供应商质量管理程序
SQM供应商质量管理工作流程及内容

SQM供应商质量管理工作流程及内容1SQM供应商质量管理工作流程及内容1.0 SQM定义:SQM(Supplier Quality Management)是提升供应商品质管理的一种活动。
2.0 SQM目的:维持和改进供应商的品质保证能力,一贯提供品质符合或超越本公司要求及最终客户要求的产品。
推动供应商品质持续改善,以阻止不良,减少变异,消灭浪费。
配合本公司生产Product quality conformance , On time delivery, After-sale service, Cost management & Technology contributions3.0 SQM应用范围:所有交货本公司的供应商(制造商和代理商,制造商须应用至它的下游制造商;代理商须应用至它的制造商)。
4.0 责任:Supplier:提供符合或超越本公司要求的产品,遵守双方签定的品质合约。
R&D:零部件的Approved;SEF/ITV出版。
PE:来料不良分析,FA报告提供。
PROD:来料不良数据收集统计,来料品质异常提出。
SCM:主导新供应商的评估,定期召开Commodity Meeting,Poor Supplier处理。
SQM:推动供应商持续改善。
5.0 SQM程序:5.1 SQM Process Flow ChartPrevention----Quality assurance----Monitoring5.2 供应商品质保证(Quality Assurance)5.2.1新供应商的评估·SCM建立新供应商评估计划。
新供应商的开发及条件:A. 新机种之新类型之材料(现有的供应商无法供应之材料);B. 某现有供应商被PHASE OUT,需增补新供应商;C. 现有供应商产能不能满足本公司要求;D. 现有供应商配合不佳;E. 现有供应商制程能力不足,无法达到本公司品質要求;F. 新供應价格具竟争力;G. 某材料现有供应商数量不足(2nd Source);H. 其他认为需要开发新供应商者,如外包厂商之开发.·SCM对新供应商进行初步评估(也可进行问卷调查),准备相关资料如下表(如工厂介绍,品管组织,QC 工程图等)并确定评估日期,通知R&D、SQM等相关部门。
IATF16949程序文件26供应商管理程序

IATF16949程序文件26供应商管理程序1、目的本程序的目的在于建立一套规范、有效的供应商管理体系,以确保所采购的产品和服务符合规定的要求,从而保障公司的生产运营和产品质量。
2、适用范围本程序适用于公司所有原材料、零部件、包装材料、服务(如运输、校准、检测等)供应商的选择、评估、监控和改进。
3、职责31 采购部门负责供应商的寻找、初步筛选和联系。
组织供应商的评估和审核。
与供应商进行商务谈判,签订合同。
负责与供应商的日常沟通和协调,处理采购相关问题。
32 质量部门参与供应商的评估和审核,重点评估供应商的质量管理体系和产品质量。
负责对供应商提供的产品进行检验和测试。
提供质量改进的建议和要求给供应商。
33 技术部门参与供应商的评估和审核,重点评估供应商的技术能力和产品技术规格。
提供技术规范和要求给供应商。
协助供应商解决技术问题。
34 其他相关部门参与供应商的评估和审核,提供相关的意见和建议。
反馈供应商产品和服务在使用过程中的问题和意见。
4、供应商的选择41 供应商信息收集采购部门通过各种渠道(如网络搜索、行业推荐、展会等)收集潜在供应商的信息,包括但不限于供应商的名称、地址、联系方式、产品范围、生产能力、质量管理体系认证情况等。
42 初步筛选采购部门根据公司的需求和供应商的基本情况,对潜在供应商进行初步筛选,剔除明显不符合要求的供应商。
筛选的标准包括但不限于供应商的产品或服务是否符合公司的需求、供应商的生产能力是否能够满足公司的订单量、供应商的质量管理体系是否健全等。
43 供应商调查对通过初步筛选的供应商,采购部门发放供应商调查问卷,要求供应商如实填写其公司的基本情况、质量管理体系、生产设备、技术能力、主要客户等信息。
同时,采购部门可以要求供应商提供相关的证明文件(如质量管理体系证书、产品检测报告、营业执照等)。
44 现场考察(如有需要)对于重要的供应商或存在疑问的供应商,采购部门可以组织质量、技术等相关部门进行现场考察。
供应商管理程序-IATF16949程序

交付业绩统计
市场部
品质部
1.检验员将公司产品使用质量状况反馈品质部、市场部。
2. 市场部三包服务人员将用户使用质量状况反馈品质部、市场部。
3.品质部将到货检验情况汇总通报市场部。
5.市场部采购员需要统计供方的按时到货率、到货合格率、过程装配合格率、服务态度、超额运费等供货业绩,每月将评价结果通知供应商。
5.供应商应通过ISO9001质量体系要求或制定有相应开发计划。
《供方调查评价表》《供方现场评审表》
5.4
审批
市场部
管理者代表经理
A类产品申请需经总经理审批。 B类产品申请需经市场部负责人审核,总经理审批。
《供方调查评价表》
5.5
签订试制合同
市场部
品质部
技术部
1. 市场部向技术部申请发放相关图纸、验收标准、技术要求;
5.9
纳入合格供方
市场部
1.市场部根据供方评审的结果,对《合格供方名录》进行维护发布,并建立新供方档案,按采购产品的分类对供方进行分类管理。
2.提供A类采购产品的供方为A类供方;提供B类采购产品的供方为B类供方;提供C类采购产品的供方为C类供方;当供方同时提供多种产品时,按重要度最高的类别确定。
3.由市场部与供应商签订相关《采购合同》、《质量协议》及《环保协议书》
《潜在供应商开发建议书》
5.2
审核
市场部
市场部根据现有供应商的质量保证能力、供货保证能力、服务质量,对提交的《潜在供应商开发建议书》进行评审,做出是否采纳的意见。
5.3
评估
市场部
1.对市场部评审采纳的A、B类潜在供应商开发建议,由市场部向供应商发《供方调查评价表》由供应商填写相关信息,供应商信息返回后,由市场部组织品质部、技术部等相关部门进行评审,必要时组织现场评审。
上海通用供应商质量管理16步程序
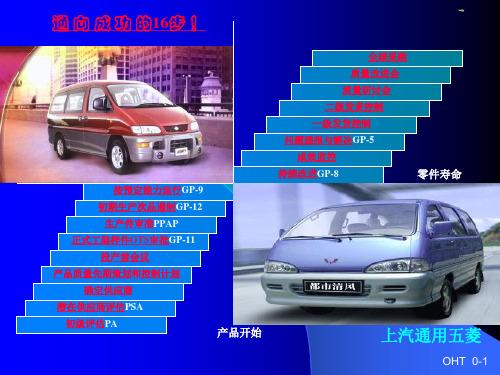
初级评估(PA / TA)
定义:在潜在供应商评估之前,对新的潜在供应商作一个初步评估,或
让供应商自我评估以确定其是否具备基本的质量体系、合适的技
术能力和良好的管理水平。
目的:通过半天的评估以确认新的潜在供应商是否有资格进行潜在供应
商评估。
范围:适用于所有被认作是潜在来源的新的供应商。
程序:A 采购员、经理或工程师进行现场评估
范围: 适用于需提供新样件的所有供应商。
程序:-由客户提供对样件的检验清单
-供应商得到有关提供样件要求的通知
-供应商得到GP-11中提出的要求
-供应商提交样件和按客户要求等级提供文件
-供应商会得到提交样件审理结果的通知:
―批准用于样车制造
―可用于样车制造
―不可用于样车制造
样件审批或工装样品(OTS)认可(GP—11)
按预定能力运行(GP—9)
定义:实地验证供应商生产工序是否有能力按照预定生产能力制造
符合质量及数量要求的产品。
目的: 通过事先进行生产的“按预定能力运行”来降低正式投产和加
速生产时失败的风险。
范围:除非由采购部门供应商质量及采购总监授权豁免以外,所有新
的零件都必须执行“按预定能力运行”。
程序:进行风险评估
OHT3-2
质量研讨会
定义:在供应商现场进行质量研讨,解决具体质量问题。
目的:尽快解决问题,使产品质量迅速提高,并建立一个具备控制和
持续改进质量的系统。
范围:可在供应商质量改进过程中任何时候进行。当某产品批量生产
不合格品PPM较高,或有反复PR/R,或受发货控制,或查访及
风险评估期间被特别指出时。
成效监控
持续改进GP-8
供应商管理程序
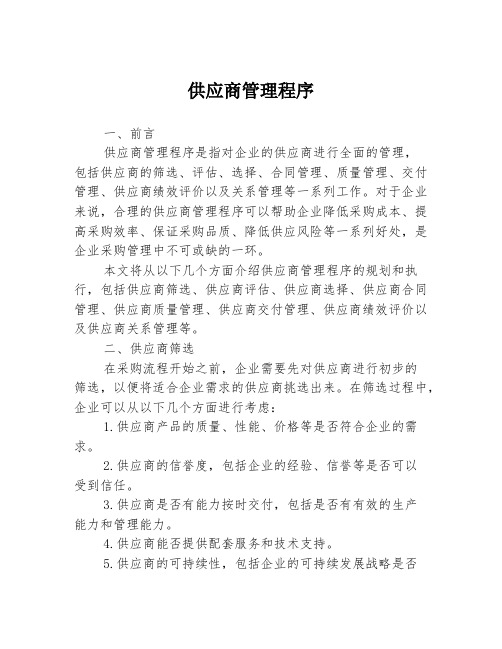
供应商管理程序一、前言供应商管理程序是指对企业的供应商进行全面的管理,包括供应商的筛选、评估、选择、合同管理、质量管理、交付管理、供应商绩效评价以及关系管理等一系列工作。
对于企业来说,合理的供应商管理程序可以帮助企业降低采购成本、提高采购效率、保证采购品质、降低供应风险等一系列好处,是企业采购管理中不可或缺的一环。
本文将从以下几个方面介绍供应商管理程序的规划和执行,包括供应商筛选、供应商评估、供应商选择、供应商合同管理、供应商质量管理、供应商交付管理、供应商绩效评价以及供应商关系管理等。
二、供应商筛选在采购流程开始之前,企业需要先对供应商进行初步的筛选,以便将适合企业需求的供应商挑选出来。
在筛选过程中,企业可以从以下几个方面进行考虑:1.供应商产品的质量、性能、价格等是否符合企业的需求。
2.供应商的信誉度,包括企业的经验、信誉等是否可以受到信任。
3.供应商是否有能力按时交付,包括是否有有效的生产能力和管理能力。
4.供应商能否提供配套服务和技术支持。
5.供应商的可持续性,包括企业的可持续发展战略是否符合企业的要求等。
在以上几个方面,企业可以制定相应的筛选标准和流程,以便挑选出适合企业的供应商。
三、供应商评估对于通过初步筛选的供应商,需要进一步进行评估,以便确定最终的供应商。
在评估过程中,企业可以从以下几个方面进行考虑:1.供应商的信誉度,包括企业的经验、信誉等是否可以受到信任。
2.供应商的财务状况,包括供应商的资本状况、流动性、盈利能力等。
3.供应商的生产能力、管理能力、运营效率等。
4.供应商的产品质量、服务质量和客户反馈等。
5.供应商的环保和社会责任等。
在评估过程中,可以采用评估表的方式进行,根据不同的标准和权重进行评估,最终得出评估结果,以便企业进行最终的供应商选择。
四、供应商选择供应商选择是供应商管理的重要环节。
在选择过程中,企业需要根据前期的筛选和评估结果,以及企业的实际需求,综合考虑供应商的产品质量、价格、交货期、售后服务等因素进行选择。
@上汽通用五菱-供应商质量管理16步程序

初期生产次品遏制程序(GP—12) 初期生产次品遏制程序(GP—12)
定义: 供应商正式生产件审批程序控制计划的加强措施, 定义 供应商正式生产件审批程序控制计划的加强措施,初期生产次 品遏制计划( 品遏制计划(GP-12)与产品先期质量策划及控制计划参考手 ) 册中的投产前控制计划是一致的。 册中的投产前控制计划是一致的。 目的: 帮助供应商验证对其工序的控制, 目的 帮助供应商验证对其工序的控制,使质量问题能迅速在供应商 现场被发现和纠正,而不影响到客户的生产线。 现场被发现和纠正,而不影响到客户的生产线。 范围:本程序适用于所有需要通过正式生产件审批程序的零件, 范围:本程序适用于所有需要通过正式生产件审批程序的零件,包括 所有小批量供货,加上采购部门指定的数量。 所有小批量供货,加上采购部门指定的数量。此程序不只限项 目的开始。 目的开始。 程序:作为质量先期策划之组成部分,供应商将制定 程序:作为质量先期策划之组成部分,供应商将制定GP-12投产前控 投产前控 制计划, 控制计划是PPAP正式生产件审批程序的要求 制计划,GP-12控制计划是 控制计划是 正式生产件审批程序的要求 之一,在达到此阶段放行标准之前必须按该计划执行。 之一,在达到此阶段放行标准之前必须按该计划执行。
投产前会议
定义:与供应商进行交流以明确零件质量合格及持续改进的要求。 定义:与供应商进行交流以明确零件质量合格及持续改进的要求。 目的: 目的:保证所有质量要求在供应商及客户负责供应商的部门之间得到 确切的交流。 确切的交流。 范围:建议对所有需要进行PPAP的新部件或新材料行使本程序,依 的新部件或新材料行使本程序, 范围:建议对所有需要进行 的新部件或新材料行使本程序 照其风险程度之不同来确定先后。 照其风险程度之不同来确定先后。(这是先期质量策划的一个部 分) 程序: 程序:通过供应商与客户有关人员在产品开发小组会议上进行密切的 交流以对质量,生产能力和进度等要求进行研讨并取得认同。 交流以对质量,生产能力和进度等要求进行研讨并取得认同。
供应商质量管理流程图:步骤详解
• 提高供应商评审和评估的准确性和有效性
降低供应链质量风险
• 建立供应商风险管理机制
• 及时发现和应对供应商质量问题
• 提高供应链的可靠性和稳定性
供应商质量管理对企业竞争力的影响
提高产品质量
降低生产成本
增强企业竞争力
• 增强产品性能和客户满意度
• 优化供应链管理,提高生产效率
⌛️
质量控制与改进
• 建立供应商的质量控制体系
• 制定供应商的质量检验标准和程序
• 促进供应商持续改进质量管理体系和产品质量
供应商质量管理体系的建立与实施
制定供应商质量管理手册
• 明确供应商质量管理的基本要求和程序
• 制定供应商质量管理的操作指南和实施细则
• 确保供应商质量管理手册符合标准和法规要求
• 流程连接:表示流程步骤之间的关联和依赖关系
供应商质量管理流程图的绘制步骤与方法
确定流程图的绘制目标
绘制流程图的框架
• 明确供应商质量管理的关键环节和流程
• 绘制顶层流程图,展示供应商质量管理的
• 确定流程图的层次结构和详细程度
整体流程
• 确定子流程图的布局和顺序
绘制流程图的细节
检查和优化流程图
• 建立良好的供应商合作关系
• 提高市场竞争力和品牌价值
• 降低不良品返工和维修费用
• 提高市场份额和品牌价值
• 降低客户投诉和退换货率
• 提高企业盈利能力
• 降低供应链风险
02
供应商的选择与评估
供应商选择的标准与依据
质量标准
• 供应商的产品质量水平
• 供应商的质量管理体系和认证
供应商质量管理流程图
合格后录入系 统,开始进入 样品阶段。
质量合作协议 签订
OK
NG
验证合后,此项改善 结束,问题关闭
直接取消备选 供应商资格
《供应商品质月报》 产品质量统计项中产 品原料检验有3批检 验不良率≥2%或产品 原料拒收≥2次时,开 具《供应商不符合报 告及验证记录》提出 整改要求并对供应商 整改措施实施效果进 行确认。
《供应商品质月报》 中成品质量统计项中 有1批检验不良率 ≥2%或产品退货≥1次; 时,开具《供应商不 符合报告及验证记录》 提出整改要求并对供 应商整改措施实施效 果进行确认。
优秀供应商 不合格供应商
收集供应商纠正预 防措施,并审核, 审核通过后进行纠 正预防措施验证。
对不合格供应商 进行质量辅导, 考核为D的供应 商暂停下单,待
验证纠正
连续出现3个批次的 同一种产品出货检验 合格率≤98%时,开 具《供应商不符合报 告及验证记录》提出 整改要求并对供应商 整改措施实施效果进 行确认。
做好样品和小批量 确认,明确质量标 准,固化产品工艺
识别好关键过程和 特种工序,做好过 程SPC统计分析。
关键物料生产时, 做好现场技术质量 支持,必要时安排 驻厂人员及时跟踪 确认产品质量
依据审核准则的评 分标准,给出质量 系统评价意见和得
分
确保产品各项 指标满足公司 要求和客户需
要
供应商月度质量数据、 市场产品质量数据统 计
新供应商开发认证(质量)
供应商质量日常管理
供应商质量管理流程图
供应商质量绩效考核
供应商审核
供应商质量改善
依据资源需求, 品质部门做好供 应商前期开发和 认证前准备工作
品质部门安排资 深供应商质量管 理工程师参与现
供应商质量管理流程
以下是一般的供应商质量管理流程:
1.制定质量标准:明确采购物品的质量要求,包括技术规格、性能
指标、检验标准等。
2.选择供应商:根据质量标准选择合适的供应商,可以通过招标、
评估、审核等方式进行。
3.签订合同:与供应商签订合同,明确质量要求、交货期、价格、
售后服务等条款。
4.质量检验:对采购物品进行检验,包括进货检验、生产过程检验、
成品检验等,确保符合质量标准。
5.建立质量档案:记录供应商的质量表现,包括检验结果、投诉处
理、质量改进等信息。
6.供应商评估:定期评估供应商的质量表现,根据评估结果采取相
应的措施,如奖励优秀供应商、督促改进不足之处、淘汰不合格供应商等。
7.持续改进:与供应商合作,共同改进质量,提高采购物品的质量
水平。
供应商质量管理流程图
同意 不同意
信息反馈供应商管 部,从系统中注销 供应商资格。
进行高层沟通,组 建辅导团队,再次 进行质量辅导
SQE 审核报 告并验证改 善措施效果
OK
NG
验证合格后,此 项改善结束,问 题关闭
直接取消备选 供应商资格
月来料合格率低于 80%(总批数大于 10批),SQE开具 VCAR
优秀供应商 不合格供应商
收集供应商纠正预 防措施,并审核, 审核通过后进行纠 正预防措施验证。
对不合格供应商 进行质量辅导, 考核为D的供应
验证纠正
来料质量在某时期 内表现非常差,进 行系统质量改善辅 导,SQE 开出系统 改善的项目点和提 出具体质量目标
新供应商开发认证(质量) 供应商质量日常管理
供应商质量管理流程图
供应商质量绩效考核
供应商审核
供应商质量改善
依据资源需求, 供应商管理部做 好供应商前期开 发和认证前准备 工作
质量部门安排 资深供应商质 量管理工程师 参与现场认证
依据审核准则 要求全面、客 观评价新供应评价意见和得 分
依据PO 信息,提 前沟通,让其充 分理解产品技术 质量要求
做好样品和小批 量确认,明确质 量标准,固化产
识别好关键过程 和特种工序,做 好过程SPC 统计
关重物料和紧急 物料生产时,做 好现场技术质量 支持,需要时安 排驻厂人员及时 跟踪确认产品质 量
确保来料质 量满足要求 和客户需要, 各项考核指 标达到年度
统计供应商月度来料 质量数据(LAR,上线 DPPM,VCAR回复情况, 样品认证情况)
依据供应商月度评分 准则(质量部分),对 供应商月度来料进行 评分.
- 1、下载文档前请自行甄别文档内容的完整性,平台不提供额外的编辑、内容补充、找答案等附加服务。
- 2、"仅部分预览"的文档,不可在线预览部分如存在完整性等问题,可反馈申请退款(可完整预览的文档不适用该条件!)。
- 3、如文档侵犯您的权益,请联系客服反馈,我们会尽快为您处理(人工客服工作时间:9:00-18:30)。
供应商质量管理程序
一、目的
对供应商提供的外购件、外协件、进口件进行质量管控,确保采购的产品能够持续满足生产需求。
二、适用范围
本质量管理程序仅适用于为我司提供材料配件的供应商的品质异常控制。
三、职责
1、质量管理中心负责对来料件进行产品的质量检验,品质的异常处理,并负责配合采购部门实施对供应商选择和评价;
2、采购部门负责对供应商的选择、评价、考核管理,按季/年度组织供应商业绩评鉴、督促、供应商品质整改。
3、工程项目管理中心负责将材料送至质量管理中心验收抽检,并及时反馈材料不良信息。
4、仓库负责入库材料的验收、库存管理和不良品标识等。
5、生产管理中心负责制程在线材料(原材料、外购件、外协件、进口件)不良信息的反馈、退库办理,配合不良品的处理。
四、管理要求
1、材料(原材料、外购件、外协件、进口件)品质异常发现和处理
①来料检验,经质量管理中心依据图纸,材料国家(行业)标准以及《来料检验指导书》抽检判定为不合格品时,由质量部门作出处理意见,并经部门领导批准执行处理方式:筛选、拒收、让步接收、返工、退货。
②生产部在制造过程中发现材料(原材料、外购件、外协件、进口件)品质不良时,反馈给质量管理中心查实并提出处理意见,经生产部领导确认执行。
在线材料(原材料、外购件、外协件、进口件)处理方式:筛选、让步接受、返工、退货。
2、供应商品质不良的处置和索赔
①当发现供应商材料(原材料、外购件、外协件、进口件)品质不良时,质量部门应将不良材料标识、隔离,在线不良品时,还应立即通知仓库冻结、标识和隔离不良材料;
②质量管理中心应将不良信息立即反馈给采购部,重大批量不良时,采购部必须通知供应商两个工作日内到公司确认解决。
③供应商对品质异常的处理时限:收到投诉两个工作日必须书面回复解决方案。
④供应商材料不良的索赔和处罚:
A、批量不良材料让步使用特采时,涉及功能性不良材料的特采批,扣除当批货款
的10%,外观不良的特采批,扣除当批货款的5%;
B、生产、安装在线材料批不良:需要公司生产或安装人员100%筛选或返工,所
发生给用由供应商承担,人员费按小时计;
C、供应商经多道工序加工后发现批量品质不良,所造成的加工材料等损失,由供
应商承担;
D、供应商材料品质不良造成工程投诉,索赔等严重后果,相关损失由供应商承担;
E、供应商不守诚信,不按我司质量整改要求进行改善,连续三批重复提交同类品
质不良产品,零星产品以XXX-XXX元处罚,批量不良处以XXXX-XXXX元处罚。
⑤质量索赔的执行:由质量部填写《质量不良索赔通知单》,附加《投诉/退货通知单》,损失计核单据等,交采购部送于供应商签章。
⑥供应商将签章后的索赔单扫描或快递至采购部,由采购部把索赔单发放至质量管理中心和财务室,由财务室扣除其款项。
3、供应商的质量考评
①质量管理中心通过产品管理体系负责对来料的不良数据,与客户反馈的一些不良信息进行汇总,当作为供应商的质量不良信息的考评。
②采购部通风《供应商管理程序》定期组织对其供应商进行考评,质量管理中心负责提供其质量不合格信息进行考评,评分标准如下:
A、供应商当月质量评比低于95%,按每降低1%扣两分的标准计算;
B、生产部、项目管理部在线材料轻微不良,每次扣2分;在制作过程中重大不良,
造成(返工、停产现象)每次扣5分。
C、客户投诉不良信息,每次扣10分;
D、不按规定时间回复投诉每次扣2分,不按规定整改、重复提交不合格每次扣5
分;
E、供应商不按时提供原材料和材质分析资料,生产部、项目部投诉一次扣2分。
③在供应商业绩考评中,服务、交期、成本项目按《供应商管理程序》进行考评。
4、考评分级及供应商动态管理
②采购部根据供应商(月/季度)考评进行供应商分级管理,计划成本室根据考核信息对供应商下达的任务进行分配和监督。
③连续两(月/季度)考评为C级供应商,计划成本室停止对其下达计划,列入淘汰供应商名单,重新选择新的供应商。
④评定为D级供应商,计划成本室停止对其下达计划,采购部门应立即报告给公司总经理,同时选择新的供应商为之将其替代。
⑤被淘汰的供应商经重新质量整改后,由采购部和质量管理中心进行重新评估合格后,方可以选择其为进入我公司供应商之列。
⑥本供应商质量管理程序由发布之后生效。
附加《供应商质量不良索赔评估通知单》
供应商质量不良索赔评估通知单
编号:。