汽车工艺工艺-冲压件模具结构工艺性分析方法规范模板
冲压件工艺性分析
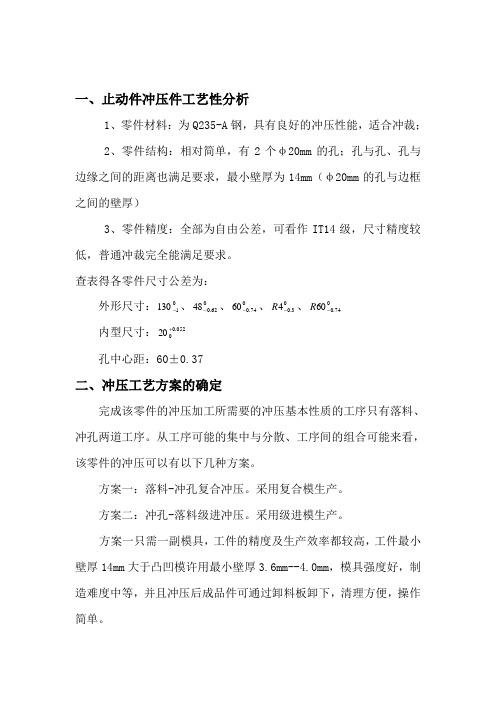
一、止动件冲压件工艺性分析1、零件材料:为Q235-A 钢,具有良好的冲压性能,适合冲裁;2、零件结构:相对简单,有2个φ20mm 的孔;孔与孔、孔与边缘之间的距离也满足要求,最小壁厚为14mm (φ20mm 的孔与边框之间的壁厚)3、零件精度:全部为自由公差,可看作IT14级,尺寸精度较低,普通冲裁完全能满足要求。
查表得各零件尺寸公差为:外形尺寸:01130-、062.048-、074.060-、03.04-R 、074.060-R 内型尺寸:052.0020+孔中心距:60±0.37二、冲压工艺方案的确定完成该零件的冲压加工所需要的冲压基本性质的工序只有落料、冲孔两道工序。
从工序可能的集中与分散、工序间的组合可能来看,该零件的冲压可以有以下几种方案。
方案一:落料-冲孔复合冲压。
采用复合模生产。
方案二:冲孔-落料级进冲压。
采用级进模生产。
方案一只需一副模具,工件的精度及生产效率都较高,工件最小壁厚14mm 大于凸凹模许用最小壁厚3.6mm--4.0mm ,模具强度好,制造难度中等,并且冲压后成品件可通过卸料板卸下,清理方便,操作简单。
方案二也只需一副模具,生产效率高,操作方便,工件精度也能满足要求,但是模具结构复杂,制造加工,模具成本较高。
结论:采用方案一为佳三、模具总体设计(1)模具类型的选择由冲压工艺分析可知,采用复合模冲压,所以模具类型为复合模。
(2)定位方式的选择因为该模具采用的是条料,控制条料的送进方向采用导料板,无侧压装置。
控制条料的送进步距采用挡料销定距。
而第一件的冲压位置因为条料长度有一定余量,可以靠操作工目测来定。
(3)卸料、出件方式的选择因为工件料厚为1.5mm,相对较薄,卸料力也比较小,故可采用弹性卸料。
又因为是倒装式复合模生产,所以采用上出件比较便于操作与提高生产效率。
(4)导向方式的选择为了提高模具寿命和工件质量,方便安装调整,该倒装式模采用导柱导向方式。
冲压件工艺流程范文
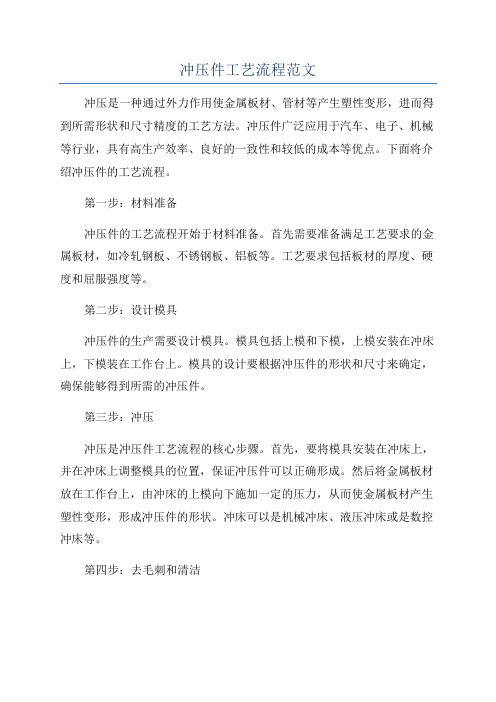
冲压件工艺流程范文冲压是一种通过外力作用使金属板材、管材等产生塑性变形,进而得到所需形状和尺寸精度的工艺方法。
冲压件广泛应用于汽车、电子、机械等行业,具有高生产效率、良好的一致性和较低的成本等优点。
下面将介绍冲压件的工艺流程。
第一步:材料准备冲压件的工艺流程开始于材料准备。
首先需要准备满足工艺要求的金属板材,如冷轧钢板、不锈钢板、铝板等。
工艺要求包括板材的厚度、硬度和屈服强度等。
第二步:设计模具冲压件的生产需要设计模具。
模具包括上模和下模,上模安装在冲床上,下模装在工作台上。
模具的设计要根据冲压件的形状和尺寸来确定,确保能够得到所需的冲压件。
第三步:冲压冲压是冲压件工艺流程的核心步骤。
首先,要将模具安装在冲床上,并在冲床上调整模具的位置,保证冲压件可以正确形成。
然后将金属板材放在工作台上,由冲床的上模向下施加一定的压力,从而使金属板材产生塑性变形,形成冲压件的形状。
冲床可以是机械冲床、液压冲床或是数控冲床等。
第四步:去毛刺和清洁冲压后的冲压件上可能会残留一些毛刺或边角不平整的部分。
为了提高冲压件的质量,需要进行去毛刺和清洁处理。
去毛刺可以使用切割、打磨或喷丸等方法,清洁可以通过化学清洗或机械清洗来完成。
第五步:装配和调试对于一些需要多个冲压件组合成的产品,需要进行装配和调试。
装配可以使用螺栓、焊接或胶接等方法,确保冲压件能够正确连接在一起。
调试包括调整冲压件的位置和调整装配后产品的尺寸精度等。
第六步:表面处理为了提高冲压件的表面质量和使用寿命,可以进行表面处理。
常见的表面处理方法包括电镀、喷涂和阳极氧化等。
表面处理可以提高冲压件的外观、防腐蚀性能和耐磨损能力。
第七步:质量检验冲压件的生产结束后,需要进行质量检验。
质量检验包括外观检查、尺寸测量和功能测试等。
通过质量检验,可以确保冲压件符合设计要求和客户需求。
总结起来,冲压件的工艺流程包括材料准备、设计模具、冲压、去毛刺和清洁、装配和调试、表面处理以及质量检验。
汽车车门制造冲压工艺分析

汽车车门制造冲压工艺分析摘要:在对汽车车门进行制造时,所使用的材料以及制造工艺都会影响车门的强度与钢度。
大部分汽车车门的制造过程是冲压,焊装,涂装最后与车身其他部件总装为一个白车身。
汽车车门的制造工艺是整车工艺的一个缩影,从小见大,了解它也就能帮助我们了解整车制造工艺。
笔者介绍了一种冲压工艺方法在汽车车门内板上的具体应用,降低了拉延模具制造难度,降低了制造成本。
关键词:车门材料;冲压工艺;分析一、制件冲压工艺概述冲压件一般需经过拉延/修边+冲孔/整形(或翻边)+冲孔等工序才能得到合格产品。
对于稍微复杂的钣金件,通过拉延仅能得到冲压件大概轮廓,经过后序的修边冲孔,再配合整形翻边等工序才能得到最终零件。
整形翻边等工艺可以降低拉延深度,简化拉延模面的形状,提高成形性,也就是提高了模具制造的可实现性及易操作性。
以常见的车门外板为例,展示普通冲压外覆盖件的工艺流程。
车门外板采用4步工序实现了零件的制造过程,因车门外板拉延深度较小,型面相对简单,因此采用的是一次拉延成形的方法,配合后面的修边、冲孔、翻边工序而成,这种一次拉延的冲压工艺方案是通过拉延得到基本的零件轮廓,后期的整形、翻边等都是对R角的微小型面进行小范围改变,这种工艺方法在实际生产中广泛应用,但同时也存在如下缺点和不足:(1)一次拉延工序得到几乎整个零件的全部形状特征,后工序主要是修边、冲孔、翻边,以及对局部的(小面积的)难以一次成形的型面做整形,得到零件。
此工艺比较死板,灵活变动的空间较小,限制了工艺设计的多样性。
(2)因为是一次拉延得到了零件的基本形状,所以拉延深度是固定的,零件的造型决定了拉延深度的大小,也就决定了成形的可实现性。
对于拉延深度较大的零件就存在拉延状态不稳定及拉延开裂的风险。
(3)拉延深度较大的零件拉延工序存在拉毛风险,为减少拉毛的概率,对于拉延模质量要求较高,比如硬度、光洁度都要提升一个等级,同时也要加强模具的日常保养维护,增加了制造成本。
(完整版)汽车零部件的工艺分析及模具设计开题报告
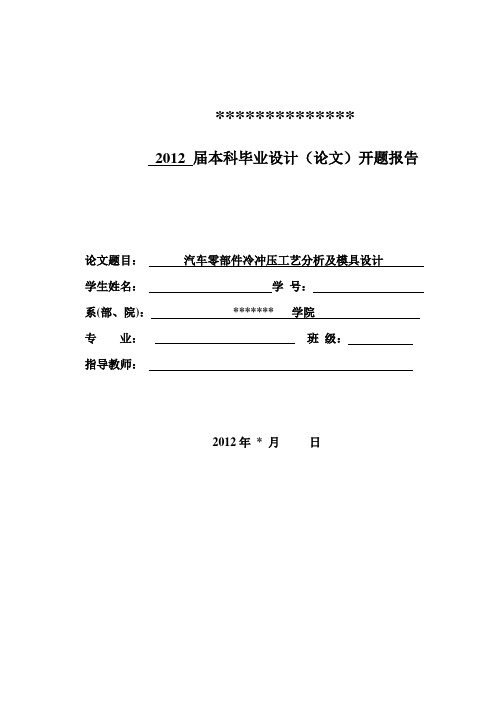
**************
2012 届本科毕业设计(论文)开题报告
论文题目:汽车零部件冷冲压工艺分析及模具设计
学生姓名:学号:
系(部、院):******* 学院
专业:班级:
指导教师:
2012年* 月日
开题报告填写要求
1. 开题报告作为毕业设计(论文)答辩委员会对学生答辩资格审查的依据材料之一。
在指导教师指导下,学生在毕业设计(论文)工作开始前完成,指导教师签署意见、教研室审查后生效;
2. 学生应按照统一要求(从教务处网站下载开题报告标准格式电子文档)填写开题报告,其中:字体小4号宋体,行距20磅,日期的填写一律用阿拉伯数字书写,如“2006年1月17日”或“2006-01-17”;
3. 根据专业的具体情况,学生应查阅一定数量的参考文献(不包括辞典、手册);
4. 完成后及时交给指导教师签署意见。
2012 届本科毕业设计(论文)开题报告。
冲压模具设计说明书
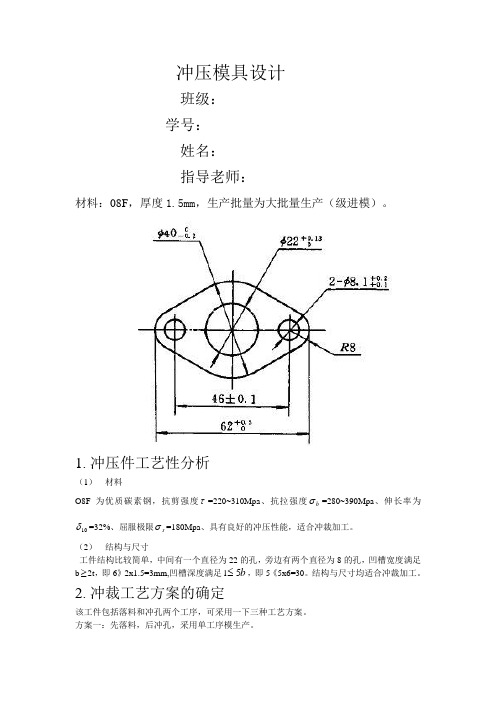
冲压模具设计班级: 学号: 姓名: 指导老师:材料:08F ,厚度1.5mm ,生产批量为大批量生产(级进模)。
1. 冲压件工艺性分析(1) 材料O8F 为优质碳素钢,抗剪强度τ=220~310Mpa 、抗拉强度b σ=280~390Mpa 、伸长率为10δ=32%、屈服极限s σ=180Mpa 、具有良好的冲压性能,适合冲裁加工。
(2) 结构与尺寸工件结构比较简单,中间有一个直径为22的孔,旁边有两个直径为8的孔,凹槽宽度满足b ≥2t ,即6》2x1.5=3mm,凹槽深度满足l b 5≤,即5《5x6=30。
结构与尺寸均适合冲裁加工。
2. 冲裁工艺方案的确定该工件包括落料和冲孔两个工序,可采用一下三种工艺方案。
方案一:先落料,后冲孔,采用单工序模生产。
方案二:落料——冲孔复合冲压,采用复合模生产。
方案三:冲孔——落料级进冲压,采用级进模生产。
综合考虑后,应该选择方案三。
因为方案三只需要一副模具,生产效率高,操作方便,工件精度也能满足要求,所以应该选用方案三比较合算。
3.选择模具总体结构形式由于冲压工艺分析可知,采用级进冲压,所以模具类型为级进模。
(1)确定模架及导向方式采用对角导柱模架,这种模架的导柱在模具对角位置,冲压时可防止由于偏心力矩而引起模具歪斜。
导柱导向可以提高模具寿命和工件质量,方便安装调整。
(2)定位方式的选择该冲件采用的柸料是条料,控制条料的送进方向采用导料板,无侧压装置;控制条料的送进步距采用侧刃粗定距;用导正销精定位保证内外形相对位置的精度。
(3)卸料、出件方式的选择因为该工件料厚1.5mm,尺寸较小,所以卸料力也较小,故选择弹性卸料,下出件方式。
4.必要的工艺计算(1)排样设计与计算该冲件外形大致为圆形,搭边值为a1=1.5mm,条料宽度为43.57mm,步距为A=88.4mm,一个步距的利用率为63.98%。
见下图S=1668.7-11x11x3.14-2x4x4x3.14=1188.28项目分类计算方法和结果排样冲裁件面积面积为1188.28mm条料宽度B=39.97+1.8+1.8=43.57mm 步距A=86.9+1.5=88.4mm材料利用率η冲压力的相关计算F 冲=KLt b τ=1.3*275*1.5*300=160875N F 卸=K 1F=0.04*160875=64350N F 推=nK 2F=4*0.055*160875=35392.5N F= F 冲+ F 卸+ F 推=260617.5N (3)计算模具压力中心代入公式X0=132.25115.69132.25396.14874.61132.2519.44115.6993.26132.250396.148++++++X X X X =19.73Y0=132.25115.69132.25396.14827.13132.250115.69)27.13(132.250396.148+++++-+X X X X =0(4) 计算凸、凹模工作部分尺寸并确定其制造公差 由于凸凹模的形状相对简单且材料较厚,冲裁间隙较大,可采用分开加工法确定凸凹模的刃口尺寸及公差。
冲压件模具工艺性分析毕业论文
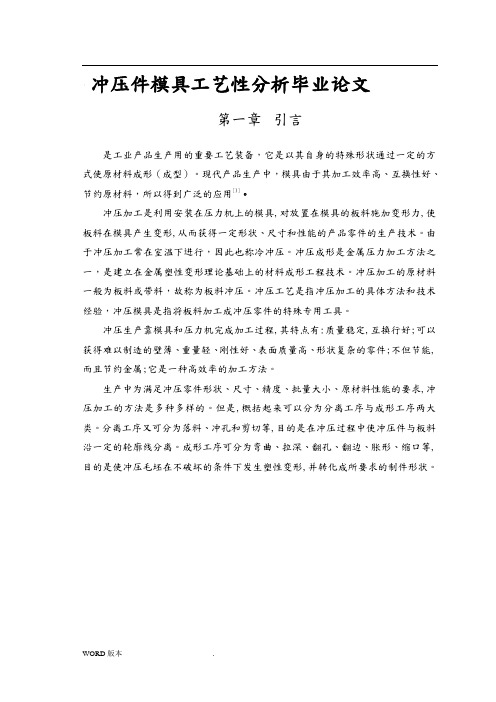
冲压件模具工艺性分析毕业论文第一章引言是工业产品生产用的重要工艺装备,它是以其自身的特殊形状通过一定的方式使原材料成形(成型)。
现代产品生产中,模具由于其加工效率高、互换性好、节约原材料,所以得到广泛的应用[1]。
冲压加工是利用安装在压力机上的模具,对放置在模具的板料施加变形力,使板料在模具产生变形,从而获得一定形状、尺寸和性能的产品零件的生产技术。
由于冲压加工常在室温下进行,因此也称冷冲压。
冲压成形是金属压力加工方法之一,是建立在金属塑性变形理论基础上的材料成形工程技术。
冲压加工的原材料一般为板料或带料,故称为板料冲压。
冲压工艺是指冲压加工的具体方法和技术经验,冲压模具是指将板料加工成冲压零件的特殊专用工具。
冲压生产靠模具和压力机完成加工过程,其特点有:质量稳定,互换行好;可以获得难以制造的壁薄、重量轻、刚性好、表面质量高、形状复杂的零件;不但节能,而且节约金属;它是一种高效率的加工方法。
生产中为满足冲压零件形状、尺寸、精度、批量大小、原材料性能的要求,冲压加工的方法是多种多样的。
但是,概括起来可以分为分离工序与成形工序两大类。
分离工序又可分为落料、冲孔和剪切等,目的是在冲压过程中使冲压件与板料沿一定的轮廓线分离。
成形工序可分为弯曲、拉深、翻孔、翻边、胀形、缩口等,目的是使冲压毛坯在不破坏的条件下发生塑性变形,并转化成所要求的制件形状。
第二章冲压件工艺性分析2.1冲裁件的工艺性分析冲裁件的工艺性是指冲裁件对冲压工艺的适应性。
即冲裁件的结构、形状、尺寸及公差等技术要求是否符合冲裁加工的工艺要求,难易程度如何。
工艺性是否合理,对冲裁件的质量、模具寿命和生产效率有很大影响。
良好的冲裁工艺性能使材料消耗少、工序数量少、模具结构简单且使用寿命长、产品质量稳定。
2.1.1 冲裁件的形状和尺寸(1)冲裁件的形状设计应尽量简单、对称,同时应减少排样废料。
(2)除在少、无废料排样或采用镶拼模结构是,允许工件有尖锐的清角外,冲裁件的外形或孔交角处应采用圆角过渡,避免清角。
汽车钣金冲压工艺图文详解

冲压基础工艺培训
1.冷冲压:是指在常温下,利用安装在压力机上的冲模对材料施加压力, 使其产生分离或塑性变形,从而获得所需要零件的一种压力加工方 法
2.冷冲压的特点: 产品尺寸稳定,精度高,重量轻,刚度好,互换性好,高效低耗,
操作简单,易于实现自动化
冲压设备
冲压零件
模具
工艺条件
冲压零件影响因素
冲压基本工序分类
落料
BL
斜楔翻边/冲 CFL/CPI/CT
孔/修边
R
基本模具结构图 G
P
F
C M
E J
B
B
A
A
N
D
HLeabharlann DHNA
双
B
A
动B M
C
K
F
J
E
L
P G
H
J
K
U V
B
N
修翻
R M
Q
L
T
X
P
L
E
C S
G 边边 W 冲整
孔形
E
F
Y
D
A K
H
L
K
单 动
拉延方向的选择 合理的拉延方向应符合以下原则:
1.保证凸模能将工件需拉深的部位在一次拉深中完成,不应有凸 模接触不到的死区(即“倒勾”形)。 2.拉延开始时,凸模与毛坯的接触状态应良好;接触面积应尽 量大而靠近中心;凸模表面同时接触毛坯的点要多而分散,并 尽可能分布均匀,防止毛坯窜动。 3.尽可能减小拉延深度,并使各部位拉延深度趋于均匀。
压料面
B
A
A
B
A
分模线
分模线
B A
修边线
冲压件工艺分析
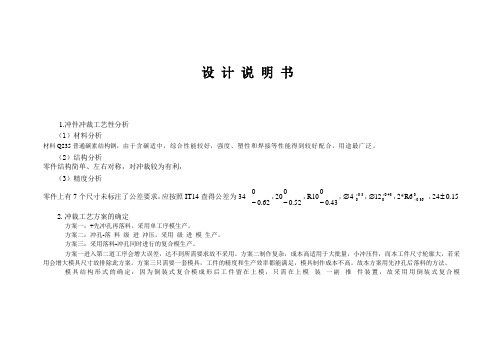
设 计 说 明 书1.冲件冲裁工艺性分析 (1)材料分析材料Q235普通碳素结构钢,由于含碳适中,综合性能较好,强度、塑性和焊接等性能得到较好配合,用途最广泛。
(2)结构分析零件结构简单、左右对称,对冲裁较为有利,(3)精度分析零件上有7个尺寸未标注了公差要求,应按照IT14查得公差为34.00-,2052.00-,R1043.00-,4∅3.00+,43.0012+∅,2*R6036.0- ,2415.0± 2.冲裁工艺方案的确定方案一:+先冲孔再落料。
采用单工序模生产。
方案二:冲孔-落 料 级 进 冲压。
采用 级 进 模 生产。
方案三:采用落料-冲孔同时进行的复合模生产。
方案一进入第二道工序会增大误差,达不到所需要求故不采用。
方案二制作复杂,成本高适用于大批量,小冲压件,而本工件尺寸轮廓大,若采用会增大模具尺寸故排除此方案。
方案三只需要一套模具,工件的精度和生产效率都能满足,模具制作成本不高。
故本方案用先冲孔后落料的方法。
模具结构形式的确定:因为倒装式复合模成形后工件留在上模,只需在上模 装 一副 推 件装置,故采用用倒装式复合模材料Q235 t=2一、 冲裁工艺计算 (一)凸、凹模刃口尺寸计算查表得Z min=0.246,Zmax=0.36, Z max-Z min=0.074.落料件 :3462.00-,2052.00-,R1043.00-. ,R6036.0- ,X=0.5 (3462.00-) : D A =(D max – x △)A0δ+=33.690.030+D T =( D A –Z min) 0T δ-= 33.44400.02- (2052.00-): D A =19.75025.00+ , D T =19.50402.00+(1043.00-):D A =9.68502.00+ , D T =9.439002.0-(R6036.0-) :D A =5.98202.00+ , D T =5.736002.0-冲孔件,4∅3.00+,43.0012+∅,3.0012+∅ : d T =(d min + x △) 0T δ-= 12.21500.02-dA = (d min + x△+ Z min) Aδ+=12.46102.0+4∅43 .0+: dT =4.1500.02-,dA=4.39602.0+孔中心距2415.0±LA=(Lmin+0.5△)±△/8= 25±0.0375排样分析零件形状,应采用单直排的排样方式,零件可能的排样方式有下图所示的两种。
- 1、下载文档前请自行甄别文档内容的完整性,平台不提供额外的编辑、内容补充、找答案等附加服务。
- 2、"仅部分预览"的文档,不可在线预览部分如存在完整性等问题,可反馈申请退款(可完整预览的文档不适用该条件!)。
- 3、如文档侵犯您的权益,请联系客服反馈,我们会尽快为您处理(人工客服工作时间:9:00-18:30)。
XX公司企业规范
编号xxxx-xxxx
汽车工艺设计-
冲压件模具结构工艺性分析方法规范模板XXXX发布
冲压件模具结构工艺性分析方法规范
1 工作目的
冲压件的模具结构工艺性分析主要是指在用冲压的方法完成零件的加工时,在确保零件冲压成形性、稳定性、工序合理的前提下,充分考虑模具结构实现的可能性和难易性,找出零件自身存在的缺陷并提出改进方案。
为了提高冲压件模具结构工艺性分析的工作效率,同时保证在工程化设计阶段尽可能完全消除零件的模具结构工艺性问题,以确保后期模具设计的质量和周期进度,特编写此分析方法,为以后此项分析提供方法指导和操作规范。
2 工作内容
a)找出零件导致模具工序增加的部位,提出改进方案;
b)找出零件导致模具结构难度大的部位,提出改进方案;
c)找出各工序零件存在冲压负角的部位,提出改进方案;
d)找出零件修边条件不良的部位,提出改进方案;
e)找出零件冲孔条件不良的部位,提出改进方案;
f)找出零件造成模具废料排出不顺畅的部位,提出改进方案;
g)找出零件造成模具强度有问题的部位,提出改进方案;
h)找出零件造成模具结构布置有问题的部位,提出改进方案。
3 工作输入
a)白车身材料清单;
b)产品数模。
4 工作输出
产品冲压问题报告。
5 工作步骤
第一步:获得白车身材料清单和产品数模后,熟悉冲压零件的几何形状、材料性能及装配关系;
第二步:根据冲压零件的几何形状、材料性能及装配关系,结合生产纲领及冲压设备能力,初步制定冲压工序的性质、数目、顺序及内容;把握好制定冲压工序原则:在保证冲压件质量的前提下,工序尽量少、排废料要通畅、模具强度要好;
第三步:设定各工序的冲压方向和送料方向;把握好设定冲压方向原则:有利于拉延成形,保证后工序好修、好翻边、好定位;
第四步:根据冲压工序内容,对产品的模具结构工艺性进行分析,分析零件是否存在导致模具结构无法实现或者难以实现的设计缺陷;比如:导致模具工序增加、结构复杂,存在冲压负角、修边冲孔条件差,造成模具废料排出不畅、强度差、结构无法布置等;
第五步:根据模具结构工艺性分析的结果,提出改进方案并制定产品冲压问题报告,申请更改产品;
第六步:跟踪设计部门对产品冲压问题报告的采纳情况,通过和设计人员的交流,尽可能在设计阶段消除所有发现的设计缺陷,然后跟踪产品冲压问题报告的闭环情况。
6 分析方向、方法(结合实例)
6.1 冲压负角
由于车身设计人员设计产品时并不十分地了解零件的冲压工序及冲压方向,而制定冲压工艺时经常需要对零件进行适当的旋转,可能导致零件的局部区域出现负角,工艺和模具无法实现。
以下为几种常见冲压负角的实例:
a) 翻边负角
在翻边工序的冲压方向下,产品的翻边面存在负角,翻边后零件会卡在模具上无法取出。
图1为翻边负角的实例,图2为翻边负角区域断面图。
图1 翻边负角的实例 图2 负角区域断面图
解决翻边负角方法主要是:在翻边序的冲压方向下,将零件局部型一定角度的旋转处理,直到零件能够满足翻边的要求为止(消除负角且有回弹余量)。
b) 拉延负角
产品在拉延工序的冲压方向下出现负角区域,负角区域零件是无法成形的,且在模具结构上也无法实现。
如图3所示,零件侧壁局部区域出现拉延负角,在不影响零件的使用情况下,对零件的局部型面进行了修改,最终将负角消除。
图3 拉延负角问题的改进
6.2 修边条件不良
对于零件边界的确定,车身设计者更多考虑的是边界的光顺性,但在有些情况下这样的边界反而会导致修边时模具的刃口弱甚至无法修边。
此类解决缺陷的方法是:对产品边界的形状进行适当的处理,使零件最终满足修边要求。
以下为几种常见修边条件差的实例:
a) 修边尖角
零件修边时存在尖角,需要增加工艺圆角过渡(如图4所示)。
工艺圆角尽量取R3以上,以保证模具刃口的加工和强度。
图4 修边尖角问题的改进
增加圆角过渡 修改形状,使弯曲前轮廓为直线
b)斜面上修边
斜面上修边有三种情况:与斜面的倾斜线平行的修边(纵切)、与斜面的倾斜线垂直的修边、在斜面上斜向修边。
为保证修边良好,要分别满足各条件(参照冲压设计标准)。
如图5所示,零件局部在斜面上斜向修边,不满足修边条件,需要更改产品轮廓。
图5 斜面上修边问题的改进
c)边到圆角距离过小
产品边界到圆角距离原则上5mm以上,确保模具的强度和产品的修边质量。
如图6所示,修边到圆角距离过小,需要更改产品轮廓。
图6 边到圆角距离过小问题的改进
d)修边困难
如图7所示,不合理的产品边界会导致修边困难,模具结构无法实现。
改进措施:修改产品轮廓保证修边的可行性,同时兼顾产品的功能和装配关系。
图7 修边困难问题的改进
e)侧修能否改为正修
侧修需要安装斜楔机构,导致模具结构复杂、模具尺寸变大、加工调试难度变大,所以尽量考虑侧修改为正修的可能性。
如图8所示,调整产品轮廓,使其满足正修条件。
6.3 冲孔条件不良
图8 侧修改为正修
a)不满足冲孔面角度要求
标准孔按孔径的大小对冲孔面角度有不同要求,大的异型孔可参照修边条件。
如图9所示,修改冲孔面的角度或者移动孔的位置,直至满足冲孔条件。
图9 不满足冲孔角度问题的改进
b)冲孔到修边线距离过小
冲孔和修边在同一工序完成时,孔边界到修边轮廓距离原则上5mm以上,确保模具的强度和产品的质量。
如图10所示,孔边界到修边轮廓距离过小,加大修边轮廓或者移动孔位置,直至满足冲孔条件。
图10 冲孔距离修边太近问题的改进
c)冲孔到侧壁距离过小
如图11所示,孔边界距离侧壁太近,导致凹模强度差。
改进措施:保证孔边界距离侧壁圆角5mm 以上,保证凹模强度。
图11 冲孔到侧壁距离过小的改进
d)冲头与零件干涉
如图12所示,侧冲孔时冲头与零件干涉。
改进措施:移动孔的位置,确保冲头与零件不相碰。
图12 冲头与零件干涉问题的改进
6.4 工艺缺口设计不合理导致废料的排出不畅
在产品设计过程中,根据自身功能的要求及车身轻量化设计的需要,经常在零件的某些区域增加工艺缺口。
如果工艺缺口的形状、位置设计不合理,容易导致零件修边时排料困难,甚至出现卡料的现象。
解决这类缺陷方法通常是:去除工艺缺口或者适当修改工艺缺口的形状。
如图13所示,将工艺缺口改为敞开口样式,保证废料的排除顺畅。
图13 排料困难问题的改进
6.5 模具结构布置问题
因工序数目及内容的限制,有些机构在模具上没有足够的空间布置,需要更改产品或增加工序数目。
如图14所示,相邻斜楔机构干涉,建议移动侧冲孔位置或取消侧冲孔。
图14 相邻斜楔机构干涉问题的改进
6.6 导致模具工序增加
因产品局部结构导致模具工序增加,考虑能否通过修改产品减少工序数量。
如图15所示,取消局部向上翻边,可节省一工序。
图15 导致工序增加问题的改进
7 工作要求
a)把握分析方向,逐一分析判断,防止分析漏项;
b)熟悉产品在整车中的功能和尺寸要求,提高设计变更要求的采纳率;
c)熟悉各种类型模具的结构,掌握模具设计标准。