002铸轧工艺操作规程
铸造工艺操作规程范本

铸造工艺操作规程范本第一章总则第一条为加强铸造工艺操作,确保铸造质量,保障生产安全,制定本操作规程。
第二条本规程适用于铸造工艺的操作和管理,所有参与铸造工艺的人员必须遵守本规程。
第三条铸造工艺操作人员应具备相关的铸造知识和技能,严格遵守操作规程和工艺要求。
第二章工艺准备第四条铸造工艺操作前,必须进行工艺准备,包括准备材料、设备和工具等,确保顺利进行。
第五条铸造工艺操作人员应对所用的铸造材料进行检验,确保其质量符合要求。
第六条铸造工艺操作人员应检查设备及工具的完好程度,确保其能够正常使用。
第三章环境与安全第七条铸造工艺操作时,必须确保操作环境清洁、整齐,并保证通风良好。
第八条铸造工艺操作人员必须佩戴符合安全要求的个人防护装备,包括安全帽、防护眼镜、耳塞等。
第九条铸造工艺操作人员应熟悉和遵守相关的安全操作规程,严禁违章操作。
第四章操作程序第十条铸造工艺操作必须按照规定的操作程序进行,不得随意更改和省略。
第十一条铸造工艺操作人员应仔细阅读工艺文件和要求,了解工艺流程和工序要求。
第十二条铸造工艺操作必须严格按照标准要求进行操作,确保产品质量。
第十三条铸造工艺操作人员应注意操作和设备的安全,发现异常情况及时报告。
第十四条铸造工艺操作人员应做好记录工作,包括工艺参数、设备运行状态等。
第五章现场管理第十五条铸造工艺操作现场必须保持整洁,杂物要及时清理、整理。
第十六条铸造工艺操作人员应按照工艺要求组织、协调好相关工作。
第十七条铸造工艺操作现场必须禁止吸烟、明火和乱堆乱放。
第六章故障处理第十八条铸造工艺操作中出现设备故障、异常情况时,操作人员应立即停机,通知相关人员进行处理。
第十九条铸造工艺操作人员应熟悉常见故障现象和处理方法,能够迅速排除故障。
第二十条铸造工艺操作人员应及时向领导层报告故障处理情况,并提出改进意见。
第七章质量控制第二十一条铸造工艺操作人员必须按照工艺要求进行质量控制,确保产品合格。
第二十二条铸造工艺操作人员应认真填写相应的质量记录,确保质量数据准确完整。
铸轧工艺操作规程
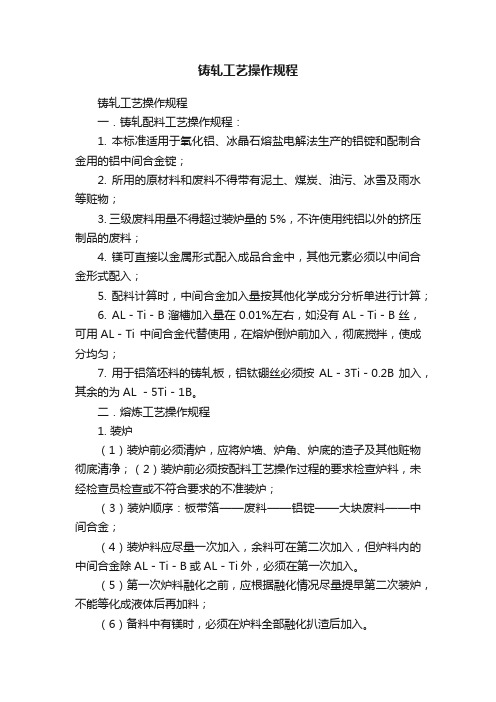
铸轧工艺操作规程铸轧工艺操作规程一.铸轧配料工艺操作规程:1. 本标准适用于氧化铝、冰晶石熔盐电解法生产的铝锭和配制合金用的铝中间合金锭;2. 所用的原材料和废料不得带有泥土、煤炭、油污、冰雪及雨水等赃物;3. 三级废料用量不得超过装炉量的5%,不许使用纯铝以外的挤压制品的废料;4. 镁可直接以金属形式配入成品合金中,其他元素必须以中间合金形式配入;5. 配料计算时,中间合金加入量按其他化学成分分析单进行计算;6. AL-Ti-B溜槽加入量在0.01%左右,如没有AL-Ti-B丝,可用AL-Ti 中间合金代替使用,在熔炉倒炉前加入,彻底搅拌,使成分均匀;7. 用于铝箔坯料的铸轧板,铝钛硼丝必须按AL-3Ti-0.2B加入,其余的为AL -5Ti-1B。
二.熔炼工艺操作规程1. 装炉(1)装炉前必须清炉,应将炉墙、炉角、炉底的渣子及其他赃物彻底清净;(2)装炉前必须按配料工艺操作过程的要求检查炉料,未经检查员检查或不符合要求的不准装炉;(3)装炉顺序:板带箔——废料——铝锭——大块废料——中间合金;(4)装炉料应尽量一次加入,余料可在第二次加入,但炉料内的中间合金除AL-Ti-B或AL-Ti外,必须在第一次加入。
(5)第一次炉料融化之前,应根据融化情况尽量提早第二次装炉,不能等化成液体后再加料;(6)备料中有镁时,必须在炉料全部融化扒渣后加入。
2. 熔炼(1)按燃气熔炼炉安全操作规程要求点火,先明火后燃气,如一次点不着,立即关闭燃气阀,打开空气吹尽炉膛内残余燃气,再进行第二次点火,点燃后检查燃烧情况,调整风量,已达到最佳燃烧;(2)当炉料已大部分熔化时,可用耙子将液面上的凸包推平或进行轻微搅拌;(3)炉料全部熔化后,在熔炼温度范围内进行彻底搅拌,时间不能低于10—15分钟,扒渣时,操作要平稳,要先近后远,要扒净,并尽量避免带出金属;(4)熔炼温度范围:纯铝700-760°C,合金720-760°C;(5)取样:在熔炼温度范围内,用干净的取样勺,在炉子两个炉门的中间,液体宽度和深度的中部舀取试样,试样不得有气孔、夹渣、裂纹;(6)根据快速分析结果,按合金化学成分标准和铸轧工艺要求调整成分;(7)冲淡要用原铝锭或确知成份和牌号的纯铝一级废料。
2023年铸造工艺操作规程

2023年铸造工艺操作规程第一章总则第一条为规范和规范化2023年铸造工艺的操作流程,提高生产效率,确保产品质量,制定本操作规程。
第二条本规程适用于所有从事铸造工艺操作的工作人员。
第三条所有从事铸造工艺操作的工作人员必须遵守本规程,严格按照操作流程进行操作。
第四条铸造工艺操作应遵循安全第一、质量第一的原则,确保操作人员的身体安全和生产环境的安全。
第五条铸造工艺操作应遵守相关的法律法规和政策规定,保护环境和资源。
第二章岗位职责第六条所有从事铸造工艺操作的工作人员应具备相关的岗位职责,按照工艺操作流程完成工作任务。
第七条铸造工艺操作的岗位职责包括但不限于以下几个方面:1.准备工作:包括准备材料、检查设备、调整设备参数等。
2.操作工作:包括开机、调试、加工等操作工作。
3.检测工作:包括对产品进行质量检测和检验,保证产品符合要求。
4.维护工作:包括设备维护、保养等工作,确保设备正常运行。
5.安全工作:包括安全检查、消防设备检查等工作,确保工作场所的安全。
第三章操作流程第八条铸造工艺操作应按照以下流程进行:1.准备工作:包括准备材料、检查设备、调整设备参数等。
2.操作工作:按照工艺流程进行操作,确保产品质量。
3.检测工作:对产品进行质量检测和检验,保证产品符合要求。
4.维护工作:对设备进行维护、保养等工作,确保设备正常运行。
5.安全工作:进行安全检查、消防设备检查等工作,确保工作场所的安全。
第九条操作前,应制定具体的操作计划和操作指导,明确操作程序和注意事项。
第四章操作规范第十条所有从事铸造工艺操作的工作人员应遵循以下操作规范:1.严格遵守操作流程,不得随意改变工艺流程。
2.熟悉设备功能和操作方法,严禁未经培训或未获得许可使用设备。
3.严格遵守操作规程,保持操作规范,不得违规操作。
4.严格按照操作规程进行质量检测和检验,不得随意抽检或漏检。
5.认真维护设备,按时进行保养和维修,确保设备正常运行。
第五章安全防护第十一条铸造工艺操作应加强安全防护,确保操作人员的身体安全。
铸轧操作规程

铸轧车间¢1000×1850 ㎜双驱动铸轧机工艺操作规程(一)、设备主要技术参数一、设备主要技术参数表 1二、¢1000×1850 ㎜双驱动铸轧机主要参数 表 2序号 项目单位 数值1 适应材料1 系、 8 系、 3 系2 铸轧板厚 ㎜ ~103 铸轧板宽 ㎜ 900~17004 卷材外径 ㎜ ¢800~17005 最大卷重 ㎏100006 最大轧制力 MN7 最大卷取力 KN 50 8铸轧速度㎜/min800~11009工作辊直径㎜¢950~1000数值13000-15000850360Cz500 硅碳棒6×3项目炉膛尺寸炉子容量炉膛温度功率加热元件热区数序号123456单位㎜ ㎏℃KW(二)、大清炉3.静置炉每一个月进行一次大清炉。
正常情形下,静置炉炉料铸干或者改换合金时进行大清炉。
特殊情形下,由于持续生产相同合金,静置炉长时刻不能铸干或者改换合金时,由生产计划员安排在每一个月 25-31 日之间将静置炉铸干,进行大清炉。
4、大清炉时,先将炉内残留金属全数放干,把炉渣彻底清除,然后撒入20±2 ㎏粉状溶剂,并将炉温升至800℃以上,用三角铲把炉墙、炉角、炉底的渣子彻底铲净、扒出。
(三)、导炉及精炼5.导炉及精炼导炉:5.1.1导炉前静置炉炉膛温度不得低于740℃,熔体导入前,先将炉墙及炉底熔渣松动待精炼后一路扒出。
5.1.2 当熔炼炉内熔体成份合格,温度适合(720-745℃),后即可导炉,若是在熔炼炉内没有精炼,则导炉进程应进行过流精炼。
为保证产品质量熔体在熔炼炉内的保温时刻,(精炼完毕到导炉开始)不得超过一小时,最长不得超过 4 小时不然应在熔体表面撒上覆盖剂,导炉前从头搅拌、扒渣。
并适当降低熔体温度。
5.1.4 正常铸轧进程,导炉前静置炉熔体深度不该低于200mm。
静置炉内精炼:5.2.1 精炼时熔体温度:740~760℃5.2.2 精炼方式:5.2.2.1 每熔次在导炉前(本公司) 采用四氯化碳进行精炼。
铸轧车间工艺技术操作规程

铸轧车间工艺技术操作规程《修订本》****铝业有限责任公司二00八年十月目录1、原辅材料工艺管理规程-------------------3 2配料工艺操作规程------------------------4 3熔炼工艺操作规程------------------------5 4铸轧工艺操作规程------------------------8 5铸轧辊辊套修磨工艺规程------------------11 6炉子管理技术规程------------------------11 7煤气发生沪技术操作规程----------------- 12 8供料嘴组装尺寸--------------------------14 9铸轧车间工序质量标准及检查程序和方法----16 10铝及铝合金铸轧带材行业标准-------------19原辅材料工艺管理规程一..铝锭材料管理规程1进入铸轧材料仓库铝锭,必须要有化学成份分析单且应满足表1的规定。
3表面应整洁,无严重的飞边、气孔、夹渣和腐蚀。
铝锭不得粘附泥土、雨水、霜雪和油污.打包标准铝锭只许放二层,。
二、中间合金及添加剂4、进入铸轧材料仓库的中间合金或金属添加剂,必须要有化学成份分析单,并且化学成份合格,存放时必须要有明显标志,切勿混装运输或与铝锭混淆。
见表2,仓库发出时应按先后顺序,避免先购回产品因时间过长而变质报废.表2 中间合金化学成份及颜色标志三、复化锭5 进入铸轧材料仓库的复化锭,必须要有化学成份分析单。
6 复化锭表面应整洁、无严重飞边、气孔、夹渣和腐蚀,不得粘附有泥土、雨雪、油污等脏物。
7 复化锭外形尺寸不做统一规定,但每批形状应规整统一。
8复化锭应按合金成份不同分开存放,并且要有明显标志,堆放应整齐,高度不能超过1.2米。
四废料9 废料的分级:废料按三级分类,其标准见表3(1)所有废料必须按级别、合金牌号的不同分开保管,不能混放,(2)各车间必须按废料标准的分级和合金分组严格管理,杜绝混料。
铸轧机操作工艺

铸轧机操作工艺铸轧机操作工艺一、熔炼炉工艺操作规程1 有专人常常检查熔炼炉到静置炉的倒炉流槽是否通畅,发觉问题,准时处理2 熔炼炉低温点火,必需先用风机吹扫炉内残余煤气后,将火把放在烧嘴口,再开煤气,然后给适量的空气3 当炉料达到约10t(约250mm深)时,举行测温,当温度达到730-740℃时,撒入除渣剂10kg,扒渣,然后搅拌4 当炉料达到预定吨位时举行测温,假如温度达到730-740℃,撒入除渣剂10kg举行扒渣,搅拌5 当炉料升温至770-780℃时,撒入8kg除渣剂,彻底扒出底渣和表面渣,取样分析Fe、Si、Cu含量.对纯铝而言,控制Fe/Si比为1.2-2.06 用除气砖4块,在炉门口除气精炼7 除气精炼后,拔出表面渣,预备导炉,导炉前必需检查导炉流槽是否通畅,并预热好8 每熔次导完炉后举行小清炉,每五熔次举行一次大清炉,将熔炼炉内的炉墙,炉底的渣子彻底清理扒出二、静置炉工艺操作规程1 静置炉内剩余金属层约6t时,开头从熔炼炉往静置炉导炉,最好每次倒满17t,每导一次炉为新熔次号开头2 导完炉后,测温,控制炉温(金属温度)为760-770℃3 检查并预热扒渣耙,扒除表面渣4 用除气砖4块,分离同时在两个炉门举行除气精炼,不留死角,精炼除气时光普通为10-15分钟5 彻底扒除表面渣,使金属液面如镜面6 预热取样勺,取炉前分析试样,分析Fe、Sa、Cu含量,并填入随行卡片7 插入热电偶,调好定温8 关好两个炉门,防止散温三、立板操作1 立板前的预备a .检查铸轧机列各部分及冷却水系统是否运转正常,须要时试运转,同时将各个辊子表面清理整洁,特殊是铸轧辊要清擦整洁b.开动高压泵,调节好压力,调好辊缝,辊缝按照需要普通控制在6.0-6.2mm之间,传动侧比操作测大0.02-0.03mmc.用火焰喷涂预热润滑铸轧辊d.从加热炉内取出供料嘴,检查,并在嘴子拼装平台上举行组装,用大头针固定好分流块及边块,盖上上嘴扇.做好前箱液面高度标记e.将嘴子放在升降台上,对正键槽,调节好上下、左右、前后尺寸,上好压紧螺丝,缓慢将嘴子推向轧辊,调好嘴辊间隙,并调节铸轧区至合适位置,装上耳子并压紧,将铸轧辊反向转动,打磨耳子及嘴唇f.架上前箱,用棉将嘴子各部空隙塞好,防止漏铝g.架上前箱流槽,在衔接处用棉塞好,调节好直管与浮标之间位置h.将各处放流箱摆好,架好暂时流槽i.将各种工具就位,特殊是大钳子,不得少于2根2立板工艺操作规程1)打开大钎子(静置炉石墨堵头)向除气箱供流,并负责控制好流槽内金属水平,在直管下的流槽处开头放流,并放上温度计2)当金属液流温度达到正常铸轧温度730-740℃时,堵死放流口,往前箱注流,注流前将前箱往铸嘴放流的流口用小堵头堵死3)当前箱内铝液将要漫过前箱上沿时,开头注入嘴腔,主操立刻启动轧机,使轧辊以最高速度运转,此时前箱金属水平由前箱操作人员负责控制,使其液面平稳4)在铝液温度达到成型温度时,主操按照状况减慢主机速度5)主操凝视轧机电流的变化(上下辊电流),当电流上升时(是铸轧开头的信号)要通过操作控制手柄(主机调速旋钮)渐渐降低铸轧速度,并密切凝视铸轧板状况和前箱金属温度(正常轧辊电流约为20-25A)6)当铸轧板正常后,出口侧人员,将铸轧板托上托辊(支撑辊),.然后托上送入剪扳机.当铸轧板长1米左右时,打开水阀供水,冷却轧辊,点燃火焰喷涂,开头润滑轧辊7)前箱操作人员放上控流浮标,稳定前箱金属液面8)测量铸轧板同板差,主操利用单侧压下或双侧压下手柄调节压力,使两边板厚全都9)当铸轧板进入剪扳机,切掉铸轧板不规章的板头10)主操升起卷取机前面的导板,按下钳口定位按钮,启动卷取机,缩紧卷取机涨缩缸,使导板前端与卷取机钳口对齐11)铸轧板进入卷取机钳口后,送板人员敲板为信号,主操立刻涨开卷取机涨缩缸(一定要到位),启动卷取机,调速不行太快,当铸轧板快拉平常,按下张力投入按钮,开头卷板,此时主操不行万事大吉,必需等铸轧板在卷筒上卷够一圈,压住板头后方可放心12)调节好铸轧板张力(普通控制在12-16A)13)启动钛丝机,开头供钛丝,供丝速度为50%为18cm/min,60%为21cm/min.按照板面晶粒度状况举行调节14)待板面及同板差所有正常后,剪断废料,开头重新上卷,卷成品四、正常铸轧工艺操作规程1 坚守工作岗位,精确准时记录各种工艺参数,如发觉板面浮现缺陷要找到缘由准时处理.并在生产卡片上照实做好记录.同时在铸轧板边部对应位置做上标记2 样取1)每切一卷成品卷,切一块长度为100-160mm左右试样送化验室作晶粒度检查,并将式样放在该卷内.另切一块长度为300mm左右试样,测量同板差,并将测量结果填入随行卡2)每熔次普通为2卷,在切第一卷后,在浮标下流槽内取铝液化验试样2块,送化验室一块,另一块做备查.化学分析Fe、Si、Cu(纯铝而言)含量,并将化验数据填入随行卡3 卸卷: 当卷重(或卷厚)为生产方案要求时,举行卸卷.卸卷程序如下1)启动低压泵2)将小车送入铸轧卷下,升起小车,使小车导辊基本挨着铸轧卷3)剪断铸轧板,迅速卷板,剪扳机切二块试样4)当铸轧卷板头临近小车前导辊时,停止转动,缩紧卷筒,调节小车高度,打开活动支撑,用推料板与小车同步,推出铸轧卷5)按下钳口定位按钮,启动卷取机,升起导板,将活动支撑支撑,将在线铸轧板板头送入卷取机钳口,然后涨紧卷取机,使卷取机转动,当铸轧板快拉平常,按下张力投入按钮6)等铸轧卷卷至三到五圈后,关闭低压泵7)将小车上的铸轧卷用钢带打捆吊放在铸轧卷堆放架上.在铸轧卷侧面写上编号4 卸卷小车最大承载分量为7t,最大卷径为1700mm(也就是说最大卷厚为600mm)文档内容到此结束,欢迎大家下载、修改、丰富并分享给更多有需要的人。
铸轧工艺操作规程

铸轧工艺操作规程1、根据实际板厚调整好辊缝,并将轧辊转动用纤维粘将辊面清理干净,新辊需用棉纱粘四氯化碳将轧辊油渍清理干净,并用液压气喷涂枪携带压缩空气将轧辊辊面温度烘烤到50-60℃,并根据实际板宽清理边部积炭;2、磨耳子:用120目的纱纸贴严轧辊,将软耳子弧度磨成与两辊完全吻合,磨好后将轧辊辊面清理干净;3、检查设备正常后开始安装铸咀:4. 软质铸咀的组装:4.1从保温炉内,将成型的咀扇和垫块取出。
4.2在安装铸咀前先检查铸咀实际尺寸是否符合生产规格尺寸;4.3、检查铸咀是否损坏,如有损坏需更换咀扇;4.4按铸轧宽度要求,将供料咀放在小车支撑上,对中供料咀小车,咀子后部与咀子小车金属支撑平齐;4.5保证上下咀扇平齐,凸出金属支撑尺寸一致,咀子端部与轧辊中心线平行。
4.6稍稍拧紧压紧螺丝,从两边至中间对称逐个拧紧,每个螺丝拧紧程度要均匀,保证供料咀牢固、不变形。
4.7 调整4.7.1 将供料咀小车缓慢推入两辊间,在侧面观察咀端与铸轧辊是否对中,要求上、下咀唇应同时接触上、下辊面。
4.7.2沿咀子宽度数点测量咀端与轧辊中心线的距离,两边间距要求一致。
4.7.3 将进给小车退回,固定好咀子,并保持辊缝。
4.7.4 启动轧机,使轧辊快速倒转。
4.7.5 将进给小车推入, 使咀子与辊面接触,向前推进3mm左右磨咀子。
4.7.6 将咀子退出检查,要求上、下咀唇磨削对称,沿整个宽度均匀一致。
4.7.7重新推入, 每次推进3mm左右磨咀子,直至获得要求的铸轧区及咀辊间隙(上:0.5mm,下0.8mm)为止,停止轧辊转动。
4.7.8 测量铸轧区,当达到要求的数值时,标记好进给小车的位置,退出咀子,并吹扫干净。
4.7.9重新把小车推入到原来位置,并退后2~3mm。
4.8 固定边部耳子4.8.1 在咀子两侧插入磨好的软耳子,推到与上下轧辊吻合为止。
4.8.2 装好硬质副耳子,硬质耳子不能与上下辊接触,拧紧边部紧固螺丝。
002铸轧工艺操作规程

2、作业程序序号作业顺序作业方法作业标准1设备准备1.新辊立板前必须把辊面的油污擦干净,并用明火(液化气)烘烤4小时以上;平常立板前必须把辊面清理干净。
2。
立板时保温炉内的铝水温度控制较正常轧制时温度上限增加20~30℃。
3。
主要设备的检查.对主转动机构、轧辊压上系统、喷涂系统、液压剪、推料板、送料小车、卷取涨缩、液压及电气系统等进行全面检查.确认正常方可立板。
4.辊缝预设。
通过手动调节楔块系统,改变轧辊轴承座之间的间隙调整辊缝,根据板厚要求不同,辊缝控制:5.5~6。
8mm。
5.安装好过滤片并进行预热。
6.检查、关闭冷却水.辊面积碳均匀;辊缝两边差小于0.02mm。
2铸嘴准备1。
铸嘴制作形状按下图所示进行制作。
1.1铸嘴制作时,若粘贴内腔垫片的溶胶从垫片周围溢出,或内腔粘上溶胶时,必须把溶胶清理干净或在该处刷上氮化硼。
1.2尺寸要求:4>3>2>1,采用渐宽布流;a=80~85mm,b=100mm、120mm、140mm.(根据板宽选择使用)1。
3各垫片、垫条用大头针或钢钉固定。
1。
4在底盘组装时要对中、平直,铸嘴用压板压牢、螺栓进行固定。
1。
5对中固定好两侧耳子,并沿铸嘴前沿根部切出15°的倒角。
2。
铸嘴保温.加工好的铸嘴平稳吊放在保温炉内,保温温度60~150℃,保温时间不小于3小时.3。
铸嘴的安装3.1把铸嘴装配组件从保温炉内取出,检查其是否变形、松动,并进行调整、加固。
3。
2将组装好的铸嘴用行车运至铸嘴平台,通过其快速夹紧装置进行对中、固定.3。
3由步进电机驱动铸嘴平台把铸嘴组件推至距辊缝一段安全位置,然后由水平调节装置把铸嘴调节到目标位置。
3。
4由步进电机调节铸嘴的水平及垂直度.3.5调节过程中,操作人员在出口侧随时观察铸嘴位置及嘴辊间隙.嘴辊间隙:上:1。
6~2。
0mm,下:1.2~1。
6mm;新辊时偏小1mm左右。
3.6检测铸嘴两侧铸轧区是否一致,若不一致,进行单侧调整,使之符合要铸嘴两边厚度差小于0。
- 1、下载文档前请自行甄别文档内容的完整性,平台不提供额外的编辑、内容补充、找答案等附加服务。
- 2、"仅部分预览"的文档,不可在线预览部分如存在完整性等问题,可反馈申请退款(可完整预览的文档不适用该条件!)。
- 3、如文档侵犯您的权益,请联系客服反馈,我们会尽快为您处理(人工客服工作时间:9:00-18:30)。
2、作业程序
序号
作业
顺序
作业方法作业标准1
设备
准备
1.新辊立板前必须把辊面的油污擦干净,并用明火(液化气)烘烤4小时
以上;平常立板前必须把辊面清理干净。
2.立板时保温炉内的铝水温度控制较正常轧制时温度上限增加20~30℃。
3.主要设备的检查。
对主转动机构、轧辊压上系统、喷涂系统、液压剪、
推料板、送料小车、卷取涨缩、液压及电气系统等进行全面检查。
确认正
常方可立板。
4.辊缝预设。
通过手动调节楔块系统,改变轧辊轴承座之间的间隙调整辊
缝,根据板厚要求不同,辊缝控制:5.5~6.8mm。
5.安装好过滤片并进行预热。
6.检查、关闭冷却水。
辊面积碳
均匀;
辊缝两边
差小于
0.02mm。
2
铸嘴
准备
1.铸嘴制作形状按下图所示进行制作。
1.1铸嘴制作时,若粘贴内腔垫片的溶胶从垫片周围溢出,或内腔粘上溶
胶时,必须把溶胶清理干净或在该处刷上氮化硼。
1.2尺寸要求:4>3>2>1,采用渐宽布流;a=80~85mm,b=100mm、120mm、
140mm。
(根据板宽选择使用)
1.3各垫片、垫条用大头针或钢钉固定。
1.4在底盘组装时要对中、平直,铸嘴用压板压牢、螺栓进行固定。
1.5对中固定好两侧耳子,并沿铸嘴前沿根部切出15°的倒角。
2.铸嘴保温。
加工好的铸嘴平稳吊放在保温炉内,保温温度60~150℃,
保温时间不小于3小时。
3.铸嘴的安装
3.1把铸嘴装配组件从保温炉内取出,检查其是否变形、松动,并进行调
整、加固。
3.2将组装好的铸嘴用行车运至铸嘴平台,通过其快速夹紧装置进行对中、
固定。
3.3由步进电机驱动铸嘴平台把铸嘴组件推至距辊缝一段安全位置,然后
由水平调节装置把铸嘴调节到目标位置。
3.4由步进电机调节铸嘴的水平及垂直度。
3.5调节过程中,操作人员在出口侧随时观察铸嘴位置及嘴辊间隙。
嘴辊
间隙:上:1.6~2.0mm,下:1.2~1.6mm;新辊时偏小1mm左右。
3.6检测铸嘴两侧铸轧区是否一致,若不一致,进行单侧调整,使之符合
铸嘴两边
厚度差小
于0.1mm;
铸轧区长
度两边差
小于1mm。