弯曲模,拉伸模的基本基础原理
基础实验-塑料弯曲强度-实验讲义
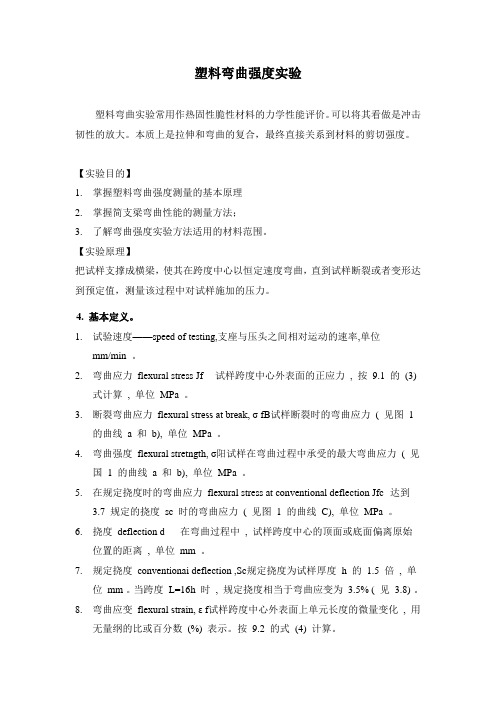
塑料弯曲强度实验塑料弯曲实验常用作热固性脆性材料的力学性能评价。
可以将其看做是冲击韧性的放大。
本质上是拉伸和弯曲的复合,最终直接关系到材料的剪切强度。
【实验目的】1.掌握塑料弯曲强度测量的基本原理2.掌握简支梁弯曲性能的测量方法;3.了解弯曲强度实验方法适用的材料范围。
【实验原理】把试样支撑成横梁,使其在跨度中心以恒定速度弯曲,直到试样断裂或者变形达到预定值,测量该过程中对试样施加的压力。
4. 基本定义。
1.试验速度——speed of testing,支座与压头之间相对运动的速率,单位mm/min 。
2.弯曲应力flexural stress Jf 试样跨度中心外表面的正应力, 按9.1 的(3)式计算, 单位MPa 。
3.断裂弯曲应力flexural stress at break, σ fB试样断裂时的弯曲应力( 见图1的曲线 a 和b), 单位MPa 。
4.弯曲强度flexural stretn gth, σ阳试样在弯曲过程中承受的最大弯曲应力( 见国 1 的曲线 a 和b), 单位MPa 。
5.在规定挠度时的弯曲应力flexural stress at conventional deflection Jfc 达到3.7 规定的挠度sc 时的弯曲应力( 见图1 的曲线C), 单位MPa 。
6.挠度deflection d 在弯曲过程中, 试样跨度中心的顶面或底面偏离原始位置的距离, 单位mm 。
7.规定挠度conventionai deflection ,Sc规定挠度为试样厚度h 的1.5 倍, 单位mm 。
当跨度L=16h 时, 规定挠度相当于弯曲应变为 3.5% ( 见 3.8) 。
8.弯曲应变flexural strain, ε f试样跨度中心外表面上单元长度的微量变化, 用无量纲的比或百分数(%) 表示。
按9.2 的式(4) 计算。
9.断裂弯曲应变flexural strain at break , 如试祥断裂时的弯曲应变( 见图1的曲线 a 和b) 。
三种杨氏模量测量方法比较

三种杨氏模量测量方法比较周晓明【摘要】The measuring methods of young's modulus in college physics experimental teaching are compared,and the main errors are analyzed.According to their characteristics and the aspect of cultivating student's innovative capability through physics experimental teaching,some beneficial teaching suggestions of measuring methods of young's modulus are put forward in combining the teaching reform practice.%对大学物理实验课程中三种杨氏模量测量方法进行了比较,分析了其主要误差来源。
根据各种测量方法的特点,从通过实验教学培养学生综合能力的角度,结合教改实践给出了杨氏模量测量实验教学的若干参考建议。
【期刊名称】《实验科学与技术》【年(卷),期】2011(009)006【总页数】3页(P97-99)【关键词】杨氏模量;误差来源;教学建议【作者】周晓明【作者单位】华南理工大学物理学院,广州510640【正文语种】中文【中图分类】G642.423;O4-33杨氏模量是表征固体材料弹性形变性质的基本力学参数,也是工程设计中选择机械构件的一个重要依据,杨氏模量测定在科学研究和技术应用中都具有重要意义。
测量杨氏模量的方法有很多,如拉伸法、梁弯曲法、百分表法、光杠杆法、干涉条纹法、共振法等,每种方法各有其特点,适合不同的测试条件。
在大学物理实验中,固体材料杨氏模量的测量是理工科院校物理实验中必做实验之一,很多高校开设了用不同方法测量杨氏模量的多个实验,构成具有相对独立性的一个实验项目子系列。
塑料橡胶 拉伸试验步骤(目的原理步骤结果处理)
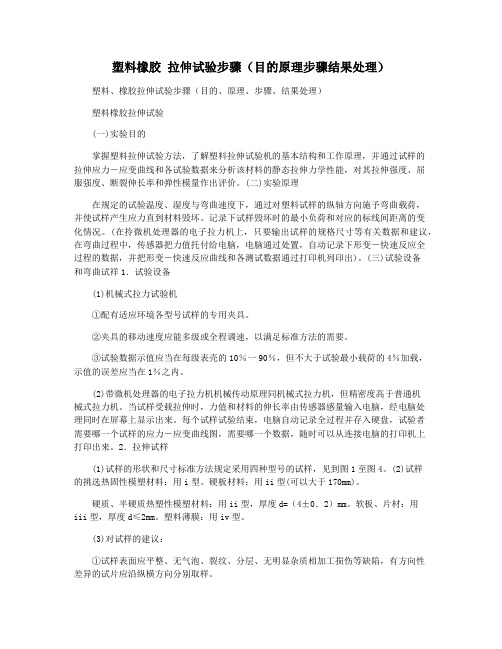
塑料橡胶拉伸试验步骤(目的原理步骤结果处理)塑料、橡胶拉伸试验步骤(目的、原理、步骤、结果处理)塑料橡胶拉伸试验(一)实验目的掌握塑料拉伸试验方法,了解塑料拉伸试验机的基本结构和工作原理,并通过试样的拉伸应力―应变曲线和各试验数据来分析该材料的静态拉伸力学性能,对其拉伸强度、屈服强度、断裂伸长率和弹性模量作出评价。
(二)实验原理在规定的试验温度、湿度与弯曲速度下,通过对塑料试样的纵轴方向施予弯曲载荷,并使试样产生应力直到材料毁坏。
记录下试样毁坏时的最小负荷和对应的标线间距离的变化情况。
(在拎微机处理器的电子拉力机上,只要输出试样的规格尺寸等有关数据和建议,在弯曲过程中,传感器把力值托付给电脑,电脑通过处置,自动记录下形变―快速反应全过程的数据,并把形变―快速反应曲线和各测试数据通过打印机列印出)。
(三)试验设备和弯曲试祥1.试验设备(1)机械式拉力试验机①配有适应环境各型号试样的专用夹具。
②夹具的移动速度应能多级或全程调速,以满足标准方法的需要。
③试验数据示值应当在每级表壳的10%一90%,但不大于试验最小载荷的4%加载,示值的误差应当在1%之内。
(2)带微机处理器的电子拉力机机械传动原理同机械式拉力机,但精密度高于普通机械式拉力机。
当试样受载拉伸时,力值和材料的伸长率由传感器感量输入电脑,经电脑处理同时在屏幕上显示出来。
每个试样试验结束,电脑自动记录全过程并存入硬盘,试验者需要哪一个试样的应力―应变曲线图,需要哪一个数据,随时可以从连接电脑的打印机上打印出来。
2.拉伸试样(1)试样的形状和尺寸标准方法规定采用四种型号的试样,见到图1至图4。
(2)试样的挑选热固性模塑材料:用i型。
硬板材料:用ii型(可以大于170mm)。
硬质、半硬质热塑性模塑材料:用ii型,厚度d=(4±0.2)mm。
软板、片材:用iii型,厚度d≤2mm。
塑料薄膜:用iv型。
(3)对试样的建议:①试样表面应平整、无气泡、裂纹、分层、无明显杂质相加工损伤等缺陷,有方向性差异的试片应沿纵横方向分别取样。
模具设计与制造基础复习题

模具设计与制造基础复习题1.模具是成形制品或零件生产的重要工艺装备。
2.冲压模具:在冲压加工中,将材料(金属或非金属)加工成冲件(或零件)的专门工艺设备,称为冲压模具。
曲柄压力机技术参数:滑块行程、滑块行程次数、公称压力、闭合高度、工作台尺寸和滑块底面尺寸、模柄孔尺寸。
3.合理的冲压成形工艺、模具、冲压设备是必不可少三要素。
4.冲压加工可分为分离工序和成形工序两类。
5.分离工序:被加工材料在外力作用下,因分离而形成一定形状和尺寸的加工方法。
6.成形工序:被加工材料在外力作用下,因产生塑性变形,从而得到一定形状和尺寸的加工方法。
7.分离工序要紧有冲孔、落料、切断等8.成形工序要紧有弯曲、拉深、翻边、胀形等9.冲压模具依照工艺性质分类有(1)冲裁模;(2)弯曲模;(3)拉深模;(4)其他成形模。
10.冲压模依照工序组合程度分类有(1)单工序模;(2)复合模;(3)连续模。
单工序模:在压力机的一次行程中,只完成一道工序的冲裁模。
复合模:在压力机的一次行程中,在模具的不同部位上同时完成数道冲压工艺的模具连续模:在压力机的一次行程中,在模具的同一位置完成两道以上的工序的模具。
11.压工艺对材料的差不多要求是:(1)对冲压性能的要求;(2)对表面质量的要求;(3)对材料厚度公差的要求。
12.冲压常用的材料有黑色金属、有色金属、非金属材料。
1*:中性层:弯曲变形前后长度保持不变的金属层或弯曲变形时切向应力变为零的金属层。
13.冲裁过程大致可分为三个时期:(1)弹性变形时期;(2)塑性变形时期;(3)断裂时期.14.冲裁件的尺寸精度要紧决定于凸模和凹模的刃口尺寸精度.15.在确定凸凹模刃口尺寸必须遵循下述原则:(1)设计落模料时,先确定凹模刃口尺寸,以凹模为基准,间隙取在凸模上,即冲裁间隙通过减小凸模刃口尺寸来取得。
设计冲孔模时,先确定凸模刃口尺寸,以凸模为基准,间隙取在凹模上,即冲裁间隙通过增大凹模刃口尺寸来取得。
拉伸强度、拉伸模量、弯曲强度的单位

拉伸强度、拉伸模量、弯曲强度是材料力学性能的重要指标,它们可以评价材料的抗拉和抗弯能力。
在工程实践中,正确理解并使用这些指标对于材料选择和设计具有重要意义。
本文将分别介绍拉伸强度、拉伸模量和弯曲强度的单位以及其在工程中的应用。
1. 拉伸强度的单位拉伸强度是材料在拉伸过程中抵抗断裂的能力,它是材料的重要力学性能指标之一。
拉伸强度的单位通常使用帕斯卡(Pa)来表示,1Pa 等于1牛顿/平方米。
在工程中,常使用兆帕(MPa)作为拉伸强度的单位,1MPa等于10^6Pa。
2. 拉伸模量的单位拉伸模量是材料受拉力时的应变和应力之间的比值,它可以衡量材料的刚性和变形能力。
拉伸模量的单位通常也是帕斯卡(Pa),在工程中常使用兆帕(MPa)或千兆帕(GPa)作为拉伸模量的单位。
3. 弯曲强度的单位弯曲强度是材料在受弯曲作用时抵抗断裂的能力,它可以评价材料在弯曲应力下的表现。
弯曲强度的单位同样是帕斯卡(Pa),在工程中常使用兆帕(MPa)来表示。
以上是拉伸强度、拉伸模量和弯曲强度的单位,它们是描述材料力学性能的基本指标。
在工程设计和材料选择时,我们需要根据实际应用需求合理选择材料,并且理解和运用这些指标对于提高工程质量和安全性具有重要意义。
希望本文对于读者们加深对以上指标的理解有所帮助。
拉伸强度、拉伸模量和弯曲强度作为材料力学性能的重要指标,在工程实践中扮演着至关重要的角色。
它们不仅在材料选择和设计中起着决定性作用,还对产品的质量和可靠性产生深远影响。
本文将继续深入探讨拉伸强度、拉伸模量和弯曲强度的相关知识,以便读者更全面地了解和运用这些指标。
4. 拉伸强度的应用拉伸强度是材料在拉伸过程中所能承受的最大应力,它直接影响材料的拉伸性能和断裂特性。
高拉伸强度的材料意味着在受拉力作用下具有更好的抗拉性能,能够更好地承受外部拉伸力的作用。
拉伸强度是评价材料抗拉性能的重要参数,广泛应用于航空航天、汽车制造、建筑结构等领域。
常用冲压工艺基本原理

常用冲压工艺基本原理冲压工艺是一种通过冲压设备将金属或非金属材料加工成所需形状的加工方法。
它广泛应用于制造行业中,如汽车制造、航空航天、电子等领域。
常用冲压工艺的基本原理如下:1.冲裁:冲裁是冲压工艺的基础,通过在金属材料中施加剪切力,将材料分离成所需的形状。
冲裁要求冲压设备具有足够的压力和刚度,以确保能够将材料切割成准确的形状,并保持相对平整的边缘。
2.弯曲:弯曲是将金属材料弯曲成所需的形状。
通过将材料置于折弯模具中,并施加压力使其弯曲。
弯曲要求冲压设备具有足够的刚度,以确保能够在材料上施加足够的压力,并保持所需的形状。
3.拉伸:拉伸是将金属材料拉伸成所需的形状。
通过将材料固定在一端,然后通过施加拉力来延长材料并形成所需的形状。
拉伸要求冲压设备具有足够的拉力和刚度,以确保能够在材料上施加足够的拉力,并保持所需的形状。
4.成形:成形是将金属材料压制成所需的形状。
通过在材料表面施加压力,使其逐渐变形成所需的形状。
成形要求冲压设备具有足够的压力和灵活性,以确保能够在材料上施加足够的压力,并保持所需的形状。
5.切削:切削是将金属材料切割成所需形状的方法。
通常采用冲床、剪切机等设备,在材料上施加切割力,将材料切断成准确的形状。
切削要求冲压设备具有足够的切削力和刚度,以确保能够将材料切割成准确的形状,并保持相对平整的边缘。
6.模具设计:模具是冲压工艺中不可缺少的工具,它影响着冲压加工的质量和效率。
模具设计要求考虑材料的物理特性、形状复杂程度以及生产要求等因素,以确保能够精确加工出所需的形状,并保持高效的生产速度。
综上所述,常用冲压工艺的基本原理包括冲裁、弯曲、拉伸、成形、切削和模具设计等。
这些原理在冲压加工中起着重要的作用,决定了加工质量和效率。
因此,工程师在进行冲压加工时需要充分理解和应用这些基本原理,以确保能够获得满足生产要求的加工零件。
五金模具结构基础介绍(中英文)

作用:垫冲子及入子,防止冲子尾部挤压伤模座,增加模具高度
模具结构:
外限位(限位作用) Stop block
挂钩(悬挂脱料板) Retainer
键(模板的定位) Key
夹板(固定冲头) Punch holder
模具结构:
切边冲头 Trim punch
字印冲头 Marking 折弯冲头 Bending punch
模具结构:
上模座 punch set Upper die shoe
起吊环 Handing Lifting ring
下模座 Die set/ lower die shoe
作用:起支撑和固定作用,安装外导柱(主导柱引导)
模具结构:
上垫板 Punch pad Upr padding block
下垫板 die pad Lwr padding block
切边冲头(安装顶针,防止废料粘冲头)
模具结构:
脱料板 Stripper plate
作用:脱料作用、压料作用(安装内导柱,插针)
模具结构:
起始线-料带第一次送料的位臵(防止 多,少送导致废料留至模面) Startline 下浮板即抬料板(抬料,送料作用) Elevation table
导料板(材料送料导向)
上垫脚 UPR Parellel
上托板 Top Plate
上垫板Punch pad UPR padding block
脱料板Strippe下浮板 Elevation ta
下模板 Die holder/l
下垫板 die pad/lwr pa
下模座Die set/lwr die 下垫脚Lwr parellel 垫板:backup plate/ sub-plate/ enhancer 下托板 Bottom plate
弯曲模具的基本原理
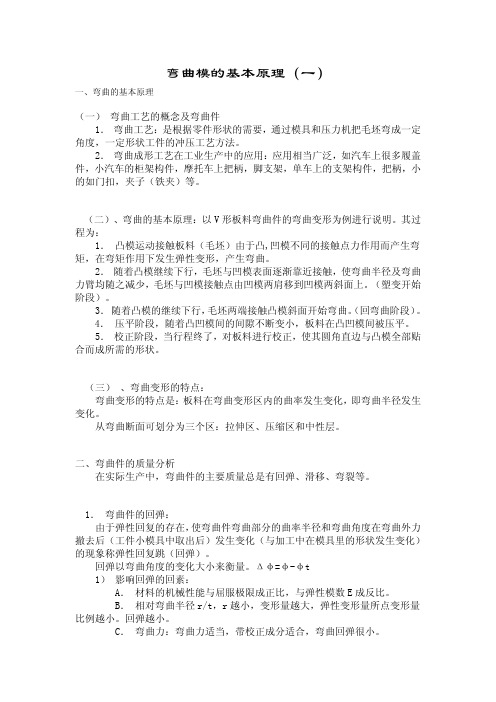
弯曲模的基本原理(一)一、弯曲的基本原理(一) 弯曲工艺的概念及弯曲件1. 弯曲工艺:是根据零件形状的需要,通过模具和压力机把毛坯弯成一定角度,一定形状工件的冲压工艺方法。
2. 弯曲成形工艺在工业生产中的应用:应用相当广泛,如汽车上很多履盖件,小汽车的柜架构件,摩托车上把柄,脚支架,单车上的支架构件,把柄,小的如门扣,夹子(铁夹)等。
(二)、弯曲的基本原理:以V形板料弯曲件的弯曲变形为例进行说明。
其过程为:1. 凸模运动接触板料(毛坯)由于凸,凹模不同的接触点力作用而产生弯矩,在弯矩作用下发生弹性变形,产生弯曲。
2. 随着凸模继续下行,毛坯与凹模表面逐渐靠近接触,使弯曲半径及弯曲力臂均随之减少,毛坯与凹模接触点由凹模两肩移到凹模两斜面上。
(塑变开始阶段)。
3. 随着凸模的继续下行,毛坯两端接触凸模斜面开始弯曲。
(回弯曲阶段)。
4. 压平阶段,随着凸凹模间的间隙不断变小,板料在凸凹模间被压平。
5. 校正阶段,当行程终了,对板料进行校正,使其圆角直边与凸模全部贴合而成所需的形状。
(三) 、弯曲变形的特点:弯曲变形的特点是:板料在弯曲变形区内的曲率发生变化,即弯曲半径发生变化。
从弯曲断面可划分为三个区:拉伸区、压缩区和中性层。
二、弯曲件的质量分析在实际生产中,弯曲件的主要质量总是有回弹、滑移、弯裂等。
1. 弯曲件的回弹:由于弹性回复的存在,使弯曲件弯曲部分的曲率半径和弯曲角度在弯曲外力撤去后(工件小模具中取出后)发生变化(与加工中在模具里的形状发生变化)的现象称弹性回复跳(回弹)。
回弹以弯曲角度的变化大小来衡量。
Δφ=φ-φt1) 影响回弹的回素:A. 材料的机械性能与屈服极限成正比,与弹性模数E成反比。
B. 相对弯曲半径r/t,r越小,变形量越大,弹性变形量所点变形量比例越小。
回弹越小。
C. 弯曲力:弯曲力适当,带校正成分适合,弯曲回弹很小。
D. 磨擦与间隙:磨擦越大,变形区拉应力大,回弹小。
凸、凹模之间隙小,磨擦大,校正力大,回弹小。
- 1、下载文档前请自行甄别文档内容的完整性,平台不提供额外的编辑、内容补充、找答案等附加服务。
- 2、"仅部分预览"的文档,不可在线预览部分如存在完整性等问题,可反馈申请退款(可完整预览的文档不适用该条件!)。
- 3、如文档侵犯您的权益,请联系客服反馈,我们会尽快为您处理(人工客服工作时间:9:00-18:30)。
弯曲模的基本原理(一)一、弯曲的基本原理(一)弯曲工艺的概念及弯曲件1.弯曲工艺:是根据零件形状的需要,通过模具和压力机把毛坯弯成一定角度,一定形状工件的冲压工艺方法。
2.弯曲成形工艺在工业生产中的应用:应用相当广泛,如汽车上很多履盖件,小汽车的柜架构件,摩托车上把柄,脚支架,单车上的支架构件,把柄,小的如门扣,夹子(铁夹)等。
(二)、弯曲的基本原理:以V形板料弯曲件的弯曲变形为例进行说明。
其过程为:1.凸模运动接触板料(毛坯)由于凸,凹模不同的接触点力作用而产生弯短矩,在弯矩作用下发生弹性变形,产生弯曲。
2.随着凸模继续下行,毛坯与凹模表面逐渐靠近接触,使弯曲半径及弯曲力臂均随之减少,毛坯与凹模接触点由凹模两肩移到凹模两斜面上。
(塑变开始阶段)。
3.随着凸模的继续下行,毛坯两端接触凸模斜面开始弯曲。
(回弯曲阶段)。
4.压平阶段,随着凸凹模间的间隙不断变小,板料在凸凹模间被压平。
5.校正阶段,当行程终了,对板料进行校正,使其圆角直边与凸模全部贴合而成所需的形状。
(三)、弯曲变形的特点:弯曲变形的特点是:板料在弯曲变形区内的曲率发生变化,即弯曲半径发生变化。
从弯曲断面可划分为三个区:拉伸区、压缩区和中性层。
二、弯曲件的质量分析在实际生产中,弯曲件的主要质量总是有回弹、滑移、弯裂等。
1.弯曲件的回弹:由于弹性回复的存在,使弯曲件弯曲部分的曲率半径和弯曲角度在弯曲外力撤去后(工件小模具中取出后)发生变化(与加工中在模具里的形状发生变化)的现象称弹性回复跳(回弹)。
回弹以弯曲角度的变化大小来衡量。
Δφ=φ-φt1)影响回弹的回素:A.材料的机械性能与屈服极限成正比,与弹性模数E成反比。
B.相对弯曲半径r/t,r越小,变形量越大,弹性变形量所点变形量比例越小。
回弹越小。
C.弯曲力:弯曲力适当,带校正成分适合,弯曲回弹很小。
D.磨擦与间隙:磨擦越大,变形区拉应力大,回弹小。
凸、凹模之间隙小,磨擦大,校正力大,回弹小。
E.弯曲件的形状:弯曲部分中心角越大,弹性变形量越大,回弹大,形状越复杂,回弹时各部分相应牵制,回弹小。
2)回弹值的确定,可查表。
3)减小回弹的措施:A.从工件设计上采取措施。
a). 加强筋的设计b). 材料的选用:选用弹性模数大,屈服极限小,机械性能稳定的材料。
B.工艺措施a). 采用校正弯曲,增加弯曲力b). 冷作硬化材料,弯曲前进行退火,降低屈服极限。
c). 加热弯曲d). r/t>100用拉深弯曲C.模具结构上采取措施。
a).r>t时,V形弯曲可在凸模上减去一个回弹角,U形弯曲可将凸模壁作出等于回弹角的倾斜角或将凸模顶面做成弧面。
b).减小凸模与工件的接触区,使压力集中于角部。
c). U形件可以采用较少的间隙。
2.弯曲件的弯裂弯曲件变形区外边是拉伸区,当此区的拉应力超出材料的应力极限时(强度极限)就产生裂纹。
弯曲件的相对弯曲半径r/t越小,则变形越大,越易拉裂。
3.弯曲件的滑移由于毛坯与模具之间磨擦的存在,当磨擦力不平衡时造成毛坯的移位,称作滑移,使弯曲件的尺寸达不到要求:1)产生滑移的原因:由于两边磨擦力不等。
A.工作不对称,毛坯两边与凹模接触面不相等。
B.凹模两边的边缘圆角半径不相等,半径小,磨擦力更大。
C.两边折弯的个数不一样。
D. V形弯曲中凹模不是中心对称,角度小的一边正压力大,磨擦大E.凹模两边的间隙和润滑情况不一样。
2)防止滑移的措施A.尽可能采用对称凹模,边缘圆角相等,间隙均匀。
B.采用弹性顶件装置的模具结构。
C.采用定位销的模具结构。
4.补充内容:A.弯曲可以压力机上进行,亦可以专用的弯曲机械弯曲设备上进行。
B.弯曲分自由弯曲和校正弯曲:自由弯曲是指当弯曲终了时,凸模、毛坯和凹模三者吻合后就不再下压。
校正弯曲是指三者吻合后继续下压,对工件起校正作用,产生进一步的塑变。
弯曲模的基本原理(二)三、弯曲件的工艺性:对弯曲件工艺性影响最大的是弯曲半径,弯曲件的几何形状,材料的机械性能及尺寸精度。
1.最小弯曲半径:在保证外层纤维不发生破坏的条件下,所能弯曲零件内表面的最小圆角半径,称作弯曲件的最小弯曲半径,表示弯曲时的成形极限。
最小弯曲半径的影响因素:A. 材料的机械性能。
B. 弯曲线的方向:由于板料的扎制造成板料性能和各项异性,扎制方向塑性较好,使弯曲的切向变形方向与扎制方向一致。
C. 板料宽度:宽度加大,最小弯曲半径增大。
D. 板料的表面质量。
E. 弯曲角。
F. 板料的厚度。
2.弯曲件直边高度弯曲件的弯曲边高度不宜太小,h>R+2t,如弯曲边高度太小,则难以形成足够的弯矩。
3.阶梯形弯曲件的弯曲。
阶梯毛坯进行弯曲时,在阶梯根部易产生裂纹,需把阶梯根部设计在弯曲变形区之外,或采用切槽的方法。
4.弯曲件的孔边距。
如果预先冲出的孔位于板料的弯曲变形区,则弯曲后孔要发生变形,要把孔设计在弯曲变形区以外。
孔壁与弯曲半径r中心的距离Z与板料厚度有关。
t=<2mm,L>=tt>=2mm,L>=2t弯曲模的基本原理(三)四、弯曲毛坯的尺寸计算弯曲零件毛坯展开尺寸具体计算的程序是:先将零件划分成直线和圆角的各个不同单元体。
直线部分的长度不变,而弯曲的圆角部分长度则需要考虑材料的变形和应变中性层的相对移动。
故整个毛坯的展开尺寸应等于弯曲零件各部分长度的总和。
ρ=R+kt其中k是中性层位移系数,与r/t有关。
1.有圆角半径的弯曲r>0.5t的弯曲件即称有圆角半径的弯曲件。
由于弯曲部分变薄不严重及断面畸变较小,所以可按中性层展开长度等于毛坯长度的原则,求得毛坯尺寸。
L=ΣlE+ΣlwL----弯曲件毛坯长度;ΣlE----弯曲件各直线段之各;Σlw-各弯曲部分的展开长度之和。
Lw=πα/180°(γ+kt)其中:α-弯曲中心角k---中性层位移系数。
2.无角半径的弯曲、、无圆角半径或圆角半径很小(r<0.5t)的弯曲件,其毛坯尺寸是根据毛坯与制件体积相等,并考虑到在弯曲时材料变薄的情况而求得的。
在这种发问下,毛坯长度等于各直线长度之各再加上弯角处的长度,即:L=ΣlE+kntL-毛坯总长度ΣlE--各直线段长度之和;n-弯角数目t-材料厚度k-系数,取0.2~0.5。
3.铰链式弯曲件铰链式弯曲件毛坯展开长度的计算和一般弯曲件尺寸计算相似,所不同的只是中性层由材料厚度中间向弯曲外层移动。
毛坯展开长度可按下式:L=1.5πρ+R+l其中ρ=R+ktk-系数。
五、弯曲力的计算弯曲力是设计冲压工艺过程和选择设备的重要依据之一。
弯曲力的大小与毛坯尺寸、零件形状、材料的机械性能、弯曲方法和模具结构等多种因素有关。
弯曲力急剧上升部分表示由自由弯曲到接触弯曲转化为校正弯曲的过程。
1.自由弯曲力的计算:P=kbt2/(rp+t)* σbσb-材料抗拉强度rp -凸模圆角半径;b-弯曲线长度;t-材料厚度;k-系数2.校正弯曲时的弯曲力的计算:P=F*qP-校正弯曲力;F-校正部分投影面积;q-单位校正力。
3.顶件力和压料力对于设有顶件装置或压料装置的弯曲模,其顶件力或压料力Q值可近似取自由弯曲力的30~80%。
弯曲模的基本原理(四)六、弯曲件的工序安排确定弯曲件的制造工艺时,先要分析研究从毛坯到成品需要几道工序。
工序安排的一般原则是先弯外角后弯内角,后次弯曲不影响前次弯曲部分的变形和前次弯曲必须考虑到后次弯曲时有合适的定位基准。
工序安排尽量做到在满足工件精度质量要求前提下使工序次数少,模具结构简单,操作方便,产量高,废品率低。
弯曲件工序安排的一般方法是:1.对于形状简单的弯曲件,如V形、U形、Z形等件,可以采用一次压弯成形。
2.对于形状复杂的弯曲件,一般需要采用二次或多次压弯成形。
3.对称弯曲。
即工件本身带有单面几何形状的弯曲,在拟定工艺方案时,应尽量成对弯曲,然后再切开。
4.加连接带弯曲。
当弯曲工件其边缘部分有缺口时,如直接连同缺口也冲出,必然发生叉口现象,严重时将无法成形,遇此情况时必须加添连接带将缺口连接在一起,待弯曲成形后,再将缺口多余部分切除。
5.对于批量大、尺寸较小的弯曲件,为提高生产率,可以采用多工序的冲裁压弯切断连续工艺成形。
七、弯曲模的基本结构弯曲模的结构与一般冲裁模结构相似,分上下两个部分,它由凸、凹模,定位、卸料、导向及紧固件等组成,但弯曲模具还有它的特点,如凸、凹模除一般动作外,有时还需要作摆动、转动等动作。
弯曲模结构形式应根据弯曲件形状,精度要求及生产批量等进行选择。
1.简单动作弯曲模该模具由模架、凸模、凹模、定位销、卸料杆、顶板、顶杆等零件组成。
工作时,毛坯由顶板上的两个定位销定位,这样保证在弯曲过程中不产生滑移。
2.复杂动作弯曲模(模拟动画)复杂弯曲模是指在一次冲程中完成两个以上的动作。
可以弯制简单弯曲模所不能制出的工件。
闹钟双铃提环弯曲模,其结构特点是在下模上装有二件摆块,并在凸模、顶料板的配合下,进行压弯成形。
模具的前面装有斜面储料斗,通过冲床曲轴的动力带动偏心连杆机构把料斗中的料坯逐一送进,上模部分有自动卸料机构。
3.圆管形件的弯曲圆管形件弯曲方法,可有两次弯成和一次弯成两种。
两次弯成的第一步是先弯成波浪形,第二步再弯成圆形。
4.连续弯曲模(模拟动画)同时进行冲孔,切断和压弯的连续模,用以弯制侧壁带孔的双角弯曲件。
条料以导尺导料并从卸料板下面送至挡块右侧定位,当上模下压,条料首先被剪断并随即将所剪断的毛坯压弯成形。
与此同时,冲孔凸模在条料上冲出一个孔,上模回程时,卸料板卸下条料,顶件销在弹簧的作用下推出工件。
5.铰链件弯曲模铰链件通常是将毛坯头部预弯,然后卷圆。
弯曲模的基本原理(五)八、弯曲模工作部分的设计1.凸模和凹模的圆角半径A.凸模圆角半径一般凸模的工作圆角半径取弯曲件的内侧弯曲半径,即rt=r,但不能小于材料允许的最小弯曲半径。
当弯曲件的弯曲半径较大时,还要考虑曲率回弹量。
如因工件结构上的需要,出现r<rmin 时,则应取rt>rmin然后加一次整形工序,整形模的尺寸为rt=r。
B.凹模圆角半径凹模圆角半径不能过小,以免材料表面擦伤。
在实际生产中,凹模圆角半径通常根据材料的厚度来选取:当t<2 Ra=(3~6)tt=2~4 Ra=(2~3)tt>4 Ra=2tV形凹模底部可开退刀模或取圆角半径Ra为:Ra=(0.6~0.8)(rt+t)2.凹模工作深度凹模深度l要适当,若过小,则工件两端的自由部分太多,弯曲件回弹大,不平直,影响零件质量;若过大,凹模增大,消耗模具钢材多,且需要压力机有较大的行程。
3.凸模和凹模的间隙弯曲U形件时,其凸凹模间隙z的大小,对弯曲件质量有直接影响。
过大的间隙将引起回弹角的增大,过小时,引起工件材料厚度的变薄,降低了模具使用寿命。