单级齿轮减速器机械优化设计
基于matlab的单级圆柱齿轮减速器优化设计
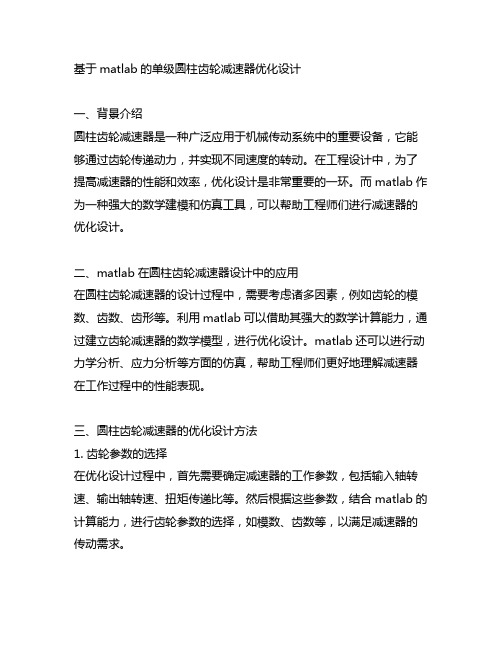
基于matlab的单级圆柱齿轮减速器优化设计一、背景介绍圆柱齿轮减速器是一种广泛应用于机械传动系统中的重要设备,它能够通过齿轮传递动力,并实现不同速度的转动。
在工程设计中,为了提高减速器的性能和效率,优化设计是非常重要的一环。
而matlab作为一种强大的数学建模和仿真工具,可以帮助工程师们进行减速器的优化设计。
二、matlab在圆柱齿轮减速器设计中的应用在圆柱齿轮减速器的设计过程中,需要考虑诸多因素,例如齿轮的模数、齿数、齿形等。
利用matlab可以借助其强大的数学计算能力,通过建立齿轮减速器的数学模型,进行优化设计。
matlab还可以进行动力学分析、应力分析等方面的仿真,帮助工程师们更好地理解减速器在工作过程中的性能表现。
三、圆柱齿轮减速器的优化设计方法1. 齿轮参数的选择在优化设计过程中,首先需要确定减速器的工作参数,包括输入轴转速、输出轴转速、扭矩传递比等。
然后根据这些参数,结合matlab的计算能力,进行齿轮参数的选择,如模数、齿数等,以满足减速器的传动需求。
2. 齿形的优化齿轮的齿形对于减速器的传动性能具有重要影响,通过matlab可以进行齿形的优化设计,以确保齿轮的传动效率和传动平稳性。
3. 传动效率的分析传动效率是评价减速器性能的重要指标之一,利用matlab可以进行减速器传动效率的分析,找出影响传动效率的因素,并进行优化设计,提高减速器的传动效率。
4. 结构强度的分析除了传动效率外,减速器的结构强度也是需要考虑的重要因素。
matlab可以进行减速器的结构强度分析,找出可能存在的弱点并进行设计改进,以保证减速器的结构强度和稳定性。
四、实例分析通过一个实例来展示基于matlab的单级圆柱齿轮减速器的优化设计过程。
首先我们需要确定减速器的工作参数,比如输入轴转速为1000rpm,输出轴转速为100rpm,扭矩传递比为10。
然后利用matlab进行齿轮参数的选择,计算得到需要的模数和齿数。
机械优化设计-1组-对一对单级圆柱齿轮减速器-以体积最小为目标进行优化设计学习资料

《机械优化设计》课程作业(2014至2015学年度第2学期)班级学号姓名郑杨机械1207 A07120157机械优化设计案例1. 题目对一对单级圆柱齿轮减速器,以体积最小为目标进行优化设计。
2.已知条件已知数输入功p=58kw ,输入转速n 1=1000r/min ,齿数比u=5,齿轮的许用应力[δ]H =550Mpa ,许用弯曲应力[δ]F =400Mpa 。
3.建立优化模型3.1问题分析及设计变量的确定由已知条件得求在满足零件刚度和强度条件下,使减速器体积最小的各项设计参数。
由于齿轮和轴的尺寸(即壳体内的零件)是决定减速器体积的依据,故可按它们的体积之和最小的原则建立目标函数。
单机圆柱齿轮减速器的齿轮和轴的体积可近似的表示为:]3228)6.110(05.005.2)10(8.0[25.087)(25.0))((25.0)(25.0)(25.0222122212221222212212122221222120222222222121z z z z z z z z z z z g g z z d d l d d m u mz b bd m u mz b b d b u z m b d b z m d d d d l c d d D c b d d b d d b v +++---+---+-=++++-----+-=πππππππ式中符号意义由结构图给出,其计算公式为b c d m umz d d d mumz D mz d mz d z z g g 2.0)6.110(25.0,6.110,21022122211=--==-===由上式知,齿数比给定之后,体积取决于b 、z 1 、m 、l 、d z1 和d z2 六个参数,则设计变量可取为Tz z T d d lm z bx x x x x x x ][][211654321==3.2目标函数为min)32286.18.092.0858575.4(785398.0)(2625262425246316321251261231232123221→++++-+-+-+=x x x x x x x x x x x x x x x x x x x x x x x x x x f3.3约束条件的建立1)为避免发生根切,应有min z z ≥17=,得017)(21≤-=x x g2 )齿宽应满足max min ϕϕ≤≤d b,min ϕ和max ϕ为齿宽系数d ϕ的最大值和最小值,一般取min ϕ=0.9,max ϕ=1.4,得04.1))(0)(9.0)(32133212≤-=≤-=x x x x g x x x x g3)动力传递的齿轮模数应大于2mm ,得 02)(34≤-=x x g4)为了限制大齿轮的直径不至过大,小齿轮的直径不能大于max 1d ,得 0300)(325≤-=x x x g5)齿轮轴直径的范围:max min z z z d d d ≤≤得0200)(0130)(0150)(0100)(69685756≤-=≤-=≤-=≤-=x x g x x g x x g x x g6)轴的支撑距离l 按结构关系,应满足条件:l 2min 5.02z d b +∆+≥(可取min ∆=20),得0405.0)(46110≤--+=x x x x g7)齿轮的接触应力和弯曲应力应不大于许用值,得400)10394.010177.02824.0(7098)(0400)10854.0106666.0169.0(7098)(0550)(1468250)(224222321132242223211213211≤-⨯-⨯+=≤-⨯-⨯+=≤-=---x x x x x x g x x x x x x g x x x x g8)齿轮轴的最大挠度max δ不大于许用值][δ,得003.0)(04.117)(445324414≤-=x x x x x x g9)齿轮轴的弯曲应力w δ不大于许用值w ][δ,得5.5106)1085.2(1)(05.5104.2)1085.2(1)(1223246361612232463515≤-⨯+⨯=≤-⨯+⨯=x x x x x g x x x x x g4.优化方法的选择由于该问题有6个设计变量,16个约束条件的优化设计问题,采用传统的优化设计方法比较繁琐,比较复杂,所以选用Matlab 优化工具箱中的fmincon函数来求解此非线性优化问题,避免了较为繁重的计算过程。
单级圆锥齿轮减速器 机械设计课程设计

4.判断放松、压紧端
FS1+Fa=705.18+462.15=1167.33N>FS2
故,轴承2压紧,轴承1放松。
则Fa1=FS1=705.18N ,Fa2=FS1+Fa=1167.33N
5.计算当量动载荷
对轴承1 =0.35=e, P1=Fr1=2014.79N
(1)确定轴上零件的定位和固定方式(如图)
(2)按扭转强度估算轴的最小直径
dmin≥
查表取A0=105,于是得dmin≥ =34.28mm
(3)确定轴各段直径和长度
左起第一段,取轴径40mm,长度80mm,,轴端进行2×45°倒角。左起第二段,轴径取46mm,长度46mm。左起第三段,取轴径50mm,长度为46mm。左起第四段,取轴径60mm,长度取90mm。左起第五段,取轴径54mm,长度取60mm。左起第六段,,取轴径50mm,长度取50mm。
1.电动机类型选择
根据电源及工作机工作条件,选用卧式封闭型Y(IP44)系列。
2.选择电动机
(1)工作所需功率Pw
Pw =4.5KW
(2)电动机输出功率Pd
查表得V带传动效率η1=0.97,滚动轴承效率η2=0.97,圆锥齿轮传动效率η3=0.97,联轴器效率η4=0.98,滑动轴承效率η5=0.96。
YF2=YFa2YFsa2=2.1704×1.7996=3.91。
因为 = =0.035, = =0.020
> ,故将 代入计算。
mm≥ =4.38
(4)计算大端模数
m= = =5.15
查表取m=5.5
(5)计算分度圆直径
d1=mZ1=5.5×17=93.50mm
一级圆柱齿轮减速器的优化设计

一级圆柱齿轮减速器的优化设计
一级圆柱齿轮减速器是使用于机械设备中的一种齿轮机构,用于减速电机的转速或改变转矩大小,从而实现传动装置运行的高精度驱动。
随着社会的发展,人们对设备的要求越来越高,一级圆柱齿轮减速器的优化设计变得尤为重要。
一方面,一级圆柱齿轮减速器应当具有较高的传动精度,确保机械设备的运行精度。
通常,为了提高传动精度,机械设计应在减速器的全部轴线上安装参数调节滑动轴承,并在轴承外壳上安装调节螺栓,以便将轴承松接夹具推向轴线,获得更好的精度。
其次,一级圆柱齿轮减速器应当具有良好的耐久性。
为此,齿轮机构的耐磨性和耐腐蚀性可以采用优质的优质合金整体热处理工艺,以获得良好的高强度硬度和特定的硬度值。
此外,可以采用分段调节双积分膜片结构,采用转速和扭矩的双重优化方法,使用更短的尺寸设计,来实现减速器的高效传动。
最后,应严格控制减速器的加工投入,以确保减速器的寿命。
此外,优化设计中还应结合现有技术进行改进。
首先,应根据设备的工作原理和使用状况,采用适当的模型作为参数来检测减速器的工作状态,以确保减速器的精度和可靠性;其次,应采用现代计算机辅助设计技术,将设计过程中的参数及各细节考虑在内,实现合理的减速器结构;最后,应实施新材料和新零件的采用,使减速器更加经济和可靠。
综上所述,优化一级圆柱齿轮减速器设计,应包括调节精度,耐
久性,传动效率,以及设计过程中的模型检验,计算机辅助设计,新材料新零件的考虑,以便更加有效的满足机械设备的要求。
单级圆柱齿轮减速器的优化设计

单级圆柱齿轮减速器的优化设计单级圆柱齿轮减速器的优化设计齿轮减速器是一种常用的机械传动装置,广泛应用于各种机械设备中。
其中,单级圆柱齿轮减速器是一种常见的减速器类型,具有结构简单、传动效率高等优点。
本文将围绕单级圆柱齿轮减速器的优化设计展开讨论。
首先,我们需要明确单级圆柱齿轮减速器的工作原理。
单级圆柱齿轮减速器是通过两个相互啮合的圆柱齿轮进行传动的。
其中,一个齿轮称为主动齿轮,另一个齿轮称为从动齿轮。
主动齿轮通过电机等动力源驱动,从而带动从动齿轮旋转。
通过不同大小的齿轮组合,可以实现不同的减速比。
在进行优化设计时,我们可以从以下几个方面考虑:1. 齿轮材料的选择:齿轮材料的选择直接影响到减速器的使用寿命和传动效率。
一般来说,常用的齿轮材料有钢、铸铁、铜合金等。
在选择材料时,需要综合考虑其强度、硬度、耐磨性等因素,并根据具体应用场景进行选择。
2. 齿轮参数的优化:齿轮参数包括模数、压力角、齿数等。
通过优化这些参数,可以提高减速器的传动效率和承载能力。
例如,增大模数可以增加齿轮的强度和承载能力;选择合适的压力角可以减小齿轮啮合时的摩擦损失。
3. 齿轮啮合传动的优化:齿轮啮合传动是减速器最关键的部分,也是能量损失最大的部分。
通过优化齿轮啮合传动的设计,可以减小能量损失,提高传动效率。
例如,采用精密加工工艺可以提高齿轮的啮合精度;采用润滑油膜技术可以减小摩擦损失。
4. 减速器结构的优化:减速器的结构设计也会影响其性能。
通过优化结构设计,可以降低噪声、提高刚度、减小体积等。
例如,采用斜齿圆柱减速器可以减小噪声;采用刚性箱体结构可以提高刚度。
5. 传动效率的测试与改进:在优化设计完成后,需要对减速器的传动效率进行测试,并根据测试结果进行改进。
通过不断地测试与改进,可以逐步提高减速器的传动效率。
综上所述,单级圆柱齿轮减速器的优化设计涉及到多个方面,包括材料选择、齿轮参数优化、齿轮啮合传动优化、结构优化以及传动效率测试与改进等。
单级斜齿圆柱齿轮减速器的优化设计
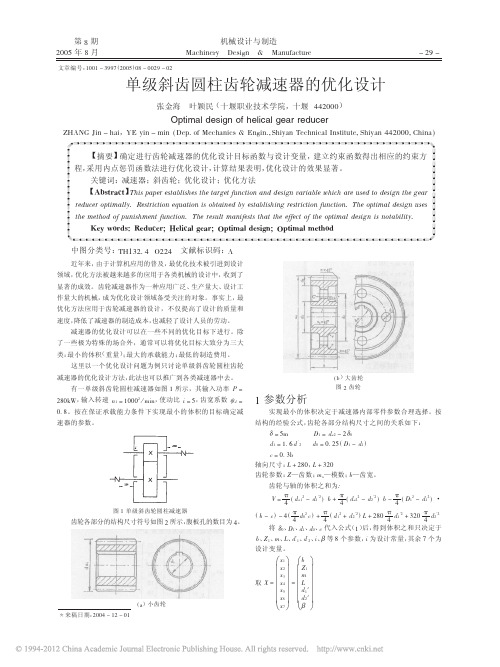
第$期
第@期 344> 年 @ 月
文章编号: 0440 9 8;;< = 344> ? 4@ 9 4480 9 43
AB(CDE’FG
机械设计与制造 /’HDIE J ABE-KB()-F’
9 80 9
组合机床空间角度的计算软件开发和总体设计
付晓岚 0 郭鸿勋 3 (0 广东机电职业技术学院,广州 >04>0> ? = 3 一拖开创装备科技有限公司,洛阳 1<0441)
4 T)大齿轮 图 ! 齿轮
% 参数分析
实现最小的体积决定于减速器内部零件参数合理选择。按 结构的经验公式, 齿轮各部分结构尺寸之间的关系如下: " R M3 2% R %8 U 2 V ! <% R 2&! $ ! "" 2" R "8 !M 4 <% $ 2% H
0 ; "8 IT 轴向尺寸: = W !N" , = W I!" 齿轮参数: >—齿数; 5/—模数; *—齿宽。 齿轮与轴的体积之和为 ? ! ! ! @ ; 4 2&%! $ 2% X! H * W 4 2&!! $ 2! X! H * A 4 <%! $ 2%! H ・ # # # ! ! ! ! X! ! X! ! X! 4 * A 0 H $ # 4 2" 0 H W 4 2% W 2! H = W !N" 2 W I!" 2 # # # % # ! (% ) 后, 得到体积之和只决定于 将 "" 、 <% 、 2% 、 2" 、 0 代入公式 其余 L 个为 *、 >% 、 5、 =、 2B% 、 2B! 、 #、 # 等 N 个参数, # 为设计常量, 设计变量。
单级直齿圆柱齿轮减速器的优化设计[五篇]
单级直齿圆柱齿轮减速器的优化设计[五篇]第一篇:单级直齿圆柱齿轮减速器的优化设计单级直齿圆柱齿轮减速器的优化设计一、问题描述设计如图所示的单级圆柱齿轮减速器。
减速器的传动比u=5,输入功率P=75+5⨯44=295kW,输入轴转速n=980r/min。
要求在保证齿轮承载能力的条件下,使减速器的质量最小。
xbxz1xmX=[x1 x2 x3 x4 x5 x6]T =xl1X5d1X6d2二、分析减速器的体积主要决定于箱体内齿轮和轴的尺寸三、数学建模积v可近似的表示为根据齿轮几何尺寸及结构尺寸的计算公式,单极圆柱齿轮减速器箱体内齿轮和轴的总体v=π(d42s221-db1+2s1)π⎛π2⎫+d(l1+l2)-D-D(b2-c)-4 d0c⎪44⎝4⎭'22'21ππ((d422-d2s2)b2+π4ds2 1(l1+l3))由上式克制,单极标准直齿圆柱齿轮减速器优化设计的设计变量可取为这里近似取b1=b2=b0根据有关结构设计的经验公式将这些经验公式有δ=5m、D2=d2-2δ、、c=0.2b,并取l2=32mm、l3=28mm将这些经验公式及数据代入式d0=0.25(D2-D1)(2-1)且用设计变量来表示,整理得目标函数的表达式为222222f(x)=0.785398154.75x1x2x3+85x1x2x3-85x1x3+0.92x1x6-x1x52222+0.8x1x2x3x6-1.6x1x3x6+x4x5+x4x6+28x5+32x6() 1)为避免发生根切,应有Z1≥Zmin=17应有于是得约束函数(2-1)g1(x)=17-x2≤0(2-2)2)根据工艺装备条件,跟制大齿轮直径d2不超过1500mm故小齿轮直径d1不应超过300mm即mz1≤30cm于是有约束函数(2-3)g2(x)=x2x3-30≤0(2-4)足16≤b≤35,由此得m-1g(x)=xx-35≤0(2-5)3133)为保证齿轮承载能力同时又避免载荷沿齿宽分布严重不均,要求齿宽系数Φm=-1g4(x)=16-x1x3≤0(2-6)b满m4)对传递动力的齿轮,模数不能过小,一般m≥2mm,且取标准系列值,故有() g5x=0.2-x3≤0(2-7)5)按经验,主、从动轴直径的取值范围为10cm≤d≤15cm,故有() g6x=10-x5≤0(2-8)() g7x=x5-15≤0(2-9)() g8x=13-x6≤0(2-10)() g9x=x6-20≤0(2-11)6)按结构关系,轴的支承跨距满足:l1≥b+2∆+0.5ds2,其中∆为箱体内壁到轴承中心线的距离,现取∆=2cm,则有约束函数g10(x)=x1+0.5x6+4-x4≤0(2-12)7)按齿轮的接触疲劳强度和弯曲疲劳强度条件,应有:336KT1(u+1)σH=≤[σH]abu(2-13)3σF=12KT1≤σF1bd1mYF111[](2-14)σF=1σFYFYF2≤σF2[](2-15)式中,a为齿轮传动的标准中心距,单位为cm,a=0.5mz1(u+1);K为载荷系数,这里取K=1.3;T1为小齿轮传递扭矩,单位为N•cm,T1=955000P/n1=95500⨯295/980N•cm≈287474N•cm;为齿轮的许用接触应力,单位为MPa,这里取;σF1、σF2分别为小齿轮与大齿轮的许用弯曲应力,单位为MPa,这里取σF1=261MPa、σF2=213MPa;YF1、YF2分别为小齿轮、大齿轮的齿形系数,对标准齿轮:[][][][]YF1=0.169+0.006666z1-0.000854z12(2-16)(2-17)2YF2=0.2824+0.003539z1-0.000001576z2对以上公式进行代入、运算及整理,得到满足齿轮接触强度与弯曲强度条件的约束函数:(2-18)2(0.169+0.6666⨯10-2x2-0.854⨯10-4x22)-261≤0(2-19)g12(x)=7474/x1x2x32(0.2824+0.177⨯10-2x2-0.394⨯10-4x22)-21 3≤0(2-20)g13(x)=7474/x1x2x3[][]根据主动轴(本例即小齿轮轴)刚度条件,轴的最大弯曲挠度ymax应小于许用值[y],即xxx g11(x)=45002(2-21)1--1-12231-855≤0ymax-[y]≤0其中取[y]=0.003l1;ymax则由下式计算:3y=Fl/(48EJ)(2-22)maxn式中,Fn为作用在小齿轮齿面上的法相载荷,单位为N,Fn=2T1/(mz1cosα),α为齿轮压力角,α=20︒;E为轴的材料的弹性模数,E=2⨯105MPa;J为轴的惯性矩,单位为cm,对圆形截面,J=πds41/64。
单级圆柱齿轮减速器优化设计与分析
单级圆柱齿轮减速器优化设计与分析减速器是工程实践中常见的机械传动装置,用于降低传动装置的转速并增加转矩。
圆柱齿轮减速器是一种常用的传动方式,其设计优化可以提高传动效率、减小噪音和振动,本文对单级圆柱齿轮减速器的优化设计与分析进行探讨。
1. 齿轮减速器的基本原理单级圆柱齿轮减速器由两个或多个相互啮合的齿轮组成,通过不同齿轮的大小和齿数来实现转速和转矩的变换。
具体来说,主动轮驱动从动轮,从而实现输出转矩。
2. 减速器的设计要素减速器的设计要素包括齿轮的模数、齿轮的齿数、齿轮的齿形、齿轮的间隙、齿轮的啮合角等。
在优化设计时,需要综合考虑这些要素,以提高减速器的性能。
3. 优化设计方法在单级圆柱齿轮减速器的优化设计中,可以采用多种方法。
一种常见的方法是基于理论计算,根据设计要求和理论公式计算齿轮参数,以满足传动比和输出转矩的要求。
另一种方法是基于仿真模拟,利用专业软件模拟齿轮传动的工作状态,通过调整齿轮参数,不断优化减速器的性能。
4. 优化设计指标在单级圆柱齿轮减速器的优化设计中,常用的指标包括传动效率、噪音和振动。
传动效率是指减速器输入功率与输出功率之比,可以通过优化齿轮参数和润滑条件来提高。
噪音和振动是影响减速器工作环境的重要因素,可以通过调整齿轮的齿形和间隙,以及采用减振措施来降低。
5. 优化设计案例以某公司生产的圆柱齿轮减速器为例,通过优化设计,取得了显著的效果。
首先,进行了齿轮的模数优化,选择了合适的模数以提高传动效率。
其次,通过改进齿轮的齿形和间隙,大大降低了噪音和振动。
最后,加入了减振设备,进一步提升了减速器的使用效果。
6. 分析优化效果通过优化设计,单级圆柱齿轮减速器的传动效率得到了明显提高,噪音和振动也得到了有效降低。
同时,减振设备的应用进一步增强了减速器的使用稳定性和可靠性。
因此,优化设计对于提升齿轮减速器的性能具有重要意义。
7. 总结与展望单级圆柱齿轮减速器的优化设计是提高传动效率、减小噪音和振动的重要手段。
机械优化设计三个案例
机械优化设计案例11. 题目对一对单级圆柱齿轮减速器,以体积最小为目标进行优化设计。
2。
已知条件已知数输入功p=58kw ,输入转速n 1=1000r/min ,齿数比u=5,齿轮的许用应力[δ]H =550Mpa ,许用弯曲应力[δ]F =400Mpa 。
3.建立优化模型3。
1问题分析及设计变量的确定由已知条件得求在满足零件刚度和强度条件下,使减速器体积最小的各项设计参数。
由于齿轮和轴的尺寸(即壳体内的零件)是决定减速器体积的依据,故可按它们的体积之和最小的原则建立目标函数.单机圆柱齿轮减速器的齿轮和轴的体积可近似的表示为:]3228)6.110(05.005.2)10(8.0[25.087)(25.0))((25.0)(25.0)(25.0222122212221222212212122221222120222222222121z z z z z z z z z z z g g z z d d l d d m u mz b bd m u mz b b d b u z m b d b z m d d d d l c d d D c b d d b d d b v +++---+---+-=++++-----+-=πππππππ 式中符号意义由结构图给出,其计算公式为b c d m umz d d d mumz D mz d mz d z z g g 2.0)6.110(25.0,6.110,21022122211=--==-===由上式知,齿数比给定之后,体积取决于b 、z 1 、m 、l 、d z1 和d z2 六个参数,则设计变量可取为T z z T d d l m z b x x x x x x x ][][211654321== 3。
2目标函数为min )32286.18.092.0858575.4(785398.0)(2625262425246316321251261231232123221→++++-+-+-+=x x x x x x x x x x x x x x x x x x x x x x x x x x f3.3约束条件的建立1)为避免发生根切,应有min z z ≥17=,得017)(21≤-=x x g2 )齿宽应满足max min ϕϕ≤≤d b ,min ϕ和max ϕ为齿宽系数d ϕ的最大值和最小值,一般取min ϕ=0。
单级圆柱齿轮减速器的优化设计
单级圆柱齿轮减速器的优化设计单级圆柱齿轮减速器是一种常见的机械传动装置,广泛应用于各种工业领域。
然而,随着科技的不断进步和实际应用需求的提高,对减速器的性能和效率也提出了更高的要求。
因此,对单级圆柱齿轮减速器进行优化设计具有重要的现实意义。
在传统的单级圆柱齿轮减速器设计中,主要传动比、扭矩和效率等指标。
然而,随着工业领域的不断发展,对减速器的要求也越来越高,包括更小的体积、更轻的重量、更高的强度和更低的噪音等。
为了满足这些要求,必须对减速器进行优化设计。
单级圆柱齿轮减速器的基本原理是利用齿轮的啮合传递动力,实现减速的目的。
在优化设计中,我们可以从以下几个方面进行分析和改进:齿轮强度:提高齿轮的强度是优化设计的关键之一。
可以采用更优质的材质、精确的齿形设计和适当的热处理工艺来提高齿轮的强度和寿命。
传动效率:通过优化齿轮的几何尺寸、降低齿轮副的摩擦系数和提高齿轮的制造精度,可以降低功率损失,提高传动效率。
噪音控制:采用低噪音齿轮、优化齿轮副的动态特性、避免共振等方法,可以有效降低减速器的噪音。
根据上述原理分析,可以采用以下优化设计方案:采用高强度材料,如渗碳或淬火钢,以提高齿轮强度和寿命。
通过计算机辅助设计软件,精确设计齿轮几何形状和尺寸,以降低啮合冲击和振动。
采用润滑性能良好的材料和精确的加工工艺,以减小摩擦损失。
通过改变齿轮宽度、改变齿轮副的动态特性和优化减震装置等措施,以降低减速器噪音。
为了验证优化设计方案的有效性,可进行实验验证。
实验中,可以测量减速器的传动效率、扭矩、噪音等指标,并将其与原设计进行对比分析。
实验结果表明,优化后的减速器在各方面均有所改善,具体数据如下:传动效率提高:优化后的减速器传动效率较原设计提高了10%以上。
扭矩增加:在相同的输入功率下,优化后的减速器输出扭矩增加了20%以上。
噪音降低:优化后的减速器噪音降低了20分贝以上。
通过对单级圆柱齿轮减速器的优化设计,可以显著提高其传动效率、增加输出扭矩并降低噪音。
- 1、下载文档前请自行甄别文档内容的完整性,平台不提供额外的编辑、内容补充、找答案等附加服务。
- 2、"仅部分预览"的文档,不可在线预览部分如存在完整性等问题,可反馈申请退款(可完整预览的文档不适用该条件!)。
- 3、如文档侵犯您的权益,请联系客服反馈,我们会尽快为您处理(人工客服工作时间:9:00-18:30)。
青岛理工大学琴岛学院机械优化设计课题名称:单级齿轮减速器的优化设计学院:机电工程系专业班级:机械设计及其自动化143 学号学生:指导老师:青岛理工大学教务处2016年11月 27日《单级齿轮减速器的优化设计》说明书摘要机械优化设计是一种非常重要的现代设计方法,能从众多的设计方案中找出最佳方案,从而大大提高设计的效率和质量。
每一种优化方法都是针对某一种问题而产生的,都有各自的特点和各自的应用领城。
常用的机械优化设计方法包括无约束优化设计方法、约束优化设计方法、基因遗传算方法等并提出评判的主要性能指标。
机械优化设计的目的是以最低的成本获得最好的效益,是设计工作者一直追求的目标,从数学的观点看,工程中的优化问题,就是求解极大值或极小值问题,亦即极值问题。
本文从优化设计的基本理论、优化设计与产品开发、优化设计特点及优化设计应用等方面阐述优化设计的基本方法理论。
关键词:机械优化设计;优化方法;优化应用。
目录摘要 (II)1设计任务 (1)2 齿轮的传统设计 (2)3优化设计的数学模型 (7)3.1确定设计变量和目标函数 (7)3.2确定约束条件 (7)4 Matlab计算机程序 (9)5结果分析 (11)参考文献 (12)1设计任务设计如图2-40所示的单级直齿圆柱齿轮减速器,其齿数比2.3u =,工作寿命要求10年两班制,原动机采用电动机,工作载荷均匀平稳,小齿轮材料为40Cr,调质后表面淬火,齿面硬度HB=235~275,MPa H 531][1=σ, MPa F 5.297][1=σ,大齿轮材料为45钢,调质,齿面硬度为HB=217~255,a 513][2MP H =σ,MPa F 4.251][2=σ,载荷系数k=1.3,P=28KN ,n=1440rad/min 要求在满足工作要求的前提下使两齿轮的重量最轻。
2 齿轮的传统设计一、按齿面接触疲劳强度设计 (1)由式子试算小齿轮分度圆直径,即][)][(*1u *2d 32111H H E H dH Z Z Z u T K σσφε-+≥ 1)确定公式中的各参数值1. 试选3.1K 1=H2. 计算小齿轮传递的转矩。
mmN mm N n P •⨯=•⨯⨯=⨯=466110569.181440/281055.9/1055.9T3. 查表并查图选取齿宽系数1=d ϕ,区域系数5.2=H Z ,材料的弹性影响系数MPa Z E 8.189= ,4. 计算接触疲劳强度用重合度系数εZ ︒=⨯+︒⨯=+=841.29)]1224/(20cos 24arccos[)]2/(cos arccos[*11a1a h z z αα︒=⨯+︒⨯=+=666.23)]1277/(20cos 77arccos[)]2/(cos arccos[*22a1a h z z ααπααααεα2/`)]tan (tan `)tan (tan [2111-+-=a a z z711.12/)]20tan 666.23(tan 77)20tan 841.29(tan 24[=︒-︒⨯+︒-︒⨯=π 873.03711.1434Z =-=-≥εε 5. 计算接触疲劳强度许用应力][H σ查图得小齿轮和大齿轮测接触疲劳极限分别为MPa m H 590][1l =σ、MPa m H 540][2l =σ计算应力循环次数:911101472.41030082(114406060N ⨯=⨯⨯⨯⨯⨯⨯==)h jL n9912 10293.1)24/77/(101472.4/N ⨯=⨯==u N查图取接触疲劳寿命系数90.01=HN K 、95.02=HN K 。
取失效概率为1%、安全系数S=1,由式子得MPa MP S K H HN H 531a 159090.0][1lim 11=⨯==σσMPa MP S K H HN H 513a 154095.0][2lim 22=⨯==σσ取1][H σ和2][H σ中的较小者作为该齿轮副的接触疲劳许用应力,即MPa 513][][21==H H σσ2) 试算小齿轮分度圆直径32111)][(*1u *2d σφεZ Z Z u T K E H dH +≥ mm )513873.08.1895.2(24/77124/77110948.93.12324⨯⨯⨯+⨯⨯⨯⨯=)()(mm466.74=(2)调整小齿轮分度圆直径 1)计算实际载荷系数前的数据准备。
1、圆周速度v 。
s m s m n d t /6.5/1000601440466.74100060v 11=⨯⨯⨯=⨯=ππ2、齿宽b.mmmm d t d 466.74466.741b 1=⨯==φ2)计算实际载荷系数u K 。
1、查表取使用系数1A =K 。
2、根据s m /6.5v =、7级精度,查图得动载荷系数2.1v =K 。
3、齿轮的圆周力。
N N d T t 3411 t110987.4466.74/10948.92/2F ⨯=⨯⨯==mmN mm N m N /100/9.66/466.74/10329.31b KF 3 t1 =⨯⨯=查表得齿间载荷分配系数2.1H =αK4、查表用插值法查得7级精度、小齿轮相对支承非对称布置时,得齿向载荷分布系数421.1H =βK 。
由此,得到实际载荷系数051.2421.12.12.11K K K K K H H v A H =⨯⨯⨯==βα3)由式子得,可得按实际载荷系数算得的分度圆直径mm K K H H 675.863.1051.2466.74d d 3t 11=⨯== 及相应的齿轮模数mmmm z d 611.324/675.86/m 11===二、按齿根弯曲疲劳强度设计 (1)由式子试算模数,即321111)][(*2m FSAFa d F Y Y z Y T K σφε≥ 1) 确定公式中的各参数值 1、试选3.1F1=K 。
2、由式子计算弯曲疲劳强度用重合度系数。
688.0711.175.025.075.025.0=+=+=εεεY 3、计算][F saFa Y Y σ。
查图得65.21=Fa Y 、23.22=Fa Y 。
应力修正系数58.11s =a Y 、76.12sa =Y 。
小齿轮和大齿轮的齿根弯曲疲劳极限分别为MPa im F 4901l =σ、MPa im F 4002l =σ。
弯曲疲劳寿命系数 85.01=FN K 、88.02=FN K 。
取弯曲疲劳安全系数S=1.4。
由式子得MPa MP S K F FN F 5.297a 4.149085.0][1lim 11=⨯==σσ MPa MP S K F FN F 4.251a 4.140088.0][2lim 22=⨯==σσ0141.05.29758.165.2][111=⨯=F sa Fa Y Y σ 0156.04.25176.123.2][222=⨯=F sa Fa Y Y σ 因为大齿轮的][F saFa Y Y σ大于小齿轮,所以取 0156.0][][222==F sa Fa F sa Fa Y Y Y Y σσ2)试算模数3243211110156.0241688.010948.93.12)][(*2m ⨯⨯⨯⨯⨯⨯=≥F SA Fa d F Y Y z Y T K σφεmm 080.2=(2)调整齿轮模数1)计算实际载荷系数前的数据准备。
1、圆周速度v 。
mm mm z 92.4924080.2m d 1t =⨯==s m s m n d t /76.3/100060144092..49100060v 11=⨯⨯⨯=⨯=ππ2、齿宽b 。
mmmm d d 92.4992.491b 1=⨯==φ3、宽高比b/hmm mm m c h da 68.4080.2)25.012()2(h 1**=⨯+⨯==67.1068.4/92.49b/h ==2) 计算实际载荷系数F K1、根据s m /76.3.v =,7级精度,查图得动载荷系数08.1v =K2、由NN d T t 3411 t11044.792.49/10948.92/2F ⨯=⨯⨯==,mmN m N mm N b /100/149/92.49/1044.71/F K 3 t1A =⨯⨯=,查表得齿间载荷分配系数0.1F =αK 。
3、查表用插值法查得417.1H =βK ,结合67.10b/=h 查图得34.1F =βK 。
则载荷系数为33.24.142.117.11K K K K K F F v A F =⨯⨯⨯==βα3)由式子,可得按实际载荷系数算得的齿轮模数mm K K F F 527.23.133.2080.2m m 3t 1=⨯== 对比计算结果,由齿面接触疲劳强度计算的模数m 大于由齿根弯曲疲劳强度计算的模数,由于齿轮模数m 的大小主要取决于弯曲疲劳强度所决定的承载能力,而齿面接触疲劳强度所决定的承载能力,仅与齿轮直径有关,可取由弯曲疲劳强度算得的模数mm 527.2并就近圆整为标准值mm 3=m ,按接触疲劳强度算得的分度圆直径mm 675.86d 1=,算出小齿轮齿数89.283/675.86/d z 11===m 。
取29z 1=,则大齿轮齿数4.92292.3z z 12=⨯==u ,取92z 2=,1z 与2z 互为质数。
这样设计出的齿轮传动,既满足了齿面接触疲劳强度,又满足齿根弯曲疲劳强度,并做到结构紧凑,避免浪费。
3优化设计的数学模型3.1确定设计变量和目标函数取设计变量和目标函数T d T z m x x x x ],,[],,[1321ϕ==,其中m 为齿轮模数,1z 为小齿轮齿数,d ϕ为齿宽系数。
设小齿轮分度圆直径为1d ,大齿轮分度圆直径为2d ,齿轮宽度为b ,要求圆柱齿轮的重量最轻,也就要求体积最小,因此可建立目标函数:4))(221b d d x f +=(π由齿数比12d d u =,齿宽系数1d d b =ϕ,目标函数转化为: 321d3128279.84))1)(x x x mz u x f =+=ϕπ((3.2确定约束条件(1)边界约束条件模数限制:1021≤≤x ; 齿数限制: 40202≤≤x ; 齿宽系数限制: 4.18.03≤≤x ;(2)性能约束接触疲劳强度的限制: 0][1u *2][-)g 3111≤-+==H d EH H H u d KT Z Z x σφσσ( 式中:H σ为齿面接触疲劳强度;K 为载荷系数,K=1.3;H Z 为节点区域系数,H Z =2.5;E Z 为弹性影响系数,E Z =189.8,代入以上参数得0550238.377717)(g 33231≤-=x x x x弯曲疲劳强度的限制:0][2][-2131≤-=F S F dF F Y Y z m KT σφσσ式中, 为齿根弯曲疲劳强度; 为齿形系数; 为齿根应力校正系数。