机床主轴回转精度实验报告
机床精度(学生实验报告)

三 、实验原理
机床几何精度测量
按 JB2314—78 普通机床规定,机床精度检 验包括机床导轨直线度、垂直度、平行度、 端面的平面度,机床部件之间直线度、垂直 度、平行度、同轴度,机床部件的运动精度, 主轴回转精度等18项。
四、 实验步骤与方法
►
框式水平仪的工作原理: 框式水平仪主要部分是一个弧形玻璃管,它的内壁磨成100米左右的 曲率半径。刻有刻度的玻璃管内充以少量乙醚液体,中间留一个气泡。 如图1所示。不论水平仪放在什么位置,玻璃管中的页面总是处于水 平,气泡总是向高处移动,读出气泡两端边缘,移动的格数,即可求 出相应的高度差。水平仪的刻度值为0.02/1000,它表示将该水平仪 放在1米长的平尺表面上,在平尺右端垫起0.02mm的高度,平尺便倾 斜一个a角,此时,水平仪正好移动一个刻度值。
△H △H L1 L
图1 水平仪测量升落差的原理图
►
如果我们在实验中,框式水平仪不是放在1米的平尺上, 而是放在200mm的平板上,那么△H为多少呢Tga=△H △H=200*Tga=0.004mm 水平仪读数的符号,习惯上规定:气泡移动方向和水平 移动方向相同时读数为正值,相反时为负值。
►
1. 溜板在垂直水平面的不直度
反向间隙误差可能起因
► 用于弥补原有反向间隙而对机床进行的反向间补
偿的数值过大,导致原来具有正值反向间隙问题 的机床出现负值反向间隙。 ► 机器可能受到编码器滞后现象的影响 ► 在机床的导轨中可能存在间隙,导致当机床在被 驱动换向时出现在运动中跳跃。
反向间隙对加工带来的影响
在机器上负值反向间隙的影响为圆弧插 补的刀具轨迹将出现一向内凹的跳跃。
主轴锥孔中心线的径向跳动
测量位置 a b 1 2 允差 是否合格
加工中心主轴回转精度试验

加工中心主轴回转精度试验发布时间:2021-08-10T09:24:06.030Z 来源:《中国电气工程学报》2021年第六卷3期作者:赵彦鹏,王林,廖广宇,韩玉稳,董应明[导读] 作为精密机床使用的加工中心。
主轴回转运动误差主要由轴向窜动、径向跳动和角度摆动三种形式分别对加工精度造成影响。
赵彦鹏,王林,廖广宇,韩玉稳,董应明云南省机械研究设计院/云南省机电一体化应用技术重点实验室,云南昆明 650031摘要:作为精密机床使用的加工中心。
主轴回转运动误差主要由轴向窜动、径向跳动和角度摆动三种形式分别对加工精度造成影响。
对加工中心主轴回转精度进行测量,介绍测量的方法,后期数据处理并进行误差分析。
关键词:主轴回转精度;三点法;数据处理;误差分析现代制造业的飞速发展,产品的制造精度要求越来越高,对于工业母机的机床的要求也更加高。
特别是作为精密机床使用的加工中心。
主轴回转运动误差主要由轴向窜动、径向跳动和角度摆动三种形式分别对加工精度造成影响。
主轴回转精度的检测是机床设计、制造、调整和维修的重要环节,是提高机床加工精度的重要措施。
1、机床主轴回转精度的概念主轴回转误差是指主轴各瞬间的实际回转轴线相对其平均回转轴线的变动量。
产生主轴径向回转误差的主要原因有:主轴几段轴颈的同轴度误差、轴承本身的各种误差、轴承之间的同轴度误差、主轴绕度等。
因为机床的主轴传递着主要的加工运动,故其回转误差将在很大的程度上决定工件的加工质量。
2、加工中心主轴回转精度试验2.1试验内容及目的被测对象为TGK4663A加工中心主轴,采用动态测量法通常是选用一种测量传感器,利用传感器测得的位移信号进行分析处理。
2.2试验参考依据GB/T17421.7 《机床检验通则第七部分;回转轴线的几何精度》2.3测量装置及示意图2.5试验条件(1)试验的机床为按相关国家、行业等标准检验合格的产品;(2)试验前让主轴以中速(3000r/min)空运转30min;(3)试验前校正测量棒,在安装传感器位置处,使测量棒的径向跳动小于15μm;(4)试验时,传感器距主轴前定位端盘距离为180mm;(5)试验时,X轴、Y轴、Z轴及B轴不做进给运动。
「背景资料 综合实验一机床主轴回转误差运动测试」

实验一机床主轴的回转误差运动测试随着科学技术的飞速发展,很多行业对回转轴差动误差的测量都极为重视,例如,有许多行业的设备都需要高精度的机械零件,它们的形状误差和表面粗糙程度往往要求在0.1~0.25μm以下。
要加工出这样高精度的机械零件,需要多方面的条件来配合才能够满足要求,其中的机床主轴的回转精度是最关键的条件之一。
而测量主轴的误差运动则可以了解机床主轴的回转状态及产生误差的原因,对机床的加工而言,它可以用来预测机床的理想加工条件下所能达到的最小形状误差,并判断产生加工误差的原因。
本实验对如何正确测量机床主轴的误差运动进行一些探讨。
一、有关的基础知识1 轴误差运动理想回转轴线——回转轴运转时,其轴心线在空间的位置稳定不变,即与空间的一条直线相重合,且无轴向的相对移动,我们就称这条固定直线为理想轴线。
但实际上,回转轴组件由于各零件的加工误差及安装误差存在,它的回转轴线在空间的位置是漂移的,并非固定不变。
那么,我们就把回转过程中实际的回转轴轴心线对理想线的相对位置的相对位移定义为回转轴的误差运动。
在实际研究中,往往根据不同的研究对象和目的,可以将理想轴线有选择地和不同的元件“固接”在一起。
例如,我们研究轴承时,可以把理想轴线和轴壳“固接”,这时的误差运动是回转过程中回转轴线对轴承壳体的相对运动,反映出轴承的回转质量,如果研究的是加工设备(如机床),对刀具回转类机床,理想轴线可以与工件“固接”;对于工件回转加工类机床,理想轴线则可与刀具“固接”;这时主轴的回转误差运动就是刀具——工件之间的相对位移,反映出来的是加工误差。
但应注意,回转误差运动是一个复杂的合成误差,它是由几个方向的误差所组成,下面来具体分析(见图1-1):总的来讲,实际回转轴线对理想轴线AB在每一个瞬间的相对运动可以分解为三类五个运动:纯轴向运动z(t),纯径向运动x(t)和y(t),倾角运动α(t)和β(t)。
从分解的五种运动的特点可看出,径向误差运动r(t)是由纯径向运动x(t) 、y(t) 和倾角运动α(t)、β(t)合成的结果。
简要叙述机床回转轴回转精度检测的实验方案
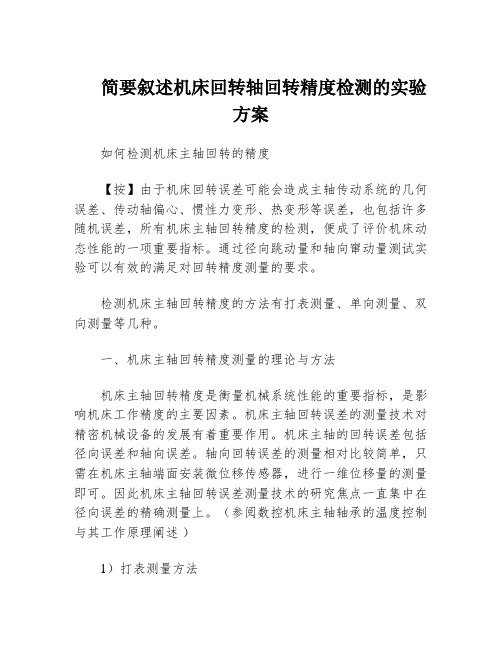
简要叙述机床回转轴回转精度检测的实验方案如何检测机床主轴回转的精度【按】由于机床回转误差可能会造成主轴传动系统的几何误差、传动轴偏心、惯性力变形、热变形等误差,也包括许多随机误差,所有机床主轴回转精度的检测,便成了评价机床动态性能的一项重要指标。
通过径向跳动量和轴向窜动量测试实验可以有效的满足对回转精度测量的要求。
检测机床主轴回转精度的方法有打表测量、单向测量、双向测量等几种。
一、机床主轴回转精度测量的理论与方法机床主轴回转精度是衡量机械系统性能的重要指标,是影响机床工作精度的主要因素。
机床主轴回转误差的测量技术对精密机械设备的发展有着重要作用。
机床主轴的回转误差包括径向误差和轴向误差。
轴向回转误差的测量相对比较简单,只需在机床主轴端面安装微位移传感器,进行一维位移量的测量即可。
因此机床主轴回转误差测量技术的研究焦点一直集中在径向误差的精确测量上。
(参阅数控机床主轴轴承的温度控制与其工作原理阐述)1)打表测量方法早期机床主轴回转精度不太高时,测量机床主轴误差的常用方法是将精密芯棒插入机床主轴锥孔,通过在芯棒的表面及端面放置千分表来进行测量。
这种测量方法简单易行,但却会引入锥孔的偏心误差,不能把性质不同的误差区分开,而且不能反映主轴在工作转速下的回转误差,更不能应用于高速、高精度的主轴回转精度测量。
除此之外也有采用测量试件来评定主轴的回转误差。
2)单向测量方法单向测量法又称为单传感器测量法。
由传感器拾得“敏感方向”的误差号,经测微仪放大、处理后,送入记录仪,以待进一步数据处理。
然后以主轴回转角作为自变量,将采集的位移量按主轴回转角度展开叠加到基圆上,形成圆图像。
误差运动的敏感方向是通过加工或测试的瞬时接触点并平行于工件理想加工的表面的法线方向,非敏感方向在垂直于第三方向的直线上。
单向测量法测量的主轴回转误差运动实质上只是一维主轴回转误差运动在敏感方向的分量。
因此单向测量法只适用于具有敏感方向的主轴回转精度的测量,例如工件回转型机床。
机床主轴测试实验报告
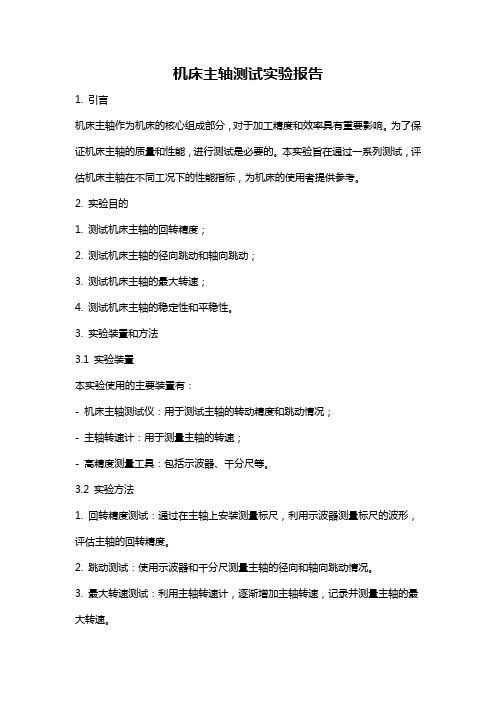
机床主轴测试实验报告1. 引言机床主轴作为机床的核心组成部分,对于加工精度和效率具有重要影响。
为了保证机床主轴的质量和性能,进行测试是必要的。
本实验旨在通过一系列测试,评估机床主轴在不同工况下的性能指标,为机床的使用者提供参考。
2. 实验目的1. 测试机床主轴的回转精度;2. 测试机床主轴的径向跳动和轴向跳动;3. 测试机床主轴的最大转速;4. 测试机床主轴的稳定性和平稳性。
3. 实验装置和方法3.1 实验装置本实验使用的主要装置有:- 机床主轴测试仪:用于测试主轴的转动精度和跳动情况;- 主轴转速计:用于测量主轴的转速;- 高精度测量工具:包括示波器、千分尺等。
3.2 实验方法1. 回转精度测试:通过在主轴上安装测量标尺,利用示波器测量标尺的波形,评估主轴的回转精度。
2. 跳动测试:使用示波器和千分尺测量主轴的径向和轴向跳动情况。
3. 最大转速测试:利用主轴转速计,逐渐增加主轴转速,记录并测量主轴的最大转速。
4. 稳定性和平稳性测试:连续运行主轴一定时间,在不同转速下观察主轴的稳定性和平稳性。
4. 实验结果与分析4.1 回转精度测试结果经过测试,得到主轴的回转精度为0.005 mm。
根据要求,机床主轴的回转精度应在0.01 mm以内,因此主轴的回转精度在合理范围内。
4.2 跳动测试结果径向跳动测试结果显示,主轴的径向跳动在0.02 mm以内,轴向跳动在0.01 mm以内。
根据标准,机床主轴的径向跳动和轴向跳动应在0.03 mm以内,因此主轴的跳动情况符合要求。
4.3 最大转速测试结果经过测试,主轴的最大转速为8000 rpm。
根据要求,机床主轴的最大转速应在6000 rpm以上,因此主轴的最大转速符合要求。
4.4 稳定性和平稳性测试结果在连续运行主轴2小时的实验中,主轴的转速保持稳定,无明显波动。
在不同转速下,主轴的转速变化不超过2%,达到了平稳运行的要求。
5. 结论通过本次实验,得到了以下结论:1. 机床主轴的回转精度、跳动情况、最大转速以及稳定性和平稳性都符合要求;2. 主轴的回转精度为0.005 mm,径向跳动和轴向跳动均在0.03 mm以内;3. 主轴的最大转速为8000 rpm,稳定性测试显示转速变化不超过2%。
机床主轴回转精度实验报告

机床主轴回转精度实验报告姓名:学号:实验时间:课程名:制造技术基础实验室:金切实验室机械制造及其自动化2012一、实验概述随着机械制造业的发展,对零件的加工精度要求越来越高,由此对机床精度要求也越来越高。
作为机床核心——主轴部件的回转误差运动,直接影响机床的加工精度,它是反映机床动态性能的主要指标之一,在《金属切削机床样机试验规范》中已列为机床性能试验的一个项目。
多年来,国内外一直在广泛开展对主轴回转误差运动测量方法的研究,并取得一定的成果。
研究主轴误差运动的目的,一是找出误差产生的原因,另一是找出误差对加工质量影响的大小。
为此,不仅对主轴回转误差运动要能够进行定性分析,而且还要能够给出误差的具体数值。
二、实验目的1.通过实验,熟悉机床主轴运动误差的表现特征、评定方法、及测定技术、产生原因及对机床加工精度的影响。
使同学加深理解工艺装备运动精度与加工误差的关系;2.理解主轴回转误差的测量数据处理技术与基本原理。
三、实验要求1.实验员演示主轴回转误差测量的全过程,讲解主轴回转精度的定义、主轴回转误差测量原理和测量仪器的操作方法;2.同学观察实验过程,记录实验数据,并学习使用MATLAB完成实验数据处理,将实验数据处理过程的计算和结果写入实验报告。
四、报告内容1.简述实验系统的组成结构与原理;2. 什么是主轴回转误差运动?造成机床主轴回转运动误差的因素可能有哪些?3.实验数据记录与处理数据采样时间固定为2ms;测量距离单位为mm;4.采用Matlab绘制极坐标误差带圆图并打印1)从采样记录文件按单周采样点数(n)截取数据;2)打开matlab,使用file->Import导入数据文件,数据将保存在data变量中;3)使用命令x=(0 : 2*pi/n : 2*pi-2*pi/n )生成极坐标刻度,并进行转置x=x’;4)使用polar(x,data)命令,绘制极坐标图。
机床主轴回转误差运动测试(精)
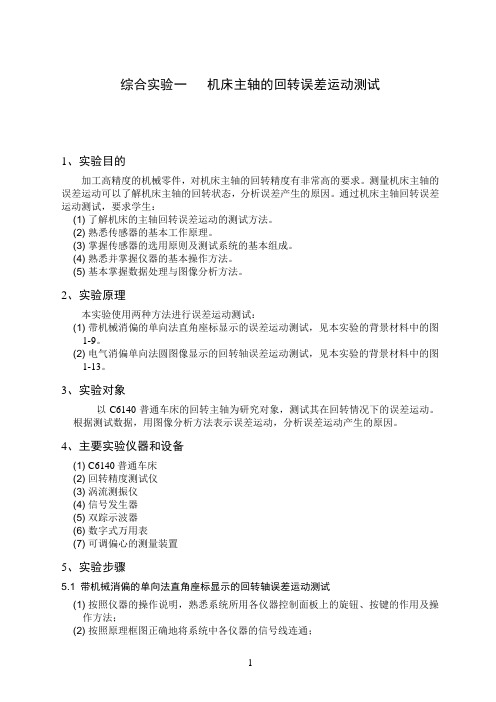
综合实验一机床主轴的回转误差运动测试1、实验目的加工高精度的机械零件,对机床主轴的回转精度有非常高的要求。
测量机床主轴的误差运动可以了解机床主轴的回转状态,分析误差产生的原因。
通过机床主轴回转误差运动测试,要求学生:(1) 了解机床的主轴回转误差运动的测试方法。
(2) 熟悉传感器的基本工作原理。
(3) 掌握传感器的选用原则及测试系统的基本组成。
(4) 熟悉并掌握仪器的基本操作方法。
(5) 基本掌握数据处理与图像分析方法。
2、实验原理本实验使用两种方法进行误差运动测试:(1) 带机械消偏的单向法直角座标显示的误差运动测试,见本实验的背景材料中的图1-9。
(2) 电气消偏单向法圆图像显示的回转轴误差运动测试,见本实验的背景材料中的图1-13。
3、实验对象以C6140普通车床的回转主轴为研究对象,测试其在回转情况下的误差运动。
根据测试数据,用图像分析方法表示误差运动,分析误差运动产生的原因。
4、主要实验仪器和设备(1) C6140普通车床(2) 回转精度测试仪(3) 涡流测振仪(4) 信号发生器(5) 双踪示波器(6) 数字式万用表(7) 可调偏心的测量装置5、实验步骤5.1 带机械消偏的单向法直角座标显示的回转轴误差运动测试(1) 按照仪器的操作说明,熟悉系统所用各仪器控制面板上的旋钮、按键的作用及操作方法;(2) 按照原理框图正确地将系统中各仪器的信号线连通;(3) 调整标准盘1(作为补偿信号)和标准盘2(作为误差的测量信号)的偏心量,标准盘2的偏心量e2应尽可能小,仅稍大于被测量轴回转误差值,以保证得到信号即可,偏心量一般调整到0.03mm~0.05mm;标准盘1的偏心量e1应尽可能调大,大到使被测量轴回转误差值相对于偏心量可以忽略不计,及得到一个接近于纯偏心信号的光滑曲线,但因受涡流传感器工作间隙的限制,偏心量无法无限制地加大,一般调到0.40mm~0.60mm即可,并使e1和e2相差180o;(4) 经指导老师检查系统连接正确后,接通电源预热仪器;(5) 按测振仪使用要求调整好涡流传感器的工作间隙;(6) 调整好机床转速,启动机床;(7) 调整测振仪灵敏度,使之满足下面的关系式:e1.k1传感.k1测振仪= e2.k2传感.k2测振仪(8) 将满足以上关系式的两路输出信号经加法器(借用回转精度测试仪后面板上的加法器,此时应将总接口插板抽出)相加,在示波器上得到误差曲线,曲线上最高点与最低点的高度差即为圆度误差的相对值,曲线最大的垂直度即为粗糙度的相对值;(9) 标定,方法为:用正弦信号发生器输出一标准正弦信号,使其幅值为测振仪当前档位(如30um档)的满量程输出的电压值,将该正弦信号送入加法器输入端,在示波器上得到一幅值为A mm的正弦信号,则该测量系统的标定系数为30um/A mm;(10) 求出绝对误差=相对误差(mm)×30um/A mm;(11) 停机床、关仪器,并拆除仪器的所有连接线,整理现场。
主轴回转精度动态测试技术研究

主轴回转精度动态测试技术研究摘要:随着磨床技术发展,对主轴回转精度的要求越来越高。
回转精度包括了轴的径向误差、轴向误差、角度误差及由此衍生出的表面误差和半径误差五种。
其中,径向误差尤其重要。
对于径向误差的动态测量及分析,我们采用了单向测量法和双向测量法,测得主轴不同转速下的同步误差值及非同步误差值,以选取主轴最佳磨削转速。
关键词:同步误差非同步误差径向误差引言自20世纪五十年代开始,我国磨床发展历程中,主轴类零件的制造精度要求一直被设计师认为能够完全实现。
因此,在制造过程中,轴类零件的几何精度要求并不是难点。
社会发展至今,由于汽车工业及计算机技术领域发展的需要,对零件的加工精度要求不断提高,甚至达到了微米级以上。
此种情况下,为了满足市场需求,生产高精度磨床就成为必然。
而主轴的回转运动误差是影响机床加工精度的主因之一。
因此,对高精度磨床的开发,研究主轴回转的动态特性具有现实的重要意义。
在日常生产中,如果磨床达不到磨削精度要求时,我们通常的做法是采取增加机床刚性、结构阻尼、改变零件几何形状以及降低磨床温升等方法来改进磨削性能。
但是,这些改进措施仅能从表面上对磨床工作精度有所改进,根本不能改变磨床的基本性能,即对提升磨床性能作用不大。
我们需要了解主轴性能,通过对主轴的动态测量,将主轴各项运动误差用数据准确地描述出来,以些为据,判断磨床的改进方向,从而准确预测及控制工件加工质量。
1 主轴运动误差在主轴动态回转特性中,通常存在三个基本误差:①径向误差;②轴向误差;③角度误差。
在此三个基本误差的基础上,又可以衍生出两个复合误差:①表面误差;②半径误差。
表面误差是由轴向误差和角度误差共同作用产生的,而半径误差是由径向误差和角度误差共同作用产生的。
对主轴精度影响最大是应该是径向运动误差。
如(图1)所示,当主轴在低速转动时,不会产生角度偏移,也不会发热,此时得到的是一个纯半径的运动误差,轴向误差与角度误差可以忽略不计,并不存在两个复合误差。
- 1、下载文档前请自行甄别文档内容的完整性,平台不提供额外的编辑、内容补充、找答案等附加服务。
- 2、"仅部分预览"的文档,不可在线预览部分如存在完整性等问题,可反馈申请退款(可完整预览的文档不适用该条件!)。
- 3、如文档侵犯您的权益,请联系客服反馈,我们会尽快为您处理(人工客服工作时间:9:00-18:30)。
实验报告
实验名称:机床主轴的回转精度实验
班级:
姓名:
学号:
成绩:
湖南工业职业技术学院机械系数控中心
实验三:机床主轴的回转精度实验
一、实验目的:
1、掌握机床回转误差运动状态及对工件加工精度的影响;
2、了解车床主轴回转误差的测量方法。
二、实验器材:
1、C620车床一台,
2、圆柱心棒一根,
3、千分表三个。
实验方法:
4、按图示把心轴安装到车床主轴上;
2、按图示安装上千分表;分别离主轴前端50mm,100mm,200mm,400mm,600mm处测量各一次;
3、低速(150r/min)开动机床,记录跳动值和窜动值;
4、高速(630r/min)开动机床,记录跳动值和窜动值;
5、依下列方式计算出角向摆动:
tgα=(600mm处的跳动值-100mm处的跳动值)/(600-100),多算几处,取平均值。