价值流程图VSM案例分析精品PPT课件
VSM价值流管理(PPT100页)名家精品课件

1.思維迷思 2.設計能力 3.計畫與
不足
管理不當
38
為何流動/快不起來?
思維迷思
-農耕心態 -追求利潤
最大化
設計能力 不足
-職能切割 -工程切割 -防坡堤設計 -分批-等待模式 -訂單/計畫的
不穩定 -轉換時間長 -物與情報
被切斷
計畫與管理 不當
-PMC中央管控 -預測式需求 -人為的不穩定 -不良多
• 傳統心理學研究: 找出不快樂的原因;給予消除
• 但,不滿足沒有不滿=/ 滿足 • 去除不滿足;並沒有得到滿足 • 因此,另外做不同的研究
46
如何才能快樂?
• 花25年對幾千人做研究 • 每人配帶call機 • 隨機響;就記下當時的作為與感受
• Flow:暢快;
順暢&爽快才能快樂
47
如何才能flow順暢?
11.開到 修理廠
消費時間:210分鐘
創造價值的時間:58分鐘
12.排隊、 描述問題
13.等候 借用車
14.委託 修理
創造價值的時間/總時間:28%
15分鍾
15.排除、 付款
20分鍾
16.駕車 回家
34
為何流動/快不起來 ?
35
價值流管理VSM
• 強調價值要快速流動
• 首先,要把沒有價值的去除: -以客戶角度定義價值 -給予價值最大化
• 搭配一個現場管理試驗,啟發思考 • 如何完成VSM的分析,不在此次課程
15
一.為何要做VSM 價值流管理?
常見老板的二大抱怨
• 交期長;又不準時 • 不要用的,一大堆; 要用的.卻沒有
17
為何要推動VSM?
1. 快速掌握企業經營系統 2. 全面瞭解企業的問題 3. 清析的瞭解瓶頸工程所在 4. 設備與人力配置研判 5. 日常管理執行與落實方向指引 6. 成為流程改善工具 7. 讓改善內容明確化與明確優先順序 8. 做為內外部的溝通工具
VSM价值流程图(共75张PPT)
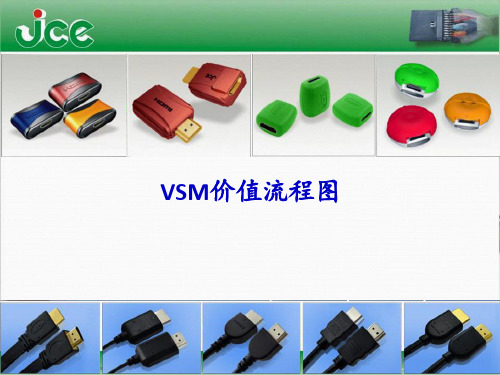
an unstable production process makes effective problem solving difficult, if not
impossible
*不稳定生产制程迫使危机管理取代了策略领导
an uncrisis management instead of strategic
5)How——简单说明价值流图析的应用方法。
价值流程图分析常见的七种工具
1.流程活动图(Process Activity Mapping)。 起源: 工业工程。 2.供应链反应矩阵(Supply Chain Response Matrix)。 起源: 时间加速与后勤学。 3.生产多样性漏斗(Production Variety Funnel)。 起源: 运营管理。 4.质量过滤图(Quality Filter Mapping)。 5.需求扩大图(Demand Amplification Mapping)。 起源: 系统动力学。 6.决策点分析(Decision Point Analysis)。 起源: 有效消费者反应/物流学。 7.物理结构图(Physical Structure Mapping)。
并有利于对生产流程进行指导,朝向理想化方向发展。
什么是价值流
所谓价值流,是当前产品通过其基本生产过程所要求的全部活动。这些活动包括 给产品增加价值
和不增加价值两部分,包括了从产品最基本的原材料阶段一直到产品 交付顾客的全部过程,如一辆汽车的制造, 包括了从顾客要求到概念设计、产品设计、 样车制造、试验、定型、投产到交付后的使用、信息反馈和回收过程,
➢ 顾客需求节拍应根据实际供货的历史加以修正。
➢ 顾客拉动和成品仓库发货拉动两种方式实际上都是由顾客需求拉动的,关键区别在 于是否
价值流图VSM绘图教程ppt课件

精益改善 线平衡 Line/Operator Balance
线平衡率 =
Σ(各工序作业时间) 瓶颈岗位时间 ∗ 人数
线平衡是指工程流动间或者工序流动间 负荷之差最小、流动顺畅、减少因时间差所造成的等待或滞留现象。
精益知识点 拉式生产、看板
物料员/水蜘蛛到上游超市取走需要的半成品, 提取生产看板,向上游工序发出生产指令,即生产拉动信号。
2. 连续流的多工序也可用一个工序表示
3. 物料流应按照工序从左向右绘制 而不是按照工厂的实际布局
4. 在车间沿物料流走一遍, 需要收集一些必要的、可以帮助 绘制未来状态图的数据, 并记录在数据箱中
• 周期时间 • 增值时间 • 设备开机率 • 工作时间 • 库存
• 员工数量 • 产品种类 • 良品率 • 换模时间 • 生产批次间隔(EPE)
感谢您的聆听
22
价值活动
任何增加市场或产品和服务的功能或市场形式的活动 (客户愿意为此付费的活动)
无增值活动
任何不增加市场或产品和服务的功能 (这些活动应当消除,简化,减少或合并)
优点: • 看到全流程,而不是单个工序 • 发现浪费并找到浪费的源头 • 同时体现信息流和物料流
• 材料入库 • 来料检查 • 库存 • 物料搬运
价值流图绘图教程
季正勇
目录
01
价值流图
02Leabharlann VSM图标03绘制现状图
04
绘制未来图
价值流图VSM
价值流程图(Value Stream Mapping,VSM)是丰田精益制 造(Lean Manufacturing)生产系统框架下的一种用来描述 物流和信息流的形象化工具。
VSM形象化地从系统层面观察生产过程中的物流和信息流, 发现浪费并制定相应的改善计划。
VSM价值流分析PPT课件
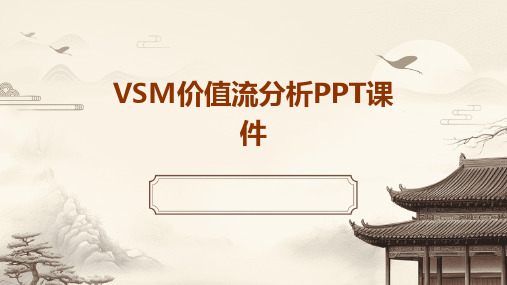
生产线平衡率计算
生产线平衡率 = 各工序时间总和 / ( 最长工序时间 * 工序数) * 100%。
提高设备利用率和员工工作效率,减 少在制品库存和等待时间,提高产品 质量和客户满意度。
生产线平衡方法
工序时间测定
通过秒表测时、预定时间标准等方法 ,准确测定各工序所需时间。
瓶颈工序识别
找出生产线上耗时最长的工序,即瓶 颈工序,进行重点改善。
02
收集数据
收集生产过程中的相关数据,如生产 周期、在制品数量、不良品率等。
01
03
绘制价值流图
使用标准的符号和工具绘制价值流图 ,包括流程图、数制定相应的改进计划, 包括优化生产布局、减少批量大小、 改进质量控制方法等。
05
04
分析浪费
在价值流图中标识出浪费的环节和原 因,如等待、运输、不良品等。
作业改善
通过作业分析、动作研究等方法,对 瓶颈工序进行作业改善,提高生产效 率。
生产线调整
根据改善后的工序时间,对生产线进 行调整,使各工序时间与节拍相等或 成整数倍关系。
改善措施制定
目标设定
原因分析
根据生产线平衡率和企业实际情况,设定 合理的改善目标。
针对生产线不平衡的原因进行深入分析, 找出根本原因。
收集生产过程中的相关 数据,通过统计分析识
别浪费现象。
员工参与法
鼓励员工积极参与,提 出生产过程中的浪费问
题和改进建议。
改善机会挖掘
01
02
03
04
消除浪费环节
针对识别出的浪费现象,制定 相应的改善措施,消除浪费环
节。
优化生产流程
通过改进生产工艺、调整设备 布局等方式,优化生产流程,
价值流图分析(PPT 59张)

—查找和发现浪费的-mail:lgddyangwenku@
价值流图分析 VSM
目的
了解价值流分析的作用
掌握绘制价值流图的步骤 加深对精益思想的理解
价值流图分析 VSM
主要内容
第一部分 价值流分析基础知识 第二部分 价值流图的绘制步骤 第三部分 价值流分析的作用 作业
采用5W1H方法
1. Who——确定谁来做 需要一位了解产品价值流而且能推进其改进的人,这个人具有领导职责 (价值流经理),由他来领导一个小组进行价值流图析工作。 2. What——确定做哪些产品的价值流图析(正确选择确定物流) 通常我们首先按照80—20原则,对影响企业最大的产品进行图析。 3. When——确定何时做(正确选择确定物流) 应在实施改进之前对价值流进行分析,以确定应首先改进哪些过程。 4. Where——确定在哪里做(如何获取真实、正确的数据信息) 在现场!只有在现场收集的数据才能真正反映价值流的状况。 5.Why—为什么做价值流图析 明确价值,消除浪费 6、 How ——进行图析
价值流图分析 VSM
价值流图基本概述
价值流图分析 VSM
价值流图基本概述
价值流图与流程图区别
价值流图: • 让所有人看见整体 情况 • 根据真实数据 • 改善蓝图 • 持续改善 流程图: • 只能反映局部工艺 周期、流程 • 根据工程标准或旧 数据 • 一年一次的大计划
价值流图分析 VSM
价值流图析步骤
(以前的认识是我们创造了产品的价值,并且由此确定了其价值。)
总之,永远站在客户立场上看待我们的工作价 值。谁对我们的工作进行最终评判和衡量,谁就是 我们的客户。 客户—我们从事一切生产经营活动并进行改善的最根本的出发点和落脚点
2024版价值流程图VSM案例分析PPT课件

价值流程图VSM案例分析PPT课件目录•引言•案例分析:某制造企业生产流程优化•案例分析:某电商平台订单处理流程改进•案例分析:某医院患者就诊流程优化•总结与展望01引言提高生产效率降低成本提升产品质量目的和背景通过价值流程图VSM分析,识别生产过程中的浪费环节,优化生产流程,提高生产效率。
减少生产过程中的非增值活动,降低生产成本,提高企业竞争力。
通过价值流程图VSM分析,发现生产过程中的问题点,改进生产工艺,提升产品质量。
价值流程图VSM简介定义价值流程图VSM是一种可视化工具,用于描述产品或服务的整个价值流,包括从原材料到最终产品或服务的所有活动。
作用帮助企业识别生产过程中的浪费环节,优化生产流程,提高生产效率和质量。
适用范围适用于制造业、服务业等各个领域的企业。
02案例分析:某制造企业生产流程优化当前生产流程存在过多的环节和等待时间,导致生产效率低下。
生产流程繁琐资源浪费严重质量问题突出生产过程中的物料、人力和时间等资源未能得到充分利用,造成资源浪费。
产品质量不稳定,客户投诉率高,影响企业声誉和市场竞争力。
030201企业现状及问题分析深入企业生产现场,全面了解现有生产流程、设备、人员配置等情况。
流程调研收集生产过程中的关键数据,如生产周期、在制品数量、设备利用率等。
数据收集基于调研和收集的数据,绘制价值流程图VSM ,直观展示生产过程中的价值流动情况。
VSM 绘制价值流程图VSM 构建识别并消除生产过程中的浪费环节,如减少等待时间、降低库存等。
消除浪费优化生产流程,合并或取消不必要的环节,提高生产效率。
简化流程加强产品质量控制,采用先进的质量管理方法和技术手段,提高产品质量稳定性。
强化质量控制生产流程优化方案设计01020304生产效率提升资源利用率提高产品质量改善企业竞争力增强实施效果评估通过优化生产流程,提高生产效率,缩短生产周期。
充分利用物料、人力和时间等资源,降低生产成本。
通过生产流程优化,提高企业市场竞争力,实现可持续发展。
VSM价值流程图精品PPT课件

VSM Tools 绘制价值流分析图所需工具
Manufacturing Process
Scrap
Kaizen闪光点/ 爆炸点
外部资源/ 客户
数据盒
I
库存
o oo
卡车运输
成品至客户
缓冲区/ 安全库存
手工的 信息流 Electronic Information Flow
Production Kanban
• Ties together lean concepts and techniques helps avoid cherry-picking 结合精益的概念与技术…避免“只挑容易的” 来改进
• Forms the basis of an implementation plan 形成实施计划的基础
• Describes what you are actually going to do to affect the quantitative data 描绘为了影响这些定量的数据,应该做些什么
两班生产
冲压
I
焊接 #1
焊接 #2
装配 #1
装配 #2
I
I
I
I
I
MCT =23.5 Days
VA = 188 Sec
信息收集—顾客信息:
➢发货频次 ➢发货量 ➢需求信息来源
➢发货方式 ➢顾客装配班次 ➢顾客休息日
信息收集—原材料/成品信息:
原材料信息 ➢ 库存量 ➢ 供应商性质 ➢ 采购周期 ➢ 信息交流方式 ➢ 发货方式 ➢ 发货量
价值流图 V alue Stream
M apping
防错 M istake P ro o fin g
全面设备维护 T o ta l
价值流程图(VSM)案例分析27页PPT
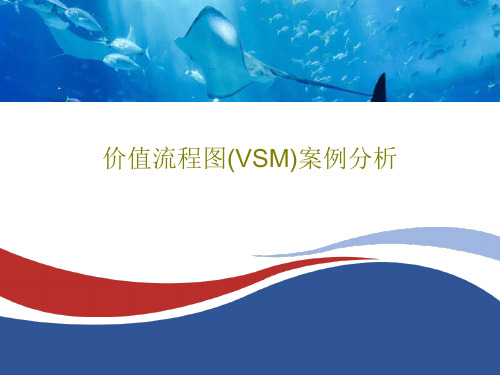
价值流程图 价值流程图( Value stream mapping,WSM)是丰 田精益制造( Learn Manufacturing)生产系统框架 的一种用来描述物流和信息流的形象化工具。目的是 为了辨识和减少生产过程中的浪费,并用于说明生产 过程中所减少的“浪费”总量。 VSM对生产制造过程中的周期时间、待机时间、在 制品库存、原材料流动、信息流动等情况进行描摹和 记录,有助于形象化当前流程的活动状态,并有利于 对生产流程进行指导,朝向理想化方向发展。 VSM通常包括对“当前状态”和“未来状态”两 状态的描摹
价值流程图
主要容 价值流概念 二、价值流程图 三、价值流程图案例分析
、价值流的概念 价值流是制造产品所需一切活动的总和,包含了增 值活动和不增值活动。 使用价值流分析意味着对全过程进行研究,而不 只是研究单个过程;改进全过程,而不是仅仅优化局 部 据统计,增值活动约占企业生产和经营活动的5%, 不增值活动约占95%。因此,应在价值流中识别不增 值活动,通过持续不断地开展价值流改进,消除各种 浪费,降低成本。 价值流改进重点在于物流和信息流。
VSM分析的两个流程 第一个是信息流程,即从市场部接到客户订单或市场部预测 客户的需求开始,到使之变成采购计划和生产计划的过程 第二个是实物流程,即从供应商供应原材料入库开始,随后 出库制造、成品入库、产品出库,直至产品送达客户手中的过 程。此外,实物流程中还包括产品的检验、停放等环节。 企业在进行VSM分析时,首先要挑选出典型的产品作为深入 调查分析的对象,从而绘制出信息流程和实物流程的现状图, 然后将现状图与信息和实物流程的理想状况图相比较,发现当 前组织生产过程中存在的问题点,进而针对问题点提出改进措 施
ቤተ መጻሕፍቲ ባይዱ
- 1、下载文档前请自行甄别文档内容的完整性,平台不提供额外的编辑、内容补充、找答案等附加服务。
- 2、"仅部分预览"的文档,不可在线预览部分如存在完整性等问题,可反馈申请退款(可完整预览的文档不适用该条件!)。
- 3、如文档侵犯您的权益,请联系客服反馈,我们会尽快为您处理(人工客服工作时间:9:00-18:30)。
设备布置也应作相应调整,具体布置如图所示
未来价值流程图
需要注意的是,由于钻孔、精车抛光、检验三道工序是2个 人在U形生产线中完成的,如采用逐兔式完成,因此每人115s完 成三道工序的生产即115s共完成两个工件的加工,同时粗车工 人120s完成两个毛坯加工,因此相当于U形生产线中57.5s完成 一个零件的加工。因此,图3-2中后面三道工序的加工周期标注 57.5s。
(2) 过分加工的浪费 (6)制造过多/过早的浪费
(3) 动作的浪费
(7)等待的浪费
(4) 搬运的浪费
(8)管理的浪费
价值流程图分析特征
价值流程图分析以客户的观点分析现有价值流程图 每一个活动的必要性,画出期待的价值流的未来状态 图,并制定实施计划。
(1)绘制出并简单显示出物流和信息流 (2)揭示产生浪费的原因 (3)创建一个改善的价值流 (4)创建和协调一个跨部门团队方法
供应商
信息流 生产控制
每周计划
粗车 1
无价值
有价值
钻孔 1
精车、抛光 1
物料流
客户
VSM分析的对象
VSM分析的主旨是暴露存在的浪费问题,并彻底排 除浪费。在JIT 生产方式中,凡是超出增加产品价值 所绝对必需的最少量的物料、设备、人力、场地和时 间的部分都是浪费。
VSM分析关注的八大浪费包括:
(1) 不良/ 修理的浪费 (5)库存的浪费
价值流程图
主要内容
一、价值流概念 二、价值流程图 三、价值流程图案例分析
一、价值流的概念
价值流是制造产品所需一切活动的总和,包含了增 值活动和不增值活动。
使用价值流分析意味着对全过程进行研究,而不 只是研究单个过程;改进全过程,而不是仅仅优化局 部。
据统计,增值活动约占企业生产和经营活动的5%, 不增值活动约占95%。因此,应在价值流中识别不增 值活动,通过持续不断地开展价值流改进,消除各种 浪费,降低成本。
价值流改进重点在于物流和信息流。
二、价值流程图
价值流程图(Value Stream Mapping,VSM)是丰 田精益制造(Learn Manufacturing)生产系统框架下 的一种用来描述物流和信息流的形象化工具。目的是 为了辨识和减少生产过程中的浪费,并用于说明生产 过程中所减少的“浪费”总量。
VSM对生产制造过程中的周期时间、待机时间、在 制品库存、原材料流动、信息流动等情况进行描摹和 记录,有助于形象化当前流程的活动状态,并有利于 对生产流程进行指导,朝向理想化方向发展。
VSM通常包括对“当前状态”和“未来状态”两个 状态的描摹。
VSM分析的两个流程
第一个是信息流程,即从市场部接到客户订单或市场部预测 客户的需求开始,到使之变成采购计划和生产计划的过程;
粗车工序零件毛坯库存储备天数=350/700=0.5(天)
粗车和钻孔工序间库存储备天数=175/700=0.25(天)
同理依次计算出各工序间库存储备天数,并绘制出当前价 值流程图
绘制当前价值流程图
当前价值流程图
分析当前价值流程图
装配工位每天对该零件的需求量为700件,且其与车间和原 料、半成品仓库均实行两班制,每班有效时间25200s,使用率 100%,因此
第二个是实物流程,即从供应商供应原材料入库开始,随后 出库制造、成品入库、产品出库,直至产品送达客户手中的过 程。此外,实物流程中还包括产品的检验、停放等环节。
企业在进行VSM分析时,首先要挑选出典型的产品作为深入 调查分析的对象,从而绘制出信息流程和实物流程的现状图, 然后将现状图与信息和实物流程的理想状况图相比较,发现当 前组织生产过程中存在的问题点,进而针对问题点提出改进措 施。
三、价值流程图案例分析粗车钻孔精车、抛光检验
物料搬运由1个专人负责,搬运设备为手推车。搬运工 每班从仓库向车间搬运一次毛坯,从车间向装配工位搬运 两次成品零件。装配工位每天对该零件的需求为700件,每 料盘25件,并把他们的每月预测和每日需求信息发给车间 调度部门。
车间调度部门把每周计划下发给零件加工车间各工位和搬 运工,此外,将其每月预测和每周计划信息发给原料、半成品 仓库。粗车工位零件毛坯在制品库存为350件,以后三道工序在 制品库存以及零件成品在制品库存均为175件。
目前生产中钻孔和检验工序生产能力得不到发挥,存在很大 浪费。因此,可以考虑减少一个作业者。因为钻孔和检验总共 用时35s+25s=60s,可以考虑将这两道工序合并。
同时,可以考虑采用流水线生产和拉式生产相结合的生产 和管理方式。因为这样不仅有利于减少在制品库存,缩短提前 期,也非常有利于对装配工位需求的响应。此外,由于定拍工 序粗车节拍为60s,采取拉式生产有利于为减少生产过多过早的浪 费。
价值流程图分析的好处
(1)目视化工具 (2)信息沟通方式 (3)有利于发现存在的问题 (4)创建一个改善的价值流
价值流程图分析步骤
选择一个 产品
从头到位聚焦一个产品、过 程或服务,搜集相关数据
分析当前问题: 信息、物料、交互
设计一个精益价值流 建立想要达到的理想状态
计划和实施
实施计划,达到的理想状态
因此,目前生产单位零件的生产过程时间过长,也就是说 生产提前期过长,这会造成生产响应需求的能力降低,不利于 企业竞争。
其次,各工序间在制品库存最小库存储备天数为0.25天,即
0.25x25200x2/60=210(min),很明显在制品库存水平过高,会 造成在制品库存的浪费。
此外,各工序作业统一由车间调度部门调度,各工序间实 行推动式生产,不利于及时响应需求的变化和减少在制品库存 。
各工序作业节拍分析
容易看出,车间加工时间最长的工序粗车时间为60s<72s, 因此目前生产会造成制造过多、过早的浪费。
各工序生产还不平衡,易造成等待浪费。
该零件加工周期=60+35+55+25=175(s),一个零件的生产 加工时间(包括物流等时间)即生产提前期 =0.5+0.25+0.25+0.25+0.25=1.5(天)。因此
存在的问题
(1)目前生产会造成制造过多、过早的浪费; (2)各工序生产还不平衡,易造成等待浪费; (3)生产提前期过长,这会造成生产响应需求的能力降低,不利
于企业竞争; (4)在制品库存水平高,会造成在制品库存的浪费; (5)实行推动式生产,不利于及时响应需求的变化和减少在制品
库存。
改进方案设想