注塑工艺验证报告1
注塑成型工序验证报告

注塑成型工序验证报告
注塑成型操作人员资格确认表
DXC001
原材料明细一览表
DXC002
原材料使用性验证确认表
DXC 003
原材料使用性验证确认表
DXC 004
原材料使用性验证确认表
DXC005
原材料使用性验证确认表
DXC006
原材料使用性验证确认表
DXC007
注塑设备一览表
DXC008
注塑机安装验证相关资料确认表
DXC013
注塑机安装验证相关资料确认表
DXC010
旋臂式机械手安装验证相关资料确认表
DXC011
注塑机相关文件资料验收明细表
DXC012
验证人:审核人:日期:13.02.16
注塑成型机安装确认表
DXC013
机械手安装试运行确认表
DXC014
注塑成型机试运行确认表
DXC015
注塑成型机技术参数验收情况确认表
DXC016
注塑成型机技术参数验收情况确认表
DXC017
注塑成型机技术参数验收情况确认表
DXC018
注塑成型机技术参数验收情况确认表
DXC019
注塑成型机技术参数验收情况确认表
DXC020
DXC021
DXC022
计量器具确认表
DXC023
注塑使用模具一览表
注塑模具安装试运行确认表
注塑零部件一览表 DXC027。
注塑试模报告

注塑试模报告报告人:日期:试模材料:注塑机:模具:注塑条件:(以上信息应列在报告首页上)一、试模目的:二、试模成品:三、试模过程:1.注塑工艺参数:2.注塑机调整:3.温度控制:四、试模结果:1.缺陷分析:2.改善措施:五、结论:六、建议:(以上内容应在正文中详细论述)注塑试模报告范例报告人:张三日期:20XX年X月X日试模材料:ABS注塑机:Haitian 120T模具:注塑汽车后视镜壳体模注塑条件:温度280℃、压力90MPa、注射速度50mm/s一、试模目的:测试模具结构和工艺参数,寻求最优注塑工艺参数并分析产品缺陷原因,提供解决方案。
二、试模成品:两个注塑汽车后视镜壳体,尺寸和表面色泽均符合标准要求。
三、试模过程:1.注塑工艺参数:温度280℃、压力90MPa、注射速度50mm/s、回程速度30mm/s、调试反应速度5。
2.注塑机调整:对定位针和流道进行调整,使之保持平衡。
3.温度控制:调整模具温度,温度达到设定值后加热时间延长至2小时。
四、试模结果:1.缺陷分析:在试模过程中出现行政区划 defect,原因可能是流道直径不足或温度不均匀所致。
2.改善措施:将流道直径加大或加设射出嘴,并适当调整温度控制区域,如果仍存在行政区划 defect,则需调整模具结构进一步改善注塑效果。
五、结论:通过调整工艺参数和模具结构,可以获得符合产品质量标准的注塑汽车后视镜壳体。
六、建议:对模具的设计进行优化,进一步提高模具的使用性能及耐用性。
塑料成型实验报告

一、实验目的1. 理解塑料成型工艺的基本原理和过程。
2. 掌握塑料成型过程中主要工艺参数对成型质量的影响。
3. 通过实验,验证理论知识的正确性,并提高动手操作能力。
4. 学习使用塑料成型设备,了解不同成型方法的适用范围。
二、实验原理塑料成型是将塑料原料加热熔化,然后在压力和(或)模具的作用下,使其成型为所需形状和尺寸的制品。
根据成型方法的不同,塑料成型可分为挤出成型、注塑成型、吹塑成型、压塑成型等。
三、实验器材1. 塑料原料:聚乙烯(PE)、聚丙烯(PP)等。
2. 塑料成型设备:挤出机、注塑机、吹塑机、压塑机等。
3. 模具:挤出模具、注塑模具、吹塑模具、压塑模具等。
4. 辅助设备:加热器、冷却水系统、物料输送设备等。
四、实验方法与步骤1. 挤出成型实验(1)将塑料原料放入挤出机料斗,调整温度和压力,使塑料熔化。
(2)打开挤出机,使熔融塑料通过挤出模具,形成所需形状的制品。
(3)调整模具和设备参数,观察制品的质量,记录实验数据。
2. 注塑成型实验(1)将塑料原料放入注塑机料斗,调整温度和压力。
(2)将模具闭合,注入熔融塑料,使其充满模腔。
(3)保压一定时间,使塑料冷却固化。
(4)打开模具,取出制品,观察质量,记录实验数据。
(1)将塑料原料放入吹塑机料斗,调整温度和压力。
(2)将熔融塑料通过挤出机挤出,形成型坯。
(3)将型坯放入吹塑模具,通入压缩空气,使其吹胀成型。
(4)冷却、脱模,取出制品,观察质量,记录实验数据。
4. 压塑成型实验(1)将塑料原料放入压塑机料斗,调整温度和压力。
(2)将模具闭合,使塑料熔化。
(3)施加压力,使塑料充满模腔。
(4)保压一定时间,使塑料冷却固化。
(5)打开模具,取出制品,观察质量,记录实验数据。
五、实验结果与分析1. 挤出成型实验实验结果表明,挤出成型过程中,温度和压力对制品质量有显著影响。
温度过高或过低会导致熔体流动性差,制品表面出现气泡、熔接痕等缺陷;压力过大或过小会影响制品尺寸精度和外观。
注塑试模产品报告模板

注塑试模产品报告模板一、试模背景及目的本次试模的背景是为了测试某个注塑产品的生产工艺及模具可行性,并验证产品的质量符合要求。
试模的目的是通过实际注塑生产出的产品,评估其尺寸精度、表面质量以及材料流动性等性能。
二、试模过程及参数设置1. 模具选择:XXX型号模具;2. 原料选择:XXX材料;3. 注塑设备:XXX注塑机;4. 注塑参数设置:- 射出压力:XXX MPa;- 射速:XXX mm/s;- 射胶量:XXX g;- 螺杆转速:XXX rpm;- 模具温控温度:XXX ;- 冷却时间:XXX s。
三、试模结果分析1. 尺寸精度测量了注塑产品的尺寸,并与设计要求进行对比分析。
结果显示,产品的尺寸精度符合要求,各个关键尺寸的偏差在允许范围内。
2. 表面质量观察了注塑产品的表面质量,除了小部分产品存在一些细微的表面瑕疵外,整体表面质量良好,没有明显的气泡、划痕或色差。
3. 材料流动性通过观察产品的浇口、水口及排气情况,评估了材料在注塑过程中的流动性。
结果显示,材料流动性良好,浇口和水口处没有明显挤出现象,且排气通畅。
四、问题分析及解决方案根据试模结果,发现了一些问题,如单个产品出现略微尺寸偏差等。
经过分析,可能是以下原因导致:1. 模具加工精度不够,导致产品尺寸偏差;2. 注塑参数设置不合理,影响了产品的质量。
为了解决以上问题,采取了以下措施:1. 优化模具的制造工艺,提高精度,确保产品尺寸稳定;2. 调整注塑参数,如调整射胶量及温控温度等,以改善产品的质量。
五、本次试模总结本次试模结果显示,注塑产品在尺寸精度、表面质量和材料流动性等方面均符合要求。
通过问题分析和解决方案,确定了进一步优化模具和注塑参数的方向,以提高产品质量和生产效率。
未来将根据试模结果的反馈,继续进行改进和优化,以提高生产工艺的稳定性和产品的竞争力。
以上是本次注塑试模产品的报告模板,希望对您的工作有所帮助。
如有需要,请根据具体情况进行修改和补充。
大型汽车工程部件注塑成型实验报告

大型汽车工程部件注塑成型实验报告一、实验目的1、掌握注塑成型工艺中各参数如塑件材料、成型压力、温度、注射速度、浇注系统等因素对其成型质量的影响大小。
2、介绍塑件各种成型瑕疵的构成机理,以及各工艺参数对各种瑕疵构成的影响大小。
3、初步介绍压铸成型分析软件moldflow的各项功能及基本操作。
4、初步介绍ug软件三维建模功能。
5、初步介绍ug软件三维模具设计功能。
二、实验原理1、moldflow压铸成型分析软件的功能十分齐全,具备完备的分析模块,可以分析出来压铸成型工艺中各个参数例如塑件材料、成型压力、温度、口服速度、浇筑系统等因素对成型质量的影响,还可以模拟出成型瑕疵的构成,以及如何改良等等,还可以预测每次成型后的结果。
2、注射成型充填过程属于非牛顿体、非等温、非稳态的流动与传热过程,满足黏性流体力学和基本方程,但方程过于复杂所以引入了层流假设和未压缩流体假设等。
最后通过公式的分析和计算,就可以得出结果。
三、实验器材硬件:计算机、游标卡尺、注塑机、打印机软件:ug软件、moldflow软件四、实验方法与步聚1、ug软件模型创建和模具设计(已省却);2、启动moldflow软件;3、新建一个分析项目;4、输出分析模型文件;5、网格分割和网格修正;6、流道设计;7、冷却水道布置; 8、成型工艺参数设置; 9、运转分析解器; 10、制作分析报告11、用试验模具在注塑机上进行工艺试验(已省去);12、分析演示分析报告(省却与实验结果相比较这一步骤); 13、得出结论五、前置处理相关数据 1.网格处理情况1)展开网格确诊,可以看见网格重合和最小四海比等问题; 2)网格确诊,并依次修正存有的网格问题; 3)修正回去后,再次检查网格情况。
2.材料选择及材料相关参数在在方案任务视窗里双击第四项材料,插入例如图材料挑选窗可直接选常用材料,也可根据制造商、商业名称或全称搜索3. 工艺参数设置双击方案任务视窗里的“成型条件设置”,这里直接用默认值。
注塑产品检验报告
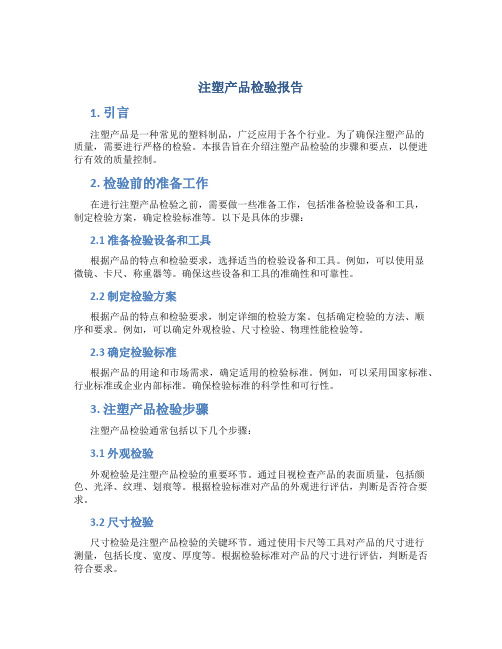
注塑产品检验报告1. 引言注塑产品是一种常见的塑料制品,广泛应用于各个行业。
为了确保注塑产品的质量,需要进行严格的检验。
本报告旨在介绍注塑产品检验的步骤和要点,以便进行有效的质量控制。
2. 检验前的准备工作在进行注塑产品检验之前,需要做一些准备工作,包括准备检验设备和工具,制定检验方案,确定检验标准等。
以下是具体的步骤:2.1 准备检验设备和工具根据产品的特点和检验要求,选择适当的检验设备和工具。
例如,可以使用显微镜、卡尺、称重器等。
确保这些设备和工具的准确性和可靠性。
2.2 制定检验方案根据产品的特点和检验要求,制定详细的检验方案。
包括确定检验的方法、顺序和要求。
例如,可以确定外观检验、尺寸检验、物理性能检验等。
2.3 确定检验标准根据产品的用途和市场需求,确定适用的检验标准。
例如,可以采用国家标准、行业标准或企业内部标准。
确保检验标准的科学性和可行性。
3. 注塑产品检验步骤注塑产品检验通常包括以下几个步骤:3.1 外观检验外观检验是注塑产品检验的重要环节。
通过目视检查产品的表面质量,包括颜色、光泽、纹理、划痕等。
根据检验标准对产品的外观进行评估,判断是否符合要求。
3.2 尺寸检验尺寸检验是注塑产品检验的关键环节。
通过使用卡尺等工具对产品的尺寸进行测量,包括长度、宽度、厚度等。
根据检验标准对产品的尺寸进行评估,判断是否符合要求。
3.3 物理性能检验物理性能检验是注塑产品检验的重要指标之一。
通过使用相应的设备对产品的物理性能进行测试,包括强度、韧性、硬度等。
根据检验标准对产品的物理性能进行评估,判断是否符合要求。
3.4 包装检验包装检验是注塑产品检验的最后一道环节。
通过检查产品的包装是否完整、合理,包括包装箱、标签、防护措施等。
根据检验标准对产品的包装进行评估,判断是否符合要求。
4. 检验结果和分析根据注塑产品的检验结果,可以进行相应的分析和判断。
如果产品符合检验标准,则可以判定为合格品;如果产品不符合检验标准,则需要进一步分析原因,并采取相应的措施进行改进。
工艺验证报告模板
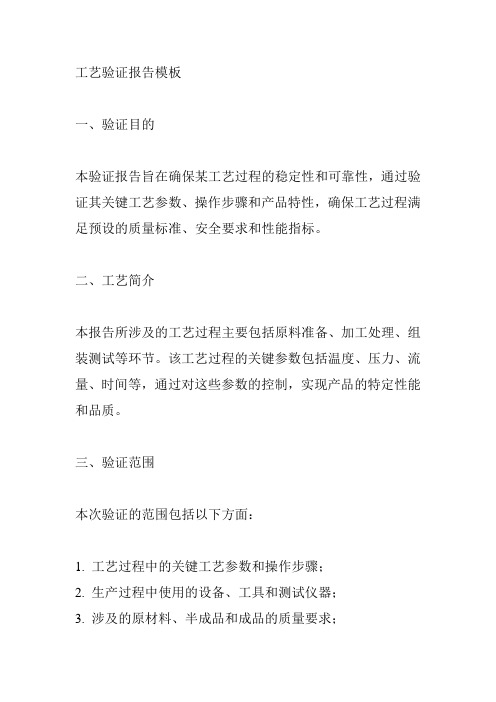
工艺验证报告模板一、验证目的本验证报告旨在确保某工艺过程的稳定性和可靠性,通过验证其关键工艺参数、操作步骤和产品特性,确保工艺过程满足预设的质量标准、安全要求和性能指标。
二、工艺简介本报告所涉及的工艺过程主要包括原料准备、加工处理、组装测试等环节。
该工艺过程的关键参数包括温度、压力、流量、时间等,通过对这些参数的控制,实现产品的特定性能和品质。
三、验证范围本次验证的范围包括以下方面:1. 工艺过程中的关键工艺参数和操作步骤;2. 生产过程中使用的设备、工具和测试仪器;3. 涉及的原材料、半成品和成品的质量要求;4. 生产环境的温湿度、清洁度等要求。
四、验证方法本次验证采用以下方法:1. 对工艺过程中的关键参数进行监测和记录;2. 对产品进行抽样检测,以评估其性能和品质;3. 对设备、工具和测试仪器进行校准和维护;4. 对生产环境进行监控和记录。
五、验证数据记录在验证过程中,我们对各个工艺环节的关键参数进行了详细的监测和记录,包括温度、压力、流量、时间等。
同时,我们也对产品的性能和品质进行了抽样检测,并记录了相应的数据。
这些数据包括但不限于:生产过程中设备的运行数据、工艺参数的监测数据、产品的检测数据等。
六、数据分析与结论根据验证过程中收集的数据,我们对工艺过程的稳定性和可靠性进行了分析。
具体分析方法可以包括数据统计分析、趋势分析等。
通过对数据的分析,我们可以得出以下结论:1. 工艺过程中的关键参数是否稳定可控;2. 产品性能和品质是否符合预设要求;3. 设备运行是否正常,工具和测试仪器是否准确可靠;4. 生产环境是否满足工艺要求。
七、改进建议根据以上结论,我们提出以下改进建议:1. 对工艺参数进行优化调整,提高产品性能和品质;2. 对设备进行定期维护和校准,确保其正常运行;。
注塑试产报告范文
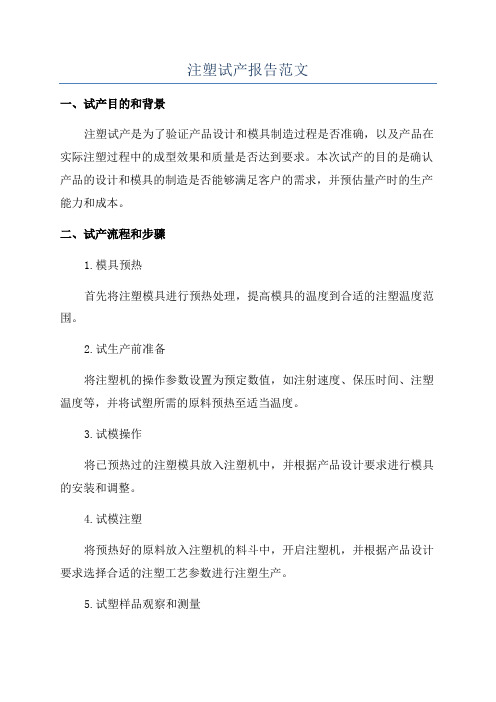
注塑试产报告范文一、试产目的和背景注塑试产是为了验证产品设计和模具制造过程是否准确,以及产品在实际注塑过程中的成型效果和质量是否达到要求。
本次试产的目的是确认产品的设计和模具的制造是否能够满足客户的需求,并预估量产时的生产能力和成本。
二、试产流程和步骤1.模具预热首先将注塑模具进行预热处理,提高模具的温度到合适的注塑温度范围。
2.试生产前准备将注塑机的操作参数设置为预定数值,如注射速度、保压时间、注塑温度等,并将试塑所需的原料预热至适当温度。
3.试模操作将已预热过的注塑模具放入注塑机中,并根据产品设计要求进行模具的安装和调整。
4.试模注塑将预热好的原料放入注塑机的料斗中,开启注塑机,并根据产品设计要求选择合适的注塑工艺参数进行注塑生产。
5.试塑样品观察和测量在注塑生产过程中,及时观察和记录塑件的成型情况,检查是否存在缺陷如气泡、短射、烧焦等,并对试塑样品进行尺寸测量和功能测试。
6.样品评估和分析根据试塑样品的表面质量、尺寸精度和功能性能等方面的评估和分析,判断产品是否符合设计要求,并根据评估结果对模具和注塑工艺进行调整和优化。
7.报告撰写和总结根据试塑过程中的观察和测试结果,撰写试产报告,总结试产过程中遇到的问题和解决方案,并提出改进措施。
三、试产结果和分析本次试产的样品成型情况较理想,产品尺寸精度控制在设计要求范围之内,外观质量良好,无气泡、短射和烧焦等缺陷。
功能测试结果也符合设计要求,产品能够正常工作。
通过对样品的评估和分析,以及问题的解决和优化,确认产品的设计和模具制造是准确和可行的。
四、量产准备和建议基于试产结果,为了确保量产的生产能力和质量稳定,有以下建议:1.进一步优化注塑工艺,提高生产效率和产品质量。
2.进行模具维护和保养,确保模具的使用寿命和稳定性。
3.进行生产工艺记录和培训,确保操作人员能够正确操作注塑机和模具。
4.建立质量控制体系,对每个生产批次进行质量跟踪和检验。
5.与客户沟通,根据客户的要求进行量产前的样品确认,确保量产产品符合客户的需求。
- 1、下载文档前请自行甄别文档内容的完整性,平台不提供额外的编辑、内容补充、找答案等附加服务。
- 2、"仅部分预览"的文档,不可在线预览部分如存在完整性等问题,可反馈申请退款(可完整预览的文档不适用该条件!)。
- 3、如文档侵犯您的权益,请联系客服反馈,我们会尽快为您处理(人工客服工作时间:9:00-18:30)。
200℃
2.04
OK
180℃
1.94
OK
中区(Max):
180℃
2.04
OK
160℃
1.94
OK
后区(Max):
160℃
2.04
OK
150℃
1.94
OK
模温:
60℃
OK
注射压力:
一压力:
50±10kg
OK
二压力:
25±10kg
OK
注塑时间:
4±2秒
OK
保压+冷却:
4±2秒
OK
七、结论:本次验证结果表明以下的工艺满足注塑过程的要求。
验证报告审核会签表:
报告起草人/日期
报告编制会签名
签字
日期
品管部主任
生技课组长
注塑车间课长
九、工艺验证流程图
否
是
附件1:注塑工艺参数验证排列表
规格
型号
零件
名称
试验
次数
工艺
参数
1
2
3
温度(℃)
注射压力(kg)
成型周期
温度(℃)
注射压力(kg)
成型周期
温度(℃)
注射压力(kg)
成型周期
前区
中区
后区
一压力
170
155
50
25
4S
4S
180
160
150
40
15
2S
2S
G000000911
USB plug
200
180
160
60
35
6S
6S
190
170
155
50
25
4S
4S
180
160
150
40
15
2S
2S
2S
G000000911
USB plug
200
180
160
60
35
6S
6S
190
170
155
50
25
4S
4S
180
160
150
40
15
2S
2S
G000000911
USB plug
200
180
160
60
35
6S
6S
190
170
155
50
25
4S
4S
180
160
150
40
15
2S
2S
G000000911
一、验证目的:
1.医疗器械数据传输线生产中,注塑是生产过程中影响产品质量的主要环节之一。注塑质量影响到产品整体的性能和外观,配合等方面因此,对注塑工艺进行有效的控制并验证,以保证实现在正常的生产条件下,生产出符合标准的医疗器械产品。
2.本报告的目的在于为评价注塑工艺参数的状况对注塑产品的外观及尺寸的影响,以确认最佳的注塑工艺参数。
二、报告验证小组成员:
技术部:韦克
品管部:梁淑梅
模具部:韦敏
注塑车间:吴健先
本报告的由技术部编制,由品管部、技术部协同努力设计完成,由工程师审核批准。
三、验证依据:产品工程图纸(GED-E-M-11249)和相关作业参数(SOP)。
四、验证项目:注塑设备性能,注塑压力、温度、成型周期对产品质量的影响。
2、经计算:
关键工艺为:
a)温度
推杆类:前区:180℃――200℃
中区:160℃――180℃
后区:150℃――160℃
模温:60℃
b)注射压力:
一压力:50±10kg
二压力:25±10kg
注塑时间:4±2 Sec
保压+冷却:4±2 Sec
3、对取得的结果进行数据分析:
工艺参数设定
Cpk
判定
温度
推杆类:
160
60
35
6S
6S
190
170
155
50
25
4S
4S
180
160
150
40
15
2S
2S
G000000911
USB plug
200
180
160
60
35
6S
6S
190
170
155
50
25
4S
4S
180
160
150
40
15
2S
2S
G000000911
USB plug
200
180
160
60
35
6S
6S
190
注塑时间:4±2 Sec
保压+冷却:4±2Sec
五、验证方法
OQ:
1、参数设置:设置好各类参数:温度、时间、压力,使机器预热升温至额定值。
2、出样:空注出模头样,手动闭模,注塑2-3模产品。
3、检验:检验产品外观及尺寸是否符合有关要求及图纸,如果全部合格,则投入正常生产,如果一项或某几项不合格,则需回到第一步,进行参数调整,重新进行验证。
设备编号:GTL-AM-066
验证条件设置:
1.注塑区环境条件:
a)温度:18-28℃
b)湿度:50-65%RH
2.注塑工艺参数:
a)温度
推杆类:前区:180℃――200℃
中区:160℃――180℃
后区:150℃――160℃
模温:55℃---65℃
b)注射压力:
一压力:50±10kg
二压力:25±10kg
工艺参数设定
温度
推杆类:
前区(Max):
200℃
180℃
中区(Max):
180℃
160℃
后区(Max):
160℃
150℃
模温:
60℃
注射压力:
一压力:
50±10kg
二压力:
25±10kg
注塑时间:
4±2秒
保压+冷却:
4±2秒
八、最终批准:验证小组审阅上述所有结果及评价分析意见,同意验证结果,并按此结论编制注塑工艺过程卡。
二
压力
注射
时间
降压
+
冷却
前区
中区
后区
一压力
二
压力
注
射
时
间
降压
+
冷却
前区
中区
后区
一压力
二
压力
注
射
时
间
降压+冷却
G000000911
USB plug
200
180
160
60
35
6S
6S
190
170
155
50
25
4S
4S
180
160
150
40
15
2S
2S
G000000911
USB plug
200
180
160
PQ:
4、连续运行:在OQ取得的工艺基础上,连续运行3批,每批至少生产15模产品。
5、工艺记录:运行过程中,读取每模的工艺运行的参数,并做记录(见附件1)。
6、产品测试:品质部对取得的全部产品按有关图纸或检验规程检验产品外观及尺寸,并做好记录。
六、结果分析和评价:
1、运用统计技术分析工艺参数和产品性能之间的关系。确定关键工艺。并评价其稳定性。
160
150
40
15
2S
2S
G000000911
USB plug
200
180
160
60
35
6S
6S
190
170
155
50
25
4S
4S
180
160
150
40
15
2S
2S
G000000911
USB plug
200
180
160
60
35
6S
6S
190
170
155
50
25
4S
4S
180
160
150
40
15
2S
注:
1、本报告仅为样本,请依据公司的实际情况予以修订;
2、修订时,请特别注意红色斜体部分;
3、正式报告发布时请将文中的红色斜体部分删除;
4、过程确认是一项复杂、耗时的研究工作,目的在于保证生产设备、生产工艺、检验技术能确保提供稳定的、安全性高的产品,特别适用于一些高风险的工艺,产品性能检测成本高的过程,如灭菌过程、无菌医疗器械的封口过程等;
USB plug
200
180
160
60
35
6S
6S
190
170
155
50
25
4S
4S
180
160
150
40
15
2S
2S
G000000911
USB plug
200
180
160
60
35
6S
6S
190
170
155
50
25
4S
4S
180
160
150
40
15
2S
2S
G000000911
USB plug
200
180
5、过程确认本身是一种过程,通常应依据PDCA执行。
6、过程确认需要判断该过程是否稳定,通常需要使用一些统计技术,如Cpk计算、控制ቤተ መጻሕፍቲ ባይዱ、直方图、回归分析、正交表等,请依据公司的实际情况选择。