高强度灰铸铁生产中不可忽视的技术问题
灰铸铁几个关键技术问题的探讨_逄伟

实际上我们还发现, 当铸件中含有较多数量 碳化钛和氮化钛颗粒时, 高速切削的刀具寿命并 不差,我们也有意做过不加钛的试验,目的就是减 少钛的硬质点数量,但并没有因此改善切削性能。 对于多加钛确实影响到切削性能主要的原因是, 钛使石墨产生过冷倾向,是由于恶化了石墨形态, 使断屑性能明显变差, 不能归结为是形成氮化钛 或碳化钛硬质点。
2 硬质点颗粒对断屑性能的影响
切削性能差时我们往往归结为材料中有硬质 点 , 如 碳 化 物 或 其 他 硬 质 点 ( 碳 化 钛 、氮 化 钛 ), 所 以要改善切削性能, 就要尽可能采取措施减少硬 质点,数量越少越好 。因此通常合金化大都采取 以 加 铜 、锡 为 主 , 并 且 加 大 孕 育 量 , 认 为 这 对 切 削 性能有利。之所以得出这样的结论是认为硬质点 会打刀。
1 灰铸铁中锰、硫的特性及作用
灰铸铁中的锰、硫是一对非常特殊的元素,由 于锰、硫要形成 M nS 夹杂物,这就使得锰、硫的作 用变得有些特殊。
(1)锰 我们一直把锰作为一个 合 金 化 元 素 来用,认为加锰能提高灰铸铁的强度和硬度,这种 观点很少有人怀疑过。但是,通过试验却发现事实 并非如此。在碳硅量高,硫量也较高的情况下,加锰 后灰铸铁的性能并没有提高,反而下降。对于这样 的结论,我们经过了反复的验证,试验结果见表 1。
现在就可以解释为什么在碳硅当量高、硫量 也较高的情况下,灰铸铁中加锰不起合金化作用, 性能反而降低: 因为在碳硅当量高、硫量也较高 时,锰高就会中和铁液中硫,形成 M nS,锰量增加, 中和的硫量就大,使铁液中的自由硫量降低,石墨
形态就要发生不利的变化,石墨变得平顺,长度变 长,端部的钝化效果变差,这些变化都会影响到性 能。另外,大量 M nS 夹杂物的一部分会成为石墨 的晶核,还有一部分会发生聚集,形成局部密集的 M nS 排列,夹杂物本身是要影响材料性能的。这就 是加锰反而使灰铸铁性能降低的原因。锰的合金 化 作 用 被 形 成 M nS 的 这 一 特 性 所 带 来 的 不 利 影 响掩盖了。锰与硫在碳硅量高、硫量也较高的灰铸 铁中的这一特性一定要引起重视。如果不了解锰、 硫的这一特性, 把锰作为提高性能的合金元素的 结果是:加入许多锰,性能反而降低。如果再加入 更多的其他合金元素,又会使铸造性能变差,极其 有害,这种情况很容易被人忽略。
灰铁铸件质量控制与缺陷识别方法

灰铁铸件质量控制与缺陷识别方法灰铁铸件是一种常见的工业材料,具有较低的生产成本和良好的加工性能。
然而,由于材料特性以及生产过程中可能存在的不完美,灰铁铸件的质量问题和缺陷成为制约其应用的重要因素。
因此,灰铁铸件质量控制与缺陷识别方法显得尤为重要。
一、灰铁铸件质量控制的重要性灰铁铸件广泛应用于汽车零部件、机械设备等领域,其质量直接关系到产品的性能和安全性。
良好的质量控制能够提高产品的使用寿命和可靠性,降低质量问题带来的生产成本和后续维护费用。
因此,对灰铁铸件质量控制的重视程度不可忽视。
二、常见的灰铁铸件缺陷1. 气孔:气孔是灰铁铸件中最为普遍的缺陷之一。
它们通常以气泡的形式存在于铸件中,使得铸件的力学性能下降。
2. 砂眼:砂眼是由于砂芯粘结剂挥发或砂芯被刮伤导致的缺陷。
它们通常以凹陷的形式出现在铸件表面。
3. 裂纹:裂纹是在灰铁铸件冷却过程中由于内部应力超过材料强度引起的。
裂纹不仅对铸件的力学性能产生不利影响,还可能导致铸件的完全失效。
三、灰铁铸件质量控制方法1. 严格控制铸造过程:灰铁铸件的质量问题往往源自于铸造过程中的不完善,因此,严格控制铸造过程是保证灰铁铸件质量的关键。
包括熔炼温度的控制、熔融金属的净化、铸型的预热等。
2. 合理设计铸型和砂芯:铸型和砂芯的设计对于灰铁铸件质量至关重要。
合理的铸型设计能够减少铸件内部气体的积聚;而砂芯的设计则可以避免砂眼等常见缺陷的产生。
3. 使用先进的检测设备:随着科技的进步,越来越多的先进检测设备被应用于灰铁铸件的质量控制中。
例如,X射线检测、超声波检测等技术能够快速且准确地检测出灰铁铸件的缺陷并进行修复。
四、灰铁铸件缺陷识别方法1. 目测检查法:目测检查是最常用也是最简单的铸件缺陷识别方法之一。
通过观察铸件表面,如有裂纹、气孔等可见缺陷的出现,可以及时发现并进行处理。
2. 渗透检测法:渗透检测法是一种常用的缺陷检测方法,利用缺陷表面张力的改变来识别缺陷。
灰铸铁件生产中的几点技术措施

灰铸铁件生产中的几点技术措施 <宏达铸造工具铸顶芯撑>发布者:枣强县宏达毛刷厂发布时间:2011-6-28 阅读:665次【字体:大中双击自动滚屏小】如何改善铸件的内在与外观质量,提高铸件的技术含量,应对市场的竞争,是国内部分生产企业所面临的课题。
铸件生产中的每个环节对质量都有着重要影响,不可忽视。
现将本人在实际工作中总结的一些技术措施归纳如下,供借鉴。
一、砂芯和砂型的刚性砂型浇注后,由于铁液的静压力或凝固而引起的膨胀力,常导致型壁移动和砂芯溃散,这就会使铸件产生内部缩孔和表面缩陷。
因此为使铸件尺寸稳定,要最大限度地使铸型紧实。
为了节约造型材料,造芯时广泛采用了空心砂芯,它比实体芯轻,故热容量小,凝固速度慢,这会导致砂型扩张或砂芯溃散。
此外,铁液可能通过芯头或砂芯上的裂纹而渗入其中空部分,这也会使铸件产生缺陷。
为了提高空心砂芯的刚性,可用湿型砂或水玻璃砂充填;也可将壳芯作成两半,其内部设置加强筋,造芯后粘合可得到坚硬的砂芯。
二、正确选择浇注温度1.浇注温度过低时可能形成的缺陷(1)硫化锰气孔此种气孔位于铸件表皮以下且多在上面,常在加工后显露出来,气孔直径约2~6mm。
有时孔中含有少量熔渣,金相研究表明,此缺陷是由MnS偏析与熔渣混合而成,原因是浇注温度低,同时铁液中含Mn和S量高。
为防止这种缺陷,用冲天炉化铁时可在多孔材料的浇包中用气流连续脱S,将S降至0.06%~0.08%。
这样的含S量和适宜的含Mn量(0.5%~0.65%),可以显著改善铁液纯度,从而有效地防止这类缺陷。
(2)液体夹渣加工后铸件表皮之下会发现一个个单体的小孔,孔的直径一般为1~3mm。
个别情况下只有1~2个小孔。
金相研究表明,这些小孔与少量的液体夹渣一起出现,但该处未发现S的偏析。
研究表明,这种缺陷与浇注温度有关,浇注温度高于1380℃时,铸件中未发现这种缺陷,故浇注温度应控制在1380—1420℃。
值得一提的是改变浇注系统设计,未能消除此缺陷,故此种缺陷可以认为是由于浇注温度低以及铁液在微量还原气氛下浇注时形成的。
灰铸铁缺陷产生的原因分析及预防措施

灰铸铁缺陷产生的原因分析及预防措施灰铸铁是一种铸铁材料,广泛应用于工业生产中。
然而,灰铸铁在生产过程中常常会产生一些缺陷,影响产品质量和使用寿命。
本文将分析灰铸铁缺陷的一些常见原因,并提出相应的预防措施。
首先,原材料的选择和质量会直接影响灰铸铁的缺陷产生。
原材料中的含碳量不均匀、硫、磷含量过高等都可能导致气孔、夹杂物等缺陷的产生。
因此,在原材料采购时,应选择质量稳定可靠的供应商,严格控制原材料的成分和质量。
其次,铸造工艺是产生灰铸铁缺陷的重要原因之一、铸造温度、浇注速度、冷却速度等工艺参数的不当选择都可能引起缺陷。
例如,铸造温度过高会导致灰铸铁组织粗化,同时加速固化速度,容易产生疏松缺陷;而铸造温度过低则容易使灰铸铁凝固速度过慢,产生大的铁素体晶粒和残余奥氏体,导致脆性增加。
因此,应根据具体工件的要求,合理选取铸造工艺参数,确保铸件质量。
此外,铸造设备的状态和操作对于灰铸铁缺陷的产生也有影响。
设备的使用寿命、维护保养情况都会影响铸件质量。
例如,设备老化导致温度控制不稳定,浇注时温度波动较大,容易引起疏松缺陷。
为了减少设备因素引起的缺陷,应定期对设备进行检查和维护,并采取合适的设备调整措施。
为了预防灰铸铁缺陷的产生,可以从以下几个方面采取相应的措施。
首先,在原材料选择上,应选用质量稳定的材料,并进行严格的原材料检测,确保其成分和质量符合要求。
其次,在铸造工艺中,应根据具体情况合理选择铸造温度、浇注速度和冷却速度等工艺参数,以获得良好的铸件结构和性能。
另外,在铸造过程中,可以采取保温措施,增加浇注温度的稳定性,避免因温度波动而引起的缺陷。
此外,设备的维护和保养也是很重要的,定期对设备进行检查和维修,确保设备的正常运行,减少因设备因素引起的缺陷。
最后,铸造工艺的控制和优化也是减少灰铸铁缺陷的重要手段。
通过工艺优化和改进,可以进一步提高产品质量和减少缺陷产生的可能性。
综上所述,灰铸铁缺陷的产生主要与原材料、铸造工艺和设备等因素有关。
灰铁件铸造易产生的13种缺陷,原因与防止方法,铸造人必备!

灰铁件铸造易产生的13种缺陷,原因与防止方法,铸造人必备!灰铸铁件由于造型制芯时造成的主要缺陷及其原因分析与防止方法(1)气孔特征及发现方法:局部气孔:铸件的局部地方,出现的孔穴表面较干净光滑的单个气孔或蜂窝状气孔用外观检查,机械加工或磁力探伤可以发现。
原因分析:1.浇注系统设置不合理,使排气不畅通或产生涡流,卷入气体2.砂型紧实度过高,降低了透气性3.砂芯排气不良,或通气道堵塞防止方法:1.浇注系统的设置应考虑型腔内排气畅通及平稳流入铸型2.砂型紧实度要求均匀,不宜过紧3.砂芯排气要求畅通。
合箱时,注意封死芯头间隙,以免铁液钻人,堵塞通气道4.在铸件的最高处,可设置出气孔或出气片等5.起模和修型时,不宜刷水过多6.对于大平面铸件,可采用倾斜浇注,出气孔处稍高,以利排气7.芯撑和冷铁必须千净,无锈(2)砂眼特征及发现方法:铸件的孔穴内含有砂粒用外现检查,机械加工或磁力探伤可以发现原因分析:1.浇注系统位置不合适,如直对砂芯,或浇口太小,铁液冲刷力大。
破坏局部砂型2.由于模型结构设计不够好,发生粘模,而砂型又未修理好,或对铸件拐弯处未捣圆角3.湿型在浇注前的停留时间过长,使干澡部分或凸出部位脱落4.造型和合箱时的落砂,未清砂干净防止方法:1.浇注系统位置和大小合适2.合理选择起模斜度和圆角,手工造型时,可压出圆角。
成批生产中,模样应涂刷分型剂,以免粘模,并往意修理好损坏部位。
3.缩短湿型在浇注前的停留时间4.合理选用芯头和芯座之间的间隙,以免合箱时压碎5.合箱前,必须将型内落砂清扫干净,仔细合箱,并及时盖住浇冒口,以免重新掉入砂粒(3)夹砂特征及发现方法:在铸件表面上,一层铁和铸件之间夹有一层型砂用外观检查或机械加工可以发现原因分析:铁液进人砂型后。
使型面层的水分向内迁移,在离型面3~5mrn 处形成高水分带。
该处强度大大降低,易引起铁液潜入,或由于硅砂粒高温膨胀的应力使表面层鼓起,铁液钻入,形成夹砂。
灰铸铁缺陷及预防措施

灰铸铁缺陷及预防措施灰铸铁是一种常见的铸造材料,广泛应用于汽车制造、机械制造、建筑工程等领域。
然而,灰铸铁在生产过程中可能会出现一些缺陷,如气孔、夹杂物、砂眼等,这些缺陷会降低铸件的质量和性能。
为了提高灰铸铁的质量,需要采取一些预防措施。
1. 控制原材料的质量:灰铸铁的原材料主要包括铁水、生铁、废铁和合金等。
在生产过程中,应对原材料进行严格的质量控制,确保其符合标准要求。
特别是废铁和合金等次生材料,需要经过严格的筛选和检测,以避免其中的杂质对铸件质量的影响。
2. 控制熔炼工艺参数:熔炼是灰铸铁生产的关键环节,熔炼工艺参数的控制对铸件质量至关重要。
首先,需要选择合适的炉型和燃料,以确保熔炼温度和熔化能力的稳定。
其次,需要合理控制熔炼时间和熔炼温度,避免过热或过冷导致铸件缺陷的产生。
同时,还需要控制熔炼过程中的气氛和熔体的搅拌方式,以提高熔体的均匀性和纯净度。
3. 严格控制铸造工艺参数:铸造是灰铸铁生产的关键环节之一,铸造工艺参数的控制对铸件质量有着重要影响。
首先,需要选择合适的铸型材料和型腔设计,以确保铸件的凝固过程稳定。
其次,需要控制浇注温度、浇注速度和浇注方式等参数,避免热裂纹、冷隔和气孔等缺陷的产生。
同时,还需要合理控制铸件的冷却速度和冷却方法,以保证铸件的显微组织和力学性能。
4. 加强铸件的检测和质量控制:在生产过程中,需要对铸件进行全面的检测和质量控制,以确保其达到设计要求。
常用的检测方法包括尺寸检测、外观检查、磁粉探伤、超声波检测等。
此外,还可以采用金相显微镜、扫描电镜等高级检测设备,对铸件的组织和缺陷进行分析和评估。
通过加强检测和质量控制,可以及时发现和解决铸件的缺陷问题,提高产品的合格率和可靠性。
5. 加强员工培训和技术支持:为了保证灰铸铁生产的质量和稳定性,需要加强员工的培训和技术支持。
员工应具备良好的铸造技术和操作技能,了解铸造工艺和设备的使用方法。
同时,还需要定期组织技术培训和交流,提高员工的综合素质和技术水平。
灰铸铁缺陷及预防措施
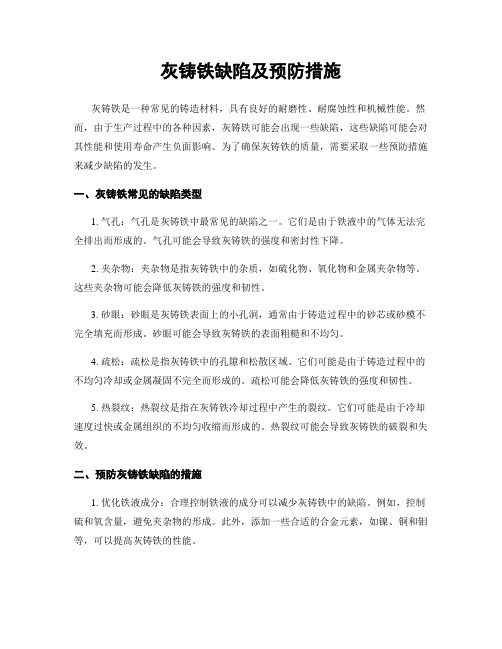
灰铸铁缺陷及预防措施灰铸铁是一种常见的铸造材料,具有良好的耐磨性、耐腐蚀性和机械性能。
然而,由于生产过程中的各种因素,灰铸铁可能会出现一些缺陷,这些缺陷可能会对其性能和使用寿命产生负面影响。
为了确保灰铸铁的质量,需要采取一些预防措施来减少缺陷的发生。
一、灰铸铁常见的缺陷类型1. 气孔:气孔是灰铸铁中最常见的缺陷之一。
它们是由于铁液中的气体无法完全排出而形成的。
气孔可能会导致灰铸铁的强度和密封性下降。
2. 夹杂物:夹杂物是指灰铸铁中的杂质,如硫化物、氧化物和金属夹杂物等。
这些夹杂物可能会降低灰铸铁的强度和韧性。
3. 砂眼:砂眼是灰铸铁表面上的小孔洞,通常由于铸造过程中的砂芯或砂模不完全填充而形成。
砂眼可能会导致灰铸铁的表面粗糙和不均匀。
4. 疏松:疏松是指灰铸铁中的孔隙和松散区域。
它们可能是由于铸造过程中的不均匀冷却或金属凝固不完全而形成的。
疏松可能会降低灰铸铁的强度和韧性。
5. 热裂纹:热裂纹是指在灰铸铁冷却过程中产生的裂纹。
它们可能是由于冷却速度过快或金属组织的不均匀收缩而形成的。
热裂纹可能会导致灰铸铁的破裂和失效。
二、预防灰铸铁缺陷的措施1. 优化铁液成分:合理控制铁液的成分可以减少灰铸铁中的缺陷。
例如,控制硫和氧含量,避免夹杂物的形成。
此外,添加一些合适的合金元素,如镍、铜和钼等,可以提高灰铸铁的性能。
2. 控制浇注温度和速度:合理控制浇注温度和速度可以减少气孔和疏松的形成。
温度过高或过低都会对灰铸铁的质量产生不利影响。
此外,控制浇注速度可以减少砂眼的发生。
3. 优化砂芯和砂模设计:合理设计砂芯和砂模可以减少砂眼和热裂纹的形成。
确保砂芯和砂模完全填充,并避免过度收缩和应力集中。
4. 控制冷却速度:合理控制灰铸铁的冷却速度可以减少热裂纹的形成。
可以采用适当的冷却介质和冷却时间来控制冷却速度。
5. 加强质量检测:对灰铸铁进行严格的质量检测可以及早发现和排除缺陷。
常用的检测方法包括金相显微镜检测、超声波检测和磁粉检测等。
灰铸铁件损伤、冷裂、温裂、变形、金相不合格、过硬六大缺陷的防止方法

灰铸铁件损伤、冷裂、温裂、变形、金相不合格、过硬六大缺陷的防止方法灰铸铁件由于落砂清理、热处理时造成的主要缺陷及其原因分析与防止方法(1)损伤特征及发现方法:损坏了铸件的完整性用外观检查可以发现原因分析:1.在开箱、搬运或清理时不注意2.打浇、冒口的方向不对或冒口颈过大,造成带肉缺陷防止方法:1.认真按照工艺规程和要求操作2.正确掌握打浇、冒口的方向(2)冷裂特征及发现方法:1.薄壳零件落砂时被振裂,并违反操作规程2.采用水爆清砂时,热应力较大,当应力超过铸件某部分的抗拉强度时,应生冷裂防止方法:1.对易裂的薄壳零件,清理时应挑出,另行清理,并认真执行合理的操作规程2.根据铸件结构和性能特点,选用合理的清理方式和清理工其3.严格执行水爆工艺4.在运输和清理过程中,尽量减轻碰撞(3)温裂特征及发现方法:开裂处金属表皮氧化用外观检查,透光法,磁力探伤,打压试验,煤油渗透等方法发现原因分析:由于气割、焊接或热处理不当,温度应力大所引起防止方法:正确制订并认真执行合理的焊接、热处理规范和操作规程(4)变形特征及发现方法:长的或扁平类铸件在靠近壁厚的一方凹入成弯曲形用外观检查,划线等方法发现原因分析:在铸件冷却过程中,产生的铸造应力超过该材质的屈服极限时,则产生塑性变形和挠曲为减少和消除铸件的残留应力,可采用人工时效(即退火热处理),若热处理规范不正确,仍会产生变形和挠曲防止方法:1.改变热处理规范,使其合理,并认真执行2.延长开箱时间或把刚落砂的铸件送入保温炉中保温,并随炉缓慢冷却(5)金相不合格特征及发现方法:铸件断面的粗视组织和显微组织不符合标准或技术条件用断面观察,金相检验可以发现原因分析:1.开箱时间不当2.热处理规范不正确防止方法:1.按技术要求,合理控制铸件的开箱时间2.改变热处理规范,使其合理,并认真执行(6)过硬特征及发现方法:在铸件边缘和薄璧处出现白口铁组织断面观察,硬度试验,机械加工可以发现原因分析:开箱时间过早防止方法:适当延长开箱时间或在退火炉中缓慢降温。
- 1、下载文档前请自行甄别文档内容的完整性,平台不提供额外的编辑、内容补充、找答案等附加服务。
- 2、"仅部分预览"的文档,不可在线预览部分如存在完整性等问题,可反馈申请退款(可完整预览的文档不适用该条件!)。
- 3、如文档侵犯您的权益,请联系客服反馈,我们会尽快为您处理(人工客服工作时间:9:00-18:30)。
高强度灰铸铁生产中不可忽视的技术问题1、摘要:灰铸铁是“面大量广”的常用金属结构材料。
本文主要论述了合金元素硫、锰含量及其比例,微量元素钛和氮的控制,以及孕育剂加入量对灰铸铁组织和性能的影响。
据统计,2007年我国铸件产量达到了3000万多吨,其中,灰铸铁占60-70%。
由于灰铸铁具有独特的性能特点,它在机械、机床、冶金、汽车等行业的应用中占有非常重要的位置。
改革开放30年来,我国的灰铸铁生产技术水平获得了很大提高。
但与国外先进国家相比,还存在着较大差距。
在高强度灰铸铁生产过程中,我国大多数工厂比较注重五大元素、合金元素、熔炼温度、铸造工艺等因素的控制,这些因素的控制对提高灰铸铁的内在质量和外在质量是至关重要的。
但是,还有一些其他因素没有引起人们足够的重视,这些同样对灰铸铁的质量有着重要影响,譬如,元素硫与锰的含量与比例,微量元素钛、氮的控制以及孕育剂加入量等细节的掌握。
本文就这些因素对灰铸铁组织和性能的影响进行讨论,抛砖引玉,以期引起人们的注意。
1硫、锰的控制(1)硫过去,由于我国的灰铸铁和球墨铸铁大部分利用冲天炉熔炼,铁液的增硫比较严重,导致原铁液的含硫量较高,使得铸铁的铸造性能、力学性能降低,球化效果不好,所以,在人们的记忆中硫是一个有害元素。
随着电炉熔炼工艺的发展,可以容易获得含硫量低的铁液,这对处理球墨铸铁非常有利。
但是,有些工厂在灰铸铁生产中发现,电炉灰铸铁的材质性能还不如冲天炉好。
因此,硫不能被简单的被认为是一个有害元素。
在灰铸铁生产中发现,硫量控制在一定范围内,随着硫量的增加,片状石墨长度变短,石墨形态变得弯曲,而且石墨的头部变得钝化,并细化共晶团,提高强度。
为什么硫在一定范围内,促进石墨化,改善石墨形态?硫在铁水中的溶解度很低,对Fe-C 系平衡相图的影响不是很大。
但硫降低碳在铁水中的溶解度,理应是一个促进石墨化的元素,实际上它对石墨化的影响比较复杂。
硫对铸铁的凝固呈现双重作用【1】,一方面,硫与Mn、Sr、Ba等元素形成硫化物,为共晶石墨的成核提供基底,增加共晶团数量;另一方面,硫作为表面活性元素,富集在结晶前沿,会抑制共晶团的生长,增加结晶过冷度,白口倾向增大。
硫可溶于液态铸铁中,但不溶于凝固的奥氏体和共晶团中,所以适当的硫(0.04-0.10%S)富集于共晶团的边界而干涉原子的扩散,从而限制共晶团的生长,使石墨分枝减少,导致生成厚而短的片状石墨。
当硫含量较低(<0.03%)时,结晶前沿硫阻挡层的限制较弱,同时,缺乏硫化物石墨晶核,降低孕育效果,则易于生成大个共晶团的D型石墨和菊花状石墨。
当铁液中的含硫量增加到0.04-0.10%时,铸铁的孕育效果增强,同时铁水的表面张力б降低,铁水与石墨的湿润角θ减小,使得更多的硫化物基底成为石墨核心,共晶团数增加,A型石墨取代了D型石墨。
当铸铁的硫量超过0.11%,石墨由片状又逐渐返回到丛状D型石墨【2】。
这是由于当含硫量较高时,硫对铸铁结晶生长的抑制作用加强,使结晶的过冷度加大,造成有利于过冷石墨生长条件,甚至产生白口组织。
经过大量生产和试验发现,将含硫量控制在0.06-0.10%范围内,可以增强孕育效果,改善石墨形态,对提高灰铸铁强度是有利的,同时,又能改善铸铁的机加工性能【3】。
对于电炉熔炼灰铸铁,经常遇到含硫量低的情况,必须采取增硫措施,才能获得优质灰铸铁件。
(2)锰在普通灰铸铁中,锰一直作为合金元素控制基体的珠光体含量,通常认为加锰可以提高灰铸铁的强度和硬度。
实际上,锰对灰铸铁的强度性能的影响具有双重作用【4】:一方面,锰能促进珠光体的形成,细化珠光体,有助于提高强度;另一方面,含锰量太高,影响铁液结晶时的形核,使共晶团数量减少,石墨粗大,甚至可能出现过冷石墨,从而使铸铁的强度降低。
近年来,通过生产实践证明,灰铸铁强度并不是随锰量提高而增加,如在汽缸盖生产中,锰量增加,灰铸铁抗拉强度降低,如表1所示【5】。
在铁液中,锰与硫化合形成MnS,随着锰量增加,与锰结合的硫量就大,使铁液中的自由硫含量降低,抑制了硫的有利作用,石墨长度增加,端部钝化效果变差,导致铸铁性能下降。
另外,形成的大量MnS夹杂物,一部分形成石墨核心,另一部分则会发生聚集,形成局部密集的MnS 排列,消弱了基体的强度。
因此,含锰量增加,灰铸铁的强度降低。
另外,有资料表明【6】,锰对灰铸铁强度的影响与碳当量有关。
当碳当量为3.65-3.95%时,其抗拉强度随着锰量的增加显着降低。
当碳当量为3.96-4.15%时,其抗拉强度随着锰量的增加有所提高。
(3)Mn/S比由于硫在灰铸铁则会具有双重作用,同时,锰与硫化合形成的MnS又具有核心功能,但过多的MnS对灰铸铁的强度没有益处。
所以,硫和锰的含量在铸铁中存在着相互制约的关系,即存在着一个合理的Mn/S。
通常认为,当S<0.2%时,以Mn=1.7S+0.3来考虑锰含量。
生产实践证明【6】,Mn/S对灰铸铁的性能有较大的影响。
当CE为3.70%~3.85%时,σb随Mn/S的增大而降低;当CE为3.90%~4.05时,σb随Mn/S的增大先降低然后提高。
当CE为3.70%~3.95%时,Mn/S=3~5,抗强度较佳,取Mn/S=4;当S=0.07%~0.15%时,Mn 0.3%~0.6%。
当CE为3.96%~4.05%时,Mn/S=5~7,抗拉强度较佳,取Mn/S=6,当S=0.07%-0.15%时,Mn 0.4%~0.9%。
2钛的控制钛是强烈形成碳化物,与碳、氮、氧具有很强的化学亲和力,形成TiN、TiC、或Ti(N C),其硬度极高(TiC 3200Hv,VC 2800Hv),常以颗粒状存在于铸铁基体中。
少量的Ti可以细化石墨,但随着钛含量的增加,D型石墨增多,并且,Ti分布在D型石墨区域。
当Ti含量超过0.15%,D型石墨达到95%。
Ti对灰铸铁抗拉强度有较大的影响【7】。
当含Ti量在0.13%以下时,灰铸铁的抗拉强度随含Ti量的增加而下降,含Ti量为0.13%时,出现了最低值222.20MPa;当含Ti量大于0.13%时,其抗拉强度随含Ti量的增加而升高,当含Ti量增加到0.36%时,抗拉强度升高到271.79MPa。
Ti对灰铸铁硬度也有较大的影响。
当含Ti量在0.04%以下时,随Ti量的增加硬度下降;当含Ti量大于0.04%时,其硬度随含Ti量的增加而增加;当含Ti量为0.36%时,硬度高达226HB。
Ti含量小于0.03%时,铁液的白口倾向减小,具有提高灰铸铁冶金质量指标的趋势。
值得注意的是,含钛量的大小对灰铸铁的加工性能影响较大【8】。
随着钛含量的增加,刀具磨损严重,同时,影响加工铸件的表面光洁度。
3氮的控制一般情况下,氮在灰铸铁中含量较低,生产单位大都不具备化验氮的手段和仪器,所以,它对灰铸铁的作用没有引起人们的足够重视。
研究表明【9】,氮对灰铸铁的组织有较大的影响,主要作用表现两个方面:一是对基体组织的影响,二是对石墨形态的影响。
氮降低灰铸铁的共析转变温度,并使得共析转变温度区间加大【10】。
氮对灰铸铁基体的影响表现在三个方面:一是氮可以使初生奥氏体枝晶臂间距减小,二是氮作为碳化物稳定元素,促进铸态珠光体的含量增加和稳定性,三是有效地促进共晶形核,细化基体组织,增加珠光体和铁素体的显微硬度。
氮对铸铁石墨的形态、数量、分布有很大影响。
日本张博等人的研究表明,铸铁中吹入氮气,不加入任何球化元素,可以使石墨球化。
对于普通灰铸铁,加入适量的氮可使得片状石墨长度缩短、弯曲程度增加、端部钝化、长宽比减小。
因此,灰铸铁中含有一定的氮,可显着提高强度和硬度。
生产实践证明,在相同化学成分条件下,冲天炉熔炼铁液浇注的铸件力学性能低于电炉熔炼。
通常认为,其原因是冲天炉铁液温度低,存在着炉料遗传问题。
实际上,这与铁液的含氮量有关。
冲天炉熔炼时,由于使用生铁量较多,而高碳生铁的含氮量较低,一般冲天炉灰铸铁中的含氮量为40-70ppm【11】。
通常废钢的含氮量比铸造生铁高的多,用感应电炉熔炼铸铁时,炉料中所用生铁较少,废钢比例较大,另外,电炉熔炼多使用增碳剂,而大多数增碳剂中氮含量较高,所以,感应电炉熔制的灰铸铁含氮量比较高。
一般,炉料中废钢比例越大,铸铁中含氮量越高,如表1所示【11】。
另外,需要指出,不同炼钢工艺获得的废钢的含氮量也是不同的,如表2所示。
氮是廉价的资源,对改善灰铸铁的组织和力学性能具有积极的作用,在当今铁合金价格飞涨的形势下,有效利用氮对灰铸铁进行微合金化是值得重视的技术。
但是,也应该充分注意过量的氮将造成气孔甚至微观裂纹缺陷。
因此,在氮的应用中,应注重其科学性,充分合理地利用氮的积极作用,尽量避免其消极作用。
4孕育剂加入量控制孕育处理是高强度灰铸铁生产中的重要技术环节。
孕育的主要目的是:促进石墨化,减少白口倾向;改善断面均匀性;控制石墨形态,减少过冷石墨,获得细小的A型石墨;增加共晶团数量;改善力学性能和其他性能。
由于孕育可显着提高共晶团数量,有些工厂为了提高灰铸铁的强度,认为孕育剂加入量越多越好,有的达到0.8-1.0%。
实际上这是一个错误的认识。
孕育剂加入量是孕育工艺中必须考虑的一个重要因素。
加入量太少,将导致孕育不足产生白口和硬度太高的现象,从而使力学性能和加工性能降低。
但是,孕育剂加入量过多,并不能增加孕育效果,可能带来以下不利影响:过多的孕育剂加入量,使铁液降温增加,可能造成熔化不完全,增加夹渣的可能性;使铁液的收缩量加大而生产缩孔的可能性加大;由于共晶团数过多,导致粥状凝固,石墨化膨胀增加产生型壁位移,而易产生缩松,造成铸件的渗漏。
生产实践发现【3】,有意识的降低原铁液的含硅量而加大孕育量,灰铸铁的力学性能并不比高硅原铁液通过适量孕育得到力学性能好。
一般认为,对原铁液尽量控制较高的含硅量,将孕育量控制在0.4%左右为宜。
通常所讲的强化孕育处理,不是指加大孕育剂用量,而是指选择合适的优质孕育剂,改进孕育工艺方法。
5结束语当前,随着市场竞争的加剧,灰铸铁作为一种传统的金属结构材料,正面临着质量、性能和价格的严重挑战。
铸造企业应顺应灰铸铁材质高强度化、高附加值化和工艺稳定化的趋势,提高铸件质量,加大技术开发力度,籍以全面提升产品和服务质量,增强市场竞争力,提高技术经济效益。
在灰铸铁的生产过程中,以往人们只注重常规五大元素对铸铁材质的影响,而对其他一些微量元素认识不足,仅仅有的也是一个定性认识。
近年来,由于铸造技术的进步,熔炼设备也在不断的更新,焦炭价格节节攀升,冲天炉熔炼成本逐渐增加,很多企业正在考虑用电炉代替冲天炉熔化铁液。
电炉熔炼固然有其冲天炉不可比拟的优点,但电炉熔炼也失去了冲天炉熔炼的一些优点,这样,某些微量元素对灰铸铁的影响也就反映出来。