零件变形的原因
机械零件加工变形的原因分析及其改进

机械零件加工变形的原因分析及其改进摘要:机械零件在加工过程中发生变形难以避免,同时也是机械加工行业中广泛关注的问题。
由于机械零件加工中发生变形容易影响零件质量,因此,应尽可能减少由于变形而引起的质量问题。
文章首先分析了机械零件加工变形的原因,然后寻找相应的改进策略,以期对机械零件加工变形的处理提供参考借鉴。
关键词:机械零件;加工变形;原因;改进机械加工过程中由于受到种种因素的影响,机械零件加工的变形问题一直层出不穷,变形的零件不仅给机械加工业带来了经济损失,而且还影响到了企业在社会上的信誉,产品质量不能得到保证,这样的发展现状不利于机械加工业的正常运营,所以必须找到机械零件加工变形的原因,从而寻求解决问题的办法,推进机械加工业的长期发展。
1 常见机械零件加工中变形的原因1.1 由于内力的作用,零件加工精度改变因为在车床加工的过程中,通常采用四爪卡盘卡紧零件,然后利用其向心内力的作用,对零件进行加工。
并且在零件加工的过程中,也会受到内径向力的作用。
如果没有很好的掌控这两种内力,会导致机械零件松动,进而导致零件加工变形现象的发生。
另外,还应该注意如果机械零件的夹紧力减小,则机械的切削力也要随之而减小,相反机械零件夹紧力变大,机械的切削力也必须加大,只有这样才能保证所加工的零件受力均匀。
但是在实际加工中所面临的问题是,加工后的机械零件的形状与需要形状并不匹配,其精确度已经出现了很大的出入,而出现这种状况的原因是加工不够细腻,导致质量不过关。
1.2 热处理后和加工后机械零件变形问题一些比较薄的机械零件很容易变形,因为他们的长径比例较大,在加工或者热处理后会出现弯曲的状况,这种弯曲被称为草帽弯曲。
这种弯曲会导致其平面变大,而长径比较小的机械零件经过热处理或是加工后也会出现变形,导致零件的直线度相对偏大。
原因是零件本身就具有内应力,而这种内应力是相对平衡的状态,但经过热处理或加工之后,零件自身的内应力发生改变,从而导致零件的外观发生变形。
铝压铸零件抛丸变形原因
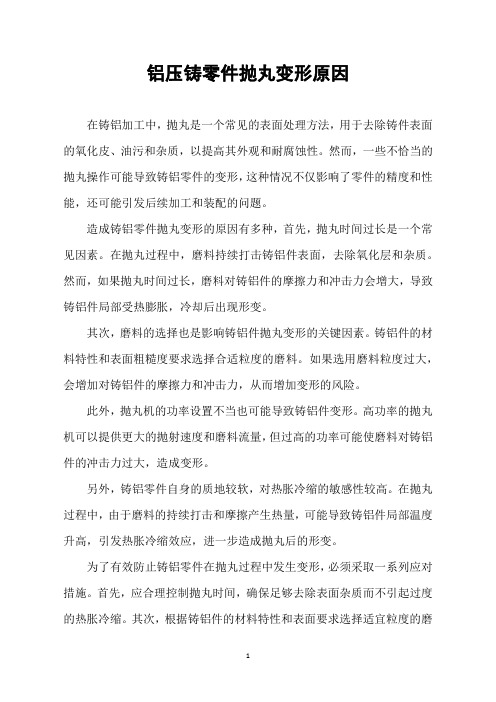
铝压铸零件抛丸变形原因在铸铝加工中,抛丸是一个常见的表面处理方法,用于去除铸件表面的氧化皮、油污和杂质,以提高其外观和耐腐蚀性。
然而,一些不恰当的抛丸操作可能导致铸铝零件的变形,这种情况不仅影响了零件的精度和性能,还可能引发后续加工和装配的问题。
造成铸铝零件抛丸变形的原因有多种,首先,抛丸时间过长是一个常见因素。
在抛丸过程中,磨料持续打击铸铝件表面,去除氧化层和杂质。
然而,如果抛丸时间过长,磨料对铸铝件的摩擦力和冲击力会增大,导致铸铝件局部受热膨胀,冷却后出现形变。
其次,磨料的选择也是影响铸铝件抛丸变形的关键因素。
铸铝件的材料特性和表面粗糙度要求选择合适粒度的磨料。
如果选用磨料粒度过大,会增加对铸铝件的摩擦力和冲击力,从而增加变形的风险。
此外,抛丸机的功率设置不当也可能导致铸铝件变形。
高功率的抛丸机可以提供更大的抛射速度和磨料流量,但过高的功率可能使磨料对铸铝件的冲击力过大,造成变形。
另外,铸铝零件自身的质地较软,对热胀冷缩的敏感性较高。
在抛丸过程中,由于磨料的持续打击和摩擦产生热量,可能导致铸铝件局部温度升高,引发热胀冷缩效应,进一步造成抛丸后的形变。
为了有效防止铸铝零件在抛丸过程中发生变形,必须采取一系列应对措施。
首先,应合理控制抛丸时间,确保足够去除表面杂质而不引起过度的热胀冷缩。
其次,根据铸铝件的材料特性和表面要求选择适宜粒度的磨料,以减小摩擦力和冲击力。
此外,调整抛丸机的功率至适当水平,以保持适当的抛射速度和磨料流量。
同时,可以在铸铝件的热敏感区域采取适当的冷却措施,以降低局部温度升高的风险。
通过这些措施的综合应用,可以显著减少铸铝零件在抛丸过程中的变形问题,提高加工效率和零件质量。
机械零件变形及矫正方法

机械零件变形及矫正方法
机械零件在制造和组装过程中,可能会出现变形的情况。
这些变形会导致零件
的功能和性能受到影响,甚至使整个机械系统无法正常工作。
因此,及时发现和矫正机械零件的变形是非常重要的。
首先,我们需要了解机械零件变形的原因。
机械零件的变形可能是由于材料应力、温度变化、加工误差或装配问题等引起的。
一旦发现机械零件出现变形,我们可以采取以下几种方法进行矫正。
1. 机械矫正:对于小型变形,可以使用机械手工矫正的方法。
通过在变形处施
加适当大小的力或压力,使零件恢复到设计规格。
2. 热处理:对于材料应力引起的变形,可以采用热处理方法。
通过将零件加热
至适当温度,并进行冷却处理,可以消除或减小应力,使零件恢复原状。
3. 水平调整:一些较大的机械零件变形可能需要进行整体调整。
通过在机械系
统中添加补偿件或调整装配结构,可以达到修正变形的目的。
4. 加强设计与制造控制:为了避免机械零件变形的发生,我们需要在设计和制
造过程中注意控制材料的应力分布、温度的影响、加工精度和装配质量等相关因素。
通过优化设计和加强制造过程的质量控制,可以降低机械零件变形的风险。
需要注意的是,在矫正机械零件变形时,我们应根据具体情况选择合适的方法。
对于复杂的机械系统,可能需要专业技术人员进行分析和处理。
同时,我们还应注意不要过度矫正,以免引入新的问题或导致零件损坏。
总之,机械零件的变形对机械系统的性能和可靠性有重要影响。
通过了解变形
原因,并采取合适的矫正方法,我们可以及时修正机械零件的变形,保障机械系统的正常运行。
铸铝为变形原因
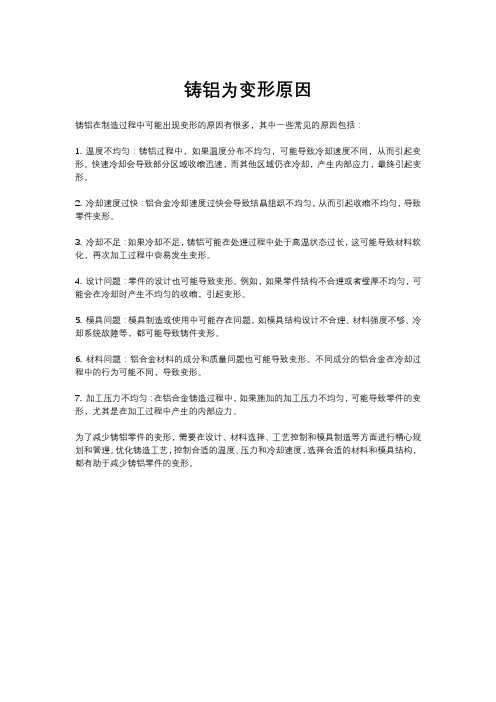
铸铝为变形原因
铸铝在制造过程中可能出现变形的原因有很多,其中一些常见的原因包括:
1. 温度不均匀:铸铝过程中,如果温度分布不均匀,可能导致冷却速度不同,从而引起变形。
快速冷却会导致部分区域收缩迅速,而其他区域仍在冷却,产生内部应力,最终引起变形。
2. 冷却速度过快:铝合金冷却速度过快会导致结晶组织不均匀,从而引起收缩不均匀,导致零件变形。
3. 冷却不足:如果冷却不足,铸铝可能在处理过程中处于高温状态过长,这可能导致材料软化,再次加工过程中容易发生变形。
4. 设计问题:零件的设计也可能导致变形。
例如,如果零件结构不合理或者壁厚不均匀,可能会在冷却时产生不均匀的收缩,引起变形。
5. 模具问题:模具制造或使用中可能存在问题,如模具结构设计不合理、材料强度不够、冷却系统故障等,都可能导致铸件变形。
6. 材料问题:铝合金材料的成分和质量问题也可能导致变形。
不同成分的铝合金在冷却过程中的行为可能不同,导致变形。
7. 加工压力不均匀:在铝合金铸造过程中,如果施加的加工压力不均匀,可能导致零件的变形,尤其是在加工过程中产生的内部应力。
为了减少铸铝零件的变形,需要在设计、材料选择、工艺控制和模具制造等方面进行精心规划和管理。
优化铸造工艺,控制合适的温度、压力和冷却速度,选择合适的材料和模具结构,都有助于减少铸铝零件的变形。
零件装夹变形分析与解决措施

零件装夹变形分析与解决措施零件变形主要表现在装夹变形;切削力、切削热使零件产生变形;加工方法和技巧不当使零件产生变形;材料应力释放零件原因导致的变形等。
如果在生产过程中工件产生变形,那么肯定就会影响工件的形位精度,尺寸精度以及表面粗糙度,所以提高易变形零件加工质量和加工效率的关键就是装夹方法以及车削,铣削时的加工方法和技巧。
标签:装夹方法;刀具选择;切削用量1 为什么会产生零件装夹变形我们在加工生产中会遇到各种各样的问题,譬如在加工薄壁易变型零件时,就必须根据其不同的特点,找出薄弱环节,选用不同的工艺方法和夹紧方法来保证加工要求。
很多时候我们要具体问题具体分析,找到切实可行的办法来应对遇到的实际问题。
1.1 工件装夹不当为什么会产生变形?在我们生产实际操作中,如果我们采用三爪卡盘夹紧薄壁外圆,就会由于夹紧面积过小,夹紧力不均匀分布,那么拆卸以后,被卡爪夹紧部分就可能因弹性变形而涨大,最终导致零件出现多角形变化。
1.2 相对位置调整时候偏差,产生壁厚不均的现象经过多年的工作实践,我发现由于夹具、刀具,工件和机床主轴旋转中心的位置调整相对不准确,导致工件几何形状变化和壁厚不均匀现象。
我们遇见很多薄壁零件对于均匀性要求非常高,但对其尺寸精度要求却不高这种现象。
此时工件如果采用常规刚性定位,就会误差非常大,壁的厚度很容易超差。
这样工件在装夹过程中,假设我们没有根据实际特性,也就是工件刚度较低(薄壁件),或者不注意夹紧力的方向和施力点,那么支撑点和压紧点不能够重合就形成力矩效应,最终会引起零件变形。
1.3 为什么要强调零件壁厚差重要性有一部分薄壁零件对均匀性要求非常高,而对其尺寸精度要求却不高。
这种工件和彩刚性定位,就会误差很大,壁厚非常容易超差。
在装夹过程中的工件,假设刚度较低(薄壁件)或者夹紧力方向,施力点选择不恰当,支撑点与压紧点不重合必然形成力矩效应将会引起零件变形。
1.4 选用什么样的刀具至关重要我们选择什么样的刀具,会直接影响零件精度以及表面粗糙度。
如何分析产生变形的原因
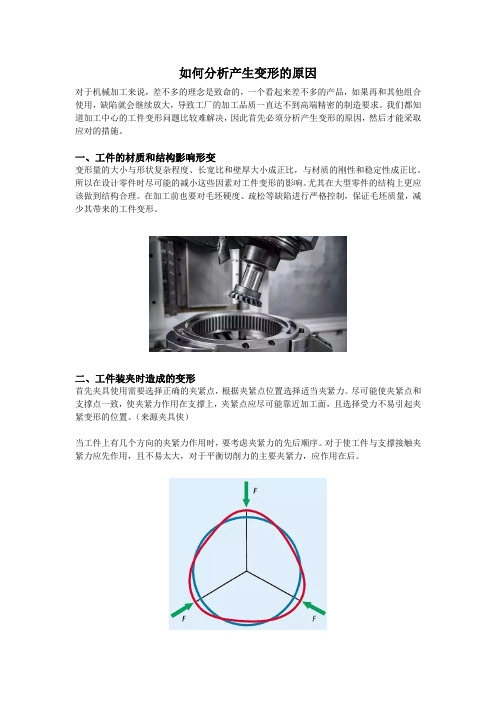
如何分析产生变形的原因对于机械加工来说,差不多的理念是致命的,一个看起来差不多的产品,如果再和其他组合使用,缺陷就会继续放大,导致工厂的加工品质一直达不到高端精密的制造要求。
我们都知道加工中心的工件变形问题比较难解决,因此首先必须分析产生变形的原因,然后才能采取应对的措施。
一、工件的材质和结构影响形变变形量的大小与形状复杂程度、长宽比和壁厚大小成正比,与材质的刚性和稳定性成正比。
所以在设计零件时尽可能的减小这些因素对工件变形的影响。
尤其在大型零件的结构上更应该做到结构合理。
在加工前也要对毛坯硬度、疏松等缺陷进行严格控制,保证毛坯质量,减少其带来的工件变形。
二、工件装夹时造成的变形首先夹具使用需要选择正确的夹紧点,根据夹紧点位置选择适当夹紧力。
尽可能使夹紧点和支撑点一致,使夹紧力作用在支撑上,夹紧点应尽可能靠近加工面,且选择受力不易引起夹紧变形的位置。
(来源夹具侠)当工件上有几个方向的夹紧力作用时,要考虑夹紧力的先后顺序。
对于使工件与支撑接触夹紧力应先作用,且不易太大,对于平衡切削力的主要夹紧力,应作用在后。
增大工件与夹具的接触面积或采用轴向夹紧力。
增加零件的刚性,是解决发生夹紧变形的有效办法,但由于薄壁类零件的形状和结构的特点,导致其具有较低的刚性。
这样在装夹施力的作用下,就会产生变形。
增大工件与夹具的接触面积,可有效降低工件件装夹时的变形。
如在铣削加工薄壁件时,大量使用弹性压板,目的就是增加接触零件的受力面积;在车削薄壁套的内径及外圆时,无论是采用简单的开口过渡环,还是使用弹性芯轴、整弧卡爪等,均采用的是增大工件装夹时的接触面积。
这种方法有利于承载夹紧力,从而避免零件的变形。
采用轴向夹紧力,在生产中也被广泛使用。
设计制作专用夹具可使夹紧力作用在端面上,可以解决由于工件壁薄,刚性较差,导致的工件弯曲变形。
三、工件加工时造成的变形工件在切削过程中由于受到切削力的作用,产生向着受力方向的弹性形变,就是我们常说的让刀现象。
薄壁零件加工中存在的问题

薄壁零件加工中存在的问题在薄壁零件加工中,可能会面临一些常见的问题。
解决这些问题需要仔细分析每个步骤,并采取相应的措施。
以下是一些可能存在的问题和解决建议:1.变形问题:原因:薄壁零件在加工中容易发生变形,主要是由于切削力引起的材料内应力释放。
解决方案:选择合适的切削参数,采用适当的刀具,减小切削力。
可以考虑采用工艺补偿或者后续的校正工序。
2.毛刺和切屑:原因:薄壁零件的切屑很容易残留在切削区域,形成毛刺。
解决方案:采用适当的切削速度和进给速度,选择合适的切削刃具。
可以考虑添加冷却液以减少热影响,避免切削区域积聚切屑。
3.表面质量问题:原因:薄壁零件的加工可能导致表面粗糙度增加或表面平整度降低。
解决方案:使用高精度的加工设备和刀具。
确保刀具磨损良好,避免振动和共振问题。
定期检查和维护设备。
4.工艺稳定性问题:原因:薄壁零件的加工可能受到环境温度、湿度等因素的影响,导致工艺不稳定。
解决方案:控制加工环境的温湿度,采用合适的工艺参数。
在加工之前,对材料和设备进行预热,确保加工过程中的稳定性。
5.材料选择问题:原因:不同的材料对于薄壁零件加工的难度不同。
解决方案:在设计阶段选择适合加工的材料,考虑材料的强度、塑性等特性。
必要时,进行材料热处理以提高加工性能。
6.加工成本问题:原因:薄壁零件的加工可能涉及到高难度的工艺,导致加工成本增加。
解决方案:寻找合适的工艺和设备,优化刀具选择和切削参数,以降低加工成本。
考虑批量生产以提高效益。
通过综合考虑材料、工艺、设备和人员等因素,可以有效解决薄壁零件加工中可能出现的问题,提高加工质量和效率。
铝压铸零件抛丸变形原因
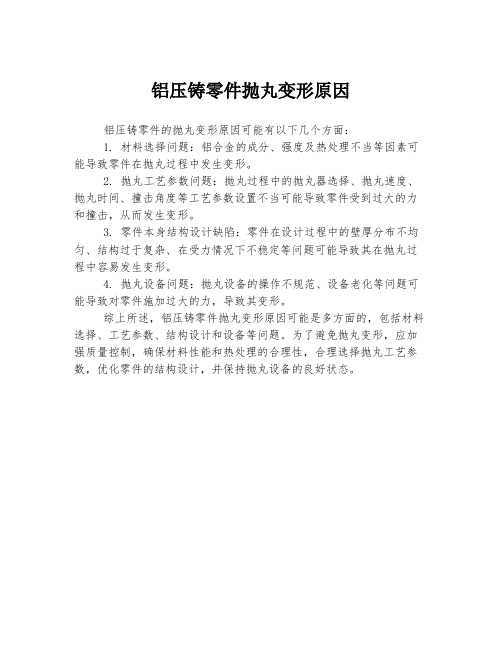
铝压铸零件抛丸变形原因
铝压铸零件的抛丸变形原因可能有以下几个方面:
1. 材料选择问题:铝合金的成分、强度及热处理不当等因素可能导致零件在抛丸过程中发生变形。
2. 抛丸工艺参数问题:抛丸过程中的抛丸器选择、抛丸速度、抛丸时间、撞击角度等工艺参数设置不当可能导致零件受到过大的力和撞击,从而发生变形。
3. 零件本身结构设计缺陷:零件在设计过程中的壁厚分布不均匀、结构过于复杂、在受力情况下不稳定等问题可能导致其在抛丸过程中容易发生变形。
4. 抛丸设备问题:抛丸设备的操作不规范、设备老化等问题可能导致对零件施加过大的力,导致其变形。
综上所述,铝压铸零件抛丸变形原因可能是多方面的,包括材料选择、工艺参数、结构设计和设备等问题。
为了避免抛丸变形,应加强质量控制,确保材料性能和热处理的合理性,合理选择抛丸工艺参数,优化零件的结构设计,并保持抛丸设备的良好状态。
- 1、下载文档前请自行甄别文档内容的完整性,平台不提供额外的编辑、内容补充、找答案等附加服务。
- 2、"仅部分预览"的文档,不可在线预览部分如存在完整性等问题,可反馈申请退款(可完整预览的文档不适用该条件!)。
- 3、如文档侵犯您的权益,请联系客服反馈,我们会尽快为您处理(人工客服工作时间:9:00-18:30)。
1.零件变形的原因:毛坯制造、机械加工、操作使用、修理质量。
2.磨损的表示方法:磨损量、磨损率、耐磨性、相对耐磨性。
3.装配工艺过程一般由:装配前准备、装配工作、校正、检验、油封及包装。
组织形
式,固定式装配、移动式装配。
4.典型零件磨损过程:跑合阶段、稳定磨损阶段、急剧磨损阶段。
5.机械修复方法:镶加零件修复法、局部修复法、塑性变形法、金属扣合法。
机械联
接(螺纹联接、键、铆、销、过盈配合)和机械变形。
6.确定直齿圆柱齿轮变位系数方法:公法线长度测量、啮合中心距法、固定弦齿厚的
测量。
1.局部互换法:考虑到各零件的加工误差是随机的,可以将尺寸链中各环的公
差放宽些,使其容易加工,降低成本。
2.热喷涂:用高温热源将喷涂材料加热至熔化或呈塑性状态同时用高速气流使
其雾化,喷到经过预处理的工作表面,将喷涂层继续加热,使之达到熔融状
态而与基体形成冶金结合,获得牢固的工作层。
3.平尺作用:用于检验工件的直线度、平面度误差,也可以做为研刮的基准,
有时还用来检验零、部件的相互位置精度。
4.基准不变修理法:在修复尺寸链的精度时,只选取一个基面,而所有的作用
面的修理,都以此面为基准。
5.修配法:把零件的公差放大制造,使零件装配时能够有一定的返修余量,经
过个别零件的修配加工,最后达到所要求的装配精度。
8电镀:利用电解的方法,使金属或合金沉积在零件表面上形成金属镀层的方法。
1.
1.调整法:将补偿件移动一定距离或者装入一个具有补偿量的补偿件来实现误
差的补偿。
锥形尺寸棒作用:主要用来检验主轴、套筒类零件的径向跳动,
轴向串动,也用来检验直线度、平行度、同轴度、垂直度等。
2.一、细刮:a).用细刮刀进行,在粗刮的基础上进一步增加接触点。
b)刮削时,刀
花宽应在6-8mm,长10-25mm,刮深0.01-0.02mm。
c)刮第二遍时应与第一遍交叉45°-60°的方向进行。
d)在刮削中,应将高点周围部分也刮去,以使周围的次高
点容易显示出来,可节省刮削时间。
e)细刮后的点子一般在每刮方内12-15点即可。
3.二、精刮:a)在细刮后,为进一步提高工件表面质量b)刮削时,要用小型刮刀或
将刀口磨成弧形c)刀花宽应在3-5mm,长3-6mm左右,每刀均应落在点子上d)刮去最大最亮的点子,挑开中等点子,小点子留下不刮e)精刮后表面点子数在20-25点以上。
4.三、环氧沙浆的配方及原料:配方,6101环氧树脂E-44 100份苯二甲酸二丁酯
17份乙二胺(固化剂)8份沙(填粒)250份方法:1.将E-44用水浴或沙浴加热到80℃;2.加入苯二甲酸二乙脂;3冷却至30-35加入乙二脂;4把沙加热到30-35作为填料加入。
5.四、刷度工作原理:刷度时工件与专用直流电源的负极相连,刷镀笔与电源正极连
接,刷镀笔上的阳极包裹着棉花和棉纱布,蘸上刷镀专用的电解液,与工件待镀表
面接触并做相对运动,接通电源后,电解液中的金属离子在电场作用下向工件表面
迁移,从工件表面获得电子还原成金属原子,结晶沉积在工件表面上形成金属镀层。
6.五、粘接的工艺原理:1使粘接接头受剪不受拉。
2适当增大粘接面积3机体材料
与粘接剂具有相同的膨胀系数。
7.六、疲劳断裂的原理及断口图:零件受循环载荷时,在局部将出现很大的塑性变形,
表面将出现一些滑移线或滑移带,滑移带中产生一些缺口峰,峰底将产生高度集中
应力,在持续反复载荷作用下,经过一定周期,发展成微观裂纹,微观裂纹进一步
加强滑移带的应力集中,在循环负荷作用下,裂纹继续向内部发展。
很多裂纹的深
度增加,连接成一个主导裂纹,当其达到临界长度后,突然发生断裂。
8.七、
螺母
F
F
预应力钢筋矫直原理:在桥式起重机主梁下盖板两端,焊上两个刚性很强的支架角钢如图.在角钢上钻孔,再安装上两端带螺纹、经过强度计算的钢筋,用螺母拧紧,拉紧钢筋,使之产生适度的预应力,使起重机主梁反拱而矫正主梁下挠。
1.八、用公法线确定齿轮模数:1分别测k、k-1或k+1个齿得公法线长度Wk、Wk-1、
Wk+1;2计算基圆齿距Pb=Wk-Wk-1或Pb=Wk+1-Wk;3查基圆齿距表,经分析初
步确定m;4用其他方法如齿形卡板法或标准齿轮滚刀对齿法校验确定m.
2.九、轴类零件测绘注意事项:1必须了解该轴、套的用途及各个构成部分的作用2
了解该轴、套在部件中的安装位置所构成的尺寸链;3测绘时在草图上标明各种配
合要求或公差数值、表面粗糙度、材料和热处理及其他技术要求;4测量零件各部
分尺寸;5注意基准是否完好;6细长轴应妥当放置,防止测绘变形。
3.十、粘接工艺:1不受材料限制2粘接温度不高3不破坏原强度,不易产生局部应
力4工艺简便,成本低,便于现场修复5胶缝有密封、耐磨、耐腐蚀和绝缘等特性。
4.十一、齿轮测绘步骤:1了解被修设备的名称、型号、生产国、出厂日期及生产厂
家。
2初步判定齿轮类别;3查找与主要几何要素有关的资料;4作被测齿轮精度等级、材料和热处理鉴定;5分析被测齿轮的失效形式原因;6测绘、推算齿轮参数及画齿轮工作图。
5.十二、S1-s3/x=D/L l/L=Y/x y=bl/D e=a1-a3/2
6.十三、设置一个调整环,1计算总公差;2分配公差,TM=TΣ/(t√(λ)²Mi(n-1));3
按向体确定组成除调整环公差;4计算上下极限偏差BMAΣ=ΣBMAi增-ΣBMAi减;5
验算精度是否满足TΣ=t√ (Σλi²Ti²);6验算超差率T’Σ=√(Σki²Ti²)。