QP-008外部提供产品、服务和过程控制程序
QP08生产过程控制程序

文件修订履历制/改订:日期:审核:日期:批准:日期:1.目的对生产过程中直接影响产品质量的各种因素进行控制,确保产品满足顾客的需求。
2.适用范围适用于本公司吸塑过程及相关的生产过程的控制,包括从原材料到成品入库前的过程控制。
3.职责3.1 生产部制定生产计划,负责生产设备的维护保养,生产设备的审批。
3.2工程部负责负责技术标准的制订、工艺技术文件的审核及批准。
3.4生产部确保作业现场基础设施适用及工作环境良好3.5生产部负责协调车间及各部门的生产技术活动,组织实施作业指导书、操作规程的制订和相关生产活动的协调和安排。
3.6品管部负责按照《产品检验控制程序》以及检验指导书、图纸、工艺卡等进行相关过程的产品的检验和试验控制。
4.工作程序4.1过程策划由相关人员进行工艺、设备、工装、生产、检验等的策划,如需要,相关人员应编制必要相应的工艺卡、检验指导书、作业指导书和操作规程,现场使用的各类作业指导书和用于指导生产的各种样品/样件、缺陷图片等须放置在相应工位处,使操作人员易于得到。
4.2 生产计划4.2.1 根据合同评审的结果,考虑库存情况,结合车间的生产能力,制订各车间制定生产计划并将随供应、生产、销售等情况的变动,在适当的时候进行修改。
4.2.2 车间根据生产计划安排生产,并填《领料单》向仓库领取所需物料,并统计每天的产量,以生产日报表的形式统计每月生产的完成情况。
对于调整排期后,仍然无法加工的工件,申请外发加工,按《供应商管理和采购控制程序》执行。
4.3原材料、外购、外协件控制4.3.1品管部负责对进厂的原材料、外购、外协件实施入库检验控制。
按《产品的监视和测量控制程序》的规定执行,杜绝不合格的原材料、外购、外协件被投入生产和使用。
发现不良或偏差时,应按《不合格品控制程序》或《不合格和纠正措施程序》的要求,及时发单通知车间采取相应纠正措施。
4.3.2仓库管理人员必须严格按照的规定作好产品标识和批次管理。
QP-08 生产过程控制程序

生效日期:2019/5/10 生产过程控制程序编制人:日期:2019-5-10审核人:日期:2019-5-10批准人:日期:2019-5-10版本:A/0 状态:2019年5月10日发布 2019年5月10日实施生效日期:2019/5/10■制订□修订□废止分发部门总经理/质量负责人市场部采购部工程生产部品管部行政部财务部▲▲▲分发(份) 1 1 1修订履历版本版次修订日期修订内容修订人A0 首版发行2019/5/10生效日期:2019/5/10 1.0 目的通过有效控制直接影响产品质量的各要素,确保公司提供的产品满足质量要求。
2.0 适用范围本程序适用于本公司全部生产过程。
3.0 职责3.1 生产部负责生产计划的制定及生产任务的下达;3.2 品质部负责生产作业过程中的品质控制和产品在生产过程中的一致性检验;3.3工程部负责生产作业过程中的工艺确定《作业指导书》的制定、审核;3.4仓库负责生产作业过程中的物料准备与发放,成品入库;3.5生产部门负责生产过程中的产品制作和品质保证.4.0 工作程序4.1 生产准备4.1.1 生产部根据工艺文件要求,确定合理的生产工位工序排列。
4.1.2生产部确认所需物料都已准备齐全且全部符合标准。
4.1.3 生产过程中所用到的图纸、技术文件等完全具备且满足要求。
4.1.4 确认工序生产人员的资格满足要求。
4.1.5 确认产品质量检验规范齐备和满足要求。
4.2 生产过程的控制4.2.1 工程部对产品生产过程进行策划,形成合理的工艺路线,编制相应的工艺生效日期:2019/5/10 文件。
4.2.2 工艺文件中应有明确规定完成工作的方法、验收及核准。
4.2.3 现场使用的技术文件应一致、完整、清晰,使用文件不得涂改。
4.2.4 生产所用设备仪器由生产部进行日常维护、保养,以保证过程能力。
设备仪器由品质部按《设施设备和工作环境管理程序》进行周期检定和周期捡修维护。
4.2.5 生产现场的环境,由生产部按工作环境检查标准进行检查。
XXQP008与顾客有关过程控制程序
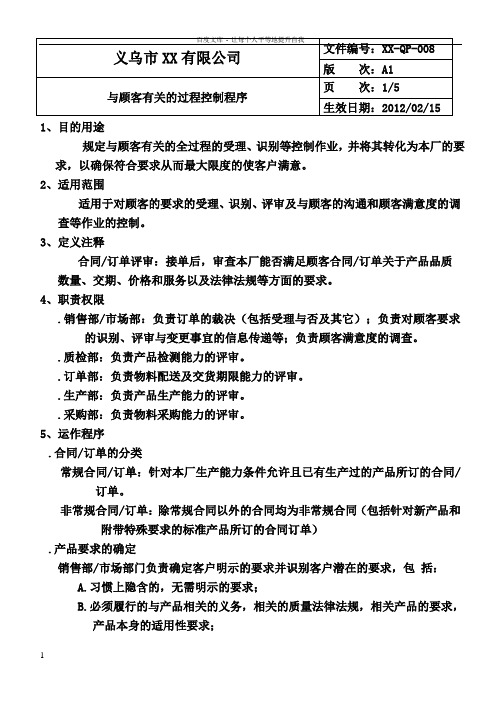
1、目的用途规定与顾客有关的全过程的受理、识别等控制作业,并将其转化为本厂的要求,以确保符合要求从而最大限度的使客户满意。
2、适用范围适用于对顾客的要求的受理、识别、评审及与顾客的沟通和顾客满意度的调查等作业的控制。
3、定义注释合同/订单评审:接单后,审查本厂能否满足顾客合同/订单关于产品品质数量、交期、价格和服务以及法律法规等方面的要求。
4、职责权限.销售部/市场部:负责订单的裁决(包括受理与否及其它);负责对顾客要求的识别、评审与变更事宜的信息传递等;负责顾客满意度的调查。
.质检部:负责产品检测能力的评审。
.订单部:负责物料配送及交货期限能力的评审。
.生产部:负责产品生产能力的评审。
.采购部:负责物料采购能力的评审。
5、运作程序.合同/订单的分类常规合同/订单:针对本厂生产能力条件允许且已有生产过的产品所订的合同/订单。
非常规合同/订单:除常规合同以外的合同均为非常规合同(包括针对新产品和附带特殊要求的标准产品所订的合同订单).产品要求的确定销售部/市场部门负责确定客户明示的要求并识别客户潜在的要求,包括:A.习惯上隐含的,无需明示的要求;B.必须履行的与产品相关的义务,相关的质量法律法规,相关产品的要求,产品本身的适用性要求;C.顾客对产品的可靠性,运输、自身的健康、安全、环境等方面。
在第一次与顾客签订合同时,对应的经过顾客的书面认可的相关资料应作为合同附件。
订货要求须包括但不限于:——产品型号——规格要求(无要求则视为常规产品)——数量——交付日期及地点——单价所有订货合同涉及的与产品有关的要求由销售部/市场部经理签字盖章后交生产计划部经理批准后再执行。
同时填写“生产计划表”以便追溯。
5.2.4.销售部/市场部根据顾客规定的订货要求直接由订单部寻求供应商下采购订单索取相关要求产品与相应的部门配合出货作业。
5.3.合同/订单评审合同的评审应在合同签订之前进行,以确保顾客的各项要求合理、明确、书面化、双方协调一致、公司有能力满足。
QP10-产品和服务的实现过程控制程序
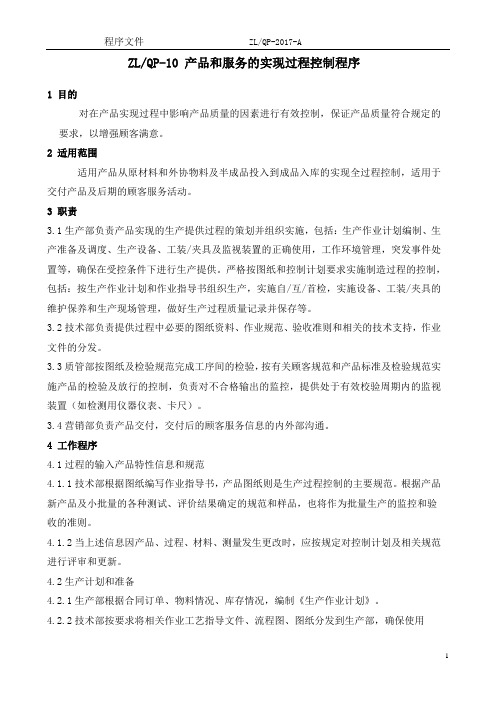
ZL/QP-10 产品和服务的实现过程控制程序1 目的对在产品实现过程中影响产品质量的因素进行有效控制,保证产品质量符合规定的要求,以增强顾客满意。
2 适用范围适用产品从原材料和外协物料及半成品投入到成品入库的实现全过程控制,适用于交付产品及后期的顾客服务活动。
3 职责3.1生产部负责产品实现的生产提供过程的策划并组织实施,包括:生产作业计划编制、生产准备及调度、生产设备、工装/夹具及监视装置的正确使用,工作环境管理,突发事件处置等,确保在受控条件下进行生产提供。
严格按图纸和控制计划要求实施制造过程的控制,包括:按生产作业计划和作业指导书组织生产,实施自/互/首检,实施设备、工装/夹具的维护保养和生产现场管理,做好生产过程质量记录并保存等。
3.2技术部负责提供过程中必要的图纸资料、作业规范、验收准则和相关的技术支持,作业文件的分发。
3.3质管部按图纸及检验规范完成工序间的检验,按有关顾客规范和产品标准及检验规范实施产品的检验及放行的控制,负责对不合格输出的监控,提供处于有效校验周期内的监视装置(如检测用仪器仪表、卡尺)。
3.4营销部负责产品交付,交付后的顾客服务信息的内外部沟通。
4 工作程序4.1过程的输入产品特性信息和规范4.1.1技术部根据图纸编写作业指导书,产品图纸则是生产过程控制的主要规范。
根据产品新产品及小批量的各种测试、评价结果确定的规范和样品,也将作为批量生产的监控和验收的准则。
4.1.2当上述信息因产品、过程、材料、测量发生更改时,应按规定对控制计划及相关规范进行评审和更新。
4.2生产计划和准备4.2.1生产部根据合同订单、物料情况、库存情况,编制《生产作业计划》。
4.2.2技术部按要求将相关作业工艺指导文件、流程图、图纸分发到生产部,确保使用者易于获取和使用有效版本的文件。
4.2.3质管部按《产品和服务的监视与测量控制程序》要求,提供并确保在生产过程中所使用的监视和测量装置处于校验周期内,并满足测量的要求。
QP-008产品设计和开发管理程序V1.0

QP-008 V1.0产品设计和开发管理程序修订历史1目的明确新产品各开发阶段作业内容, 作为设计开发作业管控依据, 使产品合乎市场及客户需求。
2范围适用于公司所开发设计的产品。
3定义3.1MRS(C0)阶段 --- Marketing Request Specification, New product proposal and feasibilitystudy.产品企划阶段,新产品提案(市场分析与规格拟定)及可行性研究(成本、设备、产能).3.2EVT(C1)阶段--- Engineering Verification Testing, usually associated with Alpha phase.工程设计及验证阶段,依MRS进行样机雏型制作以确定功能及成本符合MRS要求.3.3DVT(C2)阶段--- Development Verification Testing, usually associated with Beta phase.工程试作阶段,证明产品可进行生产及符合可靠度、EMC及安规相关要求,且可给客户承认。
3.4PVT(C3)阶段--- Product Verification Testing, once the product is released and ready forshipment. 小批量生产验证阶段,验证产品可进行大量生产及出货给客户.3.5EBOM---研发工程物料清单,用于EVT/DVT阶段及PVT前期研发工程样品备料用的BOM。
4职责4.1研发中心:负责产品ID设计及产品的机构设计、电子设计和软件的设计工作及产品试投跟进工作。
4.2生产技术工程师:负责所有产品PVT阶段的试投主导工作,并在EVT/DVT阶段参与工程样品制做。
4.3项目管理员:负责所有新产品开发计划的制订及更新(总进度延误半个月需更新版本),开发进度的跟踪,每个开发阶段的检讨、总结及本程序的完善、执行督导工作。
QP-008供应商评估与管理程序
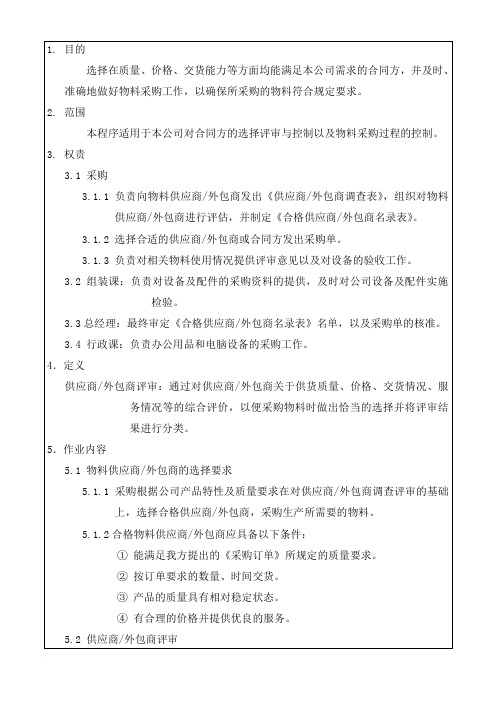
④《采购订单》等采购资料发出后如果需要更改,则由采购人员电话和供应商/外包商联系重新确认。
5.5.6若客户或公司要求在供应商/外包商现场进行验收时,采购信息发出时必注明验收的时间、验收标准以及放行的相关要求。
5.6采购物品验收:
5.6.1所有生产物料(含外包加工),采购均应在投入生产前及时采购到公司。
5.5.4采购员负责全过程中的催货、到货接收、物品随附采购单据及送货单交质检单位检验或验证。其中以“请购单”形式实施采购的物资直接入库。
5.5.5对于需预订的主料、贵重物资,采购人员应提前填写《采购订单》,其中:
①必须填写清楚物料名称、型号、规格、数量、交货日期等,必要时应注明价格、质量要求等。
②若是特殊规格的物资采购,应附上相应的技术资料,如图纸、样品、质量要求等。
2.4 D级厂商
1)延长票期30天;并需出席品质会议作改善报告。
2)连续二次考核D级者,延长票期45天;并须排入稽核与辅导名单。
3)连续三次考核D级者,延长票期60天;并项目呈报经理裁示,将考虑予以除名。
4)经公告予以除名之厂商,除非经经理核示或重新再经评鉴合格,否则不得再继续往来。
三.将考核结果记录在《供应商/外包商考核表》上。
5.4零星采购的控制
5.4.1对于零星采购,由采购根据需要选择相应的供应商/外包商,并进行初步判断,认为合格后实施采购。
5.4.2采购回来以后,由质检部对其质量进行检验,不合格的立即退回,合格的投入使用。
5.4.3采购将零星采购在《请购单》中予以记录。
5.4.4若在一年之内在同一家供应商/外包商实施零星采购超过2次,则应对其进行评审,合格后列入《合格供应商/外包商名录表》中。
ZAE-QP-008 Production Material Planning Control Procedure生产、物料计划控制程序_REV2
Document No.: Production Material Planning Control ProcedurePage of 81Document Number and Revision文件编号及版本:ZAE-QP-008 Rev · 2Document Title 文件题目:Production Material Planning Control Procedure生产、物料计划控制程序Approvals(批准)Page No.1 2 3 4 5 6 7(页码)Rev. No.2 2 2 2 2 2 2(版本号)Page. No.8(页码)Rev. No.2(版本号)生效日期Effective date:Jun 08, 2011Document No.: Production Material Planning Control ProcedurePage of 82 Revision History (更改历史):Revision (更改)From ToDate(日期)Revision Description(更改内容)Changed by(更改人)Checked by(复核人)0 1 2Mar 1, 2010Jan 10,2011Jun 08,2011New Document7.2生产计划及物料计划由PMC主管批准7.2生产与物料计划的制定Chary HuangAngus ChenDaisy LiaoLand LiangWayne GuoKobe LongDocument No.: Production Material Planning Control ProcedurePage of 83 CONTENTS (目录)1.0 目的PURPOSE2.0 范围SCOPE3.0 定义DEFINITION4.0 参考文件REFERENCE5.0 职责RESPONSIBILITY6.0 资格和培训QUALIFICATION AND TRAINING7.0 程序PROCEDURE7.1 订单的接收Receive Customer Order7.2 生产与物料计划的制定Prepare production and material plan7.3 采购申请单的审核Approve the Purchase Request7.4 物料的跟进Material tracking7.5 生产任务单的下达Release Manufacturing Order7.6 物料的发放Material Issuing7.7 生产计划的跟进Follow up the Production Schedule7.8 协助船务出货Coordinate the shipment with Shipping8.0 记录RECORD9.0 附录APPENDIXDocument No.: Production Material Planning Control ProcedurePage of 841.0 目的Purpose:为确保物料能准时到位,生产能顺利完成,合理调配相关资源,制订本程序。
AJ-QEP008生产作业管制程序
生产进度延迟报告
首件/IPQC巡检检验记录表
品管部成品/出货检验记录表/标示OK异常联络单
特采单/特殊作业需求单
报废单/退料/退货单
仓库入库单/帐本
业务部出货通知单
送货单
4.程序内容
4.1业务部按照《合同评审程序》进行生产订单评审,当确认已具备量产条件(样品已得到客户承认,公司内部量产说明会已召开)后,下达 [生产通知单]至各单位。
4.2生管依据业务部下达的[生产通知单]及仓库之相关半成品/成品库存报表,结合制造部的生产能力制订出[生产计划表],分发至制造部、品管部、物控等相关单位。
4.10若生产进度无法按期达成时,则由制造单位做[生产进度延迟报告]交生管及业务。
4.11若生产计划变更时,业务部及生管须依本程序4.1、4.2重新编排生产计划。
4.12产品出货时,相关单位则按《产品出货管制程序》要求执行作业。
4.13所有记录按《记录管制程序》保存,文件按《文件管制程序》作业。
5.附页
******修订履历 ******
版次
修订内容
页次
*****分发单位*****
总经理1份品管部1份
副总经理2份工模部1份
制造部1份资材部1份
工程部1份业务部1份
行政部1份财务部1份
设计部1份
核准
审核
承办
发行/制订部门
签名
董志彬
制造部
日期
2003/12/12
1.目的
为使本公司产能有所依据,满足客户需求,以保证本公司履行合同的能力,降低库存成本,提高生产效率,特拟定本程序。
4.3物控依据[生产计划表]及仓库之相关材料库存报表,拟定出材料需求[请购单],同时对所需物料进行跟催到位。
008采购管理程序
6.0 相关文件
6.1 进料检验管理程序
7.0 相关质量记录
7.1 供应商调查表 7.2 供应商考察表 7.3 供应商复审表 7.4 采购单 7.5 物料需求一览表 7.6 合格供应商一览表 7.7 RoHS 禁止化学物质调查表 7.8 RoHS 合格供应商名册
ISO9001:2008 质量管理体系文件
5.0 工作流程图:
5.1 供应商评估流程图(附件一) A.海外供应商; B.客户指定供应商; C.贸易公司(以“RoHS 禁止化学物质调查表”方式调查) ; C.声誉良好的大型企业。 D.符合我司要求的方可纳入“RoHS 合格供应商名册” 。 5.2 供应商确定的控制 5.2.1 通过评审组审定合格的供应商确定为正式供应商, 采购部汇集正式供应商的所有资料和其它相关资料建档。 提供给供应商的资料应进行统一登记管理。 5.2.2 对于已经通过认定的合格供应商,根据实际使用情况每半年进行一次复审,复审小组为原评审小组。 复审小组主要对该供应商的供货能力、质量情况.3 采购控制 5.3.1 采购计划制定 采购部根据《物料需求一览表》进行采购。 5.3.2 采购要求确认及采购计划实施 电话与供应商进行业务洽谈,确定采购产品的规格、型号、数量、价格、交货期等。签订合同或确定相关 订货清单。 由于生产急需,对于已定点的供应商暂且不能提供需方所需原材料时,由采购部向新的供应商采集样品,送品管 部做样品检测,填写《进料检验报告》 。确认合格后,由采购部采用非正式合同方式实施采购。按《进料检验管 理程序》进行检验,合格后投入使用,不合格退货、换货处理。评审小组根据使用情况,可将新的供应商纳入定 点的考核范围。 5.3.3 产品验证及管理 a、 采购进厂的产品,按《进料检验管理程序》中的条款,对采购产品进行验证。3C 认证产品的关键元器件和
IATF16949-2016标准条款及程序文件矩阵
记录应保持顾客接受替代方法(见9.1.1.1)替代方法的顾客接受记录应与替代测量系统分析的结果一起保留
●
7.1.5.2.1
校准/验证记录
●
7.1.6
组织知识
知识管理程序
公司知识管理列表,各岗位需具备的知识需在职务说明书或任职资格表中描述(或用员工培训教材、外来文件清单等方式)15版新增,必须提供
○
○
●
○
○
7.2.2
○
○
○
●
○
○
○
7.2.3
内部审核员能力
组织应有一个形成档的过程,在考虑顾客特定要求的基础上,验证内部审核员的能力。在通过培训来取得人员能力的情况下,应保留形成文件的信息,证实培训师的能
力符合上述要求
7.3
意识
QP-206
人力资源管理程序
公司通公告、会议、培训等方式提升员工意
○
○
○
●
7.5.3
QP-002
文件与数据管制程序0.0
●
7.5.3.2.1
记录保存
QP-202
记录管理程序
组织应有一个确定的形成档的并且被执行的记录保存政策。对记录的控制应满足法律法规、组织及顾客的要求。应保留生产件批准文
●
7.50.0
组织应有形成文件的过程,以保证按顾客要求的时间安排及时评审、发放和实施所有顾客工程标准/规范及其更改。组织应保留每项更改在生产中实施日期的记录。实施应包括对档的更新
●
8.3.6
设计开发的变更
QP-302
开发设计变更管制程序
组织应保留下列形成文件的信息a)设计和开发变更b)评审的结果c)变更的授权d)为防止不利影响而采取的措施
- 1、下载文档前请自行甄别文档内容的完整性,平台不提供额外的编辑、内容补充、找答案等附加服务。
- 2、"仅部分预览"的文档,不可在线预览部分如存在完整性等问题,可反馈申请退款(可完整预览的文档不适用该条件!)。
- 3、如文档侵犯您的权益,请联系客服反馈,我们会尽快为您处理(人工客服工作时间:9:00-18:30)。
外部提供产品服务和过程控制程序
制作:
审核:
批准:
文件发放部门明细
□行政部□业务部□采购部□生产部
□品质部□工程部□仓储部□财务部
盖受控章处
1.目的
规定供应商调查、认可、考核及资格取消办法,确保其供应物料在技术、品质、价格、交期及服务等方面满足公司要求。
2.适用范围
本程序适用于向本公司提供生产用原辅物料及零部件的供应商(包括生产厂家和代理商及分销商)3.定义
本公司生产用原辅物料共分为以下类别:
3.1 A类物料:在产品组成中具功能特性的物料;
3.2 B类物料:在产品组成中除A类物料外的其它物料;
3.3 C类物料:在产品形成过程中,用于帮助作业或保护产品且对产品品质影响较大的辅助物料;
3.4 D类物料:在产品形成过程中,用于帮助作业或保护产品,但对产品品质影响较小的辅助材料。
4.职责
4.1 采购部负责寻找新供应商并定期对供应商价格、交期及服务等方面进行评估和管理。
4.2 工程部负责物料承认工作,必要时协助品质部评估供应商的产品开发、设计及技术能力能否满足公司要求。
4.3 品质部负责对供应商的品质体系进行评估及定期稽核,并负责(合格供应商名单》的维护和更新。
4.4 总经理负责批准《合格供应商名单》。
5.作业程序
5.1供应商选择
5.1.1采购部根据公司生产要求,通过新闻媒体、网络、产品展销会等各种途径寻找并收集具开发
潜力的供应商资料。
5.1.2公司对供应商选择原则上是针对生产厂商,但某销售商为生产厂家指定代理商时,则该销售
商可视为生产厂商。
5.2供应商评估
5.2.1提供新物料供应商如以前曾为公司供应过其它物料时,可依其以往表现予以评估;与公司无
业务关系的新供应商,采购人员与其初步洽谈并了解其基本情况后要求填写《供应商调查表》提交采购及品管主管。
5.2.2 采购主管及品管部经理根据该供应商具体情况及提供的物料类别,确定是否须对其现场评估。
①对于生产厂商,如须现场评估时,则由采购、技术、及品质部组成评估小组对其进行现场评估。
评估完成后,评估小组填写《供应商评估报告》后由品质部存档。
②对于代理商/分销商,应由采购人员及品质部对其代理和分销等级、销售业绩、管理能力及售
后服务等重大资讯进行评估和现场考察。
③如认为无考察必要(主要是C、D类物料)或存在实际困难(主要是部分海外供应商),可由供
应商提供相关资料(如IS09000证书、质量体系文件、公司概况及相关的产品测试资料等)。
品质部、采购部、工程部组成评估小组对其资料进行评估。
5.2.3供应商评估结论包括优秀/合格/需要改善/不合格等情况,采购主管及品管主管根据评估
结果决定其后续处理方式。
①评估结论为优秀或合格,采购人员要求供应商提交样品和相关资,交工程部进行物料承认作业。
②评估结果为需要改善但由于特殊原因需再次认可此供应商时,可由采购人员提出申请,品质部
向其发出《供应商改善行动要求》(SCAR)
限期改善后再次稽核。
如仍不合格或需要改善则由采购部寻找新的供应商(对同一生产厂商最多进行两次稽核和评估)。
③评估结果为不合格时则由采购部寻找新的供应商。
5.2.4在特殊情况下(如工程部急需样品),可由供应商先送样承认,再作供应商评估,但只有送
样承认及评估合格时方可将其列入合格供应商名单。
5.2.5如已认可生产厂商发生重大变化(如变换生产地点或制程重大变更等),应按以上之6.2.2~
6.2.3重新评估。
5.3合格供应商名单控制
5.3.1评估及送样承认合格的供应商,经品管及采购主管批准后,采购文员将其资料录入ERP系统
(需提供合格证书或安全证书的供应商必须作特定标记)后生成供应商代码并告之品质部。
5.3.2如客户指定、独家专卖或专利技术之厂商,不受6.2项限制,经采购部经理批准后,品质部
将其列入《合格供应商名单》。
5.3.3品质部将其列入AVL并交品管及采购主管审核后呈总经理批准。
批准后的AVL以受控文件分
发至品管、采购、生产部门。
5.3.4 品质部负责AVL的更新与维护,品管主管每三个月检查电脑中存储AVL版本是否正确。
采购
人员分发采购订单时,必须以最新受控文件中的AVL版本为准选择交易对象,任何电脑打印AVL只限打印当天参考。
如AVL有任何变动时,品质部必须及时通知相关部门。
5.4供应商表现评估
5.4.1供应商日常来料发生品质问题时,品质部及时向其发出SCAR ,要求进行原因分析并限期提出改善对策。
采购人员负责跟进SCAR 处理进度,品质部跟踪品质问题的改善效果并记录和关闭SCAR 。
5.4.2品质部每月根据IQC 检验结果、生产投诉不良率等对供应商品质状况分析,并对品质较差的供应商制程进行稽查,以了解其品质倾向。
如发现重大缺陷时填写《供应商纠正预防报告》交其限期改善。
5.4.3品质部每季度组织采购、IQC 、业务等部门对供应商表现进行考核后填写《供应商季度考核报告》,并根据评估结果对供应商进行等级评定。
5.4.4供应商季度考核评价项目及分数比例如下(满分100分): ①品质水平:40分 ②交期:20分 ③价格:15分 ④服务:15分
⑤产能/订货周期:10分
5.4.5供应商评分及等级评定标准如下:
①品质水平:IQC 每月根据以下项目确定每一供应商品质评分,以此衡量供应商来料质量水平:
A )来料抽检不良品率(40%)计算公式:
抽检不良品率(D )=每月抽样总数每月抽检不良品
×100%
得分=(1—D )×40%×40分 B )来料不良批数率(30%)计算公式:
不良批数率(L )=每月来料总批数每月不良批数
×100%
得分=(1—L )×30%×40分
C )生产投诉不良率(30%)计算公式:
生产投诉不良率(P )=每月生产部投诉批数
每月来料总批数×100%
得分=(1—P )×30%×40分 D )供应商每月品质总得分=A+B+C
E)供应商每季度品质得分=(每月得分总和)/3
②交期评分:采购部依订单规定交期对供应商当月各批订单交货进行评分,评分方法为:
A)准时交付得20分
B)延迟2日每批次扣2分
C)延迟3—4日每批次扣5分
D)延迟5—6日每批次扣10分
E)延迟7日以上得0分
采购部每月将同一供应商当月各批订单交货评分予以平均,得出该供应商该月交期平均分,然后再计算该供应商季度交期平均分。
③价格评分:采购部每季度根据供应商价格水平及报价评分,评分方法为:
A)报价迅速,价格具竞争力:15分
B)报价迟缓,价格尚公平:10分
C)报价迅速,价格稍偏高:8分
D)报价迟缓,价格稍偏高:5分
E)报价迟缓,价格偏高:0分
④服务评分:品质部和采购部根据供应商服务水平及解决问题的态度好坏评分。
评分方法为: A)SCAR回复时间长短评分
·回复时间为3天内8分
·回复时间为1周内6分
·回复时间为1—2周3分
·回复时间为1个月1分
·回复时间超过1个月0分
B)不良退货交换行动评分
·按期更换7分·偶尔拖延5分
.经常拖延3分·置之不理0分
⑤产能/订货周期评分:采购部根据供应商确定交货时间的长短予以评分,评分方法为: A)交期为1周10分 B)交期为1-2周8分
C)交期为3—4周6分 D)交期为5—6周3分
E)交期为6周以上1分
⑥品质部根据供应商季度考核得分总和,将供应商分级如下:
注:对于提供多种来料的供应商,取其品质水平得分之平均数决定其品质评分等级。
如总分达到等级分数要求,但质量评分达不到,则依照质量评分该供应商降一级。
5.4.6采购订单首先要与A级和B级供应商签订。
但对于独家供应或客户指定或由于其它原因短期内难以更换之D级,可由采购部提出供应商改善申请,品管、工程等部门派相应工程师协助供应商进行品质体系、生产技术等方面改善。
5.5供应商资格取消
5.5.1供应商首批来料不良时,品质部向其发出SCAR,如果连续两批来料不良且主要缺点批退时,品质部再次发出SCAR;第三批来料仍因主要缺陷批退时,品质部提出取消该供应商资格申请,经品管主管批准后(报总经理批准)将其从AVL中删除。
5.5.2品质部不定期稽核供应商制程,发现重大缺点时发出SCAR要求其改善,如第二次稽核时仍未改善则取消其供应商资格。
5.5.3供应商资格取消后,品质部应立即更新电脑中AVL,并将更新后的AVL重新审批后分发至相关部门。
6.相关文件
6.1《合格供应商名单》
6.2《供应商调查表》
6.3《供应商评估报告》
6.4《供应商改善行动要求》(SCAR)。