变速器外文资料翻译
自动变速器的工作原理外文翻译、中英文翻译、外文文献翻译

How Automatic Transmissions Workby Karim NiceIntroduction to How Automatic Transmissions WorkIf you have ever driven a car with an automatic transmission, then you know that there are two big differences between an automatic transmission and a manual transmission:There is no clutch pedal in an automatic transmission car.There is no gear shift in an automatic transmission car. Once you put the transmission into drive, everything else is automatic.Both the automatic transmission (plus its torque converter) and a manual transmission (with its clutch) accomplish exactly the same thing, but they do it in totally different ways. It turns out that the way an automatic transmission does it is absolutely amazing!Automatic Transmission Image GalleryIn this article, we'll work our way through an automatic transmission. We'll start with the key to the whole system: planetary gearsets. Then we'll see how the transmission is put together, learn how the controls work and discuss some of the intricacies involved in controlling a transmission.Just like that of a manual transmission, the automatic transmission's primary job is to allow the engine to operate in its narrow range of speeds while providing a wide range of output speeds.Photo courtesy DaimlerChryslerMercedes-Benz CLK, automatic transmission, cut-away modelWithout a transmission, cars would be limited to one gear ratio, and that ratio would have to be selected to allow the car to travel at the desired top speed. If you wanted a top speed of 80 mph, then the gear ratio would be similar to third gear in most manual transmission cars.You've probably never tried driving a manual transmission car using only third gear. If you did, you'd quickly find out that you had almost no acceleration when starting out, and at high speeds, the engine would be screaming along near the red-line. A car like this would wear out very quickly and would be nearly undriveable.So the transmission uses gears to make more effective use of the engine's torque, and to keep the engine operating at an appropriate speed.The key difference between a manual and an automatic transmission is that the manual transmission locks and unlocks different sets of gears to the output shaft to achieve the various gear ratios, while in an automatic transmission, the same set of gears produces all of the different gear ratios. The planetary gearset is the device that makes this possible in an automatic transmission.Let's take a look at how the planetary gearset works.Planetary Gearsets & Gear RatiosWhen you take apart and look inside an automatic transmission, you find a huge∙An ingenious planetary gearset∙ A set of bands to lock parts of a gearset∙ A set of three wet-plate clutches to lock otherparts of the gearset∙An incredibly odd hydraulic system that controlsthe clutches and bands∙ A large gear pump to move transmission fluidaroundThe center of attention is the planetary gearset. About the size of a cantaloupe, this one part creates all of the different gear ratios that the transmission can produce. Everything else in the transmission is there to help the planetary gearset do its thing. This amazing piece of gearing has appeared on HowStuffWorks before. You may recognize it from the electric screwdriver article. An automatic transmission contains two complete planetary gearsets folded together into one component. See How Gear Ratios Work for an introduction to planetary gearsets.From left to right: the ring gear, planet carrier, and two sun gearsAny planetary gearset has three main components:∙The sun gear∙The planet gears and the planet gears' carrier∙The ring gearEach of these three components can be the input, the output or can be held stationary. Choosing which piece plays which role determines the gear ratio for the gearset. Let's take a look at a single planetary gearset.One of the planetary gearsets from our transmission has a ring gear with 72 teeth and a sun gear with 30 teeth. We can get lots of different gear ratios out of this gearset.Also, locking any two of the three components together will lock up the whole device at a 1:1 gear reduction. Notice that the first gear ratio listed above is a reduction -- the output speed is slower than the input speed. The second is an overdrive -- the output speed is faster than the input speed. The last is a reduction again, but the output direction is reversed. There are several other ratios that can be gotten out of this planetary gear set, but these are the ones that are relevant to our automatic transmission. You can try these out in the animation below:So this one set of gears can produce all of these different gear ratios without having to engage or disengage any other gears. With two of these gearsets in a row, we can get the four forward gears and one reverse gear our transmission needs. We'll put the two sets of gears together in the next section.Compound Planetary GearsetThis automatic transmission uses a set of gears, called a compound planetary gearset, that looks like a single planetary gearset but actually behaves like two planetary gearsets combined. It has one ring gear that is always the output of the transmission, but it has two sun gears and two sets of planets.Let's look at some of the parts:How the gears in the transmission are put togetherLeft to right: the ring gear, planet carrier, and two sun gearsThe figure below shows the planets in the planet carrier. Notice how the planet on the right sits lower than the planet on the left. The planet on the right does not engage the ring gear -- it engages the other planet. Only the planet on the left engages the ring gear.Planet carrier: Note the two sets of planets.Next you can see the inside of the planet carrier. The shorter gears are engaged only by the smaller sun gear. The longer planets are engaged by the bigger sun gear and by the smaller planets.Inside the planet carrier: Note the two sets of planets.Automatic Transmission GearsFirst GearIn first gear, the smaller sun gear is driven clockwise by the turbine in the torque converter. The planet carrier tries to spin counterclockwise, but is held still by the one-way clutch (which only allows rotation in the clockwise direction) and the ring gear turns the output. The small gear has 30 teeth and the ring gear has 72, so the gear ratio is:Ratio = -R/S = - 72/30 = -2.4:1So the rotation is negative 2.4:1, which means that the output direction would be opposite the input direction. But the output direction is really the same as the input direction -- this is where the trick with the two sets of planets comes in. The first set of planets engages the second set, and the second set turns the ring gear; this combination reverses the direction. You can see that this would also cause the bigger sun gear to spin; but because that clutch is released, the bigger sun gear is free to spin in the opposite direction of the turbine (counterclockwise).Second GearT his transmission does something really neat in order to get the ratio needed for second gear. It acts like two planetary gearsets connected to each other with a common planet carrier.The first stage of the planet carrier actually uses the larger sun gear as the ring gear. So the first stage consists of the sun (the smaller sun gear), the planet carrier, and the ring (the larger sun gear).The input is the small sun gear; the ring gear (large sun gear) is held stationary by the band, and the output is the planet carrier. For this stage, with the sun as input, planet carrier as output, and the ring gear fixed, the formula is:1 + R/S = 1 + 36/30 = 2.2:1The planet carrier turns 2.2 times for each rotation of the small sun gear. At the second stage, the planet carrier acts as the input for the second planetary gear set, the larger sun gear (which is held stationary) acts as the sun, and the ring gear acts as the output, so the gear ratio is:1 / (1 + S/R) = 1 / (1 + 36/72) = 0.67:1To get the overall reduction for second gear, we multiply the first stage by the second, 2.2 x 0.67, to get a 1.47:1 reduction. This may sound wacky, but it works.Third GearMost automatic transmissions have a 1:1 ratio in third gear. You'll remember from the previous section that all we have to do to get a 1:1 output is lock together any two of the three parts of the planetary gear. With the arrangement in this gearset it is even easier -- all we have to do is engage the clutches that lock each of the sun gears to the turbine.If both sun gears turn in the same direction, the planet gears lockup because they can only spin in opposite directions. This locks the ring gear to the planets and causes everything to spin as a unit, producing a 1:1 ratio.OverdriveBy definition, an overdrive has a faster output speed than input speed. It's a speed increase -- the opposite of a reduction. In this transmission, engaging the overdrive accomplishes two things at once. If you read How Torque Converters Work, you learned about lockup torque converters. In order to improve efficiency, some cars have a mechanism that locksup the torque converter so that the output of the engine goes straight to the transmission.In this transmission, when overdrive is engaged, a shaft that is attached to the housing of the torque converter (which is bolted to the flywheel of the engine) is connected by clutch to the planet carrier. The small sun gear freewheels, and the larger sun gear is held by the overdrive band. Nothing is connected to the turbine; the only input comes from the converter housing. Let's go back to our chart again, this time with the planet carrier for input, the sun gear fixed and the ring gear for output.Ratio = 1 / (1 + S/R) = 1 / ( 1 + 36/72) = 0.67:1So the output spins once for every two-thirds of a rotation of the engine. If the engine is turning at 2000 rotations per minute (RPM), the output speed is 3000 RPM. This allows cars to drive at freeway speed while the engine speed stays nice and slow.ReverseReverse is very similar to first gear, except that instead of the small sun gear being driven by the torque converter turbine, the bigger sun gear is driven, and the small one freewheels in the opposite direction. The planet carrier is held by the reverse band to the housing. So, according to our equations from the last page, we have:Ratio = -R/S = 72/36 = 2.0:1So the ratio in reverse is a little less than first gear in this transmission.Gear RatiosThis transmission has four forward gears and one reverse gear. Let's summarize the gear ratios, inputs and outputs:After reading these sections, you are probably wondering how the different inputs get connected and disconnected. This is done by a series of clutches and bands inside the transmission. In the next section, we'll see how these work.Clutches and Bands in an Automatic TransmissionIn the last section, we discussed how each of the gear ratios is created by the transmission. For instance, when we discussed overdrive, we said:In this transmission, when overdrive is engaged, a shaft that is attached to the housing of the torque converter (which is bolted to the flywheel of the engine) is connected by clutch to the planet carrier. The small sun gear freewheels, and the larger sun gear is held by the overdrive band. Nothing is connected to the turbine; the only input comes from the converter housing.To get the transmission into overdrive, lots of things have to be connected and disconnected by clutches and bands. The planet carrier gets connected to the torque converter housing by a clutch. The small sun gets disconnected from the turbine by a clutch so that it can freewheel. The big sun gear is held to the housing by a band so that it could not rotate. Each gear shift triggers a series of events like these, with different clutches and bands engaging and disengaging. Let's take a look at a band.BandsIn this transmission there are two bands. The bands in a transmission are, literally, steel bands that wrap around sections of the gear train and connect to the housing. They are actuated by hydraulic cylinders inside the case of the transmission.One of the bandsIn the figure above, you can see one of the bands in the housing of the transmission. The gear train is removed. The metal rod is connected to the piston, which actuates the band.The pistons that actuate the bands are visible here.Above you can see the two pistons that actuate the bands. Hydraulic pressure, routed into the cylinder by a set of valves, causes the pistons to push on the bands, locking that part of the gear train to the housing.The clutches in the transmission are a little more complex. In this transmission there are four clutches. Each clutch is actuated by pressurized hydraulic fluid that enters a piston inside the clutch. Springs make sure that the clutch releases when the pressure is reduced.Below you can see the piston and the clutch drum. Notice the rubber seal on the piston -- this is one of the components that is replaced when your transmission gets rebuilt.One of the clutches in a transmissionThe next figure shows the alternating layers of clutch friction material and steel plates. The friction material is splined on the inside, where it locks to one of the gears. The steel plate is splined on the outside, where it locks to the clutch housing. These clutch plates are also replaced when the transmission is rebuilt.The clutch platesThe pressure for the clutches is fed through passageways in the shafts. The hydraulic system controls which clutches and bands are energized at any given moment.FROM: /automatic-transmission.htm自动变速器的工作原理耐斯·卡瑞姆介绍自动变速器的工作原理如果你驾驶过带有自动变速器的汽车,那么你一定知道手动变速器与自动变速器之间存在两个很大的区别:·自动变速器中没有离合器踏板·自动变速器中没有换档手柄,一旦让变速器传递动力,那么接下来的一切都是自动完成的了。
变速器介绍外文文献翻译、中英文翻译、外文翻译

附录附录A 英文文献Transmission descriptionTransmission gearbox's function the engine's output rotational speed is high, the maximum work rate and the maximum torque appears in certain rotational speed area. In order to display engine's optimum performance, must have a set of variable speed gear, is coordinated the engine the rotational speed and wheel's actual moving velocity. The transmission gearbox may in the automobile travel process, has the different gear ratio between the engine and the wheel, through shifts gears may cause the engine work under its best power performance condition. Transmission gearbox's trend of development is more and more complex, the automaticity is also getting higher and higher, the automatic transmission will be future mainstream.Automotive Transmission's mission is to transfer power, and in the process of dynamic change in the transmission gear ratio in order to adjust or change the characteristics of the engine, at the same time through the transmission to adapt to different driving requirements. This shows that the transmission lines in the automotive transmission plays a crucial role. With the rapid development of science and technology, people's car is getting higher and higher performance requirements, vehicle performance, life, energy consumption, such as vibration and noise transmission depends largely on the performance, it is necessary to attach importance to the study of transmission.Transmission gearbox's pattern the automobile automatic transmission common to have three patterns: Respectively is hydraulic automatic transmission gearbox (AT), machinery stepless automatic transmission (CVT), electrically controlled machinery automatic transmission (AMT). At present what applies is most widespread is, AT becomes automatic transmission's pronoun nearly.AT is by the fluid strength torque converter, the planet gear and the hydraulic control system is composed, combines the way through the fluid strength transmission and the gear to realize the speed change bending moment. And the fluid strength torque converter is the most important part, it by components and so on pump pulley, turbine wheel and guide pulley is composed, has at the same time the transmission torque and the meeting and parting function.And AT compare, CVT has omitted complex and the unwieldy gear combination variable transmission, but is two groups of band pulleys carries on the variable transmission. Through changes the driving gear and the driven wheel transmission belt's contact radius carries on the speed change. Because has cancelled the gear drive, therefore its velocity ratio may change at will, the speed change is smoother, has not shifted gears kicks the feeling.AMT and the hydraulic automatic transmission gearbox (AT) is the having steps automatic transmission equally. It in the ordinary manual transmission gearbox's foundation, through installs the electrically operated installment which the microcomputer controls, the substitution originally coupling's separation which, the joint and the transmission gearbox completes by the manual control elects to keep off, to shift gears the movement, realizes fluid drive.Manual transmission gear mainly uses the principle of deceleration. Transmission within the group have different transmission ratio gear pair, and the car at the time of shift work, that is, through the manipulation of institutions so that the different transmission gear pair work. Manual transmission, also known as manual gear transmission, with axial sliding in the gears, the meshing gears through different speed to achieve the purpose of torque variation. Manual shift transmission can operate in full compliance with the will of the driver, and the simple structure, the failure rate is relatively low, value for money.Automatic transmission is based on speed and load (throttle pedal travel) fortwo-parameter control gear in accordance with the above two parameters to automatically take-off and landing. Automatic transmission and manual transmission in common, that is, there are two-stage transmission, automatic transmission can only speed the pace to automatically shift, manual transmission can be eliminated, "setback" of the shift feel.Automatic transmission is a torque converter, planetary gears and hydraulic manipulation of bodies, through the hydraulic transmission and gear combination to achieve the purpose of variable-speed torque variation.Also known as CVT-type continuously variable CVT. This transmission and automatic transmission gear generally the biggest difference is that it eliminates the need of complex and cumbersome combination of variable-speed gear transmission, and only two groups to carry out variable-speed drive pulley.CVT transmission than the traditional structure of simple, smaller and it is not the number of manual gear transmission, no automatic transmission planetary gear complex group, mainly rely on the driving wheel, the driven wheel and the transmission ratio brought about by the realization of non-class change.Widely used in automotive internal combustion engine as a power source, the torque and speed range is very small, and complex conditions require the use of motor vehicles and the speed of the driving force in the considerable changes in the scope. To resolve this contradiction, in the transmission system to set up the transmission to change transmission ratio, the expansion of the driving wheel torque and speed range in order to adapt to constantly changing traffic conditions, such as start, acceleration, climbing and so on, while the engine in the most favorable conditions to work under the scope; in the same direction of rotation of the engine under the premise of the automobile can be driven back; the use of neutral, interruption of power transmission, in order to be able to start the engine, idle speed, and ease of transmission or power shift . Transmission is designed to meet the above requirements, so that the conditions in a particular vehicle stability.In addition to transmission can be used to meet certain requirements, but also to ensure that it and the car can have a good match, and can improve the car's power andeconomy to ensure that the engine in a favorable condition to increase the scope of the work of the use of motor vehicles life, reduce energy consumption, reduce noise, such as the use of motor vehicles.Today the world's major car companies CVT are very active in the study. The near future, with electronic control technology to further improve, electronically controlled Continuously Variable Transmission-type is expected to be a wide range of development and application.附录B 文献翻译变速器介绍发动机的输出转速非常高,最大功率及最大扭矩在一定的转速区出现。
变速器外文资料翻译
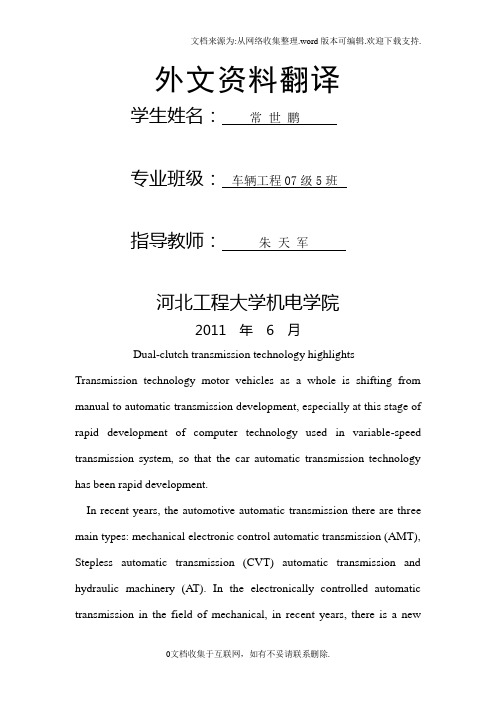
自动变速器英文文献翻译

毕业设计外文翻译THE RESEARCHS OFAMT SHIFTING SCHEDULESThe modern automatic transmission is by far,the most complicated mechanical component in today`s automobile. It is a type of transmission that sifts itself.A fluid coupling or torque converter is used instead of a manually operated clutch to connect the transmission to the engine.There are two basic types of automatic transmission based on whether the vehicle is rear wheel drive or front wheel drive. On a rear wheel drive car,the transmission is usually mounted to the back of the engine and is located under the hump in the center of the floorboard alongside the gas pedal position. A drive shaft connects the transmission to the final drive which is located in the rear axle and is used to send power to the rear wheels. Power flow on this system is simple and straight forward going from the engine,through the torque converter,then trough the transmission and drive shaft until it reaches the final drive where it is split and sent to the two rear transmission.On a front wheel drive car,the transmission is usually combined with the final drive to form what is called a transaxle. The engine on a front wheel drive car is usually mounted sideways in the car with the transaxle tucked under it on the side of the engine facing the rear of the car. Front axles are connected directly to the transaxle and provide power to front wheels. In this example,power floes from the engine,through the torque converter to a larger chain that sends the power through a 180 degree turn to the transmission that is along side the engine. From there,the power is routed through the transmission to the final drive where it is split and sent to the two front wheels throughthe drive axles.There are a number of other arrangements including front drive vehicles where the engine is mounted front to back instead of sideways and there are other systems that drive all four wheels but the two systems described here are by far the most popular. A much less popular rear and is connected by a drive shaft to the torque converter which is still mounted on the engine. This system is found on the new Corvette and is used in order to balance the weight evenly between the front and rear wheels for improved performance and handling. Another rear drive system mounts everything,the engine,transmission and final drive in the rear. This rear engine arrangement is popular on the Porsche;The modern automatic transmission consists of many components and systems that designed to work together in a symphony of planetary gear sets,the hydraulic system, seals and gaskets,the torque converter,the governor and the modulator or throttle cable and computer controls that has evolved over the years into what many mechanical inclined individuals consider to be an art from. Here try to used simple,generic explanation where possible to describe these systems.1Planetary gear setsAutomatic transmission contain many gears in various combinations. In a manual transmission,gears slide along shafts as you move the shift lever from one position to another,engaging various sizes gears as required in order to provide the correct gear ratio. In an automatic transmission,how ever,the gears are never physically moved and are always engaged to the same gears. This is accomplished through the use of planetary gear sets.The basic planetary gear set consists of a sun gear,a ring and two or more planet gears,all remaining in constant mesh. The planet gears are connected to each other through a common carrier which allows the gears to spin on shafts called “pinions” which are attached to the carrier.One example of a way that this system can be used is by connecting the ring gear to the input shaft coming from the engine,connecting the planet carrier to the output shaft,and locking the sun gear so that it can`t move. In this scenario,when we turn the ring gear,the planets will “walk” along the sun gearwhich is held stationary causing the planet carrier to turn the output shaftin the same direction as the input shaft but at a slower speed causing gearreduction similar to a car in first gear .If we unlock the sun gear and lock any two elements together,this will causeall three elements to turn at the same speed so that to output shaft will turnat the same rate of speed as the input shaft. This is like a car that is thirdor high gear. Another way we can use a planetary gear set is by locking the planetcarrier from moving,then applying power to the ring gear which will cause thesun gear to turn in opposite direction giving us reverse gear.The illustration in Figure shows how the simple system described above wouldlook in an actual transmission. The input shaft is connected to the ring gear,theoutput shaft is connected to the planet carrier which is also connected to a“Multi-disk” clutch pack. The sun gear is connected to drum which is also connected to the other half of the clutch pack. Surrounding the outside of thedrum is a band that can be tightened around the drum when required to preventthe drum with the attached sun gear from turning.The clutch pack is used,in this instance,to lock the planet carrier with thesun gear forcing both to turn at the same speed. If both the clutch pack andthe band were released,the system would be in neutral. Turning the input shaftwould turn the planet gears against the sun gear,but since noting is holdingthe sun gear,it will just spin free and have no effect on the output shaft. Toplace the unit in first gear,the band is applied to hold the sun gear from moving.To shift from first to high gear,the band is released and the clutch is appliedcausing the output shaft to turn at the same speed as the input shaft.Many more combinations are possible using two or more planetary sets connected in various way to provide the different forward speeds and reversethat are found in modern automatic transmission.2Clutch packA clutch pack consists of alternating disks that fit inside a clutch drum.Half of the disks are steel and have splines that fit into groves on the insideof the drum. The other half have a friction material bonded to their surfaceand have splines on the inside edge that fit groves on the outer surface of the adjoining hub. There is a piston inside the drum that is activated by oil pressure at the appropriate time to squeeze the clutch pack together so that the two components become locked and turn as one.3One-way ClutchA one-way clutch also known as a “sprag” clutch is a device that will allow a component such as ring gear to turn freely in one direction but not in the other. This effect is just like that bicycle,where the pedals will turn the wheel when pedaling forward,but will spin free when pedaling backward.A common place where a one-way clutch is used is in first gear when the shifter is in the drive position. When you begin to accelerate from a stop,the transmission starts out in first gear. But have you ever noticed what happens if you release the gas while it is still in first gearThe vehicle continues to coast as if you were in neutral. Now,shift into Low gear instead of Drive. When you let go of the gas in this case,you will feel the engine slow you down just like a standard shift car. The reason for this is that in Drive,one-way clutch is used whereas in Low,a clutch pack or a band is used.4Torque ConverterOn automatic transmission,the torque converter takes the place of the clutch found on standard shift vehicles. It is there to allow the engine to continue running when the vehicle comes to a stop. The principle behind a torque converter is like taking a fan that is plugged into the wall and blowing air into another fan which is unplugged. If you grab the blade on the unplugged fan,you are able to hold it from turning but as soon as you let go,it will begin to speed up until it comes close to speed of the powered fan. The difference with a torque converter is that instead of using air it used oil or transmission fluid,to be more precise.A torque converter is a lager doughnut shaped device that is mounted between the engine and the transmission. It consists of three internal elements that work together to transmit power to the transmission. The three elements of the torque converter are the pump,the Turbine,and the Stator. The pump is mounteddirectly to the torque housing which in turn is bolted directly to the engine’s crankshaft and turns at engine speed. The turbine is inside the housing and is connected directly to the input shaft of the transmission providing power to move the vehicle. The stator is mounted to a one-way clutch so that it can spin freely in one direction but not in the other. Each of the three elements has fins mounted in them to precisely direct the flow of oil through the converter.With the engine running,transmission fluid is pulled into the pump section and is pushed outward by centrifugal force until it reaches the turbine section which stars it running. The fluid continues in a circular motion back towards the center of the turbine where it enters the stator. If the turbine is moving considerably slower than the pump,the fluid will make contact with the front of the stator fins which push the stator into the one way clutch and prevent it from turning. With the stator stopped,the fluid is directed by the stator fins to re-enter the pump at a “help” angle providing a torque increase. As the speed of the turbine catches up with the pump,the fluid starts hitting the stator blades on the back-side causing the stator to turn in the same direction as the pump and turbine. As the speed increase,all three elements begin to turn at approximately the same speed. Sine the ‘80s,in order to improve fuel economy,torque converters have been equipped with a lockup clutch which locks the turbine to the pump as the vehicle reaches approximately 40-50 mph. This lockup is controlled by computer and usually won’t engage unless the transmission is in 3rd or 4th gear.5Hydraulic SystemThe hydraulic system is a complex maze of passage and tubes that sends that sends transmission fluid and under pressure to all parts of the transmission and torque converter and. Transmission fluid serves a number of purpose including : shift control ,general lubrication and transmission cooling;Unlike the engine ,which uses oil primary for lubrication ,every aspect of a transmission ‘s function is dependant on a constant supply of fluid is send pressure. In order to keep the transmission at normal operating temperature,aportion of the fluid is send to through one of two steel tubes to a special chamber that is submerged in anti-freeze in the radiator. Fluid passing through this chamber is cooled and then returned to the transmission through the other steel tube. A typical transmission has an avenge of ten quarts of fluid between the transmission,torque converter,and cooler tank,In fact,most of the components of a transmission are constantly submerged in fluid including the clutch packs and bands. The friction surfaces on these parts are designed to operate properly only when they are submerged in oil.6Oil PumpThe transmission oil pump not to confused with the pump element inside the torque converter is responsible for producing all the oil pressure that is required in the transmission. The oil pump is mounted to front of the transmission case and is directly connected to a flange on the engine crankshaft,the pump will produce pressure whenever the engine is running as there is a sufficient amount of transmission fluid available. The oil enters the pump through a filter that is located at bottom of the transmission oil pan and travels up a pickup tube directly to the oil pump. The oil is then sent,under pressure to the pressure regulator,the valve body and the rest of the components,as required.7Valve BodyThe valve body is the control center of the automatic transmission. It contains a maze of channels and passages that direct hydraulic fluid to the numerous valves which when activate the appropriate clutch pack of band servo to smoothly shift to the appropriate gear for each driving situation. Each of the many valves in the valve body has a specific purpose and is named for that function. For example the 2-3 shift valve activates the 2nd gear up-shift or the 3-2 shift timing valve which determines when a downshift should occur.The most important valve and the one that you have direct control over is the manual valve. The manual valve is directly connected to the gear shift handle and covers and uncovers various passages depending on what position the gear shift is paced in. When you place the gear shift in Drive,for instance,the manual valve directs fluid to the clutch pack s that activates 1st gear. Italso sets up to monitor vehicle speed and throttle position so that it can determine the optimal time and the force for the 1-2 shift. On computer controlled transmission,you will also have electrical solenoids that are mounted in the valve body to direct fluid to the appropriate clutch packs or bands under computer control to more precisely control shift points.8Seals and GasketsAn automatic transmission has many seals and gaskets to control the flow of hydraulic fluid and to keep it from leaking out. There are two main external seals : the front seal and the rear seal. The front seal seals the point where the torque converter mounts to the transmission case. This seal allows fluid to freely move from the converter to the transmission but keeps the fluid from leaking out. The rear seal keeps fluid from leaking past the output shaft.A seal is usually made of rubber similar to the rubber in a windshield wiper blade and is used to keep oil from leaking past a moving part such as a spinning shaft. In some cases,the rubber is assisted by a spring that holds he rubber in close contact with the spinning shaft.A gasket is a type of seal used to seal two stationary parts that are fasted together. Some common gasket materials are : paper,cork,rubber,silicone and soft metal.Aside from the main seals,there are also a number of other seals and gasket that vary from transmission to transmission. A common example is the rubber O-ring that seals the shaft for the shift control lever. This is the shaft that you move when you manipulate the gear shifter. Another example that is common to most transmission is the oil pan gasket. In fact,seals are required anywhere that a device needs to pass through the transmission case with each one being a potential source for leaks.9Computer ControlsThe computer uses sensors on the engine and transmission to detect such things as throttle position,vehicle speed,engine speed,engine load,stop light switch position,etc. to control exact shift points as well as how soft or firm the shift should be. Some computerized transmission even learn your driving style andconstantly adapt to it so that every shift is timed precisely when you would need it.Because of computer controls,sports models are coming out with the ability to take manual control of the transmission as through it were a stick shift lever through a special gate,then tapping it in one direction or the other in order to up-shift at will. The computer monitors this activity to make sure that the driver dose not select a gear that could over speed the engine and damage it.Another advantage to these “ smart” transmission is that they have a self diagnostic mode which can detect a problem early on and warn you with an indicator light on the dash. A technician can then plug test equipment in and retrieve a list of trouble codes that will help pinpoint where the problem is.Vehicular Automatic Transmission can be divided into three types: Automatic TransmissionAT, Automated Mechanical Transmission AMT and Continuously Variable TransmissionCVT. LMT has become a kind of transmission that is full of potentiality, due to its high transfer efficiency, low cost and easiness to manufacture.The research on AMT shifting performance is key technology in the developing. Shifting performance directly influence the market competition and industrialization of AMT.AMT has good market expectation, but during the shifting procedure, the power must be cut off which causes the poor shifting performance than AT and CVT. Only through improving the shitting performance can the commercial competence be established. So the virtual important thing is to find the way to improve shifting performance.The development of AMT can be divided into three phases: semi-automatic, automatic, and intelligent. The two major part of AMT are: the hardware including the mastered object, executor , sensors and TCU; and the software performing the control strategy.The performance of AT shift influences greatly the performance of the vehicle. So the research on at shift quality is an important problem in the domain of AT researching. 5hi代q notify control of AT is accomplished by electronic andhydraulic system. To shift smoothly, according the real time throttle calve opening and vehicle speed signal, the controller sends electronic signals to control oil pressure changing curve of the applying elements. this paper analyzes and research detailed shift quality control system, the analyzing model of shifting process and pressure changing curve of the applying elements.Firstly this paper summaries the existing evaluated quota of shift quality, and fully analyzes and introduces the existing control manner of AT shift quality.To meet the needs of research of vehicle starting and the real time control of shift, this paper puts forward a simplified model of engine-torque and a dynamics model of AT shifting process. Through the applying of the established model, this paper fully analyses the process al' the AT shitting.This paper drafts the proper oil pressure changing curve of the applying elements which can improve the AT shift quality, and gives the material calculated methods of the AG4 AT. This paper simulates the AG4 AT's shifting process of 2H to results of the simulation validate the established simplified models and the expected oil pressure changing curve.This paper fully analyses the mechanism of the pressure regulating and flow controlling system of the AG4 AT, and preparatory discusses the design of the block-diagram of the shift quality control. This paper test the control system and hydraulic system of the AG4 AT by the AT hydraulic-electronic testing-bed. The result of the test validates the correction of these analyses.Automated Mechanical Transmission, as so called AMT, is a new-style transmission technology applies the automatic. technology to the manual mechanical transmission and makes the selection-gear, shift, clutch and throttle implement automatically. AMT technology is suitable for the situation of our country, and has an expansive market arid development foreground. Shift schedules decide the time to shill and are the soul of the AMT. When the AMT is working, by comparing the states of the vehicle with the optimal shift schedules, the AMT decides the optimal shift time and achieves the shill automatically. This will lessen the tiredness of the drier and improve thesafety. all the same time, the power and fuel-economy of the vehicle can also be improved. The author chooses the shift schedule as the key technology problem to be researched and the main study aim of this thesis is to get the optimal shill schedules for the AMT and so improve the power and fuel-economy of the vehicle. Through analyzing the influence factors of power and fuel-economy far the automobile, the author get the establishment methods for the optimal-power shift schedule and optimal fuel-economy shill schedule. In order to solve the influence of mass on the shift schedule, the author presents a variable-structure-controlled shift system. This enriches the theory of shift schedules. Because the computer simulation can save a lot of manpower and material resources comparing with the true-car test, so in this thesis, the author uses the simulation toolbox MATLABI/Simulate to setup the simulation model for shift schedules. Using this model, the optimal-power shift schedule and optimal fuel-economy shift schedule above are simulated and proved to be reasonable.Shifting performance is defined as the extent of swiftness and softness during the procedure of non-power shifting and to extend the left of the power train. The index is comfort of passenger, time duration and shock, nine Factors maybe influence the shifting performance, and two experimental methods can be used to investigate the nature of this performance: one is collecting real-time data during road experiment and analyzing them, the other is the simulation of the operation conditions of the vehicle.The core of the AMT system is the control strategy, the principle of the clutch engagement, shifting procedure, the choice of` control method and the CAN communication between TCU and ECU can influence the shifting performance.Shilling schedule is the schedule of auto shifting time between two shifts with controlling parameters. It includes economical and dynamical shilling schedule. At present, shilling schedule of two controlling parameters Vehicle speed and opening on throttle is mainly used. If shifting schedule is not good, shifting will not happen at right time and the working condition of engine will be severe. It will make the sound of engine abnormally and stability badly throughthe whole shifting procession. Sometimes even flame out Schedule of clutch engagement is determined by releasing journey of clutch, opening of throttle, shifting, Vehicle speed and loading. The main.Controlling goals are engaging quantity and engaging speed. The engaging control of clutch is mainly referred to the control of engaging speed. It is divided into three stages: fast, slow, Fast. Shifting quality is directly influenced by the second stage. If engaging harder, it will make shitting concussion, even flame out: if` engaging more slowly, it will make the Friction time longer and reduce its longevity. The main controlling parameters are difference between initiative and passive and torques on both sides. When torques being approximately equal, it is proved by experiments that it can guarantee shifting time and not make concussion through the procession of engagement at the time of difference of rotating speed below some Value. Meanwhile, the abrasion of clutch is not severe.Shifting procedure is the procedure through working harmoniously among engine, clutch and transmission. Their cooperation will affect shifting time heavily. In order to decrease the shining tune, the time that is spent on the Friction of the clutch should be decreased First. If we intend to increase the time of non-load stage, which helps to minimize the difference of the rotary speed between the driving disc and the driven disc. If we intend to shorten the time of the non-toad stage, engage the clutch immediately after the gear change. The clutch can engage in a satisfying period ii` the new method of controlling the engaging speed of the clutch is realizable. And the time that is spent on synchronizing the gears should also he shortened. It can be realized in the following two ways. The first is to decrease the difference of the driving gear and the driven gear. The second is to increase the shifting force. If realizing the union control between and TCU by CAN bus, AMT has the best control and the best shitting performance by use of communication strategy between TCU and ECU.Influence on shifting performance by hardware.The elements in hardware system are the basis of proper functions of AMT. Executors, sensors, electronic components, hydraulic systems have influenceson shifting performance, the choice of hardware parameters is of` vital important to improvement of shilling performance.With the development of the theory and technology of vehicle, the technical increasingly mature of microprocessor and the extensive application of electronic technique on the car, people have no limit at satisfying the automotive means of transportation only, facing gradually from the request of the ear power, economy and easily manipulating, flexibility, safety, an d the intelligent type of car becomes the focus in the vision of people increasingly. Company's publicity slogan of" person, car, life"," make people the center" etc. On the side exhibit the expectation of people to the automotive individuation, humanity.In the development direction of the car intelligence, the intelligence of the automatic gearbox has important effect. But the intelligence of the automatic. gearbox embodies at the establishment of the shill regulation. For the fashion, for satisfying people to the new automotive request, far competitive advantage of the car type, at present each big factory in world worked very much in shill regulation of new car type. Among those, the mast arresting is AL4 automatic gearbox developed by PELIGEGTICITROEN and RENAULT in that there unexpectedly are the 1 D kinds of so many shift regulations. In the big system of person-car-road, the goad and had of the car control, reflect primarily in the coordination of the vehicle and environment road, the coordination of the vehicle and person. And so, the electronic automatic control system can same various regulations to provide the driver to choose to use, not only having the economic regulation ,motive ca11 to sport the type again regulation, but also still having the general usual regulation ,environment temperature and regulation with the outsider condition variety Namely, the point of` shilling can be Li-eely enacted for every kind of regulation. In the intelligence direction of` the shill regulation, everyone has made much work up to now, parts of the results has been applied on the car. But the work that developing this intelligent shill regulation still is hard, this is mainly.because of:1 .The intelligence degree of the current intelligent gearbox needs to be increased, and it expresses at that accurate degree to identify environment t,riot high and to identify the driver's driving can't give satisfaction.2. The intelligence function is still not perfect. The intelligent automatically ship system is an open system; it must he continuously perfect and plentiful on the current foundation. Only this way, it can adapt to the driving request of the different drivers, reducing the driver's labor strength, Increasing the performance of the whole vehicle.Conventional design method which used in the structure parameters' design of automobile gear box and synchronizer is a time-wasting job and hard work and it is difficult to get idea design parameters and no good to the enhancement of products qualities. The optimum design of automobile gearbox and synchronizer which take the advantage of computers seeking the best structure parameters within constrains is a perfect and high-quality design method. The main target of this article is to set up a optimum mathematical model of structure parameters of the truck's gearbox and synchronizer, the auth or use a optimum method based an K-T equation to improve the design level automobile gearbox and synchronizer. Gearbox is a important part of transmission, so the optimization of automobile gearbox is very important because the transmission is a main part of automobile. According to the design request and character sofa sort of truck, the optimum mathematical model of` track's gearbox is analyzed and set up in this article to decrease iGs weight and volume when the strength, stiffness, and lifetime of parts are permitted. hind we can receive a satisfaction result through optimizing it's parameter for instance.Synchronizer is a important part of automobile gearbox, it make drive gear and driven gear engaged after their synchronized, so it can decrease engaged shock and noise, it can decrease shift forcing and make it comfort to gear shill and increase the life of synchronizer. The synchronized process of synchronizer is analyzed in this article; we can recei4'e a satisfaction result through optimizing its influence parameter for instance when the synchronized time is the shortest. The optimum toolbox of MATLAB is a convenient of ware of modern。
变速器外文翻译

Continuously Variable Transmissions An Overview of CVT Research Past, Present, and FutureKevin R. Lang21W. 732May 3, 2000Table of Contents Introduction (1)CVT Theory & Design (2)Push Belt (2)Toroidal Traction Drive (2)Variable Diameter Elastomer Belt (3)Other CVT Varieties (3)Background & History (3)Inherent Advantages & Benefits (4)Challenges & Limitations (5)Research & Development (6)New CVT Research (7)Future Prospects for CVTs (9)CVTs & Hybrid Electric Vehicles (9)Conclusion (10)Works Cited (11)Figures and TablesFigure 1 – Metal Push Belt CVT (2)Figure 2 – Toroidal CVT (2)Figure 3 – Variable Diameter Belt CVT (3)Figure 4 – GM’s New CVT Design (6)Figure 5 – Audi CVT with link chain (6)Figure 6 – Cutaway of Audi CVT (7)Table 1 – Efficiency vs. Gear Ratio for Automatic Transmission (4)Table 2 – Efficiency of Various CVT Designs (4)AbstractAs the U.S. government enacts new regulations for automotive fuel economy and emissions, the continuously variable transmission, or CVT, continues to emerge as a key technology for improving the fuel efficiency of automobiles with internal combustion (IC) engines. CVTs use infinitely adjustable drive ratios instead of discrete gears to attain optimal engine performance. Since the engine always runs at the most efficient number of revolutions per minute for a given vehicle speed, CVT-equipped vehicles attain better gas mileage and acceleration than cars with traditional transmissions.CVTs are not new to the automotive world, but their torque capabilities and reliability have been limited in the past. New developments in gear reduction and manufacturing have led to ever-more-robust CVTs, which in turn allows them to be used in more diverse automotive applications. CVTs are also being developed in conjunction with hybrid electric vehicles. As CVT development continues, costs will be reduced further and performance will continue to increase, which in turn makes further development and application of CVT technology desirable.This paper evaluates the current state of CVTs and upcoming research and development, set in the context of past development and problems traditionally associated with CVTs. The underlying theories and mechanisms are also discussed.IntroductionAfter more than a century of research and development, the internal combustion (IC) engine is nearing both perfection and obsolescence: engineers continue to explore the outer limits of IC efficiency and performance, but advancements in fuel economy and emissions have effectively stalled. While many IC vehicles meet Low Emissions Vehicle standards, these will give way to new, stricter government regulations in the very near future. With limited room for improvement, automobile manufacturers have begun full-scale development of alternative power vehicles. Still, manufacturers are loath to scrap a century of development and billions or possibly even trillions of dollars in IC infrastructure, especially for technologies with no history of commercial success. Thus, the ideal interim solution is to further optimize the overall efficiency of IC vehicles.One potential solution to this fuel economy dilemma is the continuously variable transmission (CVT), an old idea that has only recently become a bastion of hope to automakers. CVTs could potentially allow IC vehicles to meet the first wave of new fuel regulations while development of hybrid electric and fuel cell vehicles continues. Rather than selecting one of four or five gears, a CVT constantly changes its gear ratio to optimize engine efficiency with a perfectly smooth torque-speed curve. This improves both gas mileage and acceleration compared to traditional transmissions.The fundamental theory behind CVTs has undeniable potential, but lax fuel regulations and booming sales in recent years have given manufacturers a sense of complacency: if consumers are buying millions of cars with conventional transmissions, why spend billions to develop and manufacture CVTs? Although CVTs have been used in automobiles for decades, limited torque capabilities and questionable reliability have inhibited their growth. Today, however, ongoing CVT research has led to ever-more-robust transmissions, and thus ever-more-diverse automotive applications. As CVT development continues, manufacturing costs will be further reduced and performance will continue to increase, which will in turn increase the demand for further development. This cycle of improvement will ultimately give CVTs a solid foundation in the world’s automotive infrastructure.Figure (1) – Metal Push Belt CVTFrom [3]Figure (2) – Toroidal CVTFrom [3]CVT Theory & DesignToday’s automobiles almost exclusively use either a conventional manual or automatictransmission with “multiple planetary gear sets that use integral clutches and bands to achieve discrete gear ratios” [3]. A typical automatic uses four or five such gears, while a manual normally employs five or six. The continuously variable transmission replaces discrete gear ratios with infinitely adjustable gearing through one of several basic CVT designs.Push BeltThis most common type of CVT usessegmented steel blocks stacked on a steel ribbon, asshown in Figure (1). This belt transmits powerbetween two conical pulleys, or sheaves, one fixedand one movable [3]. With a belt drive:In essence, a sensor reads the engine output and then electronically increases or decreases thedistance between pulleys, and thus the tension of the drive belt. The continuously changing distance between the pulleys—their ratio to one another—is analogous to shifting gears. [6]Push-belt CVTs were first developed decades ago, but new advances in belt design have recently drawn the attention of automakers worldwide.Toroidal Traction-DriveThese transmissions use the high shear strength of viscousfluids to transmit torque between an input torus and an outputtorus. As the movable torus slides linearly, the angle of a rollerchanges relative to shaft position, as seen in Figure (2). Thisresults in a change in gear ratio [3].Variable Diameter Elastomer BeltThis type of CVT, as represented in Figure (2), usesa flat, flexible belt mounted on movable supports. Thesesupports can change radius and thus gear ratio. However,the supports separate at high gear ratios to form adiscontinuous gear path, as seen in Figure (3). This can lead to the problems with creep and slip that have plagued CVTs for years [3]. This inherent flaw has directed research and development toward push belt CVTs.Other CVT VarietiesSeveral other types of CVTs have been developed over the course of automotive history, butthese have become less prominent than push belt and toroidal CVTs. A nutating traction drive uses a pivoting, conical shaft to change “gears” in a CVT. As the cones change angle, the inlet radius decreases while the outlet radius increases, or vice versa, resulting in an infinitely variable gear ratio [3]. A variable geometry CVT uses adjustable planetary gearsets to change gear ratios, but this is more akin to a flexible traditional transmission than a conventional CVT.Background & HistoryTo say that the continuously variable transmission (CVT) is nothing new would be a grossunderstatement: Leonardo da Vinci sketched his idea for a CVT in 1490 [1]. In automotive applications,CVTs have been around nearly as long as cars themselves, and certainly as long as conventionalautomatics. General Motors actually developed a fully toroidal CVT in the early 1930s and conducted extensive testing before eventually deciding to implement a conventional, stepped-gear automatic due to cost concerns. General Motors Research worked on CVTs again in the 1960s, but none ever sawproduction [2]. British manufacturer Austin used a CVT for several years in one of its smaller cars, but “it was dropped due to its high cost, poor reliability, and inadequate torque transmission” [2]. Many early CVTs used a simple rubber band and cone system, like the one developed by Dutch firm Daf in 1958 [1].Figure (3) – Variable Diameter Belt CVTFrom [3]However, the Daf CVT could only handle a 0.6 L engine, and problems with noise and rough starts hurt its reputation [1]. Uninspired by these early failures, automakers have largely avoided CVTs until very recently, especially in the United States.Inherent Advantages & BenefitsCertainly, the clunk of a shifting transmission is familiar to all drivers. By contrast, a continuously variable transmission is perfectly smooth—it naturally changes “gears” discreetly and minutely such that the driver or passenger feels only steady acceleration. In theory, a CVT would cause less engine fatigue and would be a more reliable transmission, as the harshness of shifts and discrete gears force the engine to run at a less-than-optimal speed.Moreover, CVTs offer improved efficiency and performance. Table (1) below shows the power transmission efficiency of a typical five-speed automatic, i.e. the percentage of engine power translated through the transmission. This yields an average efficiency of 86%, compared to a typical manual transmission with 97% efficiency [3]. By comparison, Table (2) below gives efficiency ranges for several CVT designs.Table (1) Efficiency vs. Gear Ratio for Automatic Transmission [3] Gear Efficiency Range160-85%260-90%385-95%490-95%585-94%Table (2) Efficiency of Various CVT Designs [3] CVT Mechanism Efficiency Range Rubber Belts90-95%Steel Belts90-97%Toroidal Traction70-94%Nutating Traction75-96%Variable Geometry85-93%These CVTs each offer improved efficiency over conventional automatic transmissions, and their efficiency depends less on driving habit than manual transmissions [3]. Moreover:Because the CVT allows an engine to run at this most efficient point virtuallyindependent of vehicle speed, a CVT equipped vehicle yields fuel economy benefitswhen compared to a conventional transmission (3)Testing by ZF Getriebe GmbH several years ago found that “the CVT uses at least 10% less fuel than a 4-speed automatic transmission” for U.S. Environmental Protection Agency city and highway cycles. Moreover, the CVT was more than one second faster in 0-60 mph acceleration tests [5]. The potential for fuel efficiency gains can also be seen in the CVT currently used in Honda’s Civic. A Civic with atraditional automatic averages 28/35 miles per gallon (mpg) city/highway, while the same car with a CVT gets 34/38 mpg city/highway [4]. Honda has used continuously variable transmissions in the Civic for several years, but these are 1.6 liter cars with limited torque capabilities. Ongoing research and development will inevitably expand the applicability of CVTs to a much broader range of engines and automobiles.Challenges & LimitationsCVT development has progressed slowly for a variety of reasons, but much of the delay in development can be attributed to a lack of demand: conventional manual and automatic transmissions have long offered sufficient performance and fuel economy. Thus, problems encountered in CVT development usually stopped said progress. “Designers have … unsuccessfully tried to develop [a CVT] that can match the torque capacity, efficiency, size, weight, and manufacturing cost of step-ratio transmissions” [6].One of the major complaints with previous CVTs has been slippage in the drive belt or rollers. This is caused by the lack of discrete gear teeth, which form a rigid mechanical connection between to gears; friction drives are inherently prone to slip, especially at high torque. With early CVTs of the 1950s and 1960s, engines equipped with CVTs would run at excessively high RPM trying to “catch up” to the slipping belt. This would occur any time the vehicle was accelerated from a stop at peak torque:“For compressive belts, in the process of transmitting torque, micro slip occurs betweenthe elements and the pulleys. This micro slip tends to increase sharply once thetransmitted torque exceeds a certain value …” [8]For many years, the simple solution to this problem has been to use CVTs only in cars with relativelylow-torque engines. Another solution is to employ a torque converter (such as those used in conventional automatics), but this reduces the CVT’s efficiency [2].Perhaps more than anything else, CVT development has been hindered by cost. Low volume and a lack of infrastructure have driven up manufacturing costs, which inevitably yield higher transmission prices. With increased development, most of these problems can be addressed simply by improvements in manufacturing techniques and materials processing. For example, Nissan’s Extroid “is derived from aFigure (4) – GM’s New CVT designFrom [6]Figure (5) – Audi CVT with link chainFrom [1]century-old concept, perfected by modern technology, metallurgy, chemistry, electronics, engineering,and precision manufacturing” [2].In addition, CVT control must be addressed. Even if a CVT can operate at the optimal gear ratio at any speed, how does it “know” what ratio to select? Manual transmissions have manual controls,where the driver shifts when he or she so desires; automatic transmissions have relatively simple shifting algorithms to accommodate between three and five gears. However, CVTs require far more complex algorithms to accommodate an infinite division of speeds and gear ratios.Research & DevelopmentWhile IC development has slowed in recent years asautomobile manufacturers devote more resources to hybrid electricvehicles (HEVs) and fuel cell vehicles (FEVs), CVT research anddevelopment is expanding quickly. Even U.S. automakers, who havelagged in CVT research until recently, are unveiling new designs:General Motors plans to implement metal-belt CVTs in some vehiclesby 2002 [6].The Japanese and Germans continue to lead the way in CVT development. Nissan has taken a dramatic step with its “Extroid” CVT, offered in the home-market Cedric and Gloria luxury sedans. This toroidal CVT costs more than a conventional belt-driven CVT, but Nissan expects the extra cost to be absorbed by the luxury cars’ prices [2]. The Extroid uses a high viscosity fluid to transmit power between the disks and rollers, rather than metal-to-metal contact. Coupled with a torque converter, this yields“exceptionally fast ratio changes”. Most importantly, though, theExtroid is available with a turbocharged version of Nissan’s 3.0 literV6 producing 285 lb-ft of torque; this is a new record for CVTtorque capacity [2].Audi’s new CVT offers both better fuel mileage than a conventional automatic and better acceleration than even aFigure (6) – Cutaway of Audi CVT From [1]manual transmission. Moreover, Audi claims it can offer the CVT at only a slight price increase [1]. This so-called “multitronic” CVT uses an all-steel link plate chain instead of a V-belt in order to handle up to 280 lb-ft of torque [1]. In addition, “Audi claims that the multitronic A6accelerates from 0-100 km/h (0-62 mph) 1.3 s quicker than a gearedautomatic transmission and is 0.1 s quicker over the same speed than anequivalent model with “optimum” use of a five speed manual gearbox”[1]. If costs were sufficiently reduced, a transmission such as this couldbe used in almost any automobile in the world.Many small cars have used CVTs in recent years, and many more will use them in the near future. Nissan, Honda, and Subaru currently use belt-drive CVTsdeveloped with Dutch company Van Doorne Transmissie (VDT) in some of their smaller cars [7]. Suzuki and Daihatsu are jointly developing CVTs with Japanese company Aichi Machine, using analuminum/plastic composite belt reinforced with Aramid fibers. Their CVT uses an auxiliary transmission for starts to avoid low-speed slip. After about 6 mph, the CVT engages and operates as it normally would[7]. “The auxiliary geartrain’s direct coupling ensures sufficiently brisk takeoff and initial acceleration”[7]. However, Aichi’s CVT can only handle 52 lb-ft of torque. This alone effectively negates itspotential for the U.S. market. Still, there are far more CVTs in production for 2000 than for 1999, and each major automobile show brings more announcements for new CVTs.New CVT ResearchAs recently as 1997, CVT research focused on the basic issues of drive belt design and power transmission. Now, as belts by VDT and other companies become sufficiently efficient, research focuses primarily on control and implementation of CVTs.Nissan Motor Co. has been a leader in CVT research since the 1970s. A recent study analyzing the slip characteristics of a metal belt CVT resulted in a simulation method for slip limits and torque capabilities of CVTs [8]. This has led to a dramatic improvement in drive belt technology, since CVTs can now be modeled and analyzed with computer simulations, resulting in faster development and moreefficient design. Nissan’s research on the torque limits of belt-drive CVTs has also led to the use of torque converters, which several companies have since implemented. The torque converter is designed to allow “creep,” the slow speed at which automatic transmission cars drive without driver-induced acceleration. The torque converter adds “improved creep capability during idling for improved driveability at very low speeds and easy launch on uphill grades” [9]. Nissan’s Extroid uses such a torque converter for “smooth starting, vibration suppression, and creep characteristics” [2].CVT control has recently come to the forefront of research; even a mechanically perfect CVT is worthless without an intelligent active control algorithm. Optimal CVT performance demands integrated control, such as the system developed by Nissan to “obtain the demanded drive torque with optimum fuel economy” [13]. The control system determines the necessary CVT ratio based on a target torque, vehicle speed, and desired fuel economy. Honda has also developed an integrated control algorithm for its CVTs, considering not only the engine’s thermal efficiency but also work loss from drivetrain accessories and the transmission itself [12]. Testing of Honda’s algorithm with a prototype vehicle resulted in a one percent fuel economy increase compared to a conventional algorithm. While not a dramatic increase, Honda claims that its algorithm is fundamentally sound, and thus will it become “one of the basic technologies for the next generation’s powerplant control” [12].Although CVTs are currently in production, many control issues still amount to a “tremendous number of trials and errors” [10]. One study focusing on numerical representation of power transmission showed that “both block tilting and pulley deformation meaningfully effected the pulley thrust ratio between the driving and the driven pulleys” [10]. Thus, the resultant model of CVT performance can be used in future applications for transmission optimization. As more studies are conducted, fundamental research such as this will become the legacy of CVT design, and research can become more specialized as CVTs become more refined.As CVTs move from research and development to assembly line, manufacturing research becomes more important. CVTs require several crucial, high-tolerance components in order to function efficiently; Honda studied one of these, the pulley piston, in 1998. Honda found that prototype pistons“experienced a drastic thickness reduction (32% at maximum) due to the conventional stretch forming method” [11]. A four-step forming process was developed to ensure “a greater and more uniform thickness increase” and thus greater efficiency and performance. Moreover, work-hardening during the forming process further increased the pulley piston’s strength [11].Size and weight of CVTs has long been a concern, since conventional automatics weigh far more than manual transmissions and CVTs outweigh automatics. Most cars equipped with automatic transmissions have a curb weight between 50 and 150 pounds heavier than the same cars with manual transmissions. To solve this problem, Audi is currently developing magnesium gearbox housings, a first for cars in its class. This results in nearly a 16 pound weight reduction over conventional automatics. [1]. Future Prospects for CVTsMuch of the existing literature is quick to admit that the automotive industry lacks a broad knowledge base regarding CVTs. Whereas conventional transmissions have been continuously refined and improved since the very start of the 20th century, CVT development is only just beginning. As infrastructure is built up along with said knowledge base, CVTs will become ever-more prominent in the automotive landscape. Even today’s CVTs, which represent first-generation designs at best, outperform conventional transmissions. Automakers who fail to develop CVTs now, while the field is still in its infancy, risk being left behind as CVT development and implementation continues its exponential growth. Moreover, CVTs are do not fall exclusively in the realm of IC engines.CVTs & Hybrid Electric VehiclesWhile CVTs will help to prolong the viability of internal combustion engines, CVTs themselves will certainly not fade if and when IC does. Several companies are currently studying implementation of CVTs with HEVs. Nissan recently developed an HEV with “fuel efficiency … more than double that of existing vehicles in the same class of driving performance” [14]. The electric motor avoids the low-speed/high torque problems often associated with CVTs, through an innovative double-motor system. At low speeds:A low-power traction motor is used as a substitute mechanism to accomplish thefunctions of launch and forward/reverse shift. This has made it possible to discontinueuse of a torque converter as the launch element and a planetary gearset and wet multiplateclutches as the shift mechanism. [14]Thus use of a CVT in a HEV is optimal: the electric portion of the power system avoids the low-speed problems of CVTs, while still retaining the fuel efficiency and power transmission benefits at high speeds.. Moreover, “the use of a CVT capable of handling high engine torque allows the system to be applied to more powerful vehicles” [14]. Obviously, automakers cannot develop individual transmissions for each car they sell; rather, a few robust, versatile CVTs must be able to handle a wide range of vehicles.Korean automaker Kia has proposed a rather novel approach to CVTs and their application to hybrids. Kia recently tested a system where “the CVT allows the engine to run at constant speed and the motor allows the engine to run at constant torque independent of driving conditions” [15]. Thus, both gasoline engine and electric motor always run at their optimal speeds, and the CVT adjusts as needed to accelerate the vehicle. Kia also presented a control system for this unified HEV/CVT combination that optimizes fuel efficiency for the new configuration.ConclusionToday, only a handful of cars worldwide make use of CVTs, but the applications and benefits of continuously variable transmissions can only increase based on today’s research and development. As automakers continue to develop CVTs, more and more vehicle lines will begin to use them. As development continues, fuel efficiency and performance benefits will inevitably increase; this will lead to increased sales of CVT-equipped vehicles. Increased sales will prompt further development and implementation, and the cycle will repeat ad infinitum. Moreover, increasing development will foster competition among manufacturers—automakers from Japan, Europe, and the U.S. are already either using or developing CVTs—which will in turn lower manufacturing costs. Any technology with inherent benefits will eventually reach fruition; the CVT has only just begun to blossom.Works Cited[1]S. Birch: “Audi takes CVT from 15th century to 21st century”. Automotive Engineering International,January 2000.[2]J. Yamaguchi: “Nissan’s Extroid CVT”. Automotive Engineering International, February 2000.[3]M.A. Kluger and D.R. Fussner: “An Overview of Current CVT Mechanisms, Forces andEfficiencies” SAE Paper No. 970688, in SAE SP-1241, Transmission and Driveline SystemsSymposium, pp. 81-88 SAE, 1997.[4]U.S. Environmental Protection Agency, /feg/findacar.htm.Accessed 4/15/00.[5]M. Boos and H. Mozer: “ECOTRONIC – The Continuously Variable ZF Transmission (CVT)” SAEPaper No. 970685, in SAE SP-1241, Transmission and Driveline Systems Symposium, pp. 61-67 SAE, 1997.[6]J.L. Broge: “GM Powertrain’s evolving transmissions”. Automotive Engineering International,November 1999.[7]J. Yamaguchi: “Two new CVTs for mini cars”. Automotive Engineering International, March 1999.[8]D. Kobayashi, Y. Mabuchi and Y. Katoh: “A Study on the Torque Capacity of a Metal Pushing V-Belt for CVTs” SAE Paper No. 980822, in SAE SP –1324, Transmission and Driveline Systems Symposium, pp. 31-39 SAE, 1998.[9]K. Abo, M. Kobayashi and M. Kurosawa: “Development of a Metal Belt Drive CVT Incorporating aTorque Converter for Use with 2-liter Class Engines” SAE Paper No. 980823, in SAE SP-1324, Transmission and Driveline Systems Symposium, pp. 41-48 SAE, 1998.[10]T. Miyazawa, T. Fujii, K. Nonaka and M. Takahashi: “Power Transmitting Mechanism of a DryHybrid V-Belt for a CVT – Advanced Numerical Model Considering Block Tilting and PulleyDeformation” SAE Paper No. 1999-01-0751, in SAE SP-1440, Transmission and Driveline Systems Symposium, pp. 143-153 SAE, 1999.[11]K. Ohya and H. Suzuki: “Development of CVT Pulley Piston Featuring Variable Thickness andWork-Hardening Technologies” SAE Paper No. 980826, in SAE SP-1324, Transmission andDriveline Systems Symposium, pp. 71-79 SAE, 1998.[12]S. Sakaguchi, E. Kimura and K. Yamamoto: “Development of an Engine-CVT Integrated ControlSystem” SAE Paper No. 1999-01-0754, in SAE SP-1440, Transmission and Driveline SystemsSymposium, pp. 171-179 SAE, 1999.[13]M. Yasuoka, M. Uchida, S. Katakura and T. Yoshino: “An Integrated Control Algorithm for anSI Engine and a CVT” SAE Paper No. 1999-01-0752, in SAE SP-1440, Transmission and Driveline Systems Symposium, pp. 155-160 SAE, 1999.[14]N. Hattori, S. Aoyama, S. Kitada and I. Matsuo: “Functional Design of a Motor Integrated CVTfor a Parallel HEV” SAE Paper No. 1999-01-0753, in SAE SP-1440, Transmission and Driveline Systems Symposium, pp. 161-167 SAE, 1999.[15] C. Kim, E. NamGoong, S. Lee, T. Kim and H. Kim: “Fuel Economy Optimization for ParallelHybrid Vehicles with CVT” SAE Paper No. 1999-01-1148, in SAE SP-1440, Transmission and Driveline Systems Symposium, pp. 337-343 SAE, 1999.。
变速器(英文版文献)

Transmission (mechanics)A transmission or gearbox provides speed and torque conversions from a rotating power source to another device using gear ratios. In British English the term transmission refers to the whole drive train, including gearbox, clutch, prop shaft (for rear-wheel drive), differential and final drive shafts. The most common use is in motor vehicles, where the transmission adapts the output of the internal combustion engine to the drive wheels. Such engines need to operate at a relatively high rotational speed, which is inappropriate for starting, stopping, and slower travel. The transmission reduces the higher engine speed to the slower wheel speed, increasing torque in the process. Transmissions are also used on pedal bicycles, fixed machines, and anywhere else rotational speed and torque needs to be adapted.Often, a transmission will have multiple gear ratios (or simply "gears"), with the ability to switch between them as speed varies. This switching may be done manually (by the operator), or automatically. Directional (forward and reverse) control may also be provided. Single-ratio transmissions alsoexist, which simply change the speed and torque (and sometimes direction) of motor output.In motor vehicle applications, the transmission will generally be connected to the crankshaft of the engine. The output of the transmission is transmitted via driveshaft to one or more differentials, which in turn drive the wheels. While a differential may also provide gear reduction, its primary purpose is to change the direction of rotation.Conventional gear/belt transmissions are not the only mechanism for speed/torque adaptation. Alternative mechanisms include torque converters and power transformation (e.g., diesel-electric transmission, hydraulic drive system, etc.). Hybrid configurations also exist.ExplanationEarly transmissions included the right-angle drives and other gearing in windmills, horse-powered devices, and steam engines, in support of pumping, milling, and hoisting.Most modern gearboxes are used to increase torque while reducing the speed of a prime mover output shaft (e.g. a motor crankshaft). This means that the output shaft of a gearbox willrotate at slower rate than the input shaft, and this reduction in speed will produce a mechanical advantage, causing an increase in torque. A gearbox can be setup to do the opposite and provide an increase in shaft speed with a reduction of torque. Some of the simplest gearboxes merely change the physical direction in which power is transmitted.Many typical automobile transmissions include the ability to select one of several different gear ratios. In this case, most of the gear ratios (often simply called "gears") are used to slow down the output speed of the engine and increase torque. However, the highest gears may be "overdrive" types that increase the output speed.UsesGearboxes have found use in a wide variety of different—often stationary—applications, such as wind turbines.Transmissions are also used in agricultural, industrial, construction, mining and automotive equipment. In addition to ordinary transmission equipped with gears, such equipment makes extensive use of the hydrostatic drive and electrical adjustable-speed drives.SimpleThe simplest transmissions, often called gearboxes to reflect their simplicity (although complex systems are also called gearboxes in the vernacular), provide gear reduction (or, more rarely, an increase in speed), sometimes in conjunction with a right-angle change in direction of the shaft (typically in helicopters, see picture). These are often used on PTO-powered agricultural equipment, since the axial PTO shaft is at odds with the usual need for the driven shaft, which is either vertical (as with rotary mowers), or horizontally extending from one side of the implement to another (as with manure spreaders, flail mowers, and forage wagons). More complex equipment, such as silage choppers and snowblowers, have drives with outputs in more than one direction.The gearbox in a wind turbine converts the slow, high-torque rotation of the turbine into much faster rotation of the electrical generator. These are much larger and more complicated than the PTO gearboxes in farm equipment. They weigh several tons and typically contain three stages to achieve an overall gear ratio from 40:1 to over 100:1, depending on the size of the turbine. (For aerodynamic and structuralreasons, larger turbines have to turn more slowly, but the generators all have to rotate at similar speeds of several thousand rpm.) The first stage of the gearbox is usually a planetary gear, for compactness, and to distribute the enormous torque of the turbine over more teeth of the low-speed shaft. Durability of these gearboxes has been a serious problem for a long time.Regardless of where they are used, these simple transmissions all share an important feature: the gear ratio cannot be changed during use. It is fixed at the time the transmission is constructed.For transmission types that overcome this issue, see Continuously Variable Transmission, also known as CVT.Multi-ratio systemsMany applications require the availability of multiple gear ratios. Often, this is to ease the starting and stopping of a mechanical system, though another important need is that of maintaining good fuel efficiency.Automotive basicsThe need for a transmission in an automobile is aconsequence of the characteristics of the internal combustion engine. Engines typically operate over a range of 600 to about 7000 revolutions per minute (though this varies, and is typically less for diesel engines), while the car's wheels rotate between 0 rpm and around 1800 rpm.Furthermore, the engine provides its highest torque outputs approximately in the middle of its range, while often the greatest torque is required when the vehicle is moving from rest or traveling slowly. Therefore, a system that transforms the engine's output so that it can supply high torque at low speeds, but also operate at highway speeds with the motor still operating within its limits, is required. Transmissions perform this transformation.Many transmissions and gears used in automotive and truck applications are contained in a cast iron case, though more frequently aluminium is used for lower weight especially in cars. There are usually three shafts: a mainshaft, a countershaft, and an idler shaft.The mainshaft extends outside the case in both directions: the input shaft towards the engine, and the output shaft towards the rear axle (on rear wheel drive cars- front wheel drives generally have the engine and transmission mountedtransversely, the differential being part of the transmission assembly.) The shaft is suspended by the main bearings, and is split towards the input end. At the point of the split, a pilot bearing holds the shafts together. The gears and clutches ride on the mainshaft, the gears being free to turn relative to the mainshaft except when engaged by the clutches.Types of automobile transmissions include manual, automatic or semi-automatic transmission.ManualMain article: Manual transmissionManual transmission come in two basic types:a simple but rugged sliding-mesh or unsynchronized / non-synchronous system, where straight-cut spur gear sets are spinning freely, and must be synchronized by the operator matching engine revs to road speed, to avoid noisy and damaging "gear clash", and the now common constant-mesh gearboxes which can include non-synchronised, or synchronized / synchromesh systems, where diagonal cut helical (and sometimes double-helical) gear sets are constantly "meshed" together, and a dog clutch is used for changing gears. On synchromesh boxes, friction cones or "synchro-rings" are used in addition to the dog clutch.The former type is commonly found in many forms of racing cars, older heavy-duty trucks, and some agricultural equipment.Manual transmissions are the most common type outside North America and Australia. They are cheaper, lighter, usually give better performance, and fuel efficiency (although the latest sophisticated automatic transmissions may yield results slightly better than the ones yielded by manual transmissions). It is customary for new drivers to learn, and be tested, on a car with a manual gear change. In Malaysia, Denmark and Poland all cars used for testing (and because of that, virtually all those used for instruction as well) have a manual transmission. In Japan, the Philippines, Germany, Italy, Israel, the Netherlands, Belgium, New Zealand, Austria, Bulgaria, the UK, Ireland, Sweden, Estonia, France, Spain, Switzerland, the Australian states of Victoria and Queensland, Finland and Lithuania, a test pass using an automatic car does not entitle the driver to use a manual car on the public road; a test with a manual car is required.Manual transmissions are much more common than automatic transmissions in Asia, Africa, South America and Europe.Most manual transmissions include both synchronized andunsynchronized gearing, such as a reverse gear and a low-speed "granny gear", both of which can only be shifted into when stopped. Shifting from granny gear to a low synchronized gear is generally available while in motion, while shifting out of reverse to any other gear typically requires the vehicle to be stopped.Non-synchronousMain article: Non-synchronous transmissionsThere are commercial applications engineered with designs taking into account that the gear shifting will be done by an experienced operator. They are a manual transmission, but are known as non-synchronized transmissions. Dependent on country of operation, many local, regional, and national laws govern the operation of these types of vehicles (see Commercial Driver's License). This class may include commercial, military, agricultural, or engineering vehicles. Some of these may use combinations of types for multi-purpose functions. An example would be a PTO, or power-take-off gear. The non-synchronous transmission type requires an understanding of gear range, torque, engine power, and multi-functional clutch and shifter functions. Also see Double-clutching, and Clutch-brakesections of the main article at non-synchronous transmissionsAutomaticMain article: Automatic transmissionEpicyclic gearing or planetary gearing as used in an automatic transmission.Most modern North American and Australian and many larger, high specification European and Japanese cars have an automatic transmission that will select an appropriate gear ratio without any operator intervention. They primarily use hydraulics to select gears, depending on pressure exerted by fluid within the transmission assembly. Rather than using a clutch to engage the transmission, a fluid flywheel, or torque converter is placed in between the engine and transmission. It is possible for the driver to control the number of gears in use or select reverse, though precise control of which gear is in use may or may not be possible.Automatic transmissions are easy to use. However, in the past, automatic transmissions of this type have had a number of problems; they were complex and expensive, sometimes had reliability problems (which sometimes caused more expenses in repair), have often been less fuel-efficient than their manualcounterparts (due to "slippage" in the torque converter), and their shift time was slower than a manual making them uncompetitive for racing. With the advancement of modern automatic transmissions this has changed.Attempts to improve the fuel efficiency of automatic transmissions include the use of torque converters which lock up beyond a certain speed, or in the higher gear ratios, eliminating power loss, and overdrive gears which automatically actuate above certain speeds; in older transmissions both technologies could sometimes become intrusive, when conditions are such that they repeatedly cut in and out as speed and such load factors as grade or wind vary slightly. Current computerized transmissions possess very complex programming to both maximize fuel efficiency and eliminate any intrusiveness.For certain applications, the slippage inherent in automatic transmissions can be advantageous; for instance, in drag racing, the automatic transmission allows the car to be stopped with the engine at a high rpm (the "stall speed") to allow for a very quick launch when the brakes are released; in fact, a common modification is to increase the stall speed of the transmission. This is even more advantageous forturbocharged engines, where the turbocharger needs to be kept spinning at high rpm by a large flow of exhaust in order to keep the boost pressure up and eliminate the turbo lag that occurs when the engine is idling and the throttle is suddenly openedSemi-automaticMain article: Semi-automatic transmissionThe creation of computer control also allowed for a sort of cross-breed transmission where the car handles manipulation of the clutch automatically, but the driver can still select the gear manually if desired. This is sometimes called a "clutchless manual," or "automated manual" transmission. Many of these transmissions allow the driver to give full control to the computer. They are generally designed using manual transmission "internals", and when used in passenger cars, have synchromesh operated helical constant mesh gear sets.Specific type of this transmission includes: Easytronic, and Geartronic.A "dual-clutch" transmission uses two sets of internals which are alternately used, each with its own clutch, so that only the clutches are used during the actual "gearchange".Specific type of this transmission includes: Direct-ShiftGearbox.There are also sequential transmissions which use the rotation of a drum to switch gears.Bicycle gearingMain articles: Bicycle gearing, Derailleur gears, and Hub gear Bicycles usually have a system for selecting different gear ratios. There are two main types: derailleur gears and hub gears. The derailleur type is the most common, and the most visible, using sprocket gears. Typically there are several gears available on the rear sprocket assembly, attached to the rear wheel. A few more sprockets are usually added to the front assembly as well. Multiplying the number of sprocket gears in front by the number to the rear gives the number of gear ratios, often called "speeds".Hub gears use epicyclic gearing and are enclosed within the axle of the rear wheel. Because of the small space, they typically offer fewer different speeds, although at least one has reached 14 gear ratios and Fallbrook Technologies manufactures a transmission with technically infinite ratios.Causes for failure of bicycle gearing include: worn teeth, damage caused by a faulty chain, damage due to thermal expansion,broken teeth due to excessive pedaling force, interference by foreign objects, and loss of lubrication due to negligence.Uncommon typesDual clutch transmissionMain article: Dual clutch transmissionThis arrangement is also sometimes known as a direct shift gearbox or powershift gearbox. It seeks to combine the advantages of a conventional manual shift with the qualities of a modern automatic transmission by providing different clutches for odd and even speed selector gears. When changing gear, the engine torque is transferred from one gear to the other continuously, so providing gentle, smooth gear changes without either losing power or jerking the vehicle. Gear selection may be manual, automatic (depending on throttle/speed sensors), or a 'sports' version combining both options.Continuously variableMain article: Continuously variable transmissionThe Continuously Variable Transmission (CVT) is a transmission in which the ratio of the rotational speeds of twoshafts, as the input shaft and output shaft of a vehicle or other machine, can be varied continuously within a given range, providing an infinite number of possible ratios.The continuously variable transmission (CVT) should not be confused with the Infinitely Variable Transmission (IVT) (See below).The other mechanical transmissions described above only allow a few different gear ratios to be selected, but this type of transmission essentially has an infinite number of ratios available within a finite range. The continuously variable transmission allows the relationship between the speed of the engine and the speed of the wheels to be selected within a continuous range. This can provide even better fuel economy if the engine is constantly running at a single speed. The transmission is in theory capable of a better user experience, without the rise and fall in speed of an engine, and the jerk felt when poorly changing gears.Infinitely variableThe IVT is a specific type of CVT that has an infinite range of input/output ratios in addition to its infinite number of possible ratios; this qualification for the IVT implies thatits range of ratios includes a zero output/input ratio that can be continuously approached from a defined 'higher' ratio. A zero output implies an infinite input, which can be continuously approached from a given finite input value with an IVT. [Note: remember that so-called 'low' gears are a reference to low ratios of output/input, which have high input/output ratios that are taken to the extreme with IVT's, resulting in a 'neutral', or non-driving 'low' gear limit.] Most (if not all) IVT's result from the combination of a CVT with an epicyclic gear system (which is also known as a planetary gear system) that facilitates the subtraction of one speed from another speed within the set of input and planetary gear rotations. This subtraction only needs to result in a continuous range of values that includes a zero output; the maximum output/input ratio can be arbitrarily chosen from infinite practical possibilities through selection of extraneous input or output gear, pulley or sprocket sizes without affecting the zero output or the continuity of the whole system. Importantly, the IVT is distinguished as being 'infinite' in its ratio of high gear to low gear within its range; high gear is infinite times higher than low gear. The IVT is always engaged, even during its zero output adjustment.The term 'infinitely variable transmission' does not imply reverse direction, disengagement, automatic operation, or any other quality except ratio selectability within a continuous range of input/output ratios from a defined minimum to an undefined, 'infinite' maximum. This means continuous range from a defined output/input to zero output/input ratio.Electric variableThe Electric Variable Transmission (EVT) is a transmission that achieves CVT action and in addition can use separate power inputs to produce one output. An EVT usually is executed in design with an epicyclic differential gear system (which is also known as a planetary gear system). The epicyclic differential gearing performs a "power-split" function, directly connecting a portion of the mechanical power directly through the transmission and splitting off a portion for subsequent conversion to electrical power via a motor/generator. Hence, the EVT is called a Power Split Transmission (PST) by some.The directly connected portion of the power travelling through the EVT is referred to as the "mechanical path". The remaining power travels down the EVT's "electrical path". Thatpower may be recombined at the output of the transmission or stored for later, more opportune use via a second motor/generator (and energy storage device) connected to the transmission output.The pair of motor/generators forms an Electric Transmission in its own right, but at a lower capacity, than the EVT it is contained within. Generally the Electric Transmission capacity within the EVT is a quarter to a half of the capacity of the EVT. Good reasons to use an EVT instead of an equivalently-sized Electrical transmission is that the mechanical path of the EVT is more compact and efficient than the electrical path.The EVT is the essential method for transmitting power in some hybrid vehicles, enabling an Internal Combustion Engine (ICE) to be used in conjunction with motor/generators for vehicle propulsion, and having the ability to control the portion of the mechanical power used directly for propelling the vehicle and the portion of mechanical power that is converted to electric power and recombined to drive the vehicle.The EVT and power sources are controlled to provide a balance between the power sources that increases vehicle fueleconomy while providing advantageous performance when needed. The EVT may also be used to provide electrically generated power to charge large storage batteries for subsequent electric motor propulsion as needed, or to convert vehicle kinetic energy to electricity through 'regenerative braking' during deceleration. Various configurations of power generation, usage and balance can be implemented with a EVT, enabling great flexibility in propelling hybrid vehicles.The Toyota single mode hybrid and General Motor 2 Mode hybrid are production systems that use EVTs. The Toyota system is in the Prius, Highlander, and Lexus RX400h and GS450h models. The GM system is the Allison Bus hybrid powertrains and are in the Tahoe and Yukon models. The Toyota system uses one power-split epicyclic differential gearing system over all driving conditions and is sized with an electrical path rated at approximately half the capacity of the EVT. The GM system uses two different EVT ranges: one designed for lower speeds with greater mechanical advantage, and one designed for higher speeds, and the electrical path is rated at approximately a quarter of the capacity of the EVT. Other arrangements are possible and applications of EVT's are growing rapidly in number and variety.EVT's are capable of continuously modulating output/input speed ratios like mechanical CVT's, but offer the distinct difference and benefit of being able to also apportion power from two different sources to one output.HydrostaticSee also Continuously variable transmission > Hydrostatic CVTs Hydrostatic transmissions transmit all power hydraulically, using the components of hydraulic machinery. Hydrostatic transmissions do not make use of the hydrodynamic forces of the fluid flow. There is no solid coupling of the input and output. The transmission input drive is a central hydraulic pump and final drive unit(s) is/are a hydraulic motor, or hydraulic cylinder (see:swashplate. Both components can be placed physically far apart on the machine, being connected only by flexible hoses. Hydrostatic drive systems are used on excavators, lawn tractors, forklifts, winch drive systems, heavy lift equipment, agricultural machinery, etc. An arrangement for motor-vehicle transmission was probably used on the Ferguson F-1 P99 racing car in about 1961.The Human Friendly Transmission of the Honda DN-01 is hydrostatic.HydrodynamicIf the hydraulic pump and/or hydraulic motor make use of the hydrodynamic effects of the fluid flow, i.e. pressure due to a change in the fluid's momentum as it flows through vanes in a turbine. The pump and motor usually consist of rotating vanes without seals and are typically placed in close proximity. The transmission ratio can be made to vary by means of additional rotating vanes, an effect similar to varying the pitch of an airplane propeller.The torque converter in most automotive automatic transmissions is, in itself, a hydrodynamic transmission.It was possible to drive the Dynaflow transmission without shifting the mechanical gears.Hydrodynamic transmissions are used in many passenger rail vehicles. In this application the advantage of smooth power delivery may outweigh the reduced efficiency caused by turbulence energy losses in the fluid.ElectricElectric transmissions convert the mechanical power of the engine(s) to electricity with electric generators and convertit back to mechanical power with electric motors. Electrical or electronic adjustable-speed drive control systems are used to control the speed and torque of the motors. If the generators are driven by turbines, such arrangements are called turbo-electric. Likewise installations powered by diesel-engines are called diesel-electric. Diesel-electric arrangements are used on many railway locomotives, ships and large mining trucks.。
自动变速器发展现状及趋势外文文献翻译、中英文翻译、外文翻译

Current situation and development trend of automatic transmissionFirst, transmission profile1 manual transmission (MT)As we all know, the manual transmission gearbox is one of the most common car, its basic principle is to perform power transmission with a few parallel shafts and several meshing spur or helical gear, namely the input shaft axis and the axis constitute the main gearbox, plus a reverse gear and shaft synchronizer etc.. The working process is as follows: the driver through the drive rod to achieve different gear meshing, and ultimately to achieve different gear ratio gear.2 automatic manual transmission (AMT)Automatic manual transmission (AMT) is actually a machine system to complete the operation of the clutch and select the two movements. The AMT driver is simple, saves the clutch pedal, as long as the driver stepped on the accelerator, the best time selector system will automatically choose to shift, thereby eliminating the engine, clutch and transmission errors, to avoid the wrong bit shift. This is very important for both novice and vehicle reliability. Speed reducer greatly reduces the complexity of driving, so that AMT car driving more simple, worry, and to ensure the lowest power loss. By the selector to complete the driver to step on the clutch shift action, the timing of the shift is more accurate than the driver to complete. Therefore, the background for the growing shortage of energy and the emission of CO2 AMT under increasing pressure, conform to the "energy saving" this door, the best time selector system will automatically choose to shift, thereby eliminating the engine, clutch and transmission errors, to avoid the wrong change gear. This is very important for both novice and vehicle reliability. Speed reducer greatly reduces the complexity of driving, so that AMT car driving more simple, worry, and to ensure the lowest power loss. By the selector to complete the driver to step on the clutch shift action, the timing of the shift is more accurate than the driver to complete. Therefore, the background for the growing shortage of energy and the emission of CO2 AMT under increasing pressure, conform to the "energy saving" this door, the best time selector system will automatically choose to shift, thereby eliminating theengine, clutch and transmission errors, to avoid the wrong change gear. This is very important for both novice and vehicle reliability. Speed reducer greatly reduces the complexity of driving, so that AMT car driving more simple, worry, and to ensure the lowest power loss. By the selector to complete the driver to step on the clutch shift action, the timing of the shift is more accurate than the driver to complete. Therefore, the background for the growing shortage of energy and the emission of CO2 AMT under increasing pressure, conform to the "energy saving" this door, the best time selector system will automatically choose to shift, thereby eliminating the engine, clutch and transmission errors, to avoid the wrong change gear. This is very important for both novice and vehicle reliability. Speed reducer greatly reduces the complexity of driving, so that AMT car driving more simple, worry, and to ensure the lowest power loss. By the selector to complete the driver to step on the clutch shift action, the timing of the shift is more accurate than the driver to complete.3 electronically controlled hydraulic automatic transmission (AT)Electronic control of hydraulic automatic transmission (AT) in recent years, new technologies are constantly in use, it is moving toward multi block, digital control, etc.. Japan's largest automatic transmission manufacturer AISIN AW in 2006, the successful launch of model AA80E 8 speed automatic transmission (see Figure 3), is currently being used in the Lexus LS460 car. This will form a larger total transmission ratio, while the transmission ratio is also closer than the 5 speed transmission. Therefore, the driver can choose the best transmission ratio in almost all driving conditions. Electronic control module can choose more transmission ratio, the transmission ratio depends on the driving conditions, thereby reducing fuel consumption and improve the ride comfort. The optimal matching of engine speed and running state means that the engine improves the power and fuel economy and reduces the running noise.4 continuously variable transmission (CVT)Continuously variable transmission (CVT) is only two groups of removable cone and transmission belt or transmission chain, you can achieve the number of forward gear transmission process. The CVT drive to choose power transmission and the transmission ratio of the transmission chain and the variable cone groove width belt, when cone groove widthchanges, corresponding changes in the driving wheel and the driven wheel drive belt speed contact radius. CVT is a truly stepless, and AT compared with a high operating efficiency, low fuel consumption. Through the application of the market in recent years, the momentum of development is also relatively rapid, currently in our country has been applied to the rapid development of 5 models, more than 6 kinds of. Figure 4 shows the market outlook for the Chinese market in the next few years.At present, the world each big automobile manufacturers in order to improve the competitiveness of their products are vigorously engaged in research and development of CVT, equipped with CVT, TOYOTA, NISSAN car sales are FORD, GM, AUDI and other well-known car brands in the world, CVT's annual production has reached nearly 500 thousand vehicles. It is worth noting that, equipped with CVT car market, from the initial Japan, Europe has penetrated into the North American market, CVT has become the main trend of the development of today's automobile.5 dual clutch transmission (DCT)Dual clutch transmission (DCT) is the first German V olkswagen technology, so in theV olkswagen car system also known as DSG transmission. It can be said to be the world's most advanced, revolutionary transmission system, V olkswagen in 2002 in Wolfsburg, Germany for the first time to show the world the technological innovation. DSG transmission is designed to meet the consumer's desire to drive a sense of movement and fuel-efficient vehicles, for those who love the manual transmission drivers provide a best choice. DSG brings in low fuel consumption and vehicle performance without any loss, also has excellent acceleration and top speed, and the same with the traditional automatic transmission can realize smooth shift without affecting the traction force. Therefore, not only ensures the comfort, but also embodiesDynamic acceleration.Two, the development trend of transmissionAccording to industry estimates, statistical data will be the 2013 European transmission market changes, equipped with a manual transmission car will account for 52%, equippedwith automatic manual transmission will account for 10%, equipped with CVT will account for 2%, equipped with dual clutch transmission will account for 16%, equipped with automatic transmission will account for 20%. But industry experts have pointed out that the prediction was based on the transmission type of the existing new transmission products are constantly in the development process, so in the future transmission car market may also have some changes.1 automatic transmission to multi block developmentWith the automatic transmission car quantity rise, automatic transmission technology has evolved from the past traditional simple 4 speed electronic control (3 solenoid valve) to today's 6, 7, 8 (multi speed solenoid valve control) of the fuzzy control and network control logic. In recent years, the trend of increasing the number of automatic transmission is very obvious, from the traditional 4 speed to the 5, 6, 7, speed. Block number increase means that the total transmission ratio in the range widening, and two adjacent block between the transmission ratio and closer, so the shift time will be in advance, and in the launch to ensure the fuel economy, but also meet the acceleration performance. Now, the world's largest automatic transmission manufacturers have launched more than 5 speed multi speed automatic transmission, such as Z F's 6HP series AISIN; AW company U151/U250E,TF-60SN and TR-60SN; JATCO company's J F506E transmission G M company; T40E,6L50/80E etc..2 mechanical structure gradually simplifiedAlthough the new type of transmission block number in the number, but it does not mean that the transmission of the whole structure and volume become complex and increase, this is because of the combination of mechanical components from a large number of shift actuator control multiple planetary gear to achieve a simple 4 1 variable function, the development of today's 5 shift execution the so-called "Laipeilaijie element control type planetary gear set by logic combination can achieve 6 top 1 down transmission function. The number of parts is reduced by half, and the 6hp series reducer produced by ZF is an example (see Figure 7). At present, the German ZF company and Japan AISIN AW company has successfully pushed the 8 speed automatic transmission, but the gear part is still in use for gear, thus we will find outwhether the traditional Simpson series and Lavinia, or today's Laipeilaijie type planetary gear, are composed of "single planetary gear set single row gear and single row double gear" two forms. To this end, as long as we are familiar with the two kinds of planetary gear transmission on the OK, and when we go to analyze the production of different companies 5, 6, 7, block change.3 electronic control humanizationIn the mechanical and hydraulic aspects seem to be more and more simplified structure, less components, valve number is less, but in the overall control of the electronic control method has become more and more complicated, and requires more precise control, especially in the coordinated torque control, safety control, fuzzy logic control, overlapping shift control others of the more obvious. In order to improve the shift quality, reflect the driving comfort, the engine must realize the torque coordinated control of shift process of automatic transmission, the engine is mainly through the instant change of fuel injection quantity and the ignition delay function to maintain a smooth transition in the shift performance of the shift process of automatic transmission; safety protection control mainly refers to the failure of automatic transmission machinery hydraulic, electronic control, and the fault can be a greater threat to the transmission, in order to protect the transmission from further damage, protected by an automatic transmission through the computer receives the sensor information after the start; fuzzy logic control function, it is a microcomputer to imitate human brain function, can predict to the driver's next move, and finally realize the optimum shift time control and shift point switch Such control. Here we focus on understanding the overlapping shift control, this is because many of the maintenance staff is still relatively vague understanding. The so-called overlapping shift control this new words explanation is that shifting process is actually the process of friction friction element, in the common friction clutch and clutch or clutch and brake in the shift, if the friction torque of replacement process will cause improper timing, sharp fluctuations in output torque. The replacement of the friction torque between the two clutches or between the clutch and the brake, there will always be more or less interruption interval or overlap. Overlapping or excessive overlap, will produce undue shift impact. Overlap is the separation of the clutch to be separated too fast oil separation, to be combinedwith the clutch failed to establish sufficient oil pressure, thus the emergence of the two clutch torque transmission phenomenon. In this time of overlap, the output torque is first decreased too much, and then rise sharply, resulting in a larger torque disturbance. At the same time, the engine speed can not get a smooth transition, the first is due to the reduction of load growth, but also because of the rapid increase in load and speed down. Overlap is too much in the combination of the clutch has been able to transmit a lot of torque, the clutch should be separated from the oil separation is not very good, so there are two agencies working at the same time. In a short period of time, the two gears overlap, so that the engine and the output shaft are subject to braking, so the output shaft has a large torque disturbance. Subsequently, the clutch should be separated so that the transmission4 the number of actuators is increasing, and the type of control is changingYou will find that the automatic transmission actuator solenoid valve number increasing, the switch type solenoid valve is less, while the frequency is too much, the number of mechanical valve and control circuit is also less (more solenoid valve control is to improve the quality of the shift). A slide valve may be based on the conversion of the oil to achieve multi-purpose, a simple solenoid valve will be multi-purpose, it can achieve shift control, but also can take charge of oil pressure control. In the past the traditional type of electronic control automatic transmission, switching circuit is switched by shifting the solenoid valve to control the switching circuit, the circuit is a switching type (for shifting actuator junction without excessive vibration, the buffer control circuit is usually used in throttling and storage device to achieve slow control). The actuator in the 6HP series, the 6 has a pulse width modulation solenoid valve features high flow high frequency, 1 of them (E D S5) is mainly used to complete the system pressure regulating function, the other 1 (E D S6) is used to complete the engine and the transmission gearbox mechanical connection function (T C C) and the remaining 4 solenoid valve (E D S1-A, E D S2-B, E D S3-C, E D S4-E/D) respectively control 5 shift actuators of engagement and separation, that is to say the shift circuit controlled by the switch into the original regulation, thus greatly improve the shift quality. Shift control, but also can undertake the oil pressure control. In the past the traditional type of electronic control automatic transmission, switching circuit is switched by shifting thesolenoid valve to control the switching circuit, the circuit is a switching type (for shifting actuator junction without excessive vibration, the buffer control circuit is usually used in throttling and storage device to achieve slow control). The actuator in the 6HP series, the 6 has a pulse width modulation solenoid valve features high flow high frequency, 1 of them (E D S5) is mainly used to complete the system pressure regulating function, the other 1 (E D S6) is used to complete the engine and the transmission gearbox mechanical connection function (T C C) and the remaining 4 solenoid valve (E D S1-A, E D S2-B, E D S3-C, E D S4-E/D) respectively control 5 shift actuators of engagement and separation, that is to say the shift circuit controlled by the switch into the original regulation, thus greatly improve the shift quality.自动变速器发展现状及趋势一、变速器简介1.手动变速器(MT)大家知道,手动变速器是汽车中最常见的变速器之一,其基本原理是用几根平行轴及若干相啮合的直齿或斜齿齿轮进行动力传递,即由输入轴、轴出轴和中间轴构成变速器的主体,再加上一根倒挡轴及同步器等部件。
汽车变速器的设计外文文献翻译、中英文翻译、外文翻译

汽车变速器的设计外文文献翻译、中英文翻译、外文翻译A manual n。
also known as a standard n。
XXX。
It consistsof gears。
synchros。
roller bearings。
shafts。
and gear selectors。
The main clutch assembly is used to engage and disengage the engine from XXX gears are used to select the desired。
and the sector fork moves gears from one to another using the gearshift knob。
Synchros are used to slow the gear to a。
before it is XXX。
The counter shaft holds the gears in place and against the main input and output shaft。
Unlike automatic ns。
XXX。
as there isno XXX。
Note: XXX "n Shifter" was deleted as it had no XXX.)XXX have four to six forward gears and one reverse gear。
However。
some cars may have up to eight forward gears。
while semi trucks XXX by the number of forward gears。
such as a 5-speed standard n.The n of a standard n includes three shafts: the input shaft。
- 1、下载文档前请自行甄别文档内容的完整性,平台不提供额外的编辑、内容补充、找答案等附加服务。
- 2、"仅部分预览"的文档,不可在线预览部分如存在完整性等问题,可反馈申请退款(可完整预览的文档不适用该条件!)。
- 3、如文档侵犯您的权益,请联系客服反馈,我们会尽快为您处理(人工客服工作时间:9:00-18:30)。
外文资料翻译学生姓名:常世鹏专业班级:车辆工程07级5班指导教师:朱天军河北工程大学机电学院2011 年 6 月Dual-clutch transmission technology highlights Transmission technology motor vehicles as a whole is shifting from manual to automatic transmission development, especially at this stage of rapid development of computer technology used in variable-speed transmission system, so that the car automatic transmission technology has been rapid development.In recent years, the automotive automatic transmission there are three main types: mechanical electronic control automatic transmission (AMT), Stepless automatic transmission (CVT) automatic transmission and hydraulic machinery (AT). In the electronically controlled automatic transmission in the field of mechanical, in recent years, there is a new variable-speed transmission, that is, double-clutch automatic transmission speed (Dual Clutch Transmission), due to both inherited and the AMT structure manual transmission easy to install Compact space, light weight, high-efficiency drive, many of the advantages of low manufacturing costs, and the integration of AT under the uninterrupted power, the rapid shift of the good characteristics of a smooth, quickly became the industry's R & DCT will be the new hot spot for a certain On the degree of change to the existing transmission market. In the next few years, the global transmission of light vehicle market will be AT, CVT, and between the DCT.Dual-clutch transmission technology development and application ofthe history of the status quo:Dual-clutch transmission (DCT) to the concept of the 1960s are now history. As early as 1939 in Germany to apply for the Kegresse.A first dual-clutch gearbox of the patent, a manual transmission will be divided into two parts, the design concept, part of the odd file transfer, even another part of the file transfer. And the transmission of power through the linking of the two clutch two input shaft, adjacent to the file of passive gear and the two staggered mesh gear input shaft, with two clutch control can be achieved without cutting off power conversion of the transmission ratio, thus shortening the Shift time, effectively enhance the quality of transmission,The transmission has been carried out in the cargo on board the pilot, was limited to the control of technology, such transmission has not deployed mass production. Then in the 1980s, Porsche is also dedicated to the invention of the car's dual-clutch gearbox (PDK), but it will not DCT technology into mass production.Dual-clutch transmission characteristics of the structure and working processStructural characteristics:Dual-clutch gearbox are built by the clutch set off by the two-device manual transmission based on the three-axis variable-speed gear system, automatic transmission agencies, electronically controlled hydrauliccontrol system. Input shaft assembly by a solid axle shaft and its external sleeve combination of the two-input drive system, odd and even stall the drive gear stalls were arranged in both input shaft. Clutch with a solid input shaft linked to control the odd file, with 2 clutch sleeve (hollow) associated input shaft, and even control file. The two take turns to double- clutch drive system transfer power. The power of the output shaft is the difference between the two, the output shaft to achieve a low profile when the power output, the root of another high-speed shaft and reversing the power output file, the output shaft of the two power transmission and have the final output axis Together, will transfer power to the wheels, in addition Biansuchilun group on the layout did not adopt the traditional layout, Biansuchilun the place is not in accordance with the order of the stalls, so that the two stalls in the adjacent Transmission Gear will no longer share a synchronizer, which is to achieve a seamless transfer of power to provide technical assurance.Process:When the car stalls put up a running start, the odd file to control the input shaft through a clutch, so that the odd file to connect the solid input shaft rotation, a file-synchronization automatically with the low profile of a file output shaft gear mesh, with Low-speed file-axis output. In the low end of the output shaft of a helical gear, helical gear will rely on the power output to the differential, the longer the end to the output shaft. Ina file synchronization and file a gear meshing with the same time, file sync 2 devices are electronically controlled components and under the control of the 2-phase meshing gears file, in the work of stand-by status.2 files look at the power transmission line, when the transmission linked to a file, even control the input shaft of the gear clutch 2 is separated, so at this time in the engine and disconnect the power completely, even at this time to connect the sets of files Cylinder (hollow) input shaft 2, although the files will be driven by the gear rotation, but it is entirely in the other with the odd file with the gears turning, no power output only for the next file or prepared to do . Therefore, even stall the input shaft will not enter the file on the odd-numbered axle of the interference caused by power, high-speed file will follow the output shaft rotation, but also in a state of idling, there is no power output, so there is no power output The occurrence of any power to interfere with each other. 2 files into the transmission, when the clutch down a file from a file at the same time, clutch 2 connection, put up 2 files at the same time,3 and file in advance, so for the work carried out so that in gearbox into the file and pick Did not file space. Therefore, DCT transmission in the course of the work always is a combination of 2 stalls, is a work, and the other to prepare for the next step. Even the control file in the clutch ECU control, and engine power output, control input file odd-numbered axle of the clutch and engine output disconnect, it completed the input shaft of the power switch,the process, Clutch two entirely at the same time, and no longer as the traditional single-clutch gearbox, clutch and engine in the power output disconnect, there will be power interruption. At the conclusion of the second gear power switch at the same time, control of third gear synchronizer will be in control of the electronic control components, and third gear box Biansuchilun mesh, so that the third gear transmission gear on standby. In addition to the file or when, DSG will stall at a higher state of readiness, speeding in the file, the file can also be reduced for the realization of standby time to speed up the files decline.As the DCT is based on the axis parallel to the development of the manual transmission, it inherited the manual transmission in the transmission efficiency, space for the installation of compact, light weight, low prices at the same time, but also has automatic transmission and shift quality start Good character, have broad prospects for development and promote the use of significant advantages, mainly in the following areas: DCT is almost free from restrictions on transfer of power can be widely used in a variety of vehicles. DCT's production costs low. As the DCT is based on the manual transmission from the development of power transmission is still relying on the clutch and gear, the complexity of the low gear of the domestic parts and components manufacturers more mature technology, most of the transmission manufacturer has some technical basis. DCT for the development of technology to provide theconditions. DCT's production through the existing file manual transmission lines will be used to transform a little, so for the manual transmission plant product upgrade cycle short, fewer new investments, production of a good inheritance. As the transmission needs of a wide range, DCT technology (ten technical gear automatic transmission technology) application will not only be limited to automotive transmission, transport machinery in other industries, can produce the same effect of the application. China's automobile industry started relatively late, at this stage of the production line has more to the production of manual transmission file-based, in the automatic transmission is in a high growth period, the domestic automotive automatic transmission in the mainly rely on imports, the development of products that improve the DCT China's self-developed automatic transmission capacity will certainly have a positive role in promoting. At the same time, and also to adapt our industrial base.汽车变速系统技术研究汽车变速系统技术整体上是由手动换档向自动换档发展,尤其是现阶段高速发展的计算机技术应用于换档变速系统,使汽车自动变速技术得到了快速的发展。