汽车轮胎常见故障现象与动平衡检测++
任务七-汽车车轮动平衡检测课题
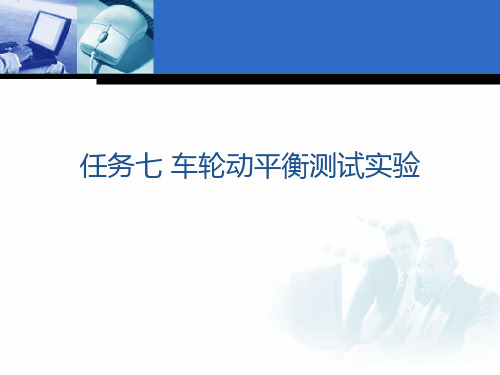
动平衡测试
四、实验设备的工作原理(2/8)
1.离车式车轮动平衡机
F1、F2为对应的离心力,fA、
fB为左右支承点传感器测 得的动反力。S为支承系 统结构参数,a为平衡机 支承点与轮胎的距离,b 车轮宽度尺寸,c为轮辋 直径。
动平衡测试
四、实验设备的工作原理(3/8)
1.离车式车轮动平衡机
由力学平衡方程式可得:
动平衡测试
四、实验设备的工作原理(6/8)
2.就车式车轮动 平衡机
驱动装置:6-电 动机、5-转轮
测量装置:2-传 感磁头、3-可调 支杆、4-底座、 传感器
指示与控制装置: 7-频闪灯、8-数 字显示屏
制动装置 小车
动平衡测试
四、实验设备的工作原理(7/8)
2.就车式车轮动平衡机
支离地面的不平衡车轮,转动时产生的横向振动通过制动底板上传感磁头、可调支杆和底座内的 传感器。传感器变成的电信号控制频闪灯闪光,指示车轮不平衡点位置,并输入指示装置指示 不平衡度(量)。
五、实验方法和步骤 (6/6)
2.就车式车轮动平衡的检测方法
驱动轮动平衡 (1)对面车轮不必用三角垫木塞紧。 (2)用发动机、传动系驱动车轮,加速至50~70 km/h的某一转速下稳定运转。 (3)测试结束后,用汽车制动器使车轮停转。 (4)其它方法同从动轮动、静平衡测试。
动平衡测试
六、实验报告的基本内容和要求
平衡机测定车轮静不平衡点位置和车轮的静不
平衡量。如果车轮的不平衡精度不能满足要求, 则安装平衡块,并进行复查。 注意:静平衡与动平衡检测的传感磁头安装位置!
(1) 实验过程的详细记录。 (2) 实验数据的记录和数据处理。 (3) 分析车轮动平衡对汽车行驶平顺性、操纵稳定性的影响。 思考:就车式动平衡检测仅仅检测的是轮胎的动平衡吗?做就车式动平衡检测有什么好处?
汽车轮胎常见故障现象与动平衡检测++

汽车轮胎常见故障现象与动平衡检测一.常见异常现象的故障判断1、大部分平衡机的测量系统都具有"自检〞功能,此功能可以检测测量系统本身是否正常.与"自检〞功能对应的操作按键可能会标注为"自检〞或"TEST〞等.用户可以在平衡机正常时,将各种设定的支承条件〔支承方式与a、b、c与两个半径等〕固定,然后使测量系统进入"自检〞状态,记录下对应此支承条件下的"自检〞状态的显示读数.当操作者认为测量系统有问题时,可以使测量系统恢复到对应原设定的支承条件下的"自检〞状态,然后检查测量系统的显示读数是否正常.2、平衡机显示的不平衡量的角度总在大致相差180度或0度左右.首先确认平衡机正常运转测量而且转子仍有一定的残余不平衡量〔甚至可以在两个配重面上分别给转子加装两个不同相位的不平衡量〕,在转子正常旋转测量的情况下:拔下1号传感器线插头,看仪表显示数值有无变化.如有明显变化,则证明此传感器线和传感器一切正常.如无变化,则证明此传感器线或传感器有问题.将1号插头插好,再将2号传感器线插头拔下,同样的方法可以判断2号传感器线和传感器是否正常.使用者可以找专业人员对照另一个传感器线和传感器对有故障的传感器线或传感器进行修理.3、平衡机在残余不平衡量较大时,故障不明显.但在残余不平衡量较小时,一次启动平衡机进入测量时,显示不平衡量值的角度总在变化.有时角度在一定X围内变化,有时角度在360度X围内变化.①为减少同频、倍频、分频干扰,工件支承轴径应避开与支承滚轮外径或其整倍数整分数相同或接近,以免干扰.比如:滚轮外径为101毫米,那么,最好避开使用91~111、46~55、32~36毫米X围内的轴径支承.②严格检查转子装配部分的稳定性.如使用工艺轴,则应着重检查轴和孔的配合.③检查转子轴〔工艺轴〕与滚轮接触处的状态,如果轴径粗糙、刀纹明显或滚轮表面有伤,均会导致小信号时不稳定.④检查滚轮与转子轴〔工艺轴〕接触处的状态,如果滚轮接触面上连续的光洁的外表面已经破坏,也会导致小信号时不稳定.当滚轮的接触面上出现较明显的伤痕时,平衡量的显示是非常不稳定的.⑤停车状态下清洁滚轮与转子轴〔工艺轴〕的接触面,加适量润滑油.⑥认真计算一下,是否你的平衡精度要求太高了.4、平衡机在残余不平衡量较大时,故障不明显.但在残余不平衡量较小时,每次配平衡后重新启动测量时,显示不平衡量值的角度总是以大致相差180度的方式变化.①所配平衡量偏多.②严格检查转子装配部分的稳定性.如使用工艺轴,则应着重严格检查配合轴和孔的间隙、椭圆度和锥度误差,尤其是椭圆度和锥度误差.二.四点法故障诊断按以上方法检测、维修完成后,如果故障仍然存在,可以按下面介绍的平衡机四点检验法对平衡机进行检验.一般情况下,用户可以依此用实物转子进行.如果有必要,用户可以将下面过程与所有数据进行记录,然后提供给平衡机的制造厂家,制造厂家可以根据这个记录判断90%以上的故障.1、首先将转子平衡至能够达到的最高精度,然后准备一个大于转子残余不平衡量30~50倍的可拆装的配重块〔以下过程按:使用配重块重100克,转子残余量应该小于2~3克〕.转子与平衡机的联结与装载形式不变,直接进入下面的试验过程.2、检查平衡机的各种设置是否正常.3、在转子的任一面指定配重圆周处45度上加一个已知重量的能够拆装的配重块〔以下按假设配重块重100克〕.启动平衡机,平衡机对应面指示值应该在40—50度、90—110克〔按90%去重率〕.4、停机后将配重块拆下安装在转子的同一面圆周135度角度上.启动平衡机,平衡机对应面指示值应该在130—140度、90—110克〔按90%去重率〕.5、停机后再将配重块拆下安装在转子的同一面圆周处225度角度上. 启动平衡机,平衡机对应面指示值应该在220—230度、90—110克〔按90%去重率〕.6、停机后再将配重块拆下安装在转子的同一面圆周处315度角度上. 启动平衡机,平衡机对应面指示值应该在310—320度、90—110克〔按90%去重率〕.7、同样过程,在转子的另一面指定配重圆周处4个角度上依次安装此配重块进行检查.8、如平衡机能够达上面所述要求,则认为平衡机没有任何故障.9、如平衡机能够近似达到以上要求,则认为平衡机有轻微定标不准确问题.此问题一般会引起操作效率的下降,而不致引起大的操作错误.如平衡机有轻微定标不准确问题,用户可以按平衡机配套说明书中的内容进行排除,也可以通知制造厂家进行处理.10、如平衡机确实不能达到上面要求,而且误差非常大,用户应通知制造厂家进行处理.11、特殊情况下,用户对平衡机的精度或质量有怀疑时,也可以对平衡机进行四点法故障诊断.有时用户会发现,转子在平衡机上已经达到平衡精度,通过以上方法检验认为,平衡机也一切正常,但转子实际安装运转时,还是有一定程度的振动,这时就需要认真分析其他的工艺方面原因了.三.认真分析振动原因,正确判断真实的平衡精度引起机械振动的原因很多,其中旋转零部件由于其平衡问题引起的振动最为直接.但这并不说明转子在平衡机上平衡好以后,就可以解决所有的振动问题.转子的不平衡问题,是由于转子的重心,偏离了转子的旋转几何中心线.转子旋转时由此产生的离心力随转子一起旋转,从而激发转子与转子的安装基础〔如:轴承座、机座、机箱、车身等〕产生振动.以下将讨论其他相关的一些工艺问题.1、平衡机本身的工艺问题高精度平衡时,应考虑万向联轴器、键等相关连接件的影响.小转子平衡过程需要加光标等附属质量的,也需要考虑其对最终平衡精度的影响.当这些相关连接件引起的不平衡量接近甚至大于用户要求的转子平衡精度时,平衡机显示的不平衡量是不可靠的.对于用万向联轴器传动的平衡机,也应定期检查万向联轴器的平衡精度.当采用工艺轴进行平衡时,工艺轴的圆跳动不能大于转子平衡精度指标e〔偏心距〕,否则必须进行翻转1800高精度平衡.或者将工艺轴报废.另外,工艺轴的结构与转子实际安装轴的结构,应尽量制作成一致或近似,保证其质量分布与实际安装状态一致.2、转子的工艺问题平衡机用户应尽量采用转子的真实安装状态进行平衡,并且保证其刚性.采用工艺轴进行平衡时,就存在工艺轴与转子实际安装轴的误差,比如转子在工艺轴和实际轴上不同的安装方法、键槽结构、工艺轴和实际轴各自的跳动,这些因素都会引起不平衡量的变化.采用工艺轴进行平衡时,必须保证转子安装孔的尺寸精度和形位公差精度,诸如:配合间隙大、孔椭圆或有锥度误差、粗糙度低等是绝对不允许的.另外转子的刚性必须保证.如果转子内部有滑动花键、活动块、摆动刀块等其他类似结构,这样的转子是永远达不到理想的平衡精度的.3、转子实际安装的工艺问题转子在平衡机上已经达到了要求的平衡精度,在转子实际安装运转时,如果在实际安装过程中有些因素不去认真考虑,还是会造成平衡精度的变化,以至引起一定程度的振动.首先是实际安装轴的跳动,这一因素非常重要.因为转子的不平衡问题,就是由于转子的重心,偏离了转子的旋转几何中心线.转子旋转时由此产生的离心力随转子一起旋转,从而激发转子与转子的安装基础产生振动.而平衡好的转子被安装在有偏心的实际安装轴上,当然会导致转子与机器的振动.另外,与转子同轴的其他零部件也会导致转子与机器的振动,如皮带轮、联轴器、电机转子等,他们的平衡精度也会与转子一起参与到机器的振动中.4、其他问题我公司技术人员在进行售后服务时发现,有个别平衡机用户在其产品生产过程中,不注意把握其产品的前期制造质量,而将其转子的运转性能完全依赖于动平衡工序,这是非常不严肃的.比如:产品设计时不考虑动平衡工序的工艺性;产品的基础件〔如支架等〕偷工减料甚至有严重缺陷;风机转子或其他焊接结构转子的外形端面跳动过大;铸造转子的质量分布不均匀误差过大;转子的安装孔精度和粗糙度太低;转子内部结构存在严重的非刚性因素〔如:漏焊、铆钉松动等〕;工艺轴的粗糙度与精度太低;转子实际安装轴精度和粗糙度太低;………….所有这些因素都会导致平衡精度的降低甚至平衡失败.另外,动平衡机属仪器仪表类试验机产品.对平衡机的野蛮操作〔如:在平衡机上进行焊接、砂磨等〕也会直接影响平衡机性能与寿命,导致平衡失败,千万注意.。
汽车检测与维修技术项目4 轮胎车轮动平衡

动反力 NL 和NR可用位移、速度或加速度传感器测 出,根据此确定F1、F2并确定平衡块质量和安装方位。
四、车轮不平衡检测方法
1.离心式车轮平衡机的检测方法
(1)准备工作 1) 清 除 被 测 车 轮 上 的 泥 土 、 石 子 和 旧 平 衡 块 。 2) 检 查 轮 胎 气 压 , 视 必 要 充 至 规 定 值 。 3)根据轮辋中心孔的大小选择锥体,仔细地装上车轮,用大螺距 螺母上紧。
假设一车轮,不平衡质量分布如下图:
F F 1
2
m2 r2
m3r3
m2 r2
m1r1
m1r1
mb rb m3r3
mb rb
F3
2.动不平衡
m1
m1 m2 '
m2
O M
m m2
' 1
2.动不平衡
动平衡的条件是:
即:分布在回转件上各个质量的离心惯性力合力为零;同时离心
力所引起的力偶的合力偶矩也为零。 动平衡原理(方法):预先选定两个平面,根据力系等效原理,分别
专用卡尺:供用户测 量轮辋直径D和轮 胎宽度B,因为轮 胎宽度用直尺难以 测量。
2)放下车轮防护罩,按下起动键,车轮旋 转,平衡测试开始,微机自动采集数据。 3)车轮自动停转或听到“笛”声按下停止 键并操纵制动装置使车轮停转后,从指示装置 读取车轮内、外不平衡量和不平衡位置。
4)抬起车轮防护罩,用手按箭头方向慢慢 转动车轮。当指示装置出现两相对箭头时停止 转动。在轮辋的内侧或外侧的上部(时钟12点位 置)加装指示装置显示的该侧平衡块质量。内、 外侧要分别进行,平衡块装卡要牢固。
就车式车轮平衡机结构示 意图
三、车轮不平衡检测原理
1.静不平衡 可在离车或就车式平衡机上检测。以就车式为例: 被测车轮先由举升器举离地面,并将车桥座落于传 感器支架6上(见上图)。操作人员推动小车手把,使摩擦轮 紧压于被测车轮 7上,启动电机 4 带动摩擦轮拖动车轮以相当 于110km/h的车速旋转,这时车轮的不平衡质量产生的不平衡 力即被力传感器感知并转变成电量,这一电信号由电缆传入 驱动小车内的电测系统予以计量和处理。光电传感器1拾取车 轮的初相位信号和转速信号,经电测电路处理后得到不平衡 质量的量值和相位值,显于仪表板上。测试前须在被测轮胎 侧面任意处贴装白色反光标志,为使光电元件正常工作,胎 侧距光电管不得超过5cm,检测程序分三次进行。
四轮定位检测及维修(附动平衡)
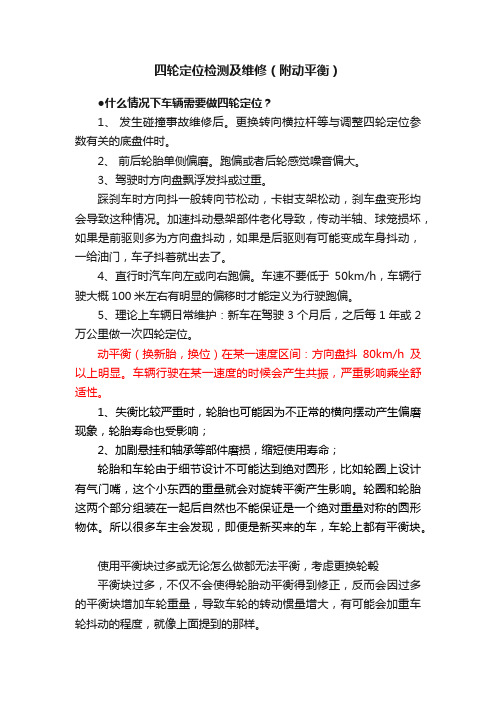
四轮定位检测及维修(附动平衡)●什么情况下车辆需要做四轮定位?1、发生碰撞事故维修后。
更换转向横拉杆等与调整四轮定位参数有关的底盘件时。
2、前后轮胎单侧偏磨。
跑偏或者后轮感觉噪音偏大。
3、驾驶时方向盘飘浮发抖或过重。
踩刹车时方向抖一般转向节松动,卡钳支架松动,刹车盘变形均会导致这种情况。
加速抖动悬架部件老化导致,传动半轴、球笼损坏,如果是前驱则多为方向盘抖动,如果是后驱则有可能变成车身抖动,一给油门,车子抖着就出去了。
4、直行时汽车向左或向右跑偏。
车速不要低于50km/h,车辆行驶大概100米左右有明显的偏移时才能定义为行驶跑偏。
5、理论上车辆日常维护:新车在驾驶3个月后,之后每1年或2万公里做一次四轮定位。
动平衡(换新胎,换位)在某一速度区间:方向盘抖80km/h及以上明显。
车辆行驶在某一速度的时候会产生共振,严重影响乘坐舒适性。
1、失衡比较严重时,轮胎也可能因为不正常的横向摆动产生偏磨现象,轮胎寿命也受影响;2、加剧悬挂和轴承等部件磨损,缩短使用寿命;轮胎和车轮由于细节设计不可能达到绝对圆形,比如轮圈上设计有气门嘴,这个小东西的重量就会对旋转平衡产生影响。
轮圈和轮胎这两个部分组装在一起后自然也不能保证是一个绝对重量对称的圆形物体。
所以很多车主会发现,即便是新买来的车,车轮上都有平衡块。
使用平衡块过多或无论怎么做都无法平衡,考虑更换轮毂平衡块过多,不仅不会使得轮胎动平衡得到修正,反而会因过多的平衡块增加车轮重量,导致车轮的转动惯量增大,有可能会加重车轮抖动的程度,就像上面提到的那样。
●正常的四轮定位后车辆会有哪些改善?1、增加行驶的安全性。
2、减少轮胎的不正常磨损。
3、保持直行时转向盘正直,维持直线行车。
4、转向后转向盘会自动归正。
5、增加驾驶的操控感。
6、减少油耗的异常消耗。
7、降低悬挂部件耗损。
●做四轮定位不准确的后果是什么?1、轮胎过度磨损:四轮定位参数不准确可以造成轮胎偏磨从而导致发生爆胎的危险。
轮胎动平衡
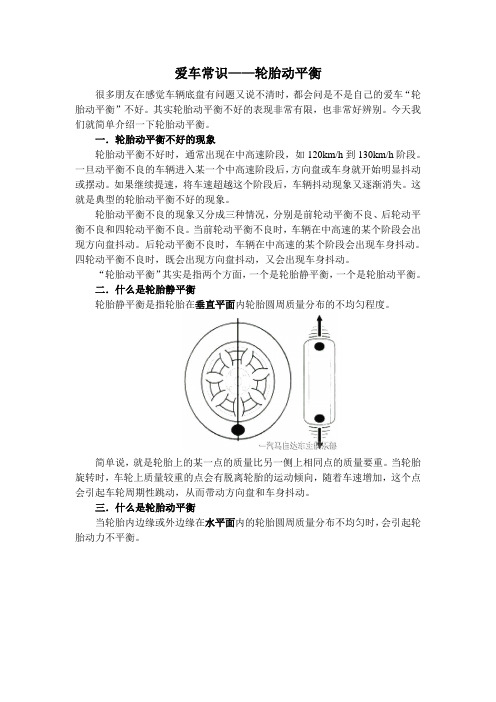
爱车常识——轮胎动平衡很多朋友在感觉车辆底盘有问题又说不清时,都会问是不是自己的爱车“轮胎动平衡”不好。
其实轮胎动平衡不好的表现非常有限,也非常好辨别。
今天我们就简单介绍一下轮胎动平衡。
一.轮胎动平衡不好的现象轮胎动平衡不好时,通常出现在中高速阶段,如120km/h到130km/h阶段。
一旦动平衡不良的车辆进入某一个中高速阶段后,方向盘或车身就开始明显抖动或摆动。
如果继续提速,将车速超越这个阶段后,车辆抖动现象又逐渐消失。
这就是典型的轮胎动平衡不好的现象。
轮胎动平衡不良的现象又分成三种情况,分别是前轮动平衡不良、后轮动平衡不良和四轮动平衡不良。
当前轮动平衡不良时,车辆在中高速的某个阶段会出现方向盘抖动。
后轮动平衡不良时,车辆在中高速的某个阶段会出现车身抖动。
四轮动平衡不良时,既会出现方向盘抖动,又会出现车身抖动。
“轮胎动平衡”其实是指两个方面,一个是轮胎静平衡,一个是轮胎动平衡。
二.什么是轮胎静平衡轮胎静平衡是指轮胎在垂直平面内轮胎圆周质量分布的不均匀程度。
简单说,就是轮胎上的某一点的质量比另一侧上相同点的质量要重。
当轮胎旋转时,车轮上质量较重的点会有脱离轮胎的运动倾向,随着车速增加,这个点会引起车轮周期性跳动,从而带动方向盘和车身抖动。
三.什么是轮胎动平衡当轮胎内边缘或外边缘在水平面内的轮胎圆周质量分布不均匀时,会引起轮胎动力不平衡。
简单说,如果在轮胎的内侧或外侧某一个点质量过大,当轮胎旋转时,这个质点的运动轨迹是既在一个垂直平面上运动,又在水平面上运动。
因此,这个轮胎就会出现左右摆动的情况。
如果这个轮胎放在前轮,那么方向盘就会出现强烈的抖动;如果这个轮胎放在后轮,车身就会出现强烈的上下跳动和左右摆动。
四.轮胎动平衡的检测和修复当车辆出现动平衡不良时,需要通过轮胎平衡机找到轮胎内侧或外侧质量最重的点,并在相对称的位置添加相同质量的铅块来补偿轮胎的质量不均匀性。
在对轮胎进行不平衡修复时,通常,要控制修复后的轮胎不平衡重量在5g以内,否则轮胎动平衡是不可能合格的。
车轮动平衡检测
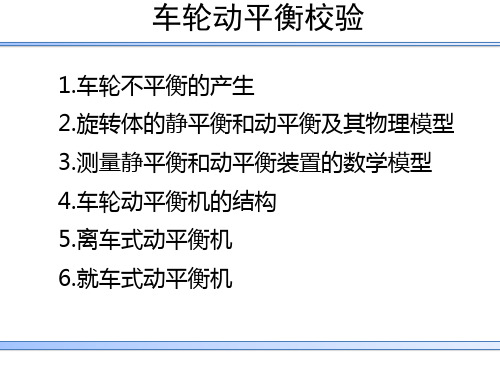
1.车轮不平衡的原因
引起车轮不平衡的主要原因如下: 1)因轮毂和轮辋定位误差使安装中心与旋转中心不重合。 2)轮胎和轮辋以及挡圈等因几何形状失准而先天形成的 重心偏离。 3)车轮碰撞造成的变形引起的质心位移。 4)翻新轮胎因定位精度不高而造成新胎冠厚度不均匀而 使重心改变。 5)高速行驶中制动抱死而引起的纵向和横向滑移,会造 成局部的不均匀磨损等。
5 离车式动平衡机
离车式动平衡机的基本结构
离车式动平衡机 如图a所示。它主要 组成为:驱动系统、 测量显示系统以及一 些附件组成。
离车式动平衡机
离车式动平衡机
(1)驱动系统 驱动系统包括主轴、电动机、传动装置和制动装置等部分。 驱动装置绝大部分在机箱内,如图b所示。 电动机经带轮带动主轴及被测车轮旋转。主轴通过轴承支 承在机箱上,在轴承下方靠近带轮处有一根应变梁,测力的 传感器经过杆件与应变梁连接,传感器基本上不受静态力作 用。
车轮动平衡机简介
在离车式车轮平衡机中,根据转轴方向不同分为: 1)立式;2)卧式。 对于立式平衡机,试验时需将车轮平放在平衡机上,装卸 车轮不如卧式平衡机方便,结构设计也比较复杂,但传感系 统的灵敏度比较高,可达3g。 对于卧式平衡机,试验时车轮固定在水平的主轴上,与实 际行驶状态相似。
车轮动平衡机简介
作为角度与位置传感器的光电编码盘输出脉冲信号,可直 接(或经光电隔离)送微控制器。微控制器将采样信号经分析 处理计算后将结果送到显示器,同时控制电动机启停制动等 操作。
离车式动平衡机
(3)附加装置 附加装置包括:车轮防护罩(安全罩)、用于固定车轮的定 位锥体和锁紧螺母以及测量轮辋宽度的专用卡尺等,附件包 括:各种平衡块以及拆装平衡块的专用工具等,如图所示。
就车式平衡机原理示意图
4、汽车轮胎常见故障现象与动平衡检测
汽车轮胎常见故障现象与动平衡检测汽车行驶系的常见故障主要有:汽车跑偏、前轮摆振,乘坐振动和轮胎异常磨损等。
一、汽车跑偏(1)现象:汽车行驶时偏向一侧,驾驶员要把住转向盘或把转向盘加力于一侧汽车才能正常行驶,否则极易偏离行驶方向。
(2)原因:①装用了不合乎规格的或磨损的轮胎,两侧轮胎大小不一;两侧轮胎气压不相等,或一侧轮胎磨损过甚。
②前轮轮毂轴承调整不当,过紧或过松;两侧前轮定位角不同或发生变化;前轴弯曲变形。
③前钢板弹簧断裂,钢板弹簧下陷;减振器失效。
④车架一侧断裂;车架变形不正。
⑤后钢板弹簧断裂,下陷;后钢板弹簧松脱。
⑥后桥壳弯曲变形或断裂。
⑦后桥与车架错位。
⑧极度偏载。
(3)排除方法:①轮胎换位,轮胎气压要一致。
②调整前轮轮毂轴承;校正前轴,恢复正确前轮定位角;调整汽车前束为正确值。
③检查更换前钢板弹簧;更换两侧减振器。
④维修车架,校正变形。
⑤检查更换后钢板弹簧,紧固固定螺栓。
⑥校正或更换后桥壳。
⑦检查与调整后轴(后桥)与车架的相对位置。
⑧注意偏载,注意行驶中载荷偏斜。
二、前轮摆振(1)现象:汽车行驶中前轮左右摆振,前轮垂直颠簸。
严重时影响汽车速度发挥。
乘坐不舒服。
(2)原因:①轮胎气压不一致;轮胎大小不一;磨损。
②车轮动不平衡。
③前轮轮毂轴承损坏或松动。
④前轮定位不正确。
(3)排除方法:①检查调整轮胎气压;更换新轮胎。
②汽车行驶速度较高,一定要对车轮总成做动平衡试验,使不平衡量控制在允许值内。
③检查并调整汽车前轮轮毂轴承和松紧度。
④汽车前轮定位和前束要正确。
三、轮胎异常磨损车轮胎是汽车的重要组成部分,关系到汽车的使用性能和行驶安全。
在汽车的使用过程中要特别注意,防止轮胎的不正常损坏,防止轮胎的早期磨损。
正确合理地使用汽车轮胎,可以有效地延长轮胎的使用寿命。
汽车驾驶员是汽车的直接使用者,应十分注意对于汽车和汽车轮胎的使用。
(1)检查和保持轮胎气压。
标准的汽车轮胎气压,决定着汽车轮胎的正确使用性能。
车轮动平衡的检测(完成稿)
2013全国中职学校“创新杯”汽修专业说课比赛山东省选拔赛车轮动平衡的检测教学设计方案济南第九职业中等专业学校万旭根据实例引入,吸引学生的注意力,让学生通过实际案例进入学习情景,导入二、提出任务分组探究(10分钟)下发任务卡,交代本节课的学习任务:任务卡任务一高速行驶中方向盘抖动的原因?任务二车轮动平衡故障的原因?任务三车轮动平衡故障的排除?(难点)任务四车轮动平衡的检修思路和规范的操作流程?(重点)解决任务:任务一:高速行驶中方向盘抖动的原因?任务二:车轮动平衡故障的原因?学生小组分析,根据前面所学的内容,解决前两个任务。
车轮动平衡故障的原因:依照机械运动的原理,由于材料组织内部的不均匀,零件外形的尺寸误差,装配尺寸的误差以及结构形状等原因,使通过车轮重心的主惯性轴线与旋转轴线不相重合,因而旋转时的车轮会产生不平衡的离心力,特别是高速运转的车轮,每秒钟旋转十几圈以上,即使有极小的偏心矩也会引起很大的不平衡力,导致车轮的持续振动,尤其是方向轮的振动会导致方向盘的抖动,会加速悬架和转向系统部件的磨损,加速车轮内轴承的磨损,振动大的汽车也很难驾驶,行车不安全.解决本节课的难点任务:任务三:车轮动平衡故障的排除.小组分析代表回答教师点评使用车轮动平衡机解决问题:设计意图:通过下发任务卡,交代给学生本节课的学习任务,学生结合实际案例以及前面所学的内容,通过小组分析、讨论,解决学习任务一、二,体现学生的主体地位,再一次通过小组分析,代表回答,教师点评,突破本节课的难点任务三。
三、小组协作完成任务(20分钟)解决本节课的重点任务任务四:车轮动平衡的检修思路和规范的操作流程学生分组讨论方案为每组学生发项目工单,小组讨论实施方案,最后由组长根据讨论情况填写完成项目工单。
教师示范:使用摄像头把教师的示范流程在多媒体上展现操作流程:1.轮胎固定清除被测车轮上的泥土、石子和旧平衡块;检查轮胎气压,必须符合原厂的规定;根据轮辋中心孔的大小选择好锥体,仔细装好车轮,用快速螺母上紧。
汽车轮胎不平衡的诊断流程
汽车轮胎不平衡的诊断流程
1、车轮碰撞造成的变形引起的质心位移。
2、因轮毂和轮辋定位误差使安装中心与旋转中心难以重合。
3、维修过程的拆装破坏了原有的整体综合重心。
4、轮胎翻新中因定位精度不高而造成新胎冠厚度不均匀而使重心改变。
5、轮胎和轮辋以及档圈等因几何形状失准或密度不均匀而先天形成的重心偏离。
6、轮辋直径过小,运行中轮胎相对于轮辋在圆周方面滑移,从而发生波状不均匀磨损。
车轮不平衡怎么办
如果车轮不平衡,当然就要做车轮动平衡了。
现在一般的修理厂都能做这个项目,很简单,也不贵。
所使用的配重块有两种,一种是外挂式的,现在使用的非常少了,另外是内贴式的,使用的比较普遍。
有些人把配重块叫做铅块,是因为以前的配重块确实是用铅做的,现在的配重块一般都是铁的,原因是便宜,但是我们还是习惯于称之为铅块。
需要注意的是我们不能无限制的往车轮上帖配重块,如果在某一侧帖的配重块超过了50克,我们就要找其它的原因了,比如轮圈变形等。
简单检查车轮动平衡的方法
如果你的车出现了高速抖动、轮胎偏磨等现象,最好做车轮动平衡检查一下。
如果你去修理厂很不方便,那么下面教你一个简单的方法来判断车轮是否平衡。
第一,将车轮支起,旋转车轮,等车轮自由停止后,在车轮的任一位置做好记号,比如在车轮上部。
第二,用力旋转车轮,使其高速旋转,并使其自由停止,观察记号所在的位置,并做好标记。
第三,反复重复步骤二数次,观察轮胎停止时记号的位置。
如果车轮始终停止在同一个位置或停止的位置成180°对称分布,就说明车轮是动不平衡的,如果车轮能停止在任意位置,就说明车轮是动平衡的。
汽车轮胎动平衡检测原理应用
汽车轮胎动平衡检测原理与应用摘要:随着经济和交通事业的不断发展、各种路桥的修建,一定程度上为车辆出行带来了方便,而汽车在行驶过程中却容易受车轮不平衡因素的影响,使得汽车无法正常运行,从而给出行者安全带来隐患。
这就需要对影响车轮不平衡的因素进行分析,轮胎动平衡检测机的出现和使用在一定程度上解决了这一问题。
为了使汽车轮胎动平衡检测机更好的发挥其作用,需要对其原理和应用等相关内容进行具体分析。
关键词:汽车;轮胎动平衡;检测原理;应用车轮作为汽车重要部件,在汽车使用过程中常会出现车轮不稳定、左右摇摆或漂移现象。
出现这种现象的主要原因是轮胎动态不平衡,这种车轮不平衡不仅仅影响乘坐者舒适度和汽车稳定性,也会使燃油量增和加剧轮胎磨损程度,使汽车质量和安全性得不到有效保障。
这种情况下,有必要采用先进的检测手段对车轮动平衡进行检测,以将轮胎危险指数降至最低。
文中主要对影响轮胎不平衡因素、汽车轮胎平衡检测原理和基于汽车轮胎动平衡检测机的应用等方面进行了论述。
一、影响轮胎不平衡的因素车辆在行驶过程中,难免会因为磨损问题而使汽车性能降低。
在汽车各部件中,轮胎的磨损程度是比较明显的,尤其是汽车轮胎受不同因素影响而出现的不平衡问题。
因轮胎的轮辋或挡圈几何形变或密度不均匀而引起的轮胎不平衡是比较常见的,一旦受这种因素影响,汽车轮胎就会出现严重的重心偏离现象;汽车送进维修中心修理时,维修中心工作人员对轮胎进行拆卸安装后,汽车轮胎和汽车之间的整体协调性会受到破坏,从而引起轮胎不平衡;汽车行驶过程中受主客观因素的影响会发生碰撞,碰撞后会使车辆变形车轮偏离原有位置,这种现象也会使轮胎出现不平衡;汽车在高速公路行驶过程中,很多时候会因制动静止而使车轮横纵向滑移,引起汽车轮胎局部磨损,最终导致车轮不平衡。
此外,轮胎补修也会使车轮出现不平衡现象。
因此,必须对影响轮胎不平衡因素进行分析,从实际出发对轮胎进行有效的测量和调整,以保证汽车行驶质量。
- 1、下载文档前请自行甄别文档内容的完整性,平台不提供额外的编辑、内容补充、找答案等附加服务。
- 2、"仅部分预览"的文档,不可在线预览部分如存在完整性等问题,可反馈申请退款(可完整预览的文档不适用该条件!)。
- 3、如文档侵犯您的权益,请联系客服反馈,我们会尽快为您处理(人工客服工作时间:9:00-18:30)。
汽车轮胎常见故障现象与动平衡检测
一.常见异常现象的故障判断
1、大部分平衡机的测量系统都具有“自检”功能,此功能可以检测测量系统本身是否正常。
与“自检”功能对应的操作按键可能会标注为“自检”或“TEST”等。
用户可以在平衡机正常时,将各种设定的支承条件(支承方式及a、b、c及两个半径等)固定,然后使测量系统进入“自检”状态,记录下对应此支承条件下的“自检”状态的显示读数。
当操作者认为测量系统有问题时,可以使测量系统恢复到对应原设定的支承条件下的“自检”状态,然后检查测量系统的显示读数是否正常。
2、平衡机显示的不平衡量的角度总在大致相差180度或0度左右。
首先确认平衡机正常运转测量而且转子仍有一定的残余不平衡量(甚至可以在两个配重面上分别给转子加装两个不同相位的不平衡量),在转子正常旋转测量的情况下:拔下1号传感器线插头,看仪表显示数值有无变化。
如有明显变化,则证明此传感器线和传感器一切正常。
如无变化,则证明此传感器线或传感器有问题。
将1号插头插好,再将2号传感器线插头拔下,同样的方法可以判断2号传感器线和传感器是否正常。
使用者可以找专业人员对照另一个传感器线和传感器对有故障的传感器线或传感器进行修理。
3、平衡机在残余不平衡量较大时,故障不明显。
但在残余不平衡量较小时,一次启动平衡机进入测量时,显示不平衡量值的角度总在变化。
有时角度在一定范围内变化,有时角度在360度范围内变化。
①
为减少同频、倍频、分频干扰,工件支承轴径应避开与支承滚轮外径或其整倍数整分数相同或接近,以免干扰。
比如:滚轮外径为101毫米,那么,最好避开使用91~111、46~55、32~36毫米范围内的轴径支承。
②严格检查转子装配部分的稳定性。
如使用工艺轴,则应着重检查轴和孔的配合。
③检查转子轴(工艺轴)与滚轮接触处的状态,如果轴径粗糙、刀纹明显或滚轮表面有伤,均会导致小信号时不稳定。
④检查滚轮与转子轴(工艺轴)接触处的状态,如果滚轮接触面上连续的光洁的外表面已经破坏,也会导致小信号时不稳定。
当滚轮的接触面上出现较明显的伤痕时,平衡量的显示是非常不稳定的。
⑤停车状态下清洁滚轮与转子轴(工艺轴)的接触面,加适量润滑油。
⑥认真计算一下,是否你的平衡精度要求太高了。
4、平衡机在残余不平衡量较大时,故障不明显。
但在残余不平衡量较小时,每次配平衡后重新启动测量时,显示不平衡量值的角度总是以大致相差180度的方式变化。
①所配平衡量偏多。
②严格检查转子装配部分的稳定性。
如使用工艺轴,则应着重严格检查配合轴和孔的间隙、椭圆度和锥度误差,尤其是椭圆度和锥度误差。
二.四点法故障诊断
按以上方法检测、维修完成后,如果故障仍然存在,可以按下面介绍的平衡机四点检验法对平衡机进行检验。
一般情况下,用户可以依此用实物转子进行。
如果有必要,用户可以将下面过程及所有数据进行记录,然后提供给平衡机的制造厂家,制造厂家可以根据这个记录判断90%以上的故障。
1、首先将转子平衡至能够达到的最高精度,然后准备一个大于转子残余不平衡量30~50倍的可拆装的配重块(以下过程按:使用配重块重100克,转子残余量应该小于2~3克)。
转子与平衡机的联结及装载形式不变,直接进入下面的试验过程。
2、检查平衡机的各种设置是否正常。
3、在转子的任一面指定配重圆周处45度上加一个已知重量的能够拆装的配重块(以下按假设配重块重100克)。
启动平衡机,平衡机对应面指示值应该在40—50度、90—110克(按90%去重率)。
4、停机后将配重块拆下安装在转子的同一面圆周135度角度上。
启动平衡机,平衡机对应面指示值应该在130—140度、90—110克(按90%去重率)。
5、停机后再将配重块拆下安装在转子的同一面圆周处225度角度上。
启动平衡机,平衡机对应面指示值应该在220—230度、90—110克(按90%去重率)。
6、停机后再将配重块拆下安装在转子的同一面圆周处315度角度上。
启动平衡机,平衡机对应面指示值应该在310—320度、90—110克(按90%去重率)。
7、同样过程,在转子的另一面指定配重圆周处4个角度上依次安装此配重块进行检查。
8、如平衡机能够达上面所述要求,则认为平衡机没有任何故障。
9、如平衡机能够近似达到以上要求,则认为平衡机有轻微定标不准
确问题。
此问题一般会引起操作效率的下降,而不致引起大的操作错误。
如平衡机有轻微定标不准确问题,用户可以按平衡机配套说明书中的内容进行排除,也可以通知制造厂家进行处理。
10、如平衡机确实不能达到上面要求,而且误差非常大,用户应通知制造厂家进行处理。
11、特殊情况下,用户对平衡机的精度或质量有怀疑时,也可以对平衡机进行四点法故障诊断。
有时用户会发现,转子在平衡机上已经达到平衡精度,通过以上方法检验认为,平衡机也一切正常,但转子实际安装运转时,还是有一定程度的振动,这时就需要认真分析其他的工艺方面原因了。
三.认真分析振动原因,正确判断真实的平衡精度
引起机械振动的原因很多,其中旋转零部件由于其平衡问题引起的振动最为直接。
但这并不说明转子在平衡机上平衡好以后,就可以解决所有的振动问题。
转子的不平衡问题,是由于转子的重心,偏离了转子的旋转几何中心线。
转子旋转时由此产生的离心力随转子一起旋转,从而激发转子及转子的安装基础(如:轴承座、机座、机箱、车身等)产生振动。
以下将讨论其他相关的一些工艺问题。
1、平衡机本身的工艺问题
高精度平衡时,应考虑万向联轴器、键等相关连接件的影响。
小转子平衡过程需要加光标等附属质量的,也需要考虑其对最终平衡精度的
影响。
当这些相关连接件引起的不平衡量接近甚至大于用户要求的转子平衡精度时,平衡机显示的不平衡量是不可靠的。
对于用万向联轴器传动的平衡机,也应定期检查万向联轴器的平衡精度。
当采用工艺轴进行平衡时,工艺轴的圆跳动不能大于转子平衡精度指标e(偏心距),否则必须进行翻转1800高精度平衡。
或者将工艺轴报废。
另外,工艺轴的结构与转子实际安装轴的结构,应尽量制作成一致或近似,保证其质量分布与实际安装状态一致。
2、转子的工艺问题
平衡机用户应尽量采用转子的真实安装状态进行平衡,并且保证其刚性。
采用工艺轴进行平衡时,就存在工艺轴与转子实际安装轴的误差,比如转子在工艺轴和实际轴上不同的安装方法、键槽结构、工艺轴和实际轴各自的跳动,这些因素都会引起不平衡量的变化。
采用工艺轴进行平衡时,必须保证转子安装孔的尺寸精度和形位公差精度,诸如:配合间隙大、孔椭圆或有锥度误差、粗糙度低等是绝对不允许的。
另外转子的刚性必须保证。
如果转子内部有滑动花键、活动块、摆动刀块等其他类似结构,这样的转子是永远达不到理想的平衡精度的。
3、转子实际安装的工艺问题
转子在平衡机上已经达到了要求的平衡精度,在转子实际安装运转时,如果在实际安装过程中有些因素不去认真考虑,还是会造成平衡
精度的变化,以至引起一定程度的振动。
首先是实际安装轴的跳动,这一因素非常重要。
因为转子的不平衡问题,就是由于转子的重心,偏离了转子的旋转几何中心线。
转子旋转时由此产生的离心力随转子一起旋转,从而激发转子及转子的安装基础产生振动。
而平衡好的转子被安装在有偏心的实际安装轴上,当然会导致转子及机器的振动。
另外,与转子同轴的其他零部件也会导致转子及机器的振动,如皮带轮、联轴器、电机转子等,他们的平衡精度也会与转子一起参与到机器的振动中。
4、其他问题
我公司技术人员在进行售后服务时发现,有个别平衡机用户在其产品生产过程中,不注意把握其产品的前期制造质量,而将其转子的运转性能完全依赖于动平衡工序,这是非常不严肃的。
比如:
产品设计时不考虑动平衡工序的工艺性;
产品的基础件(如支架等)偷工减料甚至有严重缺陷;
风机转子或其他焊接结构转子的外形端面跳动过大;
铸造转子的质量分布不均匀误差过大;
转子的安装孔精度和粗糙度太低;
转子内部结构存在严重的非刚性因素(如:漏焊、铆钉松动等);工艺轴的粗糙度及精度太低;
转子实际安装轴精度和粗糙度太低;
…………。
所有这些因素都会导致平衡精度的降低甚至平衡失败。
另外,动平衡机属仪器仪表类试验机产品。
对平衡机的野蛮操作(如:在平衡机上进行焊接、砂磨等)也会直接影响平衡机性能及寿命,导致平衡失败,千万注意。