精益生产概论
精益生产概论

1、异常停线:绝不传递次品,异常放大器;
推 动 改 善 不 断 升 级
问题 、培 育人 才 、建 立改 善创 新型 企业
自 动 化
品质保证 少人化
2、目视化异常管理:安装快速反应系统,异常看板、生产管 理板、标准作业书。
1、人机作业分离:自动检测、LCA一人减少; 2、防呆防错:5Why、三现主义消除异常、杜绝异常再发。
文化营
— 15 —
三、推进体系
3.2 JIT
序号
1
改善项目
物料与信息一体化
2
物流批量节拍
3
物流快速流动
4
物流空间最短化
5
物流流动准确化
改善方向
计划与物控指令合并 来料节拍与送料节拍,日计划来料 来料和送料裸件化、工装化、工具盒
物料到作业区最短,线边仓 看板来动、分拣单配送
(1)月计划指导供方采购 (2)周计划指导生产
供方库存不可查询
(1)供方平台报库存 (2)齐套查询
3
供应商送货
送货数量和时间不可控
(1)日计划指导送货数量和时间 (2)生产订单与供货物流合并、一致 (3)牛奶取货
4
库存过程
转运次数多、搬运次数多
线边仓建设、卸货工装车、来料裸件和工 装盒
— 25 —
五、方法体系
过渡页
11
精益生产目标体系
2 • 精益七个“零”目标体系结构 • 目标体系改善方向
— 11 —
二、目标体系
2.1 精益精益七个“零”目标体系结构
精益生产
JIT生 产计 划与 物流
追求7个“零”极限目标
一个 流
均衡 化与 同步 化系
统
自动 化
精益生产精益生产概述

精益生产概述什么是精益生产精益生产是一种优化生产流程的方法,旨在通过减少浪费和提高效率来提高产品和服务的质量。
它是源于日本汽车制造业的生产哲学,最早由丰田汽车公司引入并在全球范围推广。
精益生产的核心思想是通过消除不必要的浪费和无效的步骤,使生产变得更加高效和灵活。
它的目标是提供价值,使客户能够以最低的成本获得最高的价值。
精益生产的原则精益生产遵循一些重要的原则,以实现高效生产流程。
以下是其中的一些核心原则:1.价值的识别和增加:精益生产的关键是确定顾客真正关心的价值,通过在每个工作阶段中增加价值来实现产品质量的提高。
2.流程的流畅化:为了确保材料和信息的无缝流动,精益生产强调流程的流动性。
通过减少瓶颈和不必要的等待时间,可以大大提高生产效率。
3.拉动式生产:传统的推动式生产往往会导致过剩库存和资源的浪费。
精益生产采用拉动式生产,即根据顾客需求来启动下一个生产阶段,从而保持适当的库存和资源使用。
4.高效绩效:精益生产强调通过持续改进和培养高效的团队来提高绩效。
通过培训员工,建立透明和积极的沟通,并鼓励员工参与决策和问题解决,可以激发团队的创造力和生产力。
5.持续改进:精益生产是一个持续不断的过程。
它要求不断地寻找改进的机会,并通过内部和外部反馈来完善生产流程和产品质量。
精益生产的优势精益生产作为一种优化生产流程的方法,具有许多优势,可以帮助企业获得成功。
1.提高质量:通过消除浪费和不必要的步骤,精益生产可以提高产品和服务的质量。
减少错误和缺陷的发生,提高顾客满意度。
2.提高效率:精益生产通过优化工作流程和减少浪费,提高生产效率。
通过拉动式生产,可以避免过剩和库存积压的问题。
3.降低成本:精益生产致力于降低成本,通过减少浪费和提高效率来实现这一目标。
通过精确估算和订单驱动的生产,可以减少不必要的材料和资源的浪费。
4.提高响应能力:精益生产的流程设计注重灵活性和快速响应能力。
这使得企业能够更好地适应市场需求的变化,并及时提供客户所需的产品和服务。
精益生产概论

七种类型的浪费
• Correction
纠正、返修
• Overproduction
过量生产
• Material Movement / 物料的移动和运输
Conveyance
• Motion
动作
• Waiting
等待
• Inventory
库存
• Processing
加工过程的浪费
COMMWIP
17
返修 • 为满足客户需求修正产品 或服务
-停止装配线 / 加工工序 -在继续之前解决问题 -在源头实施适当的措施 -现场方式
恰当的自働化帮助我们在问题的源头实施正确的纠正方法
30
多种设备操作
一人操作一台设备
多重工序操作
车削
一人操作多台不同设备
一人操作多台设备 铣削 碾磨
31
人工作业中的自働化
团队主管
停线
安灯
原材料
完成品
安灯
生产状态板
18
过量生产造成浪费…
额外库存
过量生产的浪费
书面文件过多
人员过多
操作过多 空间过多 机器过多 缺陷过多
丰田的结论是过量生产是工厂中最常发现的,最糟糕的浪费。这种浪 费源于生产超出市场的需求。
市场处于上升阶段时,这种浪费可能不会很突出。但是,如果市场需 求下降,过度生产的影响就显现出来,公司经常因不能出售货物而积压库存导 致麻烦。
3. 下游拉动 – 无过量生产 – 下游触发工作开始 – 标准在制品
改进前
RAW MATERIALS
1
DRILL
5
4
HEAT
TREAT
6
2
LATHE LATHE 3 MILL
精益生产概论
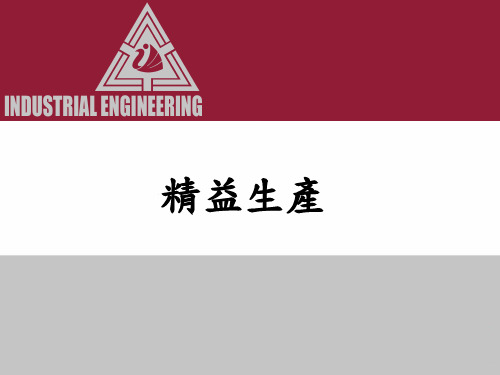
IMVP研究 - 1989
在日本的日企 在北美的日企 在北美的美企 所有欧企
生产率 (小时/辆 ) 质量 (组装缺陷数/100辆) 场地占用 (平方英尺/辆/年) 维修区面积 (以组装区的%计) 库存 ( 天数,8个样板零件)
自动化 焊接 % 涂装 % 组装 %
實施JIT之必備條件
• JIT佈置及流程設計 •預防保養 Preventive Maintenance • JIT應用於生產線流程 • JIT應用於訂單生產 •全面品質管制 •穩定排程 •與供應商合作
如何達成JIT生產
7. 改善生產設計
.標準生產規劃 .標準化及減少零件數量 .配合生產設計的製程設計 .品質期望
• 优秀的质量 • 不要让生产停止 • 一切正常 • 目标:产量 • 库存是安全的保障 • 产量多,变化少 • 部门责任制 • 单向化 • 公司架构层次多
• 零缺陷 • 不要让故障再次发生 • 持续改善 • 目标:客户满意 • 库存是浪费 • 产量少,多样化 • 价值流责任制 • 多向化 • 公司架构精简
箱容数 V20 交貨週期 1:1:1 後工程
備註
儲位
2015 慶合
生管課
M0150
箱種、收容数
交貨或生產週期
使用者
28
三現主義
注重生產現場
現地 現物 現實
根由 Root Cause
真正原因
为什麽? 为什麽?
十分接近真相的原因
为什麽?
为什麽?
表面原因
为什麽? 答案:
看到的现象
5W 追根問底
转换思维方式
国际汽车业研究计划 IMVP 国际Motor Vehicles Programme
精益生产概论

课程大纲
1 •精益思想 2 • 增 值&浪 费 3 •实践方法 4 •精益之旅
为什么精益生产 ?
两种思想
传统思想
精益思想
利
现在我们能控制
润
的只有成本
售价
成
成
本
本
利
润 售价
售价=成本+利润
利润=售价-成本
精益生产就是消除浪费!
不均衡
生产不均衡 -日生产量不均衡 -在工/在库过多 -人力配置不均衡
不合理
方法不合理 -作业不方便 -作业困难 -材料供给过多 -资材位置不合理
MUDA
3.七大浪费
1. 过量生产: 生产的数量或速度超客户需要 2. 缺陷:为满足客户要求而进行的返工,返修,检验! 3. 多余加工:没有对产品增加价值的工艺加工! 4. 库存:任何超过单件流的供应 5. 运输:任何不是为了及时生产的搬运 6. 多余动作:任何不增加价值却消耗体力,时间的移动或动作 7. 等待:工序作业之间的闲置
1.2 精益生产方式的运用
詹姆斯·沃麦克(美) 丹尼尔·琼斯 (英)
(1990)
(1996)
(2005)
精益生产无处不在
阅兵式,公交车,整理头发,如家脸盆放置
精益生产最有效,最灵活,最有竞争力的生产方式
适用于任何国家,任何文化,任何组织,任何行业,任 何时间,任何地点 如美国通用加利福尼利亚精益实践
日常过程中遇到哪些浪费?
1. 距离太远 2. 换模时间长 3. 工艺不足 4. 保养操作不良 5. 没有标准化工作 6. 没有现场管理(帮助人,支持人,改进他人不是骂人) 7. 业绩KPI考核不对(质量,成本,交期,安全无关) 8. 计划变动 9. 没有5S与目视化管理 10.供应商能力不足(猎人与农夫)
精益生产概论(PPT132页)

推行QC小组活动的意义有: ● 通过小组式的学习型组织, 提高一线员工独立思考和相互启发的能力
● 通过QC手法的学习与运用, 加强企业的基础管理 ● 通过循序渐进的课题活动, 创造有活力的工作场所 ● 发挥群众智慧,全员参与经营
1、Genius only means hard-working all one's life. (Mendeleyer, Russian Chemist)
天才只意味着终身不懈的努力。21.5.265.26.202108:3008:30:57May-2108:30
2、Our destiny offers not only the cup of despair, but the chalice of opportunity. (Richard Nixon, American President )命运给予我们的不是失望之酒,而是机会之杯。二〇二一年五月二十六日2021年5月26 日星期三
现 代
IE 运 用
均 衡 化 同 步 化
7
9、要学生做的事,教职员躬亲共做; 要学生 学的知 识,教 职员躬 亲共学 ;要学 生守的 规则, 教职员 躬亲共 守。21 .6.3021 .6.30W ednesd ay , June 30, 2021 10、阅读一切好书如同和过去最杰出 的人谈 话。15:42:0015 :42:001 5:426/3 0/2021 3:42:00 PM 11、一个好的教师,是一个懂得心理 学和教 育学的 人。21. 6.3015:42:0015 :42Jun- 2130-J un-21 12、要记住,你不仅是教课的教师, 也是学 生的教 育者, 生活的 导师和 道德的 引路人 。15:42:0015:4 2:0015:42Wed nesday , June 30, 2021 13、He who seize the right moment, is the right man.谁把握机遇,谁就心想事成。21.6.3021.6.3 015:42:0015:42 :00Jun e 30, 2021 14、谁要是自己还没有发展培养和教 育好, 他就不 能发展 培养和 教育别 人。202 1年6月 30日星 期三下 午3时4 2分0秒 15:42:0 021.6.3 0 15、一年之计,莫如树谷;十年之计 ,莫如 树木; 终身之 计,莫 如树人 。2021 年6月下 午3时4 2分21. 6.3015:42June 30, 2021 16、提出一个问题往往比解决一个更 重要。 因为解 决问题 也许仅 是一个 数学上 或实验 上的技 能而已 ,而提 出新的 问题, 却需要 有创造 性的想 像力, 而且标 志着科 学的真 正进步 。2021 年6月30 日星期 三3时4 2分0秒 15:42:0 030 June 2021 17、儿童是中心,教育的措施便围绕 他们而 组织起 来。下 午3时42 分0秒 下午3时 42分15 :42:002 1.6.30
精益生产概论

精益生产概论精益生产是一种以减少浪费和提高价值创造为目标的生产管理方法。
它的目标是通过消除浪费、提高效率和增加价值来实现产品质量的提高和生产成本的降低。
它的核心理念是通过精心设计和优化生产流程来实现这些目标。
精益生产最早起源于日本的丰田汽车公司,后来又在全球范围内得到了广泛应用。
它的核心思想是将价值创造和浪费分开,通过不断地改进和优化生产流程来减少浪费。
它强调通过标准化流程和减少变动来提高生产效率,同时也注重员工参与和持续改进。
精益生产的核心原则包括价值流图、流程改进、丰和拉、人员参与和持续改进。
价值流图是一种绘制和分析产品在生产过程中的价值流动的方法,它可以帮助我们找到并消除浪费。
流程改进是通过不断地改进和优化生产流程来提高效率和降低成本。
丰和拉是指在生产过程中通过及时供应和生产,减少库存和等待时间。
人员参与是指通过培训和激励员工参与到生产过程中,使他们成为改进生产流程的主要力量。
持续改进是指不断地寻找和消除浪费,不断地改进和优化生产流程。
精益生产的优势包括提高产品质量、降低生产成本和提高生产效率。
通过消除浪费,提高生产效率和降低生产成本,可以为企业创造更高的价值和更大的利润。
同时,精益生产还能够提高产品质量,减少缺陷和客户投诉,提高客户满意度和品牌声誉。
但是,精益生产也面临一些挑战和困难。
首先,精益生产需要企业对生产流程进行全面的分析和改进,这需要投入大量的时间和资源。
其次,精益生产需要员工的积极参与和主动改进的意识,如果员工对精益生产理念不够理解和认同,将很难实施和推广。
此外,不同企业的生产环境和条件也不同,实施精益生产需要根据具体情况进行调整和适应。
总而言之,精益生产是一种以减少浪费和提高价值创造为目标的生产管理方法。
它通过消除浪费、提高效率和增加价值来实现产品质量的提高和生产成本的降低。
它的核心原则包括价值流图、流程改进、丰和拉、人员参与和持续改进。
精益生产的优势包括提高产品质量、降低生产成本和提高生产效率,但实施精益生产也面临一些挑战和困难。
第一讲 精益生产概论

d 加 工本 身 的浪 费 ; .
e 库存 的浪 费 ; . f操 作 上 的浪 费 ; . g 制 成 次 品的浪 费 。 .
b 制定 成 本 管 理 的综 合 计 划 。所 谓 成 本 管 理 . 综合 计划 是 指制定 未 来 3 4年 全 公 司 中期 利 润 计 ~ 划 的过程 。这一 中期 利润计 划 是根 据成 本核 算所 用 的利 润 、 本 等 概念 来 制 定 。它规 定 了每 个 时 期 的 成
谓 的“ 及 时” 三 。
c 实施 降低 成本 的措 施 。在 制定 成本 管理 综 合 . 计 划 以后 , 实施 成本 规划 与 降低成 本 的措 施 , 要 每年 都 要 降低 一 定 比例 的成本 , 叫成本 递 减运 动 , 公 也 从
大野 耐 一对 实行 看板 管 理提 出 了如下 要求 : a 不 要把 次 品送往 后道 工 序 ; . b 后 道工 序 向前道 工序 领 取工件 ; . c 前道 工 序只 生产 后道 工序 领取 的数量 ; . d 进行 均衡 生 产 ; . e 用 看板 进行 生 产管 理调 整 ; .
有 如下 几个 特 征 。 1 )消除 浪 费 日本的大野耐一提 出了要消 除以下 7 种形式 的浪
费:
个 工作 小 组 都 成 立 QC小 组 自主 进 行 管 理 , Qc 用 七大 手法 解决设 计 、 产 、 程 、 生 工 质量 、 供应 链管 理 和 销售 等一 系列 日常工 作 问题 , 大 限度 地 满 足 顾 客 最 需求 , 高顾 客满 意度 。 提
司 的各个 层 面进 行 成 本 降低 活动 , 之达 到分 解 后 使
的 目标 成本 。
2 狭 义 精 益 和 广 义 精 益
- 1、下载文档前请自行甄别文档内容的完整性,平台不提供额外的编辑、内容补充、找答案等附加服务。
- 2、"仅部分预览"的文档,不可在线预览部分如存在完整性等问题,可反馈申请退款(可完整预览的文档不适用该条件!)。
- 3、如文档侵犯您的权益,请联系客服反馈,我们会尽快为您处理(人工客服工作时间:9:00-18:30)。
– 步枪的零件可以用于任何步枪
© 1995 Corel Corp.
泰勒(Frederick W. Taylor,1856~1915)
• 1911年,发表《科学管理原理》一书,被后人誉为
“ 科学管理之父”
Any Material Movement That Does Not Directly Support
任何不能直接支持生产 优化的材料移动
请列举:
您的工作业务中的该型浪费有哪些?
4) Waste of Waiting等待的浪费
Any Time That People or Machines are Idle 在一些时间里人员和机器的闲置
C
合并 (Combine)
重排 (Rearrange)
合并作业或操作内容
R
重新排列作业内容与任务
S
简化 (Simplify)
增加 (Increase)
简化作业方法
I
增加必要的作业内容
别让经验成为智慧的枷锁
人们面对变革的第一反应总是:不可能!
经过训练的跳蚤的界限
我试过了,不可能„
让变化成为计划的一部分,由此踏入精益的旅程!
• 被后人称为 “ 动作研究之父” • 研究了如何消除多余的手和身体的动作 • 试验采用适当的工具和设备来优化工作的绩 效。 • 设计了动作分类体系(therbligs),分为17 个基本动素。
© 1995 Corel Corp.
福特控制了从1908到1916的汽车产业
1903年成立福特汽车公司 1908年,福特汽车公司推出T型车 1913年,汽车组装流水线在福特汽车试验成功 容易安装, 互换部件 沿着一条移动的装配线是平衡应用的劳动力
•异常发生迅速响应 •内在质量设计保证 •建立错误预防机制
客户需求
均 衡 化
• Stability(稳定性)
平准化
单件流生产(OPF,One Piece Flow)
连续流是最经济有效的生产方式,不断减少作业批量,直至一个流
单件流或一个流,指的是一次只生产一个部件或产品; 每件立即从一个过程传递到下一个过程,中间不停顿
请列举:
您的工作业务中的该型浪费有哪些?
每个人做的越多越好吗?
整体效率与个体效率
效率改善应着眼于瓶颈
工序时间 5
(分钟)
4
3 2
1
① ② ③ ④ ⑤
工序
8)Lack of Employee Involvement 缺乏员工的参与
没有让员工真正参与生产过程的改善 改善的过程中忽视了以人为本的思想
1978
Lean
1943 - 1978
Shingijutsu
詹姆斯· 沃马克(James Womack), 美国精益企业 研究院(Lean Entreprise Institute)创始人。
典型的精益定义 • 什么是精益? • 精益生产旨在于生产的各个区域排除浪费,包 括客户关系,产品设计,供应链和工厂管理 • 它的目的是要用更少的人力资源,更少的库存, 更少的时间,更少的空间来生产产品以快速响 应客户的需求,同时以最经济有效的方式来保 证产品的高质量。
3. 火眼金睛识浪费
识别浪费考验的是眼光和智慧!
附加价值 1. 生产不良 2. 过度加工 3. 搬运的浪费 4. 等待的浪费 5. 动作的浪费 6. 库存的浪费 7. 过度生产
1) 生产不良的浪费
Repair of a Product or Service to Fulfill Customer Requirements 维修产品或改进服务以满足客户的需求
2. 丰田模式谓精益
Toyota (丰田汽车)的生产系统
丰田喜一郎于1937年创建丰田汽车公司
出生于1895年,其父亲是日本纺织大王丰田佐吉 父亲遗嘱:“我搞织布机,你搞汽车,你要和我一样,通过发明创造为国效 力。” 1982年,通用公司人均生产6辆汽车,人均利润1千4百美元,而丰田公司人均 生产55辆汽车,人均利润1.4万美元 1984年,通用公司为了学习丰田生产方式,与丰田公司合资兴建NUMMI公司。
1975
2000
亚当· 斯密
• 1776年,发表了他的古典经济学说《国富论》。 • 主张:组织和社会将从劳动分工(division of labor)中获得经济利 益,即将工作分解为狭窄的、重复性的任务。
• 工作专业化的普及,无疑都来自斯密倡导的劳动分工的经济利益。
惠特尼(Eli Whitney1765~ 1825)
您无法回收的一件东西就是被浪费的时间
Taiichi Ohno大野耐一
丰田屋
TPS
丰田生产系统
Okay 再来一个
准 时 化
前工序 后工序
自 働 化
Jidoka
JIT
•缩小批量直至单件 •后续拉动前序生产 •依照节拍整体同步
Heijunka平衡生产
• Level Loading(平衡化)
• Sequencing(序列化)
Low Down Inventory To Expose Problem 通过降库存暴露问题
库存水平
维修问题
效率问题
质量问题
交货问题
7)Waste of Overproduction过度生产的浪费
ng More Than Needed 生产大于需求 Producing Faster Than Needed 生产快于需求
请列举:
您的工作业务中的该型浪费有哪些?
6) Waste of Inventory库存的浪费
Any Supply in Excess of Customer Requirements Necessary to Produce Goods or Services Just In Time 为满足及时生产产品或提供服务的需 要,而保存过剩产品。
机器资源的浪费
人力资源的浪费
5) Waste of Motion动作的浪费
Any Movement of People or Machines That Does Not Add Value to the Product or Service 任何不会给产品/服务带来增值的人 员或机器的动作(及移动)
丰田佐吉
丰田喜一郎
Toyota Roots丰田方式的根源
1949年,日本战后的劳动生产率是美国的九分之一,大野耐一指出: 并不是美国人付出了日本人10倍的体力,一定是日本人在生产中存 在着严重的浪费和不合理。
Taiichi Ohno 大野耐一
Shigeo Shingo 新乡重夫
“One thing you can’t recycle is wasted time.”
• 科学管理理论,即应用科学方法确定从事工作的 “最佳方式”。
• 《科学管理的原理》涉及劳动组织、专业化分工、
工作方法、作业测量、工资激励制度和制造工艺过 程等问题
Frederick Taylor
吉尔布雷斯夫妇(F.B. Gilbreth, 1868-1924;L.M. Gilbreth, 1878-1972)
Problems
=
Opportunities
问题 No Problem 没有问题 No Problem
没有问题
= = = =
=
机会 No Improvement 没有改进 Problem
有问题
改善的基本原则
一般称之为ECRS四大原则,现在增加一个“I”原则,并称为5大原则。
符号 E 名称 取消 (Eliminate) 内容 消除无效(不必要)的操作、搬运等活动
请列举:
您的工作业务中的该型浪费有哪些?
2) Waste of Over processing 过度加工的浪费(或称过多工序)
• 对产品和服务无增值意义的工序 • 对于满足功能要求来说不必要的加 工或者过度加工
Engineering Changes
请列举:
您的工作业务中的该型浪费有哪些?
3)搬运的浪费
大规模
• • • • • • 劳动分工 - Adam Smith 互换部件 - Whitney 科学管理 - Taylor 流水装配线 - Ford 需求低变异 - Ford 劳工斗争 • • • •
精益Lean
高度多样化 小批量 六西格玛质量 参与 / 授权的劳动力
1875
1900
1925
1950
•库存如何确定其合理性? •安全库存真的安全吗?
Inventory Covers All Problem 库存掩盖所有问题
库存水平
维修问题
效率问题
质量问题
交货问题
Low Down Inventory To Expose Problem 通过降库存暴露问题
库存水平
维修问题
效率问题
质量问题
交货问题
精益改变思想
-精益生产的基本理念1. 效率革新漫漫路
2. 丰田模式谓精益
3. 火眼金睛识浪费 4. 持续改善除脑障
2011年7月25日 讲师:曹晓峰
1. 效率革新漫漫路
回顾制造业的历史
手工艺
• • • • • 只是根据客户规格生产 单件生产…每个产品是唯一的 变化的质量 小库存 高成本…为富人生产
批量处理 – 1 minute per piece 连续流动 – Make One Move One
A
B
C
A
B
C
Cycle Time= 30++ Min (weeks)
Cycle Time= 12 Min