车架的有限元分析及优化
山地车车架有限元分析及改进
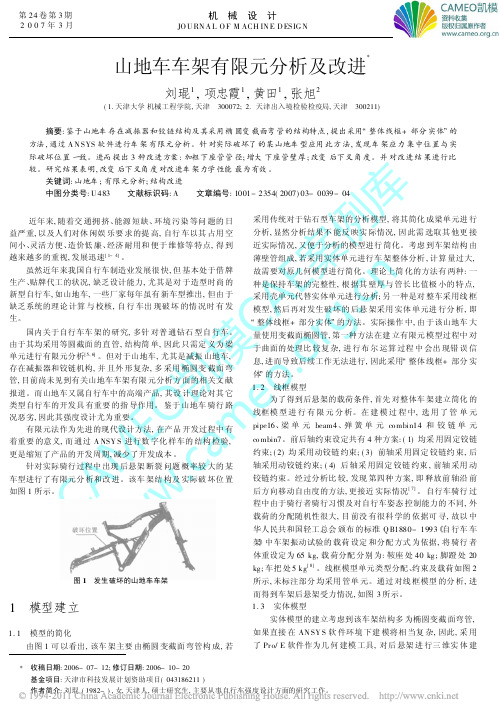
凯 o 报道。而山地车又属自行车中的高端产品, 其设 计理论对其 它
类型自行车的开发具 有重要 的指 导作用。 鉴于 山地车 骑行 路
e 况恶劣, 因此其强度设计尤为重要。 O 有限元法作为先进的现代设计方法, 在产品 开发过程中 有 E m 着重要 的意义, 而 通过 A NSY S 进行数 字化 样车的 结构 检验,
[ 2] M cK enna S P, H ill M R. H ul l a singl e l oading dir ect ion f or f at igue l ife pr edict ion an d t est ing of h andl ebars for off- road bicycles [ J ] . Int ernat ional Journal of Fat igue, 2002, 24 ( 11) : 1 149 1 157.
2007 年 3 月
刘琨, 等: 山地车 车架有限元分析及改进
41
最大计算应力值均小于其许用应力, 同样满足 强度要求。
库
例
E案 n 表 1 不同改进方案最大应力值及其变化情况
A .c 原车架 方案一 方案二
C g 最大应力/ MPa
119 96
88
r 最大应力降低值/ MPa 0
23
31
模 .o 最大应力降低幅度 0 19. 33% 26. 05%
1. 1 模型的简化
如果直接 在 AN SY S 软 件环境 下建 模将相 当复 杂, 因此, 采 用
由图 1 可 以看出, 该车 架主要 由椭圆 变截面 弯管构 成, 若 了 Pr o/ E 软件作为几 何 建模 工具, 对后 悬架 进 行三 维实 体 建
消防车副车架有限元分析及扭刚度优化研究

!技朮iE lE M n u o d e N H O W J .消防车副车架有限元分析及扭刚度优化研究Finite Element A nalysis and Torsion Stiffness Optimization Researchof Subframe of Fire Truck黄开李乡安蒋旭欧涛HUANG Kai etal长沙中联消防机械有限公司湖南长沙410200摘要:针对某款消防车在稳定试验过程中出现活动支腿离地高度过大的问题进行了研究,运用ANSYS有限元分析软件,建立了消防车的副车架、底盘和活动支腿的装配体有限元模型,对消防车作业平台进行了全工况分析,找到了离地高度最大工况及导致活动支腿离地高度过大的原因。
针对副车架设计上的不足,对副车架结构进行了优化,在不增加副车架质量的基础上,使250。
工况的离地高度降低了30%关键词:消防车副车架有限元分析离地高度Abstract This article focuses on the problem of excessive stabilizer's groundclearance of a certain fire truck during the stability test.An assembly finite elementmodel of the subframe,chassis and stabilizer of fire truck was created by the finiteelement software ANSYS.The maximum ground clearance loadcase of stabilizer isobtained through full working condition analysis.The reason for the excessive groundclearance is founded.A optimization for torsion stif&ess of subframe is performedand the ground clearance is reduced by30%without increasing the weight ofsubframe.Key words fire truck;subframe;finite element analysis;height above ground第一作者r黄开,男,1983年生,工程师,现从事消防车辆设中圈分类号:U469.60文献标识码:A文章编号:1004-0226(2020)12-0086-041前言随着市场对消防车的作业高度需求不断提升,消防车的整车质量也随之增大。
车架有限元分析

以ANSYS软件为分析工具对从国外引进的某重型车的车架进行了有限元分析、模态分析和以路面谱为输入的随机振动分析,通过用壳单元离散车架及MPC单元模拟铆打传力建立计算模型,研究该车架静、动态性能,了解该车架的优缺点。
车架是汽车的重要组成部分,在汽车整车设计中占据着重要位置,车架结构设计历来为广大汽车厂商所重视。
本文以某汽车公司从欧洲引进的某重型车车架为研究对象,对该车架结构的动、静态特性进行分析计算,消化、吸收欧洲的先进技术并在此基础上进行自主创新设计。
分析手段主要是通过建立正确的有限元分析模型,对车架进行典型工况的静态分析、模态分析和路面不平度引起的随机振动分析,以此了解车架的静态和动态特性,了解该车架的优越性能及其不足之处,为新车架的改型设计提供依据。
1 有限元分析模型的建立该车架为边梁式,由两根位于两边的纵梁和若干根横梁组成,用铆接或焊接方式将纵梁和横梁联接成坚固的刚性结构,纵梁上有鞍座,其结构如图1所示。
由于车架是由一系列薄壁件组成,有限元模型采用壳单元离散能详细分析车架应力集中问题,可以真实反映车架纵、横梁联接情况,是目前常采用的一种模型。
该车架是多层结构,纵梁断面为槽形,各层间用螺栓或铆钉联接,这种结构与具有连续横截面的车架不同,其力的传递是不连续的。
该车架长7m,宽约0.9 m,包括双层纵梁、横梁、外包梁、背靠梁、鞍座、飞机板、铸铁加强板、发动机安装板、三角支撑板和后轴等部分。
考虑到车架几何模型的复杂性,可在三维CAD软件UG里建立车架的面模型,导人到Hypermesh 软件中进行网格划分等前置处理,然后提交到ANSYS解算。
车架各层之间的铆钉联接,可以用Hypermesh-connectors中的bar单元来模拟铆钉联接,对应的是ANSYS的MPC单元,因车架各层间既有拉压应力,又有剪应力,故MPC的类型应选择Rigid Beam方式。
由于该车是多轴车,为超静定结构,为了得到车架结构的真实应力分布,必须考虑悬挂系统的变形情况。
基于有限元法的车架轻量化设计和仿真分析

基于有限元法的车架轻量化设计和仿真分析有限元法在车架轻量化设计和仿真分析中是一种常用的工具。
该方法基于数学模型,将结构划分成一系列小的单元,通过计算每个单元的应力、变形等物理量,反推得到整个结构的力学性能。
在车架轻量化方面,有限元法可以帮助我们快速地找到轻量化的设计方案,并通过仿真分析验证其性能,从而提高车架的安全性和可靠性。
首先,在轻量化设计中,我们需要寻找轻量化的潜在方案。
有限元法可以帮助我们划分车架结构,并计算不同部件的受力情况。
通过对受力情况的分析,我们可以找到那些不必要的部件或重量过剩的区域,从而进行删减。
例如,我们可以尝试使用高强度材料或降低材料使用量等方式来达到轻量化的目的。
其次,在设计轻量化方案后,需要通过仿真分析来验证其性能。
在有限元法中,我们可以将车架结构的物理特性输入到数学模型中,并通过计算得出其应力分布、变形情况等。
通过这种方式,我们可以在实际试验之前,快速地评估轻量化方案的性能,并进行修改和优化。
最后,有限元法还可以帮助我们改进设计方案,以进一步提高车架的性能。
例如,在仿真分析中,我们可以调整材料的类型和厚度,以达到更好的性能。
我们还可以通过优化部件的形状和尺寸,来减少结构的应力集中和变形等问题。
总之,有限元法在车架轻量化设计和仿真分析中是一种非常有效的工具。
通过使用该方法,我们可以快速地找到轻量化方案,并通过性能仿真进行验证和优化,最终提高车架的安全性和可靠性。
为了能更清楚地了解车架轻量化设计和仿真分析的数据,我们可以以一辆小型轿车为例,尝试列出相关数据并进行分析。
首先,我们需要了解该汽车原始的车架结构的总重量、尺寸和材料类型及数量等情况。
假设该汽车的车架总重量为1000千克,尺寸为4000毫米长、1500毫米宽和1500毫米高,使用的材料为钢材和铝材,其中钢材使用量为80%。
我们可以看到,该车架的重量相对较高,需要进行轻量化设计。
接下来,我们可以通过有限元法对该车架进行轻量化设计。
汽车结构有限元分析
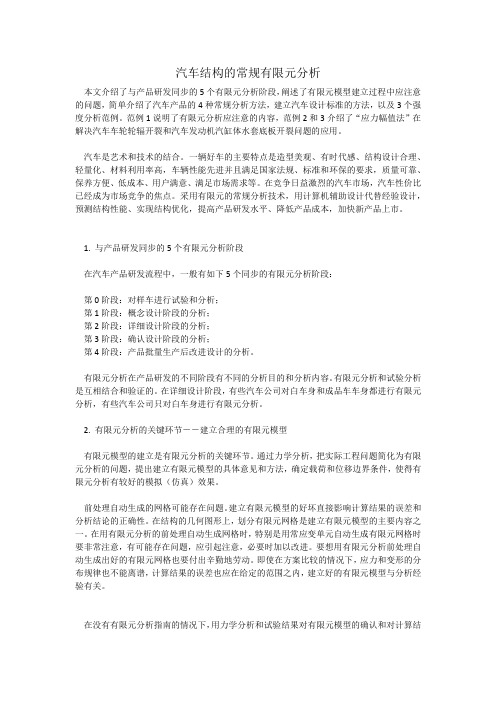
汽车结构的常规有限元分析本文介绍了与产品研发同步的5个有限元分析阶段,阐述了有限元模型建立过程中应注意的问题,简单介绍了汽车产品的4种常规分析方法,建立汽车设计标准的方法,以及3个强度分析范例。
范例1说明了有限元分析应注意的内容,范例2和3介绍了“应力幅值法”在解决汽车车轮轮辐开裂和汽车发动机汽缸体水套底板开裂问题的应用。
汽车是艺术和技术的结合。
一辆好车的主要特点是造型美观、有时代感、结构设计合理、轻量化、材料利用率高,车辆性能先进并且满足国家法规、标准和环保的要求,质量可靠、保养方便、低成本、用户满意、满足市场需求等。
在竞争日益激烈的汽车市场,汽车性价比已经成为市场竞争的焦点。
采用有限元的常规分析技术,用计算机辅助设计代替经验设计,预测结构性能、实现结构优化,提高产品研发水平、降低产品成本,加快新产品上市。
1. 与产品研发同步的5个有限元分析阶段在汽车产品研发流程中,一般有如下5个同步的有限元分析阶段:第0阶段:对样车进行试验和分析;第1阶段:概念设计阶段的分析;第2阶段:详细设计阶段的分析;第3阶段:确认设计阶段的分析;第4阶段:产品批量生产后改进设计的分析。
有限元分析在产品研发的不同阶段有不同的分析目的和分析内容。
有限元分析和试验分析是互相结合和验证的。
在详细设计阶段,有些汽车公司对白车身和成品车车身都进行有限元分析,有些汽车公司只对白车身进行有限元分析。
2. 有限元分析的关键环节――建立合理的有限元模型有限元模型的建立是有限元分析的关键环节。
通过力学分析,把实际工程问题简化为有限元分析的问题,提出建立有限元模型的具体意见和方法,确定载荷和位移边界条件,使得有限元分析有较好的模拟(仿真)效果。
前处理自动生成的网格可能存在问题。
建立有限元模型的好坏直接影响计算结果的误差和分析结论的正确性。
在结构的几何图形上,划分有限元网格是建立有限元模型的主要内容之一。
在用有限元分析的前处理自动生成网格时,特别是用常应变单元自动生成有限元网格时要非常注意,有可能存在问题,应引起注意,必要时加以改进。
基于有限元分析的车架纵梁焊接变形优化研究

变 形 。焊 接 变 形 不 但 会 引起 形 状 和 尺 寸 的 改 变 , 影 响结 构 尺 寸 的准 确 性 ,还 会 造 成 焊 接 件 在 装 配
过 程 中与 其 他 误 差 发 生 耦 合 、积 累 和 传 播 ,形 成 焊 接 制 造 的综 合 偏 差 。 同时 ,焊 接 变 形 也 会 降 低
.
2 0 1 3 -1 1 ( 上) 【 3 7 】
l 注 匐 似
1 . 2 纵梁焊接变形原因 焊 接 变 形 的 根 本 原 因 虽 然都 是不 均 匀 加 热 、
冷 却 及 产 生 不 均 匀 的 塑 性 变 形 , 但 具 体 结 构 不
在Hy p e r me s h 中对纵 梁数 模 进行 几何 清理 和 网
张 爽 ,高金刚,门玉琢 ,刘锡敏 ,王大宇
ZHANG Sh u a n g ,GAO J i n - g an g,M EN Yu - z h u o ,LI U Xi — mi n ,V V ANG Da - y u
( 长春工程学 院,长春 1 3 0 0 1 2 )
摘 要:本文利用固有应变方法 ,使用H Y P E R M E S H 和A N S Y S 软件对载重汽车车架纵梁焊接变形进行
车 架 结 构 的承 载 能 力 和 使 用 寿 命 。因 此 ,控 制 车 架 纵 梁 的焊 接 变 形 是 制 定 纵 梁 焊 接 工 艺 主 要 内容
之一。
所 示为 卡车 车架 纵梁 简 图。
A
—
A
( a ) 纵 梁 圭 视 图
纵 梁 是卡 车 的主 要部 件 , 国 内轻 型 车 车 架纵
半挂牵引车车架结构强度有限元分析及优化
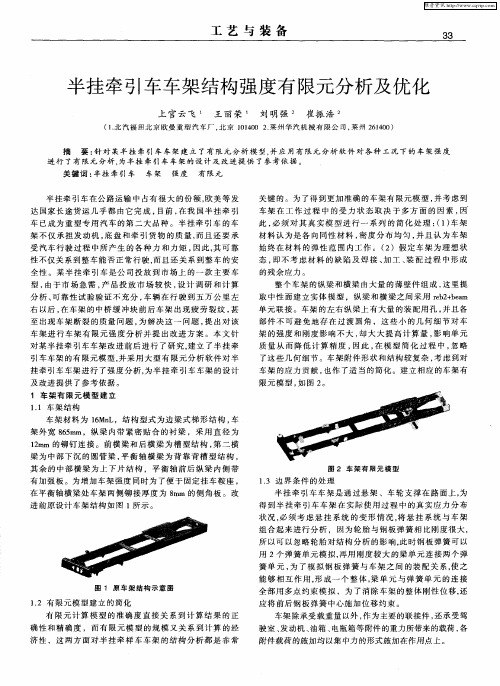
架 的强 度 和 刚度 影 响不 大 , 大 大 提 高计 算 量 , 响 单元 却 影
质量从而降低计算精度 , 因此 , 模 型 简 化 过 程 中 , 略 在 忽 了这 些几 何 细节 。车 架 附件形 状 和结 构 较复 杂 , 考虑 到对 车架 的应 力 贡献 , 作 了适 当 的简 化 。建 立 相应 的车 架有 也
摘 要 : 对 某半 挂 牵 引车 车 架 建立 了有 限 元 分析 模 型, 针 并应 用有 限元 分 析软 件 对 各种 工况 下 的车 架 强度 进 行 了有 限元 分析 , 为半挂 牵 引车车 架的 设计 及 改进 提供 了参 考依 据 。 关键 词 : 挂 牵 引车 车 架 强 度 有 限元 半
在 平衡 轴横 梁处 车 架 两侧 铆 接厚 度 为 8 m 的侧 角板 。改 m
进 前原设 计 车 架结 构如 图 1 示 。 所
半挂 牵 引车 车架 是 通 过悬 架 、车 轮 支撑 在 路 面上 , 为 得 到 半 挂 牵 引车 车 架 在 实 际使 用 过 程 中的真 实 应 力 分布
簧 单 元 , 了模 拟 钢 板 弹簧 与车 架 之 间 的装 配关 系, 之 为 使
能 够 相 互 作 用 , 成 一 个 整 体 , 单 元 与 弹 簧单 元 的 连接 形 梁
图 1 原 车架 结 构 示意 图
全 部 用多 点 约束 模 拟 ,为 了消 除车 架 的整 体 刚性 位 移, 还 应 将 前后 钢 板 弹簧 中心 施加 位 移约 束 。 车架 除 承受 载重量 以外 , 为 主要 的联接件 , 作 还承 受驾 驶 室 、 动机 、 发 油箱 、 电瓶箱 等 附件 的重力所带来 的载荷 , 各
状 况 , 须 考 虑悬 挂 系统 的变 形 情 况 , 必 将悬 挂 系 统 与 车架
中型载货汽车车架有限元静力学分析-任务书

毕业设计(论文)任务书学生姓名系部汽车与交通工程学院专业、班级指导教师姓名职称教授从事专业车辆工程是否外聘□是√否题目名称中型载货汽车车架有限元静力学分析一、设计(论文)目的、意义汽车作为交通运输工具之一,在人们的日常生活中发挥着非常重要的作用。
随着国民经济的快速发展,汽车工业也得到了飞速发展,在现代化发展的今天,生产出结构轻、性能好、质量高、用途广、安全可靠的汽车,成为了汽车厂家和客户共同关注的焦点。
作为汽车总成的一部分,车架承受着来自道路及各种复杂载荷的作用,而且汽车上许多重要总成都是以车架为载体,因此设计出重量轻而各方面性能达到要求的车架结构是一项重要的工作。
传统的车架结构设计是采用类比的思想进行经验设计,设计出的车架结构除了个别部位的应力水平较高外,大部分部位的应力水平较低。
因此,有必要采用有限元法对车架结构进行优化设计,以降低车架的重量,减小汽车的制造成本,提高市场竞争力。
二、设计(论文)内容、技术要求(研究方法)设计内容:1.选题的背景、目的及意义;2.Pro/E、ANSYS软件研究;3.车架设计的方法步骤研究;4.用Pro/E软件建立车架整体模型,然后导入ANSYS软件进行网络划分;5.假定汽车满载情况下,对车架进行弯曲、扭转、紧急刹车、急转弯四种工况下的受力和变形情况的静态有限元分析。
技术要求:1.研究中型载货汽车车架;2.有限元模型、载荷建立正确;3.生产纲领:成批生产。
三、设计(论文)完成后应提交的成果中型载货汽车车架有限元静力学分析程序一份;设计说明书(20000字以上)一份。
四、设计(论文)进度安排(1)知识准备、调研、收集资料、完成开题报告第1~2周(2.28~3.11)(2)整理资料、提出问题、撰写设计说明书草稿、熟悉Pro/E、ANSYS软件的使用第3~5周(3.14~4.1)(3)理论联系实际分析问题、解决问题,使用Pro/E、ANSYS软件完成中型载货汽车车架的三维设计、强度分析等部分设计内容,中期检查第6~8周(4.4~4.22)(4)改进完成设计,改进完成设计说明书,指导教师审核,学生修改第9~12周(4.25~5.20) (5)评阅教师评阅、学生修改第13周(5.23~5.27)(6)毕业设计预答辩第14周(5.30~6.3)(7)毕业设计修改第15~16周(6.6~6.17)(8)毕业设计答辩第17周(6.20~6.24)五、主要参考资料1.刘惟信.汽车设计.北京:清华大学出版社2.张洪信.有限元基础理论与ANSYS应用.北京:机械工业出版社,2006.13.段进,倪栋,王国业.ANSYS10.0结构分析从入门到精通.北京:兵器工业出版社,2006.104.姜勇,张波.ANSYS7.0实例精解.北京:清华大学出版社5.汽车车身结构与设计.北京:机械工业出版社6.余传文.重型载货汽车车架结构的有限元仿真及优化.吉林大学硕士学位论文,20057.黄华,茹丽妙.重型运输车车架动力学分析.车辆与动力技术8.刘新田,黄虎,刘长虹等.基于有限元的汽车车架静态分析.上海工程技术大学学报,2007,6:112~1169.中型载货汽车车架设计资料10.网络资源,超星数字图书馆11.近几年相关专业CNKI网络期刊等六、备注指导教师签字:年月日教研室主任签字:年月日。
- 1、下载文档前请自行甄别文档内容的完整性,平台不提供额外的编辑、内容补充、找答案等附加服务。
- 2、"仅部分预览"的文档,不可在线预览部分如存在完整性等问题,可反馈申请退款(可完整预览的文档不适用该条件!)。
- 3、如文档侵犯您的权益,请联系客服反馈,我们会尽快为您处理(人工客服工作时间:9:00-18:30)。
车架的有限元分析及优化
作者:马迅盛…文章来源:湖北汽车工业学院点击数:1687 更新时间:2008-8-5
有限元法将设计人员丰富的实践经验与计算机高速精确的计算完美地结合在一起,大大提高了设计计算精度,缩短了产品开发时间。
概念设计阶段车架的结构方案
参考某一同类型车架,考虑到车身安装和其他总成的布置,将概念设计阶段的车架大致结构拟定如下:选用框架式平行梯形车架结构,由2根左右分开的纵梁和8根横梁组成,全长6.3m,宽0.8m,轴距3.65m。
各梁的大致形状尺寸及板材厚度如表1所示。
除第3、4根横梁外,其他各横梁的尺寸与参考的同类型车架几乎相同。
由于参考车架的第3、4根横梁为上下两片形状复杂的钢板组合而成,无法用梁单元模拟,在概念车架中将之改用两根方型截面的等直梁代替。
第1、6横梁为非等截面梁,其宽和高分别由两个尺寸表示。
参考车架纵梁的前后两段和中间段的连接采用的是线性渐变的截面,在概念车架中用一等直梁来代替,等直梁的高度等于渐变梁的中间高度。
纵横梁上所有的孔及连接板都不予以考虑。
车架的有限元模型
为了后续的优化设计,必须对车架进行参数化建模。
选择表1中车架纵横梁的截面尺寸为模型参数,先建立左半个车架的几何模型,选用ANSYS中的二节点12自由度梁单元BEAM188号单元采用不同的梁单
元截面形式对其进行网格剖分;再将左边的几何模型和网格模型进行映射得到右边车架模型,最终合并对称面上的节点使左右车架模型“牢固的”“粘结起来”。
在ANSYS中用BEAM188单元实施网格剖分时,为了保证单元的正确方向,应事先定义该单元的方向点并检查所要剖分的线的法向。
单元截面形状和偏置量需用命令SECTYPE、SECOFFSET和SECDATA设定。
单元总数为312,节点总数为626。
网格剖分并映射后车架模型如图1所示。
图中显示出了梁单元的截面形状。
图1 车架的有限元模型
边界条件
车架刚度有多种,其中最重要的是车架的弯曲刚度和扭转刚度。
参照车架的刚度试验方法确定车架弯扭刚度的边界条件。
1.弯曲工况的边界条件
计算时约束前后桥在车架纵梁上的竖直投影点的垂直位移,让车架形成一简支梁结构,并在前后支承点中点处加一垂直向下的力,让车架产生纯弯曲变形,如图2所示。
图2 车架弯曲刚度计算车架弯曲刚度计算公式为:
①
其中:CB,弯曲刚度(N m2);
F,集中载荷(N);
A,轴距(m);
f,载荷作用点处的挠度(m)。
图3为车架有限元模型弯曲工况边界条件示意图。
图3 车架垂直弯曲工况的边界条件
2.扭转工况的边界条件
约束前桥在车架左纵梁上的竖直投影点的垂直位移,约束后桥在车架右纵梁上的竖直投影点的垂直位移,在后桥在车架左纵梁上的竖直投影点上施加一垂直向上的载荷,让车架产生纯扭转变形,如图4所示。
车架的扭转刚度计算公式为:
②
其中:CT,扭转刚度(N m/o);
F,载荷(N);
L,力臂(m);
h,挠度(m)
图4 车架扭转刚度计算
图5为车架有限元模型扭转工况边界条件示意图。
图5 前后扭转工况的车架边界条件
求解结果与分析
1.模态的计算结果
用Block Lanczos法提取自由振动时的前5阶固有频率,频率范围0.05~50Hz。
车架的前五阶固有频率及振型见表2。
相应的振型图如图6~11所示。
图6 一阶固有频率对应振型
图7 二阶固有频率对应振型
图8 三阶固有频率对应振型(俯视)
图9 三阶固有频率对应振型(全视图)
图10 四阶固有频率对应振型
图11 五阶固有频率对应振型
2.弯扭刚度计算结果
在F=1 000N时车架弯曲工况载荷作用点处的挠度为0.4595mm;在F=1 000N时车架扭转工况载荷作用点处的挠度为13.94mm。
带入公式①、②中计算得:弯曲刚度为2.2×106N m2,扭转刚度为667.2N m/°。
3.结果分析
该概念车架和其他车架动静刚度的比较如表3所示:
经对比,概念车架的固有频率明显高于其他同类车架。
分析车架振型发现:该车架第二横梁和第三横梁之间是薄弱环节,在第三阶固有频率和第五阶固有频率下都会发生明显的局部振动。
但在整车中该区域会安装发动机和驾驶室,它们对车架刚度都有显著影响,特别是发动机。
当发动机与车架的连接刚度较大且采用四点支撑时,会显著的提高该区域的车架(整体)刚度,尤其是扭转刚度,因而该概念车架的这一不足可以得到部分弥补。
对比参考车架的弯扭刚度,概念车架的值也偏高。
优化设计
取纵、横梁截面的长、宽和高共20个尺寸作为设计变量。
以车架总体积最小为目标函数对该车架进行弯曲、扭转刚度和一阶扭转频率等综合性能方面的优化。
分别选取车架的弯曲、扭转刚度及一阶扭转频率值为状态变量。
优化时,参考同类车架,将概念车架的动静刚度适当的扩大,取弯曲工况下力的作用点最大位移不超过0.6mm,扭转工况的力的作用点最大位移不超过16mm,一阶固有频率的下限取11Hz。
采用ANSYS中的一阶优化方法,对比优化前后的参数变化情况,可以得到以下结论:
1.车架模型经过11次迭代后收敛。
优化后,车架的重量减轻了1
2.5%。
2.车架的弯曲刚度和扭转刚度均有降低,其中,弯曲刚度降低29.2%,扭转刚度降低11.3%;车架的一阶固有频率变化仅为2.67%。
3.对弯曲和扭转刚度影响最大的是纵梁前后段的截面尺寸B1和H11。
其余各梁的截面尺寸也有不同程度的改变。
结语
本文利用工程分析软件ANSYS计算了某一概念设计阶段车架的静态弯曲刚度、扭转刚度以及自由振动时的前五阶固有频率和相应振型,其动静刚度性能指标均超过同类车架。
通过以车架纵、横梁截面尺寸为设计变量进行了优化设计,使该车架减重12.5%。