。测时 人员应经过事先的培训,熟悉时间消耗分类,掌握测时 的方法、要领。
6. 秒表测时法-6.1 秒表测时原理
2.操作要求 (1)观测——测时前秒表复零,组合作业要素开始 同时开动秒表,到组合作业要素最后一个作业要素终止 定时点停止秒表。在下一个组合作业要素开始时再开动 秒表,秒表继续计时。直至一组组合作业要素观测结束, 使秒表复零。 (2)记录——在被测组合作业要素结束时,读取秒 表读数,将每个被测组合作业要素,每次观测秒表读数, 记录在测时记录表中该组合作业要素相应观察顺序(分 组)时间栏中。 (3)计算——每个组合作业要素的延续时间,是每 个组合作业要素本身于测时记录表中记录的终止时间, 与其前一组合作业要素测时记录表中记录的终止时间之 差值。
(4)计算该工序各个作业要素的延续时间 a= X -A=32.5-25=7.5 s b= X -B=32.5-30=2.5 s c= X -C=32.5-26=6.5 s d= X -D=32.5-24=8.5 s e= X -E=32.5-25=7.5 s
6. 秒表测时法-6.1 秒表测时原理
(3)计算。每个作业要素本身终止时间与前一作业 要素终止时间的差值即本作业要素延续时间。 例如,某作业可划分为4个作业要素,各要素测时记 录见表6—1,表中数据单位为DM(1DM=0.01min)。 “R”表示现场观测时记录每一单元末的秒表读数(该单 元的终止时间),“T”表示该单元延续时间,为相邻单 元R值的差。 表6—1 各单元观测时间