加氢工艺
化工工艺加氢与脱氢过程

化工工艺加氢与脱氢过程化工工艺是为了提高产品质量和生产效率而进行的一系列生产过程。
其中,加氢和脱氢是常见的化工反应过程,主要用于原料的转化和产品的改性。
以下将对加氢和脱氢过程进行详细介绍。
一、加氢过程加氢是指在反应中向化合物中加入氢气的过程。
该过程通常涉及氢气与有机物之间的反应,目的是将有机物中的不饱和键加氢饱和,或是将有机物中的官能团与氢气反应生成其他目标化合物。
1.加氢工艺的原理加氢工艺主要依靠催化剂来实现。
通常使用的催化剂是金属催化剂,如铜、镍、铱等。
这些催化剂能够吸附氢气分子,并为氢气分子提供吸附位点,从而促使氢气与有机物发生反应。
在反应中,催化剂可以提供活化能,使加氢反应得以进行。
2.加氢反应的应用加氢反应在化工工艺中具有广泛的应用。
常见的应用有:加氢脱气、重整反应、加氢裂化和加氢脱硫等。
(1)加氢脱气:将氢气加入原料中,去除其中的气体成分,从而降低气体浓度,达到控制反应环境的目的。
(2)重整反应:通过加氢反应,将低碳烃转化为高碳烃,从而提高产物的价值。
(3)加氢裂化:将高碳烃加氢后进行裂化,得到较小分子量的产物。
这样做不仅能提高燃料的质量,也能减少环境污染。
(4)加氢脱硫:将含硫化合物加氢后,使其转化为易于处理和回收的化合物,从而达到脱除硫化物的目的。
二、脱氢过程脱氢是指在化学反应中去除化合物中的氢原子的过程。
通常涉及碳氢化合物与氧化剂反应,形成不饱和化合物或氧化产物。
1.脱氢工艺的原理脱氢工艺主要依靠高温、高压和催化剂来实现。
脱氢反应需要高温和高压来提供足够的能量,以克服反应的活化能。
同时,催化剂的存在可以加速反应速率,降低反应温度和压力等条件。
2.脱氢反应的应用脱氢反应在化工工艺中也具有广泛的应用。
常见的应用有:脱氢加氢反应、脱氢氧化反应和脱氢重排等。
(1)脱氢加氢反应:通过去除部分氢原子,将饱和化合物转化为不饱和化合物,从而改变产物的性质和用途。
(2)脱氢氧化反应:通过去除氢原子和加入氧原子,使得有机物部分氧化为醛、酮或羧酸,从而提高产品的氧化潜能。
加氢工艺原理与操作课件
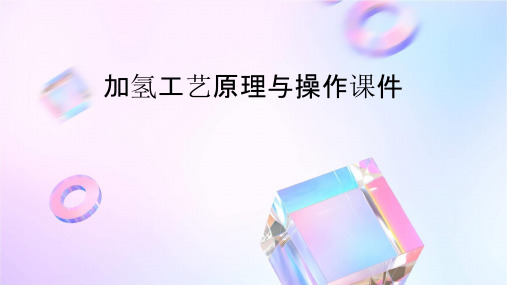
该石油公司针对现有加氢工艺流程进行优化,改进反应条件和操作参数,降低能耗和物耗,提高油品质量和产量。 同时,采用新型催化剂和反应器技术,提升加氢工艺的效率和稳定性。
某化学公司的加氢催化剂研究
总结词
研发高效加氢催化剂,降低生产成本。
详细描述
该化学公司开展加氢催化剂研究,通过实验和模拟手段探究催化剂活性组分、载体和制备方法对加氢 反应性能的影响。同时,优化催化剂的制备工艺,降低生产成本,为加氢工艺的广泛应用提供技术支 持。
高分子合成
在材料科学领域,加氢工艺可用于高分子合成的特定步骤,如聚合物链的加氢饱 和。通过加氢反应,可以提高聚合物的稳定性和性能。
04
加氢工艺的未来发展
加氢工艺的技术进步
01
02
03
高效催化剂
研发更高效、稳定的催化 剂,提高加氢反应的转化 率和选择性。
反应器优化
改进和优化反应器设计, 提高设备的传热和传质效 率,降低能耗。
催化剂的选择
根据不同的加氢反应类型和原料性 质,需要选择适宜的加氢催化剂以 保证反应的顺利进行和产物质量的 合格。
加氢工艺流程与设备
工艺流程
加氢工艺通常包括原料预处理、 反应、产物分离和精制等步骤, 各步骤之间通过管道和设备连接
形成完整的工艺流程。
主要设备
加氢工艺的主要设备包括反应器、 加热炉、压缩机、分馏塔等,这 些设备的性能和操作直接影响到 整个工艺过程的效率和产品的质 量。
氢气纯度与流量控制
加氢反应需要使用纯度较高的氢气,同时需要控制氢气的流量,以 保证反应的稳定和产物的质量。
加氢原料与产物的处理
原料预处理
加氢原料通常需要进行预处理, 如脱水和脱硫等,以去除杂质和 提高原料的质量。
加氢工艺流程
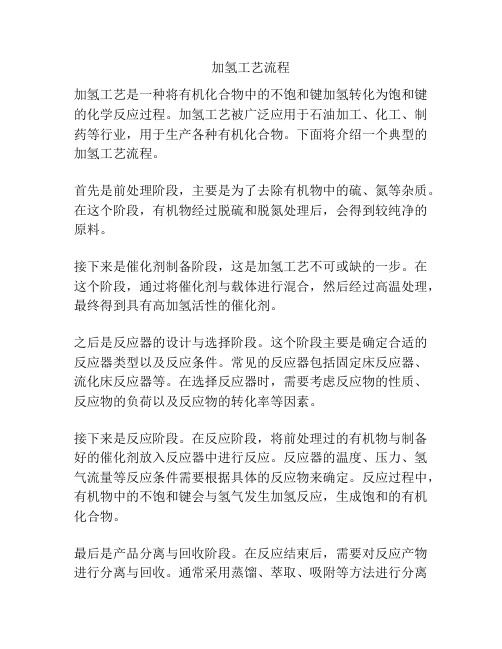
加氢工艺流程加氢工艺是一种将有机化合物中的不饱和键加氢转化为饱和键的化学反应过程。
加氢工艺被广泛应用于石油加工、化工、制药等行业,用于生产各种有机化合物。
下面将介绍一个典型的加氢工艺流程。
首先是前处理阶段,主要是为了去除有机物中的硫、氮等杂质。
在这个阶段,有机物经过脱硫和脱氮处理后,会得到较纯净的原料。
接下来是催化剂制备阶段,这是加氢工艺不可或缺的一步。
在这个阶段,通过将催化剂与载体进行混合,然后经过高温处理,最终得到具有高加氢活性的催化剂。
之后是反应器的设计与选择阶段。
这个阶段主要是确定合适的反应器类型以及反应条件。
常见的反应器包括固定床反应器、流化床反应器等。
在选择反应器时,需要考虑反应物的性质、反应物的负荷以及反应物的转化率等因素。
接下来是反应阶段。
在反应阶段,将前处理过的有机物与制备好的催化剂放入反应器中进行反应。
反应器的温度、压力、氢气流量等反应条件需要根据具体的反应物来确定。
反应过程中,有机物中的不饱和键会与氢气发生加氢反应,生成饱和的有机化合物。
最后是产品分离与回收阶段。
在反应结束后,需要对反应产物进行分离与回收。
通常采用蒸馏、萃取、吸附等方法进行分离与回收。
分离后的有机产物可以继续用于下一步的加工或应用。
总结起来,加氢工艺流程主要包括前处理、催化剂制备、反应器设计与选择、反应和产品分离与回收等阶段。
通过这些步骤,有机物中的不饱和键可以被加氢转化为饱和键,从而得到更加稳定和有用的有机化合物。
加氢工艺的广泛应用为石油加工、化工、制药等行业提供了重要的技术支持,为我们的生活带来了便利和发展。
加氢工艺安全
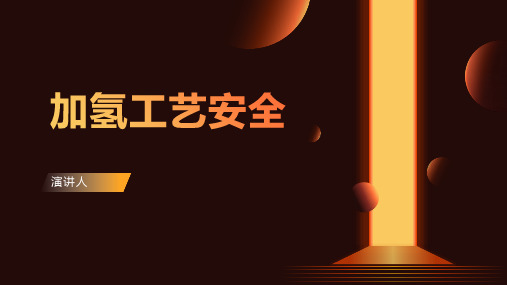
操作过程中必须穿 戴防护设备,如防 静电服、安全帽等
操作过程中必须遵 守操作规程,不得 擅自更改操作步骤
操作过程中必须注 意安全距离,避免 与设备、管线等发 生碰撞
操作过程中必须注 意防火、防爆,避 免产生火花、静电 等危险因素
操作过程中必须注 意通风,避免有毒 气体、粉尘等危害 健康
操作过程中必须注 意设备、管线的检 查与维护,确保设 备、管线处于良好 状态
操作过程中必须注 意紧急情况的处理, 如发生泄漏、火灾 等,必须按照应急 预案进行处置
安全防护措施
03
04
防静电设计:采用防静 电材料和设备,防止静 电火花引发事故
防泄漏设计:采用密封 设备,防止氢气泄漏
01
02
防火设计:设置防火设 施,防止火灾事故发生
防爆设计:采用防爆材 料和设备,防止爆炸事 故发生
金属冶炼行业:用于生产各种金 属,如铁、铜、镍等
化学工业:用于生产各种化学品, 如合成氨、甲醇等
环境保护行业:用于处理各种工 业废气、废水,如脱硫、脱硝等
加氢工艺的特点
高温高压:加氢工艺需要在高温高压下进行,以 提高反应速率和效率
催化剂:加氢工艺需要催化剂的参与,以提高反 应速率和选择性
反应条件苛刻:加氢工艺需要严格的反应条件控 制,以保证反应的顺利进行和安全
演讲人
01
02
03
04
1
加氢工艺的定义
加氢工艺是一种通过化学反应将氢气添加到 其他物质中的过程。
加氢工艺广泛应用于石油化工、煤化工、精 细化工等领域。
加氢工艺可以提高原料的利用率,降低生产 成本,提高产品质量。
加氢工艺可以提高生产过程的安全性和环 保性。
加氢工艺的应用
加氢的精制工艺流程

加氢的精制工艺流程
《加氢的精制工艺流程》
加氢是炼油行业中常用的一种精制工艺,它通过使用氢气将原油中的不饱和烃、硫化物和氮化物等杂质转化为饱和烃,从而提高油品的质量。
下面我们来详细介绍一下加氢的精制工艺流程。
1. 原料预处理
在加氢前,首先要对原油进行预处理。
这一步主要是将原油中的大分子杂质去除,以保护加氢催化剂的稳定性和活性。
通常采用脱蜡、脱沥青、脱硫等方法进行预处理。
2. 加氢反应
将经过预处理的原油送入加氢反应器中,与高压氢气接触,经过加氢反应器内的催化剂作用,不饱和烃、硫化物和氮化物等杂质被加氢转化为饱和烃以及硫化氢和氨。
这一步是整个加氢工艺的关键步骤,需要控制好反应器的温度、压力和氢气流量,才能获得理想的产品质量。
3. 分离和加工
加氢反应后的产物需要进行分离和加工,通常包括减压分离、氢气回收和产品升温卸催化剂等步骤。
其中,减压分离是将反应产物进行分离,得到干净的产品油和硫化氢等气体。
氢气回收可以将反应产生的氢气进行回收利用,节约能源。
产品升温卸催化剂则是将反应器内的催化剂进行再生,以保持其活性和稳定性。
4. 产品处理
最后得到的产品油需要进行进一步的处理,比如脱硫、脱氮、脱脂等工艺,以获得符合环保标准和市场需求的成品油。
通过上述精制工艺流程,原油中的不饱和烃、硫化物和氮化物等杂质得到有效转化和去除,从而提高了油品的质量和降低了环境污染。
加氢工艺成为了炼油行业中不可或缺的精制工艺之一。
加氢工艺安全
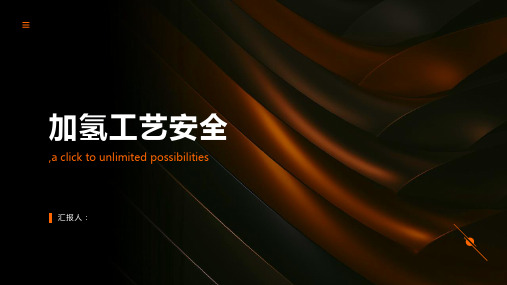
操作规程制定与执行
制定加氢工艺安全操作规程,明确各项安全要求和操作步骤。 对操作人员进行培训,确保他们熟悉并掌握操作规程。 定期对操作规程进行审查和更新,以适应新的安全要求和技术发展。 严格执行操作规程,确保加氢工艺的安全稳定运行。
定期维护与检查
设备检查:定期对加氢工艺设备进 行检查,确保设备正常运行
强化安全意识教 育
建立奖惩机制, 鼓励员工遵守安 全规定
定期开展安全活动
定期组织安全 培训:提高员 工的安全意识
和操作技能
开展应急演练: 提高员工应对 突发事件的能
力
定期检查设备: 确保设备正常 运行,避免因 设备故障导致
的安全事故
建立安全档案: 记录安全活动 和事故处理情 况,为后续工
作提供参考
03 加氢工艺的安全风险
氢气泄漏风险
氢气泄漏的危害:易燃易爆,对人体健康和环境造成威胁 泄漏原因分析:设备故障、操作失误、管道老化等 泄漏预防措施:加强设备维护保养,严格操作规程,定期检测氢气浓度 泄漏应急处理:迅速关闭阀门,通风排气,疏
氢气爆炸原理:氢 气与空气混合后, 在一定条件下会发 生爆炸
监管制度与标准
监管机构:明 确加氢工艺安 全监管的负责
机构
监管制度:建 立完善的加氢 工艺安全监管
制度
监管标准:制 定加氢工艺安 全监管的标准
和规范
监管措施:采 取有效的监管 措施,确保加
氢工艺安全
监管手段与方法
制定安全操作规程和安全管理制度,规范操作人员的行为。 对加氢工艺设备进行定期检查和维护,确保设备安全可靠。 建立应急预案,提高应对突发事件的能力。 加强安全培训和教育,提高操作人员的安全意识和技能水平。
07 总结与展望
加氢工艺原理与操作
加氢工艺原理与操作加氢工艺是一种利用氢气与物质发生反应,将其加氢处理的工艺。
加氢工艺主要应用于炼油、化工、制药等领域,可以改善产品性能,提高产品质量,降低环境污染。
加氢工艺的原理是利用氢气分子的活性和易于与其他物质发生反应的特性,将氢气从气态导入液态或固态物质中,与其发生反应,改变其物理性质或化学性质。
加氢工艺的操作主要包括氢气的供应,反应体系的控制和废气的处理。
氢气的供应是加氢工艺的基础。
一般情况下,氢气通过管道或气瓶输送到加氢设备中。
在输送过程中,需要进行氢气的压力和流量的调节,确保氢气供应的稳定性和适应性。
反应体系的控制是加氢工艺的关键。
反应体系的温度、压力、反应物浓度等参数对加氢反应的影响很大。
在加氢反应过程中,需要根据具体反应物的性质和反应条件的要求,进行温度、压力和反应物浓度的调控,以达到预期的加氢效果。
废气的处理是加氢工艺的一个重要环节。
加氢反应过程中,产生的废气中可能含有一定量的氢气和其他有害气体。
为了防止废气对环境的污染,需要进行废气的收集和处理。
一般情况下,废气通过抽气系统排放到废气处理设备中,经过吸附、洗涤等方法,将其中的有害物质去除或转化为无害物质,然后将净化后的气体排放到大气中。
加氢工艺具有广泛的应用前景。
在炼油领域,加氢工艺可以将高硫原油转化为低硫产品,降低汽油、柴油等燃油中硫含量,减少与空气中氧气反应生成二氧化硫的可能,从而降低大气污染物排放。
在化工领域,加氢工艺可以用于合成氨、加氢精制化学品等重要的工业化学过程。
在制药领域,加氢工艺可以用于合成药物,改善药物的药效和质量。
总结起来,加氢工艺是一种利用氢气与物质发生反应的工艺。
其原理是利用氢气分子的活性,改变物质的物理性质或化学性质。
加氢工艺的操作包括氢气的供应、反应体系的控制和废气的处理。
加氢工艺具有广泛应用前景,在炼油、化工、制药等领域有重要的应用价值。
加氢工艺技术
加氢工艺技术加氢工艺技术是一种重要的化工技术,在石油化工、化学工程等领域中得到广泛的应用。
其主要作用是将有机化合物中的不饱和键加氢,从而提高化合物的稳定性和降低其活性。
加氢工艺技术是一种催化反应技术,主要通过加入催化剂来促进反应的进行。
一般来说,加氢反应是在高压、高温和适当的催化剂条件下进行的。
其中,催化剂主要是金属催化剂,如铂、钯和铑等。
这些金属催化剂在反应中起到了催化作用,提高了反应速率和选择性。
加氢工艺技术主要应用于石油加工和石化行业。
在石油加工中,加氢工艺技术主要用于提炼高质量的石油产品。
通过加氢反应,可以降低石油中的硫、氮和重金属等杂质的含量,提高石油产品的质量。
同时,加氢工艺技术还可以将重质石油转化为轻质石油,提高石油产品的附加值。
在石化行业中,加氢工艺技术主要应用于合成有机化学品。
通过加氢反应,可以将不饱和烃类转化为饱和烃类。
这些饱和烃类具有较好的稳定性和活性,可以作为合成有机化学品的原料。
例如,通过加氢反应可以将乙烯转化为乙烷,乙烷是制备乙醇、乙二醇和丙酮等重要化学品的重要原料。
除了石油加工和石化行业,加氢工艺技术还在化学工程中得到广泛应用。
在化学工程中,加氢工艺技术主要用于合成高级材料和医药中间体。
通过加氢反应,可以将有机化合物中的活性基团转化为饱和基团,从而提高化合物的稳定性和降低其活性。
这对于有机合成和药物研发具有重要的意义。
加氢工艺技术具有很高的技术含量和经济效益。
通过加氢反应可以提高石油产品的质量、降低污染物的含量,同时还可以提高合成有机化学品的产率和选择性。
因此,加氢工艺技术在石化和化工行业中具有广阔的应用前景。
总之,加氢工艺技术是一种重要的化工技术,主要应用于石油加工和化学工程中。
通过加氢反应,可以提高石油产品的质量,降低有机化合物的活性,从而提高化合物的稳定性和降低其附加值。
加氢工艺技术具有很高的技术含量和经济效益,在石化和化工领域中具有广阔的应用前景。
加氢工艺流程简述
加氢工艺流程简述
加氢工艺流程简述
加氢工艺流程是指利用氢气和氢氧根离子之间的化学反应来制备和储存氢气的方法。
氢气是一种无色、无臭、无味的气体,具有良好的爆炸性和流动性,因此在能源生产、化学合成、交通运输等领域中有着广泛的应用。
加氢工艺流程通常包括以下几个步骤:
1. 氢气预处理:将原料气体(如空气、氨气、甲醇等)通过过滤器和活性炭等吸附剂去除水分和杂质,制备出清洁的氢气。
2. 加氢:将预处理后的氢气加入加氢装置中,通过加氢炉等设备将氢气加至适当的浓度。
加氢过程中需要使用高压氢气来防止氢气爆炸,同时需要控制氢气的流速和压力以保证反应的平稳和安全。
3. 分离和纯化:在加氢反应结束后,需要对氢气进行分离和纯化,以获得高纯度的氢气。
分离和纯化的过程包括蒸馏、减压蒸馏、离子交换、活性炭吸附等技术。
4. 储存和运输:纯化的氢气可以用于燃料电池、化工合成、能源储备等领域。
在储存和运输过程中,需要使用高压、低温等方式保证氢气的安全性和可靠性。
加氢工艺流程的优点是反应速率快、反应温度低、反应效率高、的产物质量好,同时可以避免高温、高压和有毒的反应条件,因此被广泛应用于燃料电池、化学工业和交通运输等领域。
随着加氢技术的不断发展,加氢工艺流程也在不断创新,例如利用太阳能、风能等可再生能源进行加氢、利用超高压加氢技术提高加氢效率等。
加氢工艺的原理和作用
加氢工艺的原理和作用1. 加氢工艺的概述加氢工艺是一种化学反应过程,通过向化合物中添加氢气,将其转化为更稳定、更有用的化合物。
加氢工艺广泛应用于石油和化工行业,用于改善和增强原料的性质,提高产品品质以及降低环境污染。
在加氢工艺中,常见的反应类型包括饱和加氢、脱硫加氢、脱氧加氢等。
这些反应可通过催化剂促进,在适当的温度和压力条件下进行。
2. 加氢反应的基本原理加氢反应是一种典型的还原反应,其基本原理可归结为以下几个方面:a) 氧化还原反应加氢过程是一种典型的氧化还原反应,其中有机物(通常是烃类)中的碳-碳键或碳-氧键被断裂,并与来自氢源(通常是分子态H2)的两个质子(H+)结合形成新的碳-碳或碳-氧键。
这个过程导致了有机物结构的改变,产生了更稳定的化合物。
b) 催化剂作用加氢反应通常需要催化剂的存在。
催化剂能够降低反应的活化能,提高反应速率,并促进有机物与氢气之间的相互作用。
常用的加氢催化剂包括铂、钯、镍等过渡金属。
c) 温度和压力控制加氢反应需要在适当的温度和压力条件下进行。
温度和压力对反应速率、平衡转化率以及产品选择性等方面都有重要影响。
高温有助于提高反应速率,但也容易导致副反应和催化剂失活;高压可以增加氢气溶解度,提高反应速率和平衡转化率。
3. 加氢工艺的作用a) 改善燃料质量加氢工艺可用于改善燃料质量,特别是涉及到石油精炼过程中的重油和残油。
通过饱和加氢反应,可将其中的不饱和烃类(如芳烃)转化为饱和烃类,降低其凝点、闪点和燃烧性能,提高燃料的稳定性和可燃性。
b) 脱硫和脱氮加氢工艺在石油和化工行业中广泛应用于脱硫和脱氮过程。
硫和氮是常见的污染物,会导致环境污染和催化剂失活。
通过加氢反应,可以将有机硫化物和有机氮化物转化为相对较稳定的化合物,降低其对环境的危害,并保护催化剂的活性。
c) 氢添加反应加氢工艺还可用于在有机分子中引入新的氢原子。
这种反应称为氢添加反应,可改变有机分子的结构、功能和性质。
- 1、下载文档前请自行甄别文档内容的完整性,平台不提供额外的编辑、内容补充、找答案等附加服务。
- 2、"仅部分预览"的文档,不可在线预览部分如存在完整性等问题,可反馈申请退款(可完整预览的文档不适用该条件!)。
- 3、如文档侵犯您的权益,请联系客服反馈,我们会尽快为您处理(人工客服工作时间:9:00-18:30)。
对加氢反应过程起作用的是反应物流中的氢分压 一般以反应器入口的氢分压为基准 氢分压的提高有利于提高加氢分压的深度,如脱氮、
芳烃饱和、裂化等,并抑制生焦反应有利于延长 催化剂寿命 目前装置提高氢分压的途径:提高补充氢纯度,降 低循环氢中非氢组分的含量,增加循环氢流量提 高氢油比等。
1.5操作参数对加氢反应的影响—压力
2.3飞温—危害
飞温会致使催化剂结构受到破坏,反应 系统的设备造成损伤,高压法兰高温变 形泄漏等。
加拿大石油炼制公司曾发生反应器“飞温” 事故,造成反应器大面积堆焊层剥离和 347SS堆焊层熔敷金属裂纹和破坏现象
2.3飞温的防范措施
在床层温度异常升高初期,只要及时发现并立 刻采取降温措施如打入大量冷氢、降低炉温等, 是可以控制住温度骤升的。因此DCS监盘人员 对裂化床层所有温度指示点都要时刻监视。
反应系统温度、压力的大幅波动易使高压法兰 发生泄漏,正常操作时要平稳控制
开停工过程中的升温升压和降温降压速度过快 也会造成泄漏,所以要按规定速度操作
2.2临氢系统泄漏的防范措施
高压高温法兰面积都很大,泄漏起火后不能用 冷却法灭火,那会使设备变形后泄漏更严重。 如曾发生过加氢裂化装置雷雨天晃电联锁自启, 反应器热量大幅变化,同时暴雨使R1101出口 法兰泄漏。
5、烷烃的加氢裂化在其正碳离子的β位处断链,很少生 成 C3 以下的低分子烃,加氢裂化的干气收率低;
6、非烃化合物基本上完全转化,烯烃也基本加氢饱和, 加氢裂化的产品质量好。
1.2加氢过程反应热
加氢过程是放热反应,主要反应的平均反应热
(单位:1×107J/kmol) 烯烃加氢饱和 10.47 芳烃加氢饱和 3.256 加氢脱硫 6.978 加氢脱氮 9.304 环烷烃加氢开环 0.93 烷烃加氢裂化 1.477×107J/mol分子增加
MoO3+H2+2H2S = MoS2+3H2O 3NiO+H2+2H2S = Ni3S2+3H2O WO3+H2+2H2S = WS2+3H2O
正常生产时必须保持催化剂在硫环境下操作
1.4加氢催化剂
加氢裂化催化剂是双功能催化剂,具备 加氢活性和酸性,实现加氢裂化反应, 酸性由载体提供。
我厂96年开工用的3825为轻油型催化剂,2002 年全部更换为中油型催化剂3976。差别在于酸 性强度不同,裂化活性的高低。
1.5操作参数对加氢反应的影响
反应温度
反应温度对加氢反应影响很大,提高反应温度, 会加快反应速度和提高转化率。
WABT—重量加权平均温度
=∑ 每床层平均温度×(单床层催化剂重量/催化剂总重量)
对于加氢裂化反应器,最理想状态是控制每个床 层的入口温度和床层温升相同,实现产品分布 的最佳
1.5操作参数对加氢反应的影响
饱和率,%
100 90 80 70 60 50 40 30 20 10 0 4
总芳烃饱和率,% 双环以上饱和率,% 三环以上饱和率,%
6
8
试验条件: 沙中VGO原料油 RN-2催化剂 反应温度380℃
体积空速1.0h-1 氢油比800v/v
10
12
14
16
氢分压,MPa
1.5操作参数对加氢反应的影响—压力
2.4高压临氢设备损伤的防范
工艺操作必须要保护设备。
在正常生产和开停工和检修过程中有很多工艺操 作规定,都是针对设备保护的:如开停工过程中 温度和压力的升降速度要求、氢气加热炉管壁 温度<550℃等等。有些操作容易被忽视,短 期内也看不出后果,但对设备的长远影响却是 很大的,所以必须要严格按规定操作,避免设 备损伤
1.3加氢装置临氢系统流程
我厂加氢裂化装置临氢系统为单段串联一次通 过流程,,即通常所说的SSOT。
目前的问题是改造后空冷器为6组,易出现偏流 正常设计应为4组或8组
我厂柴油加氢精制装置除反应器外临氢系统流 程与加氢裂化相似,所不同的是炉前混氢,须 注意防止炉管内结焦
1.4加氢催化剂
催化剂有生产初期(SOR)和生产末期(EOR) 的差异:催化剂随运转时间的增长,催化剂的 活性逐步下降,需要提高温度来弥补活性的损 失,而同时操作苛刻度和产品分布也逐渐变差, 到达末期时需要换剂或再生。
1992年,日本富士石油公司一台螺纹锁紧式高 压换热器,因检修与维护不当,造成垫片压板 变形,引起氢气泄露,导致爆炸和火灾,造成 10人死亡,7人受伤。(辽化几年前也发生过 类似事故)
2.2临氢系统泄漏的防范措施
预防泄漏事故的最好方法就是精心检查。在开 工过程的气密和正常生产状态的巡检测漏做到 有耐心精心和全面,及时发现漏点,正确处理 防止扩大
2.5工艺联锁系统
火炬排放系统是加氢装置的生命线,生 产过程中必须时刻保持流程畅通
需经常检查阀门状态、火炬罐液位等 紧急泄压系统 1)0.7MPa/min泄压联锁 自动启动:当循环氢压缩机停运时联锁自启 手动启动:循环氢压缩机不停
2.5工艺联锁系统
联锁启动后的动作:
0.7MPa/min泄压阀KV1101打开 加氢进料泵P1101自动停运;液力透平切断阀XCV601关,
空速
空速代表着反应物流在催化剂上停留时间 的长短,空速减小则停留时间增长反应 程度加深。空速与温度的作用互补。
加氢裂化反应中必须要遵守 先提量后提温, 先降温后降量的操作原则。
2、加氢装置特点及生产管理重点
加氢裂化是炼油装置中爆炸和火灾危险性 最高的甲类装置,高压、。
高温氢腐蚀 氢脆 高温硫化氢腐蚀 连多硫酸引起的应力腐蚀开裂 铬—钼钢的回火脆性 奥氏体不锈钢堆焊层的氢致剥离
2.4高压临氢设备的损伤—典型案例
80年代,日本鹿岛炼厂一重油加氢脱硫装置的 管道破裂,发生重大火灾爆炸事故。经分析为 氢腐蚀造成
国内炼厂出现过的设备损伤事故如:因重整氢 Cl-离子应力腐蚀,造成氢气加热炉管爆裂和高 换底部排凝泄漏的火灾事故;高换结垢氢气加 热炉炉管超温爆裂事故;75年石油三厂压缩机 出口管线选错材质,又未进行热处理,导致弯 曲部分管段炸裂,氢气爆炸9人死亡
2.1高压窜低压—典型事故
▪ 1987年英国一加氢裂化装置在联锁后恢复进料 过程中操作不当将高分液位调节阀置于手动全 开状态,使高分液位压空,且高分低液位开关 和切断阀未正常投用,造成低分猛烈爆炸,损 失7850万美元
▪ 1995年,辽化加氢裂化装置首次开工过程中高 压分离器排放酸性水时造成串压,导致下游装 置的酸性水罐爆炸飞起。
成小分子的烷烃及环烷-芳烃; 2、两环以上的环烷烃,发生开环裂解、异构,最终生成
单环环烷烃及较小分子的烷烃; 3、单环芳烃、环烷烃比较稳定,不易加氢饱和、开环,
主要是断侧链或侧链异构,并富集在石脑油中;
1.1加氢过程的化学反应-裂化反应特点续
4、烷烃异构、裂化同时进行,反应生成物中的异构烃含 量多,异/正比高;
1.1加氢过程的化学反应
加氢精制反应中非烃化合物的反应难易程度, 从易到难为: 脱硫>脱氧>脱氮
含氮化合物大致可以分为 碱性杂环化合物:脂肪胺及芳香胺类,吡啶、喹
啉等 非碱性氮化物:吡咯、咔唑等 后精制反应,脱除裂化过程中生成的硫醇
R=CH+H2S—— R-SH
1.1加氢过程的化学反应
加氢裂化的化学反应具有如下特点: 1、多环芳烃加氢裂化以逐环加氢/开环的方式进行,生
加氢装置工艺技术
加氢工艺技术
加氢基础理论 加氢装置特点及管理重点 开停工过程注意事项 异常现象处理
1、加氢技术有关理论知识
加氢过程的化学反应 临氢系统流程 加氢催化剂 操作参数对加氢过程的影响
1.1加氢过程的化学反应
加氢精制反应器中发生的化学反应
加氢脱硫反应 加氢脱氮反应 含氧化合物的氢解反应 加氢脱金属反应 不饱和烃的加氢饱和反应
产品氮含量, ppm
550 500 450 400 350 300 250 200 150 100 50
0
5
10
15
20
氢分压, MPa
1.5操作参数对加氢反应的影响
氢油比
氢油比的影响实质上与氢分压相同。但氢油比过 高后对增加系统氢分压已无贡献,反而增加能 耗。
对于我厂加氢裂化装置的现状,要想办法增加裂 化催化剂床层的氢油比,其手段是在温度允许 的情况下尽量增加冷氢注入量
1.4加氢催化剂
引起加氢催化剂失活的原因主要有:碳沉积、金 属沉积、杂质污染、碱性中毒、金属形态变化
碱性物质,如碱性氮化合物吸附在加氢裂化催 化剂的酸性中心上引起中毒,影响裂化反应。
原料中的杂质,如焦粉等固体颗粒堵塞催化剂 孔口,覆盖活性中心
上游装置腐蚀所带入的铁,造成床层堵塞压降 增大;硫化铁具有强的脱氢活性,促进生焦
处理较小的漏项时如紧固螺栓丝堵等要注意防 止方法不当造成漏项扩大,如7月15日柴油加
氢空冷泄漏。
高压液位计压力表的一次阀保持最小开度(如 96年9.28玻璃板破裂)
2.3飞温
飞温现象:
加氢裂化是强放热反应,温度的提高又加速了反 应的进行,据研究:裂化床层温度超过正常 12-13℃,反应速度提高一倍;如果温度超出 25℃ 反应速度提高四倍。反应温度异常升高 后烃分子连续不断的进行裂化反应,将引起温 度骤升,很难控制住。严重时在几分钟内内床 层温度会升到800度,。
2.1高压窜低压的防范—续
与高压系统相连的有关操作还包括原料油泵、新 氢压缩机,注水泵的启机和切换。这些系统虽都 安装有单向止回阀,但绝不能完全相信依赖单向 阀,在启动和切换机泵时,必须严格按操作法执 行,两人以上操作,时刻保证管路内压力与主临 氢系统的平衡,防止单向阀失灵造成压力倒窜。
1966年大庆加氢裂化装置由于切换油泵期间,泵不 上量,而泵出口未装止回阀,造成高压氢气倒泄 到油泵房,引发爆炸,装置被毁伤亡惨重