连续浸出车间操作手册
浸出工序操作规程

浸出车间作业指导书一.工艺流程溶剂周转库→溶剂油—↑﹉﹉﹉﹉﹉﹉﹉﹉﹉﹉∣↓混合油→盐析灌→混合油灌→一长蒸发器→二长蒸发器→∣预榨饼→存料箱→平转浸出器→∣湿粕→蒸脱机→成品粕→粕库→灌包计量∣↓∣(接二长蒸发器)→汽提塔→浸出毛油→炼油车间混合气体→平衡灌→冷冻回收————→排空→冷凝器→↓溶剂液体————→分水箱→溶剂周转库→去平转浸出器二、主要设备的技术参数和技术要求1.存料箱作用:①暂存一部分饼,保证对浸出器进料绞龙和浸出格连续稳定地供料,使进料绞龙能起有效的料封作用和使各浸出格装料稳定均匀;②靠自身的料层起料封作用,阻止浸出器的溶剂气体通过一刮板、存料箱而进入预榨车间或外溢。
技术参数要求:存料箱装料容积应不小于浸出格装料量的1.5倍,装料高度应不低于1.4m,本工艺要求不低于1.8m;低于0.8m应停止向平转投料。
⒉平转浸出器平转浸出器含本体、料封绞龙、混合油过滤器、大喷淋罐、混合油循环泵。
⑴平转浸出器规格型号:SMJP650B;设计产量350吨/天,内有料格24个。
为无假底固定不锈钢栅板,料格最大装料体积(扣除25cm高度)为2.27m3⑵料封绞龙主要作用:通过绞龙出料端的一段密封段(40㎝左右的长度没有绞龙叶片),阻止平转内溶剂气体带到一号刮板进入存料箱,密封段是料出口处一段距离没有绞龙叶,最后面的叶片将物料推到此处,压缩成料柱状,有效地阻断浸出器气体外串。
通常料封段长度视物料的容量、颗粒大小情况而定,预榨饼料封长度一般为绞龙直径的1.5—2倍,湿粕可以在0.8—1.5倍。
⑶混合油过滤器此设备装在平转浸出器上方,外筒尺寸为φ1000×2050,滤筒尺寸为850×1260,目前配备的筛网为60目/时,生产菜籽时应配备80—100目/时为宜。
混合油通过2#泵连续不断地泵入过滤器,经过滤器过滤后的混合油进入混合油盐析罐,滤渣人工排入平转料格。
⑷大喷淋贮罐连续小喷淋由于不适于湿粕的沥干和粕残油的降低,目前正逐步被间歇大喷淋所取代。
连续浸出车间操作手册

迪斯美连续溶剂浸出车间操作手册广州植之元油脂实业有限公司目录1.概述2.工艺介绍和操作要求2.1.原料和公用设施要求2.2.浸出工段2.3.蒸脱工段(脱溶、干燥和冷却)2.4.混合油蒸发和回收工段2.5.矿物油吸收工段2.6.溶剂收集工段2.7.脱胶工段2.8.自动安全控制装置3.浸出车间开车操作3.1.开车3.2.启动浸出工段3.3.启动混合油蒸发工段3.4.启动蒸脱工段4.操作状况的检查4.1.浸出器4.2.蒸发工段4.3.矿物油吸收系统4.4.脱溶工段4.5.溶剂规格4.6.吸收油的规格4.7.工艺设计参数5.短期停车(浸出器带料停车)5.1.浸出器停车5.2.DTDC的停车5.3.停止混合油蒸发工段5.4.停止矿物油吸收系统6.车间长期停车(把浸出器内的料走空)6.1.把浸出器内的料走空,并停止浸出器6.2.停止蒸脱工段6.3.停止混合油蒸发工段6.4.停止矿物油吸收系统7.脱溶烤粕机70S/或13SDC之后的输送设备突然停止运转后的操作8.安全措施8.1.电源故障8.2.蒸汽压力故障8.3.冷却水故障8.4.注意事项8.5.紧急停车9.设备介绍9.1.斜刮板1A9.2.插板阀8A/B9.3.密封绞龙8A/A9.4.浸出器进料斗29.5.浸出器39.6.浸出器出料斗49.7.斜刮板59.8.密封绞龙8B9.9.密封绞龙8C9.10.旋转阀8D/A1-8D/A2-8D/B 9.11.斜刮板99.12.绞龙10B/刮板10A9.13.沙克龙14A1/14A29.14.刹克龙14B9.15.混合油罐179.16.二蒸18A9.17.汽提塔18B/229.18.真空冷凝器19/239.19.溶剂预热器199.20.冷凝器20B/C9.21.最后冷凝器20D9.22.分水罐和溶剂周转罐32A/B-34 9.23.离心风机36A1/36A29.24.风机36B9.25.离心风机36V9.26.蒸汽喷射泵9.27.废水蒸煮罐459.28.泵589.29.节能器/一蒸60A和闪蒸器60B 9.30.控制阀629.31.脱溶烤粕机70S9.32.干燥冷却机13SDC9.33.热风加热器94A1/94A29.34.矿物油吸收塔1209.35.吸收油换热器181A,181B,180 9.36.解析塔1229.37.尾气风机1369.38.毛油暂存罐5019.39.脱胶反应罐5039.40.油干燥器506A/B9.41.离心机5189.42.油加热器5219.43.油油换热器581A9.44.油冷却器581B/581C9.45.油脚罐582L10.浸出器和DT消溶1.概述总体来说,油籽经过适当的预处理,再通过浸出得到毛油和粕。
浸出车间操作规程
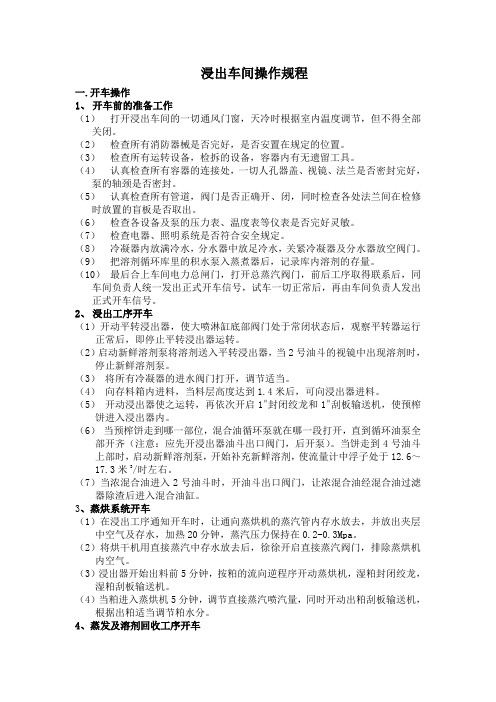
浸出车间操作规程一.开车操作1、开车前的准备工作(1)打开浸出车间的一切通风门窗,天冷时根据室内温度调节,但不得全部关闭。
(2)检查所有消防器械是否完好,是否安置在规定的位置。
(3)检查所有运转设备,检拆的设备,容器内有无遗留工具。
(4)认真检查所有容器的连接处,一切人孔器盖、视镜、法兰是否密封完好,泵的轴颈是否密封。
(5)认真检查所有管道,阀门是否正确开、闭,同时检查各处法兰间在检修时放置的盲板是否取出。
(6)检查各设备及泵的压力表、温度表等仪表是否完好灵敏。
(7)检查电器、照明系统是否符合安全规定。
(8)冷凝器内放满冷水,分水器中放足冷水,关紧冷凝器及分水器放空阀门。
(9)把溶剂循环库里的积水泵入蒸煮器后,记录库内溶剂的存量。
(10)最后合上车间电力总闸门,打开总蒸汽阀门,前后工序取得联系后,同车间负责人统一发出正式开车信号,试车一切正常后,再由车间负责人发出正式开车信号。
2、浸出工序开车(1)开动平转浸出器,使大喷淋缸底部阀门处于常闭状态后,观察平转器运行正常后,即停止平转浸出器运转。
(2)启动新鲜溶剂泵将溶剂送入平转浸出器,当2号油斗的视镜中出现溶剂时,停止新鲜溶剂泵。
(3)将所有冷凝器的进水阀门打开,调节适当。
(4)向存料箱内进料,当料层高度达到1.4米后,可向浸出器进料。
(5)开动浸出器使之运转,再依次开启1#封闭绞龙和1#刮板输送机,使预榨饼进入浸出器内。
(6)当预榨饼走到哪一部位,混合油循环泵就在哪一段打开,直到循环油泵全部开齐(注意:应先开浸出器油斗出口阀门,后开泵)。
当饼走到4号油斗上部时,启动新鲜溶剂泵,开始补充新鲜溶剂,使流量计中浮子处于12.6~17.3米3/时左右。
(7)当浓混合油进入2号油斗时,开油斗出口阀门,让浓混合油经混合油过滤器除渣后进入混合油缸。
3、蒸烘系统开车(1)在浸出工序通知开车时,让通向蒸烘机的蒸汽管内存水放去,并放出夹层中空气及存水,加热20分钟,蒸汽压力保持在0.2-0.3Mpa。
浸出车间作业指导书

连浸岗位作业指导书(1)、随时与磨矿岗位联系,及时调整下矿量及流量,保证液固比5-6:1,单槽反应时间45min和生产顺利进行;(2)、每班至少取2—4次球磨矿浆,保证磨矿粒度(80目),保证浸出率;(3)、随时用PH试纸检查各槽PH值(1#桶:1.5 2#桶:1.5-2.0 3#桶:3.6-3.8 4#桶:5.0 5#桶:5.2-5.4),及时调整加酸量;(4)、每槽每班必须检查温度4次(保证温度75—85℃),随时与锅炉房联系,及时调整(加煤量)用汽量;(5)、每班每两小时取样分析Zn:100-120g/L Fe≤15mg/L SiO≤0.3g/L及时2调整浸出温度酸度与锰粉的加入量;(6)保证出口阀门及溜槽畅通无阻。
中性浸出岗位作业指导书(可)(1)、每班取一个焙烧样送化验室,分析:Zn Zn(可) S(不) SiO2Fe Fe(可) Pb As Sb Ge(2)、按中浸操作条件,加入中性浸出槽内焙烧,并根据酸度的变化调整加料量;(3)、每桶保证进液2/3以上体积方可启动搅拌并开启蒸汽阀;(4)、与各工序及岗位随时联系,掌握原料及上清液变化情况,及时调整浸出技术条件,保证中上清产量、质量(浸出液化学成分:(g/l)Fe≯0.02 As≯0.007S b≯0.007。
);(5)、随时用PH值试纸检查酸度,及时调整加料量(浸出终点PH值:5.0-5.2 浸出液固比:8-12:1 浸出时间:120-180min);(6)、每槽中性浸出必须检查温度2-4次,保证浸出温度60-70℃;(7)、每桶保证进液2/3以上体积方可启动搅拌并开启蒸汽阀;(8)、保证出口阀门及溜槽畅通无阻。
1。
浸出车间操作规程
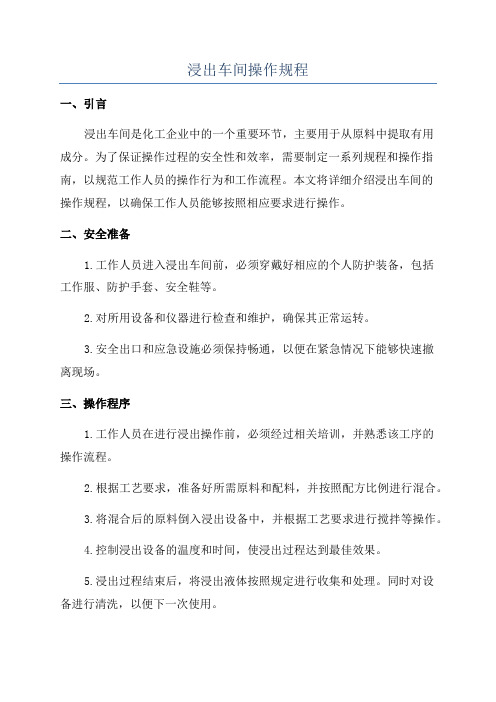
浸出车间操作规程一、引言浸出车间是化工企业中的一个重要环节,主要用于从原料中提取有用成分。
为了保证操作过程的安全性和效率,需要制定一系列规程和操作指南,以规范工作人员的操作行为和工作流程。
本文将详细介绍浸出车间的操作规程,以确保工作人员能够按照相应要求进行操作。
二、安全准备1.工作人员进入浸出车间前,必须穿戴好相应的个人防护装备,包括工作服、防护手套、安全鞋等。
2.对所用设备和仪器进行检查和维护,确保其正常运转。
3.安全出口和应急设施必须保持畅通,以便在紧急情况下能够快速撤离现场。
三、操作程序1.工作人员在进行浸出操作前,必须经过相关培训,并熟悉该工序的操作流程。
2.根据工艺要求,准备好所需原料和配料,并按照配方比例进行混合。
3.将混合后的原料倒入浸出设备中,并根据工艺要求进行搅拌等操作。
4.控制浸出设备的温度和时间,使浸出过程达到最佳效果。
5.浸出过程结束后,将浸出液体按照规定进行收集和处理。
同时对设备进行清洗,以便下一次使用。
四、操作注意事项1.操作人员必须经过岗位培训,熟悉设备的操作和相关安全规定。
2.严禁擅自更改工艺参数,必须按照工艺要求进行操作。
3.遵循安全操作规程,不能违反相关操作规定和安全管理制度。
4.起动和关闭设备时必须按照操作步骤进行,严禁操作错误和疏忽大意。
5.浸出设备周围必须保持整洁,禁止杂物堆积和火种聚集。
6.当设备出现异常情况时,必须立即停止操作,并及时汇报相关人员进行处理。
五、事故应急处理1.在操作过程中,如出现火灾、泄漏等事故,必须立即采取紧急措施,确保人员安全和设备不受损坏。
2.当事故发生时,及时报警并启动应急预案,安排人员进行紧急疏散和事故处理。
3.对事故现场进行封锁和隔离,并进行相应的处置和清理。
六、设备维护与保养1.定期对浸出设备进行检查,确保设备的正常运转和安全性。
2.清洗和保养设备,防止杂质和腐蚀物的堆积。
3.对设备进行定期维护和保养,包括润滑、紧固等工作,确保设备的可靠性和使用寿命。
浸出车间设备操作规程
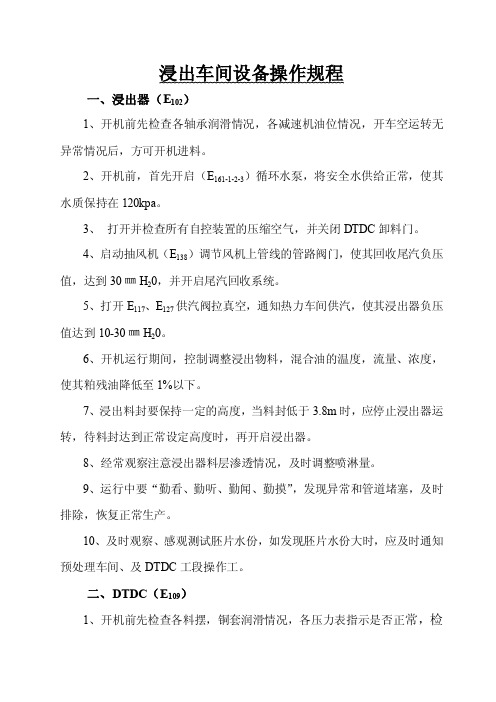
浸出车间设备操作规程一、浸出器(E102)1、开机前先检查各轴承润滑情况,各减速机油位情况,开车空运转无异常情况后,方可开机进料。
2、开机前,首先开启(E161-1-2-3)循环水泵,将安全水供给正常,使其水质保持在120kpa。
3、打开并检查所有自控装置的压缩空气,并关闭DTDC卸料门。
4、启动抽风机(E138)调节风机上管线的管路阀门,使其回收尾汽负压值,达到30㎜H20,并开启尾汽回收系统。
5、打开E117、E127供汽阀拉真空,通知热力车间供汽,使其浸出器负压值达到10-30㎜H20。
6、开机运行期间,控制调整浸出物料,混合油的温度,流量、浓度,使其粕残油降低至1%以下。
7、浸出料封要保持一定的高度,当料封低于3.8m时,应停止浸出器运转,待料封达到正常设定高度时,再开启浸出器。
8、经常观察注意浸出器料层渗透情况,及时调整喷淋量。
9、运行中要“勤看、勤听、勤闻、勤摸”,发现异常和管道堵塞,及时排除,恢复正常生产。
10、及时观察、感观测试胚片水份,如发现胚片水份大时,应及时通知预处理车间、及DTDC工段操作工。
二、DTDC(E109)1、开机前先检查各料摆,铜套润滑情况,各压力表指示是否正常,检查减速机油位情况。
2、将DTDC空开闭合,然后开启DTDC空运行15-20分钟,观察DTDC 运行情况及空载电流情况(82-90A)待设备无异常后,方可预热进料。
3、预热,先打开各直通阀门,关闭疏水器阀门,慢慢开启各层供汽阀门进行预热,使气压保持0.3Mpa左右,10分钟后,汽压升至0.5-0.7Mpa,15分钟升至0.8Mpa,20分钟升至10Mpa,最后将各疏水器阀门打开,关闭各旁通阀门,即预热完毕,等待进料。
4、正常工作时,DTDC电流一般控制在200-220A之间,成品粕出口温度控制在40℃。
5、正常运行时,操作工应及时巡查各层料摆灵活度,下料情况及电流变化情况,发现问题及时通知班长。
6、若出粕水份超标时,应及时将两台风机(E150、E151)频率加到55HZ,并开启冷风加热器阀门。
浸出车间设备操作规程

浸出车间设备操作规程一、浸出器(E102)1、开机前先检查各轴承润滑情况,各减速机油位情况,开车空运转无异常情况后,方可开机进料。
2、开机前,首先开启(E161-1-2-3)循环水泵,将安全水供给正常,使其水质保持在120kpa。
3、打开并检查所有自控装置的压缩空气,并关闭DTDC卸料门。
4、启动抽风机(E138)调节风机上管线的管路阀门,使其回收尾汽负压值,达到30㎜H20,并开启尾汽回收系统。
5、打开E117、E127供汽阀拉真空,通知热力车间供汽,使其浸出器负压值达到10-30㎜H20。
6、开机运行期间,控制调整浸出物料,混合油的温度,流量、浓度,使其粕残油降低至1%以下。
7、浸出料封要保持一定的高度,当料封低于3.8m时,应停止浸出器运转,待料封达到正常设定高度时,再开启浸出器。
8、经常观察注意浸出器料层渗透情况,及时调整喷淋量。
9、运行中要“勤看、勤听、勤闻、勤摸”,发现异常和管道堵塞,及时排除,恢复正常生产。
10、及时观察、感观测试胚片水份,如发现胚片水份大时,应及时通知预处理车间、及DTDC工段操作工。
二、DTDC(E109)1、开机前先检查各料摆,铜套润滑情况,各压力表指示是否正常,检查减速机油位情况。
2、将DTDC空开闭合,然后开启DTDC空运行15-20分钟,观察DTDC 运行情况及空载电流情况(82-90A)待设备无异常后,方可预热进料。
3、预热,先打开各直通阀门,关闭疏水器阀门,慢慢开启各层供汽阀门进行预热,使气压保持0.3Mpa左右,10分钟后,汽压升至0.5-0.7Mpa,15分钟升至0.8Mpa,20分钟升至10Mpa,最后将各疏水器阀门打开,关闭各旁通阀门,即预热完毕,等待进料。
4、正常工作时,DTDC电流一般控制在200-220A之间,成品粕出口温度控制在40℃。
5、正常运行时,操作工应及时巡查各层料摆灵活度,下料情况及电流变化情况,发现问题及时通知班长。
6、若出粕水份超标时,应及时将两台风机(E150、E151)频率加到55HZ,并开启冷风加热器阀门。
浸出车间操作规程
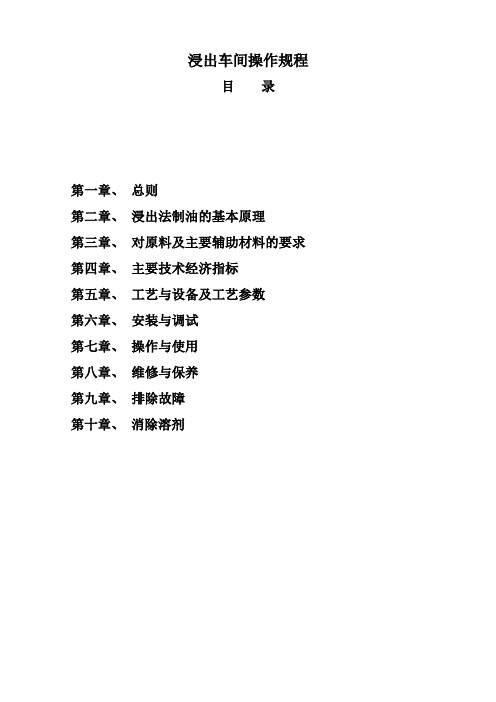
浸出车间操作规程目录第一章、总则第二章、浸出法制油的基本原理第三章、对原料及主要辅助材料的要求第四章、主要技术经济指标第五章、工艺与设备及工艺参数第六章、安装与调试第七章、操作与使用第八章、维修与保养第九章、排除故障第十章、消除溶剂第一章总则1.1植物油脂是人民生活的重要食品。
车间人员要努力提高生产技术,产品质量及出油率,为国家增产油脂。
1.2为保障人民身体健康,食用油脂要符合国家食品卫生标准,做到对动物(人体)无害。
1.3车间生产中、排出的废水、废气、废渣要符合国家及地方对三废处理的规定和要求,作好保护环境卫生。
1.4要“安全生产”,保证职工生命安全及国家财产安全,不得违章操作。
1.5车间要经常保持清洁卫生,改善工人劳动条件。
第二章浸出基本原理油脂浸出过程就是利用油料中的油脂能够溶解在选定的溶剂中的特性,并借两者之间相互扩散的作用而进行的一种制油方法。
在化工单元操作中叫萃取或提取,它实质上是一个物质传递过程,所得混合油利用溶剂(挥发性物质)与油脂(不挥发性物质)的沸点的不同进行蒸发、汽提,使溶剂变成蒸汽并与油脂分离而得到浸出毛油,溶剂蒸汽经过冷凝和冷却,回收以后继续循环使用;粕内含有一定量的溶剂,对其进行干燥处理、并回收其中溶剂,得到干粕。
第三章对原料及主要辅助材料的要求3.1入浸料胚性状要求:水分:9%—10%含油:18%—21%豆胚厚度:0.25mm—0.3mm粉末度(30目/25.4mm):≤5%温度:50℃—55℃3.2溶剂:本工艺采用国产6号溶剂油,其质量应优于(达到)如下指标:3.3蒸汽、冷却水蒸汽压力应不低于0.7MPa,含水不能过高,蒸汽应经分水处理,以便于直接蒸汽脱溶。
冷却水进水温度25℃以下(夏季不得高于30℃),出水温度不得超过35℃(夏天不得高于40℃)。
3.4熟练的操作人员和管理人员。
第四章主要技术经济指标4.1处理量:1500T/D4.2 粕残油:≤1%4.3 粕水分:11%—13%4.4粕残溶:500PPM(或引爆实验合格)4.5毛油残溶:300PPM4.6、毛油总挥发物:≤0.3%4.7溶剂损耗:1.5—2Kg/吨料4.8水蒸汽消耗:280Kg/吨料4.9水耗:1:1左右(700-800 Kg/吨料)第五章:工艺与设备及工艺技术参数5.1工艺流程说明:(祥(详)见工艺流程图)5.1.1浸出工序5.1.2蒸脱工序5.1.3蒸发工序5.1.4溶剂冷却及分水工序5.1.5尾气吸收工序5.2 设备5.3工艺技术参数5.3.1履带浸出器:a入浸物料温度:50—55℃(浸出器内温度)b溶剂温度:55℃c混合油浓度:18—22%d料层厚度:900—1100mm5.3.2DTDC蒸脱机:予脱层:间接蒸汽压力要求0.6—0.8MPa,控制溶剂蒸汽温度在75—82℃(80℃—85℃)为宜。
- 1、下载文档前请自行甄别文档内容的完整性,平台不提供额外的编辑、内容补充、找答案等附加服务。
- 2、"仅部分预览"的文档,不可在线预览部分如存在完整性等问题,可反馈申请退款(可完整预览的文档不适用该条件!)。
- 3、如文档侵犯您的权益,请联系客服反馈,我们会尽快为您处理(人工客服工作时间:9:00-18:30)。
迪斯美连续溶剂浸出车间操作手册广州植之元油脂实业有限公司目录1.概述2.工艺介绍和操作要求2.1.原料和公用设施要求2.2.浸出工段2.3.蒸脱工段(脱溶、干燥和冷却)2.4.混合油蒸发和回收工段2.5.矿物油吸收工段2.6.溶剂收集工段2.7.脱胶工段2.8.自动安全控制装置3.浸出车间开车操作3.1.开车3.2.启动浸出工段3.3.启动混合油蒸发工段3.4.启动蒸脱工段4.操作状况的检查4.1.浸出器4.2.蒸发工段4.3.矿物油吸收系统4.4.脱溶工段4.5.溶剂规格4.6.吸收油的规格4.7.工艺设计参数5.短期停车(浸出器带料停车)5.1.浸出器停车5.2.DTDC的停车5.3.停止混合油蒸发工段5.4.停止矿物油吸收系统6.车间长期停车(把浸出器内的料走空)6.1.把浸出器内的料走空,并停止浸出器6.2.停止蒸脱工段6.3.停止混合油蒸发工段6.4.停止矿物油吸收系统7.脱溶烤粕机70S/或13SDC之后的输送设备突然停止运转后的操作8.安全措施8.1.电源故障8.2.蒸汽压力故障8.3.冷却水故障8.4.注意事项8.5.紧急停车9.设备介绍9.1.斜刮板1A9.2.插板阀8A/B9.3.密封绞龙8A/A9.4.浸出器进料斗29.5.浸出器39.6.浸出器出料斗49.7.斜刮板59.8.密封绞龙8B9.9.密封绞龙8C9.10.旋转阀8D/A1-8D/A2-8D/B 9.11.斜刮板99.12.绞龙10B/刮板10A9.13.沙克龙14A1/14A29.14.刹克龙14B9.15.混合油罐179.16.二蒸18A9.17.汽提塔18B/229.18.真空冷凝器19/239.19.溶剂预热器199.20.冷凝器20B/C9.21.最后冷凝器20D9.22.分水罐和溶剂周转罐32A/B-34 9.23.离心风机36A1/36A29.24.风机36B9.25.离心风机36V9.26.蒸汽喷射泵9.27.废水蒸煮罐459.28.泵589.29.节能器/一蒸60A和闪蒸器60B 9.30.控制阀629.31.脱溶烤粕机70S9.32.干燥冷却机13SDC9.33.热风加热器94A1/94A29.34.矿物油吸收塔1209.35.吸收油换热器181A,181B,180 9.36.解析塔1229.37.尾气风机1369.38.毛油暂存罐5019.39.脱胶反应罐5039.40.油干燥器506A/B9.41.离心机5189.42.油加热器5219.43.油油换热器581A9.44.油冷却器581B/581C9.45.油脚罐582L10.浸出器和DT消溶1.概述总体来说,油籽经过适当的预处理,再通过浸出得到毛油和粕。
预处理是非常重要的过程,为溶剂浸出创造了良好条件。
也就是说,不仅能多出油,而且生产出来的油更好精炼。
使用的溶剂是己烷,己烷极易燃。
因此,浸出车间是禁区,只有被准许的人才可以进入。
严禁使用非防爆电器以及明火。
车间的操作员必须穿戴防静电的衣服和鞋。
●己烷物理性质如下:➢常压下沸点:68℃➢20℃的蒸气压:160mbar➢爆炸下限(L.E.L):1.2%V/V或42g/m3己烷/(空气+己烷)➢爆炸上限(H.E.L):7.4%V/V或265g/m3己烷/(空气+己烷)➢自然点:225℃➢己烷气体比重:2.79(空气比重为1)2.工艺介绍和操作要求2.1原料和公用设施要求浸出车间要求连续提供:●豆胚:经过良好处理的;●蒸汽:饱和干燥、10barg;●电源:380伏-3相-50赫兹;●冷却水:用于冷凝器和油节能器;●压缩空气:用于气动调节装置、~7barg;以上任一项或几项中断,将导致浸出车间不可避免的停车事故。
2.2. 浸出工段(流程图:349348/349353)该工段包含从预处理车间外到脱溶烤粕机前的所有设备。
豆胚经过输送设备输送到浸出器喂料绞龙8A/A;该绞龙与浸出器进行电气联锁,形成料封,防止空气进入浸出器。
关闭浸出器进料斗2与密封绞龙8A/A之间的气动插板阀8A/B,把浸出器与外界完全隔离。
在浸出器里,豆胚经过溶剂多次逆流萃取。
浸泡和滤干后的湿粕,在出料斗4得到缓冲后,输送到脱溶烤粕机70S。
(详细的浸出器操作见9.3)2.3. 脱溶、干燥和冷却工段浸出湿粕在脱溶烤粕机70S内进行脱溶烤粕等过程,然后在13DC 里进行干燥和冷取。
●脱溶烤粕机70S由12层组成,分成2个不同的工艺层:➢预脱溶层~7层;➢脱溶烤粕层~5层;预脱溶层的主要目的是降低粕中的水分,脱溶的主要作用是烤粕和从粕中除去溶剂。
脱溶烤粕机从上层到下层依次编号。
进入湿粕的顶层为第1层,底层为第12层。
每层都装有一对搅拌翅。
粕通过底夹层的间接蒸汽和穿过粕的直接蒸汽进行加热。
●粕干燥冷却器13S有5层:➢干燥层~4层;➢冷却层~1层。
脱溶后的粕通过穿过料层的热风进行干燥,再用穿过料层的常温空气进行冷取。
●热风系统由以下构成:➢两个鼓风机36A1/36A2;➢两个蒸汽加热器94A1/94A2;➢两个刹克龙14A1/14A2,带旋转阀8D/A1;8D/A2;●冷风系统由以下部分组成:➢风机36B;➢刹克龙14B和旋转阀8D/B。
预脱溶层、脱溶和烤粕层产生的溶剂气体,聚集在设备的顶部,然后进入一蒸60A进行冷凝,回收后的溶剂再循环到浸出器。
用水捕集DT出来的二次蒸汽中夹带的粕沫,热水在捕集器用泵P29进行循环。
循环溶剂用泵P1泵出,流量通过流量计和调节阀回路进行控制。
刮板5把浸出后的湿粕输送到脱溶烤粕机70S。
刮板9把脱溶粕输送到干燥冷却器13SDC。
刮板10A把冷却后的粕输送到预处理车间进行粉碎和结粒。
绞龙10B把刹克龙分离出来的粕沫输送到10A。
2.4 混合油蒸发和溶剂回收工段整个混合油蒸发工段都处于真空状态下,蒸发混合油中的溶剂。
最后残留在油中的溶剂,用直接蒸汽进行汽提。
混合油先是通过脱溶烤粕机70S出来的二次蒸汽进行加热。
再用蒸汽进行加热。
通过蒸汽喷射泵抽出冷凝器中的未凝气体,从而使蒸发系统形成真空。
冷凝后的溶剂进入分水罐部分32A/B,分离后流到溶剂周转部分34,并再循环使用。
所提及的设备介绍如下:2.4.1.废水蒸煮罐45来自分水罐32A/B的废水,在废水蒸煮罐45内加热到85℃以上,去除水中可能残留的溶剂。
通过蒸汽喷射泵41/19排出的蒸汽、与一个温度调节回路控制的蒸汽来加热废水。
蒸煮后的水溢流到废水节能器81-32/45,加热P32来的废水后,冷却到~45℃,流入水封池99A 和95,最后进入厂区排水道。
2.4.2.常压冷凝水罐46AT和高压冷凝水罐46B浸出车间所有高压蒸汽冷凝水进入高压冷凝水罐46B,闪蒸出来的蒸汽进入二蒸18A,冷凝水用泵P46B泵到46AT;所有低压蒸汽冷凝水进入常压冷凝水罐46AT,最后泵回到锅炉房。
2.4.3.节能器/一蒸60A一蒸是一个大面积升膜管壳式蒸发器,利用脱溶烤粕机70S出来的二次蒸汽进行加热,在真空状态下,蒸发掉大量的混合油中的溶剂。
罐17中的混合油,用泵P8泵到一蒸60A的管程,被二次蒸汽加热,产生的气体在闪发箱60B中分离后,进入冷凝器19,由蒸汽喷射泵41/19形成真空。
一蒸60A的壳程内底管板上,由泵P1泵来的溶剂进行冲洗,从而防止粕沫聚集,冲洗的时间和次数通过聚集的粕沫的多少来进行调节。
闪发箱60B中蒸发后的浓混合油,用泵P60泵到油/混合油换热器81-P60/P22,再进入二蒸18A。
2.4.4. 油/混合油换热器81-P60/P22卧式换热器,用泵P22泵来的油,加热来自一蒸的混合油。
2.4.5. 二蒸18A立式升膜列管式蒸发器,通过低压蒸汽和46B的闪蒸蒸汽加热。
该低压蒸汽的流量由一个调节回路来控制。
溶剂气体在汽提塔22上部的分离器18B中分离,与一蒸挥发的溶剂气体一道进入冷凝器19进行冷凝。
18B出来的混合油仍含有大约4~5%的溶剂,然后自流进入汽提塔22。
2.4.6. 汽提塔22混合油从二蒸18B自流进入汽提塔22。
位号22是立式层碟式汽提塔,油从顶部通过碟盘组流到底部,被从下向上穿过的直接蒸汽逆向汽提。
在通常状况下,塔底保持2500mm 以上的油位。
混合油中的溶剂,通过汽提塔底部和中部喷入的直接蒸汽蒸馏出来。
该直接蒸汽和挥发出来的溶剂气体,与油逆向向上流动,并排出塔外进入冷凝器23。
直接蒸汽由喷射泵541/06A喷入和蒸汽调节回路喷入。
2.4.7.最后脱溶:油加热器521和干燥器506A/B进入521和506A/B的油已经脱胶。
大豆油一般先脱胶再干燥。
离心机出来的油进入加热器521,加热到适当的温度,泵入干燥器516A/B进行干燥。
干燥器506A/B工作在喷射泵541/06A/06B形成的较高的真空度状态下。
喷射泵排出的蒸汽用做22汽提蒸汽。
2.4.8. 冷凝器19-20A-20B/C-20D-23冷凝器19是固定管板式冷凝器。
水走管程,冷却壳程中的来自闪发箱60B、18B和解析塔122的溶剂蒸汽。
冷凝下来的水和溶剂进入分水罐32/34,未冷凝气体由喷射泵41/19抽走。
节能器20A是立式冷凝器,新鲜溶剂由泵P1泵到该冷凝器中进行预热,而来自一蒸60A壳程排出的未凝二次蒸汽再次被冷却,并部分冷凝,冷凝液进入分水罐32/34。
再未冷凝的气体进入冷凝器20B/C。
其目的是再次回收二次蒸汽的潜热,进行预热泵到浸出器的新鲜溶剂,保持浸出温度。
20B/C是立式换热器。
来自冷凝器20A的未冷凝气体、与来自63A-C 和3和32/34和17中的自由气体都在该冷凝器中进行冷凝。
水走管程,冷凝液直接进入分水罐32/34。
浸出器、溶剂罐、混合油罐和分水罐里出来的物质也连接该冷凝罐。
剩余的未冷凝气体进入最后冷凝器20D。
最后冷凝器20D也是立式的。
来自冷凝器20B/C的未冷凝气体,被管程中的冷却水进一步冷凝。
冷凝液直接进入分水器32/34,仍未冷凝的气体进入矿物油吸收工序。
冷凝器23是卧式固定管板式的,水走管程,冷却来自汽提塔22和解析塔122的溶剂蒸汽。
由喷射泵41/23形成真空。
冷凝液流入分水器32/34。
2.4.9. 蒸汽喷射泵41/19-41/23-541/06A-541/06B和41/70蒸汽喷射泵保持各设备和冷凝器的真空要求,串联蒸汽喷射泵,从而得到不同的真空度。
蒸汽喷射泵41/19保持冷凝器19的真空,排出的蒸汽进行废水蒸煮罐45。
蒸汽喷射泵41/23抽出冷凝器23未冷凝气体,并排到冷凝器19。
喷射泵541/06A抽出干燥间506A中的蒸汽,并排到汽提塔22。
喷射泵541/06B抽出干燥器506B中的蒸汽,并排到506A。
喷射泵(注射器)41/70抽出捕集器29中的水,排到70S.2.5. 矿物油吸收工段所有接触溶剂的设备,都处于真空或微负压状态,防止溶剂气体外泄,同时增加了生产安全,但是仍然要注意设备的良好密封。