石油专用管材钻具无损探伤与分级检测
钻具检测分级标准
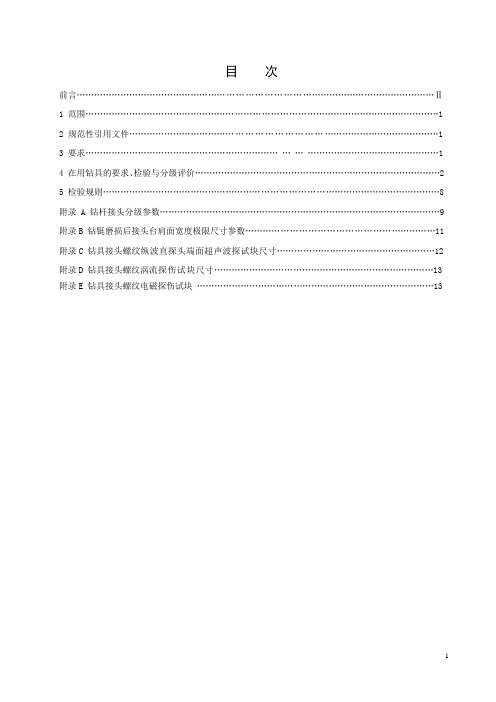
目次前言 (Ⅱ)1 范围 (1)2 规范性引用文件 (1)3 要求 (1)4 在用钻具的要求、检验与分级评价 (2)5 检验规则 (8)附录 A 钻杆接头分级参数 (9)附录B 钻铤磨损后接头台肩面宽度极限尺寸参数 (11)附录C 钻具接头螺纹纵波直探头端面超声波探试块尺寸 (12)附录D 钻具接头螺纹涡流探伤试块尺寸 (13)附录E 钻具接头螺纹电磁探伤试块 (13)前言本标准修订并替代Q/ SHXB 0021—2005《钻具检测与分级评价》。
本标准对技术内容的修改主要包括以下内容:——增加直径和壁厚测量方法的规定;——增加对方钻杆,加重钻杆的制造要求;——更改钻铤报废或停止使用的长度规定;——增加方钻杆报废或停止使用的规定;——增加加重钻杆报废或停止使用的规定;——增加加重钻杆接头报废或停止使用的规定;——增加接头螺纹探伤的规定;——增加钻杆管体电磁感应检测的规定;——增加附录D和附录E规范电磁探伤和过渡带探伤人工对比试块;——删除了涡流探伤相关内容。
钻具检测与分级评价1范围本标准规定了*****************施工地区在用钻具的使用、维修、检测与分级评价的技术要求。
本标准适用于*****************施工地区使用的钻杆、加重钻杆、钻铤、方钻杆、钻具扶正器、钻柱转换接头等钻井管具。
本标准不适用于新钻具的验收检验,新钻具的检验应采用相关产品标准和规范。
2规范性引用文件下列文件中的条款通过本标准的引用而成为本标准的条款。
凡是注日期的引用文件,其随后所有的修改单(不包括勘误的内容)或修订版均不适用于本标准,然而,鼓励根据本标准达成协议的各方研究是否可使用这些文件的最新版本。
凡是不注日期的引用文件,其最新版本适用于本标准。
GB/T22512.2 旋转台肩式螺纹连接的加工与测量GB/T 20659 石油天然气工业铝合金钻杆SY/T5051-91 钻具稳定器SY/T5144 -2007 钻铤SY/T5146 -2006 整体加重钻杆SY/T5200-2002 钻柱转换接头SY/T5290 -2000 石油钻杆接头SY/T5369 -94 石油钻具的管理与使用方钻杆、钻杆、钻铤SY/T5446-92 油井管无损检测方法钻杆焊缝超声波探伤SY/T5447-92 油井管无损检测方法超声测厚SY/T5448-92 油井管无损检测方法钻具螺纹磁粉探伤SY/T5824-93 钻杆分级检验方法SY/T5956-2004 钻具报废技术规定SY/T5987 钻杆国外订货技术条件SY/T 6427 钻柱设计和操作限度的推荐作法SY/T6474 新套管、油管和平端钻杆现场检验方法SY/T6508 油井管无损检测方法非铁磁体螺纹渗透探伤API Spec 5D 钻杆规范3 要求3.1使用过的钻具,应进行尺寸检测和探伤检测,包括接头体、管体、接头螺纹的结构尺寸和损伤检验,根据检测结果进行分级评价,未经检验或不满足要求的钻具应停止使用。
石油化工压力管道的破坏和无损检测

石油化工压力管道的破坏和无损检测石油化工压力管道是石油化工工艺中最为重要的设备之一。
由于其处于高温高压环境下,随着使用年限的增加,管道内外受到的各种因素的影响,如高温腐蚀、疲劳损伤、响应环境中的腐蚀等,可能会导致管道破坏。
因此,为了保证管道的安全运营,必须对石油化工压力管道进行定期检测。
传统的检测方法包括视觉检查、X光检查、超声波检测等方法,但这些方法都存在一些局限性。
而无损检测技术的应用能够在不影响管道正常使用的情况下,对管道进行全面、高效的检测,减少管道事故的发生。
常用的石油化工压力管道的无损检测技术包括:磁粉探伤、涡流探伤、超声波检测等。
这些技术各有优缺点,应根据管道的不同情况选择相应的技术进行检测。
磁粉探伤是一种通过磁粉局部磁化管道表面,通过磁粉的沉积来发现管道表面和近表层的裂纹和缺陷的检测方法。
这种方法检测灵敏度高、检测效率高,受到广泛应用。
但是,由于只能检测到表面缺陷,因此对于靠近管道内壁的缺陷、内部缺陷等难以检测。
超声波检测是一种通过声波在物体中传播的原理来检测表面缺陷的方法。
超声波检测的灵敏度比涡流探伤更高,能够检测到表面下更深的缺陷,如壁厚减薄、裂纹等,因此被广泛应用于管道的无损检测中。
同时,超声波的波长和能量变化都比较容易控制,便于实现自动化、在线检测。
针对存在缺陷与破坏的管道,在无损检测技术之外,还需要采取合适的修复措施。
一般来说,修复方式分为两类,即临时修复和永久修复。
临时修复包括紧急止漏、封堵等方法,这些方法可以暂时的控制管道的泄漏,但无法保证管道的长期运作。
永久修复则包括管道修补和管道更换两种方式。
这两种方法都能够保证管道的安全运行,但因为管道更换成本高昂,通常情况下都会优先考虑管道修补方式。
总之,石油化工压力管道的破坏会给生产生活带来巨大的经济和社会损失,因此对其进行全面的无损检测非常必要。
同时,还需要在检测后采取合适的修复措施,来确保管道的安全运行。
钻具无损探伤检测方法的改进

序号 名义深度{ mm) 检测深度{ mm) 误差
1项 目总 任 务
钻井工程公司管具 分公司现有的超声波无 损检测仪器 ,由于体 积和 重 量 相 对 大 , 井 场 这 种特 殊 的环 境 中作 业 , 响 探 伤 工 作 的 顺 在 影 利进行 , 进而影响 了工作质量。同时配合仪器使用的缺 陷对 比试块 , 也因为当时的制作工艺粗糙而不以模 拟钻具疲劳裂纹缺陷 ,达 不到 目前 对 探 伤 工 作 的质 量 要 求 。 针对 以上问题 ,管具分公司根据 目前超声波无损检测现状 及井 场探伤作业的实际情况 、 计划研究 内容如下 : ①寻找体积小、 重量轻、 便 于 现 场 、 场 作业 时携 带 方 便 、 强 阳 光 下 也 能 正 常 探 伤 的 仪 器 。 井 在 ②在原有钻具 事故 的调查、 统计 、 分析 的基础上 , 运用新技术 , 新方法
3 完 成 的 主 要 工 作量
31 申购 欧 能达 6 O . 10型 全 数 字超 声 探 伤 仪 。 该 仪 器 具 有 以下 性 能 和 特 点 : 大屏幕、 高亮 、 高速 彩 色 显 示 , 烈 阳 光 下正 常探 伤 。 强 键 式 操作 , 探 伤 非 常简 便 、 捷 。 使 快
注 : I 关标准规定 , AP 相 人工缺陷深度误差小于深度值的 1 %。 5
4 现 场 应 用情 况 从 20 0 9年 6月 1日至 2 0 0 9年 1 2月 3 日 ,在 B 2 0 3 0井 、 研究一种针对井下钻具断裂的不同情况 ,分析制作模拟不同规格钻 B 1 3 9井 、 4 9井、 9 K2 安 8井 、 下平 1井 等完 钻井场 、 巴参 1井 中途 具 疲 劳 裂 纹 的 对 比试 块 , 代 目前 平 底 孔 螺 纹 试块 , 于 提 高 仪器 的 替 用 井场; 1 共 8口井 , 对现场 3 3根钻铤螺纹进 行了无损检测。基本情 3 探伤灵敏度 , 减少钻具 探伤 时缺 陷的漏检率 , 提高钻具探伤 的整体水 况 如 下 表 :
石油钻具无损检测技术的应用分析

图6 新余隙活塞杆组件 图7 旧余隙活塞杆组件结构示意图 结构示意图(2)采用整体设计,取消余隙活塞杆与余隙活塞158中国设备工程 2023.07 (下)渗透液还会留在存在缺陷的内壁中,并对显影剂进行良好吸附,以此将检测后产生的结果影像清晰展示,科学160研究与探索Research and Exploration ·智能检测与诊断中国设备工程 2023.07 (下)4 超声波探测技术的具体操作现实工作开展的过程中,其中可以选择使用的设备种类较为丰富,因此,便将CTS—9003型设备来作为案例来进行分析。
在超声波探伤设备在工作中运转时,需要使用的附属设备为探伤仪器、探头、传输线路、电池等相应的设备。
在开采进行前,相应人员要对附属设备进行检查,确保检测系统整体都处于正常状态;在机械设备启动后,还要进行相应参数、比例的设置工作,以保障对钻具的高精准度检测。
之后还要对其操作时的灵敏程度调改,清理掉被测工具的表面附着物,防止对其表面的检测工作造成干扰。
之后对耦合剂进行涂抹,并将探头、钻具内的气体排空,确保检测工作进行的合理性。
不仅如此,检测工作进行的过程中,还要将探头进行上下、左右的移动,最后根据图像上显示的信息,对可能产生损害的位置进行判断。
4.1 工具选用在钻具无损检测工作开展的过程中,为确保其能够将自身的作用进行充分展现,便要在实际操作进行前,挑选适合的仪器、探头等,并且还要知晓钻具自身的厚度情况、结构种类,之后在该基础上进行挑选。
正常情况下,每个检测的区域中都应该存在三个探头,依据对其的合理使用,便可以对存在缺陷的位置、种类进行合理判断,从而保障工作开展的顺利程度。
不仅如此,在当前使用的测量设备中,都具备进行数据保存的能力,并且最高的限制为100条;面对回波数据信息时,同样能够精准保存,以及对其进行智能化处理工作,然后再使用图形的方式进行显示,这将工作开展的便利程度进行了大幅提升。
在设备仪器挑选完成后,还要对仪器的参数进行合理设置,根据操作环境的需要,在其菜单上进行材料声速、探头种类、操作频率、工件厚度等多方面合理设置。
钻具检测分级技术规程

钻具检测分级技术规程详解一、引言随着石油、天然气等资源的深入开发,钻井工程日益增多,钻具作为钻井工程的核心设备,其质量的好坏直接影响到钻井工程的成败。
为了确保钻具的质量和性能达到标准,降低钻井工程的风险,提高开发效益,对钻具进行检测和分级至关重要。
本文将详细介绍钻具检测分级技术规程的相关知识。
二、钻具检测的目的和意义钻具检测的主要目的是确保钻具的质量和性能达到规定的标准,以保证钻井工程的顺利进行。
具体来说,钻具检测的意义包括:1. 确保钻具的安全性能:通过对钻具进行全面的检测,可以及时发现其存在的缺陷和隐患,从而采取有效的措施进行修复或更换,确保钻具在钻井过程中能够安全、稳定地工作。
2. 提高钻具的使用效率:通过对钻具进行检测和分级,可以对其性能进行评估,从而根据钻井工程的具体要求选择合适的钻具,提高钻井效率。
3. 降低钻井工程的风险:钻具的质量和性能直接关系到钻井工程的安全和效益。
通过对钻具进行检测和分级,可以及时发现并解决潜在的问题,降低钻井工程的风险。
4. 延长钻具的使用寿命:通过对钻具进行定期检测和维护,可以及时发现并修复其存在的损伤和老化问题,从而延长其使用寿命。
三、钻具检测的方法和步骤钻具检测的方法主要包括外观检测、无损检测和破坏性检测等。
具体步骤如下:1. 外观检测:主要检查钻具的表面是否有裂纹、变形、锈蚀等问题。
对于发现的问题应及时进行处理。
2. 无损检测:主要包括超声波检测、磁粉检测、涡流检测等。
这些方法可以在不损伤钻具的情况下,发现其内部或表面的缺陷。
3. 破坏性检测:主要包括拉伸试验、冲击试验、硬度试验等。
这些方法主要用于评估钻具的力学性能和耐磨性。
然而,由于这些方法会对钻具造成损伤,因此通常只在必要时进行。
四、钻具分级的依据和标准钻具分级的依据主要包括其材质、制造工艺、使用条件等因素。
一般来说,钻具可以分为以下几个等级:1. 一级钻具:主要用于较浅的钻井工程,对材质和制造工艺的要求相对较低。
石油钻具失效检验中无损检测的应用研究

对于仪器探头扫查的覆盖率进行控制,使之不小于探头15%,同时,为使得超声波无损检测工作更182研究与探索Research and Exploration ·智能检测与诊断中国设备工程 2023.06 (下)行优化设计,实现检测效率的高效与创新。
3.3 荧光磁粉对钻杆螺纹的探伤3.3.1 荧光磁粉的检测流程荧光磁粉的检测原理主要是对已经发生磁化反应的钻杆螺纹进行检测,在此过程中,通过将荧光磁粉悬液施加到钻杆螺纹上,使其在磁场的充分作用下进行磁化,这对于后续工作的开展有着重要的保障作用。
例如,在某石油企业中,主要从荧光磁粉的检测原理展开着手。
荧光磁粉具有黑暗中发光显示的作用,使得技术人员在检测过程中,可以直观地了解钻杆螺纹损伤的部位与损伤的情况,进而通过专业技术手段进行补救,为石油钻具的失效检验工作进行优化,节省企业的经营成本。
在荧光磁粉的检测过程中,该石油企业技术人员与专家进行研究,将提高荧光磁粉检测钻具螺纹的灵敏性工作放在重点内容中。
通过专家与技术人员对荧光磁粉检测技术的不断改善,将突破钻具螺纹的结构与形状限制,使得仪器对检测部位的要求降低,进而增加了荧光磁粉检测螺纹部位工作的效率。
在检测中,需要工作人员对钻具螺纹表面进行洁净处理,主要是防止其出现锈蚀现象,对荧光磁粉的检测造成影响,使其很难发现在螺纹表面的损伤与裂纹,进而使得石油钻具失效,对企业造成较大的损失。
3.3.2 荧光磁粉检测优化随着科学技术的发展与创新,石油企业在钻具失效检验中无损检测技术也在不断创新。
该石油企业,通过对磁化器结构的设计与优化,将荧光磁粉的检测进行融合创新,使其在原有技术优势的基础上,进行创新,使其满足现代石油钻具无损检测技术的发展。
主要包括以下几方面:第一,对荧光磁粉检测理念的创新,这为检测系统的优化提供了理论保障。
在此过程中,专家与技术人员通过自身专业知识,对技术进行创新,并在实践中不断总结,将其理论化与制度化,并根据石油企业的管理要求,对工作人员进行灌输,使其充分理解荧光磁粉检测创新工作的重要性。
钻具无损探伤检测方法的改进

钻具无损探伤检测方法的改进钻探工具是钻井作业中的重要工具。
在长期的工作条件下,钻探工具容易损坏,影响正常操作。
在目前的情况下,有许多钻具的非破坏性测试方法,本文的内容包括改进无损检测方法和一些无损检测方法。
在具体的讨论中,首先,在钻具的无损检测的定义和常用的无损检测方法的分析中,其次,讨论了无损检测方法的正确选择,最后讨论了无损检测的改进。
通过实例分析对钻具的破坏性测试方法进行了分析,进一步提高了检测过程的可操作性。
标签:钻具;无损伤;检测方法;改进一、引言钻井探工具通常是钻井施工过程中重要的施工工具,包括活动钻杆、钻杆、岩心管、铰刀和钻头,其中每个组件均由优质无缝钢管制成。
它门具有出色的物理性能,但是随着时间的推移,钻具必须承受其自身的交变载荷、疲劳、腐蚀和磨损,钻具内部的损坏很容易损坏,必须使用非破坏性的检查方法对其进行损坏。
该检测可能存在其他影响检测顺利进行的问题,因此,根据实际情况,应改进一些无损检测方法以利于操作。
二、常用无损探伤检测方法分析无损探伤检测依靠光,声音和电磁等物理特性,通过在测试对象没有造成损坏的条件下确定测试对象内部是否存在损坏,来确定对象的技术指标是否及时满足生产要求。
通过根据测试结果等掌握内部损坏的大小、位置和数量,以便于及时调整。
无损检测的关键是要确保在检测过程中检测到的物体功能不会因检测而受到损害。
常用的无损检测方法主要包括:X射线无损检测、超声波无损检查、渗透无损探伤、涡流无损探伤以及磁粉无损探伤。
(1)X射线无损检测X射线无损检测方法主要是利用X射线对钻具的能量损失进行调查,根据反射前后的能量差确定相应的参数,最后根据这些参数绘制图形,检查钻孔工具的内部损坏。
在使用过程中会引起辐射,长期施工会对工人的健康产生一定影响。
(2)超声波无损检查超声波无损检测是利用超声波进入钻孔工具。
如果钻孔机损坏,则会发生超声波反射。
通过超声波反射判断后,使用超声波绘制的地图检查钻孔工具内部是否损坏。
钻具检测技术要求
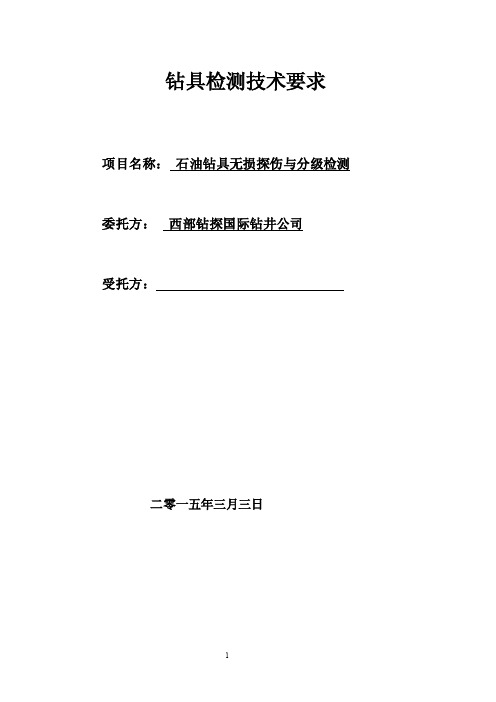
钻具检测技术要求项目名称:石油钻具无损探伤与分级检测委托方:西部钻探国际钻井公司受托方:二零一五年三月三日钻杆检测技术要求1.检测内容和技术要求1.1检测的主要内容由甲方提供的检测场所,乙方派出具备持有检测资质的技术人员及相关检测仪器为甲方提供钻杆无损探伤与分级检测的相关工作,其主要内容包括钻杆本体检测、钻杆焊缝及加厚区检测、接头及螺纹检验、壁厚及腐蚀检测,同时对钻杆进行分级判定。
1.2技术服务要求1.2.1正式检测前对钻杆进行必要的清洗和除锈,以满足检测要求。
1.2.2管体检测:采用美国OEM公司生产的ARTIS-3便携式电磁检测系统对钻杆管体的横向裂纹和壁厚损失进行检测和评价。
1.2.3焊缝及加厚区检测:1.2.3.1采用CTS-2020型或CTS-9006型便携式数字超声波探伤仪对钻杆焊缝及加厚区进行探伤和评价。
1.2.3.2采用奥林巴斯IV8630M型工业内窥镜对钻杆焊缝及加厚区进行内壁检查。
1.2.4螺纹判修:采用梳齿规、锉刀、砂纸等量具和工具对钻杆螺纹进行判修和手工修复。
1.2.5螺纹磁粉检测:采用美国派克公司生产的PL-10S磁化设备对接头进行充分磁化,运用日本LY—10型磁粉,喷上磁悬液,使用美国捷特公司生产的Maxima3500超强紫外灯对钻杆接头螺纹进行裂纹判定。
1.2.6壁厚检测:采用德国K.K公司生产的DM5E超声波测厚仪进行测量。
1.2.6.1对钻杆管体进行抽点测量,取其最小值作为测量结论。
1.2.6.2在美国OEM公司生产的ARTIS-3便携式电磁检测系统检测到管体壁厚出现超标或异常时,对其进行壁厚定量的测定。
1.2.6.3结合焊缝及加厚区检测情况对异常区域进行壁厚定量的测定。
1.2.7对钻杆腐蚀情况、压痕、刻痕、铲凿、凹坑等的测定:采用麻坑深度仪、测厚仪,结合ARTIS-3电磁检测设备和奥林巴斯IV8630M型工业内窥镜对钻杆进行检查。
1.2.8钻杆外径、长度和直线度测量:1.2.8.1采用游标卡尺或外卡钳对钻杆接头进行外径测定。
- 1、下载文档前请自行甄别文档内容的完整性,平台不提供额外的编辑、内容补充、找答案等附加服务。
- 2、"仅部分预览"的文档,不可在线预览部分如存在完整性等问题,可反馈申请退款(可完整预览的文档不适用该条件!)。
- 3、如文档侵犯您的权益,请联系客服反馈,我们会尽快为您处理(人工客服工作时间:9:00-18:30)。
石油专用管材钻具无损探伤与分级检测评价技术
安东石油技术(集团)有限公司陈先富
石油专用管材钻具(钻杆、油管、套管、钻铤、方钻杆、提升短节、配合接头、天车、游动滑车、大钩、水龙头、吊卡、吊环等)在油田使用一定时期后需要进行无损探伤及管材钻具的评价,目的是掌握其质量状况和提高使用效率,杜绝质量事故的发生,保证安全钻井生产。
其检测项目如:
1、管体电磁探伤——利用漏磁检测原理,采用美国OEM 公司生产的ARTIS—2便携式电磁检测系统对管体的横向裂纹和壁厚损失进行检测和评判。
根据API标准有关内容制作的Ø1.6㎜竖通孔标定管分别对8只检测探头进行灵敏度效验,100%的电脑化,横向裂纹和壁厚损失探伤覆盖率超过360°。
“在线诊断”、“自动停机”功能,极大地节省了寻找和验证显示凝点地时间,所有检测结果和报告达到API标准要求。
2、管端超声波探伤——利用超声波检测原理,采用汕头超声仪器研究所生产的超声波探伤仪CTS—2200、CTS—22A型等仪器对管端500㎜内进行超声波纵横向探伤,检测其有无裂纹等并进行评价。
3、螺纹荧光磁粉探伤——根据磁粉探伤原理,利用美国OEM 公司ARTIS—2便携式电磁检测系统或CYD---5000型射阳探伤机以及韩国MP-200型磁轭探伤机对管材螺纹进行磁化,运用日本LY---10型磁粉,采用美国捷特公司Maxima3500型紫外灯进行观察,检测其是否有裂纹磁痕等并进行评价。
4、管体壁厚及腐蚀检测——利用超声波检测原理,采用德国K.K.公司的DM4超声波测厚仪对管体进行多点壁厚测量,取其平均值;根据美国OEM 公司ARTIS—2便携式电磁检测系统所检测的管体状况进行测厚、超声波探伤进行复检;运用北京晋科光公司的N—2型工业内窥仪进行管体内壁检察等;综合检测结果对管体腐蚀、磨损进行综合评价。
5、管体压痕凹坑刻痕直线度检测——采用陕西汉中万目公司的ATY型麻坑深度仪,结合美国OEM 公司ARTIS—2便携式电磁检测系统所检测的管体状况进行测量并检测管体直线度状况,根据有关标准进行评定。
6、钻杆接头磨损变化的测量——采用游标卡尺、千分尺、外卡钳、深度尺等有效量具对其进行接头外径、密封台阶宽、吊卡台阶宽等磨损变化的测量,根据测量结果依据有关标准进行评定。
7、对专用管材进行综合分级评价——根据电磁、超声、磁粉、测厚、腐蚀、磨损、直
线度等检测结果,根据相关检测标准进行分级评审,并撰写综合评价报告。
8、对钻铤、方钻杆、提升短节、配合接头、天车、游动滑车、大钩、水龙头、吊卡、吊环等进行无损检测评价——利用超声波探伤原理、漏磁探伤原理、射线探伤原理对其进行检测评定,并撰写综合评价报告。
本公司自成立检测项目以来,已先后为塔指工程技服、四川川东钻探公司、四川川中钻井公司、中石油华北西部公司、中石化西北局、中石化西南局、中石化中原局、中石油吐哈钻井公司、中石化华北局等单位,成功的大量检测了钻杆、油管、钻铤、方钻杆、提升短节、配合接头、天车、游动滑车、大钩、水龙头、吊卡、吊环等构件达12万根/套/只,经检测过的石油专用管材钻具在石油勘探、开发过程中未出现质量异议,给安全生产提供了保障,其优异的质量、精悍的技术及热忱的服务赢得了广大用户的高度评价。