加工工艺参数标准规范
实用CNC加工参数设置标准
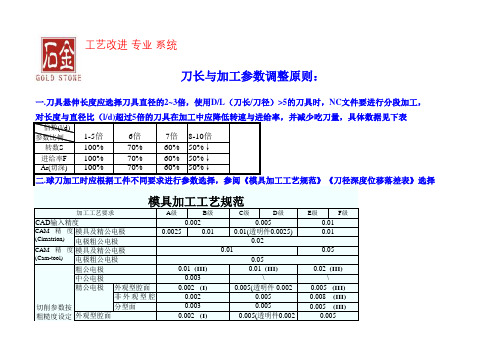
倍数(l/d)
参数比例
转数S 100%70%60%50%↓
进给率F 100%70%60%50%↓
Ar(切深)100%70%60%50%↓
A 级
B 级
C 级
D 级
E 级
F 级
0.00250.01外观型腔面非外观型腔
面分型面1-5倍6倍7倍8-10倍一.刀具悬伸长度应选择刀具直径的2~3倍,使用D/L (刀长/刀径)>5的刀具时,NC 文件要进行分段加工,二.球刀加工时应根据工件不同要求进行参数选择,参阅《模具加工工艺规范》《刀径深度位移落差表》选择
模具加工工艺规范
加工工艺要求CAD 输入精度
0.0020.0050.01CAM 精度(Cimatrion)模具及精公电极0.01(透明件0.0025)
0.01电极粗公电极
0.02CAM 精度(Cam-tool)模具及精公电极0.01
0.05电极粗公电极
0.05切削参数按
粗糙度设定平优化)粗公电极
0.01 (III)0.01 (III)精公电极0.002 (I)0.005(透明件 0.002
0.0030.0050.005 (III)0.0020.0050.008 (III)0.02 (III)中公电极
0.003\\0.005 (III)外观型腔面
0.002 (I) 0.005(透明件0.0020.005
刀长与加工参数调整原则:
工工艺改进专业系统
四.切削参数计算常用公式。
机械设计中的机械加工工艺规范要求
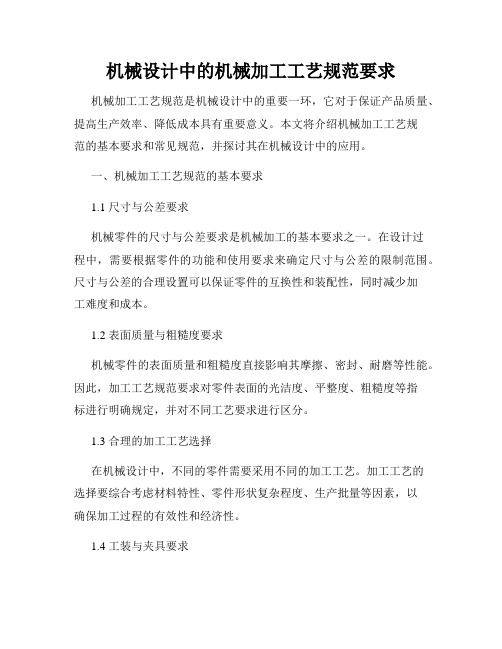
机械设计中的机械加工工艺规范要求机械加工工艺规范是机械设计中的重要一环,它对于保证产品质量、提高生产效率、降低成本具有重要意义。
本文将介绍机械加工工艺规范的基本要求和常见规范,并探讨其在机械设计中的应用。
一、机械加工工艺规范的基本要求1.1 尺寸与公差要求机械零件的尺寸与公差要求是机械加工的基本要求之一。
在设计过程中,需要根据零件的功能和使用要求来确定尺寸与公差的限制范围。
尺寸与公差的合理设置可以保证零件的互换性和装配性,同时减少加工难度和成本。
1.2 表面质量与粗糙度要求机械零件的表面质量和粗糙度直接影响其摩擦、密封、耐磨等性能。
因此,加工工艺规范要求对零件表面的光洁度、平整度、粗糙度等指标进行明确规定,并对不同工艺要求进行区分。
1.3 合理的加工工艺选择在机械设计中,不同的零件需要采用不同的加工工艺。
加工工艺的选择要综合考虑材料特性、零件形状复杂程度、生产批量等因素,以确保加工过程的有效性和经济性。
1.4 工装与夹具要求工装与夹具是机械加工过程中保证零件加工精度和质量的重要手段。
在加工工艺规范中,需要明确工装与夹具的设计要求,包括定位准确性、刚性要求、对零件表面的影响等方面的要求。
二、常见的机械加工工艺规范2.1 铣削工艺规范铣削是机械加工中常用的一种切削工艺。
在铣削工艺规范中,通常包括切割参数的选择、工艺路线的确定、刀具的选择和刀具装夹的要求等方面的规定。
2.2 钻削工艺规范钻削是机械加工中常见的孔加工工艺。
钻削工艺规范通常包括刀具选型、切削速度和进给速度的确定、冷却液的使用和孔径尺寸与公差要求等方面的规定。
2.3 镗削工艺规范镗削是机械加工中用于加工孔的高精度工艺。
镗削工艺规范包括镗削刀具的选择和装夹要求、切削速度和进给速度的确定、镗削后的孔径精度和圆度要求等方面的规定。
2.4 拉削工艺规范拉削是机械加工中用于加工轴类零件的一种工艺。
拉削工艺规范包括刀具的选择、切削速度和进给速度的确定、拉削后的尺寸公差要求和表面粗糙度要求等方面的规定。
机械加工工艺参数设定规定
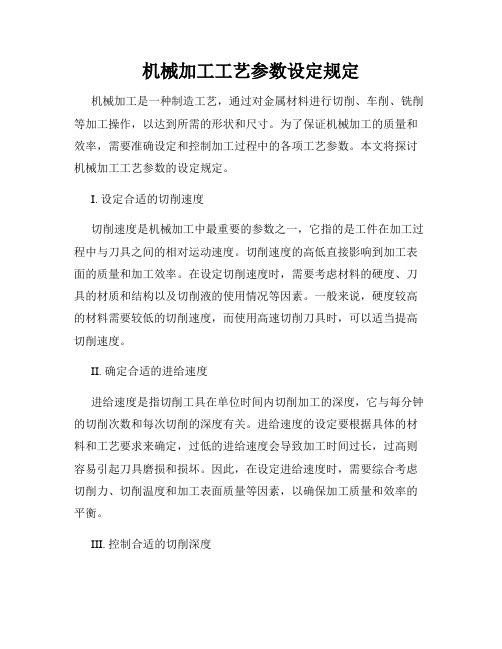
机械加工工艺参数设定规定机械加工是一种制造工艺,通过对金属材料进行切削、车削、铣削等加工操作,以达到所需的形状和尺寸。
为了保证机械加工的质量和效率,需要准确设定和控制加工过程中的各项工艺参数。
本文将探讨机械加工工艺参数的设定规定。
I. 设定合适的切削速度切削速度是机械加工中最重要的参数之一,它指的是工件在加工过程中与刀具之间的相对运动速度。
切削速度的高低直接影响到加工表面的质量和加工效率。
在设定切削速度时,需要考虑材料的硬度、刀具的材质和结构以及切削液的使用情况等因素。
一般来说,硬度较高的材料需要较低的切削速度,而使用高速切削刀具时,可以适当提高切削速度。
II. 确定合适的进给速度进给速度是指切削工具在单位时间内切削加工的深度,它与每分钟的切削次数和每次切削的深度有关。
进给速度的设定要根据具体的材料和工艺要求来确定,过低的进给速度会导致加工时间过长,过高则容易引起刀具磨损和损坏。
因此,在设定进给速度时,需要综合考虑切削力、切削温度和加工表面质量等因素,以确保加工质量和效率的平衡。
III. 控制合适的切削深度切削深度是指刀具在每次切削中削除工件材料的厚度。
切削深度的设定要根据工件的材质、硬度和稳定性来确定。
如果切削深度过大,会增加切削力和切削温度,容易导致刀具振动、工件变形和表面质量下降。
因此,在设定切削深度时,需要根据具体情况做出合理的选择,并进行试切实验以验证加工效果。
IV. 设定适当的切削液使用量切削液在机械加工过程中起到冷却、润滑和清洁的作用,能有效降低切削温度、减少切削力和延长刀具寿命。
切削液的使用量需要根据加工材料、切削速度和切削方式等因素来确定。
针对不同的工艺要求,有时需要调整切削液的类型和浓度。
在设定切削液使用量时,操作人员应掌握切削液的性能指标,并遵循相关的安全操作规范。
V. 考虑刀具的选择和磨损控制刀具的选择要根据不同的加工任务来确定,包括工件材料、形状和尺寸等方面的要求。
同时,刀具的磨损情况也需要及时控制,以保证加工质量和效率。
模具加工工艺标准

结构简单:模 具设计应尽量 简单、明了, 方便操作和维 护。
0
0
0
0
1
2
3
4
模具设计的工艺性分析
模具材料的选用:根据产品要求和生产条件选择合适的模具材料,确保模具的耐磨性、 耐腐蚀性和热稳定性。
模具结构的合理性:模具结构设计应简单、紧凑,便于制造、装配、调试和使用,同时 要充分考虑模具的强度和刚性。
热处理工艺流程:预热、加热、保温、冷却和后处理等步骤
热处理工艺参数:加热温度、保温时间、冷却速度等参数对热处理效果的影响
04
模具设计的工艺要求
模具设计的原则
符合产品要求: 模具设计应满 足产品形状、 尺寸和性能的 要求。
加工方便:模 具设计应便于 制造、装配、 检测和维修, 降低制造成本。
寿命长:模具 设计应保证模 具的使用寿命, 提高模具的可 靠性和稳定性。
根据模具材料选择合适的刀 具类型和刀片材质
考虑刀具的寿命和耐用度, 合理使用刀具补偿功能
掌握刀具的安装与拆卸方法, 确保安全操作
切削参数的优化
切削速度:根据材料和刀具选 择合适的切削速度,以提高加 工效率和降低表面粗糙度。
进给量:适当调整进给量可以 提高切削效率,同时保证加工 质量。
切削深度:合理选择切削深度 可以减少刀具磨损和加工时间, 提高加工精度。
模具加工的重要性
模具加工的精度和稳定性直 接关系到产品的质量和生产 效率,是实现产品批量生产 的关键因素。
模具加工是制造业的重要环节, 对产品生产的质量和效率具有 决ቤተ መጻሕፍቲ ባይዱ性影响。
模具加工技术的发展和应用, 能够推动制造业的技术进步 和产业升级,提高生产效率
和产品质量。
线切割加工工艺规范标准

线切割加工工艺规操作者必须受过线切割加工的专业培训,并经过考核合格取得上岗证后,才有资格进行线切割加工。
在加工前的准备和实际加工过程中,必须遵守以下守则。
一、快走丝线切割加工工艺规:1、操作者在加工前要检查图纸资料是否齐全,坯件是否符合要求;2、认真消化全部图纸资料,掌握工装的使用要求和操作方法;3、检查加工所用的机床设备,准备好各种附件,按机床按规定进行润滑和试运行;4、操作者佩戴相应的安全防护工具。
快走丝线切割加工常见质量问题、产生原因和解决方法:(一)、加工程序编制要求:1.根据工艺要求,按图纸尺寸编写加工程序,发现问题时找有关人员;2.注意图纸尺寸是否分中,确定编程基准;3.保证补偿正确;4.将程序输入机床控制电脑;5.编程坐标系应与工作坐标系一致(二)、工件装夹要求:1.看懂图纸和工艺过程卡;2.保证不拿错工件;3.各穿丝孔不能赌塞;4.工件装夹应牢固可靠,防止工件脱落砸坏机头;5.不能有异物在机头工作槽;6.机头不能与夹具发生干涉;7.机头不能超出工作台行程,工件不要在机床上拖动。
(三)、技术要求:1.电极丝直径0.1~0.25(mm);2.间隙补偿量(钼丝的外偏移量)0.001~0.009(mm);3.齿隙补偿量0.001~0.015(mm);4.开口割凹模应先放气,再加工;5.加工多个孔时先复线,按不同的孔径(规格)分类割,加工多个尺寸相同的孔时,应先加工一个凸模,再采用试切法加工孔,每加工三个孔,至少用凸模实配一次;6.加工凸模时应先加工孔再加工外围;7.不允许在带负载情况下改变脉宽,如工作过程需要改变,可在储丝筒停止时进行。
(四)、工艺参数选择(供参考)1.冷却膏浓度选择:冷却膏对加工参数影响很大,具体见下表选择:2.新快走丝线切割加工参数选择:脉冲宽度增加,功放管增多都会使切割速度提高,但加工表面粗糙度和精度会下降,其参数选择可参照下表:(五)、自检容与要求1.操作者应检查前面各工序是否符合图纸及工艺要求;2.检查工件装夹的方向是否与编程方向相符;3.根据加工程序校核加工部位的形状,尺寸是否与图纸相符;4.根据记录的坐标校核加工部位的相关尺寸是否与图纸相符;5.加工过程中要检查钼丝是否在轮上,是否出现松丝情况;6.不断检查实际坐标值是否与理论相符;7.检查加工过程中,冷却液供应是否正常。
加工工艺参数管理制度

加工工艺参数管理制度一、总则为了规范加工工艺参数管理,提高产品质量,降低生产成本,保障生产安全,制定本制度。
二、制度范围本制度适用于生产加工过程中的工艺参数管理,包括但不限于:机械加工、焊接、喷涂、涂装等工艺。
三、管理要求1.确定参数范围:根据产品特性、生产工艺以及设备性能等因素,确定每种加工工艺的参数范围。
2.参数设置:对每种加工工艺的参数进行设置,包括参数数值、单位、精度等信息,并记录在制度文件中。
3.参数检测:对加工过程中的参数进行定期检测,确保其符合要求,如发现异常情况及时调整,并记录检测结果。
4.参数修改:如有需要修改参数,需经过相关部门审批并记录修改内容、时间等信息。
5.参数备份:对每次参数设置进行备份,确保在需要时能够追溯历史设置。
6.参数培训:针对操作人员进行相关参数设置培训,确保其熟悉参数设置流程。
四、责任分工1.生产部门负责具体的参数设置和调整工作。
2.质量部门负责对参数设置进行监督和检查工作。
3.设备部门负责设备参数设置和维护工作。
4.管理部门负责对加工工艺参数管理制度的监督和落实。
五、考核评价1.定期对加工工艺参数管理制度进行评估,发现问题及时改进。
2.对相关部门和操作人员的工作进行考核评价,确保加工工艺参数的正确设置和稳定运行。
3.按照实际执行情况对加工工艺参数管理制度进行调整和完善。
六、附则1.本制度自发布之日起生效,具体实施细则由相关部门制定。
2.本制度如有变动,经相关部门审批后须重新发布。
3.本制度解释权归公司管理部门。
以上制度主要针对加工工艺参数管理进行规范,落实到具体工艺中需要结合实际情况进行具体操作。
只有加强参数管理,严格执行制度,才能确保产品质量和生产效率的提高。
机械加工车间工艺参数标准
机械加工车间工艺参数标准在机械加工车间中,工艺参数标准起着至关重要的作用。
它们用于确保机械加工过程的准确性和稳定性,从而保证产品的质量达到要求。
本文将详细介绍机械加工车间的工艺参数标准,包括其定义、作用、分类及应用等方面的内容。
一、工艺参数标准的定义及作用工艺参数标准是指在机械加工过程中,为实现特定工件的加工要求而规定的相关参数数值。
它们直接影响到机械加工的质量和效率。
以车削加工为例,常见的工艺参数标准包括切削速度、进给速度、切削深度等。
这些参数的准确控制可以保证工件表面的精度和光洁度,提高机械加工的效率。
工艺参数标准在机械加工车间中发挥着以下几个重要作用:1. 确保加工质量:通过合理设置工艺参数标准,可控制加工过程中的切削力、温度等因素,以确保工件的尺寸精度、表面质量等达到要求。
2. 提高加工效率:工艺参数标准的优化可以使加工过程更加高效,减少废品率,节约生产时间和成本。
3. 保护机床和刀具:合理设置工艺参数标准可以减小对机床和刀具的磨损和负荷,延长设备寿命。
二、工艺参数标准的分类机械加工的工艺参数标准可以根据其性质进行不同的分类。
常见的分类方法如下:1. 切削参数标准:包括切削速度、进给速度、切削深度等,用于控制切削过程中的切削量、加工速度等参数。
2. 刀具参数标准:包括刀具材料、刀具形状、刃数、切削刃角等,用于指导选择适合不同加工任务的刀具。
3. 加工工艺参数标准:包括定位误差、加工次序、夹持方式等,用于规定加工过程中的工艺要求。
4. 加工设备参数标准:包括机床精度、主轴转速、进给设定等,用于设定机床和辅助设备的相关参数。
三、工艺参数标准的应用工艺参数标准在机械加工车间中具有广泛的应用。
下面以车削加工为例,介绍其应用过程:1. 切削速度:根据加工材料的种类和硬度,选取适宜的切削速度,以确保加工过程中切削过程的稳定性和切削工具的寿命。
2. 进给速度:通过调整进给速度,可以控制切削过程中金属切削屑的形成和排除,达到减小加工表面粗糙度、提高表面质量的目的。
pcb加工工艺标准
pcb加工工艺标准
PCB加工工艺标准是指在印刷电路板的生产过程中,为了保
证产品质量和标准化生产,制定的一系列加工工艺规范和标准。
以下是常见的PCB加工工艺标准:
1. IPC标准:IPC是国际电子产业协会,制定了一系列关于PCB加工的标准,比如IPC-A-600、IPC-6012等。
这些标准涵
盖了PCB设计、制造和组装的各个方面,包括设计规范、材
料选择、工艺流程、工艺参数等。
2. PCB尺寸标准:PCB尺寸标准一般由制造厂商自己制定,
包括最小线宽、最小孔径、最小间距、最小焊盘径、最小过孔径等要求,以确保PCB能够被正常制造和组装。
3. 表面处理标准:PCB在制造过程中需要进行表面处理,常
见的方法包括化学镀金、镀锡、喷锡、沉金等。
各种表面处理方法都有相应的标准,用来规范处理效果和耐腐蚀性能。
4. 质量检测标准:制造过程中需要对PCB进行质量检测,常
见的检测项目包括线宽、线间距、孔径偏差、焊盘平整度、表面平整度等。
这些检测项目有相应的标准,例如IPC-TM-650,用来判断产品是否合格。
5. SMT组装标准:对于表面贴装(SMT)组装的PCB,有一
系列标准用来规范组装工艺,包括元件位置精度、焊锡质量、焊接温度曲线、回焊炉的参数等。
以上是一些常见的PCB加工工艺标准,不同的厂商和行业可能会有一些特定的标准要求,需要根据具体情况进行制定和执行。
机械零部件加工工艺规范
机械零部件加工工艺规范随着工业的快速发展,机械零部件的加工工艺变得越来越重要。
良好的加工工艺规范能够确保零部件的质量和性能,提高生产效率。
本文将介绍机械零部件加工工艺规范的一般要求、工艺流程以及常见加工方法。
一、一般要求1. 材料选择:根据零部件的要求和使用环境,选择适宜的材料。
要求材料具有一定的强度、硬度、耐磨性和耐腐蚀性,并且易于加工。
2. 加工精度要求:根据零部件功能和装配要求,确定加工精度。
主要包括尺寸精度、形位精度和表面粗糙度。
3. 工艺参数:根据材料的不同特性和零部件要求,合理选择切削速度、进给速度、切削深度等加工参数。
4. 加工工具选择:根据零部件的材料和结构,选择适合的切削工具。
要求工具具有良好的刚性和切削性能。
二、工艺流程机械零部件加工的一般工艺流程包括以下几个步骤:1. 工艺准备:根据加工对象的要求,制定合理的工艺方案。
包括制定加工工艺路线、选择加工方法和计算工艺参数等。
2. 材料准备:根据零部件的要求,选择合适的材料,并进行铸造、锻造或切削等加工,得到初步零件。
3. 粗加工:根据零部件的形状和尺寸,采用车削、铣削、钻削等方法对初步零件进行粗加工。
保留适当的余量以备后续加工。
4. 热处理:对需要改善材料性能的零部件进行热处理,包括淬火、回火、调质等。
根据材料的不同,选择适当的热处理工艺。
5. 精加工:对经过热处理后的零部件进行精加工,包括车削、铣削、磨削等。
精加工要求加工精度高、表面质量好。
6. 装配:将各个零部件按照要求进行装配,包括焊接、螺纹连接、铆接等。
确保零部件的准确安装和配合。
7. 表面处理:根据零部件的要求,采取表面喷涂、电镀、热喷涂等方式进行表面处理,提高零部件的耐磨性和防腐蚀性。
三、常见加工方法1. 车削:通过旋转工件,在切削刀具的作用下削除工件上的材料,得到所需的形状和尺寸。
2. 铣削:通过旋转铣刀,在刀具的作用下相对静止的工件上进行切削,得到平面、曲面等形状。
加工中心加工工艺规范范文
加工中心加工工艺规范一、龙门加工中心加工工艺规范操作者必须接受有关龙门加工中心的理论和实践的培训,并且通过考核获得上岗证,才能具备操作龙门加工中心加工的资格。
1、加工前准备1.操作者必须根据机床使用说明书熟悉机床的性能,加工范围和精度,并且熟悉机床及其数控装置和计算机各部分的作用及其操作方法。
2.检查各开头、旋钮和手柄是否在正确位置。
2、加工要求1.进行首件加工前,必须经过程序检查、轨迹检查、单程序段试切及工件检查等步骤。
2.加工时,必须正确输入程序,不得擅自更改别人的程序。
3.加工过程中,操作者必须监视显示装置,发现报警信号时,应及时停机排除故障。
4.加工中不得任意打开控制系统及计算机柜。
5.本工序是关键加工工序,所加工的工件经自检合格后,必须送检验员专检。
3、刀具与工件装夹1.刀具安装应注意刀具使用顺序,刀具安放位置须与程序要求顺序和位置一致。
2.工件装夹应牢固可靠,注意避免在工作中刀具与工件、刀具与刀具发生干涉。
4、加工参数设定1.主轴转速定义:N=1000*V/3.14*D N--主轴转速(rpm/min) V--加工速度(m/min) D--刀具直径(mm),加工速度在刀具资料中查出2.进给速度设定:F=N*M*F’ F-进给速度(mm/min),N-主轴转速(rpm/min),M-刀具刃数值,F’-刀具加工量(mm/刃口)5、工件碰数对一件装夹好的工件,可以利用碰数头对其进行碰数定工件的加工零件,步骤如下:(机械式碰数头应在旋转状态下,转数450-600rpm/min)1.手动移动工作台X轴,使碰数头碰工件的一侧面,当碰数头刚碰到工件,红灯发亮,这时就设定这点相对座标值为零。
2.手动移动工作台X轴,使碰数头碰工件的另一侧面,当碰数头刚碰到工件,记下这时的相对座标值。
3.把这时的相对座标值除以2,所得数值就是工件X轴上的中间值。
4.再移动工作台到X轴上的中间数值,把这点的X轴的相对座标值设定为零,这一点就是工件X轴上的零位。