车架电泳线线技术要求
车架电泳线线技术要求

车架电泳线线技术要求车架以及底盘小件以及薄板件电泳线技术要求甲方(需方):乙方(供方):乙方向甲方提供车架、底盘小件以及薄板件电泳线设备 1 台(台套),由乙方进行设备的设计、制造、安装、调试,验收合格后一次性交付甲方使用。
为确保项目质量,需满足如下要求:一、技术要求1、项目总体要求1.1涂装工件名称:车架以及底盘小件以及薄板件;1.2零件最大组挂尺寸:长12米*宽1.1米*高1.6米,1.3最大重量:1500KG1.4动力来源:电、压缩空气、天然气;1.3生产纲领:车架产量50000台/年,底盘小件和薄板件25000挂/年;1.4工作制度:工作制度:每年300天,每天工作20个小时,三班制;生产节拍:4.8分钟/件1.5工艺过程:工艺温度:预脱脂、脱脂温度不低于45℃;磷化温度为35~45℃;电泳温度为28~32℃;电泳烘干工件表面温度为180℃以上,其余工序常温。
工序工序内容时间(min) 温度(℃)处理方式1 上件常温自动输送过来2 预脱脂 1 不低于45 浸渍3 脱脂 3 不低于45 浸渍4 水洗 1 常温浸渍+出槽喷淋5 水洗 1 常温浸渍+出槽喷淋6 表调 1 常温浸渍7 磷化 3 35~45 浸渍8 水洗 1 常温浸渍+出槽喷淋除渣泵。
7)槽底与两侧壁板连接处采用圆弧结构,与底、侧板焊接的焊缝不在折角处,不采用槽底板与侧壁板直角对接焊。
8)槽体板与骨架按规范采用断续焊,槽体板与板之间采用连接密封焊,要求各焊缝尽量设置在骨架上,槽体要求耐压、不渗不漏。
9)预脱脂、脱脂、纯水洗等循环管路需加袋式过滤器。
10)预脱脂、脱脂过滤器中需加有高磁磁棒。
磁棒可以手工清洁。
4.1.5 搅拌系统1)要求槽底无死角,各处均能喷到。
2)每只浸槽喷射管数按保证车架表面处理质量的原则下选定。
4.1.6 喷淋系统1)脱脂采用浸的方式,去除白车架内外表面上的污油和铁屑2)磷化后水洗系统去除磷化后的车架内外表面上磷化渣。
小型电泳涂装线的设备安装工艺管理要点

小型电泳涂装线的设备安装工艺管理要点电泳涂装线是一种常用的表面涂装技术,广泛应用于汽车、家具、机械等行业。
为了确保设备安装的质量和效果,需要进行合理的工艺管理。
本文将介绍小型电泳涂装线的设备安装工艺管理的要点。
一、设备选型与准备在进行设备安装之前,首先需要进行设备选型与准备工作。
1. 设备选型:根据涂装需求和生产规模,选择合适的小型电泳涂装设备,包括电泳槽、输送系统、喷淋系统等。
还需考虑设备的品牌、性能、售后服务等因素。
2. 工厂布置与准备:根据设备尺寸和工艺流程,设计合适的工厂布置方案,确保设备的安装、维护和操作的便捷性。
同时,进行相关的土建工程、设备基础的准备工作。
二、设备安装过程设备安装是关键的环节,要确保每一个步骤的准确和流程的顺畅。
下面将介绍设备安装的具体过程。
1. 槽体安装:首先,根据设计方案进行槽体的安装,确保槽体与地面平整且稳固。
然后,根据设备尺寸和工艺要求进行管道的连接,确保液体的流动通畅。
2. 输送系统安装:根据工艺流程要求,安装输送系统,包括输送链板、驱动装置、导向装置等。
同时,进行系统的调试和测试,确保输送的稳定和准确。
3. 喷淋系统安装:根据涂装要求,安装喷淋系统,包括喷枪、喷嘴、喷淋装置等。
调试系统,测试液体喷淋的均匀性和喷射力度。
4. 配电系统安装:根据设备的功率和工作电压要求,安装配电系统,确保设备的正常供电和电气安全。
5. 控制系统安装:根据涂装设备的自动化程度,安装相应的控制系统,包括PLC、触摸屏等。
同时,进行系统的调试,确保涂装过程的稳定性和精确性。
三、设备安装验收与优化设备安装完成后,需要进行验收和优化工作,确保设备的正常运行和效果的理想。
1. 设备验收:对于设备安装工作的每一个环节,进行检查和测试,确保设备的各项指标符合要求。
如槽体的密封性、输送系统的稳定性、喷淋系统的均匀性等。
2. 设备调试与优化:根据实际生产情况,对设备进行调试和优化,优化输送速度、喷淋参数等,达到最佳的涂装效果和生产效率。
车架电泳方案

天津电动车岳;/yuekai8897@ 9-6
6
山东亮光涂装科技有限
天津电动车岳;/yuekai8897@ 9-7
扬程:21m 功率:15kw 数量:1 台 5 型号:65YWP30-15-4 流量:20 m3/h 扬程:17 m 功率:4 kw 数量:3 台 4.1.5 排风机 型号:4-72№6C 风量:15300m3/h 全压:1260Pa 功率:7.5KW 数量:2 台 4.1.6 储液槽 1 预脱脂槽 规格:L850×W2050×H1100 材质:δ=3.0 Q235 板、Q235 型材 数量:1 台 配置:双层不锈钢过滤网、DN50 排空阀等
3.2 阴极电泳: 3.2.1 由于阴极电泳具有:
2
山东亮光涂装科技有限
天津电动车岳;/yuekai8897@ 9-3
①较高的泳透力,极有利于形状复杂的工件的电泳涂覆。
②其电泳漆膜的抗蚀性能明显的高于阳极电泳漆膜。
③由于工件在施工时处于阳极电位,因此不担心在电化学
反应中工件被腐蚀。
所以针对该产品之特点采用阴极电泳工艺。
流量:25m3/h 扬程 19m 功率:3kw 数量:2 台 2 型号:100YW100-18-11 流量:80m3/h 扬程:21m 功率:11kw 数量:1 台 3 型号:65YW30-15-3 流量:20 m3/h 扬程:17m 功率:3kw 数量:2 台 4 型号:100YWP100-18-15 流量:80m3/h
汽车零部件电泳涂装线方案

汽车零部件电泳涂装线技术方案二0二一年三月一、设计依据1.生产纲领1.1.电泳线主要承担平衡夹总成等多种汽车零部件的电泳底漆、烘干等任务。
1.2.电泳线产能为双班216万件/年。
1.3.通过最大工件尺寸:1702mm*560mm*600mm。
1.4.采用阴极电泳工艺,工艺流程:前处理(无磷薄膜工艺)-电泳及后清洗-吹水-电泳烘干-强冷-漆后存储1.5.采用悬挂输送机完成工序间的输送。
1.6.前处理采用喷淋与浸渍相结合的处理方式,电泳及后清洗采用喷浸结合处理方式。
1.7.加热热源采用天然气。
2.现场条件序号名称参数1供市政电50Hz380V三相五线2供市政水0.15~0.2MPa3供压缩空气0.6~0.7MPa4供天然气10~30KPa热值:8300大卡/NM35污水排放标准GB8978-1996《污水综合排放标准》二级,由厂区污水处理站集中处理。
6废气排放标准GB16297-1996《大气污染物综合排放标准》二类7噪音≤82db3.生产制度根据业主要求,本次设计电泳车间采用两班制,一天工作16h。
4.生产线总体要求4.1.生产线设备设计以业主的品牌定位和发展战略为基础,整个生产线设备以经济、可靠、实用为基本设计原则,努力提高性价比;4.2.设计的原则:乙方根据甲方提出的设计要求、遵照国家和行业有关法规和标准,第2页共22页遵循设备的可靠性、实用性、合理性、经济耐用的设计原则进行整体设计,并应获得甲方代表签字确认。
4.3.设备整体外观设计制造应体现美观大方,富于时代感,能体现现代企业风貌;4.4.生产线的整体布局应体现空间分割合理、物流通畅、操作维护方便等特点;4.5.整套设备应满足自动化控制程度较高、能耗低的特点,尽量降低运行成本;4.6.整线工序完善,工艺设备先进;操作条件安全,良好,车间环境清洁,无粉尘污染;按同期同类产品先进水平设计,制造。
4.7.对废气、废水治理等后续工作进行通盘考虑,并预留接口。
车架阴极电泳涂装工艺说明
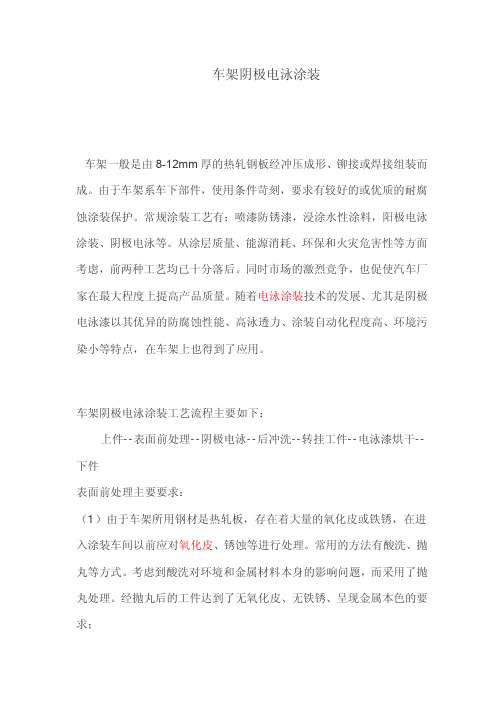
车架阴极电泳涂装车架一般是由8-12mm厚的热轧钢板经冲压成形、铆接或焊接组装而成。
由于车架系车下部件,使用条件苛刻,要求有较好的或优质的耐腐蚀涂装保护。
常规涂装工艺有:喷漆防锈漆,浸涂水性涂料,阳极电泳涂装、阴极电泳等。
从涂层质量、能源消耗、环保和火灾危害性等方面考虑,前两种工艺均已十分落后。
同时市场的激烈竞争,也促使汽车厂家在最大程度上提高产品质量。
随着电泳涂装技术的发展、尤其是阴极电泳漆以其优异的防腐蚀性能、高泳透力、涂装自动化程度高、环境污染小等特点,在车架上也得到了应用。
车架阴极电泳涂装工艺流程主要如下:上件--表面前处理--阴极电泳--后冲洗--转挂工件--电泳漆烘干--下件表面前处理主要要求:(1)由于车架所用钢材是热轧板,存在着大量的氧化皮或铁锈,在进入涂装车间以前应对氧化皮、锈蚀等进行处理。
常用的方法有酸洗、抛丸等方式。
考虑到酸洗对环境和金属材料本身的影响问题,而采用了抛丸处理。
经抛丸后的工件达到了无氧化皮、无铁锈、呈现金属本色的要求;(2)选择了与阴极电泳漆配套的磷化剂进行处理,以提高漆膜附着力和耐腐蚀性。
该线工件经前处理工艺后,工件表面达到如下要求: 1.磷化膜外观均匀、致密、无锈; 2.磷化膜重1-3g/M2; 3.结晶细度<10um4.磷化膜P 比>85﹪(即磷化膜的碱性强)。
表面前处理工艺工艺条件工序名称 处理方式 时间(s ) 温度(℃)压力 预脱脂 喷淋 60 50-65 0.10-0.12脱脂 浸渍 120 50-65 水洗1 浸渍 60 室温 表调 浸渍 30 室温 磷化 浸渍 180 40-45 水洗2 浸渍 30 室温 纯水洗浸渍60室温阴极电泳及后冲洗处理工艺工艺条件工序名称处理方式时间(s)温度(℃)压力(Mpa)阴极电泳浸渍18028-320次槽次UF冲洗喷淋10室温0.08-0.10 UF1洗浸渍30室温新鲜UF洗喷淋10室温0.08-0.10纯水洗喷淋30室温0.08-0.12。
通力车架阴极电泳涂装线工艺设计方案

陕汽集团通力专用车有限公司车架阴极电泳涂装线工艺设计方案版本号 : 004陕西邦仕涂装工程技术有限公司电话: -2005 传真: -20092008年 9月 28日、设计依据1、工程名称:汽车车架阴极电泳涂装线2、车架阴极电泳涂装线的设计纲领①车架工件的参数最大车架尺寸(长X宽X高)最短车架的长度按车架长度分类:长车架在车架总量中所占的比例短车架在车架总量中所占的比例最大车架重量最大车架面积12m X m xm20%80%200056(每吊挂放置1台车架)(每吊挂放置2台车架)kgm2②车架生产的设计纲领年生产量60000年作业天数250 每天班次 2 每班作业时间8天班小时设备系数3、涂装生产的纲领要求由年生产量计算日涂装生产量60000台/ 年十 -250天/ 年=283 台/ 天由日涂装生产量计算每班的涂装生产量283台/ 天十2 班/ 天=142 台/班由班涂装生产量和每吊挂的台车量计算涂装生产的工艺节拍142台/班X 20%= 台/班台/班十1台/挂=挂/班142台/班X 80%= 台/班台/班* 2台/挂=挂/班挂/班+挂/班=挂/班挂/班十8小时/班=挂/ 台/小时* 60分钟/小时=1 ♦挂/分钟=分钟/ 挂(平均每班每吊挂放置1台车架的车架数)(平均每班每吊挂放置1台车架的吊挂数)(平均每班每吊挂放置2台车架的车架数)(平均每班每吊挂放置2台车架的吊挂数)(每班总的平均吊挂数)小时挂/分钟4、工艺基本过程工艺基本过程应先进行喷砂、预清理(喷砂部分的工序过程由通力公司自己解决),然后按预脱脂一►主脱脂一►(水喷洗)一►水浸洗一►表调一►磷化水洗纯水洗—►电泳一►(槽上UF水冲洗)一►循环UF水冲洗-UF 2水冲洗—纯水洗^烘干固化―►转入后道工序。
5、设计前处理槽为:长X宽X高=13 m X 2.2m X 2.5m (其中包括预脱脂槽、主脱脂槽、水浸洗槽、表调槽、磷化槽、水洗槽等六个槽)设计电泳槽主槽为:长X宽X 高 =13 m x m x (其中包括纯水洗槽、电泳槽、循环UF 水洗槽、UF 2水洗槽、纯水洗槽等五个槽)。
车架电泳线设备说明
车架电泳线设备说明概述车架电泳线是一种车架表面处理设备,常用于汽车制造行业和汽车修理厂,用于保护车架表面免受腐蚀和损坏。
车架电泳线设备主要由电泳槽、前处理设备、自动输送设备、电泳设备和烘箱等设备组成。
设备组成电泳槽电泳槽是车架电泳线设备的核心部分,用于对车架进行电泳处理。
电泳槽主要有铁、不锈钢和聚丙烯等材料制成。
电泳槽的尺寸和形状根据车架的尺寸和形状而定,可定制制造。
电泳槽的内部配备有电极、循环水箱和混合器等设备,用于将电泳液体循环流动并均匀地分布在车架表面上。
前处理设备前处理设备用于预处理车架表面,以保证车架表面清洁,并且对车架进行表面处理,以便于电泳液体能够均匀地附着在车架表面上。
预处理方法主要包括机械处理、化学处理和水洗等步骤。
自动输送设备自动输送设备是车架电泳线设备的重要组成部分,用于将车架从预处理设备输送到电泳槽,再将车架从电泳槽输送到烤箱。
自动输送设备主要由链式输送装置和电机驱动装置等设备组成。
电泳设备电泳设备是车架电泳线设备的关键部分,主要用于对车架进行电泳处理。
电泳设备包括电泳源、电泳电极、电泳液体和循环水箱等部分。
电泳液体通常由电泳涂料和水组成,用于形成膜层并覆盖在车架表面上。
电极的形状和数量应根据车架的形状而定,以确保涂层均匀致密。
烘箱烘箱用于加热车架,在车架表面形成坚硬的涂层。
烘箱通常由上、下两层组成,上层为热风烤箱,下层为固态烤箱。
车架从电泳槽输送到上层烘箱进行加热处理,然后再由自动输送装置输送到下层固态烤箱,进行冷却固化。
使用方法1.将车架放入前处理设备中,进行预处理。
2.将经过预处理的车架放入自动输送设备中,输送到电泳槽。
3.将车架放入电泳槽,开启电泳设备进行电泳处理。
4.将车架从电泳槽中取出,放入自动输送设备中,输送到烘箱。
5.将车架放入烘箱中,进行加热和冷却固化处理。
6.将处理好的车架取出,进行喷漆或其他表面处理。
注意事项1.在使用车架电泳线设备前,应检查设备是否正常运转,以确保设备的稳定性。
汽车零部件电泳涂装线方案
汽车零部件电泳涂装线技术方案江苏龙杰多尔环保涂装设备有限公司二0一九年三月设计方案一、设计依据1.生产纲领1.1.电泳线主要承担平衡夹总成等多种汽车零部件的电泳底漆、烘干等任务。
1.2.电泳线产能为双班216万件/年。
1.3.通过最大工件尺寸:1702mm*560mm*600mm。
1.4.采用阴极电泳工艺,工艺流程:前处理(无磷薄膜工艺)-电泳及后清洗-吹水-电泳烘干-强冷-漆后存储1.5.采用悬挂输送机完成工序间的输送。
1.6.前处理采用喷淋与浸渍相结合的处理方式,电泳及后清洗采用喷浸结合处理方式。
1.7.加热热源采用天然气。
2.现场条件序号名称参数1 供市政电50Hz 380V 三相五线2 供市政水0.15~0.2MPa3 供压缩空气0.6~0.7MPa4 供天然气10~30KPa 热值:8300大卡/NM35 污水排放标准GB8978-1996《污水综合排放标准》二级,由厂区污水处理站集中处理。
6 废气排放标准GB16297-1996《大气污染物综合排放标准》二类7 噪音≤82db3.生产制度根据业主要求,本次设计电泳车间采用两班制,一天工作16h。
4.生产线总体要求4.1.生产线设备设计以业主的品牌定位和发展战略为基础,整个生产线设备以经济、可靠、实用为基本设计原则,努力提高性价比;4.2.设计的原则:乙方根据甲方提出的设计要求、遵照国家和行业有关法规和标准,遵循设备的可靠性、实用性、合理性、经济耐用的设计原则进行整体设计,并应获得甲方代表签字确认。
4.3.设备整体外观设计制造应体现美观大方,富于时代感,能体现现代企业风貌;4.4.生产线的整体布局应体现空间分割合理、物流通畅、操作维护方便等特点;4.5.整套设备应满足自动化控制程度较高、能耗低的特点,尽量降低运行成本;4.6.整线工序完善,工艺设备先进;操作条件安全,良好,车间环境清洁,无粉尘污染;按同期同类产品先进水平设计,制造。
4.7.对废气、废水治理等后续工作进行通盘考虑,并预留接口。
电泳线作业指导书
电泳线生产前准备工作一、检查槽液(是否达到工艺要求温度(加温过程约10小时),浓度及相关要求)。
工艺参数:二、检查各槽体循环泵工作是否正常.三、开启整流柜,检查是否正常工作。
四、检查各自行小车程序及所在工位是否正确(监控中心触摸屏)。
五、开启阳极泵检查其工作是否正常。
六、检查烘干室热风炉及各风机无异常情况,即可升温,随即开启电泳线进行以下流程。
电泳线工艺流程一、工艺流程图:上件→预脱脂→脱脂→水洗1→酸洗→水洗2→中和→水洗3→水洗4→表调→磷化→水洗5→纯水洗1→阴极电泳→UF1水洗→UF2水洗→纯水洗→烘干→下件二、主要工艺流程:1 上件:处理方式:人工控制:手动操纵控制箱1.将所需电泳的工件装入工件篮。
注意:工件摆布尽量均匀合理,工件间隙不低于5CM,并使前后电动葫芦承重尽量平衡。
2.手动操作控制箱,使自行小车补位到发车位置.3.手动操作控制箱操纵电动葫芦同降至工件篮,挂钩(人工).4.手动操作控制箱同升至运行高度。
注意:工件篮需平衡,前后左右不出现倾斜.如不平衡需加配重。
并严格检查有无脱落挂钩挂在工件篮底,须及时摘除.5。
等待整个电泳线线后续流程完全达到工艺指标后,手动操作控制箱操纵发车。
进入预脱脂工艺步骤。
2 预脱脂:工艺目的:除去工件油渍处理方式:浸温度:60℃时间:7分钟处理液:自来水,脱脂剂A,脱脂剂B备注:循环泵控制:自动、人工均可预脱脂步骤主要由PLC程序自动控制,必要时也可人工辅助控制。
具体过程:自动控制,进入预脱脂工艺步骤。
第一阶段,工件篮行走至预脱脂工位,前后电动葫芦同降至设定高度(浸入槽体)浸泡工件。
浸泡时间240秒,前后电动葫芦同升至设定位置。
第二阶段,前后电动葫芦同降,二次浸泡。
浸泡时间180秒,然后同升至前后电动葫芦上限位置,自动进入下一工位。
此步骤结束后,检查工件是否达到工艺要求,如不符合工艺要求可人工控制继续浸泡,直至工件达到工艺要求.预脱脂工艺结束,进入脱脂工艺步骤。
汽车零部件阴极电泳涂装生产线技术协议书
汽车零部件阴极电泳涂装生产线技术协议书定作方:市锦汇机械制造代表:承揽方:富山涂装工程代表:二〇一三年十一月十二日目录一、设计依据二、设备设计尺寸三、设备技术性能及结构要求四、全线能源配置表五、工程界定表六、工程进度计划表七、买卖双方的设计分工和设计联络八、机组性能保证值及验收方法九、售后服务计划十、备品、备件明细表十一、主要外购件成件配置表十二、设备配置明细单十三、平面布局图一、设计依据1、方案设计的基本原则第一、质量第一原则:经济、实用、工艺合理、低使用面积、低运行成本. 第二、环保同步治理原则:要考虑“三废治理”,在建线同时考虑环保问题,设计出对废水、废气的排放及处理的基本设施和设备要求;第三、安全可靠原则:整套设备操作方便,维护简单。
特别注意,悬链、管道、水沟、电路、通道的合理布局;第四、流程合理原则:根据工艺需要,上下挂件及每个操作点布局合理、流程顺畅,自动化程度相对要高,但留有必要的弹性空间或条件,当出现某些不确定的问题时,可以方便调整或增补设备。
第五、低成本原则:整套设备在实现满足使用功能的前提下,去除不必要的或作用不明显的步骤及设备,整线结构尽可能简单,争取最少的建线、维护费用,尽可能的降低使用成本。
第六、美观协调原则:整个结构要协调(包全线色调);外形美观大方。
要结合与其它工序在同一大车间的实际,严防烘道烟雾熏及厂房。
第七、充分利用空间原则:尽可能最大利用空间,在不影响使用和维护的前提下利于风管的布置;可以最大程度节约面积。
4、气候条件备注序号名称设计参数5、生产纲领6、工艺流程概要要求设计制造一条阴极电泳涂装+喷粉涂装生产线。
其生产线工艺流程如下:6.1、工艺工序流程6.2、工件吊装方式及装挂尺寸工件吊挂方式根据工件的形状结构采用双点活动吊挂横梁吊挂工件方式,横梁双点吊具间隔为1000mm。
最大工件中心距为4000mm,最大工件吊挂中心距为4000mm,方可保证工件运行时相互之间不碰撞。
- 1、下载文档前请自行甄别文档内容的完整性,平台不提供额外的编辑、内容补充、找答案等附加服务。
- 2、"仅部分预览"的文档,不可在线预览部分如存在完整性等问题,可反馈申请退款(可完整预览的文档不适用该条件!)。
- 3、如文档侵犯您的权益,请联系客服反馈,我们会尽快为您处理(人工客服工作时间:9:00-18:30)。
车架以及底盘小件以及薄板件电泳线技术要求甲方(需方):乙方(供方):乙方向甲方提供车架、底盘小件以及薄板件电泳线设备 1 台(台套),由乙方进行设备的设计、制造、安装、调试,验收合格后一次性交付甲方使用。
为确保项目质量,需满足如下要求:一、技术要求1、项目总体要求1.1涂装工件名称:车架以及底盘小件以及薄板件;1.2零件最大组挂尺寸:长12米*宽1.1米*高1.6米,1.3最大重量:1500KG1.4动力来源:电、压缩空气、天然气;1.3生产纲领:车架产量50000台/年,底盘小件和薄板件25000挂/年;1.4工作制度:工作制度:每年300天,每天工作20个小时,三班制;生产节拍:4.8分钟/件1.5工艺过程:工艺温度:预脱脂、脱脂温度不低于45℃;磷化温度为35~45℃;电泳温度为28~32℃;电泳烘干工件表面温度为180℃以上,其余工序常温。
(以上处理方式厂家可按照投标方的最优方案来制定)(每个工位有几个工作点根据工艺平面图确定)1.6输送方式:空中输送部分单独招标、地面输送包含在电泳线内1.7作业点:每个工位有几个工作点根据工艺平面图确定1.8厂房参数:210×18,厂房高度: 13米1.9能源: 动力电: 380 V三相 50HZ照明电: 220 V单相 50HZ自来水:2~3 Kg/cm2(以实际情况为准)压缩空气:5~6 Kg/cm2(以实际情况为准)加热源:天然气1.10有在著名工程机械单位或者汽车行业设计和建设大型阴极电泳涂装线的工程案例,且所承制的单个涂装线项目规模不小于1000万(出具合同证明);2、项目内容2.1项目工作流程1)工件在上件点上件;2)工件经前处理、电泳;3)电泳后转挂至地面链,进入电泳烘房进行烘烤、强冷;2.2分项工程1)前处理线一条2)电泳线一条(含烤房、强冷)3)地面烘烤输送系统系统一套投标报价时,除总价以外,以上几部分必须有分项报价。
3、设计和制造标准(三)、执行标准1.招标方此处所列标准仅为涉及的主要标准,而且不保证其为最新版执行标准;投标方应当在投标文件中予以补充和完善。
2.投标方需要执行的标准,应当以所供货物通过招标方将来组织的最终验收之日后需要执行的标准。
1)GB6514-95涂装作业安全规程《涂漆工艺安全及涂漆工艺通风净化》;2)GB7691-2003涂装作业安全规程《安全管理通则》;3)GB14444-2006涂装作业安全规程《喷漆室安全技术规定》;4)GB14443-2007涂装作业安全规程《涂层烘干室安全技术规定》;5)GB12942-2006涂装作业安全规程《有限空间作业安全技术要求》;6)GB16297-96《大气污染物综合排放标准》;7)GB20101-2006涂装作业安全规程《有机废气净化装置安全技术规定》;8)GB50058-92《爆炸和火灾危险场所电力装置设计规范》;9)GBZI-2002《工业企业设计卫生标准》。
备注:如果有采用国际标准的货物,其执行标准由投标方提供、招标方确认。
4、工艺及设备设计说明:整体要求:电泳线整体架高不低于3米,相关的辅助设备安装在一楼,除掉一些必须安装在外的设备。
实际安装以现场为准。
4.1前处理线4.1.1该前处理线为喷浸结合的磷化电泳处理系统,前处理电泳设备主要由预脱脂槽、脱脂槽、水洗1槽、水洗2槽、表面调整槽、磷化槽、水洗3槽、水洗4槽、泳前去离子水洗槽、加料系统(预脱脂、脱脂、表调、磷化、电泳加料)、油水分离系统、磷化除渣系统、磷化酸洗系统、倒槽系统、送排风系统、前处理污水收集系统、阴级电泳系统、一次超滤喷淋槽、二次超滤浸槽、泳后纯水洗槽、密封水槽、泵、管路和过滤器系统、温度控制系统、室体、搅拌系统、喷淋系统、供水系统、密封液系统、纯水系统、照明系统、电气控制系统等组成。
4.1.2 槽体4.1.3前处理方式采用槽浸+喷淋方式,室体通道设计为自支承结构,侧板为大面积玻璃隔板,室体骨架采用型钢制作。
室体两侧设有照明灯箱。
.前处理室体的各加热段设有抽风机,防止蒸汽逸入车间。
前处理室体配置有防水检修门。
前处理室体的内部设有适当的走道以便维修及布置相关设备的平台。
4.1.4 所有槽体基本要求:1)槽体为矩形槽;2)槽体要满足工艺长度的要求,要满足前述工件通过性的要求,槽体要满足热容量的要求(即连续通过工件槽液不降温,使温度恒定)。
3)槽体在槽液满槽最高液位时,确保强度和刚性的要求,要求槽体不变形。
4)槽体骨架立柱要承担前处理线室体、喷射系统、供风管路、自行葫芦、吊具、车架、风机平台、纵向维修行人平台及前处理线电泳线设备钢平台等重量的动静载荷。
5)前处理线脱脂、磷化槽设置附槽,附槽设有过滤网的导向槽,要求与过滤网尺寸配合便于轻松抽拉,二者之间要求严密。
6)磷化槽的槽底设为斜底和锥形斗。
锥形斗底端设有排净阀,锥形斗侧面设有管及阀,接除渣泵。
7)槽底与两侧壁板连接处采用圆弧结构,与底、侧板焊接的焊缝不在折角处,不采用槽底板与侧壁板直角对接焊。
8)槽体板与骨架按规范采用断续焊,槽体板与板之间采用连接密封焊,要求各焊缝尽量设置在骨架上,槽体要求耐压、不渗不漏。
9)预脱脂、脱脂、纯水洗等循环管路需加袋式过滤器。
10)预脱脂、脱脂过滤器中需加有高磁磁棒。
磁棒可以手工清洁。
4.1.5 搅拌系统1)要求槽底无死角,各处均能喷到。
2)每只浸槽喷射管数按保证车架表面处理质量的原则下选定。
4.1.6 喷淋系统1)脱脂采用浸的方式,去除白车架内外表面上的污油和铁屑2)磷化后水洗系统去除磷化后的车架内外表面上磷化渣。
3)磷化二次水洗后,有节拍自动控制喷纯水系统,清洗磷化后车架表面上磷化液的残留物。
4)前处理设备喷射系统各种功能要求的管路直径、阀门规格尺寸均以确保满足各种功能实现所需要的流量、压力而选定。
5)所有喷淋喷嘴采用不锈钢,可单独调节喷淋方向、调节后可固定的喷嘴。
其中顶部喷淋支管做有连接在槽侧的辅助支架,支架确保喷淋支管的支承强度。
6)喷淋管和喷嘴冲洗净白车架和底盘小件表面的铁屑和大部分的污油。
4.1.7 密封室密封室骨架要先用螺栓连接并调整好后,再进行整体焊接。
安装焊接质量要符合相关行业标准。
密封室不锈钢壁板制作时要贴保护膜,安装要按图纸要求和施工规范,注意外观质量,不得有明显划碰伤。
密封室采用加胶玻璃。
4.1.8 除油装置:1)要求能去除预脱脂、脱脂槽液中和浮在液面上的污油。
2)要求将槽内的含污油溶液加热到 80~90℃,3)槽加热采用自动控制阀组和旁通,设有压力表和温度表,对槽液温度能实现自动控制。
4)预脱脂、脱脂槽液除油共用一套除油系统,各槽液中的污油进行处理,处理后的清液回流至原液提取槽内。
5)所有管路为可拆装式法兰连接,垫片采用聚四氟乙烯垫片,连接处密封良好,不渗不漏。
4.1.9 除铁屑装置1)要求能去除预脱脂、脱脂槽液中铁屑;2)预脱脂、脱脂管路过滤器中含有永磁棒。
4.1.10 除渣系统1)保证工作液中含渣量≤300mg/L。
2)磷化除渣系统材料均为304不锈钢。
3)钢结构梁必须严格按GB50205-2001钢结构标准执行,重要翼缘板不许采用带钢。
4.1.11磷化酸洗系统1)磷化酸洗系统通过泵、管路和阀的选控对磷化板式换热器、磷化液管路及磷化液接触的泵、阀等进行清洗。
2)磷化酸洗系统可以单独对任一台磷化系统中的板式换热器进行酸洗和清洗,而不影响正常生产,也具备同时对全部磷化系统中的板式换热器进行酸洗和清洗。
3)酸洗槽由管阀控制和调节,能分别实现酸洗清洗磷化管路及系统的功能,利用管阀的切换将磷化工作液槽酸洗清洗的废酸排净。
4)槽之间不允许相互之间串液。
5) 投标方可自行设计清洗方式,选最佳方案。
4.1.12 自动调温系统1)前处理线预脱脂、脱脂槽液采用板式换热器槽外间接加热,热源为热水。
2)温度实现自动控制,冷槽升温时间≤4小时,二次升温时间≤1小时。
工艺温度的设定和控制可调。
3)加热管路上设有电动自动控制调节阀组,实现自动控制槽液温度。
调节阀组设有旁通阀和温度表。
4)磷化槽工作液工艺温度可实现自动控制和调节,磷化槽液冷槽升温时间≤4小时。
二次升温时间≤1小时。
4.1.13药品补加系统4.1.13.1 脱脂1)预脱脂、脱脂槽共用一套药品补加系统。
2)混合槽上装有液位计和搅拌器,由计量加料泵分别向预脱脂、脱脂工作液槽补液,实现药品的手动或自动补加,补液控制由处理车架和小件数量给定。
4.1.13.2 表调1)表调补加系统由混合槽、计量泵、加料管路、注水管路(自来水)、排净管路等组成。
2)全系统采用 1 台计量加料泵,流量可调。
3)全系统管路为法兰连接,所有连接均要求严密,不渗不漏。
4.1.13.3 磷化加料系统磷化药剂补加系统由磷化添加剂、促进剂两套装置组成,分别采用两台计量加料泵加料。
4.1.14倒槽系统1)磷化的工作液槽与槽之间槽液置换,倒槽后,空槽内要求无积液,贮有槽液的槽体利用泵能够循环。
2)贮槽设有排净装置,工作液槽和贮槽的槽体排净管最低位置上设清洗接头。
3)置换泵入口处设过滤网。
4.1.15 送排风系统1)前处理室体内的危害气体不允许溢出室体外,表调与磷化之间的碱性气体、酸性气体不能相串。
2)排风范围是:预脱脂段、脱脂段;排风范围是:磷化工艺区段。
3)排风风机选用不锈钢风机,所有送排风管、风阀等采用不锈钢。
4)排风出屋面风管高度≥1.5m,并设有防雨风帽。
5)所有风管、风机、风阀要密封,防止向外漏水、漏液、漏气现象。
4.1.16 纯水制备系统渗透系统产水指标:1)出水量:由设备厂商根据我司工艺计算给出。
2)电导率:≤5μs/cm3)脱盐率:≥97%a.纯水系统描述:RO系统为全自动运行,整机连锁。
在设计上充分考虑了原水水质及水温变化对RO膜产水量的影响,为确保反渗透系统长期、稳定的运行,要选用高脱盐率、高产水量的反渗透膜组件。
在系统设备材质设计及性能要求,所有水泵要设置保安过滤器、反渗透主机、高压管路部分要确保系统中关键设备局部的耐压性、抗冲击、耐酸碱性,保证系统长期、稳定、可靠的使用。
系统中要设有便于操作的反渗透就地清洗系统。
RO系统的设计为自动运行,PLC控制,同时整体连锁,报警采用声、光、电一体化结合,连线管路上皆标有水流方向等。
b.主要设备说明及要求:原水箱及原水泵:本系统原水箱设置一台,容积根据产量要求制定。
原水泵设置二台.正常工作时一用一备,原水泵采用国产优质不锈钢水泵。
多介质过滤器:设置一台介质过滤器,用于除去原水中的胶体和悬浮物,将出水的污染指数(SDI)控制在4以下,滤速为8-15m/h;其中每台过滤器配备本体阀门、进出口压力指示、人工取样阀及取样槽。
过滤器内装多级配石英砂,可有效去除原水中的胶体和悬浮物,并通过形成的滤饼增强过滤效果。