涨断连杆工艺
连杆激光涨断工艺

连杆激光涨断工艺连杆是汽车发动机中的重要零件,它连接着活塞和曲轴,其作用是将活塞的往复运动转变为曲轴的旋转运动,并把作用在活塞上的力传给曲轴以输出功率。
连杆在工作中,除承受燃烧室燃气产生的压力外,还要承受纵向和横向的惯性力。
因此,连杆在一个复杂的应力状态下工作。
它既受交变的拉压应力、又受弯曲应力。
连杆的主要损坏形式是疲劳断裂和过量变形。
通常疲劳断裂的部位是在连杆上的三个高应力区域。
连杆的工作条件要求连杆具有较高的强度和抗疲劳性能;又要求具有足够的钢性和韧性。
发动机的可靠性在很大程度上取决于连杆的可靠程度,在连杆的总成可靠性的因素之中分合面质量与定位关系是主要因素,因此解决好连杆体与连杆盖之间的定位问题,可以降低连杆的生产成本,提高发动机的可靠性。
但由于连杆的外形比较复杂、容易变形、刚性差,尺寸精度、位置精度以及表面质量等要求较高,在制造上具有一定难度。
而其连杆制造技术的好坏直接影响着连杆的使用性能和经济性能以及一个企业的生存和发展,随着生产技术的发展,传统的制造技术渐渐不能适应现在生产的要求。
先后在国外很多连杆生产厂家提出了“涨断技术”,连杆涨断工艺的应用,使连杆在加工质量、生产率和生产成本等诸多方面都发生了显著变化,柴油发动机的性能得到了进一步提升。
该技术是以整体加工代替分体加工,用切口(用机械方法或激光技术等方法制造预裂纹) 断裂,使大端连杆盖从连杆体移去,使连杆体与盖的分离达到理想的脆性断裂,并能很容易达到其连杆使用性能要求的一门先进技术.大致过程如下:1、激光加工涨断槽连杆分离面涨断工艺要考虑涨断槽的加工工艺。
利用机械加工“V”型槽,在加工过程中其刀具容易磨损,刀尖会变钝,变短,加工出来的槽的曲率半径就会增大,槽的深度就会减小,因为其“V”型槽的曲率半径越小,它的应力集中效果就越好,所需的胀断力就越小,同时增加槽的深度H也有利于减小胀断力,但由于后续工序加工余量的限制,槽的深度不能超过一定范围。
第三章_EA888发动机连杆胀断工艺存在的问题和改进措施

第三章_EA888发动机连杆胀断⼯艺存在的问题和改进措施第三章_EA888发动机连杆胀断⼯艺存在的问题和改进措施第三章 EA888发动机连杆胀断⼯艺存在的问题3.1 锻造前存在的问题3.1.1 锻造加热温度的确定锻造温度范围是指合理的始锻温度与合理的终锻温度之间的⼀段温度区间,确定锻造温度范围是热锻⼯艺设计的主要内容。
合理确定锻造温度范围的意义在于:1)保证锻件获得良好的内部组织和机械性能,也就是使钢在变形时具有良好的塑性,不产⽣加⼯硬化及残余应⼒;锻后获得细⼩、均匀的晶粒组织。
2)减少变形⼒。
3)缩短⽣产周期,提⾼⽣产效率。
4)节省能源,降低劳动强度。
EA888采⽤了世界上最新的易切削⾮调质钢36MnVS4含硫、含钒量较⾼材料,这种材料是⽬前最先进的⽤于胀断连杆的材料,在国内,⽩城中⼀尚属⾸例。
为此,我们在⽩城中⼀精锻股份有限公司做了⼤量的⼯艺实验,由于加热温度的确定和锻后冷却控制是相关联的,⼆者结合在⼀起即决定了连杆的内部质量。
3.1.2 锻造加热温度不稳定锻造加热温度的范围⼀般在30?左右,温度过⾼或过低都会直接影响连杆的内在组织和机械性能,导致锻件不合格。
所以加热温度的控制在锻造过程中尤为重要。
产⽣加热温度不稳定的原因有:1(部分国产加热炉未安装⾃动上料装置,采⽤⼈⼯摆料的⽅式,这种摆料⽅式有时会出现间断、不连续现象,导致坯料加热温度不稳定,忽⾼忽低。
2(新旧料混在⼀起加热。
坯料加热过程中,部分未达到温度要求的坯料需要进⾏重新加热再使⽤,如果加热过的坯料与未加热过的坯料混在⼀起加热,也会导致加热温度不稳定。
3.1.3 辊坯质量不合格存在辊坯⼤头抓伤、辊坯拉伤,辊坯有飞刺、折叠等缺陷。
辊坯⼤头抓伤的形成原因:在辊锻过程中,送料钳⽖长期接触⾼温坯料,会粘结坯料外层的氧化⽪,氧化⽪粘结在钳⽖上形成很硬的积瘤,再接触坯料时,积瘤就会划伤坯料表⾯,形成抓痕,经过模锻,这种抓痕就会在锻件上形成折叠缺陷。
第二章_发动机连杆胀断工艺内容
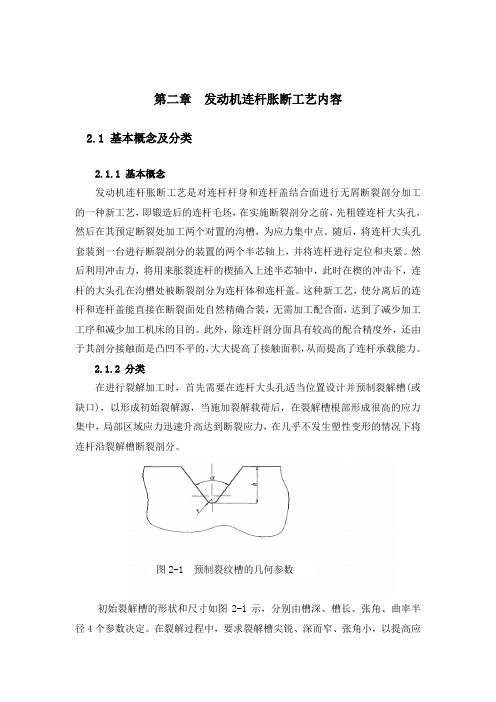
第二章发动机连杆胀断工艺内容2.1 基本概念及分类2.1.1 基本概念发动机连杆胀断工艺是对连杆杆身和连杆盖结合面进行无屑断裂剖分加工的一种新工艺,即锻造后的连杆毛坯,在实施断裂剖分之前,先粗镗连杆大头孔,然后在其预定断裂处加工两个对置的沟槽,为应力集中点。
随后,将连杆大头孔套装到一台进行断裂剖分的装置的两个半芯轴上,并将连杆进行定位和夹紧。
然后利用冲击力,将用来胀裂连杆的楔插入上述半芯轴中,此时在楔的冲击下,连杆的大头孔在沟槽处被断裂剖分为连杆体和连杆盖。
这种新工艺,使分离后的连杆和连杆盖能直接在断裂面处自然精确合装,无需加工配合面,达到了减少加工工序和减少加工机床的目的。
此外,除连杆剖分面具有较高的配合精度外,还由于其剖分接触面是凸凹不平的,大大提高了接触面积,从而提高了连杆承载能力。
2.1.2 分类在进行裂解加工时,首先需要在连杆大头孔适当位置设计并预制裂解槽(或缺口),以形成初始裂解源,当施加裂解载荷后,在裂解槽根部形成很高的应力集中,局部区域应力迅速升高达到断裂应力,在几乎不发生塑性变形的情况下将连杆沿裂解槽断裂剖分。
图2-1 预制裂纹槽的几何参数初始裂解槽的形状和尺寸如图2-1示,分别由槽深、槽长、张角、曲率半径4个参数决定。
在裂解过程中,要求裂解槽尖锐、深而窄、张角小,以提高应力集中系数,有效降低裂解加工载荷,从而减少裂解过程中因塑性变形而导致的连杆大头孔失圆,避免裂解缺陷,保证裂解加工质量。
因此,对初始裂解槽的合理设计,能有效提高缺口效应与应力集中系数,继而降低裂解力,提高裂解效率与质量。
发动机连杆胀断工艺按照裂解槽的加工方式可分为三种:机械加工初始裂解槽、线切割加工初始裂解槽和激光加工初始裂解槽三种。
2.1.2.1 机械加工初始裂解槽机械加工裂解槽是以推/拉削加工为主,如图2-2所示。
在切削过程中,通过刀柄上安装的刀具对裂解槽进行分层切削,从拉刀端头开始刀柄上每层刀具依次递增量为0.1 mm ,刀片数量根据裂解槽的深度来决定,并且裂解槽的张角、曲率半径均由推/拉刀具刃口来决定。
胀断连杆 技术要求
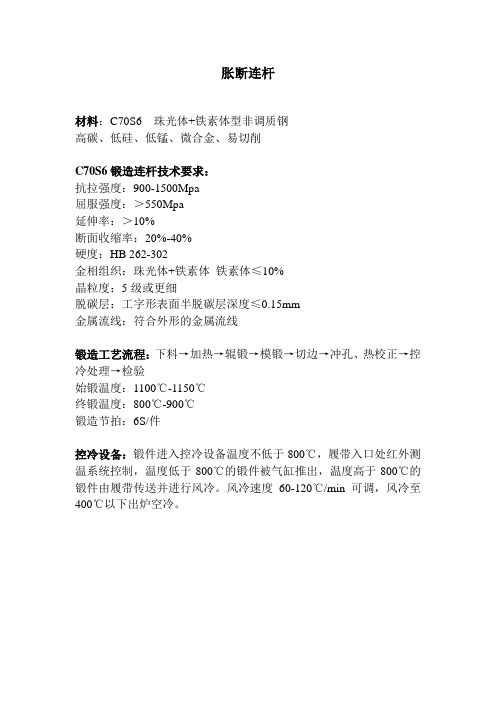
胀断连杆
材料:C70S6 珠光体+铁素体型非调质钢
高碳、低硅、低锰、微合金、易切削
C70S6锻造连杆技术要求:
抗拉强度:900-1500Mpa
屈服强度:>550Mpa
延伸率:>10%
断面收缩率:20%-40%
硬度:HB 262-302
金相组织:珠光体+铁素体铁素体≤10%
晶粒度:5级或更细
脱碳层:工字形表面半脱碳层深度≤0.15mm
金属流线:符合外形的金属流线
锻造工艺流程:下料→加热→辊锻→模锻→切边→冲孔、热校正→控冷处理→检验
始锻温度:1100℃-1150℃
终锻温度:800℃-900℃
锻造节拍:6S/件
控冷设备:锻件进入控冷设备温度不低于800℃,履带入口处红外测温系统控制,温度低于800℃的锻件被气缸推出,温度高于800℃的锻件由履带传送并进行风冷。
风冷速度60-120℃/min可调,风冷至400℃以下出炉空冷。
涨断连杆工艺

连杆分离面的涨断工艺(CRACKING TECHNOLOGY)是把连杆盖从连杆本体上断裂而分离开来。
它不是用铣、锯或拉这类传统切削加工方法,而是对连杆大头孔的断裂线处先加工出两条应力集中槽子(或在毛坯时就做出沟槽),然後带楔形的压头往下移动进入连杆大头孔,连杆大头孔与压头之间还有一对半圆套筒。
当压头往下移动时对连杆大头孔产生径向力,这样就使其在槽子处出现裂缝,在径向力的继续作用下,裂缝也继续扩大,最终把连杆盖从连杆本体上涨断而分离出来。
连杆涨断工艺的实用性取决於其分离面的可装配性。
最理想的连杆及连杆盖涨断後的分离面,是不带任何塑性变形的脆性断裂,使其可装配性达致最佳。
影响其脆性断裂的因素很多,如断裂速度及材料等。
至於连杆采用涨断工艺时对其材料的要求,据德国KREBSOEGE公司的研究结果,烧结粉末金属连杆的可涨断性较好,也是连杆涨断工艺首先在粉末金属连杆上推行的原因。
铸铁连杆最适宜的材料是GTS65-70,锻钢连杆的材料是70号钢。
但是,70号钢锻造连杆在涨裂时,不带塑性变形的脆性断裂以及70号钢的切削加工,将是该工艺的难点。
连杆分离面涨断工艺的几个工艺问题* 断裂槽的加工工艺连杆断裂槽加工有两种工艺:拉削加工和激光加工)。
采用拉削方法加工连杆大头孔的两条槽子,由於拉刀随着加工时间长而磨损,被拉削的槽子形状也随之而变化。
槽子形状的变化又影响连杆大头孔在涨断後的变形。
由於被拉削的两个断裂槽形状不一样,在连杆分离面断裂时会出现一个分离面已断开,而另一个分离面尚未完全断开的现象。
采用激光加工连杆大头孔的两条槽子,可保持形状一致,也就保证了连杆大头孔在涨断後的变形也是一致。
同时,激光加工的柔性好,加工运行的费用也小。
所以,现在很多汽车公司如上海大众汽车公司等,都倾向采用激光加工连杆断裂槽。
* 断裂槽的槽深德国ALFING机床公司的研究表明,连杆大头孔在涨断後的圆度和楔力,与大头孔预加工的槽子深度有关。
由图可知断裂槽的深度大,则连杆大头孔在涨断後的变形小及涨断时的楔力小。
涨断连杆加工工艺研究
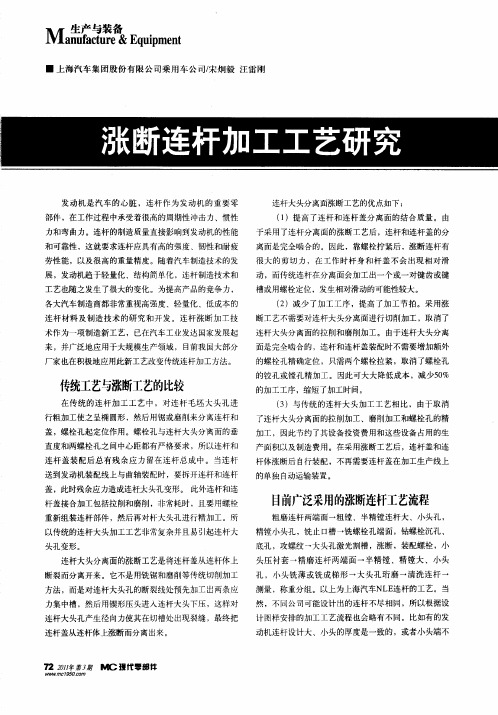
头压衬套一精磨连杆两端面一半精镗、精镗大、小头
孔 ,小 头铣 薄或铣 成梯 形 一大头 孔珩 磨 一清 洗连 杆 一
测量 ,称重分组 。以上为上海汽车NL 连杆的工艺 。当 E 然 ,不 同公司可能设计 出的连杆不尽相 同 ,所以根据设 计 图样安排 的加 工工艺流程也会略有 不同。比如有的发
和可靠性 ,这就要求连杆应具 有高的强度 、韧性和耐 疲
劳性能 ,以及很高 的重量精 度。随着汽车制造技术 的发 展 ,发动机趋于轻量化 、结 构简单化 ,连杆制造技 术和
工艺也随之发生 了很大 的变化。为提高产 品的竞争 力 , 各大汽车制造商都非常 重视 高强度 、轻量化 、低成 本的 连杆 材料 及制 造技术 的研 究 和开 发 。连杆涨 断加 工技 术作为一项制造新工艺 ,已在 汽车工业发达 国家发展起
的单独 自动运输装置。
目前广泛采用的涨断连杆工艺流程
粗磨连 杆两端面一粗镗 、半精镗连 杆大 、小头孔 , 精镗小头孔 ,铣 止 口槽一铣螺栓孔端面 ,钻螺栓沉孔 、 底孔 ,攻螺 纹一大头孔激光割槽 ,涨断 ,装配螺栓 ,小
连杆大头分离面 的涨断 工艺是将连杆盖从连杆体上
断裂而分离开来 。它不是 用铣 锯和磨削等传统切 削加 工 方法 ,而是对连杆大头孔 的断裂线处预先加工 出两 条应 力集中槽 ,然后用锲形压头进 入连杆大头下压 ,这样对 连杆大头孔产生径 向力使其 在切 槽处 出现裂缝 ,最终把
( )提高 了连杆和 连杆盖 分离面 的结合 质量 。由 1 于采用 了连 杆分离面的涨断工艺后 , 杆和连杆盖的分 连
离面是 完全 啮合的。 因此 ,靠螺栓拧 紧后 ,涨断连杆有 很 大的 剪切 力 ,在 工 作时 杆身 和杆 盖不 会 出现相 对滑 动 ,而传统 连杆在分离面会加 工出一个 或一对键齿或键 槽或用螺栓定位 ,发生相对滑动 的可 能性较大 。 ( )减少 了加工工序 ,提 高了加 工节拍 。采用涨 2 断工艺不需要对 连杆大头分离面进行切 削加 工 ,取消 了
高速柴油机连杆胀断工艺设计说明书

目录摘要ⅢAbstractⅣ第一章绪论11.1 前言11.2 国内外发动机连杆工艺进展现状和进展趋势3 1.3 连杆工艺研究方向和研究的关键问题3第二章连杆零件的分析52.1 连杆的结构功能分析52.2 连杆的要紧技术要求6第三章连杆零件机械加工工艺规程的编制73.1 生产纲领的确定73.2 连杆的工艺分析83.3 连杆的材料选择与毛坯的制造方法83.3.1连杆的材料选择83.3.2 C70S6钢的成分和力学性能103.3.3 毛坯的制造方法113.4 机械加工余量,工序尺寸及毛坯尺寸确定133.5 指定工序定位基准的选择133.6 加工工艺时期的划分和加工顺序的安排153.7 连杆加工工艺过程的拟定163.8填写机械加工工艺过程卡和机械加工工序卡16 第四章指定工序的工装设计174.1 机床夹具设计的差不多要求174.2 专用夹具设计步骤174.3激光开应力槽工装设计194.3.1 应力槽的设计194.3.2 设备的选择与改装204.3.3 拟定定位方案204.4胀断工装设计214.4.1 设备选择214.4.2拟定定位方案214.4.3夹具使用讲明214.4.4 胀断参数的计算 23总结24参考文献25致谢26105系列高速柴油机连杆工艺总体方案及指定工装设计摘要连杆是柴油发动机的要紧部件之一,它决定着发动机的性能和运行的稳定性。
随着科学技术的进展与进步,连杆的制造被注入了现代化的加工手段。
“胀断工艺”成为了连杆工艺中的又一新名词。
连杆胀断工艺的应用,使连杆在加工质量、生产率和生产成本等诸多方面都发生了显著变化,柴油发动机的性能得到了进一步提升。
本文以柴油机连杆制造工艺的总体方案为要紧研究内容,以连杆的胀断工艺为要紧研究方向。
总体方案涉及从连杆材料的选择到加工为成品的全部工艺过程。
方案特不对胀断工艺的原理及过程做了深入浅出的论述,并在认真分析连杆技术要求、广泛查阅相关文献的基础之上,制定出了一条差不多适于连杆实际生产的新型工艺方案和路线。
涨断连杆
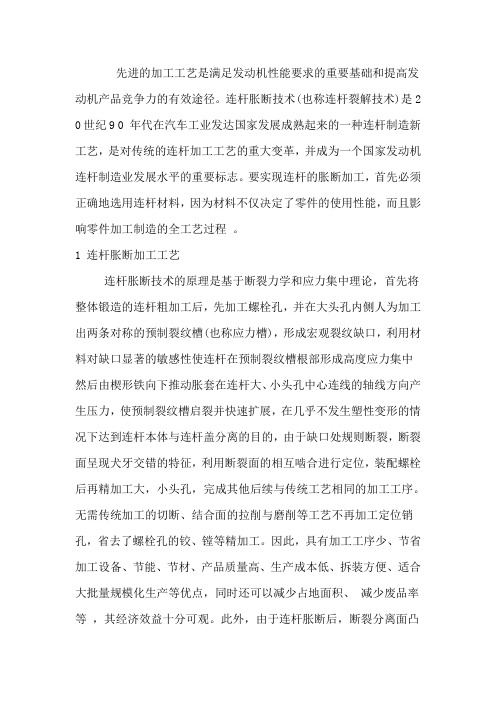
先进的加工工艺是满足发动机性能要求的重要基础和提高发动机产品竞争力的有效途径。
连杆胀断技术(也称连杆裂解技术)是2 0世纪9 0 年代在汽车工业发达国家发展成熟起来的一种连杆制造新工艺,是对传统的连杆加工工艺的重大变革,并成为一个国家发动机连杆制造业发展水平的重要标志。
要实现连杆的胀断加工,首先必须正确地选用连杆材料,因为材料不仅决定了零件的使用性能,而且影响零件加工制造的全工艺过程。
1 连杆胀断加工工艺连杆胀断技术的原理是基于断裂力学和应力集中理论,首先将整体锻造的连杆粗加工后,先加工螺栓孔,并在大头孔内侧人为加工出两条对称的预制裂纹槽(也称应力槽),形成宏观裂纹缺口,利用材料对缺口显著的敏感性使连杆在预制裂纹槽根部形成高度应力集中然后由楔形铁向下推动胀套在连杆大、小头孔中心连线的轴线方向产生压力,使预制裂纹槽启裂并快速扩展,在几乎不发生塑性变形的情况下达到连杆本体与连杆盖分离的目的,由于缺口处规则断裂,断裂面呈现犬牙交错的特征,利用断裂面的相互啮合进行定位,装配螺栓后再精加工大,小头孔,完成其他后续与传统工艺相同的加工工序。
无需传统加工的切断、结合面的拉削与磨削等工艺不再加工定位销孔,省去了螺栓孔的铰、镗等精加工。
因此,具有加工工序少、节省加工设备、节能、节材、产品质量高、生产成本低、拆装方便、适合大批量规模化生产等优点,同时还可以减少占地面积、减少废品率等,其经济效益十分可观。
此外,由于连杆胀断后,断裂分离面凸凹不平,增大了接合面的面积,同时可以保证大头孔具有较高的圆度,可增强连杆的承载能力和抗剪切能力,装配质量提高,对提高发动机整体生产技术水平具有重要作用。
2 胀断连杆材料连杆的材料及金相组织不仅决定连杆产品的性能和切削性,而且影响胀断加工质量。
胀断加工工艺要求大头孔不能产生明显的塑性变形,以保证精加工后大头孔的圆度要求。
因此,在保证连杆强韧综合性能指标的前提下,限制连杆的韧性指标,使断口呈现脆性断裂特性,以便具有良好的啮合性。
- 1、下载文档前请自行甄别文档内容的完整性,平台不提供额外的编辑、内容补充、找答案等附加服务。
- 2、"仅部分预览"的文档,不可在线预览部分如存在完整性等问题,可反馈申请退款(可完整预览的文档不适用该条件!)。
- 3、如文档侵犯您的权益,请联系客服反馈,我们会尽快为您处理(人工客服工作时间:9:00-18:30)。
论述涨断连杆与切开连杆的工艺比较
连杆分离面的涨断工艺是把连杆盖从连杆本体上断裂而分离开来。
它不是用铣、锯或拉这类传统切削加工方法,而是对连杆大头孔的断裂线处先加工出两条应力集中槽子(或在毛坯时就做出沟槽),然後带楔形的压头往下移动进入连杆大头孔,连杆大头孔与压头之间还有一对半圆套筒。
当压头往下移动时对连杆大头孔产生径向力,这样就使其在槽子处出现裂缝,在径向力的继续作用下,裂缝也继续扩大,最终把连杆盖从连杆本体上涨断而分离出来。
连杆涨断工艺的实用性取决於其分离面的可装配性。
最理想的连杆及连杆盖涨断後的分离面,是不带任何塑性变形的脆性断裂,使其可装配性达致最佳。
影响其脆性断裂的因素很多,如断裂速度及材料等。
铸铁连杆最适宜的材料是GTS65-70,锻钢连杆的材料是70号钢。
但是,70号钢锻造连杆在涨裂时,不带塑性变形的脆性断裂以及70号钢的切削加工,将是该工艺的难点。
连杆分离面涨断工艺的几个工艺问题
* 断裂槽的加工工艺
连杆断裂槽加工有两种工艺:拉削加工和激光加工)。
采用拉削方法加工连杆大头孔的两条槽子,由於拉刀随着加工时间长而磨损,被拉削的槽子形状也随之而变化。
槽子形状的变化又影响连杆大头孔在涨断後的变形。
由於被拉削的两个断裂槽形状不一样,在连杆分离面断裂时会出现一个分离面已断开,而另一个分离面尚未完
全断开的现象。
采用激光加工连杆大头孔的两条槽子,可保持形状一致,也就保证了连杆大头孔在涨断後的变形也是一致。
同时,激光加工的柔性好,加工运行的费用也小。
所以,现在很多汽车公司如上海大众汽车公司等,都倾向采用激光加工连杆断裂槽。
* 断裂槽的槽深
连杆大头孔在涨断後的圆度和楔力,与大头孔预加工的槽子深度有关。
由图可知断裂槽的深度大,则连杆大头孔在涨断後的变形小及涨断时的楔力小。
但是,断裂槽深度不能太深,否则在最後精镗大头孔时会镗不掉,建议为0.50mm左右。
* 采用涨断工艺後连杆的装配工艺
当连杆分离面断开之後,在分离面上有些金属粉粒未脱落,需要先吹净分离面才装配连杆与连杆盖,装配完毕再松开并第二次吹净其分离面,然後再装配连杆与连杆盖。
所以,采用涨断工艺後的连杆装配工艺比传统工艺要复杂。
* 连杆涨断工艺流程
连杆采用涨断工艺之後,其机械加工的工艺流程与传统工艺流程有了明显的变化。
连杆分离面涨断工艺的优点
* 简化了连杆及连杆盖的设计要求
连杆分离面采用涨断工艺後,连杆与连杆盖的分离面完全啮合,这就改善了连杆盖与连杆分离面的结合质量,所以它们的分离面不需进行
机械加工,省掉了分离面的拉削加工和磨削加工。
由於分离面完全啮合,连杆与连杆盖装配一起时,也不需增加额外的精确定位,如螺栓孔定位(或定位环孔),只要两枚螺栓拉紧即可。
这样可省掉螺栓孔的精加工(铰或镗)。
* 改善连杆总成的大头孔变形
采用传统的连杆加工工艺,在装配前需要把连杆与连杆盖的分离面磨削加工一次,以及螺栓孔作为定位用,所以螺栓孔与其分离面的垂直度和两螺栓孔的中心距尺寸都有严格的要求。
虽然以上的技术要求很高,但总有一定误差,所以连杆与连杆盖装配後有残余应力留在连杆总成。
连杆总成的两侧面和大小头孔精加工完毕後,要送到发动机装配线上与曲轴装配,这时要拆开连杆盖与连杆,释放残余应力,产生连杆大头孔变形的现象。
当连杆盖与连杆再次装到发动机的曲轴上,严重的变形就引致装不上去的质量问题。
连杆大头采用涨断工艺後,它们的分离面是最完全的啮合。
所以,没有分离面及螺栓孔加工误差等影响,而这些加工误差以0.01mm单位来计算。
采用涨断工艺时连杆大头孔亦有变形,但是比较小,其误差以0.001mm单位来计算。
* 经济效益
** 减少设备投资达25%以上;
** 缩短连杆生产线的长度,减少设备占地面积达30%以上;
** 节约能耗40%以上;
** 节约刀具费用35%以上;
** 明显地减少设备、刀具等的维护费用。
与传统工艺的区别
以整体锻件毛坯加工为例,我厂采用的连杆涨断新工艺与传统工艺相比有很多区别。
1、大头孔的粗力口工传统工艺要在切断后对大头孔进行粗拉,或者在切断前将它加工成椭圆形(或者毛坯为椭圆形),所以要在2个工位上.进行粗加工,而且因为是断续加工,振动大、刀具磨损快、刀具消耗大。
而涨断工艺将大头孔加工成圆形,所以可在1个工位上加工。
涨断工艺的生产设备只需要1个主轴,而传统工艺的生产设备则需要2个主轴。
2、连杆体、盖分离方法传统工艺采用拉断(或铣断、锯断)法,而涨断工艺是在螺栓孔加工之后涨断。
采用涨断工艺后,连杆与连杆盖的分离面完全啮合,这就改善了连杆盖与连杆分离面的结合质量,所以分离面不需要进行拉削加工和磨削加工。
由于分离面完全啮合,将连杆与连杆盖装配时,也不需要增加额外的精确定位,如螺栓孔定位(或定位环孔),只要两枚螺栓拉紧即可,这样可省去螺栓孔的精加工(铰或镗)。
3、结合面的加工传统工艺是在拉断后还要磨削结合面,且连杆体/盖的装配定位靠两个螺栓孔中的定位孔和螺栓的定位部分配合来定位,所以对螺栓孔与其分离面的垂直度和两螺栓孔的中心距尺寸
都有严格的要求。
尺寸误差导致连杆与连杆盖装配后有残余应力留在连杆总成。
连杆总成的两侧面和大小头孔精加工完毕后,要送到发动机装配线上与曲轴装配,这时要拆开连杆盖与连杆,释放残余应力,这会造成连杆大头孔变形。
当连杆盖与连杆被再次安装到发动机曲轴上时,变形严重的可导致无法安装
4、螺栓孔加工涨断工艺加工的连杆体/盖的装配定位是以涨断断面作定位,而传统工艺加土的连杆体/盖的装配定位靠两个螺栓孔中的定位孔和螺栓的定位部分配合来定位,所以对螺栓孔和螺栓的精度要求都很高。
以两个螺栓孔孔距为例:传统工艺加工时公差要求为士0.05mm,而采用涨断工艺加工时为±0.1 mm。
采用涨断工艺加工连杆时,两个螺栓孔可不同时加工,这样为多品种加工创造了便利条件。
连杆大头孔采用涨断工艺后,它们的分离面是最完全的啮合,所以没有分离面及螺栓孔加工误差等影响。
采用涨断工艺加工的连杆螺栓孔结构简单,精度要求低,使用6工位自动线就可以完成螺栓孔加工;而传统工艺加工连杆螺栓孔则需要14个工位,而且需要分别定位夹紧连杆体/盖,夹具复杂,设备工装投资很大。
二连杆加工的工艺流程
连杆加工的工艺流程是:拉大小头两端面——粗磨大小头两端面→拉连杆大小头侧定位面→拉连杆盖两端面及杆两端面倒角→拉小头两斜面→粗拉螺栓座面,拉配对打字面、去重凸台面及盖定位侧面→粗镗杆身下半圆、倒角及小头孔→粗镗杆身上半圆、小头孔及大小头孔
倒角→清洗零件→零件探伤、退磁→精铣螺栓座面及R5圆弧→铣断杆、盖→小头孔两斜端面上倒角→精磨连杆杆身两端面→加工螺栓孔→拉杆、盖结合面及倒角→去配对杆盖毛刺→清洗配对杆盖→检测配对杆盖结合面精度→人工装配→扭紧螺栓→打印杆盖配对标记号→粗镗大头孔及两侧倒角→半精镗大头孔及精镗小头衬套底孔→检查大头孔及精镗小头衬套底孔精度→压入小头孔衬套→称重去重→精镗大头孔、小头衬套孔→清洗→最终检查→成品防锈。