浅谈双色注塑成型工艺
双色注塑工艺原理
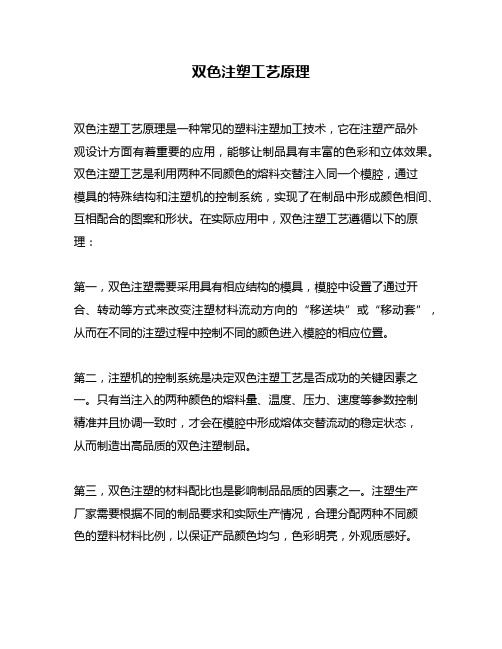
双色注塑工艺原理
双色注塑工艺原理是一种常见的塑料注塑加工技术,它在注塑产品外
观设计方面有着重要的应用,能够让制品具有丰富的色彩和立体效果。
双色注塑工艺是利用两种不同颜色的熔料交替注入同一个模腔,通过
模具的特殊结构和注塑机的控制系统,实现了在制品中形成颜色相间、互相配合的图案和形状。
在实际应用中,双色注塑工艺遵循以下的原理:
第一,双色注塑需要采用具有相应结构的模具,模腔中设置了通过开合、转动等方式来改变注塑材料流动方向的“移送块”或“移动套”,从而在不同的注塑过程中控制不同的颜色进入模腔的相应位置。
第二,注塑机的控制系统是决定双色注塑工艺是否成功的关键因素之一。
只有当注入的两种颜色的熔料量、温度、压力、速度等参数控制
精准并且协调一致时,才会在模腔中形成熔体交替流动的稳定状态,
从而制造出高品质的双色注塑制品。
第三,双色注塑的材料配比也是影响制品品质的因素之一。
注塑生产
厂家需要根据不同的制品要求和实际生产情况,合理分配两种不同颜
色的塑料材料比例,以保证产品颜色均匀,色彩明亮,外观质感好。
总之,双色注塑工艺的原理是通过模具的设计和注塑机的控制系统在模腔中实现两种不同颜色熔体交替流动,并在制品表面呈现出颜色相间、层次丰富的图案或形状。
这种技术可以广泛应用于汽车零部件、医疗器械、家用电器等制品生产中,提高了产品档次和附加值。
双色成型原理
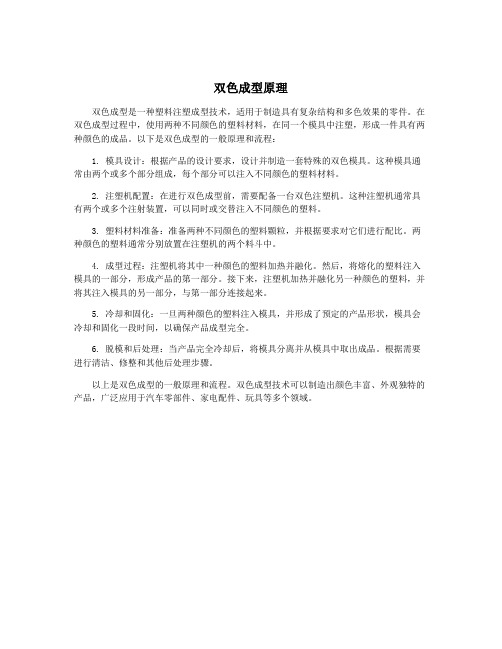
双色成型原理
双色成型是一种塑料注塑成型技术,适用于制造具有复杂结构和多色效果的零件。
在双色成型过程中,使用两种不同颜色的塑料材料,在同一个模具中注塑,形成一件具有两种颜色的成品。
以下是双色成型的一般原理和流程:
1. 模具设计:根据产品的设计要求,设计并制造一套特殊的双色模具。
这种模具通常由两个或多个部分组成,每个部分可以注入不同颜色的塑料材料。
2. 注塑机配置:在进行双色成型前,需要配备一台双色注塑机。
这种注塑机通常具有两个或多个注射装置,可以同时或交替注入不同颜色的塑料。
3. 塑料材料准备:准备两种不同颜色的塑料颗粒,并根据要求对它们进行配比。
两种颜色的塑料通常分别放置在注塑机的两个料斗中。
4. 成型过程:注塑机将其中一种颜色的塑料加热并融化。
然后,将熔化的塑料注入模具的一部分,形成产品的第一部分。
接下来,注塑机加热并融化另一种颜色的塑料,并将其注入模具的另一部分,与第一部分连接起来。
5. 冷却和固化:一旦两种颜色的塑料注入模具,并形成了预定的产品形状,模具会冷却和固化一段时间,以确保产品成型完全。
6. 脱模和后处理:当产品完全冷却后,将模具分离并从模具中取出成品。
根据需要进行清洁、修整和其他后处理步骤。
以上是双色成型的一般原理和流程。
双色成型技术可以制造出颜色丰富、外观独特的产品,广泛应用于汽车零部件、家电配件、玩具等多个领域。
双色注塑工作原理
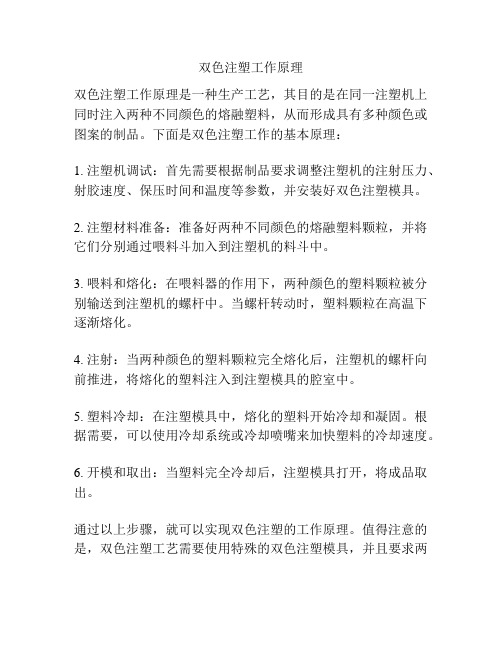
双色注塑工作原理
双色注塑工作原理是一种生产工艺,其目的是在同一注塑机上同时注入两种不同颜色的熔融塑料,从而形成具有多种颜色或图案的制品。
下面是双色注塑工作的基本原理:
1. 注塑机调试:首先需要根据制品要求调整注塑机的注射压力、射胶速度、保压时间和温度等参数,并安装好双色注塑模具。
2. 注塑材料准备:准备好两种不同颜色的熔融塑料颗粒,并将它们分别通过喂料斗加入到注塑机的料斗中。
3. 喂料和熔化:在喂料器的作用下,两种颜色的塑料颗粒被分别输送到注塑机的螺杆中。
当螺杆转动时,塑料颗粒在高温下逐渐熔化。
4. 注射:当两种颜色的塑料颗粒完全熔化后,注塑机的螺杆向前推进,将熔化的塑料注入到注塑模具的腔室中。
5. 塑料冷却:在注塑模具中,熔化的塑料开始冷却和凝固。
根据需要,可以使用冷却系统或冷却喷嘴来加快塑料的冷却速度。
6. 开模和取出:当塑料完全冷却后,注塑模具打开,将成品取出。
通过以上步骤,就可以实现双色注塑的工作原理。
值得注意的是,双色注塑工艺需要使用特殊的双色注塑模具,并且要求两
种颜色的塑料具有相同的熔融温度和流动特性,以确保制品的质量和外观。
双色模具注塑原理
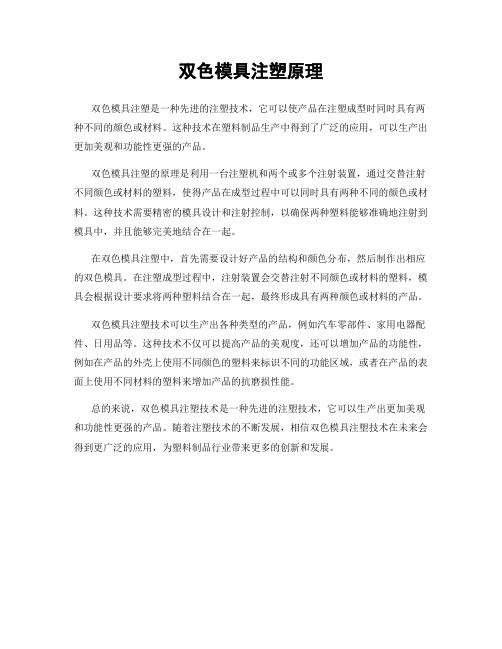
双色模具注塑原理
双色模具注塑是一种先进的注塑技术,它可以使产品在注塑成型时同时具有两种不同的颜色或材料。
这种技术在塑料制品生产中得到了广泛的应用,可以生产出更加美观和功能性更强的产品。
双色模具注塑的原理是利用一台注塑机和两个或多个注射装置,通过交替注射不同颜色或材料的塑料,使得产品在成型过程中可以同时具有两种不同的颜色或材料。
这种技术需要精密的模具设计和注射控制,以确保两种塑料能够准确地注射到模具中,并且能够完美地结合在一起。
在双色模具注塑中,首先需要设计好产品的结构和颜色分布,然后制作出相应的双色模具。
在注塑成型过程中,注射装置会交替注射不同颜色或材料的塑料,模具会根据设计要求将两种塑料结合在一起,最终形成具有两种颜色或材料的产品。
双色模具注塑技术可以生产出各种类型的产品,例如汽车零部件、家用电器配件、日用品等。
这种技术不仅可以提高产品的美观度,还可以增加产品的功能性,例如在产品的外壳上使用不同颜色的塑料来标识不同的功能区域,或者在产品的表面上使用不同材料的塑料来增加产品的抗磨损性能。
总的来说,双色模具注塑技术是一种先进的注塑技术,它可以生产出更加美观和功能性更强的产品。
随着注塑技术的不断发展,相信双色模具注塑技术在未来会得到更广泛的应用,为塑料制品行业带来更多的创新和发展。
双色注塑原理
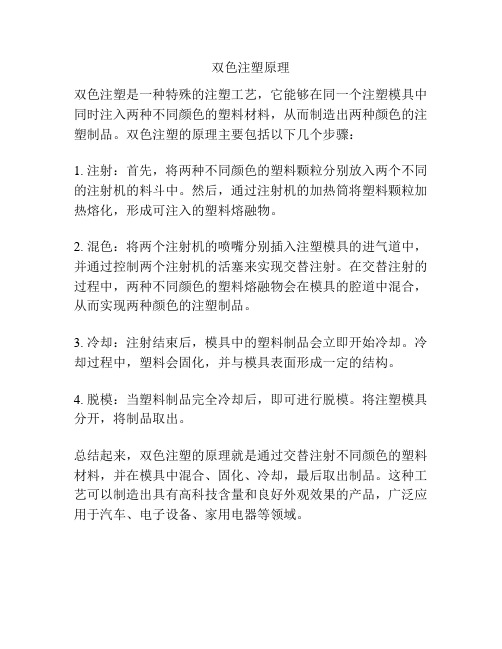
双色注塑原理
双色注塑是一种特殊的注塑工艺,它能够在同一个注塑模具中同时注入两种不同颜色的塑料材料,从而制造出两种颜色的注塑制品。
双色注塑的原理主要包括以下几个步骤:
1. 注射:首先,将两种不同颜色的塑料颗粒分别放入两个不同的注射机的料斗中。
然后,通过注射机的加热筒将塑料颗粒加热熔化,形成可注入的塑料熔融物。
2. 混色:将两个注射机的喷嘴分别插入注塑模具的进气道中,并通过控制两个注射机的活塞来实现交替注射。
在交替注射的过程中,两种不同颜色的塑料熔融物会在模具的腔道中混合,从而实现两种颜色的注塑制品。
3. 冷却:注射结束后,模具中的塑料制品会立即开始冷却。
冷却过程中,塑料会固化,并与模具表面形成一定的结构。
4. 脱模:当塑料制品完全冷却后,即可进行脱模。
将注塑模具分开,将制品取出。
总结起来,双色注塑的原理就是通过交替注射不同颜色的塑料材料,并在模具中混合、固化、冷却,最后取出制品。
这种工艺可以制造出具有高科技含量和良好外观效果的产品,广泛应用于汽车、电子设备、家用电器等领域。
双色注塑模工艺分析及模具设计
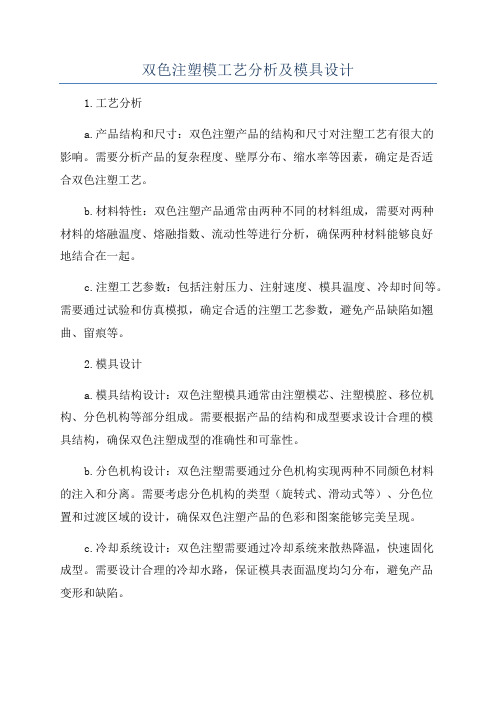
双色注塑模工艺分析及模具设计
1.工艺分析
a.产品结构和尺寸:双色注塑产品的结构和尺寸对注塑工艺有很大的
影响。
需要分析产品的复杂程度、壁厚分布、缩水率等因素,确定是否适
合双色注塑工艺。
b.材料特性:双色注塑产品通常由两种不同的材料组成,需要对两种
材料的熔融温度、熔融指数、流动性等进行分析,确保两种材料能够良好
地结合在一起。
c.注塑工艺参数:包括注射压力、注射速度、模具温度、冷却时间等。
需要通过试验和仿真模拟,确定合适的注塑工艺参数,避免产品缺陷如翘曲、留痕等。
2.模具设计
a.模具结构设计:双色注塑模具通常由注塑模芯、注塑模腔、移位机构、分色机构等部分组成。
需要根据产品的结构和成型要求设计合理的模
具结构,确保双色注塑成型的准确性和可靠性。
b.分色机构设计:双色注塑需要通过分色机构实现两种不同颜色材料
的注入和分离。
需要考虑分色机构的类型(旋转式、滑动式等)、分色位
置和过渡区域的设计,确保双色注塑产品的色彩和图案能够完美呈现。
c.冷却系统设计:双色注塑需要通过冷却系统来散热降温,快速固化
成型。
需要设计合理的冷却水路,保证模具表面温度均匀分布,避免产品
变形和缺陷。
d.模具材料选择:双色注塑模具通常由优质的工具钢制成,需要根据
产品的批量和质量要求,选择合适的模具材料,以确保模具寿命和成型效果。
以上就是双色注塑模工艺分析及模具设计的简要介绍。
在实际生产中,还需要通过试制和改进不断优化工艺和模具设计,提高双色注塑产品的质
量和产能。
双色模具注塑成型及设计,你了解多少?
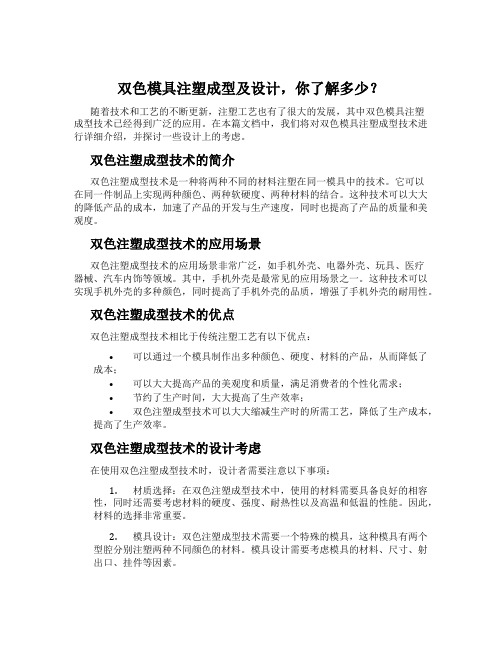
双色模具注塑成型及设计,你了解多少?随着技术和工艺的不断更新,注塑工艺也有了很大的发展,其中双色模具注塑成型技术已经得到广泛的应用。
在本篇文档中,我们将对双色模具注塑成型技术进行详细介绍,并探讨一些设计上的考虑。
双色注塑成型技术的简介双色注塑成型技术是一种将两种不同的材料注塑在同一模具中的技术。
它可以在同一件制品上实现两种颜色、两种软硬度、两种材料的结合。
这种技术可以大大的降低产品的成本,加速了产品的开发与生产速度,同时也提高了产品的质量和美观度。
双色注塑成型技术的应用场景双色注塑成型技术的应用场景非常广泛,如手机外壳、电器外壳、玩具、医疗器械、汽车内饰等领域。
其中,手机外壳是最常见的应用场景之一。
这种技术可以实现手机外壳的多种颜色,同时提高了手机外壳的品质,增强了手机外壳的耐用性。
双色注塑成型技术的优点双色注塑成型技术相比于传统注塑工艺有以下优点:•可以通过一个模具制作出多种颜色、硬度、材料的产品,从而降低了成本;•可以大大提高产品的美观度和质量,满足消费者的个性化需求;•节约了生产时间,大大提高了生产效率;•双色注塑成型技术可以大大缩减生产时的所需工艺,降低了生产成本,提高了生产效率。
双色注塑成型技术的设计考虑在使用双色注塑成型技术时,设计者需要注意以下事项:1.材质选择:在双色注塑成型技术中,使用的材料需要具备良好的相容性,同时还需要考虑材料的硬度、强度、耐热性以及高温和低温的性能。
因此,材料的选择非常重要。
2.模具设计:双色注塑成型技术需要一个特殊的模具,这种模具有两个型腔分别注塑两种不同颜色的材料。
模具设计需要考虑模具的材料、尺寸、射出口、挂件等因素。
3.工艺控制:双色注塑成型技术需要精确定位两个型腔,保证注塑的多种材料能够精准的覆盖到所需的位置,这需要高超的工艺控制水平。
双色注塑成型技术的未来双色注塑成型技术在未来将继续得到广泛的应用,随着工艺和技术的不断推进,它可以用于更多的领域,从而提高产品的质量和美观度,满足消费者的个性化需求,同时也可以大大缩减生产周期,降低生产成本。
双色注塑成型工艺
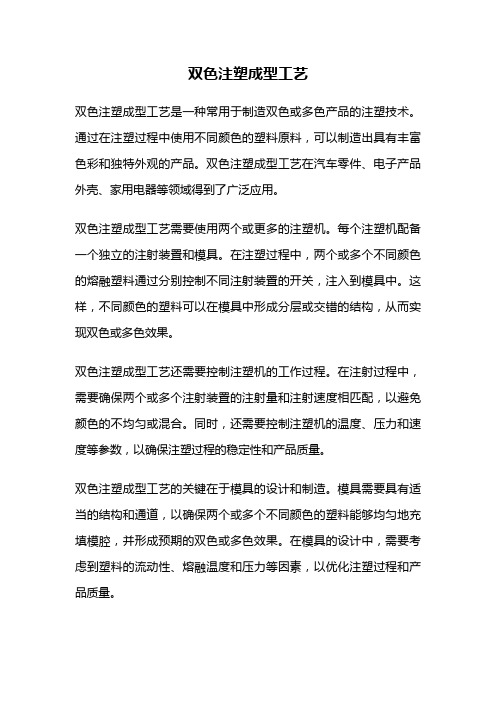
双色注塑成型工艺双色注塑成型工艺是一种常用于制造双色或多色产品的注塑技术。
通过在注塑过程中使用不同颜色的塑料原料,可以制造出具有丰富色彩和独特外观的产品。
双色注塑成型工艺在汽车零件、电子产品外壳、家用电器等领域得到了广泛应用。
双色注塑成型工艺需要使用两个或更多的注塑机。
每个注塑机配备一个独立的注射装置和模具。
在注塑过程中,两个或多个不同颜色的熔融塑料通过分别控制不同注射装置的开关,注入到模具中。
这样,不同颜色的塑料可以在模具中形成分层或交错的结构,从而实现双色或多色效果。
双色注塑成型工艺还需要控制注塑机的工作过程。
在注射过程中,需要确保两个或多个注射装置的注射量和注射速度相匹配,以避免颜色的不均匀或混合。
同时,还需要控制注塑机的温度、压力和速度等参数,以确保注塑过程的稳定性和产品质量。
双色注塑成型工艺的关键在于模具的设计和制造。
模具需要具有适当的结构和通道,以确保两个或多个不同颜色的塑料能够均匀地充填模腔,并形成预期的双色或多色效果。
在模具的设计中,需要考虑到塑料的流动性、熔融温度和压力等因素,以优化注塑过程和产品质量。
双色注塑成型工艺的优点在于能够制造出具有高级外观和独特效果的产品。
通过合理设计和选择不同颜色的塑料,可以实现丰富的色彩组合和渐变效果,提升产品的视觉吸引力和市场竞争力。
另外,双色注塑成型工艺还可以减少产品的组装和加工工序,提高生产效率和降低成本。
然而,双色注塑成型工艺也存在一些挑战和限制。
首先,模具的制造成本较高,特别是对于复杂的双色或多色产品。
其次,双色注塑成型工艺对注塑机和模具的要求较高,需要具备较高的精度和稳定性。
此外,双色注塑成型工艺还需要考虑塑料材料的相容性和附着力等问题,以确保产品的质量和使用寿命。
双色注塑成型工艺是一种能够制造出具有丰富色彩和独特外观的注塑技术。
通过合理设计和选择不同颜色的塑料,可以实现双色或多色效果,提升产品的视觉吸引力和市场竞争力。
然而,双色注塑成型工艺也面临一些挑战和限制,需要在设计和制造过程中充分考虑各种因素,以确保产品的质量和使用寿命。
- 1、下载文档前请自行甄别文档内容的完整性,平台不提供额外的编辑、内容补充、找答案等附加服务。
- 2、"仅部分预览"的文档,不可在线预览部分如存在完整性等问题,可反馈申请退款(可完整预览的文档不适用该条件!)。
- 3、如文档侵犯您的权益,请联系客服反馈,我们会尽快为您处理(人工客服工作时间:9:00-18:30)。
来源于:注塑塑胶网
浅谈双色注塑成型工艺
现在消费产品款式千变万化,既要外型美观、设计精巧,也要迅速配合市场需求。
设计师一般因消费产品不同的用途,在不同的部位上,采用不同的物料,以应付特定环境的需要,达到延长产品寿命、增加美观及实用性的目的。
这种实用性的设计要求无疑将导致生产技术也随之复杂化,双物料注塑工艺就是应这一潮流而生的。
一般的双物料产品可以采用单色注塑机制造,基本上一台注塑机就可胜任,不过后加工工序相当费时复杂,直接影响产品的质量,总生产成本并不经济。
双物料注塑工艺除了注塑机作出相应的改动外,模具设计的技巧是整项技术的灵魂。
模具通过转动移位,达到同步注塑不同物料的效果。
模具设计大致分为两类:第一类有两个模腔,利用转动模式把半成型模件转移180度到另一个模腔内,其好处是使第一和第二工序可以同步进行;另一类是单一模腔,半制成品连同模具一起转动180度。
设计上比较简单,但生产效率相应降低。
由于模具或半成品需要转动,所以模具设计及注塑机的要求更为精密。
另外,由于双物料注塑的可变性很高,所以要达到生产顺利,符合预期理想,所有的模具设计必须与产品设计同步考虑,而且市面流行的双物料注塑机规格并
不统一,导致模具设计时考虑的问题更多;加上通用性少,模具制造商必须加倍留心。
双物料制品一般以ABS、PC等硬塑料配合TPE软塑料为主,适合制造餐具、工具手柄、表壳、电话机外壳及按钮等制品。
这使得生产企业在技术上必须注意三点:两类物料的融合性、产品的复杂性及注塑机的调校。
例如,由于成本或应用的关系,采用的物料之间可能没有良好的粘合性,双物料注塑通常要在这方面进行更多地调试工作。
更多的双色注塑问题精英注塑将会继续关注。
我国正逐步成为全球消费产品的生产制造基地,近年来华南地区塑料产品的制造商承接了许多需要双物料注塑技巧的订单,使双物料注塑技术在国内的应用日益广泛。
双射成型主要以双射成型机两只料管配合两套模具按先后次序经两次成型制成
双射产品。
比起传统射出成型,双料共射射出成型制程有如下的优点:
1核心料可以使用低黏度的材料来降低射出压力。
2从环保的考虑,核心料可以使用回收的二次料。
3根据不同的使用特性,如厚件成品皮层料使用软质料,核心料使用硬质料或者核心料可以使用发泡塑料来降低重量。
4可以利用较低质量的核心料以降低成本。
5 皮层料或核心料可使用价格昂贵且具特殊表面性质,如防电磁波干扰、高电导性等材料以增加产品性能。
6适当的皮层料和核心料配合可以减少成型品残余应力、增加机械强度或产品表面性质。
7产生如大理石纹路的产品。
从多色射出成型、双料共射出成型的特性与应用可以看出未来有逐步取代传统射出成型制程的趋势。
革新性射出成型技术不但提高了射出成型制程的精密度、提供高难度制程技术,而且开拓了射出成型制程领域的范围。
创新的射出设备与制程,才足以应付愈来愈多样化、高质量、高附加价值的产品需求。