零部件检测标准
零部件首件检验标准

零部件首件检验规程(草案)1、首件是指每个生产班次加工的的第一个工件,或因换人、换料、换工装、调整机床等工艺条件改变后加工的第一个工件,有些产品首件可以规定为开始的头几件。
2、自检是指生产操作员按照图样、标准、工艺或作业指导书等文件中所规定的项目、频率等要求,在生产过程中对自己所加工或装配的工件进行检测。
如有进行记录的规定,还必须做好记录。
3、首件检验是指对生产开始或工艺条件改变后的首件(或最初几件)产品质量的检验。
4、实行首件自检、复检制度,以防止发生成批不合格品。
首件未经检验,不得继续加工或作业。
未经首件检验造成的不合格品由生产操作员负责;因首件错检造成的成批不合格品,质量检验人员应负错检责任。
5、质量检验部门检验验收的产品(包括首检零部件),都必须有明显的识别标记,填写质量证明文件,做好原始记录,办理检验验收手续,建立和保存质量检验档案,以保证质量检验工作的可追溯性。
6、对以下情况都应进行首件检验:1)刚上班或换班后加工出来的第一件产品。
2)调整设备后加工出的第一件产品。
3)调整或更换工装加工出的第一件产品。
4)改变工艺参数或操作方法加工的第一件产品。
5)改变原材料、毛坯、半成品后加工的第一件产品。
7、首件检验应检验的项目是:1)图号与加工路线单(工作票)是否相符。
2)材料、毛坯、半成品与图样和工艺规程是否相符。
3)检验材料、零件表面处理、配合部位的加工表面有无宏观的缺陷。
4)所检验的零件数量、前工序的加工质量合格与否,加工路线单上质量检验人员的盖章和签证是否正确。
5)量具应事先校对好,确保检测的数据正确无误。
6)检验加工出的首件(批)产品的质量是否符合产品的图样、工艺和技术标准的要求。
8、生产操作员要认真进行零部件首件自检,经反复调试直至零部件合格要求为止。
自检合格后,生产操作员需填写《首件自检记录表》,方可向检验人员交检,首件必须做出标识。
质量检验人员对交检的首件产品应再次进行检验,其合格率达不到要求的产品应全部退回生产工人重新进行自检,然后质量检验人员接受再次交检。
非金属材料及其零部件检测标准
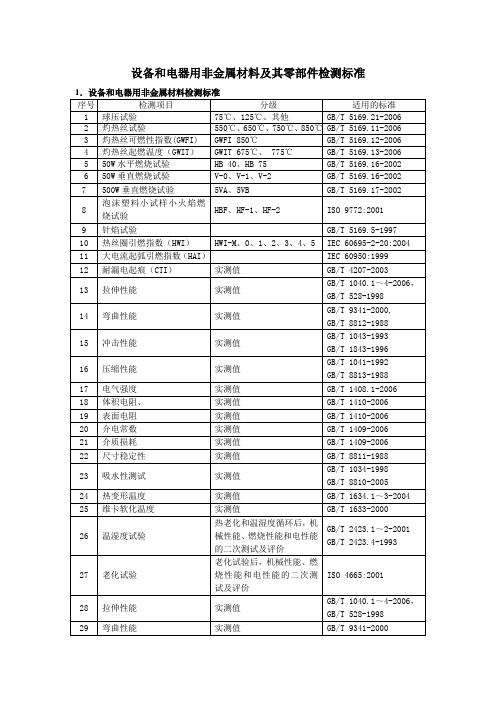
2.热分解温度
3.玻璃化温度
5
GB/T 12630一般用途薄覆铜箔环氧玻璃布层压板(制造多层印制板用)
6
GB/T 13555印制电路用挠性覆铜箔聚酰亚胺薄膜
一、产品性能
1.剥离强度(热应力后)
2.பைடு நூலகம்离强度(高温下)
3.恒定湿热后表面电阻率和体积电阻率
4.垂直于板面的电气强度
5.可焊性
3.弯曲强度(板厚1.0以上)
4.恒定湿热后表面电阻率和体积电阻率
5.热应力
6.可焊性
7.燃烧性
8.击穿电压(板厚≥0.5mm)(供选用)
9.电气强度(板厚<0.5mm)(供选用)
10.耐电弧(板厚≥0.10mm)(供选用)
11.相比电痕化指数(CTI)(供选用)
12.卤素含量(供选用)
二、材料分析
1.红外光谱分析
2.热分解温度
3.玻璃化温度
4.铅含量
4
GB/T 12629限定燃烧性的薄覆铜箔环氧玻布层压板(制造多层印制板用)
一、产品性能
1.剥离强度(热应力后)
2.剥离强度(高温下)
3.恒定湿热后表面电阻率和体积电阻率
4.热应力
5.可焊性
6.燃烧性(CEPGC-34F)
7.电气强度(供选用)
二、材料分析
5.热应力
6.可焊性
7.燃烧性
8.击穿电压(供选用)
9.耐电弧(供选用)
10.相比电痕化指数(CTI)(供选用)
11.卤素含量(供选用)
二、材料分析
1.红外光谱分析
2.热分解温度
3.玻璃化温度
4.铅含量
3
GB/T 4725印制电路用覆铜箔环氧玻璃布层压板
汽车零部件检测要求
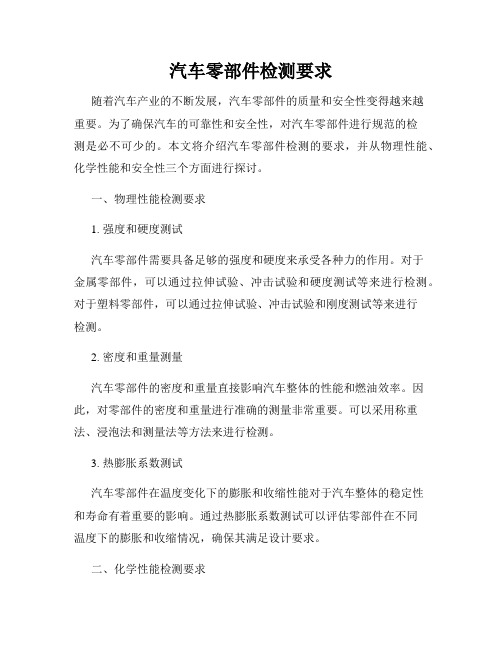
汽车零部件检测要求随着汽车产业的不断发展,汽车零部件的质量和安全性变得越来越重要。
为了确保汽车的可靠性和安全性,对汽车零部件进行规范的检测是必不可少的。
本文将介绍汽车零部件检测的要求,并从物理性能、化学性能和安全性三个方面进行探讨。
一、物理性能检测要求1. 强度和硬度测试汽车零部件需要具备足够的强度和硬度来承受各种力的作用。
对于金属零部件,可以通过拉伸试验、冲击试验和硬度测试等来进行检测。
对于塑料零部件,可以通过拉伸试验、冲击试验和刚度测试等来进行检测。
2. 密度和重量测量汽车零部件的密度和重量直接影响汽车整体的性能和燃油效率。
因此,对零部件的密度和重量进行准确的测量非常重要。
可以采用称重法、浸泡法和测量法等方法来进行检测。
3. 热膨胀系数测试汽车零部件在温度变化下的膨胀和收缩性能对于汽车整体的稳定性和寿命有着重要的影响。
通过热膨胀系数测试可以评估零部件在不同温度下的膨胀和收缩情况,确保其满足设计要求。
二、化学性能检测要求1. 化学成分分析汽车零部件在使用过程中会暴露在各种工作环境和化学物质中,因此对零部件的化学成分进行分析是十分必要的。
通过化学成分分析可以确定零部件的成分组成,确保其符合相关标准和法规要求。
2. 耐腐蚀性测试汽车零部件需要具备良好的耐腐蚀性能,以应对复杂的工作环境。
可以通过盐雾试验、湿热试验和化学试剂浸泡试验等方法来评估零部件的耐腐蚀性能,并确保其在恶劣环境下的使用寿命。
3. 表面处理性能检测汽车零部件的表面处理对于外观和使用寿命有着直接的影响。
可以通过表面质量检查、耐磨性测试和附着力测试等方法来评估零部件的表面处理质量,并确保其满足相关要求。
三、安全性检测要求1. 摩擦性能测试摩擦性能直接影响零部件与其他部件之间的紧密程度和操作的顺畅性。
可以通过滑动摩擦试验、磨损试验和耐磨试验等方法来评估零部件的摩擦性能,并确保其能够正常工作。
2. 安全阻燃性能测试汽车零部件需要具备良好的阻燃性能,以确保在发生事故时能够有效地防止火灾蔓延。
汽车零部件检测标准

汽车零部件检测标准
汽车零部件的质量直接影响着汽车的安全性能和使用寿命,因此汽车零部件的检测标准显得尤为重要。
汽车零部件检测标准是指对汽车零部件进行检测时所遵循的一系列规定和要求,其目的是保障汽车零部件的质量,确保汽车的安全性能和可靠性。
首先,汽车零部件的检测标准应包括对零部件材料的检测要求。
材料是汽车零部件的基础,对材料的检测是确保汽车零部件质量的重要环节。
在材料检测中,应包括对材料的化学成分、力学性能、物理性能等多个方面的检测要求,以确保材料的质量符合汽车零部件的使用要求。
其次,汽车零部件的检测标准还应包括对零部件制造工艺的检测要求。
制造工艺是决定汽车零部件质量的关键因素之一,对制造工艺的检测要求包括对零部件的加工精度、表面质量、装配工艺等多个方面的要求,以确保零部件在制造过程中不会出现质量缺陷。
此外,汽车零部件的检测标准还应包括对零部件性能的检测要求。
汽车零部件的性能是其最终发挥功能的保证,对性能的检测要求包括对零部件的耐久性、可靠性、安全性等多个方面的要求,以确保零部件在使用过程中能够稳定可靠地发挥其功能。
最后,汽车零部件的检测标准还应包括对零部件外观质量的检测要求。
外观质量是汽车零部件质量的重要标志之一,对外观质量的检测要求包括对零部件的表面光洁度、表面平整度、表面涂装等多个方面的要求,以确保零部件在外观上符合汽车制造商的要求。
综上所述,汽车零部件的检测标准是确保汽车零部件质量的重要保障,其内容应包括对材料、制造工艺、性能和外观质量的全面检测要求。
只有严格遵循汽车零
部件的检测标准,才能够确保汽车零部件的质量,从而保障汽车的安全性能和可靠性。
汽车零部件检测报告办理流程及测试标准(二)
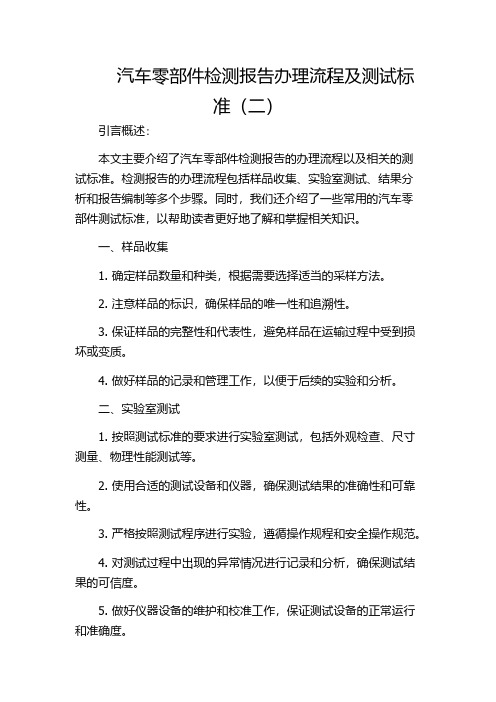
汽车零部件检测报告办理流程及测试标准(二)引言概述:本文主要介绍了汽车零部件检测报告的办理流程以及相关的测试标准。
检测报告的办理流程包括样品收集、实验室测试、结果分析和报告编制等多个步骤。
同时,我们还介绍了一些常用的汽车零部件测试标准,以帮助读者更好地了解和掌握相关知识。
一、样品收集1. 确定样品数量和种类,根据需要选择适当的采样方法。
2. 注意样品的标识,确保样品的唯一性和追溯性。
3. 保证样品的完整性和代表性,避免样品在运输过程中受到损坏或变质。
4. 做好样品的记录和管理工作,以便于后续的实验和分析。
二、实验室测试1. 按照测试标准的要求进行实验室测试,包括外观检查、尺寸测量、物理性能测试等。
2. 使用合适的测试设备和仪器,确保测试结果的准确性和可靠性。
3. 严格按照测试程序进行实验,遵循操作规程和安全操作规范。
4. 对测试过程中出现的异常情况进行记录和分析,确保测试结果的可信度。
5. 做好仪器设备的维护和校准工作,保证测试设备的正常运行和准确度。
三、结果分析1. 对实验室测试结果进行统计和分析,包括平均值、标准差、置信区间等。
2. 根据测试结果与相应标准进行比对,判断样品是否符合相关要求。
3. 对不合格样品进行分析,确定不合格的原因和改进措施。
4. 将结果分析的过程和方法记录下来,以备不时之需。
四、报告编制1. 根据测试结果和分析,编制汽车零部件检测报告。
2. 报告内容包括样品的基本信息、实验室测试方法和结果、结果分析和结论等。
3. 报告应准确、清晰地表达测试结果和分析过程。
4. 报告格式应符合相关标准和规范,包括文本、表格、图表等。
5. 报告应在规定的时间内完成,并及时交付给相关部门或客户。
总结:本文详细介绍了汽车零部件检测报告的办理流程及相关的测试标准。
通过样品收集、实验室测试、结果分析和报告编制等一系列步骤,可以确保检测报告的准确性和可信度。
同时,合理运用测试标准和分析方法,可以更好地判断样品质量,并提供改进意见。
汽车零部件检测测试标准
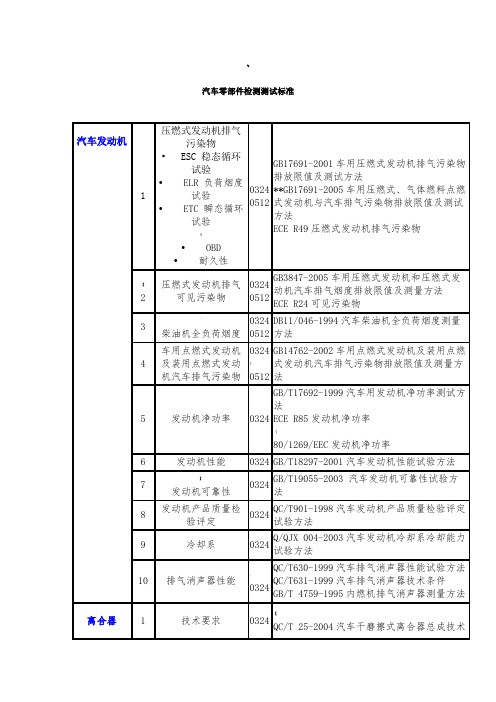
扭转疲劳
3
临界转速
半轴
1
静扭强度
0324
QC/T 294-1992汽车半轴技术条件
QC/T 293-1992汽车半轴台架试验方法
2
扭转疲劳
燃油箱
1
安全性能要求
(
0324
GB18296-2001汽车燃油箱安全性能要求和试验方法
QC/T644-2000汽车金属燃油箱技术条件
筒式减振器
1
技术条件
0324
12
侧标志灯配光性能
13
驻车灯配光性能
14
|
三角警告牌光度
汽车灯具
15
色温
0324
GB11564-1998、ECE R3、76/757/EEC、ECE R69、ECE R70、ECER104
0324
》
0512
GB14762-2002车用点燃式发动机及装用点燃式发动机汽车排气污染物排放限值及测量方法
5
发动机净功率
0324
GB/T17692-1999汽车用发动机净功率测试方法
ECE R85发动机净功率
《
80/1269/EEC发动机净功率
6
发动机性能
0324
GB/T18297-2001汽车发动机性能试验方法
GB 9341-2000塑料弯曲性能试验方法
2
力学性能
3
拉伸性能
4
~
压缩性能
5
热空气老化
6
冲击试验
7
状态调节
8
弯曲性能
汽车内饰材料
(
1
燃烧时间
0324
GB 8410-1994汽车内饰材料的燃烧特性
零部件检验标准及方法

零部件检验标准及方法零部件检验标准及方法1. 背景介绍在制造工业中,零部件的质量检验是确保产品品质的关键环节之一。
通过对零部件进行科学、严谨的检验,可以提高产品的可靠性和安全性。
本文将介绍常用的零部件检验标准及方法。
2. 外观检验•目的:检查零部件外观是否符合要求,包括表面光洁度、几何形状、尺寸精度等方面。
•方法:–直接目视检查:通过直接观察零部件外观,判断是否存在缺陷、损伤等问题。
–使用显微镜或放大镜进行检查:通过放大镜或显微镜观察细微的表面问题,如划痕、气孔等。
–使用测量工具进行尺寸检验:使用卡尺、量规等测量工具,对零部件的尺寸进行检查,确保其符合要求。
3. 功能性检验•目的:检查零部件的功能是否符合设计要求。
•方法:–运行测试:将零部件安装到相应的设备或系统中,进行正常工作状态下的运行测试,观察其功能是否正常。
–性能测试:使用专门的性能测试设备,对零部件进行负载测试、耐压测试、抗振动测试等,验证其性能是否达标。
4. 材料检验•目的:检查零部件所使用的材料是否符合要求,包括化学成分、物理性能等。
•方法:–化学分析:使用化学分析仪器,对材料进行成分分析,确保其成分符合要求。
–物理性能测试:使用拉力机、硬度计等测试材料的物理性能,如强度、硬度等。
5. 寿命检验•目的:检查零部件的使用寿命是否符合要求。
•方法:–疲劳测试:通过对零部件进行循环加载、循环使用等方式,检测其在长期使用过程中的寿命情况。
–加速老化测试:使用特定的老化设备,对零部件进行加速老化测试,模拟长期使用环境,检查其在短时间内的寿命表现。
6. 环境适应性检验•目的:检查零部件在特定环境条件下的适应性。
•方法:–温度适应性测试:将零部件暴露在不同温度条件下,观察其在不同温度下的性能变化。
–湿度适应性测试:将零部件暴露在高湿度或低湿度条件下,观察其在不同湿度条件下的性能表现。
–耐腐蚀性测试:将零部件暴露在化学腐蚀性环境中,观察其对腐蚀的抵抗能力。
汽车零部件质量检测标准

汽车零部件质量检测标准随着汽车行业的快速发展,汽车零部件的质量问题也越来越受到重视。
为了确保汽车的安全性、可靠性和性能,制定一套统一的汽车零部件质量检测标准非常重要。
本文将围绕汽车零部件质量检测标准展开论述,包括测试项目、测试方法和测试标准等方面的内容。
第一部分:测试项目在汽车零部件质量检测中,涉及到的测试项目非常多。
首先是外观检查,这是检测零部件表面是否存在缺陷、损坏或不符合设计要求的重要步骤。
其次是尺寸测量,包括长度、宽度、高度等方面的测量,以确保零部件的尺寸与设计要求一致。
此外,还包括力学性能测试、材料分析等多个测试项目。
第二部分:测试方法针对不同的测试项目,需要采用不同的测试方法。
例如,在外观检查中,可以采用人工目视检查和辅助工具检查相结合的方法,以确保零部件表面没有划痕、裂纹和变形等异常情况。
在尺寸测量中,可以使用三坐标测量仪等先进设备进行精确测量。
对于力学性能测试,可以使用拉力试验机、冲击试验机等设备进行力学性能测试。
对于材料分析,可以使用化学分析仪、显微镜等设备进行材料成分和微观结构的分析。
第三部分:测试标准为了保证汽车零部件的质量稳定、一致性和可比性,需要制定一套统一的测试标准。
在外观检查中,可以根据不同零部件的要求,制定详细的检查标准,包括外观缺陷的类型、缺陷的大小、缺陷位置等方面的要求。
在尺寸测量中,可以制定零部件的尺寸公差以及测量方法和设备要求。
在力学性能测试中,可以根据零部件的功能要求,制定相应的力学性能指标和测试方法。
对于材料分析,可以制定各种材料的成分范围和典型的微观结构要求,以确保材料的质量和性能。
小结:汽车零部件质量检测标准是确保汽车零部件质量的重要保证。
通过明确的测试项目、科学的测试方法和严格的测试标准,可以有效提高汽车零部件的质量,从而提升汽车整体的安全性和可靠性。
通过不断完善和更新汽车零部件质量检测标准,可以逐步提高汽车零部件质量,并推动整个汽车行业的可持续发展。
- 1、下载文档前请自行甄别文档内容的完整性,平台不提供额外的编辑、内容补充、找答案等附加服务。
- 2、"仅部分预览"的文档,不可在线预览部分如存在完整性等问题,可反馈申请退款(可完整预览的文档不适用该条件!)。
- 3、如文档侵犯您的权益,请联系客服反馈,我们会尽快为您处理(人工客服工作时间:9:00-18:30)。
零部件检测标准
1、目的:
提升零部件质量,有效加强过程检验控制,将制定标准符合工作需要,能够起到指导实际工作的作用。
2、适用范围:
标准规定了本公司产品的零部件检验要求及抽样方法。
本标准适用于公司生产的各种产品所需的零部件质量验收。
3、引用标准
下列标准所包含的条文,通过在本标准中引用而构成为本标准的条文。
本标准发布时,下列标准所示版本均为有效。
所有标准都会被修订,使用本标准的各方应探讨使用下列标准最新版本的可能性。
GB2828.1-2003 计数抽样检验程序第1部分:按接收质量限(AQL)检索的逐批检验抽样计划
GB2828.2-2008 计数抽样检验程序第2部分:按极限质量LQ检索的孤立批检验抽样方案
4、抽样方法
4.1所有零部件均按GB2828进行抽样检验。
4.1.1根据本公司以往检查数据,根据抽样过程平均不合格品率无偏估计值-P,
确定轴承合格品质量水平AQL=0.15,并确定为正常检查一次抽样方案,采用一般检查水平Ⅱ。
4.1.2抽样过程:
a.在表1中,由批量范围、检查水平所在列相交处,读出样本大小字码。
b.在表2中,由样本大小字码所在行向右,在样本大小栏内,读出n(样
本大小)。
另外,由样本大小字码所在行与AQL=0.15所在列相交处读出
[Ac,Re](一次抽样方案的判定数组)。
c.检查员按判定数组判定合格与否。
示例:求批量N=1000时,正常检查一次抽样方案按抽样规定AQL=0.15,IL (检查水平)=Ⅱ
a.从表1中包含N=1000的行(501~1200),与IL=Ⅱ所在列相交处,读出
样本大小字码J。
b.在表2中,由样本大小字码J所在行向右,在样本大小栏内读出n=80(样
本大小),另外,由样本大小字码J所在行与AQL=0.15所在列相交处读
出[0,1]。
c.因而所求正常检查一次抽样方案如下:
n=80,Ac=0(合格判定数),Re=1(不合格判定数)。
4.1.3 在查表2时,如遇到样本大小字码栏的字码同合格质量水平(AQL)行的相交处读出的是向下(上)箭头时,可沿箭头方向读出第一个判定数组[x x],然后由读出的这个判定数组[x x]向左,在样本大小栏内读出样本大小(n)。
4.1.4 当n大于批量数值时,不按GB2828进行抽样检验,此时按批量数进行全检。
4.1.5对抽样件规定,精度要求0.05mm以内的样件尺寸要求全检。
精度要求0.1mm—0.2mm抽检20%。
自由差抽检一至两件。
4.1.6对于铸件(铸铁、铸钢、铸铝、铸铜、粉末冶金等)的样件要求所有尺寸
全检。
4.1.7对新开的钻具、模具的样件要求全检。
4.1.8检查记录必须符合检验规定。
5、关键件检查的规定。
5.1、外协件齿轮的检测:
5.1.1、送检单位报检时检验记录完整,检验数据齐全。
5.1.2、检查员按照报检总数的6%抽检,并按图纸的要求检验。
检验项目如下:齿轮的里孔、外圆和其它孔的孔径,孔的位置度,齿轮端跳,台阶孔的同轴度,键槽的尺寸和键槽的对称度。
接收标准为0过1不过,即只要有1件不合格品即视为整批不合格,整批拒收,检查员开具不合格品处置通知单。
5.1.3、常规检验合格后,检查员将测量过的齿轮交付精测室进行齿形、齿向、和齿距累积误差的检测。
5.1.4、检查员认真填写齿轮检验记录,并与月底上报质量部。
5.2、厂内加工齿轮:
5.2.1、各种厂内加工齿轮,首件必须检验;
5.2.2、厂内齿轮在加工过程中,检查员进行抽检,每种齿轮的抽检数量为齿轮加工总量的10%,检测齿轮的公法线变动量和公法线平均长度。
5.2.3、齿轮加工结束后,检查员对加工的尾件进行检验。
尾件合格,转入仓储中心。
尾件不合格,对齿轮进行复检,合格件转入仓储中心,不合格件开具不合格品处置通知单。
5.2.4、检查员认真填写齿轮检验记录,并于月底上报质量部。
5.3、侧板检测
5.3.1、外检员对各种侧板的铸造质量进行检验,检测侧板的外观质量和铸造缺陷,铸件肥大、砂眼、疏松、清砂等,抽检数是报检总数的6%。
5.3.2、主体侧板检验:
5.3.2.1、各种主体侧板厚度是100%检验,每片侧板厚度检测9-10个位置。
5.3.2.2、侧板的平面度、垂直度、长度尺寸的检验是首件必检,每6片侧板抽检1片。
5.3.2.3、侧板孔的数量,有公差要求孔的直径及圆柱度,有公差要求的槽和型腔尺寸是100%检验。
5.3.3、油墨侧板检验:
5.3.3.1、GH524、564油墨侧板:
5.3.3.1.1外检员对侧板的厚度、平面度、垂直度等关键尺寸进行检验。
数量在50片以下时,抽检总数的8%,数量在50片以上时,抽检总数的6%。
接收标准是0过1不过。
5.3.3.1.2侧板的平行度检验是首件必检,每8对油墨侧板抽检1对。
5.3.3.1.3侧板孔的数量、有公差要求孔的直径、孔的圆柱度,有公差要求的槽和型腔尺寸是100%检验。
5.3.3.2、GH664、474油墨侧板:
5.3.3.2.1侧板厚度是100%检验,每片侧板厚度检测4个位置。
5.3.3.2.2侧板的平面度、平行度、垂直度的检验是首件必检,每6片侧板抽检1片。
5.3.3.2.3侧板孔的数量、有公差要求孔的直径、孔的圆柱度,有公差要求的槽和型腔尺寸是100%检验。
5.3.4、供纸、排纸侧板检验:
5.3.4.1、侧板厚度、平面度、平行度、垂直度的检验是首件必检,每6片侧板抽检1片。
5.3.4.2、侧板孔的数量、有公差要求孔的直径、孔的圆柱度,有公差要求的槽和型腔尺寸是100%检验。
5.3.5、检查员在侧板各道工序检验时,对侧板的铸造质量,砂眼、疏松、清砂等进行检验。
5.3.6、检测完成后,检查员填写检验记录,并于月底上报质量部。
5.4、为了强化压印辊、传纸辊咬纸牙座与夹箍的质量控制,防止不合格品进入装配车间,特制定本规定。
5.4.1、送检单位报检时检验记录完整,检验数据齐全。
5.4.2、检查员严格按照GB2828.1-2003中的要求检验, 200件以下抽检32件,200-500件以下抽检64件,执行一次抽样方案。
即只要有1件不合格品即视为整批不合格,整批拒收,检查员开具不合格品处置通知单。
5.4.3、500件以上抽检125件,执行二次抽样方案。
即125件如果全部合格,整批接收。
如果出现1件不合格,再次抽样32件,检验全部合格,接收。
再有1件不合格,整批拒收,检查员开具不合格品处置通知单。
5.4.4、检查员除检验零部件形状和位置精度外,还必须对咬纸牙座与夹箍合件进行穿轴配对检验。
5.4.5、检测完成后,检查员填写压印辊、传纸辊咬纸牙座合件抽检记录,并于月底上报质量部。
5.4.6、质量部负责统计每月进入装配车间的压印辊、传纸辊咬纸牙座合件不合格品率,并于月初反馈给外协部。